11 minute read
news
Next Article
news 26
A new partner in Hungary providing their vast experience in sheet metal working
Lamitec Kft. is Lantek’s newest partner in Hungary. The newly established company, based in Budaörs, to the west of the capital Budapest, specializes in sales, automation, and support of CNC sheet metal working machines utilizing various technologies.
Lamitec might be new, but their stakeholders are not amateurs. The company originated in 2019 from GE-CO Hungary which, over the past 22 years, has developed into one of the leading machine tool manufacturers in the Hungarian market. Within four years, the sheet metal working department, which was created in 2015, has grown to the point where it now operates independently. As a subsidiary, Lamitec dedicates itself exclusively to sheet metal working to meet the increasing needs of customers with tailor-made offers and state-of-the-art processing machines, to offer them a comprehensive service, and to also find suitable partners to this end. One of these partners is Lantek. “We see ourselves as a technology integrator rather than a company selling machines,” says Tamás Kutnyánszky, Managing Director of Lamitec. “We want to help our customers unlock the full potential of their cutting machines, and a key factor is how they use digital information.” Industry 4.0 is on everyone’s lips in Hungary as well. However, before the smart factory can become a reality, many Hungarian companies need to catch up in terms of production management to first increase productivity. Lamitec wants to close this gap by using Lantek’s software. Kutnyánszky describes the potential: “Companies receive 2D or 3D files from their customers and must therefore be able to calculate quotes in the shortest possible time.
We see ourselves as a technology integrator rather than a company selling machines
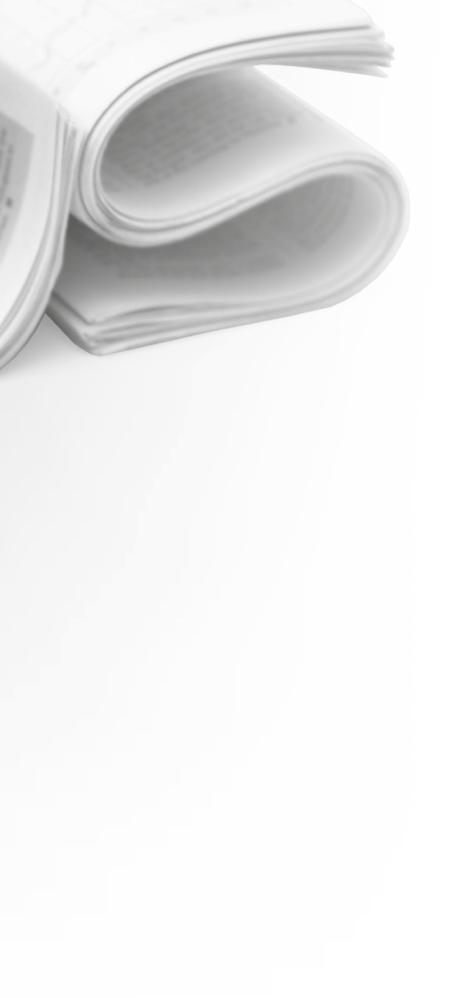
In addition, they must be able to manage the orders in production and simultaneously reduce the amount of residual sheet metal to a minimum. The better they use the available data, the more efficiently they work. So, it’s obvious what companies need to focus on: Software makes the difference.”
Currently, Lamitec mainly equips their laser cutting and punching machines from Ermkasan with Lantek software, and also offers it as an option for the manufacturer’s plasma cutting machines. “Lantek’s strength lies in its international background, quick response times, excellent sales team, and technical support,” says Kutnyánszky, explaining why Lantek was chosen.
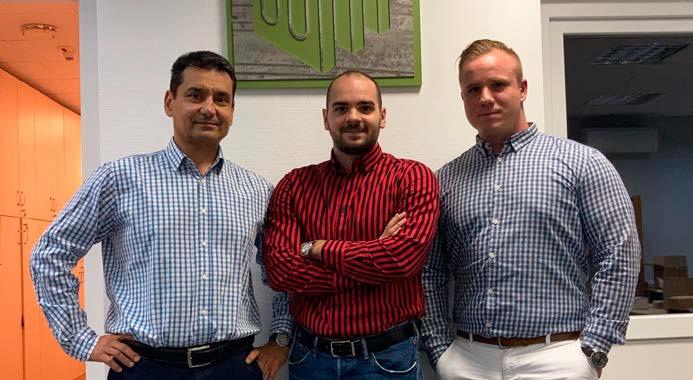
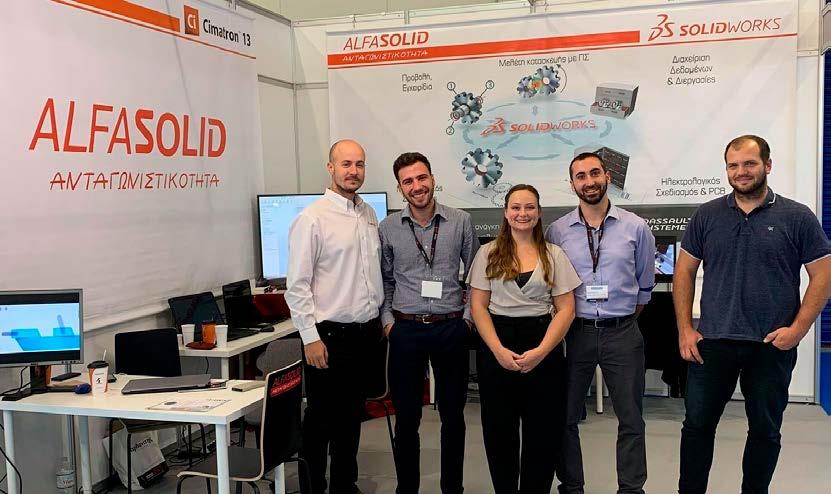
Increased presence in Southern Europe
AlfaSolid is our new sales partner in Greece and Cyprus
AlfaSolid is Lantek’s new partner for Greece and Cyprus. The Greek company is a pioneer and expert in the field of 3D mechanical design, particularly in the industrial environment, production and tooling, medical technology, household appliances and transport. With this agreement, an important alliance is being forged between two companies whose expertise and experience complement each other. It includes all Lantek CAD/ CAM products for which AlfaSolid provides sales, installation, and support. With the addition of AlfaSolid into its global distribution network, Lantek, a pioneer in the worldwide digital transformation of the sector, strengthens its position in the Southern European market. With AlfaSolid, Lantek now has distributors in over two dozen locations worldwide. They complement Lantek’s 20 offices in 14 countries and consolidate the global network for the service and availability of Lantek’s expertise to more than 24,800 customers in over 100 countries. “As part of this agreement, we have initiated market research into our range of ERP and MES solutions for companies in the sheet metal processing sector, with which we intend to be their technological partner on the road toward Industry 4.0,” says Juan José Colas, Sales and Marketing Director at Lantek. Dimitri Manolis, General Manager of AlfaSolid, is “convinced that a partnership will enable us to provide our customers with better and more advanced solutions - especially in these times of great uncertainty.”
This partnership will enable us to provide our customers with better and more advanced solutions – especially in these times of great uncertainty
About AlfaSolid
Founded in 2006 by Dimitri Manolis, AlfaSolid is the distributor of SOLIDWORKS and SolidCAM in Greece and Cyprus. The high-performing team provides the Greek industry with SOLIDWORKS 3D CAD /CAM /CAE and PDM solutions, technical support, consulting, and training. AlfaSolid’s objective is to help Greek companies to develop and produce higher quality and more innovative products and to bring them to the market faster. AlfaSolid made SOLIDWORKS its first choice as a CAD solution in Greece and Cyprus - and now Lantek is to become number one in its field.
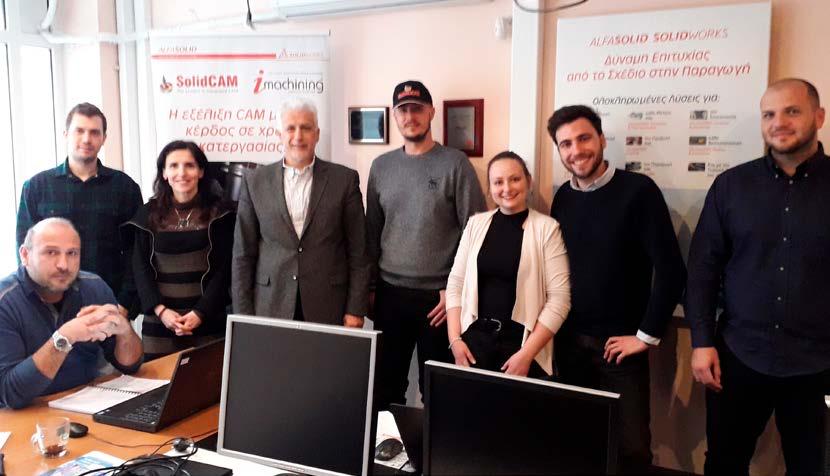
More than 1,100 new customers worldwide
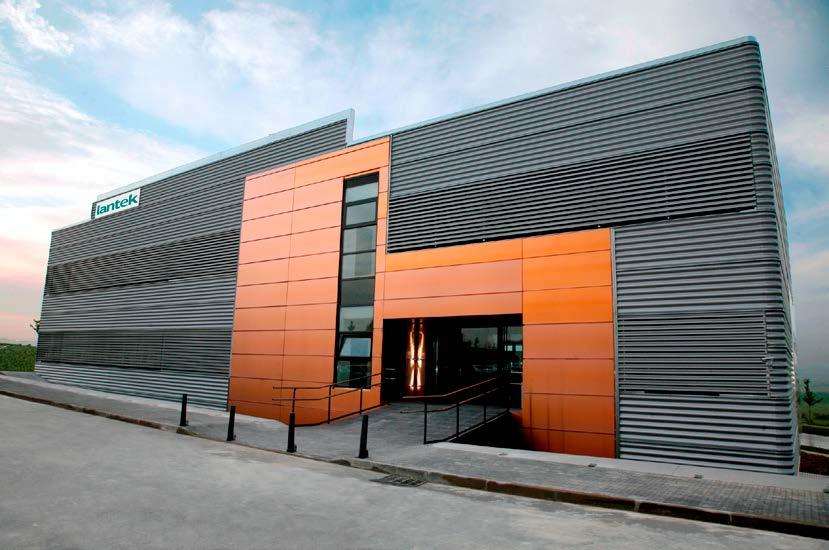
Increase in the first half of 2020 to 24,800 – Advantage of remote access. Lantek consolidates its international leading position with an increase of 1,100 new customers in the first half of 2020. Lantek gained a particularly large number of new customers in Asia, with China and Korea, followed by Europe, especially the North and East. Western Europe maintained strong growth and picked up speed in May and June. In America, the USA had the greatest impact.
The increase to a total of 24,800 customers is a further milestone - especially in these difficult times. The COVID-19 pandemic and rigid protective measures in many countries to combat it had paralyzed or, at best, slowed down production in the sheet metal processing industry. “We are very pleased with the way the market is accepting our new 2020 software version, and also with the trust that customers are placing in us to continue their business while pushing ahead with their digital transformation,” says Juan José Colás, Sales and Marketing Director at Lantek. “These are the fruits of the endeavors of the entire Lantek family. Both employees and partners have once again shown enormous professionalism and an absolute willingness to cooperate by adapting to the exceptional circumstances.” Even in the pandemic and under the conditions of the “new normal,” Lantek is providing solutions to the unsettled sheet metal processing market in the way the company does best: adaptable, so that operations are not interrupted, and production continues to increase.
Even in the pandemic and under the conditions of the “new normal”, Lantek is providing solutions to the unsettled sheet metal processing market
Accordingly, Lantek is following the trend towards working from home, enabling both its own employees and its customers to continue their work wherever they are via the Internet. The new 2020 version is prepared for all outcomes and can run in various virtualization scenarios. This means that a customer’s technical and sales staff can continue to work with Lantek products even when not on site. Likewise, Lantek can support its customers at any time and from anywhere. The innovations of the Lantek 360 cloud platform make all of this possible. “The wise use of technological breakthroughs is part of smart production. Customers expect this type of service and Lantek is ready to provide it at any time,” stresses Colás.
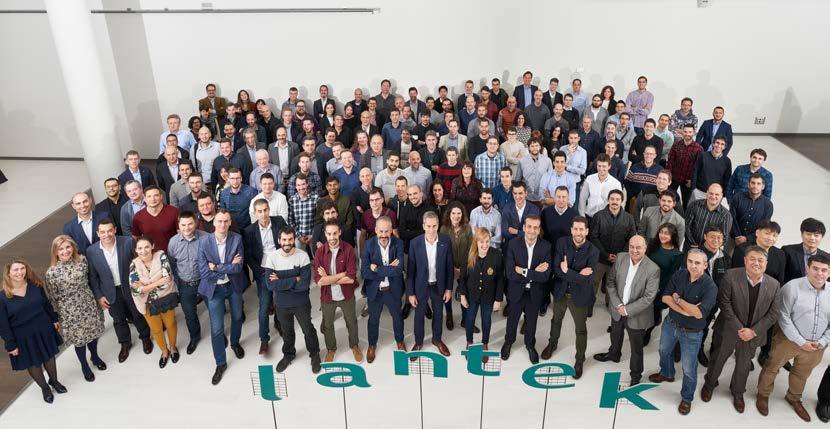
32 partners
Kerf Developments and Lantek collaboration delivers industry leading plasma technology
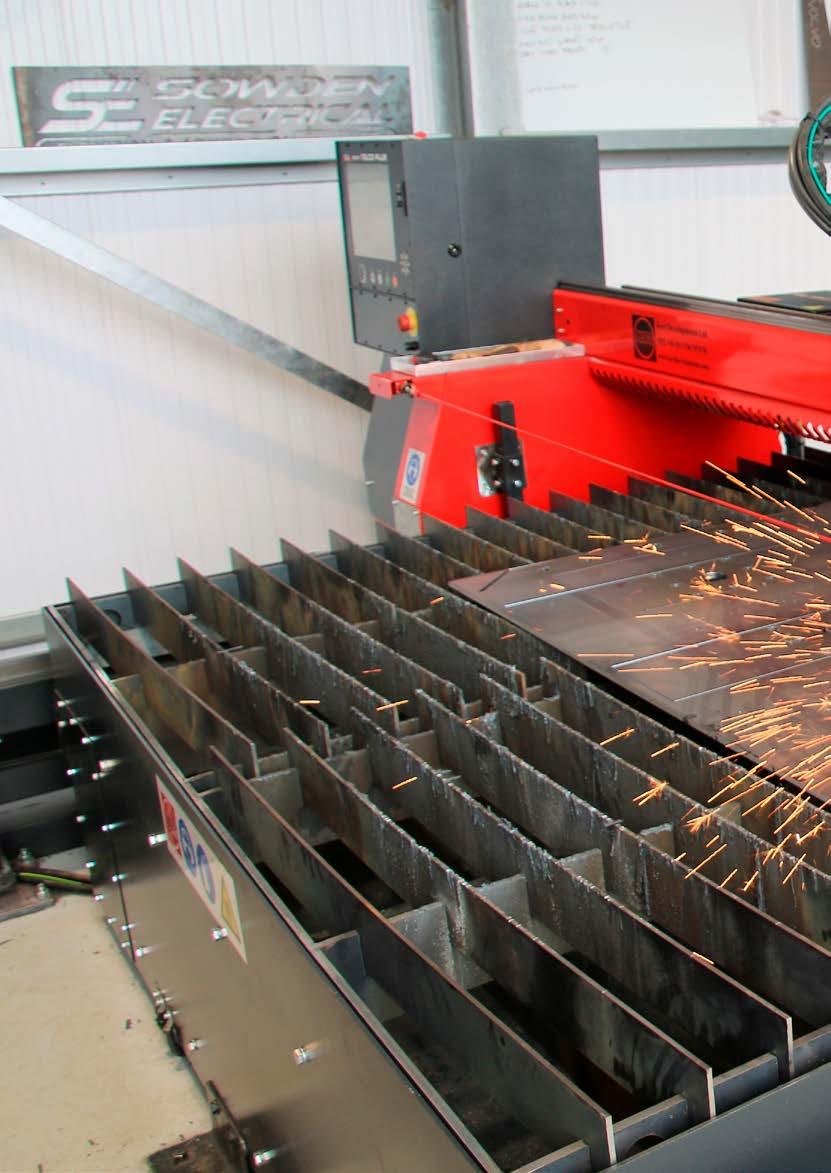
KERF DEVELOPMENTS HAS BEEN BUILDING PLASMA, OXY-FUEL, AND WATERJET CUTTING MACHINES SINCE 2002.
The company originally started as a service-based organization repairing and upgrading a broad range of profile cutting machinery. It was the experiences gained working on such a varied range of equipment that formed the basis of the current machine range. Dan Taylor, Managing Director, explains the transition to machine building, “We have a considerable amount of experience in the industry and we could see which machine configurations gave the best and most reliable performance. The machines that we build here in the workshop in Rochdale have been designed by our team of engineers which, with Kerf being completely independent, means that we can select best in class products for our turnkey solutions from leading global partners such as Lincoln Electric and Burny.”
In addition to offering a standard range of profile cutting machines, Kerf works with its customers to specify a customized machine that matches their own individual application. They design and build machines up to 4m wide and of any length with a combination of plasma and oxy-fuel heads. The smallest machine the company has supplied has a working area of 2.5m x 1.25m. The largest has a huge working area of 40m x 4m with multiple bridges.
A choice of plasma systems can be supplied with the machines ranging in cut capability from 1mm up to 90mm. For oxy-fuel applications machines can cut up to 150mm thick as standard or considerably more if the application requires it.
As part of their continued development Kerf needed to evaluate the capabilities of various CAD/CAM and nesting systems as this was becoming an everincreasing requirement from its customers. Following evaluation of several of the leading systems the one that came out on top for the engineering team at Kerf was the Lantek Expert system.
As a world leader in software for the sheet metal and fabrication sector Lantek now has over 24,800 customers in over 100 countries and 20 offices in 14 countries. Its Expert software is supported by a team of engineers around the world and is developed at the company’s Technological Excellence Center in Bilbao, Spain. Lantek has trained Kerf’s engineers so that they can provide training and first line support. Dan Taylor says, “All our field service engineers have a copy of Lantek Expert software as part of their toolbox so that they can provide an instant response to any queries. Lantek provides regular and valuable updates to the software and are always on hand to provide online support to fine tune systems and work in line with our customers’ needs.”
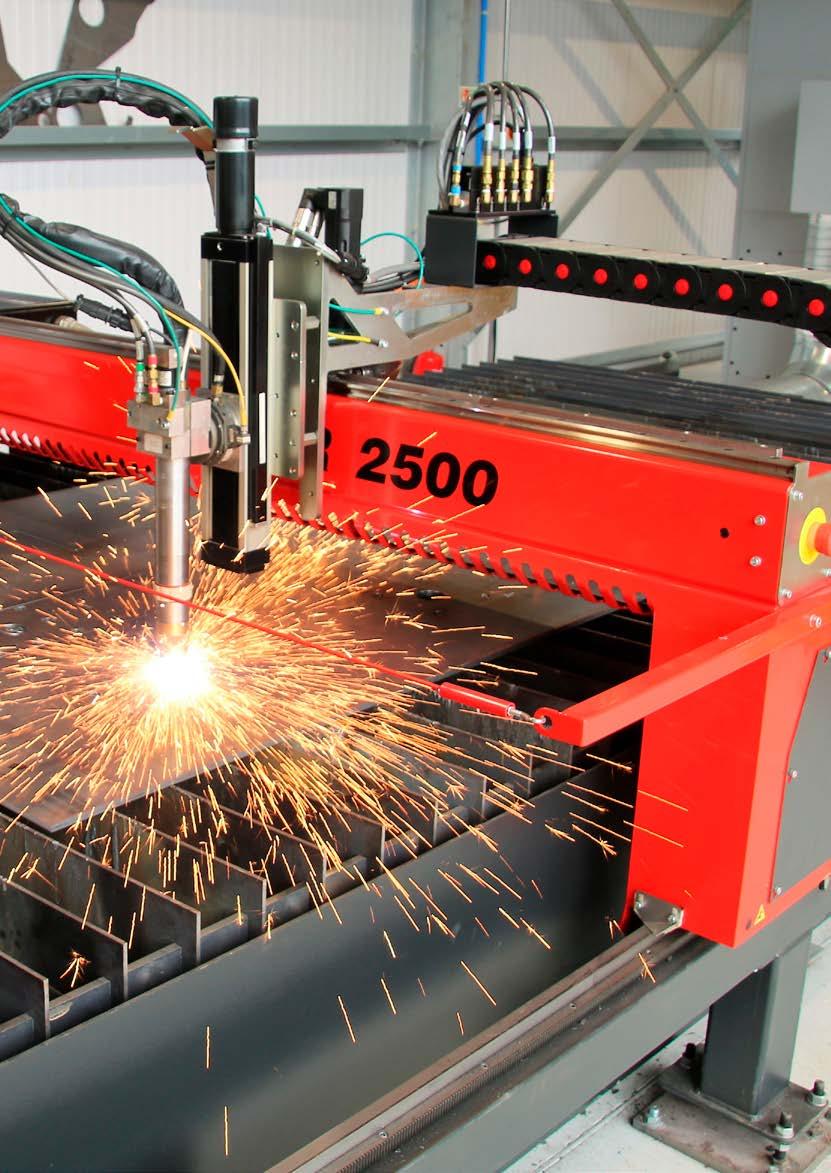
Lantek provides regular and valuable updates to the software and are always on hand to provide online support to fine tune systems and work in line with our customers’ needs
For offline programming of the cutting machines, CAD data can be imported directly into Lantek Expert, parts nested to optimize material usage, and the cutting path automatically created to provide a very fast and simple way of keeping the machine running and achieving high productivity levels and short delivery times.
As part of the collaboration, Lantek has worked closely with the engineering team at Kerf to perfect its UltraSharp technology which delivers high quality parts with a square edge, better quality edges, and 1:1 hole sizes, for example, a 5mm hole in 5mm material, a capability which would previously have been impossible on a plasma machine. For the user, this capability makes it possible to use much lower cost plasma technology rather than laser technology to manufacture parts and is especially effective for thicker components. Dan Taylor adds, “The UltraSharp technology involves internally enhanced software protocols, accelerating and decelerating the torch dynamics on tight contours and holes, controlling the power, gas pressure and flow, amongst other things, and also automatically
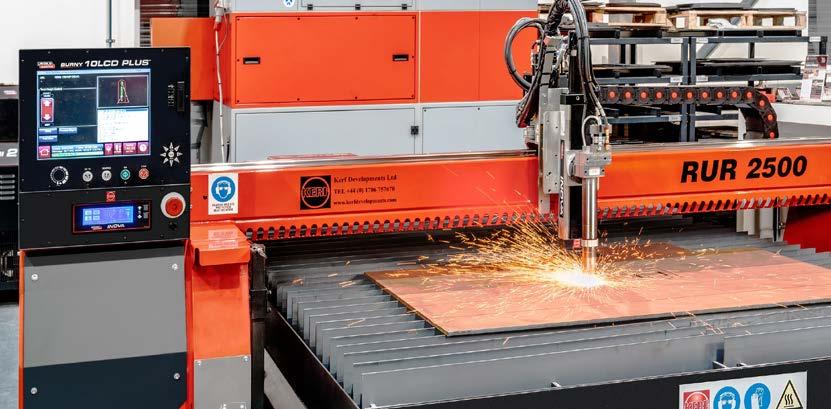
It is one of the best investments we have made. We transfer CAD data directly into Lantek, nest the parts for best yield, easily and quickly generating the CNC program
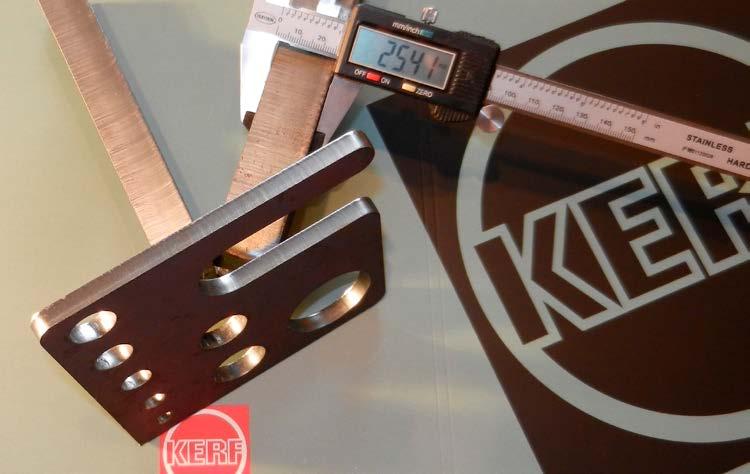
selecting special lead in and lead out configurations. The result is a constant and true arc with no lag between the top and bottom of the material being cut. All the parameters required to achieve this are built into our technology tables making it easy to achieve high quality components direct from the CAD data.”
One of Kerf Developments’ customers, Pressed Flights based in Littleborough, manufactures screw conveyors. The shape of the screw in its flat state is complex and, in many cases varies along the length of the screw depending on the material being transported.
Previously these parts were subcontracted for laser and waterjet cutting. Now the company has a Kerf RUR2500p machine with UltraSharp cutting technology and Lantek Expert software and carries out all the cutting in house achieving ± 0.25mm general tolerance. Mark Cryer, Managing Director at Pressed Flights says, “It is one of the best investments we have made. We transfer CAD data directly into Lantek, nest the parts for best yield, easily and quickly generating the CNC program. The Kerf UltraSharp plasma is very reliable producing augers which are spot on in size making it a vital part of our operation. After sales service is excellent from both companies.”
Dan Taylor concludes, “The 14-year collaboration with Lantek has enabled us to deliver industry leading technology to our customers as part of our turnkey machine packages configured to meet the demands of each client’s business. Our focus is on providing excellent service, as it has been from the start. Lantek has the same mindset making it a valuable partner for the delivery of a full process offering.”