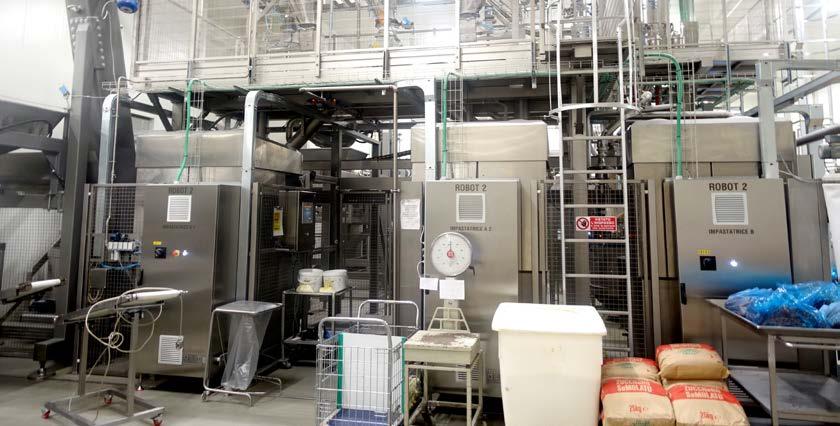
6 minute read
Efficiency through networking
The Italian baked products manufacturer Galbusera’s new production facility is taking the first steps towards Industry 4.0. Oripan, an IT company partly owned by Sancassiano, is also involved.
+A 16,000 m 2 production area south of Milan came into operation last fall. It was planned and implemented by the Italian baked products manufacturer Galbusera, which moved in the new site its production of cakes and seasonal products like panettone and Easter dove cakes from the previous site in downtown Milan. The line for panettone and dove cakes is entirely new, and the cakes line is also new, except for the oven. A third new line for a novel product is just entering the production phase, and a fourth for crackers is currently being built.
Enterprise Resource Planning (ERP)
However, the reason for the new production center was not only to increase production through more capacity and new production lines, but also the decision to take a clear step towards automation and digitization. Support for the project came from the new state funding program for Industry 4.0. The old factory already had a raw materials traceability system. According to Dante Gelmini, Head of IT, the aim here was and still is to gain more information about the detailed status of the process chain, thus raising efficiency. As an example, he illustrated some details of line Line 1, which
This controls and administers operational resources, e.g. capital, personnel or means of production, in the best possible way based on a standardized data base, and the system usually comprises materials management, sales and marketing, finance and accountancy, controlling, human resources, the management of product data, historical files, documents and an interface to production and production planning.
Manufacturing Execution System (MES)
A multi-layer fabrication management system that thinks in process chains and translates production requirements from the ERP system into the most efficient possible production planning, collects and records production, machine and operating data, and enables real-time fabrication control.
Oripan Factory System (OFS)
Undertakes communications and creates the instructions to tell machines what is to be produced, in which amounts, when and in which process chain. The starting point for the OFS is the number of SKUs (stock-keeping units = distinctly identifiable articles; article variants have different SKUs) that are to be produced. It then decides the number of batches and calculates the time up to the packaging stage.
Maschinen (PLC) produces panettone from September to December and Easter dove cakes from January to May: Breaking the production program down by process parameters and recipes, 20 different varieties and 300 different SKUs (Stock-Keeping Units) must flow through the production line efficiently and trouble-free 24/7 during this period.
Controlling individual machines and plants.
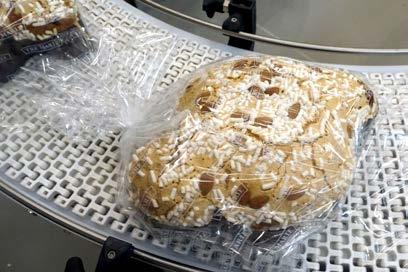
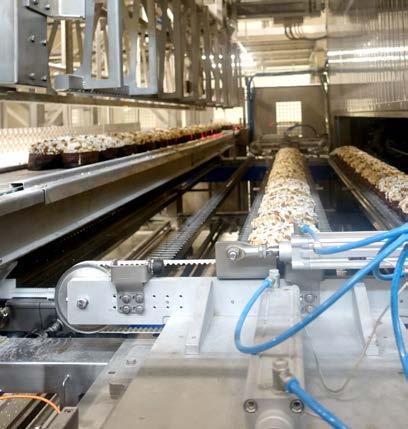
As the digitization partner, Gelmini brought on board Oripan, an IT company in Tione di Trento in which the mixer manufacturer Sancassiano in Roddi holds shares. The Piedmontese company brought in many years of process and machine knowledge, and its supervisor is responsible for the central dough preparation plant that supplies dough to all the lines. The line consists of two linear Robomixers together with metering stations for automatic loading and manual addition. There are integrated dough resting stations in which panettone doughs, for example, rest twice for up to 7.5 hours before going onto the line after a final kneading. With few exceptions, all the other plants are from Italian machine builders, and many production steps such as surface scoring, stacking flat baked products or packaging are carried out by robots. A total of 130 employees now work in the factory, 100 of them in a three-shift production operation.
Production planning starts with the Manufacturing Execution System (MES), which translates the production requirements from the ERP system into the most efficient possible
Italy promotes Industry 4.0

Italy has launched a program to promote investments that enable or speed up the automation and digitization of production processes. The national plan, “Industria 4.0”, was presented in 2016 and has provision for massive tax concessions together with numerous measures such as investments in education and training. In addition, each region is implementing its own individual broad program of incentive measures. This program has not only resulted in a considerable increase in the number of startups. In the first half of 2017, investments in machinery rose by 11.5%, in electronics by 10.7% and in research & development by 15%. In addition, Italy reduced the corporation tax rate from 27.4% to 24% in 2016.
The tax law has numerous other motivations. For example, the return on investment for certain investments up to a maximum of EUR 150,000 can be made tax-exempt for five years. There are tax credits for R&D activities, special depreciations on patents, and income tax concessions for highly-qualified people to attract them into the country.
Something that will probably make life particularly easy for Italian companies is the Finance Ministry’s plan to structure its administration in such a way that companies will now have only one contact point for both their tax liability and the subsidies.
production planning. The MES in turn sends its requirements to the Oripan Factory System, OFS, which undertakes the detailed planning.
The starting point for the OFS is the number of SKUs (stock-keeping units = distinctly identifiable articles; article variants have different SKUs) that are to be produced. It then decides the number of batches and calculates the time up to the packaging stage. To avoid congestion on the line, the supervisor plans all the processes, calculating the start of each operation backwards from the packaging phase to the raw material metering and mixing time. The algorithm optimizes the size and sequence of batches and the overlaps that may occur between them such that no collisions arise upstream the oven entry, ensuring no idling on the other hand. To this end, the first step is to verify whether all the raw materials are available and the individual stations on the line are free at the required time. Furthermore, the supervisor also checks whether the time needed to heat up the oven, or to let it cool down when necessary, was included in the calculation.
OFS synchronizes each process step with the MES and feedbacks the material consumptions for traceability and reordering purposes. It also includes raw materials warehouse supervision. The OFS correlates raw material warehouse outflow with the perspective production batches.
If people intervene in the production flow, e.g. by manually adding raw materials or giving a signal, the OFS requires confirmation by scanning barcodes on the transport containers and addition point.

The purpose of what has been installed up to now is communication and information gathering to optimize production planning. Direct interventions in individual machine controllers are reserved for subsequent further developments of the system. As the next project, Gelmini initially plans to incorporate servicing and maintenance, including preventive actions, into the factory digitization. The aim of this is to allow the company’s own technicians to immerse themselves in virtual reality, thus enabling them to remedy malfunctions based on embedded handling instructions and/or with digital support from suppliers’ technicians. Gelmini says: “We hope that will result in significantly fewer downtimes on the lines.” +++
Galbusera S.p.A.
The Italian family business was founded by Ermete Galbusera in 1930 as a cookie manufacturer in Morbegno and built up to national importance by his sons Mario and Enea Galbusera. It produces wafers, cookies and crackers on eight lines at the company’s present headquarters in Cosio Valtellino under both the Galbusera and Tre Marie owned brands, including also several private labels. A production factory opened in Vellezzo Bellini last year, producing cakes, gateaux, panettone at Christmas and colombas (dove cakes) at Easter in many variations. www.galbusera.it
Tre Marie
The Tre Marie is an historic and well-known brand in Italy, deeply rooted in the panettone and colombas markets. The previous owner, The Sammontana S.p.A., an ice cream and frozen products maker, expanded the product range to include frozen pastries such as filled croissants and cannoli. In 2013, Tre Marie was acquired by Galbusera, which carries the production of panettone, dove cakes, cookies and gateaux. Frozen pastries are yet produced by Sammontana, but the commercialization is still managed under the Tre Marie brand.
Oripan
Oripan is an Italian IT company dealing with networking complex production processes in the food industry. By using OFS (Oripan Factory System), a manufacturing execution system to plan production and automate the flow of information along the production chain in real time, Oripan lays the foundation for the process prescribed by Industry 4.0. The business is a Microsoft Partner supplying software together with selected hardware, and supports applications in Europe, Asia and North America. Oripan is a 30 years experienced company in automation and digitalization of the industrial bakeries and in 2015 become part of Sancassiano group. Oripan’s headquarters and ICT division is in Tione di Trento. The Industrial Automation division works at Sancassiano’s corporate head office in Roddi. www.oripan.it