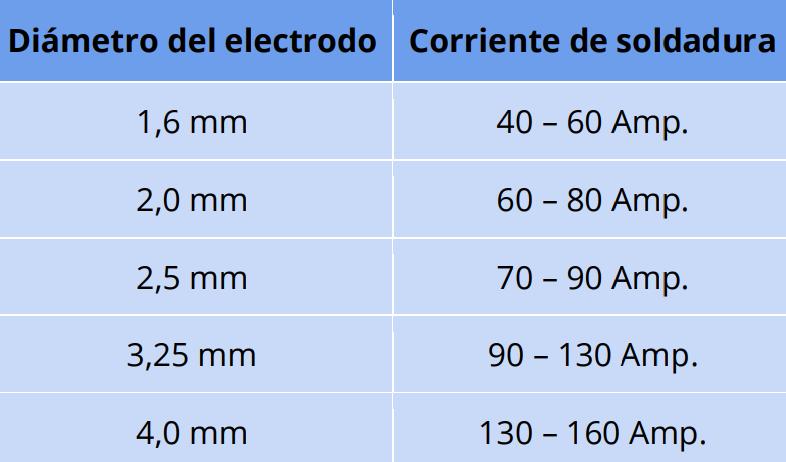
39 minute read
ENSAYO DE IMPACTO CHARPY
from REVISTA DIGITAL
1. Objetivo general:
Determinar la resistencia (tenacidad) de los materiales por medio del método Charpy para el ensayo de impacto a fin de valorar la tenacidad y los efectos de la temperatura en el comportamiento del tipo de fractura (dúctil o frágil) para un material dado.
Advertisement
2. Proposito:
El propósito de las pruebas de impacto es determinar la energía absorbida por una muestra hasta ocasionar la fractura. La propiedad relacionada con las pruebas de impacto es la tenacidad, que se define como la capacidad de un material para resistir la fractura al someterlo a una carga de impacto. Sin embargo, la resistencia de un material a la fractura, puede variar ampliamente, dependiendo de la proporción de la deformación.
3. Tenacidad:
Se define como la habilidad de un material para absorber energía sin fracturarse. La unidad de medida que valora este factor es la resiliencia. Si tenemos en cuenta el concepto anterior podemos asegurar que, como las deformaciones elásticas suelen ser muy pequeñas en relación con las deformaciones plásticas:
Si un metal es poco plástico, su deformación será pequeña y por tanto absorbe poca energía antes de romperse: es poco tenaz.
Si un material es muy plástico, la deformación antes de romperse es grande; absorbe mucha energía: es muy tenaz.
Uno de los métodos más sencillos para medir esta propiedad mecánica, es utilizando un aparato de ensayo conocido como máquina pendular de impacto. La resiliencia (Rs) obtenida de este ensayo viene expresada en unidades de energía (JOULE) dividida entre el área transversal de la probeta expresada en mm2 .
El ensayo de resistencia al impacto expresa una manera de cómo se fractura un material en función de la temperatura, mostrando además el comportamiento del material de dúctil a frágil.
4. Tipos de fracturas:
Fractura Dúctil: Un tipo de fractura que se caracteriza por una propagación lenta de la fisura. La fractura dúctil sigue por lo general una dirección en zigzag a lo largo de planos en los cuales se tiene un esfuerzo cortante resuelto máximo. Las superficies de fractura dúctil tienen, por lo general, una apariencia fibrosa y opaca.
Fractura frágil: Un tipo de fractura que se caracteriza por la nucleación y propagación rápida de una fisura con poca deformación plástica. En materiales cristalinos, las superficies de fractura frágiles se identifican por su apariencia granular y brillante.
5. Deformaciones de los metales:
Cuando un material se tensa por debajo de su límite elástico, la deformación resultante es temporal. Cuando un material se tensa más allá de su límite elástico, tiene lugar una deformación plástica o permanente, y no regresará a su forma original por la sola aplicación de una fuerza. La posibilidad de que un metal sufra deformación plástica es probablemente su característica más relevante en comparación con otros materiales. Todas las operaciones de formado, como son troquelado, prensado, hilado, laminado o rolado, forjado, estirado y extrusión, se relacionan con la deformación plástica de los metales. El comportamiento de un metal cuando se deforma plásticamente y el mecanismo mediante el cual ocurre, son de interés esencial para perfeccionar la operación de trabajado. La deformación plástica puede tener lugar por deslizamiento, por maclaje o mediante una combinación de ambos procesos.
Tipos:
Deformación por deslizamiento: Si el monocristal de un metal es esforzado tensilmente más allá de su límite elástico, se larga en forma ligera, aparece un escalón sobre la superficie indicando un desplazamiento relativo de una parte del cristal con respecto al resto y la elongación se detiene. Al aumentar la carga se producirá movimiento en otro plano paralelo y dará como resultado otro escalón. Es como si delgadas secciones vecinas del cristal se hubieran deslizado una sobre otra como cartas de barajas. El aumento progresivo de la carga, eventualmente produce fractura del material.
Imperfecciones de los cristales: Existen varias razones por las que la estructura reticular de un cristal no pueda ser perfecta. Las imperfecciones surgen a menudo naturalmente, debido a la incapacidad del material que se solidifica para seguir reproduciendo indefinidamente sin interrupción su celda unitaria; los límites de grano en los metales son un ejemplo. En otros casos, las imperfecciones se introducen intencionalmente durante el proceso de manufactura, como es el caso de la adición de un elemento que ligue con el metal para aumentar su resistencia.
6. ¿Qué otros factores de la temperatura afectan la ductabilidad y fragilidad de los metales?
Un aumento de temperatura provoca el correspondiente aumento de la ductilidad y la tenacidad. La fragilidad o la tenacidad depende no solo de las fuerzas de enlace entre los átomos, sino también de la contribución de posibles fenómenos de disipación de energía: plasticidad, microfisuración, cambio de fase, recristalización dinámica que tienen el efecto de aumentar significativamente, en obstinados sustancias, el volumen del dominio donde, en la punta de la grieta, los enlaces atómicos se oponen a su progresión al soportar el mayor esfuerzo de tracción Por tanto, la temperatura y la velocidad de deformación están especialmente implicadas
7. ¿Cuál es la función de la entalladura de la pieza de la probeta?
Consiste en colocar una probeta con entalladura tipo Charpy entre las mordazas paralelas de la máquina, luego se procede a dejar caer el péndulo desde una altura conocida que golpea la muesca, en su desviación descendente, de esta manera logra fracturarla. Seguidamente se procede a tomar la lectura directamente de la máquina, correspondiente a la cantidad de energía absorbida durante el impacto.
Dureza
1. Definición de dureza Brinell y fórmula de cálculo a. Dureza Brinell: Se denomina dureza Brinell a una escala de medición de la dureza de un material mediante el método de indentación, midiendo la penetración de un objeto en el material a estudiar. La dureza Brinell HB se obtiene de dividir la fuerza de ensayo por la superficie de penetración de la bola. b. Fórmula de Cálculo: La dureza se calcula dividiendo el valor de la fuerza aplicada al penetrador entre la superficie de la huella que produce en el material.
2. ¿Cómo se elige el diámetro de la bolilla en dureza Brinell?
El diámetro de la bolilla se elige en función del espesor y de la dureza del material. El espesor de la probeta debe ser mayor o igual que 10 veces la profundidaddepenetración.Si seconoceaproximadamenteladurezael diámetro máximo de la bolilla se calcula mediante: Si no se conoce la dureza se elige la mayorbolillaquecumplaconD≤e.serealizaelensayo ysedeterminaHB. Luego mediante la fórmula anterior se calcula Dmax y si es posible utilizar una bolilla menor utilizarla en un nuevo ensayo.
3. Cuáles son los límites de las siguientes variables para que el ensayo Brinell sea válido: Dureza, separación entre improntas, distancia de la impronta a los bordes, espesor.
Condiciones del ensayo, el método brinell no es aplicable en materiales muy duros. Para bolillas de acero duro es aceptable hasta 450HB (DIN dice no superar 300) para bolilla de carburo de tungsteno hasta 630HB.
El diámetro de la impronta es el promedio de dos diámetros medidos ortogonalmente con una precisión no inferior al 0.25% del diámetro de la bolilla.
El diámetro debe estar entre 0.2100.
Dureza rockwell superficial: usos; expresión de la profundidad de penetración; penetradores; cargas. La dureza rockwell superficial se usa para materiales similares a los ensayados rockwell (a, d, c)(materiales muy duros) y escalas “T”. Los penetradores son de cono de diamante las cargas adicionales son de 12, 27, 42. Y la expresión. La expresión de rockwell con C1= 1micrometro.
La expresión de Rockwell en función de penetración es h= C1 . (C-HR) valores de C1 (1 o 2 micrómetros según dureza a ensayar) C=100 para superficial y normal si se usa penetrador de diamante y c=130 para bolillas.
4. Dureza Rockwell.
La dureza Rockwell o ensayo de dureza Rockwell es un método para determinar la dureza, es decir, la resistencia de un material a ser penetrado. El ensayo de dureza Rockwell constituye el método más usado para medir la dureza debido a que es muy simple de llevar a cabo y no requiere conocimientos especiales.
5. Requisitos que debe cumplir la probeta a ensayar en dureza Rockwell en lo referente a preparación de la superficie, curvatura y espesor.
El resultado solo es válido si la superficie es plana. Para superficies curvas deberá aplanarse, sin embargo, para probetas cilíndricas con diámetros no menores a 6 mm en Rockwell normal ya 3 mm en Rockwell superficial podrá hacerse directamente y luego corregir el valor por tabla.
Lasuperficie aensayardebedeestarlimpia ylibre humedad,aceites, pinturas, oxido y cualquier otro material extraño que pueda afectar los resultados. Si es necesario el maquinado se debe evitar el calentamiento de la probeta.
La pieza o probeta debe apoyarse sobre un soporte rígido y con la superficie a ensayar perpendicular a la dirección de aplicación de la carga. No debe producirse durante el ensayo ningún desplazamiento de la probeta.
Al cambiarse el penetrador o el soporte de la probeta debe cuidarse el montaje firme en el alojamiento. Sin embargo, podrá haber un asentamiento al aplicar las cargas por lo que se invalidan las dos primeras lecturas luego del cambio.
El durómetro no debe sufrir vibraciones durante el ensayo y todas las operaciones manuales deben efectuarse sin brusquedades.
El espesor de la probeta debe ser el suficiente y para comprobarlo luego del ensayo debe observarse la cara opuesta a la de la impronta, donde no deben existir marcas o protuberancias visibles.
6. Dureza Vickers (conceptos generales)
En este ensayo se aplica un penetrador de diamante, conforma de pirámide recta de base cuadrada y 136° de ángulo entre caras, con una carga creciente hasta alcanzar un valor P. se mantiene esta carga P por un tiempo t y luego se retira la carga y el penetrador. En la superficie del material ensayado quedará la impresión (impronta) que deja el penetrador y se miden las dos diagonales de la base de la misma calculándose el promedio (d) de las misma.
8. Condiciones de ensayo en dureza Vickers.
El espesordelaprobetadebedesercomo mínimounavez ymedialadiagonal de la impronta (aproximadamente 10 veces la profundidad). Esta condición según las normas JIS, es válida para todos los ensayos de penetración. La superficie opuesta de la probeta no debe presentar deformación ni marcas visibles.
La superficie debe de ser plana para que los valores calculados correspondan a la dureza Vickers del material. Si la superficie es cilíndrica o esférica se podrá, dentro de ciertos límites corregir el valor mediante un coeficiente mediante tablas.
Además, debe de ser lisa y estar libre de óxidos y materiales extraños, en especial lubricantes (aceites grasos). Cuanto menor sea la carga más cuidado se deberá tener.
La distancia no debe ser menor a cuatro d entre centros de dos improntas y 2.5 d del centro de una impronta al borde de la probeta
Preguntas Y Respuestas
1. ¿Cuáles son los procesos de soldadura más comunes en la industria?
Arco eléctrico.
Laser.
Rayo de electrones.
Oxiacetilénico a) Los actos de accidentes, tiene que ver con el mismo trabajador, lleva a cabo comportamientos que son inseguros y no le pasa nada, lo que está haciendo es reforzar su mal hábito y mal comportamiento en seguridad y salud en el trabajo. b) Las condiciones de accidentes, son generadas por factores peligrosos del ambiente laboral. Las condiciones inseguras se refieren a lo mal acomodado, mal ubicado o desordenado de las cosas en el trabajo; en este sentido, la condición se refiere a cómo se encuentra el área de trabajo.
2. ¿Cuáles son los 4 tipos de soldadura básica?
Soldadura blanda.
Soldadura fuerte.
Soldadura por oxiacetilénica.
Soldadura por arco eléctrico.
3. ¿Qué es seguridad en soldadura?
Es usar el equipo de seguridad adecuado al momento de laborar, por qué la seguridad en la soldadura es importante y cómo evitar los peligros más comunes de la soldadura.
4. ¿Cuáles son las debilidades de un soldador?
Distracciones.
Exceso de confianza.
No usar equipo de protección personal.
Falta de respetos a las normas del trabajo.
5. Mencione una casuística de riesgo de seguridad en soldadura.
Supongamos que un trabajador de Sider Perú, está colocándose los equipos de seguridad para soldar dos piezas de metal, en eso lo llaman por celular y al contestar la llamada se distrae, y al finalizar de hablar comienza a soldar, cuando termino de soldar las dos piezas, él intenta sujetar las piezas, pero llega a quemarse las manos ya que, al momento de estar contestando la llamada de celular, se distrajo y no llego a colocarse los guantes de seguridad para soldar y evitar quemarse las manos.
6. ¿Cuál es la diferencia entre actos y condiciones de accidentes de soldadura?
7. ¿Qué es la norma ANSI Z 49?1?
Este Estándar cubre todos los aspectos de Seguridad y Salud en el ambiente de la soldadura, enfatizando en los Procesos de Soldadura Oxi - Gas y por Arco, con algún cubrimiento dado a la Soldadura por Resistencia. Contiene información sobre la protección del personal y el área general, ventilación, prevención de incendios y protección, y espacios confinados.
8. ¿Cuáles son las características del arco eléctrico?
El calor provocado por el arco no sólo es intenso, sino que además está muy localizado, lo que resulta ideal para la operación de soldar.
El arco eléctrico que se produce en todo proceso de soldadura se define como la corriente eléctrica que se establece a través del aire ionizado gracias a la diferencia de potencial inducida entre las partes.
La temperatura que se alcanza un arco eléctrico puede llegar a ser de 30.000º.
9. ¿Cuáles son las comparaciones entre CC y CA?
Tienen tres propiedades físicas fundamentales, la intensidad, la tensión y resistencia.
La corriente alterna cambia de sentido en su movimiento 50 veces por segundo en el caso europeo y 60 veces en el caso americano.
En la corriente continua los electrones se desplazan siempre en el mismo sentido.
10. ¿Cuáles son los principales factores para obtener un buen proceso de soldadura?
Electrodos apropiados para el trabajo, secos y bien conservados.
Longitud del arco eléctrico.
Angulo del electrodo respecto a la pieza.
Velocidad del avance.
Corriente eléctrica.
11. ¿Qué es soldadura SMAW?
La soldadura SMAW es un proceso en el cual la fusión del metal se produce debido al calor generado por un arco eléctrico que se crea entre el extremo de un electrodo y el metal base al que se va a unir.
12. ¿Cómo se genera el arco eléctrico en el proceso de soldadura SMAW?
El proceso de soldadura por arco eléctrico se origina por la fusión tanto del metal base como del metal de aporte, gracias al poder calorífico que aporta el arco eléctrico. Un metal fundido tiene, por lo general, gran avidez por fijar o absorber elementos del aire circundante
13. ¿Cuáles son las limitaciones del proceso de soldadura SMAW?
Los metales de bajo punto de fusión, como el plomo, el estaño, zinc y sus aleaciones, no se sueldan con SMAW porque el intenso calor del arco es demasiado para ellos.
El proceso no es apropiado para metales reactivos como el titanio, zirconio, tántalo y colombio porque la protección es insuficiente para evitar que la soldadura se contamine con oxígeno.
Un amperaje excesivo sobrecalienta el electrodo evapora su revestimiento químico, alterando con ello las características del arco y de la protección que se obtiene. Por esta limitación, las tasas de deposición suelen ser más bajas que en otros procesos de soldadura.
El ciclo de trabajo del soldador y las tasas de deposición globales para los electrodos cubiertos suelen ser menores que los alcanzables con un proceso de electrodo continuo.
Siempre debe eliminarse escoria en los puntos donde se inicia y se detiene antes de depositar una franja de soldadura junto a otra previamente depositada, o sobre ella.
14. ¿Qué es energía eléctrica y energía térmica en soldadura?
Energía eléctrica: La técnica soldadura eléctrica consiste en fusionar a una alta temperatura un metal (Alrededor de 4000ºC, creándose un cordón de soldadura que se forma al fundirse tanto el material base como el de aporte) este calor da paso a la corriente, que con precisión y control consiguen unir los metales.
Energía térmica: La soldadura por conducción térmica se caracteriza por una profundidad de exposición baja de un milímetro máximo. Se emplea principalmente para unir láminas de bajo espesor.
15. ¿Qué es la norma NEMA?
La norma NEMA (National electrical Manufacturers Association), define a las fuentes de corriente constante como aquellas que poseen una característica VoltAmpere descendente, entregando una corriente constante para cambios moderados en la tensión de la carga.
16. ¿Qué es un ciclo de trabajo en una máquina de soldar?
Las máquinas de soldar traen especificado el tiempo de trabajo continúo evitando sobrecalentamientos y así reducir su vida útil.
17. ¿Cuál es la longitud máxima de cables de porta electrodo y pinzas de máquina de soldar?
Juego de cables calibre 2 AWG PAS 250 Infra, son 2 cables que permiten tener repuestos que unan cualquier máquina soldadora con los electrodos. Funcionan con 600 watts. Uno de ellos es para conexión a negativo que cuenta un largo de 4 m, con una tenaza de tierra de 300 amperes y una zapata de cobre cubierta de estaño con diámetro de 1/2 pulgada. El otro es para conexión a positivo con 6 m de largo, con una zapata de cobre cubierta de estaño de 1/2 pulgada de diámetro. Están fabricados con cobre, el cual es buen conductor eléctrico; están recubiertos de plástico para hacerlos seguros, resisten temperaturas de hasta 105 grados centígrados.
18. ¿Qué es la soldadura inverter?
Los soldadores inverter son máquinas eléctricas que funcionan sin transformador de potencia, por lo que son autónomas a la hora de desarrollar cualquier trabajo. Entre otras características, aportan mucha más estabilidad que las tradicionales, y su eficiencia está más que demostrada en proyectos profesionales.
19. ¿Cuáles son las diferencias entre máquina de soldar transformador y rectificador?
Máquina de soldar transformador: Modifica la corriente eléctrica, bajando la tensión e intensidad de la red de alimentación de bajo voltaje y alto amperaje, seguros para soldar. Este tipo de máquina es más económica, pero es más pesada, ofrece menor amperaje y mayor consumo de energía. Además, solo suministra corriente alterna, lo cual la limita en los procesos de soldadura. Se utiliza para soldadura por arco con electrodo revestido (SMAW.)
Máquina de soldar rectificador: Para proteger los cables de alimentación, está conformado por un transformador que cambia la tensión e intensidad de la corriente para soldar; y por un rectificador de silicio, que permite que la energía fluya en un único sentido, es decir, convierte la corriente alterna en corriente continua.
20. ¿Por qué es peligroso utilizar electrodos húmedos?
Una cantidad relativamente alta de humedad en los electrodos de bajo hidrógeno provoca una porosidad externa visible además de la porosidad interna. También puede causar una excesiva fluidez de la escoria, una superficie de soldadura rugosa, dificultad para eliminar la escoria y agrietamiento.
21. ¿Cuántos diámetros de electrodos existen y sus amperajes de trabajo?
22. ¿Cómo elegir el diámetro del electrodo?
La elección del diámetro del electrodo es relativamente más sencilla, elige siempre el electrodo de menor diámetro que más se acerque al espesor del material que vas a soldar. Por ejemplo, para soldar un material cuyo espesor es de 1/8” (aprox 3 mm) usaremos un electrodo de 1/8, para soldar un material de ¼ (6.35 mm) es preferible utilizar un electrodo de 5/32 (3.96 mm)
23. ¿Qué se puede soldar con electrodo E-6011 y E-7018?
E-6011: Este electrodo es apto para ser utilizado en todas las aplicaciones de soldadura en acero dulce, especialmente en trabajos donde se requiera alta penetración.
E-7018: Electrodos para soldar aceros al carbón. Se emplea para la soldadura de aceros al carbono de resistencia a la tensión 70.000 psi.
24. Mencione las diferencias entre los revestimientos del electrodo a. Revestimiento celulósico: Su composición química está formada básicamente por celulosa integrada con aleaciones ferrosas (magnesio y silicio). La celulosa va a desprender gran cantidad de gases en su combustión, lo que va a reducir la producción de escorias en el cordón, a la vez que va a permitir ejecutar la soldadura en posición vertical descendente. b. Revestimiento ácido: Su composición química se basa principalmente en óxidos de hierro, y en aleaciones ferrosas de manganeso y silicio. Va a generar un baño muy fluido, lo que no va a permitir ejecutar la soldadura en determinadas posiciones. Por otro lado, este tipo de revestimiento no va a dotar al flujo de un gran poder de limpieza en el material base, por lo que puede generar grietas en el cordón. c. Revestimiento de rutilo: En su composición química predomina un mineral denominado rutilo, compuesto en un 95% de bióxido de titanio, que ofrece mucha estabilidad y garantiza una óptima estabilidad del arco y una elevada fluidez del baño, lo que se traduce en un buen aspecto final del cordón de soldadura. d. Revestimiento Básico: La composición química de este revestimiento está formada básicamente por óxidos de hierro, aleaciones ferrosas y por carbonatos de calcio y magnesio a los cuales, añadiendo fluoruro de calcio se obtiene la fluorita, que es un mineral muy apto para facilitar la fusión del baño.
25. Las funciones principales de revestimiento de electrodo es: a. Función eléctrica: b. Función física:
Mejorar el cebado del arco. Para ello al revestimiento se le dota de silicatos, carbonatos y óxidos de Fe y Ti que lo favorecen.
Estabilización del arco. Una vez originado el arco es necesario su estabilización para controlar el proceso de soldadura y garantizar un cordón con buen aspecto. Para ello, en la composición del revestimiento debe primar la presencia de iones positivos durante el proceso de soldadura. Esto se consigue añadiendo a la composición sales de sodio y potasio, que además cumplen otra función, como la de servir de aglutinante a los demás elementos de la composición del revestimiento.
Formación de escorias. La formación de escoria en el cordón permite disminuir la velocidad de enfriamiento del baño, mejorando las propiedades mecánicas y metalúrgicas del cordón resultante. Esto se consigue porque la escoria va a flotar en la superficie del baño, quedando atrapada en su superficie.
Gas de protección. Por otro lado, la función protectora se consigue mediante la formación de un gas protector que elimina el aire circundante y los elementos nocivos que ello conlleva como son el oxígeno presente en la atmósfera (que produce óxidos del metal), el nitrógeno (que da dureza y fragilidad al cordón) o el hidrógeno (que introduce más fragilidad a la unión).
Versatilidad en el proceso. La presencia del revestimiento en el electrodo va a permitir ejecutar la soldadura en todas las posiciones.
Concentración del arco. Logrando una mayor concentración del arco se consigue mejor eficiencia en la soldadura y disminuir las pérdidas de energía. Este fenómeno se consigue debido a que el alma metálica del electrodo se consume más rápidamente que el revestimiento, originándose así una especie de cráter en la punta que sirve para concentrar la salida del arco. c. Función Metalúrgica:
Mejorar las características mecánicas. Mediante el revestimiento se pueden mejorar ciertas características del cordón resultante mediante el empleo de ciertos elementos en la composición del revestimiento y de la varilla que se incorpora en el baño del cordón durante el proceso de soldadura.
Reducir la velocidad de enfriamiento. Al permitir un enfriamiento más pausado del cordón, se evitan choques térmicos que provoquen la aparición de estructuras más frágiles. Ello se consigue porque las escorias producidas quedan flotando en el baño de fusión y forman una capa protectora del cordón, que además sirve de aislamiento térmico que reduce su velocidad de enfriamiento.
26. ¿Cómo calcularía el número de electrodos para una soldadura?
I. Calcule el área de soldadura (sección transversal de la soldadura) incluyendo el refuerzo de la raíz y la tapa en milímetros cuadrados.
II. Multiplique el área de soldadura por la circunferencia de la tubería (longitud de la soldadura) para obtener un volumen de soldadura en milímetros cúbicos.
III. Divida esta respuesta por 1,000,000,000 para obtener el volumen de soldadura en metros cúbicos
IV. Multiplique el volumen de soldadura por la densidad del metal (7,800 kg / m ^ 3) para obtener la masa de metal de soldadura por soldadura (en kg) 5) Multiplique la masa por soldadura por el número total de soldaduras para dar el metal de soldadura total requerido (en kg).
V. Agregue una contingencia del 20-30% por desperdicio, etc.
VI. Calcule la masa de electrodo necesaria por kilogramo de metal de soldadura depositado (varía dependiendo del consumible, pero I utilice como regla general 1,5 kg de masa de electrodo por 1 kg de metal de soldadura.
VII. Entonces tiene la masa de electrodos necesaria en kilogramos. 9) Decida la división entre los diámetros de los electrodos, por ejemplo, el 5% de los electrodos será 2.
27. ¿Cómo clasificaría electrodos para acero inoxidable y aluminio?
I. Clasificación de electrodos para aceros inoxidables - AWS A5.4 (E XXX-YZ) a. E, indica que se trata de un electrodo para soldadura por arco. b. XXX, indican la clase AISI de acero inoxidable para el que está destinado el electrodo. c. Y, indica la posición en la que se puede soldar satisfactoriamente con el electrodo: a. 1 → Electrodo apto para soldar en todas las posiciones (plana, vertical, techo y horizontal) b. 2 → Electrodo solo aplicable para posiciones planas y horizontal c. 3 → Electrodo solo aplicable para posición plana d. 4 → Electrodo adecuado para soldadura sobre cabeza, vertical descendiente, plana y horizontal d. Z, indica el tipo de revestimiento, la clase de corriente y la polaridad a utilizarse.
II. Aluminio: Electrodo de tungsteno puro con menor conductividad eléctrica que el electrodo al 2% TH o de Lanthano, Por sus características es recomienda para aleaciones donde se requiere la corriente alterna (CA) tales como aluminio y magnesio Para una Mayor estabilidad del arco eléctrico no saque punta y permita que este deforme.
28. ¿Por qué se precalientan algunas uniones antes de soldarse?
Reduce la velocidad de enfriamiento en el metal de soldadura y el metal base, produciendo una estructura metalúrgica más dúctil con mayor resistencia al agrietamiento.
La velocidad de enfriamiento más lenta brinda una oportunidad para cualquier hidrógeno que puede estar presente para difundirse inofensivamente sin causar grietas.
Reduce las tensiones de contracción en la soldadura y el metal base adyacente, lo cual es especialmente importante en uniones muy restringidas.
29. ¿Por qué es importante el arco eléctrico en las uniones por soldadura?
La soldadura por arco es uno de varios procesos de fusión para la unión de metales. Mediante la aplicación de calor intenso, el metal en la unión entre las dos partes se funde y causa que se entremezclen directamente, o más comúnmente con el metal de relleno fundido intermedio.
30. En los procedimientos de soldeo es importante el diseño de unión, posición y secuencia de soldeo, debido a:
Debido a que un solo error pueda causar cualquier fallo en la soldadura, como la interferencia con la coordinación de los movimientos necesarios para mantener una buena secuencia de soldeo, arriesgando el trabajo que realiza el soldador.
31. El número de pasadas en soldeo está en función de:
El número de pasadas es el nº de veces que se ha tenido que recorrer longitudinalmente la unión hasta completarla. Como resultado de cada pasada se obtiene un cordón de soldadura.
32. Asumiendo la función de supervisor de soldadura, proponga una ruta y/o hoja de calificación de soldadores.
33. ¿Qué diferencia hay entre unión y posición de soldeo?
Posición: Las posiciones de soldadura, se refieren directamente a la posición del eje de la soldadura en los diferentes planos de soldar, en soldadura existen normas y códigos que rigen las diferentes posiciones vigentes para ejecutar trabajos en diferentes materiales y perfiles, entre los más destacado están las posiciones en planchas y tuberías, todas las posiciones exigen un mínimo de conocimiento y habilidad del soldador para lograr su ejecución.
Unión: Unión de dos o más materiales produciendo una continuidad en la naturaleza de los materiales por medio de calor y/o presión y con o sin la utilización de material de aportación.
34. El diseño de las uniones de soldeo está en función a:
El diseño de la unión soldada determina qué tipo de soldadura se debe producir para cumplir los estándares de calidad de la aplicación. Cuando se diseña una unión soldada, es obvio que el objetivo es proporcionar al menos una resistencia mínima adecuada para la aplicación en cuestión. Pero en algunas uniones, la máxima resistencia mecánica puede ser su principal preocupación.
35. ¿Por qué es importante el GAP o separación de espacio al soldar platina de 4 mm de espesor?
Es importante, para que, al momento de soldar con el electrono, el metal se funde, así puedan unirse y rellenando el espacio entre ambas platinas.
36. ¿Qué función cumple el Backing al soldar platinas de acero al carbono de 15 mm de espesor?
Se suele emplear para el caso que no sea posible voltear la pieza. En caso que se pueda tener acceso por el otro lado del cordón, se volvería a realizar una pasada por el cordón de raíz para resanarlo.
37. ¿Por qué la preparación de bisel en X es recomendable para espesores de 20 mm de platina de acero al carbono?
Para tener accesibilidad por ambas caras. Asimismo, para corregir o compensar las deformaciones angulares que se puedan originar se suelen realizar de forma asimétricas. También, refuerza la soldadura haciéndole más resistente.
38. ¿A criterio de soldador para soldeo en 1G sin bisel, el movimiento del electrodo sería el más adecuado, media luna, arrastre o retroceso? Explique
La medialuna, se realiza una mejor fusión al momento de soldar, el electrodo se mueve a través de las juntas, lo que asegura una buena fusión en los bordes.
39. Proponer los parámetros de soldeo en 1G de dos platinas de 300 mm de longitud, 16 mm de espesor de acero al carbono
Par Metros
Amperaje
Entre 80 - 120
Electrodo 4mm
Biselado Bisel en v 60°
Cordón Círculo, zig zag, triangular, etc.
40. Proponer los parámetros de soldeo en 2F de dos platinas de 400 mm de longitud, espesor 4 mm de acero al carbono
PARÁMETROS
Amperaje
Entre 60 - 65
Electrodo 3mm Biselado Bisel en x Cordón Media luna, zig–zag, triangular, etc.
41. ¿Cómo detectar un defecto en la soldadura?
Una técnica destructiva, pero económica y sencilla, que permite detectar la presencia de defectos en una soldadura es el examen macroscópico, que consiste en cortar el cordón soldado perpendicularmente y observarlo a simple vista o con menos de 50 aumentos, bien antes o después de ser desbastada y atacada dicha sección por un ácido que revelará el contorno de las pasadas que conforman el cordón soldado y la zona afectada por el calor. La inspección macrográfica es fácil de aplicar y de interpretar, permitiendo determinar de forma rápida si un procedimiento de soldeo está dando lugar a defectos internos no admisibles. Conociendo el aspecto que presentan los defectos macrográficos más importantes, es posible identificarlos y relacionarlos con las causas que los producen, pudiendo actuar sobre dichas causas y evitando que vuelvan a aparecer.
42. ¿Cómo determinar si es un defecto o discontinuidad en una unión soldada?
Discontinuidad: Una discontinuidad es una alteración de las propiedades normales de un metal, todos los metales presentan alguna discontinuidad. Estas discontinuidades se pueden clasificar, dependiendo de su efecto sobre las propiedades delos metales. Las discontinuidades que afectan a la soldadura en sus propiedades, pudiendo causar falla en servicio son llamados defectos. De esto podemos concluir: “Una discontinuidad se define como una variación de la estructura típica de una soldadura, falta de homogeneidad en la composición química, mecánica, metalúrgica o características físicas del material base o de aporte”.
Defecto: Discontinuidad cuyo tamaño, forma, orientación, ubicación o propiedades son inadmisibles para alguna norma específica. En particular, al realizar un ensayo no destructivo(END) se cataloga como defecto a toda discontinuidad o grupo de discontinuidades cuyas indicaciones no se encuentran dentro de los criterios de aceptación especificados por la norma aplicable.
43. ¿Cuáles son los problemas de que una soldadura se enfría demasiado rápido?
Cuando la soldadura se enfría, tiende a contraerse, y un cordón cóncavo o pequeño puede provocar tensiones de tracción a través de la superficie de la soldadura, de borde a borde. Estas tensiones normalmente son suficientes para romper la superficie.
44. ¿Qué norma se utiliza para la inspección por líquidos penetrantes?
Normas ASTM utilizadas para la inspección con líquidos penetrantes
45. ¿Qué defectos podemos encontrar con el ensayo de tintas penetrantes?
Con una inspección mediante líquidos penetrantes podemos detectar defectos en superficies fundidas, forjadas o soldadas, tales como porosidades en la superficie, pliegues de forja, y grietas de fatiga en los componentes que están en servicio.
46. ¿Qué función tiene la capilaridad?
La capilaridad se define como el movimiento de un líquido a lo largo de la superficie de un sólido causado por la atracción de las moléculas del líquido hacia las moléculas del sólido.
La soldadura y la soldadura fuerte con accesorios de soldadura capilar es el sistema más común para unir el tubo de cobre.
47. ¿Cuáles son los efectos del ZAC?
Grietas de Garganta.
Grietas de Raíz.
Grietas en el Pie.
Grietas en el Cráter.
Grietas Bajo el Cordón.
Grietas en la Zona Afectada por el Calor (ZAC)
Grietas de Metal Base
48. ¿Cómo reducir el ZAC?
Homogeneizar, en cierto nivel, la entrada de calor. De esta manera se disminuye la ZAC y se reduce la posibilidad de transformaciones microestructurales. Reducir el tiempo de enfriamiento.
49. ¿Qué es contracción y dilatación en soldadura?
Todos los metales al calentarse aumentan de tamaño y se reducen al enfriarse. Este fenómeno se conoce como dilatación y contracción, respectivamente. Durante el proceso de la soldadura, el calor producido por el arco tiende a calentar la pieza y, por lo tanto, a dilatarla. Una vez terminada la soldadura, la pieza se enfría y en consecuencia, tiende a c
50. ¿Qué diferencias hay entre soldeo en posición 3G y 3F?
Posición 3G: La soldadura en una posición 3G implica mover el electrodo verticalmente, hacia arriba y hacia abajo a través de una superficie.
Posición 3F: Platina en un plano vertical con el eje de la soldadura vertical. Platinas así ubicadas en donde la soldadura es depositada en su eje vertical.
51. ¿Por qué tomar el ensayo en posición 3g para una calificación de soldadura?
Dado que el proceso de soldadura por arco con electrodo revestidos es el proceso preferido para la mayoría de los trabajos al aire libre, tiene sentido que se tome esta calificación de soldadura. El ensayo de calificación de soldadura en la posición 3G, califica para soldar en las posiciones 1F, 2F, 3F y las posiciones 1G, 2G, 3G en acero estructural. También califica para realizar soldaduras de filetes en tubos con un diámetro mínimo de 24.
52. ¿Por qué consideran para la calificación de soldadura ensayo de tracción, inspección visual, líquidos penetrantes y doblez?
Sirven para determinar los valores característicos de los materiales. Identifica materiales que no cumplen especificaciones, facilita la corrección de defectos durante el proceso de fabricación, reduce la necesidad de posteriores ensayos no destructivos END.
53. ¿Qué significa WPS y PQR en calificación de soldadura?
Los WPS y los PQR son los planos para crear soldaduras de manera repetible, eficiente y segura. La parte B del examen del Inspector Certificado de Soldadura (CWI) se centra en la aplicación práctica de la inspección y se conoce ampliamente como la parte práctica del examen.
54. Una probeta de acero estructural de 5 x 80 x 200 mm se va a soldar en posición 3g. Determinar los parámetros de soldeo.
Par Metros
Amperaje Entre 70 - 75
Electrodo E-6011
Biselado Bisel en “X”
Cordón Media luna, en “U”,
55. Una probeta de acero estructural de 10 x 90 x 150 mm se va soldar en posición 3g. Determinar los parámetros de soldeo.
PARÁMETROS
Amperaje
Entre 60 - 65
Electrodo E-6011
Biselado Bisel en “V”
Cordón Media luna, zig–zag, triangular, etc.
56. ¿Qué diferencias hay entre soldeo en posición 4G y 4F?
Posición 4G: La pieza colocada a una altura superior a la de la cabeza del soldador, recibe la soldadura por su parte inferior. El electrodo se ubica con el extremo apuntando hacia arriba verticalmente. Esta posición es inversa a la posición plana o de nivel.
Posición 4F: Soldadura bajo techo. posiciones de soldeo de chapas a tope. Realice una soldadura 4F de filete en posición elevada, al realizar soldadura de filete convexo, de pasadas múltiples en una unión en T con electrodo E6010 de 1/8”.
57. ¿Por qué no tomar el ensayo en posición 4g para una calificación de soldadura?
Porque depende de las normas y el código, a parte que es más complicada y se tiene que realizar con todo su equipo EPP.
58. Una probeta de acero estructural de 6 x 60 x 150 mm se va a soldar en posición
4g. Determinar los parámetros de soldeo.
PARÁMETROS
Amperaje
Electrodo
Cordón
Entre 65 - 75
E-6011
Media luna
59. Una probeta de acero estructural de 14 x 80 x 200 mm se va soldar en posición
4g. Determinar los parámetros de soldeo.
PARÁMETROS
Amperaje
Electrodo
Cordón
Entre 65 - 75
E-6011
Media luna
60. ¿Por qué es tan importante la homologación de soldadores?
En un entorno industrial cada vez más competitivo y con altos requerimiento de controles de calidad, el aseguramiento de nuestros procesos y productos fabricados es una obligación industrial para el sostenimiento de la propia comercialización de los productos fabricados.
61. ¿Sería aceptable el espesor de garganta de 6 mm, al emplear electrodo de diámetro 6mm? ¿Por qué?
No, porque Según el espesor a mayor espesor utilizaremos un electrodo de mayor diámetro, y viceversa.
62. ¿Por qué esta prohibido el uso de oxicorte de aceros inoxidables?
El oxicorte no se usa para cortar acero inoxidable, ya que este material tiene un punto de fusión muy elevado, por lo tanto, no se quema fácilmente.
63. Si el cordón de estructura soldada posee exceso de tensión residual, ¿se podría hacer tratamiento térmico?
Durante el proceso de soldadura se generan efectos indeseables en el material, como el exceso detención residual. Con el fin de mitigar la influencia de este efecto no deseado las uniones soldadas requieren el calentamiento controlado tanto del metal base como del metal de soldadura. Estos procedimientos de calentamiento mantenimiento y enfriamiento controlado, se pueden dar antes, durante y después del proceso de soldadura y afectan a las propiedades mecánicas de la unión soldada de 2 mm
64. ¿Qué diferencias hay entre soldeo de tubería con soldeo plano?
Soldeo de tubería: Tubo con su eje horizontal y rodado durante la soldadura y el cordón hacia arriba.
Soldeo plano: El soldeo avanza moviéndose a través de la pieza plana en dirección horizontal y el cordón hacia abajo.
65. ¿Qué diferencias habrá entre soldeo blando con soldeo eléctrico de tubería?
Soldeo blando: EL objetivo es tener el mejor rendimiento mecánico posible, el metal se aporte se funde a menos de 450 °C.
Soldeo eléctrico de tubería: El amperaje se regula de acuerdo al espesor del tubo, el diámetro del electrodo, también influye.
66. ¿Cuáles son los parámetros para soldeo de tubo de acero estructural de 2mm de espesor y 80 mm de diámetro?
67. ¿Cuáles son los parámetros para soldeo de tubo estructural de 7 mm de espesor y 100 mm de diámetro?
3.25 mm
68. ¿Qué recomendaciones haría para soldar tubos delgados de acero estructural?
Reducir las calorías aportadas al material a soldar.
Tenemos que tener en cuenta que estamos soldando un material de 1 a 2 milímetros que pronto se pone al rojo vivo y roza su punto de fusión en muy poco tiempo.
Las paredes de estos materiales tan finos soportan muy pocas calorías en poca superficie, por lo tanto, tenemos que reducir si o si las calorías aportadas.
Utilizando electrodos delgados de poco diámetro.
69. ¿Qué diferencia hay entre tubo galvanizado, tubo laminado, tubo con costura, tubo inoxidable?
Tubo galvanizado: Es un recubrimiento de zinc, que se obtiene por inmersión en caliente, hecho con la finalidad de proporcionar una protección a la oxidación y en cierto porcentaje a la corrosión.
Tubo laminado: Son tubos que se fabrican bajo la norma EN 10255 utilizando materia prima con la calidad S 19, disponibles tanto en negro como en galvanizado. Estos tubos ofrecen una enorme resistencia mecánica, comportándose mejor frente a esfuerzos de torsión, presión, compresión, etc.
Tubo con costura: El tubo de soldadura (o con costura) se fabrica a partir una lámina o placa de acero plana, y se realiza una costura soldando el cuerpo del tubo. Este tipo de tubos incluye el tubo ERW, el tubo LSAW, y el tubo SSAW.
Tubo inoxidable: Los tubos de acero inoxidable son ampliamente utilizados en la industria y el entorno doméstico. Pueden presentar cualquier diámetro, largo o grosor, y ser desde simples y estrictamente funcionales, hasta atractivos y decorativos, usándose también en el arte.
70. ¿En qué se diferencia la soldadura por capilaridad de la soldadura por fusión?
En la soldadura por capilaridad usamos material de aporte para unir dos piezas de metal, mientras que en la soldadura por fusión calentamos las dos piezas de metal hasta que se derritan y se fundan entre sí.
71. ¿Qué ventajas presenta la soldadura por capilaridad sobre el soldeo por fusión?
-No se alcanzan cambios físicos en el material a soldar al no alcanzar la temperatura de fusión.
-No se presentan tensiones superficiales gracias a que la temperatura alcanzada es muy baja.
-Se puede conservar los recubrimientos de los materiales base.
-Facilidad para obtener uniones sanas entre materiales diferentes, incluso entre materiales metálicos y no metálicos o entre materiales de diferentes espesores.
-Se pueden obtener soldaduras en piezas de precisión
72. ¿Cuál es la principal limitación del soldeo por capilaridad?
- El diseño de las piezas, y en algunos casos su preparación, puede resultar más complicado y costoso.
- Resulta muy costosa su aplicación en el caso de piezas grandes
73. ¿Por qué es importante la separación entre bordes en el soldeo por capilaridad?
Para que el material de aporte pueda fluir correctamente por entre las superficies por donde tendrá lugar la unión, es necesario determinar la correcta separación entre las partes
74. ¿Cómo pueden limpiar las piezas a soldar?
Las zonas de las piezas a unir deben permitir un contacto lo más perfecto posible entre ellas, para ello será necesario prepararlas. También será necesario limpiarlas, eliminando la cascarilla, óxido o las posibles suciedades. Para la limpieza de la pieza utilizaremos el fundente.
75. ¿Para qué sirve el desoxidante en el soldeo por capilaridad? Desoxidantes, sirve para que se evite la oxidación.
76. ¿Por qué es necesario eliminar los residuos del desoxidante?
En el momento que descubrimos que tenemos óxido en una pieza debemos determinar en qué zona está y si es viable la reparación. El óxido puede aparecer tanto en chapas exteriores o interiores y en piezas mecánicas. Para solucionarlo podremos necesitar algún desoxidante.
77. ¿Cómo se designan los materiales de aportación para soldadura por capilaridad?
Deben reunir las siguientes características:
- Facilidad de mojado y capacidad para conseguir uniones resistentes con el metal de base.
- Temperatura de fusión adecuada y fluidez que permita una buena distribución por capilaridad.
- Homogeneidad suficiente, resistencia a la segregación (separación de algunos componentes) y pequeño contenido en elementos volátiles.
-Capacidad para conseguir uniones que respondan a las exigencias en servicio, tales como resistencia mecánica y a la corrosión.
78. Cuándo suelda por capilaridad con soplete, ¿Cómo debe realizarse el calentamiento?
Se debe calentar las piezas hasta conseguir que toda la junta se encuentre a la temperatura de trabajo. Esta operación debe realizarse moviendo el soplete a lo largo de la junta, con la llama relativamente lejos de las piezas, a fin de obtener un calentamiento uniforme.
79. ¿Cuál es la técnica de soldadura por capilaridad más recomendable para mejorar la productividad en trabajos de serie?
Es la Técnica del soldeo manual por capilaridad
80. ¿Qué significa ENA en soldadura Mig?
Se denomina Energía Neta Aportada ENA a la energía real que recibe la pieza durante la operación de soldadura.
81. ¿Qué es EBA en soldadura Mig?
Se denomina energía de aportación o Heat Input al calor puesto en juego en el proceso de soldeo. Esta energía, también llamada Energía Bruta Aportada EBA, se expresa en función de los parámetros del arco en julios por unidad de longitud de soldadura.
En donde:
U.- tensión del arco en voltios
I: intensidad de la corriente en amperios
T: tiempo de fusión del electrodo durante el cual se aporta calor a la pieza, en segundos v.- velocidad de avance de la soldadura en cm/min Como puede observarse, la EBA es independiente del diámetro del electrodo. En realidad, esta influencia va implícita en la intensidad de la corriente y el tiempo necesario para su fusión.
82. ¿Qué significa ER70S-6?
Son los alambres de mejor rendimiento y mayor costo, y los que tienen los mayores niveles de silicio y manganeso como desoxidantes. Son adecuados para la soldadura de casi todos los aceros, desde acero al carbono fino hasta placas de 1/2 pulgada (con el diámetro apropiado de alambre), funciona con las mezclas de gases más usadas y el charco posee una buena fluidez. Sus aplicaciones incluyen la fabricación de carrocerías, muebles, extinguidores, recipientes a presión y soldadura de cañerías, entre otras.
83. ¿Qué espesor se puede soldar con Mig?
Las ventajas que tiene la utilización de la soldadura MIG se pueden resumir en los siguientes puntos: Alta productividad y calidad. Soldadura de espesores desde 0,7 a 6 mm.
84. ¿Qué diámetro de alambre se utiliza según espesor de materia base?
Los hilos macizos tienen normalmente la misma composición que el material base, con el añadido de elementos que pueden ayudar en la limpieza del material base. Los diámetros de empleo más común son 0,6 - 0,8 - 0,9 - 1 - 1,2 - 1,6 mm.
85. ¿Cuáles son las diferencias de soldeo con alambres sólidos y tubulares?
Alambres sólidos: son indicados para aceros al bajo carbono, no dejan escoria sobre el cordón y el enfriamiento es rápido, por lo que su principal aplicación son los materiales de poco espesor.
Alambres tubulares: se comportan de modo similar a los electrodos revestidos.
86. Las ventajas y desventajas de soldadura Mig más representativas son:
Ventajas:
Se puede soldar en todas las posiciones.
Buena apariencia o acabado (pocos salpicados).
Poca formación de gases contaminantes y tóxicos.
Soldadura de espesores desde 0,7 a 6 mm sin preparación de bordes.
Proceso semiautomático o automáticos.
Alta productividad o alta tasa de metal adicionado.
Las principales bondades de este proceso son la alta productividad y excelente calidad
Desventajas:
El equipo es más costoso que un SMAW. Inversión inicial alta.
El equipo es más complejo y requiere mayor mantenimiento.
Cambiar de material base en algunos casos requiere compra de equipo adicional.
Producir en campo (fuera de taller) es difícil debido a que las condiciones climatológicas (aire), afectan al gas de prot a. Unión a tope: Es la más utilizada y consiste en unir las chapas situadas en el mismo plano para chapas superiores a 6 mm o para soldar por ambos lados, hay que preparar los bordes. El objetivo de esta soldadura es conseguir una penetración completa y que constituya una transición lo más perfecta posible entre los elementos soldados. b. Unión en ángulo: Consiste en unir dos chapas situadas en distinto plano bien ortogonales o superpuestas, para rellenar los bordes de las placas creadas mediante uniones de esquina, sobrepuestas y en T.
87. ¿Por qué es importante las uniones de soldadura Mig?
Las uniones de soldadura mig, nos permite unir piezas de manera más fácil y precisa, en cualquier tipo de posición manteniendo un mejor acabado a la hora de soldar.
88. ¿Qué diferencias existen entre unión a tope y unión en ángulo?
89. ¿Qué criterios tener en cuenta para emplear uniones de soldadura Mig?
Uno de los atractivos de la soldadura MIG (Soldadura por Arco con Gas Protector Inerte/Activo, respectivamente) es la facilidad para aprenderla. Con un poco de instrucción, prácticamente cualquier persona puede soldar mediante MIG tras unas horas de práctica. De hecho, cuanto más se practique, más fácil será y mejores serán las soldaduras. Sin embargo, antes de confiarnos demasiado en nuestras soldaduras, es conveniente que cortemos un cordón que hemos hecho para comprobar la penetración y otras características que nos informarán si la soldadura es tan fuerte como su aspecto.
Para poner a punto nuestro equipo MIG y comenzar a soldar de modo eficiente, el primer paso será leer todas las instrucciones y precauciones incluidas en el correspondiente manual del usuario. Le recomendamos repasar brevemente los componentes de un equipo de soldadura MIG, a fin de tener en claro lo que debemos hacer. Una vez que estamos familiarizados con los componentes de nuestro equipo y que hemos elegido el tipo de gas y el tipo de alambre a utilizar, vamos a prestar especial atención a una serie de parámetros clave que debemos ajustar para obtener una soldadura de calidad. También debemos tener en cuenta el flujo o caudal de gas protector (depende del material y del alambre utilizado), la longitud del extremo libre del alambre y la velocidad de soldeo.
90. ¿Por qué razones se prepara uniones con bisel?
Se suele emplear frecuentemente para la soldadura en chapas de espesores pequeños medianos, y los sectores que más la emplean son los de construcción naval, fabricantes de componentes ferroviarios y tubería. Es casi obligado utilizar este tipo de bisel cuando sólo se puede soldar la pieza, por un lado.
91. Las diferencias más representativas de posición de pistola y desplazamiento de cordón son: a. Posición de la pistola: La que más se recomienda es la posición horizontal o casi horizontal, ya que permite un mejor control del charco, pueden obtenerse cordones lisos y de buen aspecto y optimiza la acción del gas protector sobre el charco. b. Desplazamiento: En la soldadura MIG/MAG existen dos modos de desplazamiento de la pistola: a. Unión a tope: Son las más ampliamente usadas en todos los métodos de soldadura, puesto que cuando se sueldan producen un bajo índice de tensiones y deformaciones. Las uniones a tope, por lo general, se utilizan en las construcciones de chapas de metal. Esas uniones implican un gasto menor de metal base y de metal de aportación, así como también un tiempo más corto en la terminación de los trabajos de soldadura. Puede n ser ejecutadas con una resistencia igual a la del metal base. No obstante, para la elaboración de las uniones a tope se exige una preparación más adecuada de las piezas. Si se ejecuta a mano la soldadura de chapas metálicas de 4-8 mm de espesor, los bordes pueden ser rectos (o sea sin ninguna preparación). En este caso las chapas se colocan con una holgura de 1-2 mm. Podemos soldar a tope y por un solo lado, sin preparación de los bordes, las chapas cuyo espesor sea de hasta 3 mm; para la soldadura bilateral ese espesor puede ser de hasta 8 mm. Las planchas con un espesor de 4-26 milímetro, se unen a tope con biselado unilateral de los bordes cuando se les aplica el procedimiento de soldadura manual por arco. Este tipo de preparación de los bordes se denomina en V. Las láminas con un espesor de 12 a 40 mmm y más se sueldan previo biselado bilateral de los bordes, denominado en X. b. Unión a solapado: Tienen sus ventajas cuando se ejecuta la soldadura por arco eléctrico de estructuras de construcción fabricadas de chapas cuyo espesor no sea mayor de 10-12 mm. Estas planchas no requieren que sus bordes sean especialmente elaborados. Durante tales uniones se recomienda soldar por las dos caras, puesto que si efectuáramos la soldadura por una sola cara pudiera ocurrir que la humedad se filtrase entre la hendidura de las piezas, con la posterior oxidación del metal en ese sitio. c. Unión en T: Se usan ampliamente en la soldadura por arco y se efectúan con o sin preparación de los bordes de una cara o de las dos caras. La plancha vertical debe tener el borde base bien elaborado. Cuando los bordes de la plancha vertical se biselan por una o ambas caras, entre las piezas horizontal y vertical se deja una holgura de 2-3 mm para obtener una buena penetración en todo el espesor de la pieza vertical. El bisel en una sola cara se realiza en caso de que la construcción de la pieza no permita efectuar la soldadura en T por los dos lados. d. Unión en ángulos: Se usan para la soldadura de diferentes planchas cuyos bordes se han elaborado previamente. Las partes a soldar se colocan en ángulo recto o en otro ángulo y se sueldan por los bordes. Tales uniones se usan generalmente en la soladura de depósitos, los cuales habrán de ser sometidos a condiciones de trabajo, bajo la acción de una presión no conocida de gas o líquido. A veces las uniones en ángulo se sueldo.
A izquierda: el movimiento de la pistola va de derecha a izquierda.
A derecha: el movimiento de la pistola va de izquierda a derecha.
Estas variables dependen del material y del espesor de la pieza a soldar. Para soldar acero o metales similares, la dirección de soldadura no es relevante, pero para soldar aluminio debe emplearse el método “a izquierda”.
92. Describa la diferencia de soldeo por arco eléctrico aplicando uniones con soldadura Mig.
93.¿Por qué las uniones efectuadas resultan defectuosas por las posiciones de soldeo?
Al momento de soldar, se debe buscar una posición en la que el soldador no tenga incomodidad o problemas y que le sea favorable mantener su pulso, evitando inconvenientes.
94.
Parámetros:
Encendido en 1 o 2 En 1, debido a que el material tiene 4mm de espesor.
Voltaje Entre 18 – 20.
Velocidad de alambre En 1.
Flujo de gas En 6 o 8.
95.Proponer los parámetros de soldeo mag posición 1g de acero al carbono espesor 6 mm de platina
Parámetros:
Encendido en 1 o 2 En 2, el material es mayor a 4mm de espesor.
Voltaje Entre 25 – 30.
Velocidad de alambre En 3 o 4.
Flujo de gas En 12 o 15.
96.¿Por qué es importante los ángulos de inclinación al mover la antorcha durante el soldeo?
Es importante el ángulo de inclinación, para tener una unión mejor e uniforme. Para que abarque ambas piezas.
97.Proponer los parámetros de soldeo mig posición 2g de acero al carbono espesor de platina 8 mm.
Parámetros:
Encendido en 1 o 2 En 2, el material es mayor a 4mm de espesor.
Voltaje Entre 30 – 35.
Velocidad de alambre Entre 4 - 5.
Flujo de gas En 15 - 18.
98.Proponer los parámetros de soldeo mag posición 2f de acero al carbono espesor 10 mm de platina.
Parámetros:
Encendido en 1 o 2 En 2, el material es mayor a 4mm de espesor.
Voltaje Entre 35 – 38.
Velocidad de alambre Entre 5 - 6.
Flujo de gas En 18 - 20.
99. ¿Para soldeo de acero al carbono es más recomendable emplear gas CO2 o Argón, por qué?
El programa de soldadura de aceros al carbono, con CO2 como gas de protección, se recomienda para el soldeo de aceros al carbono en aplicaciones con gran penetración y elevadas velocidades de aportación.
El mejor atributo del CO2 es que se trata de un gas de penetración profunda, razón por la cual es incluido en las mezclas la mayoría de las veces. Soldar con argón puro produce un arco concentrado y enfocado, lo que resulta en un perfil angosto y una penetración profunda. El perfil de cordón generalmente tiene un pico más alto en el centro de la soldadura con mejor impregnación en los bordes en comparación con el CO2. El argón es el estándar para soldadura por arco de tungsteno con gas (GTAW). Sin embargo, en la GMAW se usa argón junto con otros gases.
100. El proceso de soldeo Mig Mag necesita más elementos, los cuales son a comparación de soldeo por arco y electrodo revestido.
MIG MAG: ELECTRODO REVESTIDO
Gas protector (argón, helio, co2)
Alambre macizó
Fuente de alimentación.
Pistola.
Electrodo revestido.
Fuente de alimentación.
Porta electrodo.
101. ¿Por qué la posición 3g en Mig mag se emplea para calificar soldadores y Homologación?
La homologación, se trata de un acuerdo internacional limitado y estipulado bajo ciertas normativas que deben ser respetadas y que listan las habilidades que una persona debe cumplimentar para certificarse o matricularse con ciertas habilidades de soldadura.
En la posición 3G, califica para soldar en las posiciones 1F, 2F, 3F y las posiciones 1G, 2G, 3G en acero estructural.