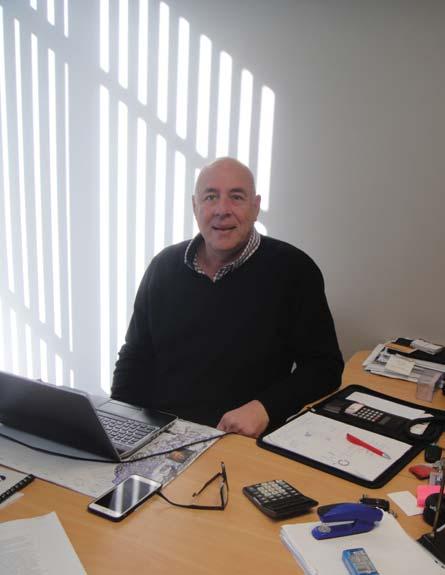
3 minute read
client advantage
John Fleet owner of SCM agent Machines R Us with some thoughts on 21 years of selling and servicing woodworking machinery in NZ
This gives our customers big advantages, the software and controls of all our high technology SCM products follow a common platform meaning an operator can operate between CNC machines and an edgebander for example with the appropriate training. Also with communication technology developing all the time the ability of machinery to share data via a common communication platform presents a great advantage to our customers. The days of simply looking at a factory as a collection of individual pieces of equipment is no longer valid as it is now possible to integrate all these individual machines into one data sharing system using SCM's technology advantage.
Flexible painting cell
For Machines R Us this is our 21st year of supporting NZ woodworkers and it has been an interesting journey for both ourselves and the industry in general.
Prior to setting up Machines R Us I qualified as a fitter & turner and was a registered electrician, so working as a technician within the woodworking industry was a good fit. In our early years we were focused only on service support for all types of equipment but inevitably customers started asking us for advice on purchasing new machinery which ultimately led us to representing several agencies for panel processing.
In 2014 the opportunity arose to represent Italian giant SCM Group in New Zealand this was really a time of growth for us with a large portfolio of high quality machinery available from SCM we were able to offer full turnkey solutions without the need to fill in the gaps with other brands. You can cut, edge, machine, sand and paint using only SCM machinery which is not something our competitors can offer from a single manufacturer.
Alongside our woodworking business we are also the largest supplier of advanced aluminium machinery in New Zealand with our CNC machines used by all but one of the extruders operating in the New Zealand market. We saw aluminium as an allied technology where our technicians could also offer the same high level of support we are known for in the woodworking industry.
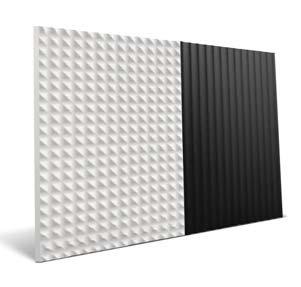
All in all we see New Zealand as a country of innovators with people willing to take up new technologies to compete in a global market and we want to be there for the future in supporting them.
As far as changes we have seen coming through over the years the growth of the internet for information sharing and for machinery shopping has had immense effect. And also the growth of the fake internet. This is dangerous as people can be led to believe what they are presented with on screen, this can portray small machinery manufacturers for example as something much more advanced than they actually are.
Also, the growth of assembly plants versus true manufacturing, today the amount of German equipment actually made in China is huge, rebranding has now become the norm for some manufacturers. While there is nothing wrong with this disguising it from potiential customers does I think raise ethical questions.
The versatility of the finishing effects is guaranteed by the "DMC Eurosystem" sanding machine, fitted with two new additions: a completely new planetary unit, ideal for structuring, chamfering, sanding the cross grain and precision finishing of any surface, and the interchangeable brushes unit, ideal for those in search of maximum production flexibility. The integration with the Superfici "mini" sprayer is essential. It is ideal for the sprayer's automation even in small businesses, that allow for the easy management of small production batches with regular product changes.
Machining centres for furniture
If the all-in-one "Morbidelli M100" machining centre for drilling and routing evolves further with the new ultra-compact, reduced bulk solution, that makes the 5-axis machine the smallest on the market, in the "Morbidelli P800" boring-milling and edgebanding centre, the combination between the MATIC work table and the innovative operator unit allows the most complex shaped pieces to be machined in just a few steps.
For nesting, the "Morbidelli X200/X400" range makes its mark by cutting pieces, even shaped ones, in a variety of forms and sizes with production levels once considered inconceivable for this kind of machining.
Flexibility and high productivity find their ideal synthesis in the drilling process with "Morbidelli UX200": thanks to 4 separate operator units (two upper and two lower), any kind of piece can be machined in a few steps. Furthermore, the possibility of machining two overlapping pieces means the production of symmetrical pieces can be doubled.
www.scmgroup.com