8 minute read
interview
by Lantek
Next Article
14 interview
“Ahora con Lantek sabemos lo que pasa en el taller en tiempo real, dónde está cada una de las piezas y el progreso de cada pedido individual”
Thyrolf & Uhle
Thyrolf & Uhle ha reducido drásticamente sus existencias de retales y ha aumentado significativamente su velocidad de procesamiento con el apoyo de Lantek.
Thyrolf & Uhle se ha labrado una excelente reputación como especialista en la preparación del perfilado y láminas metálicas para ingeniería mecánica y la construcción de acero. Desde sus orígenes en 1993 en Dessau, la ciudad de la Bauhaus, la empresa ha crecido de forma constante. Hace unos años empezó su viaje individual hacia la digitalización con la ayuda de Lantek. Entrevistamos a Johannes Rieder, quien dirige la empresa junto con Frank Köppe, y Jan Rätzer, jefe de proyecto para digitalización.
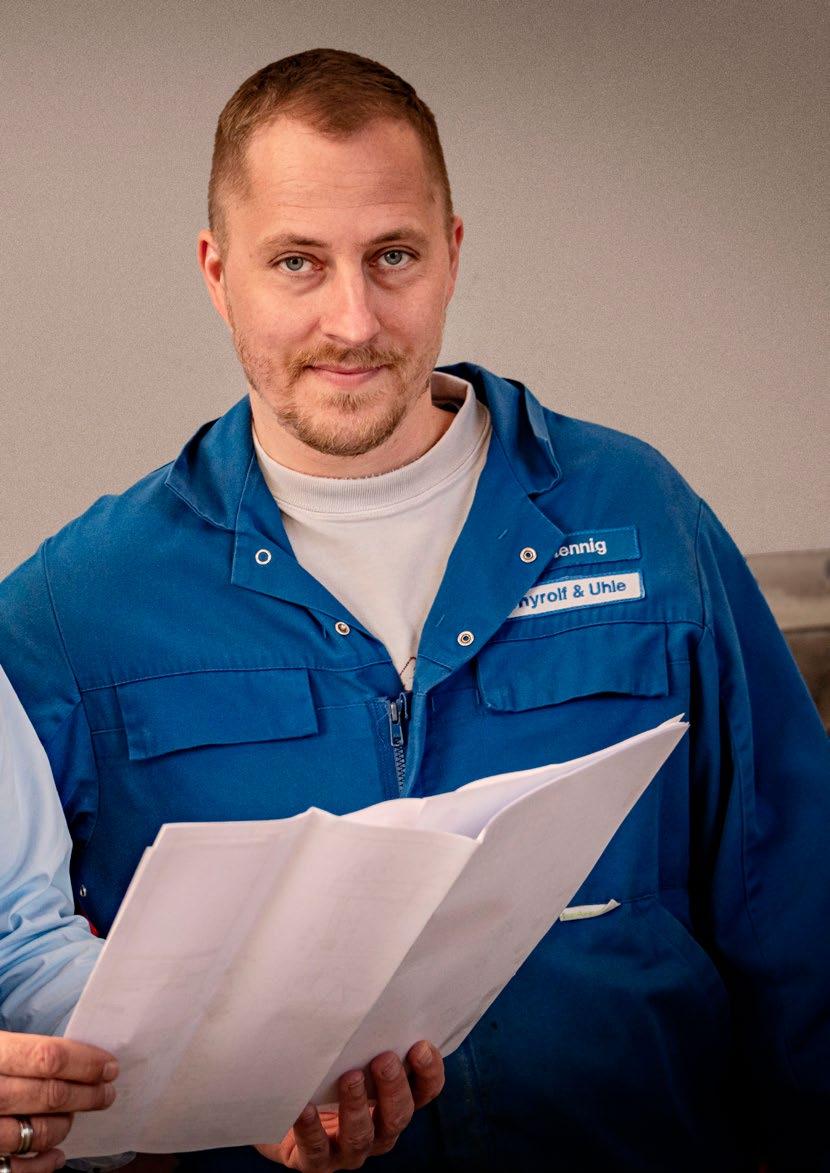
¿Qué les ha acercado a Lantek y a ustedes? Rieder: Cada año procesamos más de 10.000 toneladas de acero para el corte, el tratamiento mecánico y la construcción de acero para más de 600 clientes de industrias de lo más variadas de todo el mundo. Para ello, contamos con maquinaria muy diversa, con dos máquinas de corte láser de CO2, dos láseres de fibra, dos sistemas de oxicorte y tres máquinas de corte de plasma, además de tecnología de biselado, enrollamiento, punzonado y de boquillas, plegadoras, robots de soldadura y biselado, y centros para el procesamiento mecánico. Nuestras máquinas de corte láser tenían sistemas de programación diferentes, lo que implicaba mucho trabajo y poca flexibilidad. Queríamos una solución completa. Y entonces encontramos a Lantek, la firma desarrolladora del software de programación OEM para nuestro láser LVD. La función de su software, independiente de la máquina, y el conocimiento técnico de sus expertos fueron muy convincentes. Hace cinco años implementamos por primera vez Lantek Expert y después, gradualmente, Lantek Integra para la gestión de operaciones (ERP) y Lantek MES Manager como nuestro nuevo sistema de gestión de la producción (MES). Ahora podemos controlar todas las máquinas con un software y las tenemos a la vista en todo momento: con derechos de acceso controlados según el puesto y las autorizaciones.
¿Su cooperación con Lantek tiene más ventajas? Rieder: Ahora sabemos lo que pasa en el taller en tiempo real, dónde está cada una de las piezas y el progreso de cada pedido individual. Gracias a este software hemos aumentado nuestra velocidad un 30%, hemos reducido significativamente nuestra tasa de chatarra, hemos disminuido nuestras existencias de restos un 70% y hemos recortado los costes de la gestión de materiales en una suma de seis dígitos. Solamente la eliminación de los tiempos de espera y búsqueda minimizó significativamente nuestros tiempos de procesamiento. ¿A qué se debe? Rätzer: Solíamos trabajar en base a los pedidos. Habitualmente, estábamos registrando un rendimiento potente, una orientación ilimitada al cliente y un cumplimiento inflexible de las fechas de entrega. Para ello, solíamos definir prioridades para nuestros pedidos a diario y, como resultado, teníamos una planificación de la producción día a día, a corto plazo. La planificación estaba a la vista: más allá de un determinado tamaño de empresa y de una determinada cantidad de pedidos, esto dio lugar a tiempos de procesamiento más prolongados. La planificación se volvió imprecisa e inefectiva. El día que implementamos Lantek Integra dejamos atrás todos estos problemas. A día de hoy, vemos de un vistazo cómo hay que organizar los pedidos para optimizar cada serie. Se puede prescindir de la sesión informativa diaria: todo está escrito en el sistema. Al fin y al cabo, las tareas difíciles hay que debatirlas en persona, pero no las estándar.
¿Cómo definiría su método de trabajo actual? Rätzer: Basado en piezas. En cuanto se recibe un pedido, la programación y la producción no ven más que piezas individuales que deben ser planificadas por el sistema según su esfuerzo de procesamiento. La programación realiza un anidamiento muy efectivo de la lámina y el anidamiento respectivo recibe automáticamente la fecha de la pieza que se debe terminar primero. Cada una de las piezas se abre paso individualmente a través de la producción y, al final, todo se junta en el departamento de envíos. Esto solo es posible con el sistema de alto rendimiento que ofrece Lantek. Sin él, perderíamos la cuenta en un santiamén.
¿De dónde proceden los grandes ahorros en su gestión de materiales? Rieder: También solíamos comprar en base a los pedidos, lo cual acumulaba demasiado material, ya que se compartían muy pocos pedidos.
Apostamos por un procesamiento basado en piezas, lo que nos permite optimizar el procesamiento ya que el sistema solo ve la pieza individual y la fecha de entrega, algo que no ocurría con el método basado en pedidos
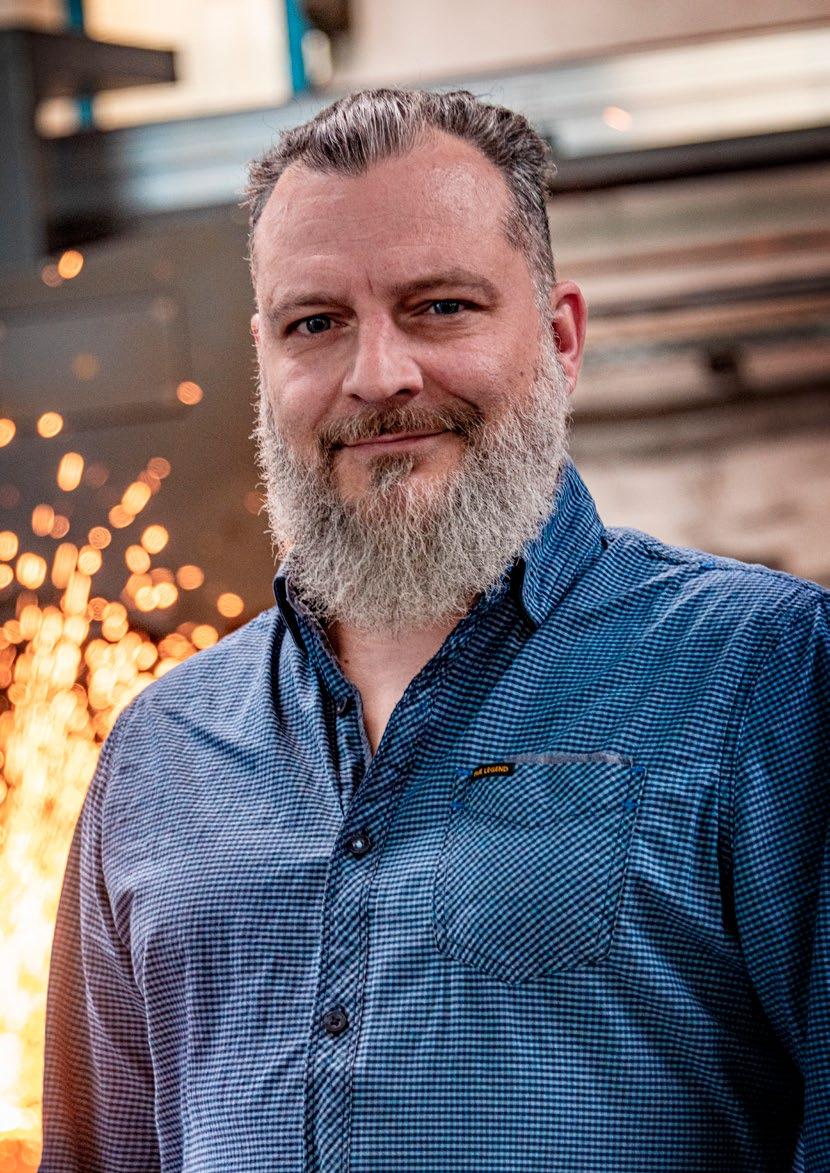
... y el resto es chatarra inservible
En consecuencia, con frecuencia pedíamos las mismas láminas varias veces en sucesión rápida y también se enviaban, con los respectivos costes logísticos. Actualmente, combinamos pedidos, lo cual nos acarrea menos gastos logísticos. El corte era elaborado y producía demasiados restos, ya que también cortábamos en base a los pedidos. El tiempo sin corte para la logística de los restos era demasiado grande. El mercado aceptó estos costes durante un tiempo, pero esto cambió en los últimos años.
¿Cómo cambiaron sus procesos? Rätzer: En primer lugar, registrando de manera geométrica todas nuestras láminas residuales y numerándolas individualmente. Pero ahora preferimos evitar de entrada estas láminas residuales. Tras un pedido, se tarda entre tres y cinco días en enviar una lámina. Empleamos este tiempo para anidar el mayor número de piezas posible en esta lámina en concreto y, con frecuencia, el resto es chatarra inservible. De este modo, la gestión de materiales no tiene que encargar una lámina para cada pedido nuevo, ya que la programación tiene una vista general de los restos en el sistema antes incluso de que se generen. En estos restos virtuales es posible añadir piezas al anidamiento e incluso llenar el espacio entre piezas grandes con piezas más pequeñas. Como he dicho, debido al procesamiento basado en piezas, la programación no presta atención a los pedidos en absoluto: solo ve la pieza individual y la fecha en que se debe terminar. Para optimizar el procesamiento, Lantek Expert ofrece multitud de funciones como multicabezal, microcortes, distancia al borde de la chapa, corte común o en cadena y mucho más. Uno de nuestros programadores está entusiasmado con la función de biselado. Antes tenía que introducir los biseles para cada pieza individualmente. Actualmente, solo lo hace una vez para una pieza y automáticamente se adopta para todas las demás.
Volvamos al principio: ¿cómo crean los pedidos? Rätzer: En cuanto un cliente realiza una solicitud, se importan las piezas respectivas en Lantek Integra (ahora esto es posible con archivos STEP), donde se muestran como una plantilla en la que se puede hacer clic. Todos los materiales y procesos se almacenan en el sistema, además de los datos de corte, los gráficos de tecnología de las máquinas y las tarifas individuales del cliente. Con toda esta información, el sistema calcula automáticamente el tiempo y los costes para la oferta, que prácticamente se genera al instante. Es asombroso lo mucho que depende la probabilidad de conseguir un contrato en función de cuándo se envía la oferta: hoy, mañana o incluso pasado mañana.
¿Qué pasa entonces? Rätzer: Una vez se ha aprobado la oferta, se transfiere al sistema como pedido de producción e inmediatamente aparece en el seguimiento de la producción de Lantek MES Manager, hasta que todo el pedido sale de nuestra fábrica hacia el centro de envío. Gracias a la digitalización total de este proceso, podemos hacer un seguimiento de todas las piezas, incluso después de su envío, en base a datos como medidas, calidad, valor o certificación. Para ello, se introduce el número de lote en el sistema en cuanto entra una chapa de metal y esto permite un seguimiento de todo el ciclo de vida de cada pieza recortada a partir de ella. De este modo, nuestra documentación también está completamente automatizada y podemos imprimir todos los documentos necesarios desde el sistema.
Estamos integrando los procesos que no son de corte dentro del sistema para optimizar aún más nuestro flujo de trabajo. Gracias a Lantek, nos estamos adentrando en la era digital

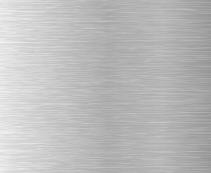
¿Cómo cambió su producción la forma de trabajo basada en piezas? Rätzer: Los empleados ya no tienen que esperar la señal del compañero que realiza el paso anterior. Todo esto se muestra en la pantalla. El jefe de taller muestra en tiempo real qué máquinas están funcionando, ofrece una visión general de su carga de trabajo y realiza un seguimiento de la producción mediante un diagrama de Gantt. También podemos planificar nuestros turnos y horas de funcionamiento. El concepto es bastante sencillo y ofrece multitud de posibilidades para generar informes según criterios individuales. Para nuestros compañeros esto ha supuesto un gran cambio, ya que tuvieron que modificar la forma de pensar y decir adiós a la producción basada en Excel. Sin embargo, dado que una lámina completamente anidada tarda entre cinco y seis horas en pasar por la máquina, tienen suficiente tiempo para asignar las piezas a su ruta posterior, para ser taladradas, soldadas, eliminar rebabas o enviarse directamente al centro de envío.
¿Tiene más planes con Lantek? Rieder: Sí, precisamente para las tareas que el Sr. Rätzer acaba de mencionar. Actualmente estamos integrando los procesos que no son de corte dentro del sistema para poder optimizar aún más nuestro flujo de trabajo. Gracias a Lantek, nos estamos adentrando en la era digital y eso es algo bueno.