
14 minute read
View From There
From farm boy to Water Pumping Institute: what makes me tick
Advertisement
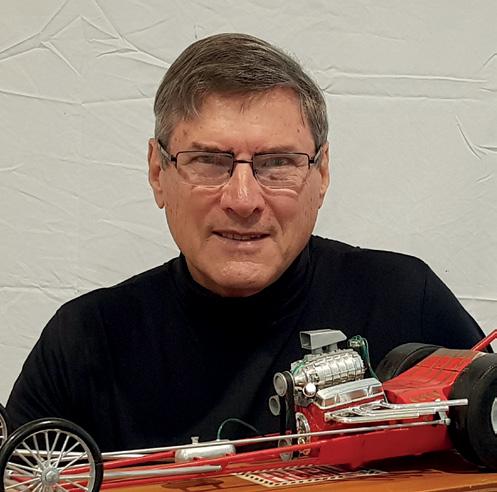
Robert Welke Managing Director
Water Pumping Institute Adelaide, South Australia
CHILDHOOD
It’s been said that our childhood years mould what we become in later life. This was especially so in my case. I grew up in the postWWII years on a 300hectare mixed farm in midnorth South Australia (SA). My father was very innovative, and every piece of machinery that was purchased for our farm went through his “how can we make this do its job better?” process. Hence, right from a young age, I learned to challenge the status quo and come up with improvements; to make a thing more fit for purpose. I also learned that some manufactured products hit the marketplace without being properly tested.
Robert Welke has 54 years’ experience in water pumping and hydraulics and is an energy efficiency consultant and teacher, principally in the irrigation industry.
As a result of this approach I learned mechanical engineering skills, and by ten years old I was welding, cutting, filing, and soldering in the farm workshop. My father bought me and my two brothers an automotive encyclopedia, straight from Detroit, USA. I studied this with great interest in my teenage years, hence I became a petrolhead in the US muscle car era, purely out of mechanical marvel.
ATTENTION TO DETAIL
The attention to detail developed in my formative years had great influence in my later years. It is epitomised by the model dragster I built when I was 16 years old. It was based on a commercially available plastic Chevy 283 Engine Kit, and I built the rest from what I could scavenge on the farm. This 60cm long model was reverse engineered from photos of
American race car driver Don Garlits’ Swamp Rat, “Big Daddy”.
SETBACK
I have learned that setbacks in life are merely opportunities to change direction and improve one’s life.
I attended boarding college and went on to study for a Mechanical Engineering degree in Adelaide. My first real setback was that in 1967, during my second year at South Australia Institute of Technology (now UniSA), Australian university textbooks changed from imperial measurement to metric. I found that extremely disruptive and dropped out of degree studies at that point. I did later master metric measurement, which I now consider much better than imperial!
I went from adversity to opportunity by joining a fitting and turning apprenticeship, provided by Commonwealth Employment Services (CES). This cemented and improved my existing mechanical skills to a professional level. The interesting part is how this apprenticeship materialised. Given my degree studies background, the CES officer skipped the usual apprenticeship application process, and I commenced with the Engineering and Water Supply Department (now SA Water) the week after that interview in February 1969.
My career for the next 25 years was handed to me on a platter, without me even choosing who my employer was to be. I merely made the most of it!
BIG BREAK – ENERGY EFFICIENCY ROLE
Upon completion of my threeyear (quick release) apprenticeship in January 1971, I was interviewed and given a choice of two roles within SA Water’s engineering staff; either drafting in the sewage branch, or assistant to the pumping engineer in the water supply department. I chose the latter with enthusiasm!
This was the first of the most amazing career opportunities I could hope for. South Australia is the driest state of the driest continent in the world, and I was responsible for monitoring the energy efficiency of SA’s extensive pumping and pipeline systems.. This involved efficiency testing of pumps up to 5,700 kW and pipelines up to 1.6m diameter. All of the expertise garnered in these times has been incorporated into Water Pumping Institute’s present training course, Pumping System Master Class.
PIPELINE EFFICIENCY TESTING
I quickly learned that it was NOT just the pumps that determined pumping system energy efficiency. Pipelines have more influence on pumping system efficiency. My role included regular HazenWilliams coefficient (C) value tests on major pipeline systems.
As a result of interesting site test results, my passion grew for pumping hydraulics, which is my number one specialty today. This is reflected in my Pumping System Master Class course material.
SA Water had a hydraulics section, and I frequently found myself spending time there picking the brains of the best hydraulic engineers in the country.
In the 1980s I was given the task of identifying the cause of significant friction
losses in about 20 kilometres of 80mm nominal bore (NB) cast iron pipe which was supplying stock water in the Loxton Country Lands area. These pipes were originally laid in the 1930s as unlined cast iron pipe. In the 1960s they were cleaned and cement lined insitu to extend their life.
My tests identified that a short section of cement lining had detached at the point where stock water flow meters were attached to the pipe after cement lining.
My recommendations resulted in 1m sections of pipe being replaced in about 12 places. This restored the pipeline’s original performance for a cost of about $10,000, staving off a possible $500,000 capital replacement.
MOTOR VEHICLE ENERGY EFFICIENCY
Occasionally I was taken off pump monitoring duties and given other interesting tasks. In the late 70s the world was going through an energy crisis and dealing with rising fuel costs. The SA Premier, the late Don Dunstan, decreed that all SA government departments would reduce their vehicle fleet fuel consumption by 10 percent.
The technical side of that task fell to SA’s largest government department, SA Water, because of its abundant resources. A technical committee was established, and I became the Committee Technical Officer, gathering data. I equipped a modern fleet car with stateoftheart fuel economy monitoring equipment
and headed to a straight, flat country road. I performed vehicle energy efficiency tests with parameters such as varying tire pressure, windows up vs windows down, removal of radiator fan and sun visors. I had a ball, and quickly came up with recommendations which identified where the 10 percent could be saved, which were ratified by our department head. (Refer to SA Water Report Motor Vehicle Fuel Efficiency Test, 1979 EWS 4505/79.)
This period of my career ignited an energy efficiency fire in me, and I have gone on to develop and apply these principles in all areas of my life.
FLOW METERS
I have a passion for flow metering of water.
My first experience with flow meters was in February 1971, when I assisted the pumping engineer with the commissioning of a 68" (1.7m diameter) magnetic flow meter for the Happy Valley outlet at Darlington. I was responsible for measuring the rate of change in water level of the four calibrated water tanks into which the metered water discharged.
The results showed that the flow meter was measuring at 30 percent slower than expected. I was astounded. This was my first exposure to water supply flow meter industry standards. That exercise resulted in half a dozen top engineers flying out from the UK, where the meter was manufactured, to observe this apparently unexpected performance, and make adjustments.
This reminded me of the poorly designed agricultural equipment my dad bought for the farm, and working on it to improve its performance.
From that day onward I have always checked the performance of new equipment as part of a commissioning process, never entrusting accuracy or performance to the supplying company. Such site commissioning results are included in a large database of equipment performance faux pas, many of which are referenced in my training courses as examples of what to look out for.
In 1975 I got to test another brand new flow meter. This one was a water leakage flow meter, designed to measure very low flow rates caused by leakage in water distribution systems. I checked this one in our Kent Town Workshops. It tested at 25 percent fast. This did not surprise me.
In the 1980s I was given technical responsibility for the 2,600 water diversion flow meters which SA Water used to measure diversion flows to irrigators from the Murray River or proclaimed area aquifers.
This came at a time when bore water from the Northern Adelaide Plains Aquifer was being metered for the first time. I set up a test rig at the National Association of Testing Authorities (NATA) approved test facilities at Ottaway Workshops to evaluate a 100NB propeller actuated flow meter commonly used for diversion metering. This meter was supposed to be accurate with 10 diameters of upstream pipework, but my tests indicated that this could never be achieved, and this flowmeter was subsequently withdrawn from service. (These tests are documented in my report Guidelines for flowmeter rehabilitation in the Northern Adelaide Plains, EWS 2122/80, June 1989.)
Such are my experiences with flow meters that to this day flow metering is one of my passions. Flow metering forms an important part of the content in the Pumping System Master Class, which emphasises how to accurately measure flow when testing pumps.

Robert regularly tested pumps ranging from 100kW up to these 5,670kW units on the Murray Bridge Onkaparinga Pipeline. This 825/675 single stage pump lifts 1,970 l/s at 201m head.
A NEW ERA
After 25 years of absolutely amazing work experiences my days with SA Water ultimately ended as the department downsized in the early 1990s.
I rescued myself from adversity by joining the irrigation industry in 1994. Initially I was technical officer of engineering for an original equipment manufacturer (OEM) company
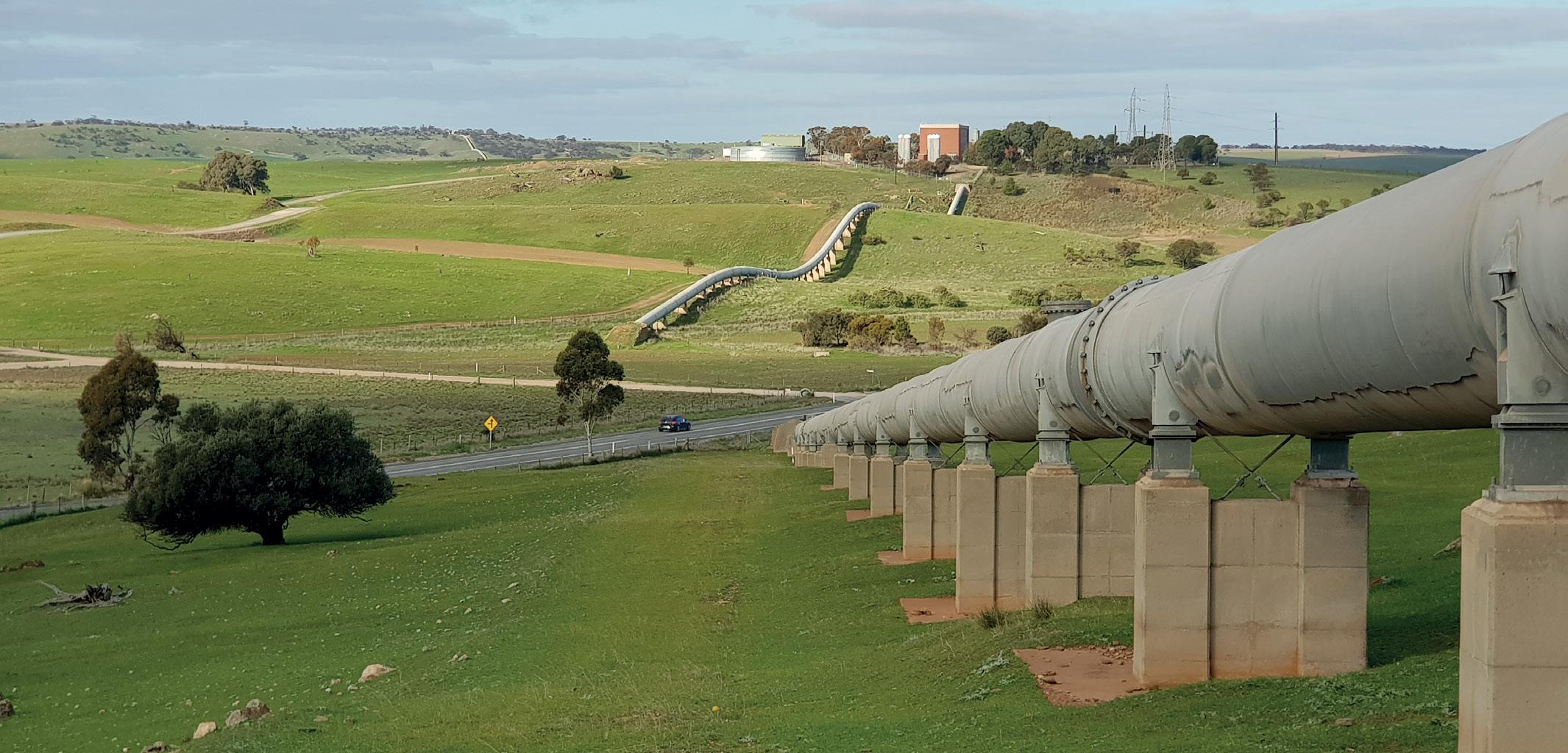
Robert regularly friction tested major pipelines such as this pipe on the Murray Bridge Onkaparinga Pipeline system. Biofilm caused significant performance reduction over time, fixed with periodic chlorination.
designing and building packaged pump systems for the turf, agriculture, horticulture, and viticulture industries.
This was a real culture shock to me. I had grown up with engineered schemes designed to last 100 years, and now I was being asked to design for 10 years. I was able to bring a wealth of knowledge from SA Water, but the reality was that the irrigation industry didn’t want to pay for it!
I got used to the lower engineering standards of the irrigation industry, but have never accepted them. Over time I designed and built nearly 100 package pump stations, some of which I got to site commission in various places all over Australia and the Pacific Islands.
CHALLENGES BUILD CHARACTER
I had some good wins for this OEM, as well as some bad experiences. It’s the bad experiences which cause us to grow and improve the most. Like when a 300NB rubber expansion joint I designed into a dry well pump station failed after two years, and flooded the pumping station, putting three 175 kW Super Titan pumps and motors under water!
Rubber expansion joints exemplify the lower engineering standards of the irrigation industry. I later learned how to manufacture custombuilt stainless steel flexible restrained dismantling joints and promote them to the irrigation industry, mainly through the Pumping System Master Class.
On another occasion, I was called out to
one of our irrigation pump stations that had two 175kW pumps on variablefrequency drives (VFDs). A pressure fitting was leaking. Being New Year’s Eve in a country town, only Mitre 10 was open, so I was restricted to replacing the fitting with a poly fitting. Two days later that fitting failed completely, spraying the inside of the pump station with a high pressure jet into the roof, deflecting off into a fine spray, and killing both the 175kW VFDs.
Someone found the renegade fitting and attached it to my office desk pin board with the words, “Rob’s $10,000 fitting”. I wasn’t fired for that, but I must surely have tested the boss’s limits! I never lived it down, but as a result, I raised my standards.
A DEFINING MOMENT IN MY CAREER
Due to our OEM’s largest client going into liquidation, our company went down with them in late 1999, again throwing me into the employment marketplace. Along came the knight in shining armour, a gentleman from Hydroplan named John Gransbury.
John had designed a 450NB pumping system for the Willunga Basin Water Company, pumping recycled water to vineyards. After 18 months the pumping system was discharging 15 percent less water. He had tested the pumps and found them to be OK. He phoned me out of the blue, knowing I had SA Water roots and good hydraulics analysis skills, and asked if I would do a friction test on the pipeline. I found that the 10km of pipeline had a biofilm issue which decreased
the HazenWilliams coefficient value to 135, resulting in 15 percent decreased output. We pigged the pipeline and restored the pumping capacity.
Now I found that my SA Water experience had helped me to contribute and add value to the irrigation industry in ways I had never thought possible, and in ways which I enjoyed. Shortly after that, John asked me to work for Hydroplan, which I did for three years, mainly on pumping and pipeline systems. John taught me how to use EPANET, software used to model water distribution systems, which I still use today for more complex hydraulic analyses.
A SEA CHANGE
In 2003 my wife Sandy and I moved from Adelaide to coastal Queensland and established Tallemenco Pty Ltd as an independent consulting business. I subcontracted to a couple of firms, mostly in irrigation system auditing roles. Most of my work involved troubleshooting problematic irrigation systems.
I developed pressure and flow data loggers which I used to analyse pumping and distribution system issues in detail. This helped me to identify problems and determine their cause.
Nothing had prepared me for what I found. After working on SA Water distribution systems, I found the standards of the irrigation industry to be appalling. Every system I audited revealed substandard pump systems and underperforming pipe systems, most often with too small a diameter. And it wasn’t
just irrigation designers that were performing poorly, but also hydraulics engineers.
CRISES BRINGING
ABOUT CHANGE
After a run of productive years in systems analysis, the September 2008 Global Financial Crisis (GFC) changed the whole world, and as money around the world dried up, so did consulting work. On top of that there were two floods and a drought in South East Queensland. I had to diversify my income stream.
Once again, I turned adversity into advantage. With little paid work available, I spent time developing a training course. Armed with my SA Water pumping and hydraulics skills and seeing the appalling state of the irrigation design industry, I wanted to contribute to improving the irrigation industry.
I developed the twoday Advanced Pumping & Hydraulics training course over a period of around 700 hours, using my own material and resources. Much of the resources were photos taken during my SA Water days. Assisted by River Murray Training, I began teaching this course online to irrigation
personnel throughout Australia.
I was enthused by the course feedback, which encouraged me to continue, and I continuously refined the course over several years.
A NEW OPPORTUNITY
In 2012 my wife and I pulled stumps in Queensland, sold up, and relocated to South Australia. I fell on my feet, with work coming from all directions. It was good to be back home!
I continued to run Advanced Pumping & Hydraulics training courses online. However, the age of energy efficiency (something I’d been implementing for 40 years) was now approaching, as shown by the Australian Federal Government offering rebates for energy audits in 2012.
My first project was energy audits for the abalone industry. Applying all I’d learned both in SA Water and the irrigation industry, I saved a number of abalone farms over $500,000 in annual pumping electricity costs in my first three years back in SA.
In 2015 I took a phone call from a stranger; John Hayes in New Zealand. He
wanted to know if I would train his clients in pumping and hydraulics. I asked what he wanted, he spelled it out, and the Pumping System Master Class was born. This course is like the Advanced Pumping & Hydraulics course on steroids! Its main theme is pumping system energy efficiency, otherwise known as sustainable irrigation pumping.
In 2021, after 50 years practicing as a paraprofessional mechanical engineer, I founded the Water Pumping Institute, an establishment which utilises my wealth of knowledge and experience in the water pumping and hydraulics world.
The Pumping System Master Class continues to be the most respected pumping training course in the irrigation industry, and has now reached over 650 people in Australia, New Zealand, the USA, Europe and South Africa.
At the end of the course, most people say it changes the way they see pumping systems. When I hear that, I feel content that I’ve helped another person in the irrigation industry to see pumping systems how they really are, with the benefit of my practical experience, successes, failures, and adversities.