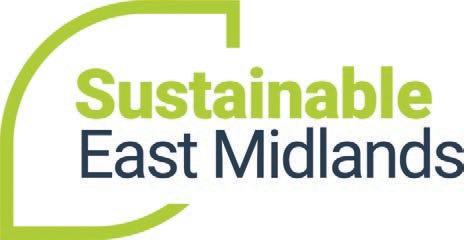
7 minute read
Building back greener in construction
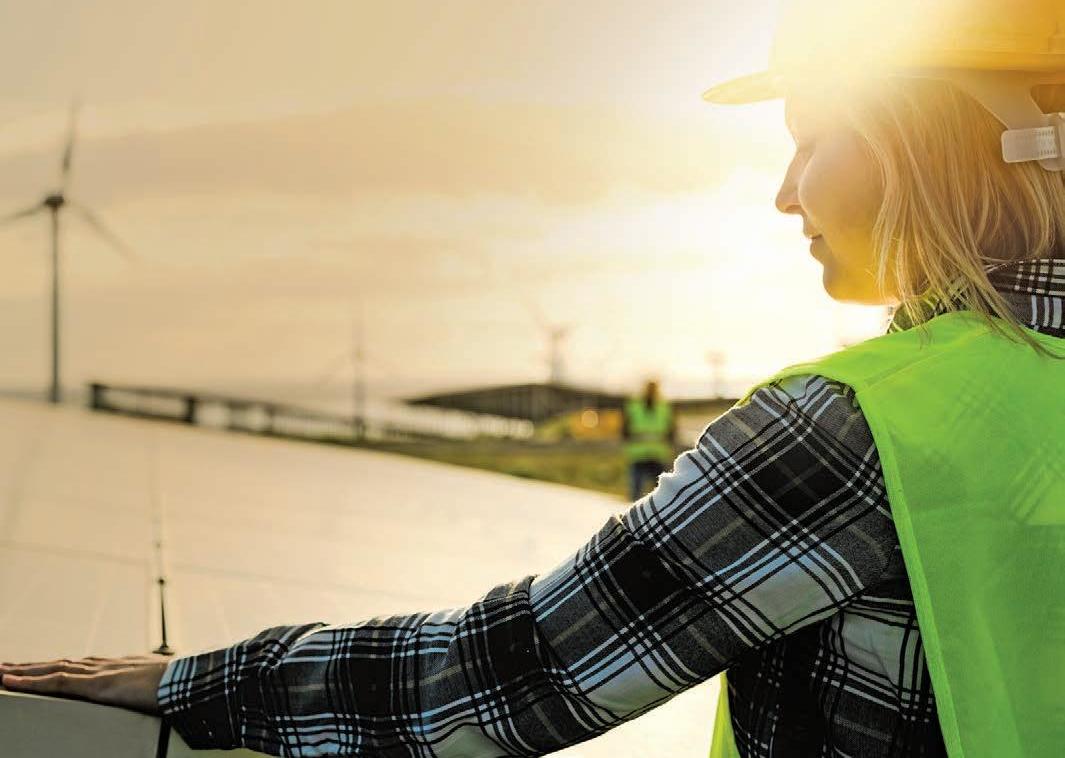
www.emc-dnl.co.uk/sustainability
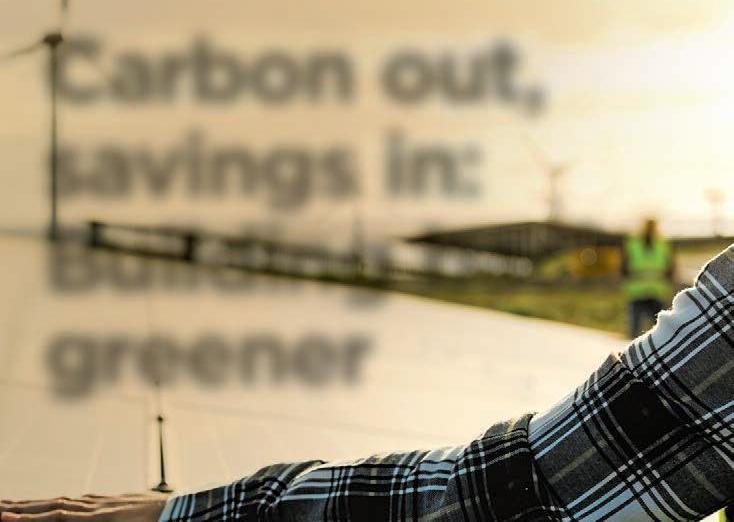
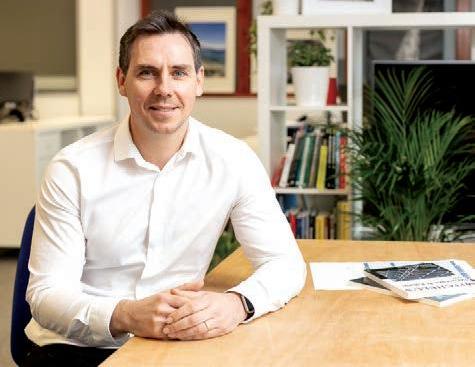
Net zero carbon definition needs agreement
The lack of an agreed net zero carbon (NZC) definition could be hampering the built environment’s decarbonisation efforts, believe sustainability experts at a Nottingham-based construction consultancy.
While the UK Government has a goal to achieve this by 2050 and three-quarters of councils are now taking action, Focus Consultants claims the net zero carbon description does not include imports.
In contrast, the UK Green Building Council (UKBGC) has a policy that expects the entire supply chain emissions to be net zero for the NZC definition to be achieved.
Jason Redfearn (pictured), managing partner at Focus, who heads up the firm’s sustainability services, said: “This raises the question of whether a building that achieves NZC adhering to the UK Government’s definition and excludes emissions associated with imported products can be seen as NZC in line with the UKBGC.
“Public bodies such as local authorities are typically aligning their definition of NZC with the central Government’s – so should those bodies wish to construct a NZC building, which definition should be used? It is unclear if such questions are being tackled.”
He said the UKGBC’s definition only addresses selected life cycle stages of a building, excluding emissions associated with replacement, refurbishment and end of life – meaning calculated whole life emissions are artificially low.
Further confusion is added by the World Green Building Council adopting two additional definitions of NZC accounting separately for operational emissions and whole-life emissions.
“The uncertainty created by so many definitions of NZC could be an obstruction to the decarbonisation in the built environment,” Jason added.
Carbon out, savings in: Building back greener
The Government wants construction to be one of the main engines behind its “building back greener” mantra but with the industry’s emissions hitting a record high in 2019, it faces a significant challenge to become more sustainable. Mark Deakin (pictured), regional strategic director for the Midlands at multinational real estate and infrastructure consultancy Turner & Townsend, explains how to crack the code of sustainable construction.
ECONOMIC OUTLOOK
The construction industry contracted by 12.5% during 2020, the sharpest drop in output since the record fall recorded in 2009 caused by the global financial crisis.
This was markedly worse than the -9.9% retrenchment across the UK economy as a whole and represented the sharpest decline of all the key industrial sectors.
By any measure, 2020 was a torrid, rollercoaster year for UK construction – but it ended on a comparatively high note.
UK GDP grew by 1.0% in Q4 2020, successfully scotching talk of a “double dip” recession. The construction industry contributed well to that growth, increasing output by 4.6% across the final three months of 2020.
THE CASE FOR BUILDING GREENER
As the economy unlocks and the Government’s generous support package for struggling firms is withdrawn, insolvency risks will emerge. Coupled with historic capacity constraints and skills shortages, inflation is likely to increase steadily across our forecast horizon.
One key driver influencing future pricing will be the increased demand and supply capacity for sustainable products as part of the Government’s green recovery and acceleration to net zero.
Although large-scale options for cost-neutral net zero retrofit schemes can be expected by the end of 2023, the dynamics of new-build properties bring a different set of challenges.
However, if the Midlands unleashed its significant regional capabilities of cutting-edge research, technology, academic leadership and business innovation, it could help drive change in the industry.
The University of Nottingham’s Research Acceleration and Demonstration (RAD) building is one of the most energy-efficient research facilities in the UK and a great example of how we can successfully build greener.
MAKING CHANGE A REALITY
Designing and implementing a truly net zero real estate strategy requires more than just warm words. Goals must be explicit and baked into the process, and while technology and data-led decision-making are important enablers, a successful shift to net zero demands permanent behavioural change too. There are five key steps to making that change a reality: • Clarity and alignment: Businesses must be clear with their supply chain about their corporate net zero vision, ensuring everyone understands what needs to be achieved and the route to achieve it. • Procuring with purpose: You can only manage what you can measure. Firms must embed agreed technology standards into their contracting and procurement strategy, to ensure all stakeholders work to common parameters. • Joined-up value engineering: Value engineering is a crucial part of cost management, right across the asset life cycle.
Rather than being taken in isolation, decisions must factor in the impact on totex, solution interoperability and whole-life carbon, as well as the environmental performance of the asset. • Getting more from the legacy estate: Asset owners must gather granular data on current progress in reducing energy use, decreasing embodied carbon and increasing renewable energy supply. IoT sensor technology offers the best way to amass huge amounts of operational data, but it must be visualised in a way that everyone can understand and act upon. • All for zero, and zero for all: In buildings with multiple tenants, or where use changes over time, net zero operational targets can slip.
Ongoing success requires owners to monitor the right data, reward the right behaviours and foster collaborative relationships with occupiers.
The logistics of sustainability trends
As logistics and distribution witness skyrocketing demand, sustainability has come to the forefront for businesses operating in those industries. Amy Deakin, channel partnership manager at Western Union Business Solutions, explains how decision-makers can deliver to these fulfilment and distribution needs while maintaining their environmental credentials.
Amy Deakin
In the five years following 2020-21, research firm IBISWorld predicted the UK’s warehousing and storage sector revenue to grow at a compound annual rate of 3.6% to £21.4bn.
Many believe this growth has been fuelled by the upsurge in online shopping, particularly for fast-moving consumer goods. Additionally, the uncertainty around Brexit and the pandemic have caused some sectors, particularly manufacturing and pharmaceuticals, to stockpile goods, driving further demand for storage and distribution.
Therefore, increased needs for distribution space, as well as shortened processing, packaging and turnaround times mean that businesses must prepare for the continued growth that lies ahead. But how can they do so sustainably?
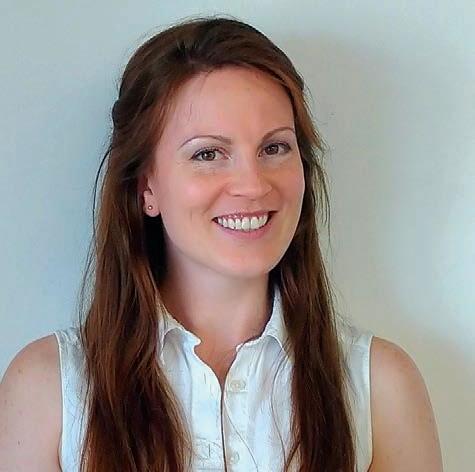
AUTOMATION
As the pandemic continues, adjustments are required to maintain a sustainable and safe work environment, as well as support employees’ health. One way to achieve this is through technology and automation.
Many businesses have started to turn towards automation with equipment such as automated forklifts, electric vehicles that enable employees to move trailers, load docks, and transport pallets and containers in and out of storage units.
Not only do these devices help support increasing needs in the logistics industry, but they do so in a sustainable way through fewer emissions, reduced maintenance, lower operating costs and reliable, clean power.
OPTIMAL FACILITY FUNCTIONS
Even the smallest of initiatives – such as converting to LED lighting, maintaining a wellinsulated building, or setting timers and sensors to reduce electricity, water or gas usage – can increase a company’s sustainability.
According to the Leadership in Energy and Environmental Design (LEED), “LEED-certified buildings use 25% less energy, have 34% lower CO2 emissions and consume 11% less water”. LEED has also diverted more than 80 million tonnes of waste from landfills.
REDUCE, REUSE AND RECYCLE
A global survey by management consultancy firm Accenture found 60% of consumers have been making more environmentally-friendly, sustainable or ethical purchases since the start of the pandemic. Nine out of 10 of those said they were likely to continue doing so.
As online shopping persists, it is important that businesses within the logistics sector look at providing sustainable packaging – which will not only increase their consumer appeal, but warehouses can also drastically reduce waste by reusing pallets, containers and recycling materials.
RENEWABLE ENERGY
According to Prologis, about 15% of a warehouse’s total operating budget goes toward energy costs. Therefore, making solar-powered warehouses and distribution centres a sought-after commodity not only saves money, but it also brings companies closer to their environmental, social and governance (ESG) goals.
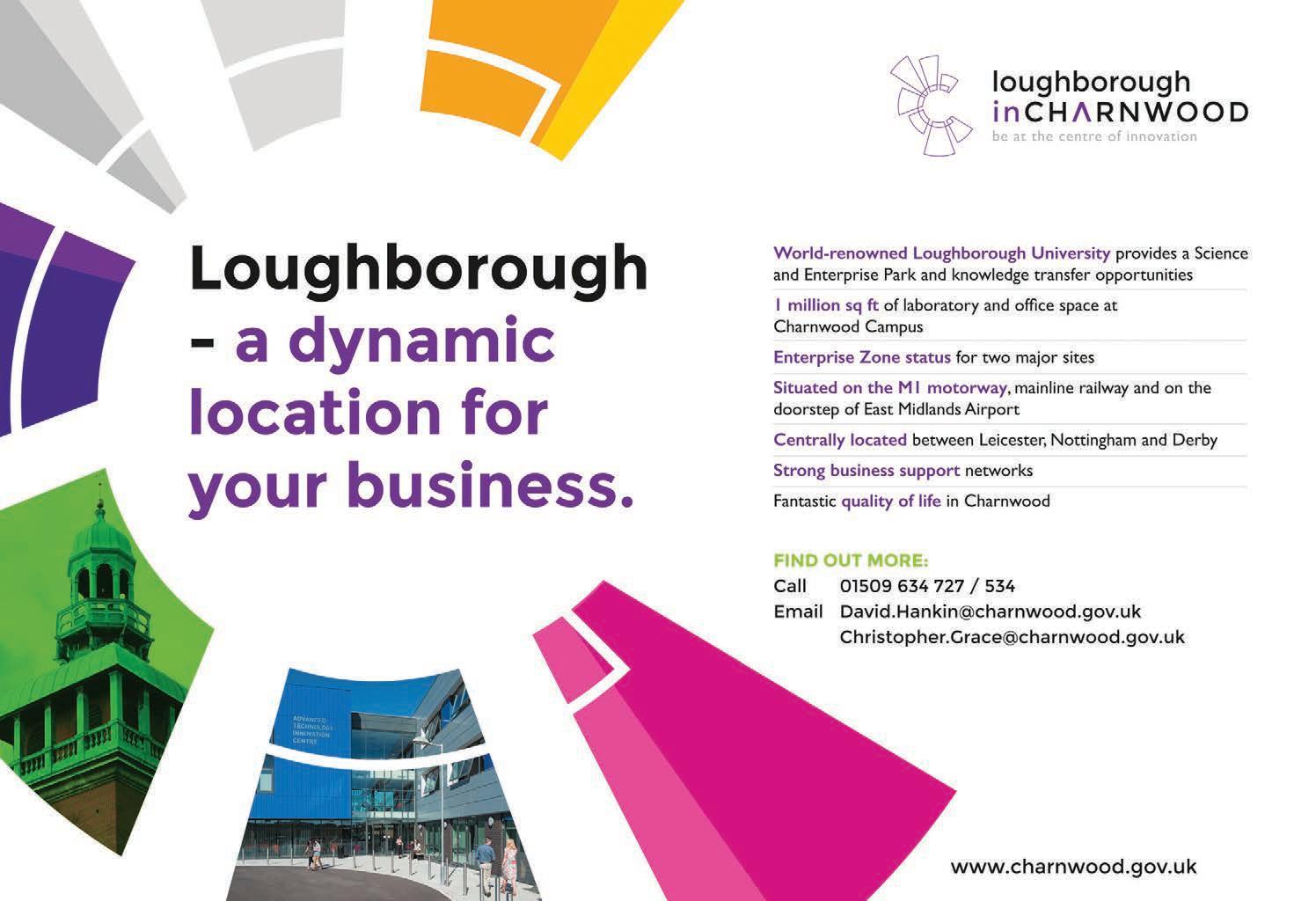