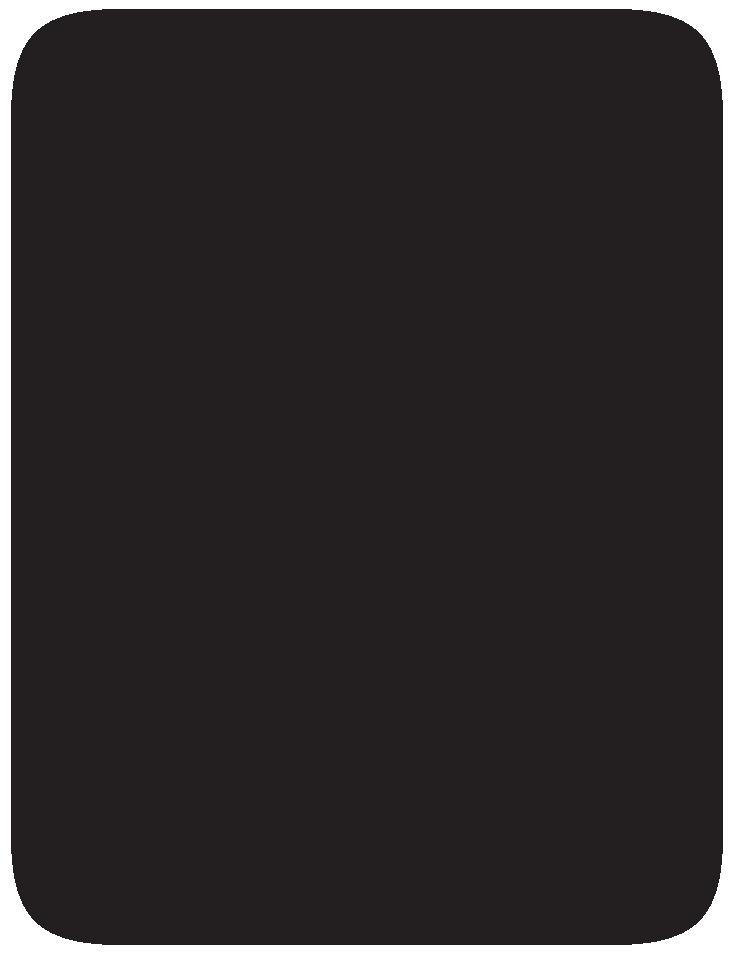
7 minute read
Successful Projects
KBL Conquers New Horizon
KBL commissioned their largest bi-directional inclined Vertical Turbine pump set at
Advertisement
Wageningen Pumping Station in Suriname.
Wageningen is the lifeline of the Nickerie rice estate area in Suriname. It’s helping the community achieve food sufficiency and facilitating their economic and social growth. The single-stage, bi-directional inclined VT pump model BHA2400S is operated with a bidirectional squirrel cage induction motor (weight 4.7 Ton) with RPM 594 and single-stage. It is majorly used in the irrigation of rice fields, drainage, disaster management, and flood control.
Supporting the Suriname Pumping Scheme
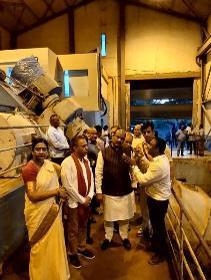
KBL has been one of the global leaders in providing pumps for irrigation, water supply, treatment, and drainage applications. With over nine decades of expertise, we have been providing fluid management solutions to customers around the world.
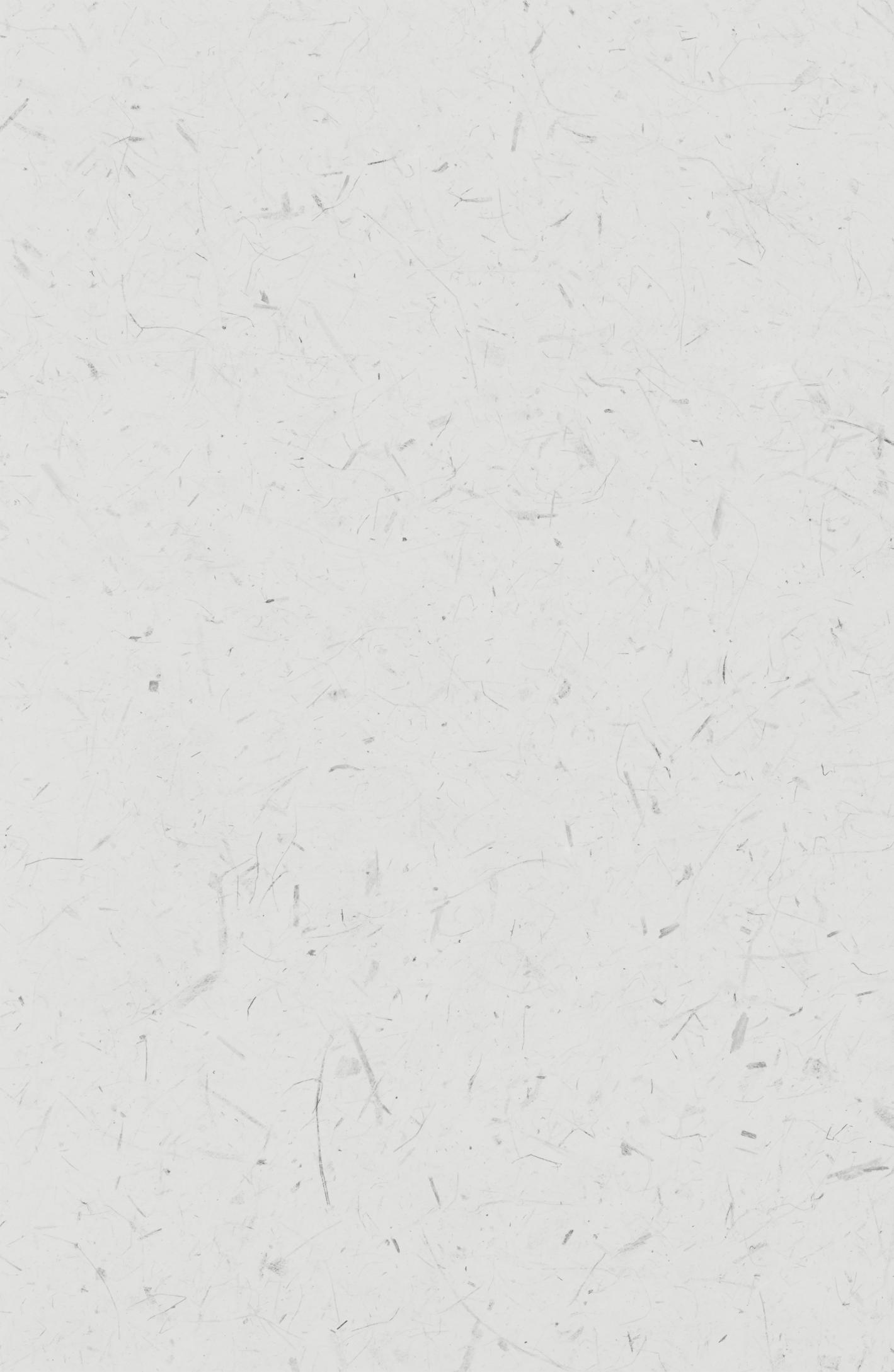
Recently, for the Wageningen Pumping Station, Suriname Project, the company provided its expertise in retro-fitment of the pump and electromechanical equipment. The KBL team provided technical support from concept to commissioning for the replacement of the pump set, electromechanical, and automation activities. The old unique pumping scheme in Suriname has inclined, bidirectional, vertical turbine pumps used for drainage and irrigation. After visiting the Suriname Wageningen Pumping Site, the team supervised electrical activity and provided technical support for the pump set commissioning. A special effort was made to commission the pumping scheme through a VFD, as the pump is designed for variable speed and bidirectional flow. After the support, the pump set satisfactorily operated in drainage and irrigation mode in the presence of the client, the Ministry of Agriculture and Fisheries in Suriname, and Indian Government Officials.
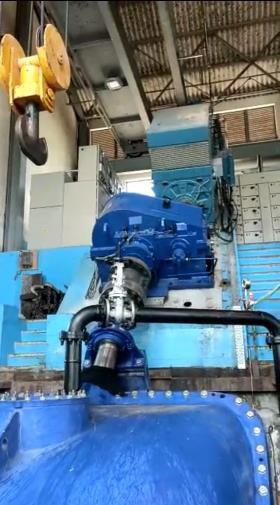
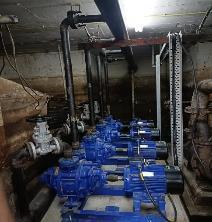
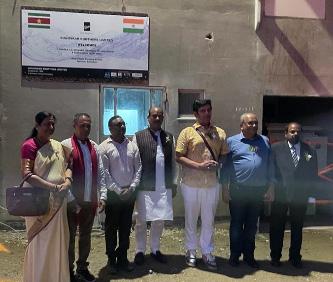
Special Pumps for Special Applications
KBL supplies Concrete Volute pump at Jawaharpur Vidyut Utpadan Nigam Limited Super Thermal Power Station.
KBL commissioned its Concrete Volute Pump (CVP) set at Jawaharpur Vidyut Utpadan Nigam Limited Super Thermal Power Station (2x660 MW) in Malawan, Etah, UP, India. The power plant has a 1.32 GW capacity and is one of the coal-fired power projects of Jawaharpur Vidyut Utpadan Nigam Ltd. (JVUNL), a 100% subsidiary of UP Rajya Vidyut Utpadan Nigam Limited (UPRVNL). The company commissioned Pump Model CVP-NV2100 single-stage Concrete Volute pumpsets, which are water-lubricated and operated with HT synchronous motor.


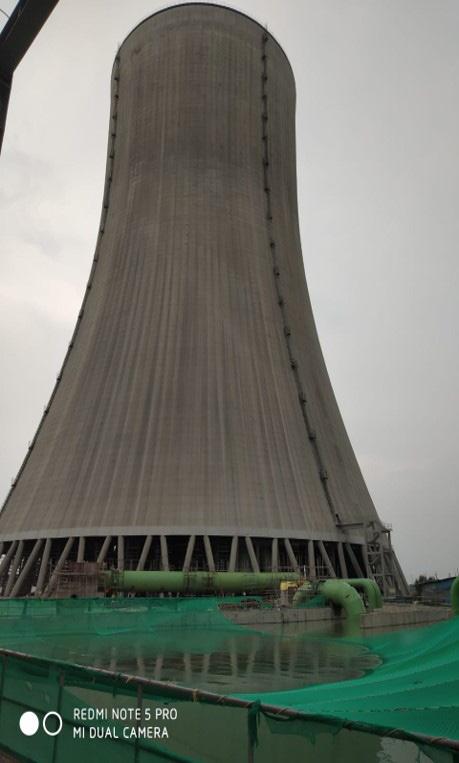
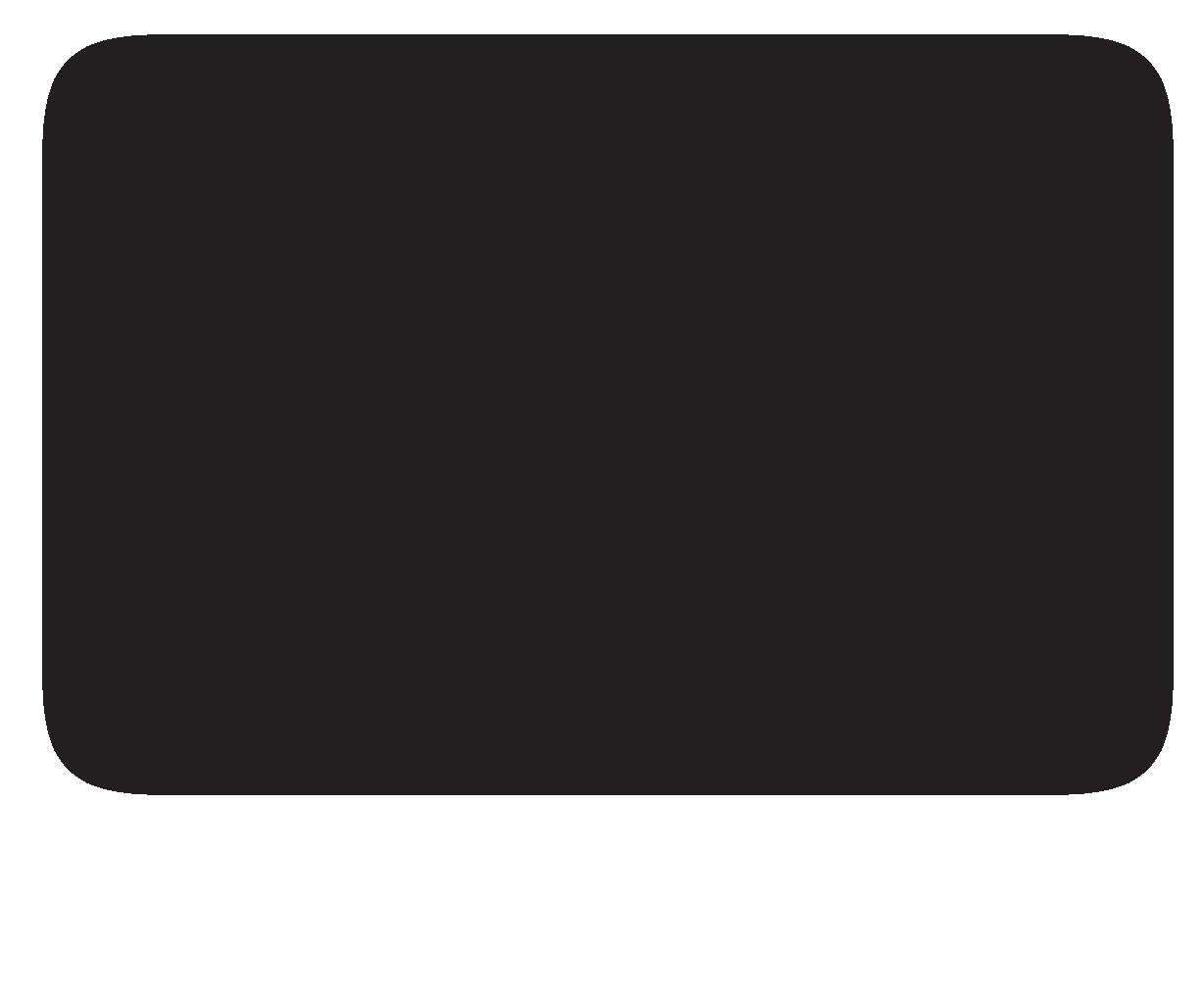
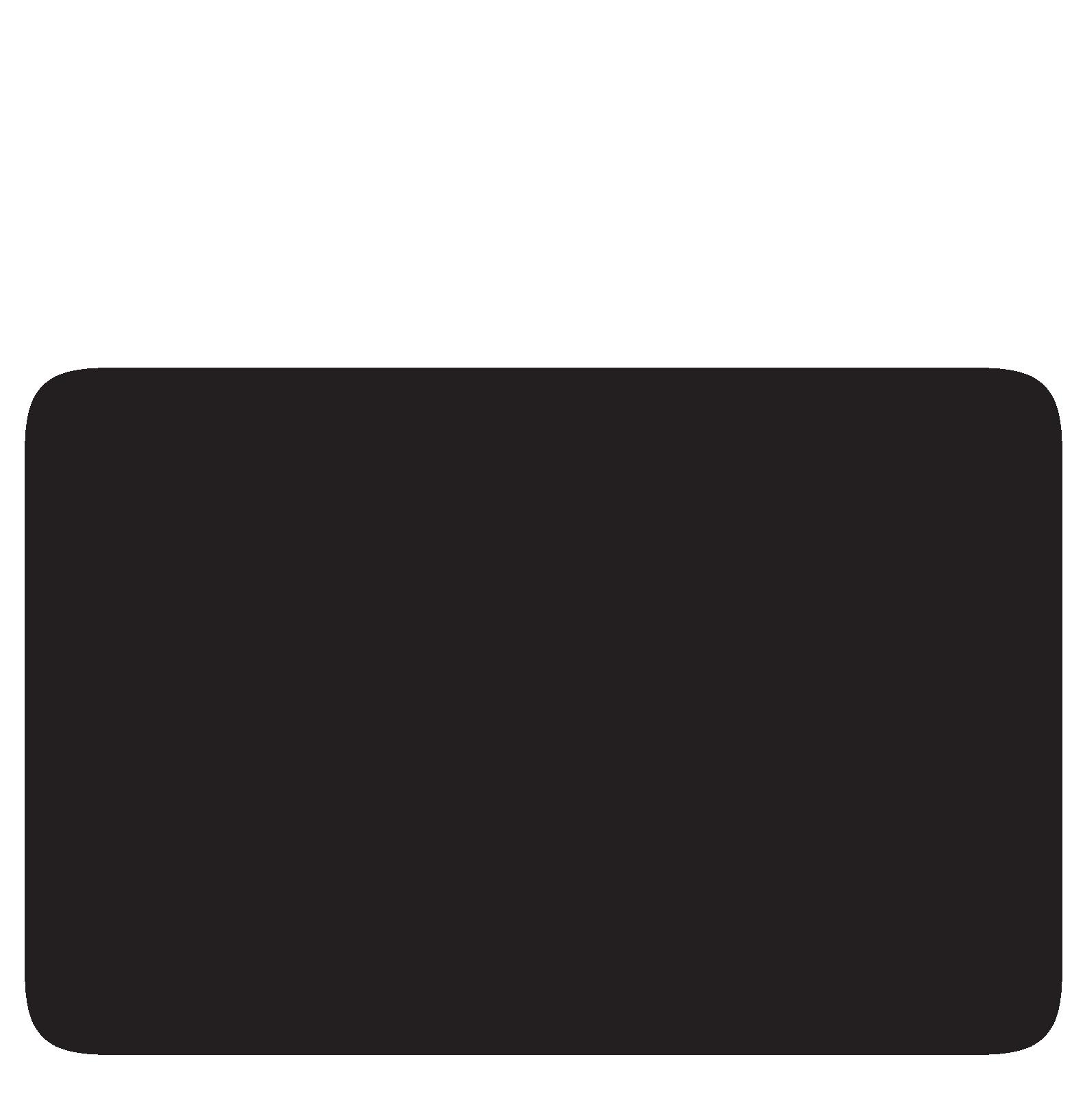
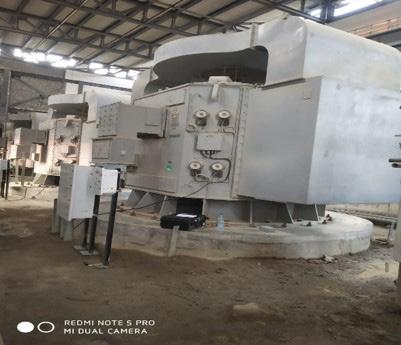
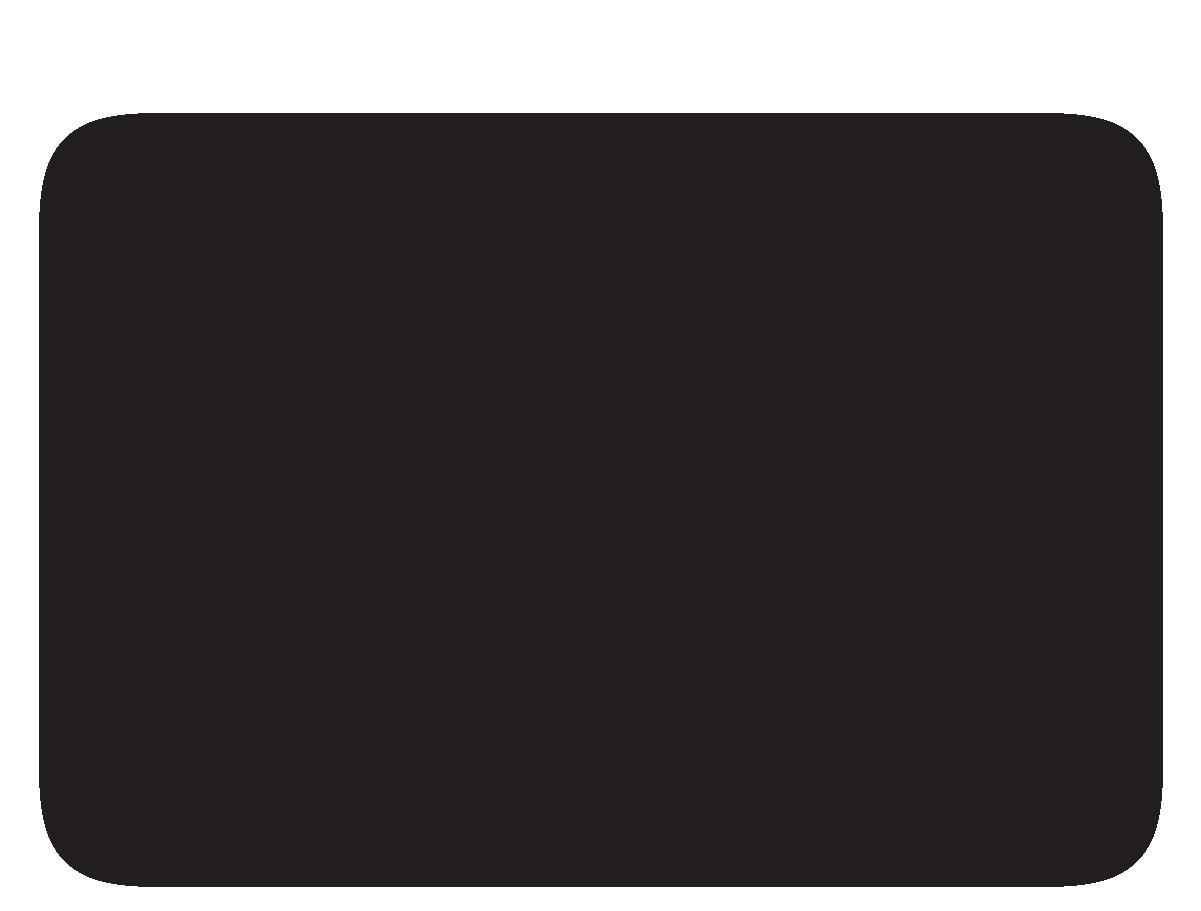
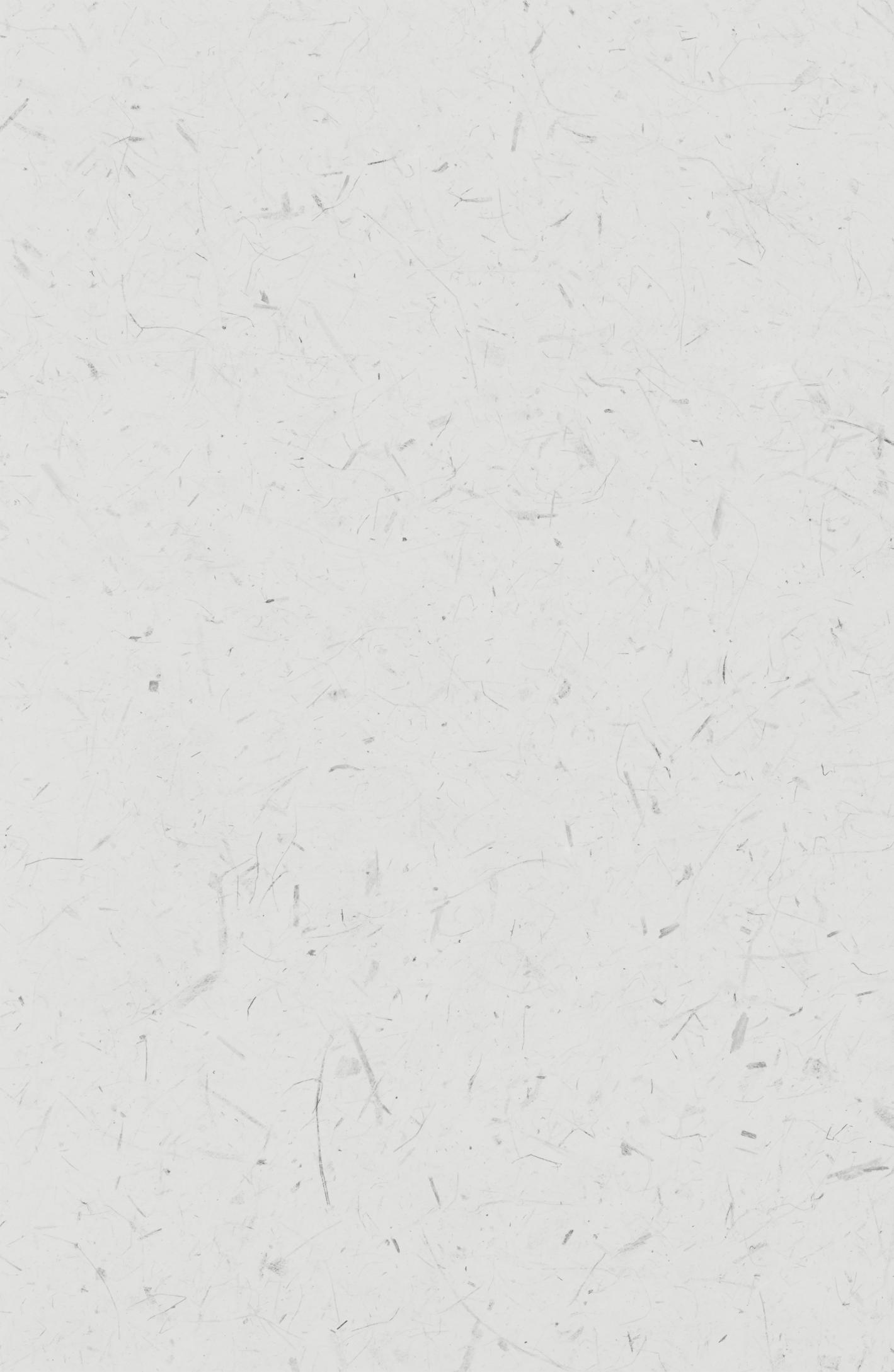
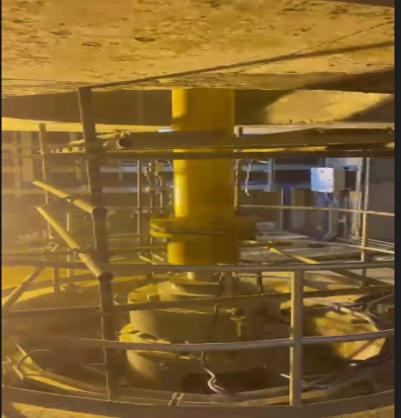
Global Order Execution
KBL supplies Horizontal Split case pump to Israel.
KBL recently executed a major order for Mekorot Water Company Limited, one of its customers in Israel. For this prestigious project, we supplied a horizontal split-case pump for drinking water supply applications. The key factor is the pumps supplied has very high efficiency going up to 93%. The heads of the pumps are 45M (24UPH3) and 55M (36UPH2I). It has a discharge of 5000m^3/hr (24UP3), and 10000m^3/hr (36UPH2I). It has been tested for a high suction pressure of 7 bars.
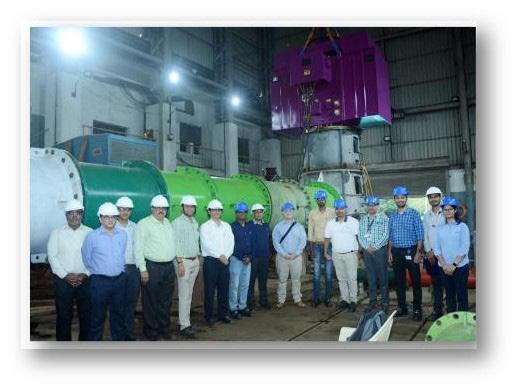
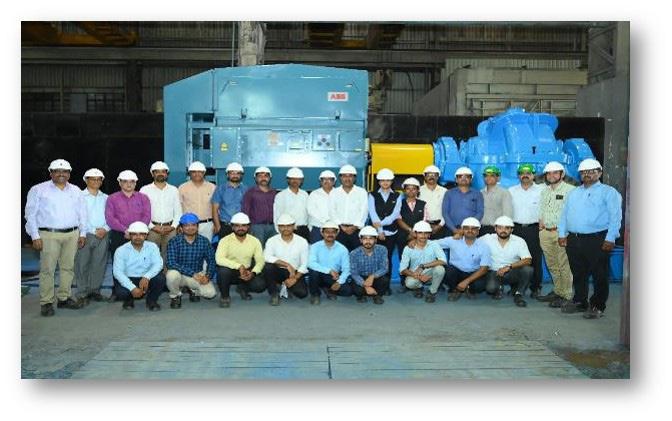
KBL supplied sea water intake pump in the Middle East
Setting another milestone, KBL completed another significant order for a customer in the Middle East. Demonstrating our advanced technology, extensive production capabilities, and dedication to providing services to the customer, the company commissioned Vertical Turbine Pump to Industrial Services SAOC Oman for Sea water intake application. The end-to-end service takes the project from concept to delivery through design, manufacturing, and testing. KBL provides the know-how, skill, and technical expertise to develop customised solutions based around customers' unique requirements. At KBL, we continue to invest in R&D that helps us innovate and improve our solutions, working closely with customers to pre-empt and meet changing market requirements.

Successful Completion of Performance Testing of 1400mm Hydraulic Operated Pump Discharge Valve
At KBL, for the first time in the Valve Business Unit, a performance testing of 1400mm Butterfly valve in horizontal position was successfully completed by a hydraulic actuator. Suitable for variety of liquids and gaseous media in water works, power plants, sewage plants, process industries, chemical and petrochemical plants for tight shut-off and control, Isolating and throttling services. Capable of manufacturing large-size valves up to 5000mm – testing, quality, and building on a long history of solutions that set the standards, our technical expertise continues to evolve and excel.
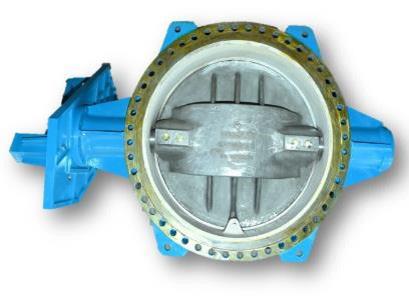
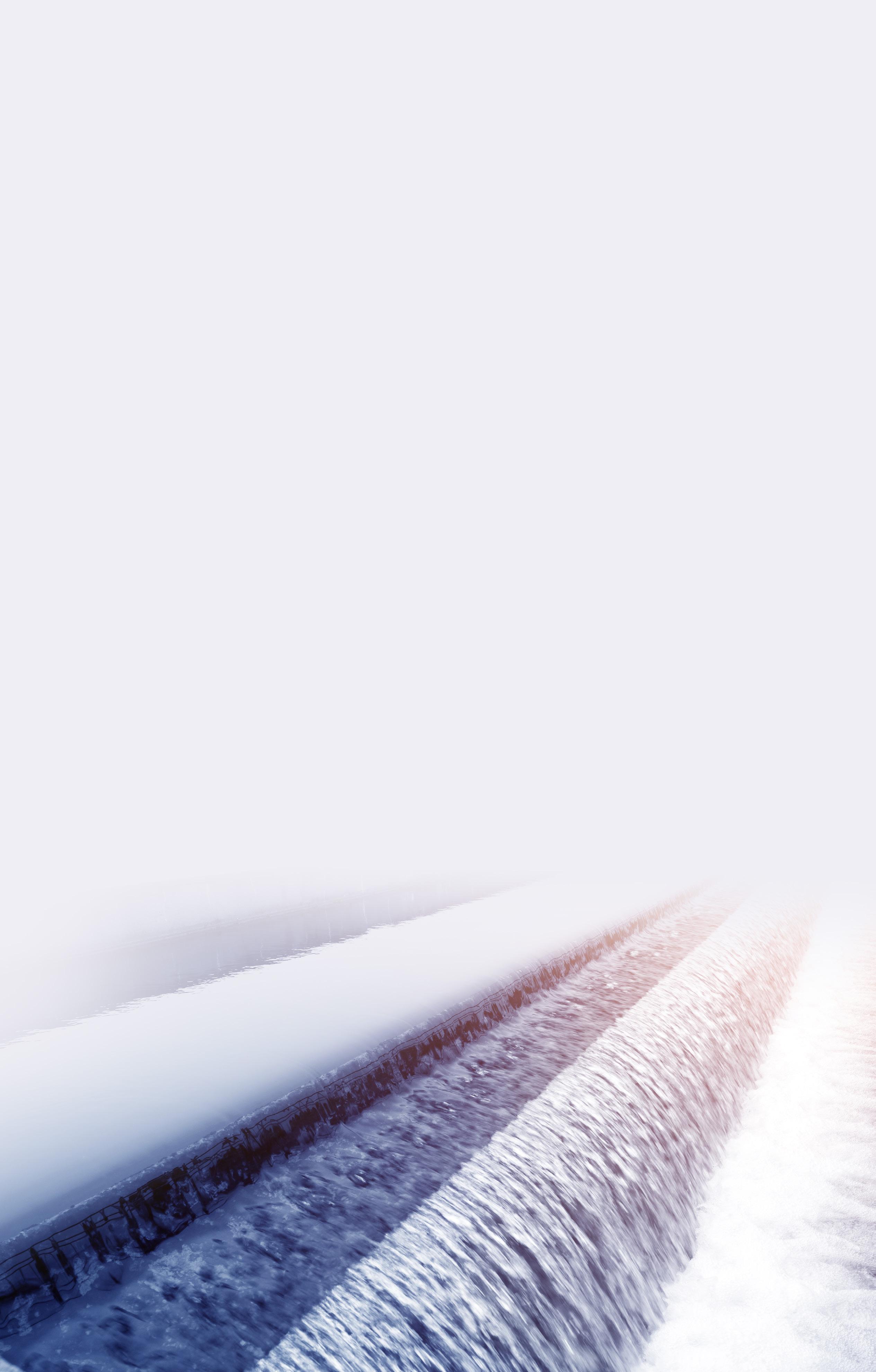
Successful Design, Testing, and Installation of Pumps with Flywheel in Vertical Orientation
Kirloskar Brothers Limited and SPP pump jointly designed 3 off Flywheel pump set for UK water company Galliford Try and Yorkshire Water. A customised engineering solution was made to overcome potential inertia (surge suppression) in the system. Additionally, the requirement was for a shear pin integrated with a flywheel of inertia of 260 Kg.m2 for surge protection and a breaking torque of 4000 Nm. The methods of using surge suppression vessels were too expensive and were putting the project at risk. SPP engineers designed a flywheel, which is the simplest and most effective solution to counter the effect of water hammer, which led the pump to gradually coast down, thus minimising large transient pressure surges (the Water Hammer Effect).
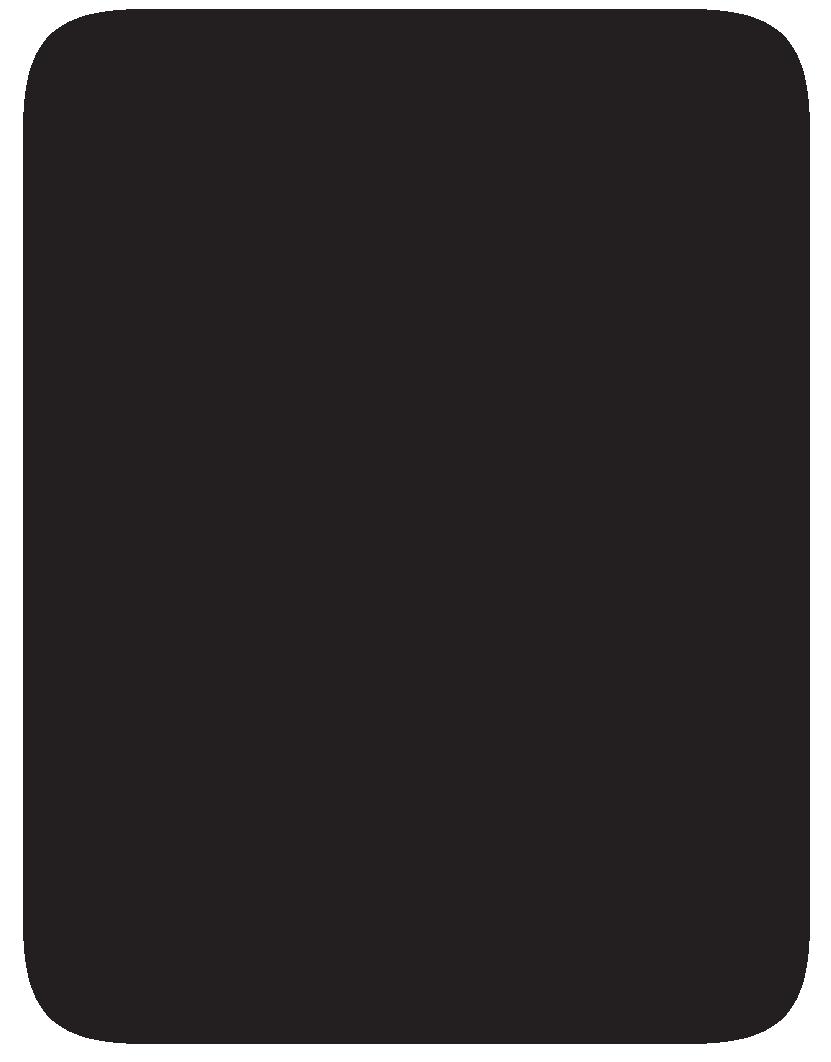
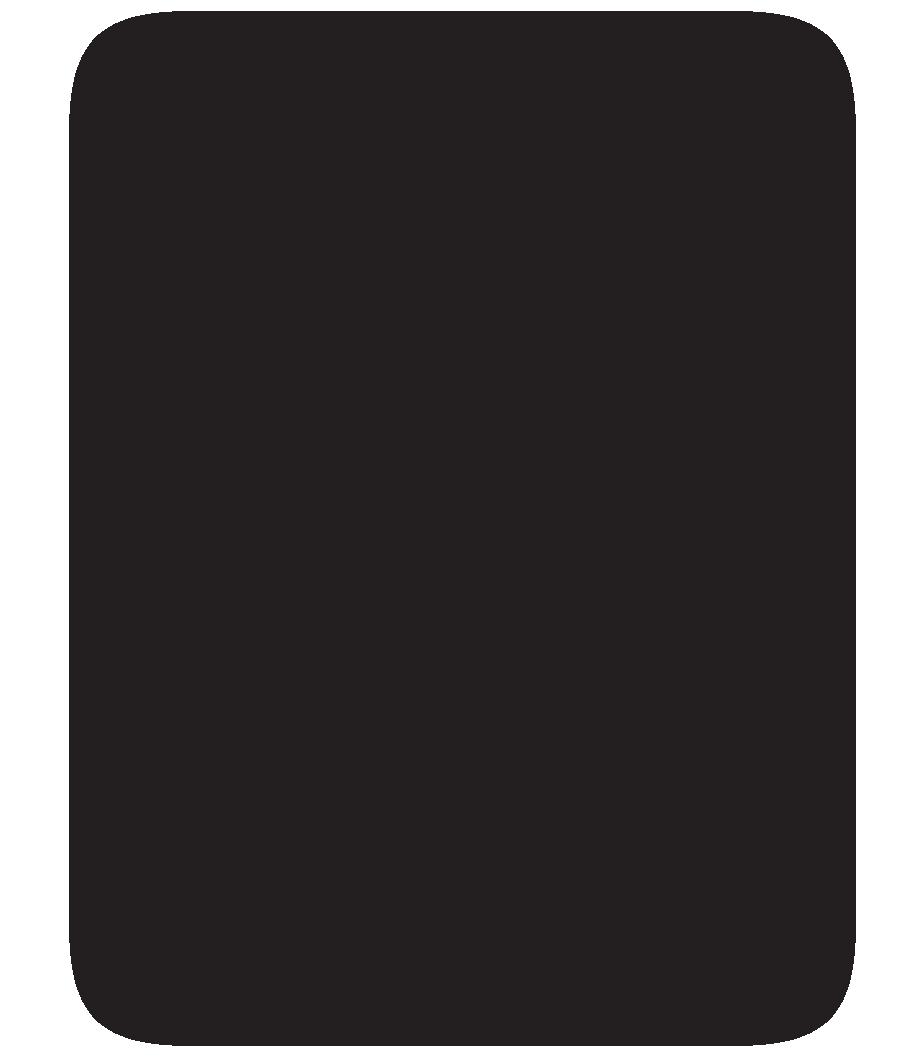
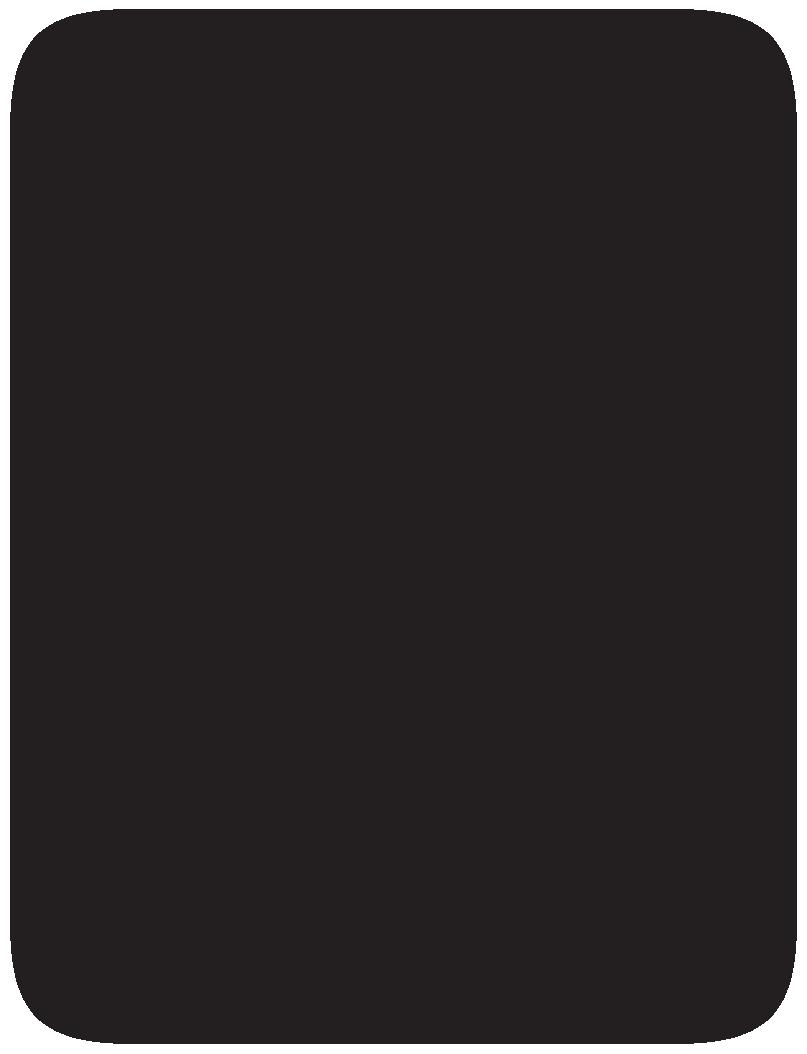
3D Prototype Engineering Design Pump after built at Factory Test Bed
Pump at Site Installation
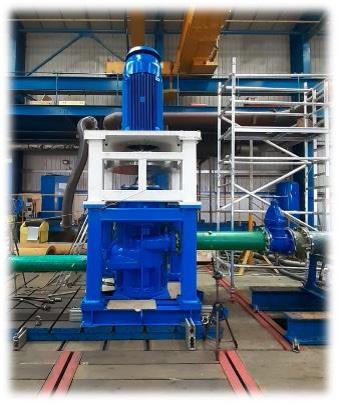
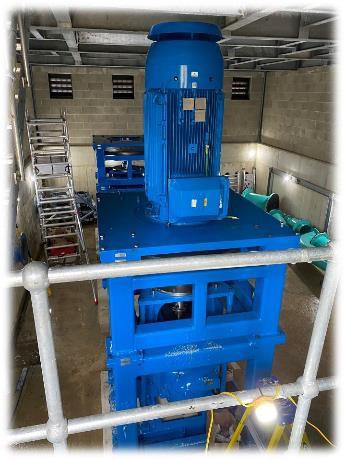
Rodelta pumps and ABB motors support the transition to low-emission biofuels.
KBL’s Dutch subsidiary and Dutch pump manufacturer, Rodelta, in collaboration with ABB, recently redesigned its close-coupled range, enabling a contract to supply pumps for one of Europe’s largest biofuel plants.
Rodelta Pumps International was selected by Shell to supply close-coupled pumps for the new Red2Green biofuel plant being constructed in Rotterdam. When planned production starts in 2024, the plant will produce 820,000 tonnes per year of sustainable aviation fuel (SAF) and renewable biodiesel, which will reduce CO2 emissions by 2.8 million tonnes every year - the equivalent of taking one million cars off the road.
Close-coupled pumps are technically very demanding. Close coupling means that the motor and pump are integrated into a single unit, with the pump impeller directly mounted on the motor shaft. The pump does not have its own bearings, and the motor’s bearings have to withstand all the forces generated. As the motor and pump are totally integrated, the motor and pump manufacturers work closely together to ensure that all tolerances are within agreed-upon specifications. Rodelta’s close-coupled pumps (OH5) are part of the company’s API range, a pump configuration defined in American Petroleum Institute standard API 610.
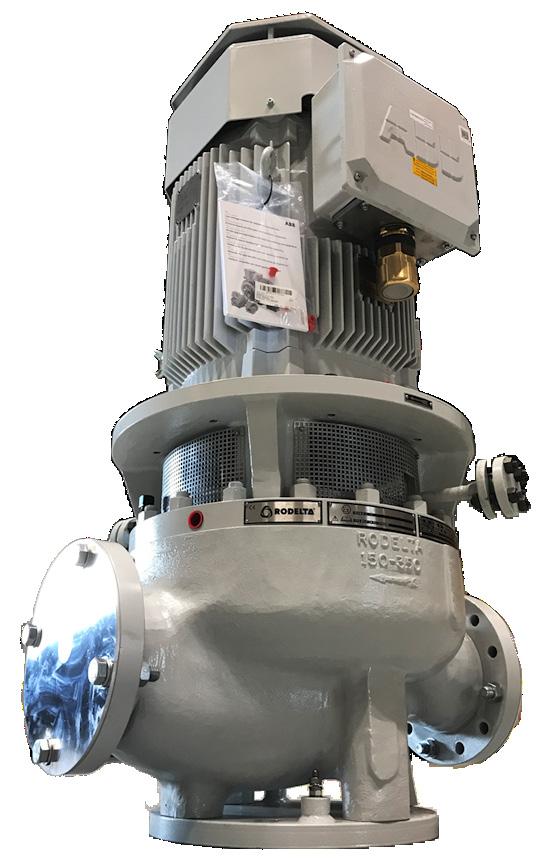
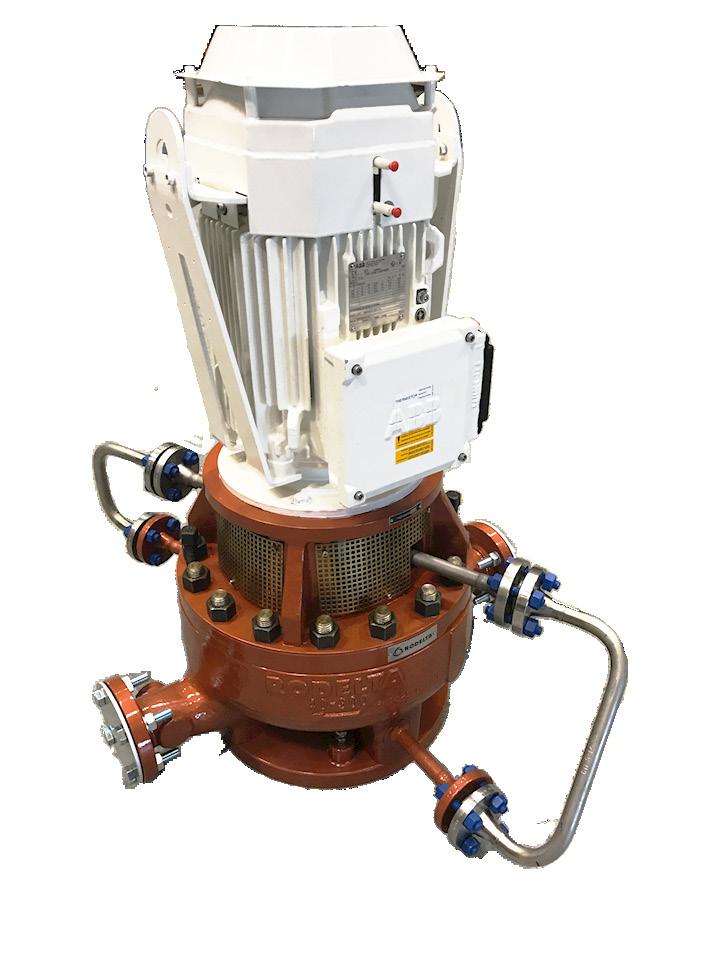

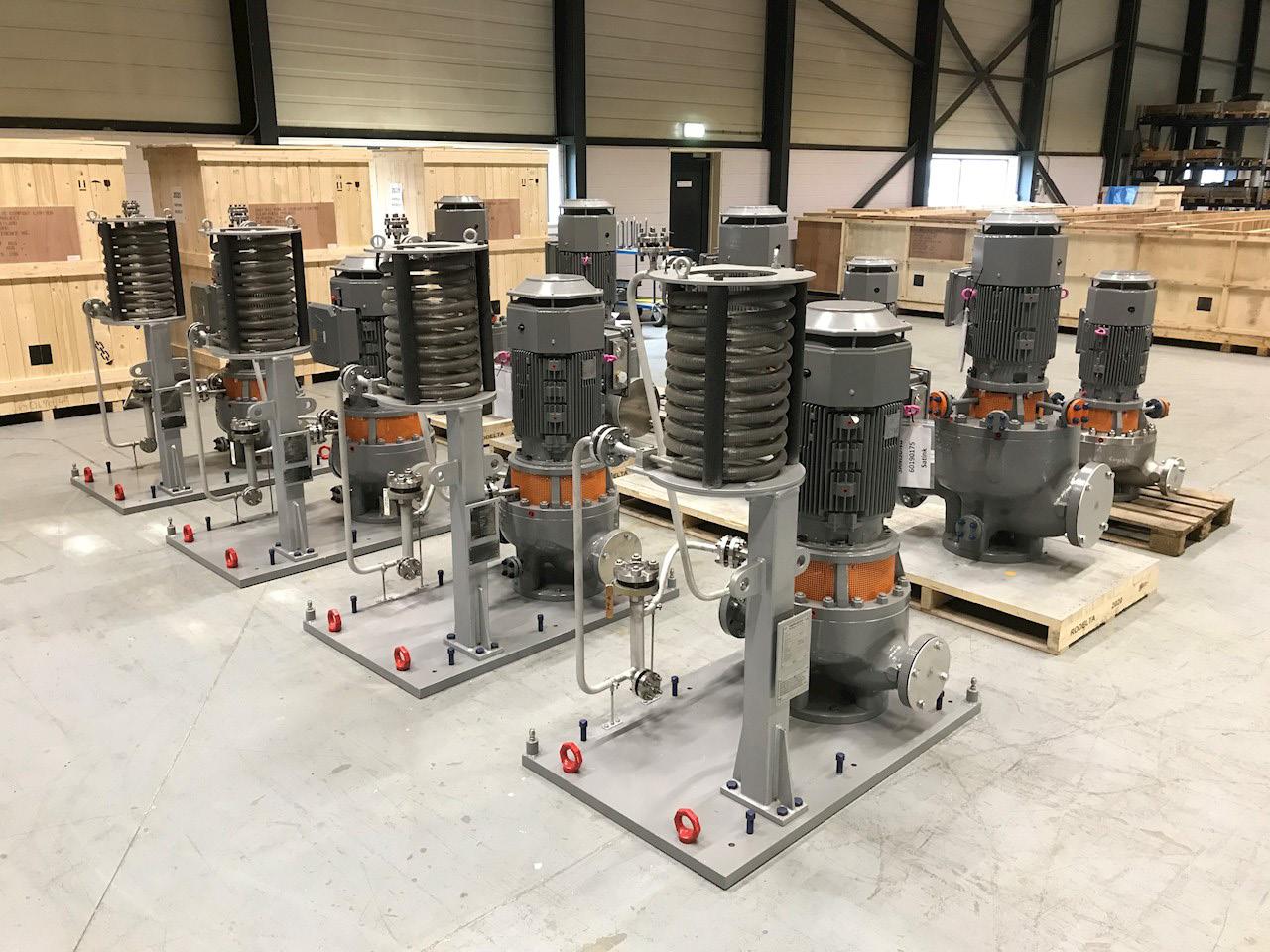
Complete hydraulic redesign
Small footprint and low maintenance
"A new edition of the API standard was released in early 2021, and this was a great opportunity for us to launch our new hydraulic redesign of OH5 pumps," says Ronald Dijkers from Rodelta. "It was a big project.
We carefully studied the new requirements and worked closely with ABB to optimise our solution. "ABB redesigned the motors according to our specifications."
Rodelta’s OH5 range previously consisted of inline pumps, but as part of the redesign, they added ‘U-turn’ versions with the suction and discharge connections on the same side. The same ABB motors are used for both versions.
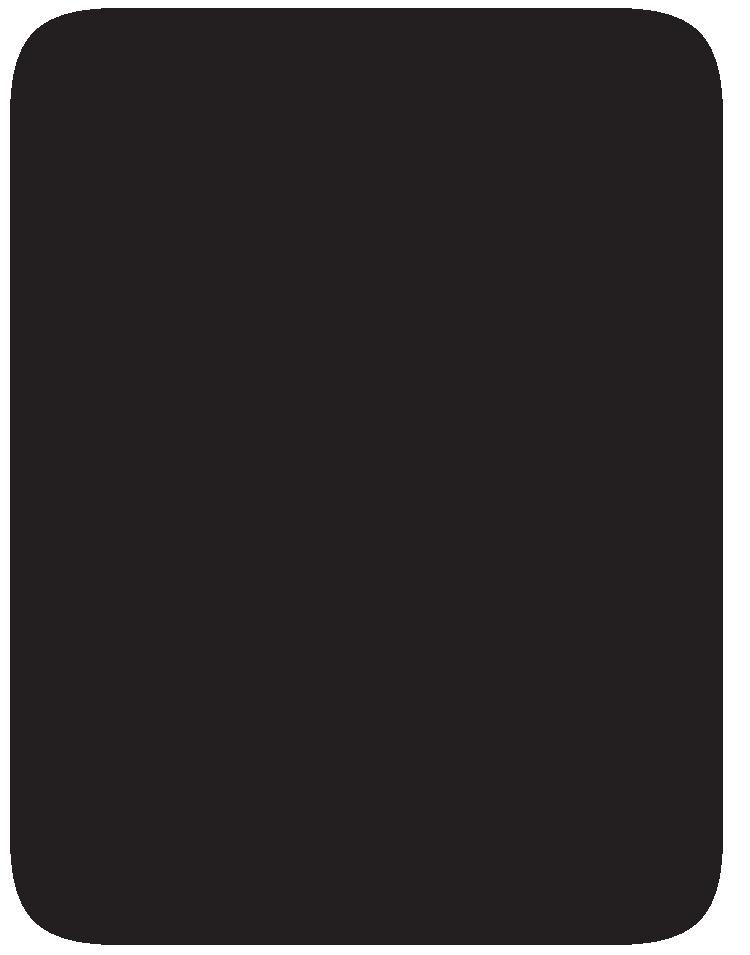

Important benefits of OH5 pumps are that they have a much smaller footprint than horizontally mounted pumps, and therefore save space. Close-coupled pumps do not have a gearbox or other coupling, which eliminates alignment issues and avoids wear problems related to mechanical components. These factors have made close-coupled pumps increasingly popular, especially in chemical, oil, and gas applications, and sales have risen rapidly in recent years.
In addition to a batch of engineered pumps for Shell’s high-profile Red2Green plant, other recent successes for Rodelta’s close-coupled pumps include seven new U-turn pumps for a second Shell project in the Netherlands, as well as 38 pumps for a project in Southeast Asia.
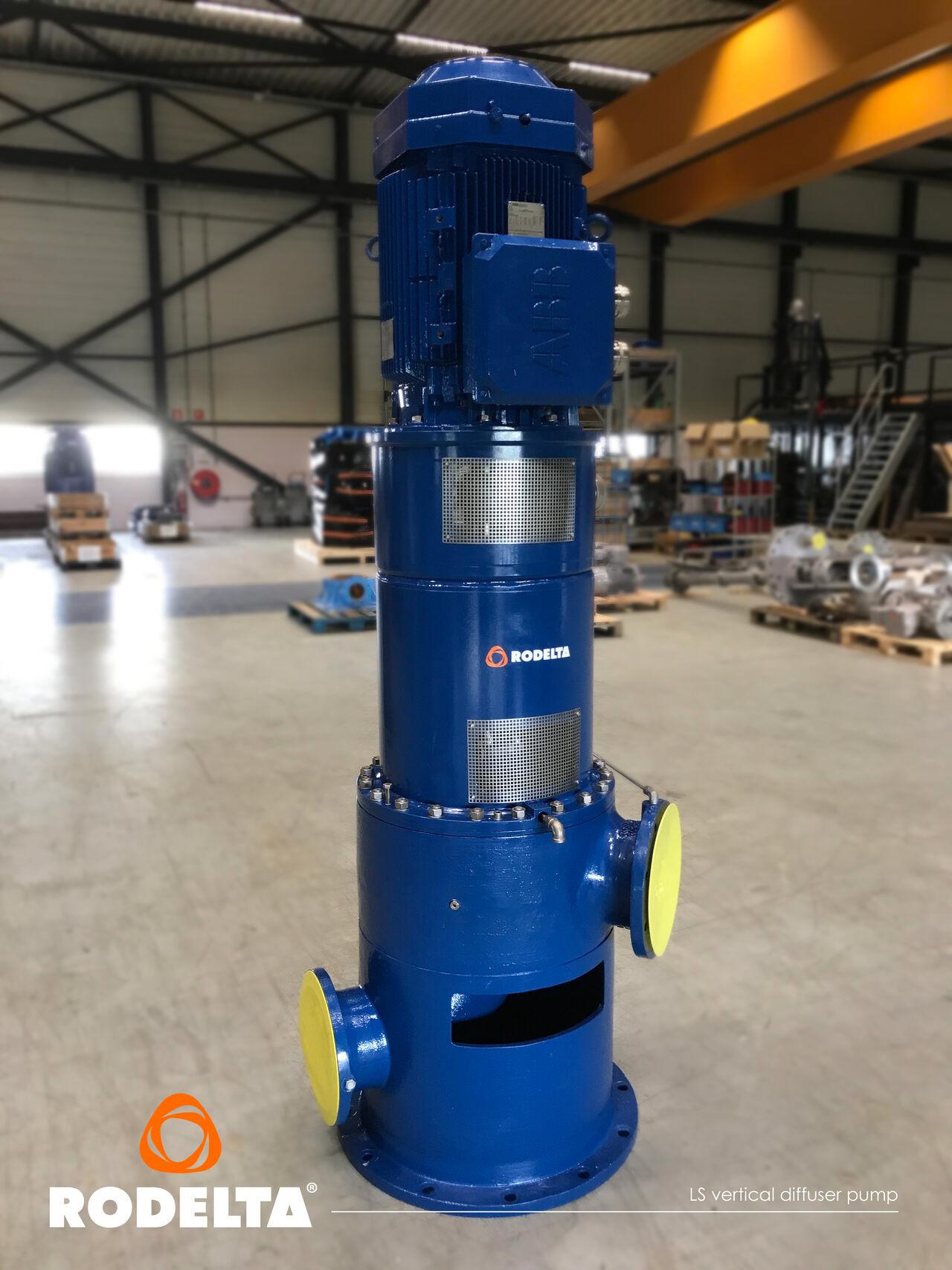