
2 minute read
Helping a pressure washer manufacturer perfect its products
When Electrajet, a leading manufacturer of forecourt and commercial pressure washer systems, wanted to improve dosing precision, chemical consumption monitoring and cost control for its customers, SEKO was commissioned to provide a bespoke pump solution.
Electrajet’s clients include commercial vehicle washes, car dealerships, food producers and sanitation specialists – all of whom share not only exacting standards but also the need to work within tight budgets amidst challenging economic conditions.
In such applications where regular, sustained equipment use means heavy chemical consumption, operators can make a significant financial impact by reducing detergent wastage.
That’s why Electrajet, keen to offer its customers the best-performing yet costeffective systems, approached SEKO with a requirement for high-precision chemical dosing pump systems to be installed in jetwash equipment and static pressure washing units.
These applications require chemical to be injected at set rates into high-pressure systems, and SEKO’s experience in the design and manufacture of dosing pumps for the water-treatment industry meant they were the natural choice for the project.
Previously, Electrajet’s system designers had found it challenging to source dosing pumps capable of achieving the ultra-precise chemical injection that would set their products apart from the competition by helping their customers save money and improve sustainability.
Another common challenge facing operators of commercial vehicle wash sites is equipment durability. Subjected to frequent and often heavy-handed usage, these systems must be robust enough to perform consistently and ensure availability at all times – especially important in hygiene-critical applications where vehicles must be cleaned with high frequency to prevent contamination.
Robust and reliable for extensive lifespan
Having taken these requirements into consideration, and after a thorough review of Electrajet’s existing systems and applications, SEKO recommended its P Series peristaltic pumps and Invikta solenoid-driven dosing pump as the ideal solutions for their equipment.

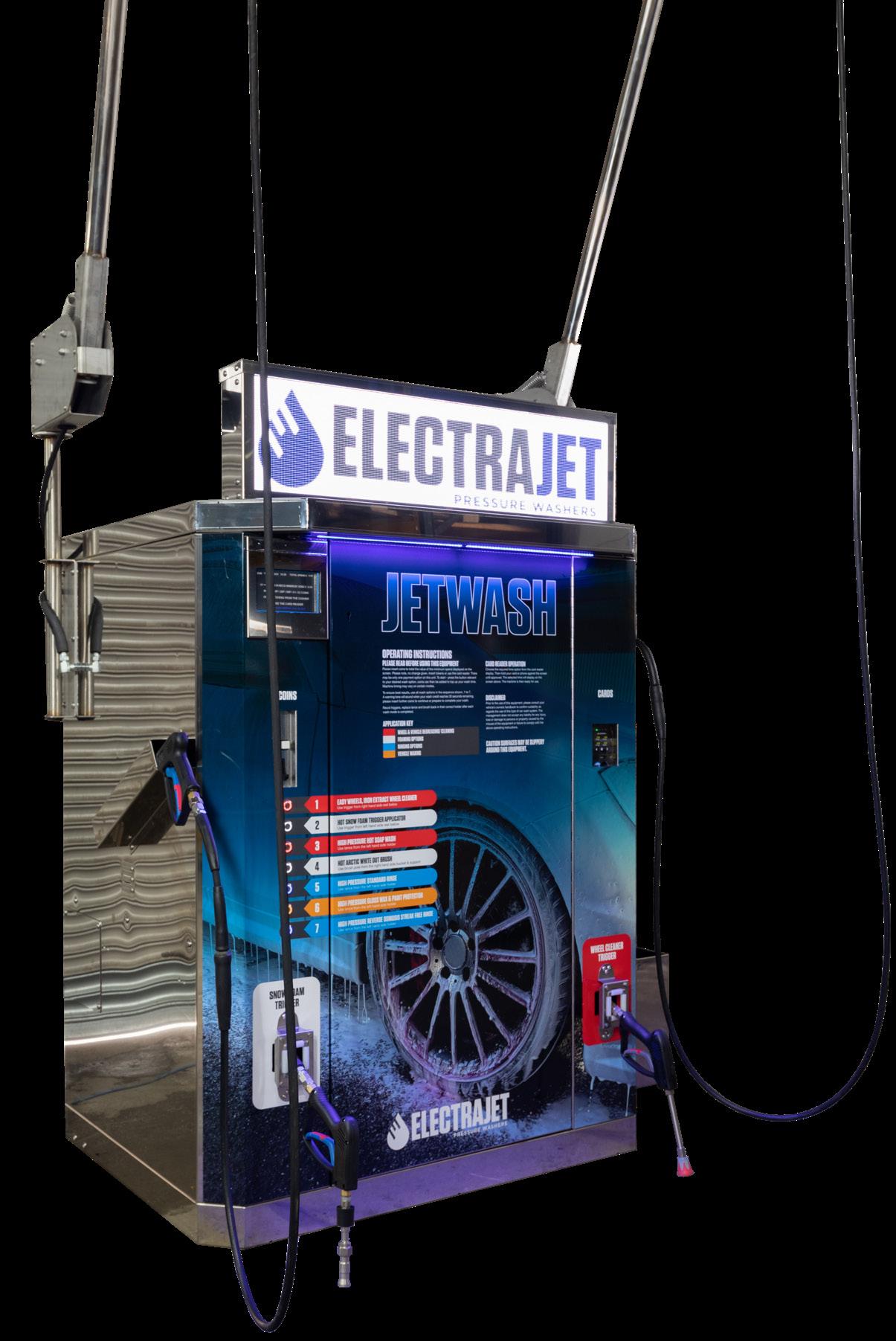
Crucially, the P Series’ and Invikta’s trademark high-precision dosing meant Electrajet’s product design team was able to calculate a precise cost in use for its systems.
This would enable the company’s business development team to present clients with an accurate, real-world figure that they could relate to – an invaluable sales tool amid rising chemical, water and energy prices.
A perfect fit
Meanwhile, with its dust-tight IP65 housing, Invikta offers excellent resistance to water jets – the perfect solution for pressure washer units used on forecourts and commercial sites that are exposed to powerful spray on a regular basis.
The P Series shares Invikta’s IP65 ingress protection and is supplied with premium-grade Santoprene peristaltic tubing as standard, with its excellent chemical compatibility ensuring dosing remains precise and consistent for longer while reducing service requirement.
Invikta’s design includes ceramic ball valves, PTFE diaphragm and PVDF-T pump head, with these components offering superior chemical compatibility for extended lifespan. This durability –backed up by a five-year guarantee on wetted parts – ensures dosing remains accurate for longer, giving Electrajet customers greater value for money while reducing service requirement.
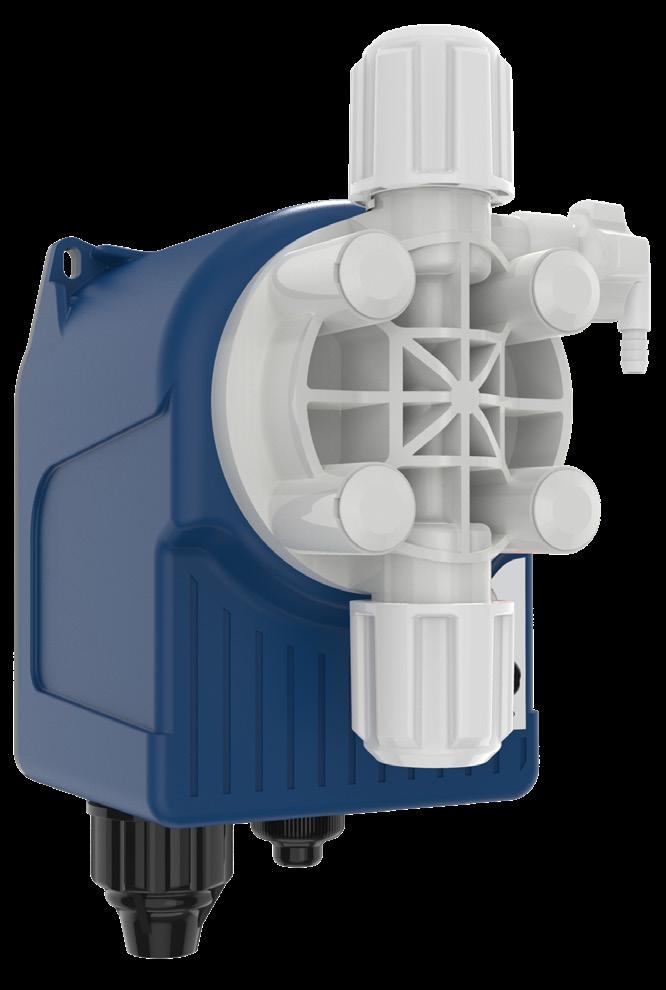
The pump is easy to mount courtesy of dedicated fixing brackets, while tube replacement can be performed without starting the pump – making the P Series among SEKO’s most convenient solutions.
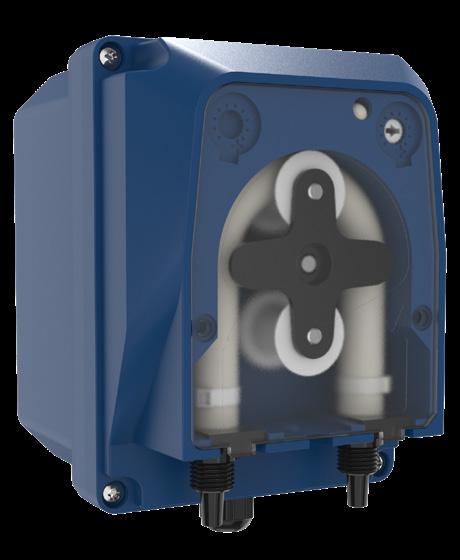
With the pumps having been fitted and the new jetwash systems assembled, Neil Harrison, Director at Electrajet, was delighted with the outcome of the SEKO collaboration:
“The pumps are robust and simple to fit as well as being easy to access during maintenance, making them serviceable for engineers.”
Another example of a SEKO solution helping customers achieve long-term, cost-effective improvements in their daily operations.
Invikta specification
• Flow rate: 0.2–5 l/h
• Pressure: up to 7 bar (101.5 psi)
• Stroke rate: 20 – 160 strokes/minute
• Wetted part materials: PVDF, PTFE, EPDM, FPM and ceramic
• Power supply: 90–265 VAC (20-60 VAC on request)
• Ingress protection: IP65
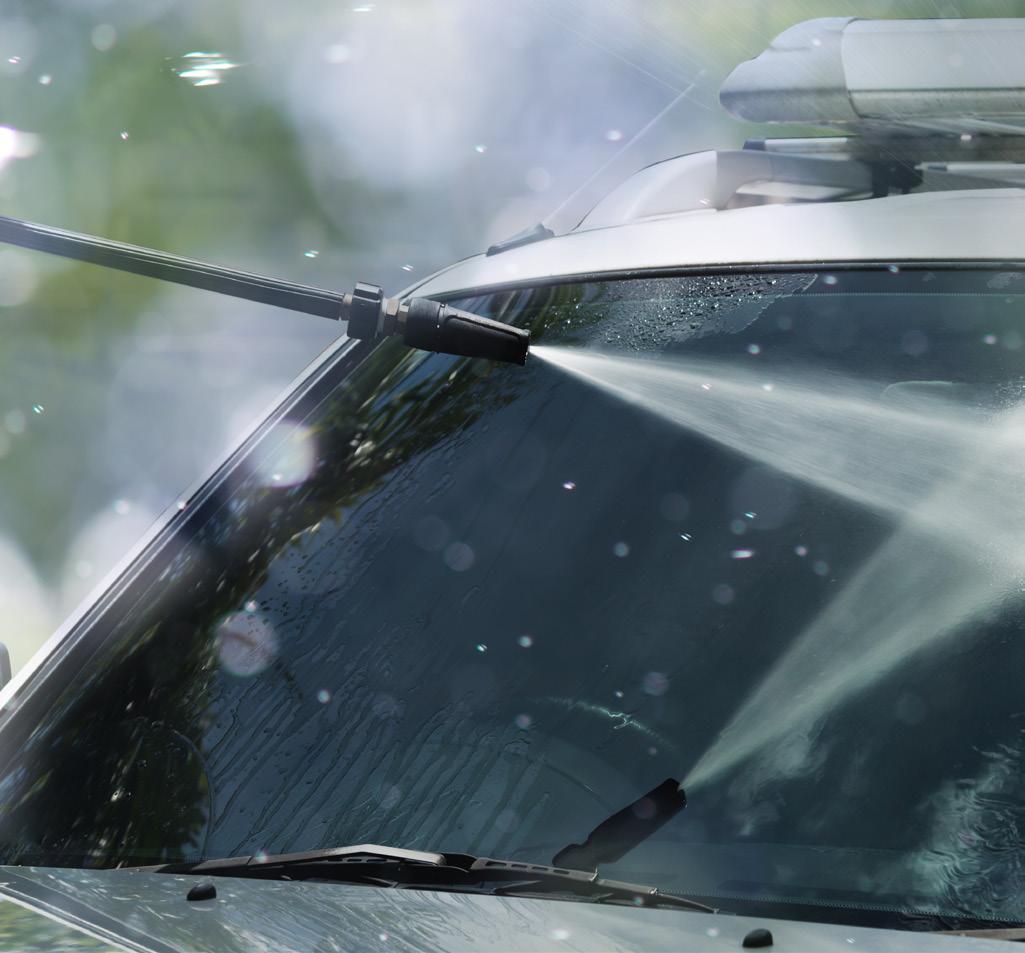
P Series specification
• Power: 100 - 1,230 V, 50 - 60 Hz
• Power consumption: 3.5 - 5 W
• Flow rate: 0.4 - 18 l/h