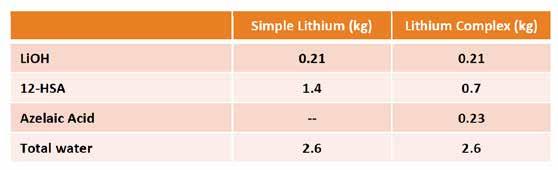
35 minute read
Back to the Basics II: Fundamental Building Blocks of Grease Formulation – The Next Chapter
Joseph P. Kaperick Afton Chemical Corporation Richmond, VA, USA
Abstract
Earlier work by the author focused on the evaluation of common additives and additive systems in a simple lithium base grease. Some routine and several less common performance tests were used to compare different types of additives and packages and look at the impact of additive combinations. The focus was on antiwear (AW), extreme pressure (EP), antioxidant (AO) and borate components along with performance packages containing different component combinations.
This study explores the different responses observed in these performance tests when using the above components in a base grease formulated with a lithium complex thickener.
Background Work
Previous work by this author investigated the performance of three types of zinc dithiophosphate, two sulfur sources, a combination of antioxidant and boron components aimed at high temperature performance and additive packages formulated to meet various performance targets. The different components were all evaluated in a simple lithium 12-hydroxy stearate grease using a variety of bench tests. The tests ranged from common bench tests included in many specifications to less common evaluations of performance aimed at differentiating characteristics of the additives employed [1].
Much work has been done to evaluate different additive components using a variety of grease bench and rig tests. Some of this work has been published on this subject. Many authors used the Four-Ball Weld test to measure the effectiveness of novel EP agents or in studies of synergies or tribochemical interactions that improve boundary lubrication protection [2-10].
Pressurized Scanning Differential Calorimetry (PDSC) was used by Reyes-Gavilan [11] to evaluate different antioxidants in polyurea- and lithium-thickened greases by a standard test method (ASTM D5483). Senthivel et al. [12] looked at PDSC as well as a variety of other techniques including spectroscopic analysis and thermal aging to investigate the high temperature behavior of greases. Samman [13] discussed relative characteristics of different components in greases and their relationship to high temperature performance, and he utilized case studies of greases in high temperature applications.
Rheological techniques have become more commonly used in evaluating the performance of high temperature greases in recent years. Nolan and Sivik [14,15] used rheology to compare the high temperature performance of a variety of different thickeners and compared those results to data obtained with a dropping point apparatus. Coe [16] looked at high temperature applications of grease formulations and examined their performance in dropping point as well as a number of other high
temperature bench tests. Kaperick [17] studied the effect of boron additives in lithium greases on performance in the dropping point test.
Rhee [18] used PDSC and a Thermal Gravimetric Analysis (TGA) procedure to build a “decomposition kinetic model” that he correlated to the high temperature wheel bearing rig test (ASTM D3527). Ward and Fish [19] also used PDSC and the D3527 wheel bearing test as a guide and evaluated several finished greases in the FAG FE8 and FE9 rig tests. Additionally, Kaperick [20] investigated tribolayer formation and the effectiveness of different additive systems in various high temperature tests including the FAG FE9 rig test.
Methods and Materials
Grease Samples The base grease used for this work was a lithium complex grease that was prepared following the same recipe as the lithium 12-hydroxy stearate greases used in the previous work [1] with the additional step of complexation using azelaic acid as shown in Table 1. This lithium complex base grease was prepared with a blend of paraffinic Group I oils with a KV@40°C of 170 cSt. The alkalinities are reported in %LiOH (not LiOH•H2O) as calculated by ASTM D128, Section 21 – Free Alkali [21]. The base grease was made in the author’s facility using a lab-scale, covered and jacketed 5-gallon kettle operated at atmospheric pressure with a single-motion, anchor-style agitator with scraper blades and fixed vertical baffle attached to the bottom of the lid cover. The heating profiles for both base greases were similar with the exception of the complexation step using azelaic acid, which added approximately 2 hours to the processing time. Heating and cooling were achieved by the circulation of heat transfer oil through the kettle’s jacket using a loop consisting of an oil reservoir, pump, heater, and heat exchanger. The kettle was connected to a second pump that circulated the contents of the kettle through a colloid mill to provide additional agitation and discharged the final product. The operation of the entire unit was computer controlled.
Table 1. Base grease description
For this study, commonly used grease tests were applied to examine the basic responses of a core slate of additives and interactions that might occur in grease formulations. All components were added to the base grease post-production, heated to 60°C for an hour and then thoroughly blended in a centrifugal mixer. These components are shown in Table 2 where some of the physical characteristics (elemental concentrations) are given along with the “IDs” used in various tables and graphs to illustrate the results of the study. Different colors are used for various components for better differentiation in graphs and figures in this paper.
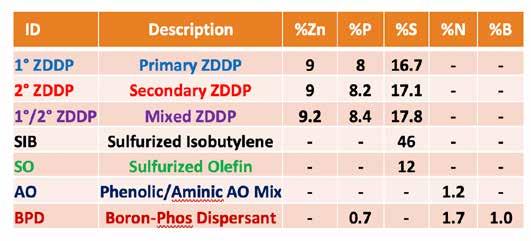
Table 2. Descriptions of components used in this study
The specific types of zinc dithiodiphosphates (ZDDPs) used in the study are shown in Table 3 along with the carbon chain lengths of the primary and secondary alcohols used to make them.

Table 3. ZDDP descriptions
Two types of sulfur compounds were used in the study – a sulfurized isobutylene with a high active sulfur content and a sulfurized olefin with a low active sulfur content. The activity of sulfur was measured using ASTM D1662 and indicated the reactivity of the sulfur componentry with copper. Details of these two components are shown in Table 4.
Table 4. Sulfur component descriptions
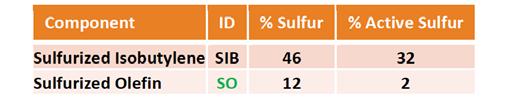
To examine the effect of high temperature componentry on grease formulations, an antioxidant (AO) mixture and a borated dispersant (BPD) were included as detailed in Table 2. These types of components are often used to provide oxidative stability to the oil component (AO) and stability to the thickener at higher temperatures (BPD).
Test Methods
The following test methods were employed with variations from standard ASTM methodology noted:
• ASTM D2265 “Standard Test Method for Dropping Point of Lubricating Grease Over Wide
Temperature Range” [22]
• ASTM D2266 “Standard Test Method for Wear Preventive Characteristics of Lubricating Grease (Four-
Ball Method)” [23].
Grease (Four-Ball Method)” [24] - This testing was carried out with the modification of using test loads at 10-kg intervals to more accurately monitor the incremental performance of the greases under extreme pressure.
Greases” [25] - According to ASTM D1743, a bearing with no rust spots larger than 1.0 mm in diameter is considered to pass, and two out of three bearings must pass for the grease to be considered acceptable. In the present study, a modified system of rating bearings from D1743 tests was employed to better estimate the impact of each variable on the level of corrosion present. The raceway on the inside of each bearing cup was rated using a visual estimate (without the use of magnification) of the percent surface area covered by rust. This rating method was described in more detail in previous work [26]. To minimize variability in this modification, the same technician did all the evaluations in this study.
Lubricating Greases Under Dynamic Wet Conditions (EMCOR Test)” [27] - Distilled water was used in this study.
• ASTM D 4048 “Standard Test Method for Detection of Copper Corrosion from Lubricating Grease” [28] - Copper strips were immersed in grease samples at the test temperature and removed after the standard 24 h period; then, the strips were rated against the ASTM standard template.
• ASTM D5483 “Standard Test Method for Oxidation Induction Time of Lubricating Greases by Pressure
Differential Scanning Calorimetry” [29] - Samples underwent the standard test method at 155°C under a 500 psi (3447 kPa) oxygen atmosphere. The extrapolated onset time was measured and reported as the oxidation induction time (OIT) for each sample. An Anton-Paar oscillatory rheometer (MCR301) was used to measure the rheological properties of the grease. The grease was compressed between a bottom plate and a parallel top plate. Both plates were 25 mm in diameter and sand-blasted. A hood that contained a temperature-controlled Peltier device was placed over the test grease and bottom plate. A temperature sweep (2°C/min) was performed on the test greases in the rheometer ranging from 40 to 250°C with a constant oscillating shear strain of 0.05%. Both storage modulus (G’) and loss modulus (G”) measurements were taken, and the ratio of the two was plotted as “Tan Delta” (G”/G’). A typical interpretation of this ratio is that as the value increases from less than one to more than one, the internal structure of the grease shifts from a more solid-like material (G’) to a more liquid-like material (G”).
Thermal Gravimetric Analysis (TGA) was completed using a PerkinElmer Pyris 1 instrument. The principle behind TGA involves the measurement of sample weight loss as a function of temperature. Grease samples were heated from 50°C to 900°C under a nitrogen atmosphere (60 ml/min) using a constant ramp of 20°C/min. The first derivative was plotted, and the rate of weight loss correlated with % weight loss as a function of temperature.
ZDDP Testing To study differences between the types of ZDDP components, six greases were formulated as shown in Table 5. Due to slight differences in elemental makeup of the different additives, a constant level of phosphorus (640 ppm P) was targeted. A “typical” treat rate of 0.6 wt% of SIB was used to assess the impact of this component on performance of the ZDDPs under various test conditions.
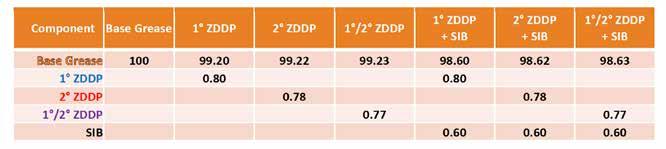
Table 5. ZDDP formulations
Corrosion testing shows some differentiation between these formulations as shown in Table 6. In all steel corrosion testing, the lithium complex base grease provided significantly better protection against rust, even without additives present. In the static rust test (ASTM D1743), the base grease alone showed no rust, so additional testing with ZDDP-containing grease was not carried out. In the more dynamic EMCOR corrosion test (ASTM D6138), the lithium complex base grease was significantly better than the simple lithium base grease with very consistent responses across three duplicate runs. For this test, the presence of ZDDP in the lithium complex base showed consistent improvement regardless of the type of ZDDP, and the presence of SIB appeared to have no impact on that response.
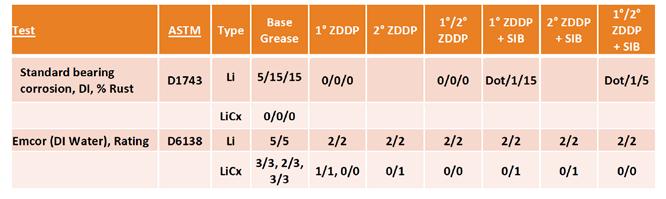
Table 6. ZDDP steel corrosion results
Copper corrosion testing also showed some differences between formulations, Table 7. Again, the lithium complex base grease showed better response than the lithium base grease; two out of three runs had 1b ratings for the lithium complex base grease. Due to this good response, it’s difficult to tell if the addition of ZDDP was helpful for the copper corrosion performance of the lithium complex base grease as was indicated for the simple lithium base. The addition of SIB did result in some improvement of copper corrosion performance across the ZDDP types, although it was difficult to distinguish between the ZDDP types. This result was similar to what was seen in the simple lithium greases but appeared to be more exaggerated in the lithium complex.

Table 7. ZDDP copper corrosion results
PDSC was used to compare the properties of ZDDP as a secondary antioxidant in both lithium and lithium complex greases. The values for the simple lithium greases were originally obtained at 155⁰C, while it was decided to use the more appropriate temperature of 180⁰C for the additional work in the lithium complex greases (see Figure 1). Therefore, the simple lithium PDSC data was converted using a common equation (Eq. 1) based on the Arrhenius relationship.
OIT(180⁰C) = OIT(155⁰C) /(2^2.5) (1)
This equation assumes that the oxidative life of a grease is reduced by half for every 10⁰C rise in temperature, with “2^2.5” being the adjustment needed with a change in temperature of 25⁰C. Under the conditions of the PDSC test, very little difference was seen between the two different thickener systems, with all the formulations containing ZDDP having a positive impact with increasing oxidation induction times (OIT). The expected relationship between the types of ZDDP was maintained with secondary ZDDP showing the best stability. The addition of SIB appeared to have more of a negative impact on the lithium complex formulation, which may correlate with the same phenomenon that we saw in copper corrosion due to interactions within the complex structure.
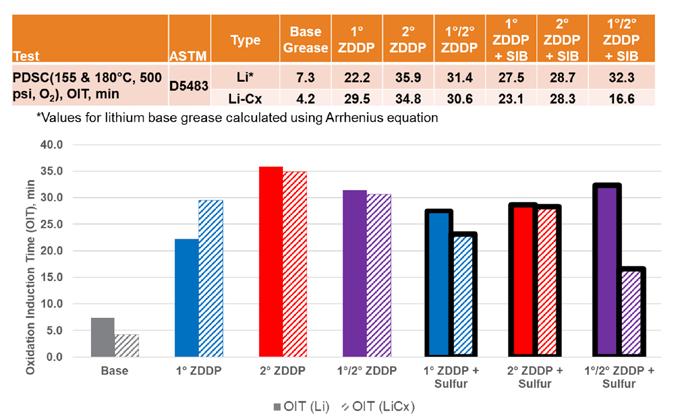
Figure 1. ZDDP oxidation (PDSC) results
To further examine the impact of ZDDP on the thermal stability of grease formulations, TGA testing was used. Since this technique is not commonly used for analysis of greases, in this study, the base grease was tested followed by duplicate runs of a fully formulated grease to evaluate repeatability. As shown in Figure 2, the base grease had two main components that were separated by their thermal stability under the conditions of the test. The majority of the grease sample (the base oil component) burned off between 200 and 430⁰C, while the thickener , which was more thermally stable, was removed between 440 and 600⁰C. The repeatability of the technique was seen with duplicate runs of a representative sample “B”.
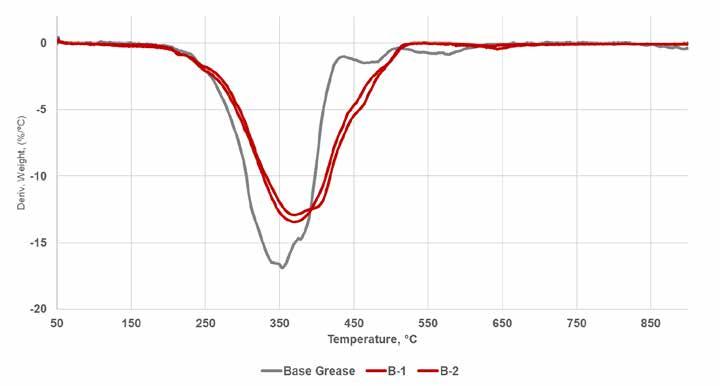
Figure 2. Base grease response and repeatability of TGA data
The differences in thermal stability between the simple and complex lithium thickeners (Figure 3) are immediately obvious and very unlike the lack of differentiation seen in the oxidative stability as measured by PDSC. It is worth noting that the TGA analysis was run in a nitrogen atmosphere and monitored weight loss as temperature was increased; therefore, TGA was more a measure of the stability of the grease structure itself, as opposed to the PDSC analysis, which was carried out under oxygen and measured the oxidative stability of the mixture. Here the lithium complex base grease demonstrated much better thermal stability than the simple lithium base grease; the bulk of the mass of the lithium complex base grease (likely the base oil) coming out at 450⁰C almost 100⁰C higher than in the simple lithium base grease. Some similar features such as small peaks seen around 370-380⁰C and at 460-470⁰C may indicate some structures common to both greases.
Figure 3. Comparison of TGA data for simple and complex lithium base greases The impact of the addition of different types of ZDDP to the lithium complex base grease stability is seen in Figure 4. In general, there is some indication of improved thermal stability in both base greases but no real differentiation between types such as was seen with oxidative stability. These improvements can be seen particularly on the right side of the peaks where the addition of ZDDP consistently increases thermal stability by 10 to 20⁰C. This effect is likely due to some additional structural stability from crosslinking between the ZDDP and soap structure, but additional study is needed to better understand how these data relate to grease structure and the impact of additives.
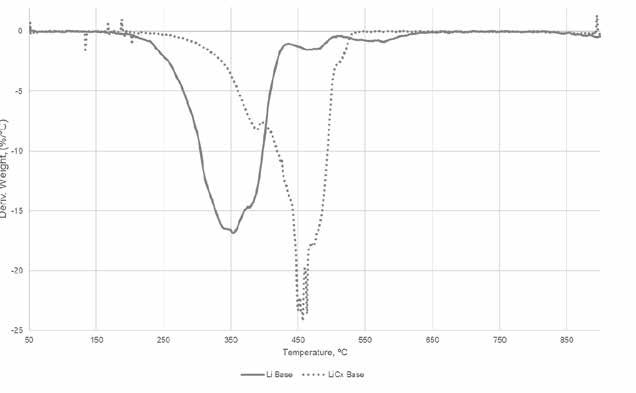
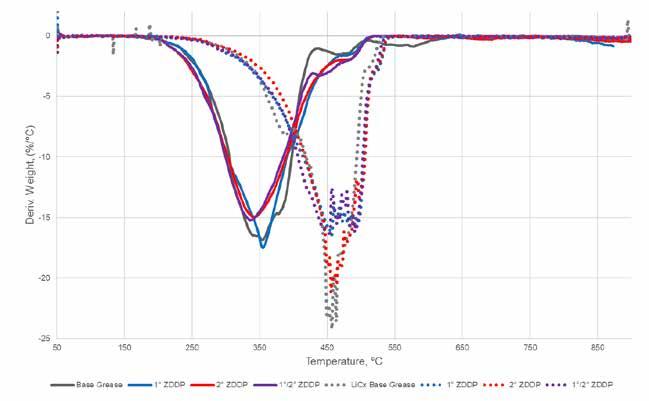
Another way to look at thermal stability of the grease structure, high temperature rheology, has been used more in recent research. By monitoring the ratio of G” and G’ while gradually raising the temperature, the impact of temperature on grease behavior can be closely observed. This ratio is typically referred to as “Tan Delta”. It characterizes the shift of the grease sample from more solid-like behavior at low Tan Delta values to more liquid-like behavior at higher values, which is commonly seen with increasing temperature. The temperature at which there is an abrupt rise in Tan Delta can be roughly correlated to the dropping point, but Tan Delta can also provide significantly more information about the high temperature performance of greases.
In the original analysis of the simple lithium base grease, as seen in Figure 5, the rise in temperature led to an initial slight “solidification” of the grease structure starting at around 60⁰C, followed by a gradual change to a more liquid-like phase from 100⁰C to approximately 190⁰C. This was followed by a sharp increase in Tan Delta that correlated roughly to the 205⁰C dropping point seen with this base grease. As the temperature continued to increase, the signal deteriorated rapidly as the oil ran out of the grease, and consistent contact between the plates was lost. The repeatability of the method was quite good as shown by the two runs overlaid on top of each other.
The lithium complex base grease showed distinct differences in this testing with markedly different response than the simple lithium grease. In the range around 200⁰C (at which temperature the simple lithium base grease lost structure), the lithium complex base grease underwent a small change in structure before it returned to its previous level of Tan Delta between 0.2 and 0.3 (see Figure 6). The response was also different in that the dropping point for the lithium complex base was 283⁰C, but there was no indication of structural loss at that temperature in the rheology scan.
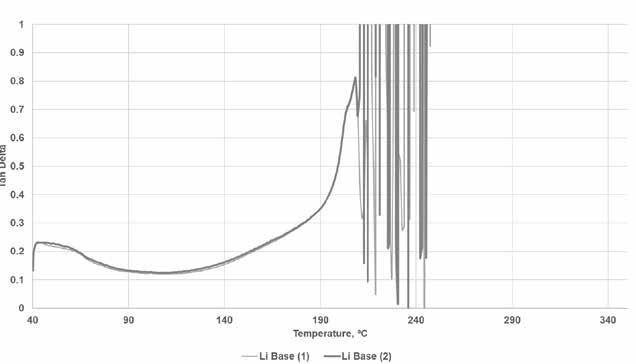
Figure 5. Base grease response in high temperature rheology
The obvious impact of ZDDP addition for both greases was to increase the structural stability as seen in Figure 7. This was more apparent in the lithium base grease at the dropping point (203⁰C), but in the lithium complex there was a more subtle “leveling” effect seen in the increase in Tan Delta between 90⁰C and 160⁰C and the reduction in Tan Delta between 200⁰C and 220⁰C. The overall impact appears to be that ZDDP helped maintain a consistent structure of the lithium complex base in a manner similar (although different in specific aspects) to that seen in the simple lithium base. And while there may be some differences between the responses of ZDDP types at medium and very high temperatures, additional work would be needed to determine their significance.
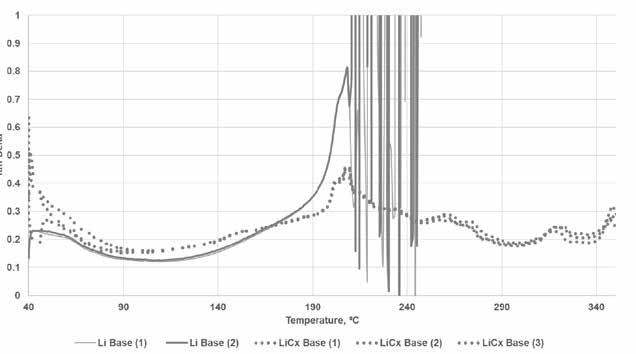
Figure 6. Comparison of base grease types (rheology)
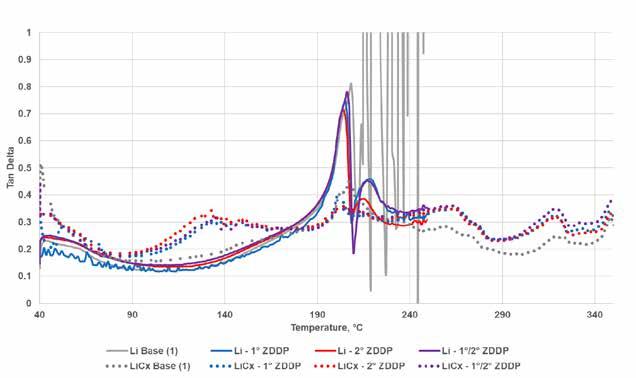
ZDDP is often used as a primary antiwear component in grease formulations, so the impact on the commonly used Four-Ball Weld and Wear tests was evaluated. As seen in Figure 8, there was a small increase in the weld load of the lithium complex base over the simple lithium, which was even greater with the addition of ZDDP. The addition of SIB, as expected, increased the weld loads even higher, but there was no indication of a variation of response between different ZDDP types. In all cases, the lithium complex base grease gave a better weld load than that seen with the simple lithium base.
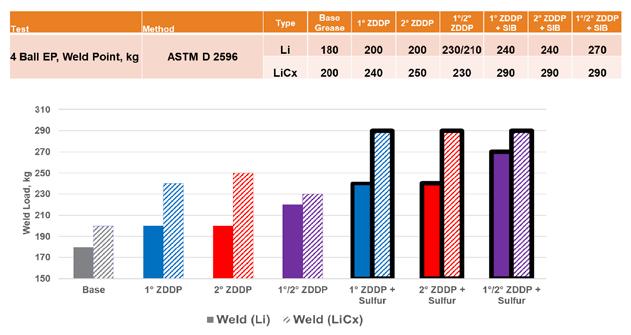
Figure 8. ZDDP extreme pressure In the evaluation of the antiwear properties using the Four-Ball Wear Test, an increase in wear protection was seen in the lithium complex base grease as well as five out of the six greases formulated with ZDDP and SIB combinations (see Figure 9). While none of the differences were statistically significant within the repeatability of ASTM D2266, the trend toward lower wear in the lithium complex base grease seems apparent. As with the weld load testing, no significant differences (or trends) were noted between different ZDDP types.
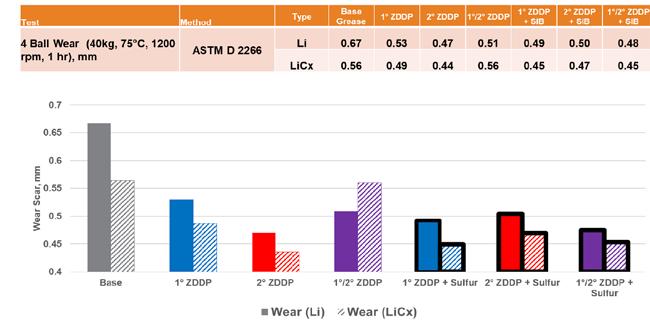
The two sulfur sources were blended into four formulations to investigate the impact of the sulfur component, alone and in the presence of the primary ZDDP (Table 8). Due to the wide disparity in sulfur content, the level of each sulfur component was calculated to target an equivalent level of sulfur (2780 ppm) in each formulation. The level of ZDDP was kept the same as in the study of the ZDDP components above.
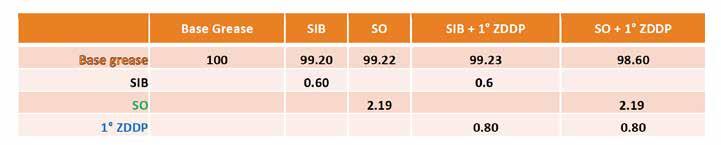
Table 8. Formulations for sulfur study
In all steel corrosion testing, the presence of the SIB surprisingly diminished the corrosion prevention properties of the lithium complex base grease (Table 9). While it was a mild impact, it was in contrast to the improvement seen with sulfurized olefin that reduced the EMCOR ratings to the same level (1/1) as the ZDDP components. This was also different from the simple lithium base, which showed only a positive impact from either sulfur source. Of interest is that the addition of ZDDP negated the impact of the SIB and brought it to the same level as the sulfurized olefin or ZDDP by itself. This contrasted with the simple lithium base grease, which showed indications of a negative impact from the interaction of sulfur and ZDDP. Further study would be needed to confirm these initial indications.
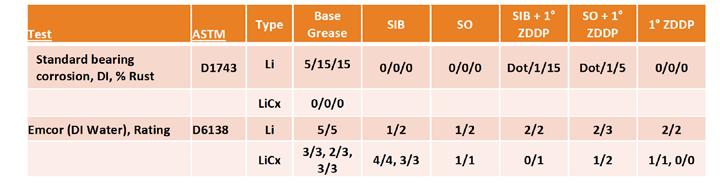
Table 9. Sulfur steel corrosion results
Variability in copper corrosion testing led to the need to repeat several observations, but the results (Table 10) seem to indicate better copper corrosion protection from the lithium complex base as compared to the simple lithium base grease. It is clear that both types of sulfur caused copper corrosion in the lithium complex grease. This was different from the performance of the sulfurized olefin in the simple lithium where no negative impact was observed. The negative results of SO in lithium complex were surprising due to its low active sulfur content and its previously shown behavior in simple lithium base. Along with other results seen in this study, this may indicate some interactions within the structure of the lithium complex grease that were not seen in the simple lithium grease. Further evidence of this might be the positive impact of the addition of ZDDP, which may interact with the sulfur to eliminate its negative effect.

Table 10. Sulfur copper corrosion results
Sulfurized olefin is used as an antioxidant in engine oils and other formulations, so it was not surprising to see that it provided oxidative stability to the simple lithium base grease. However, a similar impact was not seen in the lithium complex grease in which both sulfur types seemed to give less improvement in oxidative stability as measured by PDSC (Figure 10). The addition of ZDDP gave a boost to both sulfur types, but the overall improvement was not as great as that seen in the simple lithium base grease, and there was less differentiation between the two sulfur sources.
Since sulfur is often used primarily for extreme pressure protection, testing was done for Four-Ball Weld (Figure 11). As discussed earlier, the lithium complex base grease showed better weld loads, the addition of sulfur boosted the base grease response by about the same amount, and the difference between the sulfur types was less distinct than it was in the simple lithium grease. The addition of the ZDDP seemed to have the opposite effect by boosting the SIB-containing formulation more than the SO formulation and leading to a larger discrepancy between the two.
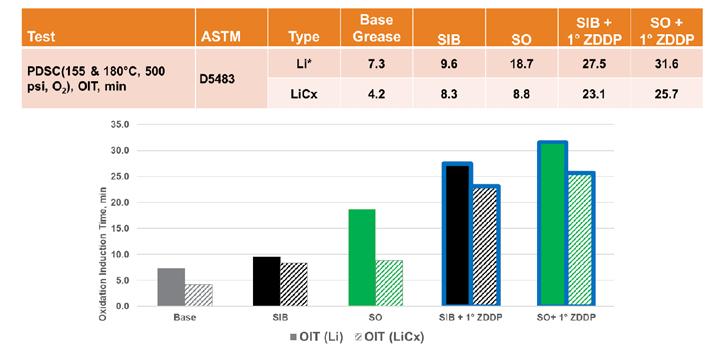
Figure 10. Sulfur oxidation results

Figure 11. Sulfur weld load results
Finally, the sulfur-containing formulations were evaluated for wear protection using Four-Ball Wear testing (Figure 12). The inherent wear reduction seen for the lithium complex base grease was even more dramatic with both sulfur types. While the addition of either sulfur source in the simple lithium grease led to very high wear levels, in the lithium complex base, they showed a reduction that if not statistically significant, at least trended in the opposite direction. The addition of ZDDP seemed to further contribute to this reduction in wear and, again, to a higher degree than in the simple lithium grease.
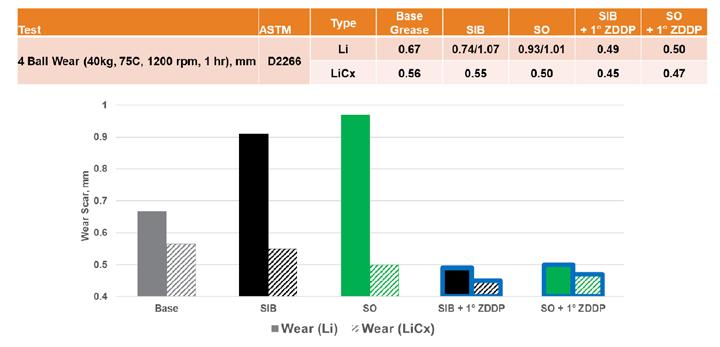
Figure 12. Sulfur wear protection results
A third category of additives was tested in the initial study because of its importance for the high temperature performance for many greases. Antioxidants are considered useful for enhancing the oxidative stability of the base oil (the major component of grease formulations) under high temperature or other conditions of thermal-oxidative stress. Borated components are also widely considered useful for improving high temperature performance due to their ability to strengthen the grease thickener structure at high temperatures as measured by dropping point. Additionally, borates are thought to work synergistically with ZDDP. For this reason, ZDDP was included with the antioxidant mixture, and borate (BPD) was added sequentially. Two levels of the borate were examined in combination with the ZDDP and the AO mixture (Table 11).
Table 11. Antioxidant/borate formulations

As expected, the lithium complex base gave a much higher dropping point than the simple lithium base grease, and the addition of AO and ZDDP had little impact on either base grease (Table 12). The addition of a lower level of the borate raised the dropping point of the complex grease, but the higher treat level appeared to disrupt the complex structure in some manner, leading to a lower dropping point than observed for the simple lithium grease with the same amount of borate. This is another example of some level of interaction between additives and the complex soap structure that would benefit from additional study.
Table 12. AO/Borate dropping point results
Minimal testing was done with copper corrosion due to the expectation that these components were unlikely to significantly affect performance. However, EMCOR corrosion testing (Table 13) gave somewhat surprising results. In the lithium base, an unexpected improvement was seen with the addition of AO and BPD, possibly due to the aminic portion of the AO componentry or the reaction of the borated species with the water, keeping it away from the steel surface. The lithium complex formulation showed the same improvement with the addition of ZDDP (as in the simple lithium base), but that impact was reduced by the addition of AO and resulted in higher EMCOR ratings in duplicate runs. Even more surprising were the ratings obtained after the addition of the BPD. The 1.5 wt% BPD treat resulted in a wide spread of results across four different duplicate runs. The 3 wt% BPD treat showed much more repeatable results that were very similar to those with only the ZDDP added. This may be further indication of interactions between structure and different componentry that has positive and negative impacts on performance in various bench tests. Further study would be needed to confirm the mechanism.

Table 13. AO/Borate steel corrosion results As expected in oxidation testing by PDSC (Figure 13), the addition of the AO mixture had an incremental benefit when used in combination with the ZDDP, which provided some oxidation stability itself. However, as seen previously with the ZDDP testing, the lithium complex greases lagged behind the simple lithium formulations. The addition of the higher treat of BPD had a significant impact on the OIT, which was not seen in the simple lithium base grease. An additional sample without ZDDP showed only an incremental benefit with this component and not a synergistic effect, such as that associated with the use of boron to raise the dropping point.
Testing by TGA showed definite evidence of increased thermal stability of the lithium complex formulations compared to simple lithium, as discussed above (Figure 14). There was evidence of slight increases in thermal stability with the addition of the BPD (especially with the pronounced peak at around 500⁰C) and the slight decrease in thermal stability seen in the formulation with no ZDDP. This is not unexpected and the lack of improvement (such as seen with the addition of the BPD to the simple lithium base) may indicate that some kind of maximum thermal stability has been reached.
High temperature rheology of these greases also highlighted the different response to high temperature by the simple lithium and lithium complex grease formulations. As seen in Figure 15, the addition of the ZDDP and AO to the simple lithium resulted in a restabilization of the signal around 230⁰C after a sharp disruption around 200⁰C (at which temperature this formulation still experienced a dropping point). However, the addition of the BPD almost completely removed that disruption, although the liquid-like nature of the sample continued to increase as the sample was heated to 300⁰C.
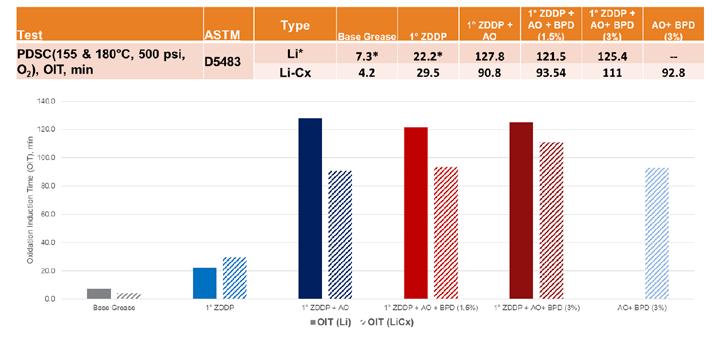
It is also worth noting that the dropping points of these samples changed significantly with the addition of the BPD as seen in Table 13. In the lithium complex base grease (Figure 16), the loss of signal disruption was previously noted and corresponded to the much higher dropping point. The addition of the ZDDP and AO showed a significant increase in liquid-like behavior of the grease between 110⁰C and 140⁰C, which was negated by the addition of the BPD and not seen without the ZDDP. At higher temperatures, there was clear evidence that the BPD added some liquid-like nature to the sample.
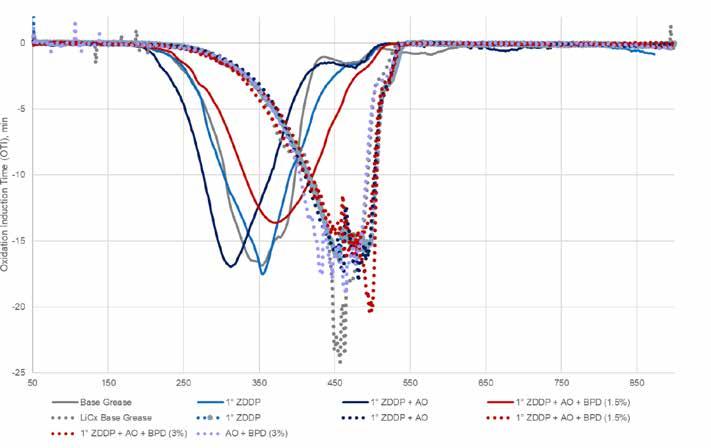
Figure 14. AO/Borate TGA results
The higher level seemed to push that liquid-like nature to a higher temperature. This may indicate some interaction between the complex thickener and the borated component. In all cases, the Tan Delta response was lower for the lithium complex greases, indicating a more thermally stable configuration, versus the simple lithium greases. Further work at these higher temperatures would be of interest as well.
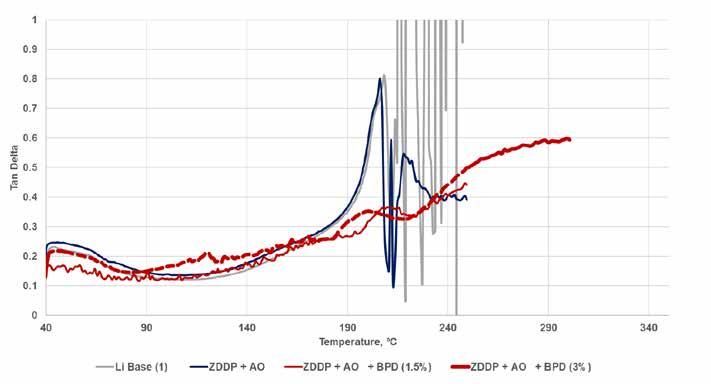
Figure 15. AO/Borate high temperature rheology results - lithium
Figure 16. AO/Borate high temperature rheology results – lithium complex
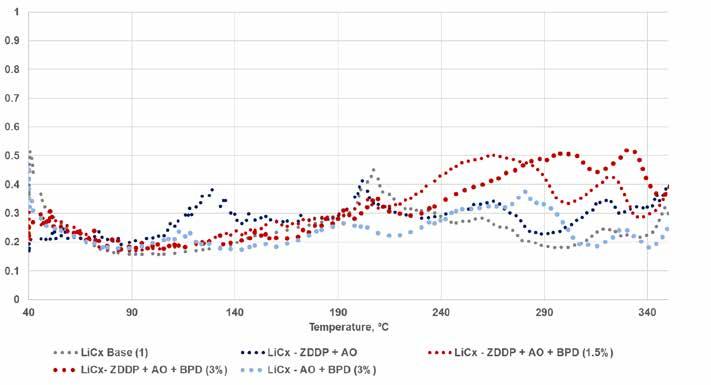
In general, the lithium complex base grease showed better performance than the simple lithium base grease in the reduction of steel corrosion, additional protection against wear and extreme pressure, and thermal stability. The thermal stability increase was seen in the dropping point, TGA data and better maintenance of structure in high temperature rheology testing. This improvement in thermal stability was not accompanied by an increase in oxidative stability, and the response in the copper corrosion tests seemed similar for both thickener systems.
ZDDP – ZDDP is typically used in grease as an antiwear agent that can also provide some benefits as a secondary antioxidant through its role as a peroxide decomposer. In this study, the ZDDP significantly boosted the performance of the lithium complex greases in the EP and AW tests; this improvement was better for the lithium complex than simple lithium greases, probably due to the performance of the unadditized base greases. In PDSC oxidation testing, the greases with the ZDDP showed good improvement over the base greases, but the lithium complex greases did not outperform the lithium greases. Protection was seen in both steel and copper corrosion tests, and evidence was also observed for stabilization of the grease thickener structure at higher temperatures in both the TGA and high temperature rheology measurements, with the lithium complex formulations showing better performance than the simple lithium formulations in all these areas. There did not seem to be any indication of different responses due to the type of ZDDP except in the case of oxidation testing, in which the order of stability was predictable: secondary>mixed>primary.
DESIGNERS & MANUFACTURERS OF PROCESS KETTLES
FOR THE PRODUCTION OF INDUSTRIAL GREASES
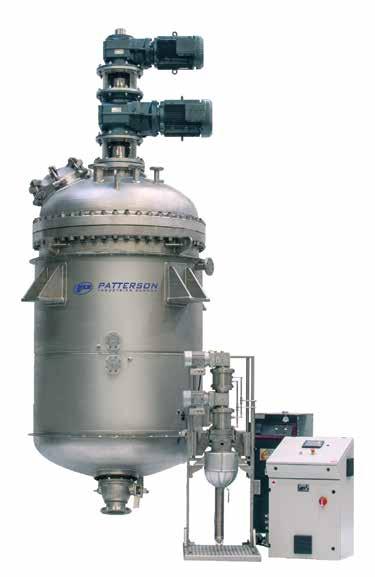
PATTERSON
INDUSTRIES CANADA "The Process Equipment People"
A Division of ALL-WELD COMPANY LIMITED • Engineers Since 1920
49 PASSMORE AVE • SCARBOROUGH (TORONTO), ONTARIO M1V 4T1 • TEL: (416) 694-3381 • FAX: (416) 691 2768 E-MAIL: process@pattersonindustries.com • WEB: www.pattersonindustries.com Sulfur – The role of sulfur
in protecting surfaces under extreme pressure was confirmed, but the normal decrease in wear protection was not seen in the lithium complex formulations. While both sulfur sources provided some additional protection against steel and copper corrosion in the simple lithium greases, in the lithium complex greases the SIB worsened both steel and copper corrosion, and the SO gave a similarly poor response in copper corrosion testing. This was unexpected due to the lower activity of the sulfur in the SO. In both cases, the ZDDP seemed to negate the poor response, possibly due to interaction with the sulfur species and/or the complex thickener itself. The sulfurized olefin also helped reduce steel corrosion by itself and provided some oxidation benefits, but not to the extent seen in the simple lithium grease. In the PDSC testing, the addition of the ZDDP again raised the performance level of both sulfur types, but differentiation between the two types was less distinct. These interactions need to be considered when formulating with both component types.
AO/Borate – While the dropping point of the lithium complex base grease was expectedly much higher than that of the simple lithium base grease, the addition of the BPD at higher levels seemed to have an effect on the complex structure as seen in a lowering of the dropping point. This may be related to the atypical behavior seen in the EMCOR corrosion testing in which the ZDDP and AO improved ratings, but a moderate treat (1.5 wt%) of the BPD resulted in wide variation in corrosion protection that might indicate some complex interactions between the BPD, lithium complex soap structure and other components present. In oxidation testing, the expected benefit of the AO was obtained along with a small additional benefit of the high treat (3
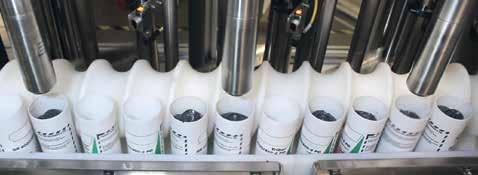
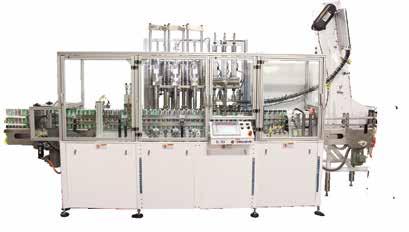
Servo Filling Systems
EST. 1985
wt%) of BPD, which was not anticipated. Finally, the benefits of the BPD, AO and ZDDP componentry in improving thermal stability were observed in both TGA and high temperature rheology testing. These benefits were in addition to the already improved stability of the lithium complex base grease compared to the lithium base grease.
Future – Additional work is needed in many areas that were examined in both of these studies of lithium-thickened greases. The high temperature work with TGA and rheology continued to show interesting differences that can be linked to additive componentry, but this area needs further study to correlate these findings to bearing response at high temperatures. Finally, it would be of interest to look further at some of the unexpected results that might indicate more complex interactions between thickener structure and additive components in several performance areas.
FORMULATING A HIGH PERFORMANCE SYNTHETIC GREASE?
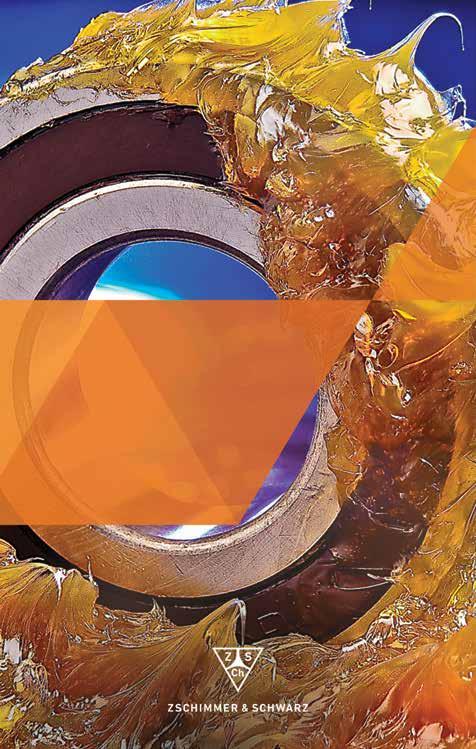
Z&S offers over 150 Synthetic Esters, optimized for Industrial, Automotive, Aviation and Marine applications.
Discover more: ZSLubes.com
Chemistry tailor-made
References
[1] Kaperick, J: “Back to the Basics - The ABC’s of Grease Additive Performance,” NLGI Spokesman, 84 (2020) 2, 27-53. [2] Scott, William P., “Extreme Pressure Lubricants,” U.S. Patent 3,133,020, (1964). [3] Collins, Albert V., “Lubricant Compositions Containing Zirconyl Soaps,” U.S. Patent 4,171,268, (1979). [4] Mobil Research, “Gear Lube Test predicts performance,” Engineering, 212, p. 1085, (Nov. 1972). [5] Fang, X.; Liu, W.; Qiao, Y.; Xue, Q. and Dang, H., “Industrial gear oil – a study of the interaction of antiwear and extreme-pressure additives,” Tribology International, 26, pp. 395-8, (1993). [6] Kubo, K.; Shimakawa, Y. and Kibukawa, M., “Study on the Load Carrying Mechanism of Sulphur-Phosphorus Type Lubricants,” Proceedings of the JSLE International Tribology Conference, 3, pp. 661-6, (1985). [7] Feher, J.J. and Malone, B.W., “The evolution of EP additives for greases and industrial gear lubricants,” NLGI Spokesman, 52, pp. 553-8, (1989).
[8] Hein, Richard W., “Evaluation of Bismuth Naphthenate as an EP Additive,” Journal of the Society of Tribologists and Lubrication Engineers, pp. 45-51, (November, 2000). [9] Ward, William C. and Najman, Morey, “Properties of Tribochemical Films from Various Additives in Grease Generated under Load,” Presented at the 72nd Annual Meeting of the NLGI, at San Antonio, Texas, (2005). [10] Fu, X.; Shao, H.; Ren, T.; Liu, W. and Xue, Q., “Tribological characteristics of di(iso-butyl) polysulfide as extreme pressure additive in some mineral base oils,” Industrial Lubrication and Tribology, 58, pp. 145-150, (2006). [11] Reyes-Gavilan, J.; Hamblin, P.C.; Laemlin, S.; Rohrbach, P.; Zschech, D.: “Evaluation of the Thermo-Oxidative Characteristics of Greases by Pressurized Differential Scanning Calorimetry,” NLGI 70th Annual Meeting, October 2003, Hilton Head, South Carolina, USA. [12] Senthivel P; Joseph, M.; Nagar S.C.; Kumar, A.; Naithani, K. P.; Mehta, A. K.; Raje, N.R.: “An Investigations Into the Thermal Behaviour of Lubricating Greases by Diverse Techniques,” NLGI 71st Annual Meeting, October 31 – November 2, 2004, Dana Point, California, USA. [13] Samman, N.: “High Temperature Greases,” NLGI Spokesman, 70 (2007) 11, pp. 1423. [14] Nolan, S.J; Sivik, M.R.: “The use of controlled stress rheology to study the high temperature structural properties of lubricating greases,” NLGI Spokesman, 69 (2005) 4, 14-23. [15] Nolan, S.J; Sivik, M.R.: “Studies on the High-Temperature Rheology of Lithium Complex Greases,” NLGI 74th Annual Meeting, June 10-12, 2007, Phoenix, Arizona, USA. [16] Coe, C: “Shouldn’t Grease Upper Operating Temperature Claims Have a Technical Basis?” NLGI Spokesman, 72 (2009) 10, 20-28. [17] Kaperick, J; Aguilar, G; Garelick, K; Miller, A; Lennon, M; Edwards, M: “Complex Issue of Dropping Point Enhancement in Grease,” NLGI Spokesman, 81 (2017) 5, 36-47. [18] Rhee, I: “Prediction of High Temperature Grease Life Using a Decomposition Kinetic Model,” NLGI Spokesman, 74 (2010) 2, 28-35. [19] Ward, W. Jr.; Fish, G.: “Development of Greases with Extended Grease and Bearing Life Using Pressure Differential Scanning Calorimetry and Wheel Bearing Life Testing,” NLGI 76th Annual Meeting, June 13-16, 2009, Tucson, Arizona, USA. [20] Kaperick, J.: “If You Can’t Stand the Heat...The Effects of Temperature on Grease Additive Performance,” NLGI 78th Annual Meeting, June 11-14, 2011, Desert Springs, CA, USA. [21] ASTM D128 “Standard Test Methods for Analysis of Lubricating Grease”, Section 21 – Free Alkalinity, ASTM International, West Conshohocken, PA. [22] ASTM D2265-15e1 “Standard Test Method for Dropping Point of Lubricating Grease Over Wide Temperature Range”, (2015) ASTM International, West Conshohocken, PA. [23] ASTM D2266-01(2015) “Standard Test Method for Wear Preventive Characteristics of Lubricating Grease (FourBall Method)”, (2015) ASTM International, West Conshohocken, PA. [24] ASTM D2596-15 “Standard Test Method for Measurement of Extreme-Pressure Properties of Lubricating Grease (FourBall Method)”, (2015) ASTM International, West Conshohocken, PA. [25] ASTM D1743-13(2018) “Standard Test Method for Determining Corrosion Preventive Properties of Lubricating Greases”, (2018) ASTM International, West Conshohocken, PA. [26] Kaperick, J.P., Rust for the Record: Significant Factors Affecting Corrosion Protection in Grease, NLGI Spokesman, 82 (2018) 3, 34-45. [27] ASTM D6138-18 “Standard Test Method for Determination of Corrosion-Preventive Properties of Lubricating Greases Under Dynamic Wet Conditions (EMCOR Test)” (2018)ASTM International, West Conshohocken, PA. [28] ASTM D4048-16e1 “Standard Test Method for Detection of Copper Corrosion from Lubricating Grease”, (2016) ASTM International, West Conshohocken, PA. [29] ASTM D5483-05(2015) “Standard Test Method for Oxidation Induction Time of Lubricating Greases by Pressure Differential Scanning Calorimetry”, (2015) ASTM International, West Conshohocken, PA.
Acknowledgements
Many thanks for valuable work carried out by the following colleagues at Afton Chemical Corporation:
Mike Lennon, Brandi Ford, Mike Jennings, Cody Walker, Zach Adams, Anna Wright, Karen Hux and Dirk Burmeister.
This paper was presented as #2020-08 at the NLGI 87th Annual Meeting, held virtually on August 27, 2020.
Learn From Experts. Build Your Network. See the Possibilities.


Reliable Plant is Back in 2021
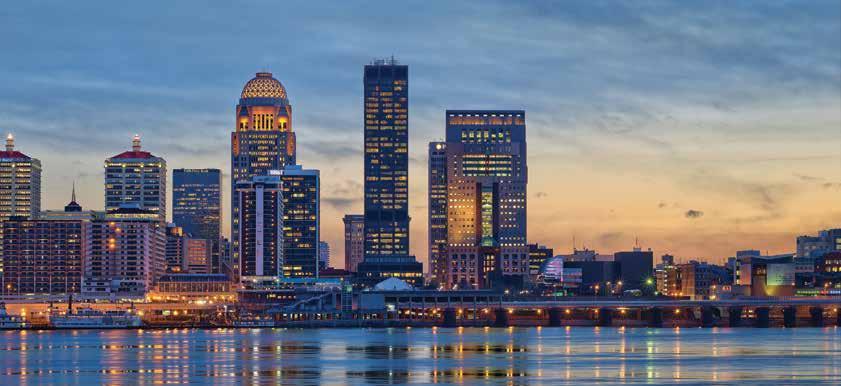
Reliable Plant is back in October 2021 with more unique opportunities to learn from world-class reliability leaders, lubrication experts and many other subject matter experts in the industry. For more than 20 years, the Reliable Plant Conference & Exhibition has been the only place where the optimal mix of technical excellence, cutting-edge technologies and proven solutions for the maintenance and reliability industry come together to share insights.
See the Possibilities
The true value of Reliable Plant is not only the world class learning, it’s the conversations that happen after class, around the lunch table or in the exhibit hall that can create that “light bulb moment.” When a mix of everyone from operators to upper-management attends Reliable Plant, new possibilities open up for reliability and maintenance teams. Ready for a more reliable plant? Join the reliability leaders gathering in Louisville, Kentucky on October 19 – 21 at Reliable Plant 2021.
About the Conference
Spanning four days, Reliable Plant 2021 includes workshops, learning sessions and case studies designed to upgrade the skills and knowledge of attendees. The conference will also feature approximately 130 exhibitors in a more than 200,000-square-foot exhibit hall inside the Kentucky International Convention Center. For more information visit Conference.ReliablePlant.com.
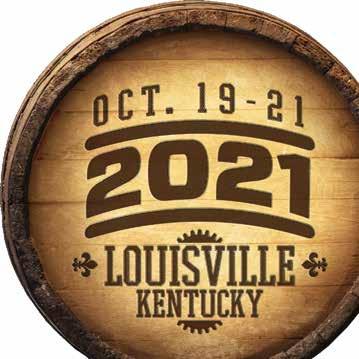
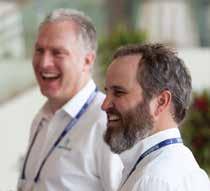
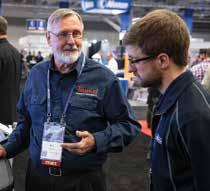
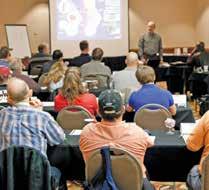