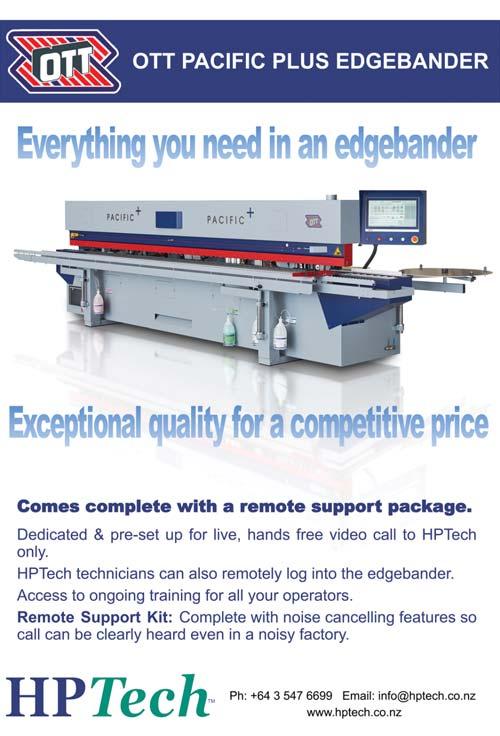
2 minute read
Bay of Islands magic
Adding value to Northlands timber resource whilst limiting exposure to dangerous dust
Cobalt dust poisoning is a real safety issue in some industries, but especially sawmilling. It’s a common problem in such areas as saw sharpening workshops in the wood processing industry.
A major sawmill processing plant, employing more than 100 staff in KeriKeri has a saw shop where the saw blades are sharpened, a process which produces a fine dust off the teeth, harmful due to the cobalt containing compounds. NZ DUCT+ DFLEX were asked to come up with a design to reduce staff exposure to this hazard.
NZ DUCT+FLEX staff first had experience of this issue at Honda UK’s car plant 20 years ago and had completed a very similar solution for another NZ sawmilling operation 2 years ago.
The KeriKeri site’s busy Saw Workshop deals with dry grinding for older machines, so the solution here included 2 moveable fume arms which can be moved out of the way for machine changes, yet pulled in close to capture the fine, dry, airborne dust.
Some machines were also ‘Wet’ with oil fluids used in the process of sharpening the blades. To deal with the mist produced, NZ DUCT +FLEX used Danish company GEOVENT’s Oil Mist Filters which extracted 1.000 m³/h of oily fume mist and removed it with a high filtration efficiency of 99% at 0.3μm ( better performance than many of the traditional oil mist filters on the market). These GEOVENT filters are ideal for filtration of oil mists in many situations: CNC lathing, milling and drilling machines which use cutting oil (regular, semisynthetic or synthetic), or waterbased emulsions. Oil captured is recycled, back to the machine, saving money.
A smaller GEOVENT Oil Drawer was also used for the removal of the oil mists from the cutting machines to ensure the mist cannot condense in the central extraction system. This simple unit is typical of a wide range of low cost but highly efficient products from GEOVENT, benefiting the working environment while protecting staff and company budgets.

Once oil free, this extracted air was then combined with the dry cobalt duct air generated by other processes in the saw workshop to a simple, cost effective, 2 Bay Bag emptying modular filter from JKF Industri, also a Danish company, serviced by a JKF 25D 4kw material handling fan.
All this was completed during the week with the sawmill operation fully functioning during the installation – NZ DUCT+ FLEX used both their install teams, permanent employees of the company, to complete the work on site withing 4 days.
Saw shop staff were very happy with the solution installed in July – the extraction system improved the work environment which was noticed by staff within hours: the problem smell and dangerous dust removed.
Says Geoff Ebdon, Sales manager for NZ DUCT+FLEX, “We are a NZ owned family business and have installed hundreds of extraction systems in NZ over the last 10 years. The company originally, in the 1980’s, only supplied metal LIPLOCK ® Ducting and flexible ducting products, but expanded to offer the widest range of dust and fume extraction products on the market. Working in conjunction with our long term Danish suppliers, we complete a new system each week on average, while also undertaking larger 1 million + projects across New Zealand, Australia and the Pacific. Backed by the largest stock and range of product in the country, we can quickly solve any level of Dust or Fume issues.”
For more information visit www.nzduct.co.nz
Or phone 0508 69 38 28
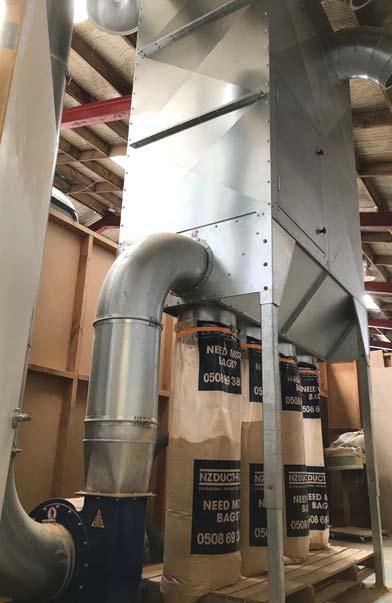
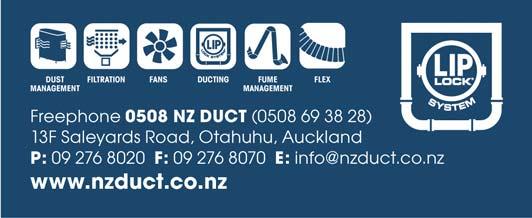


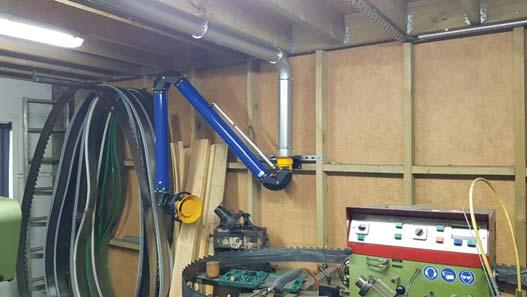