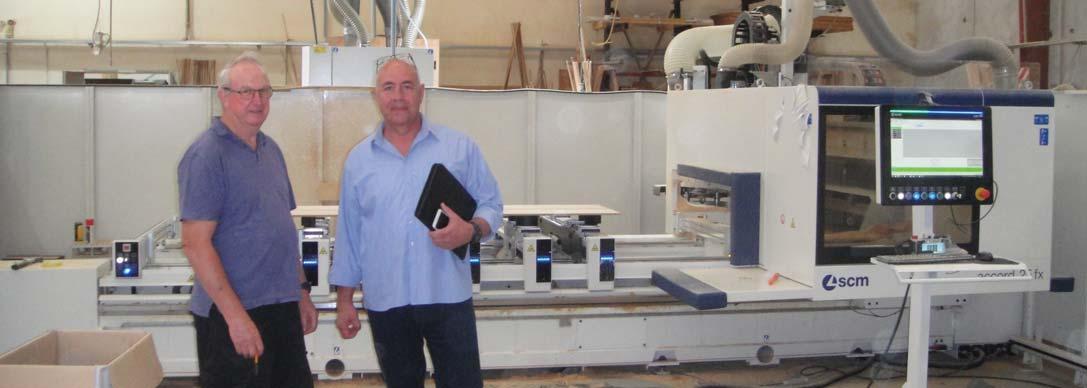
2 minute read
Hands free from SCM
Western Caskets in Kumeu just out of Auckland are one of New Zealands largest casket manufacturers producing over 10,000 caskets a year. Constant growth since its start up in 1979 has seen it regularly update its machinery and kept it at the forefront of technological innovations, no more so than it latest purchase, a pair of Accord fx 5 Axis machines from SCM which virtually eliminate sheet handling while enabling work on all faces of the panel.
The two SCM Accord 25 fx’s are full five axis gantry machines one set up with an individually motorised pod & rail system and the other with a high/low vacuum system, together they allow for great flexibility in handling sheet material through the casket manufacturing process.
For Western Caskets the purchase was a back up and replacement for their SCM Ergo CNC which was getting to the 15 year age mark. It represents their third generation of SCM machinery, however they are not exclusively loyal to the brand and always look around to find the right machine for the job.
“We were originally looking at a single, bigger machine,” says General Manager Alan Eastwood. “But we talked to John Fleet (from SCM dealer Machines R Us) and he suggested because of the nature of our work and high throughput a single machine would be operating at its upper limits, so suggested a set up of two CNC’s, one set largely for the manufacture of our lids and bottoms and the other to produce the carcass in between.”
“We went with that option and it has worked well. One of the SCM Accord fx’s features independently motorised pods and rails and is suited to the production of our carcass work. Once the cutting phase is complete the pods and rails automatically open allowing access for further edge work without handling or moving the piece. This wasn’t readily available elsewhere and had real appeal to us.
“The other Accord is set up with a high/low pressure vacuum system ideal for the way we manufacturer our lids and bottoms. It enables us to release waste and off cuts while keeping the components in the same place for further profile work.” we are now able to do all panel processingnesting, edgeprofiling and horizontal drilling - without handling the panel.
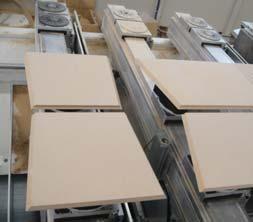
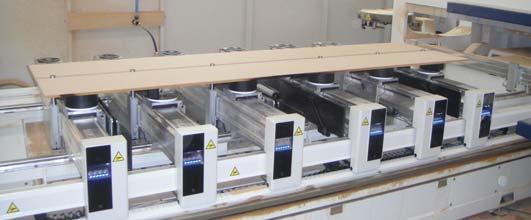
“This dual set up really does give us improved flexibility and functionality. We simply select the range we are wanting to manufacture from our library and place a sheet on the machine. The pods and rails know where to go and the operation is largely hands free as it processes each sheet, doing all cutting, drilling and edge profiling until only the finished component is left.”
“We also find the onboard software, Maestro, very good. It is easy to use, suits our requirements well, and we are able to make changes on the fly (not all caskets are off the rack) to enable individual custom sizings if required. And if there is an issue at all associated with any aspect of the machine there is always only one call to make.”
“We are very happy with the purchase,” says Alan. “John and his team at Machines R Us are very good to deal with, his advice on machines and their aptness for purpose is always relevant and their service and diagnostic skills are very good if we do run into issues.”
CNC Machining Centres
for solid wood drilling and routing
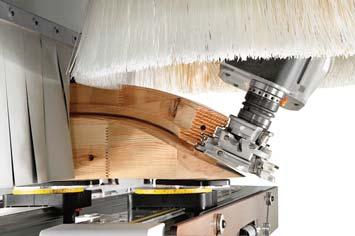