
10 minute read
INNOVATIONS: PRESENT&FUTURE
Front Line Maintenance
Aneesha Kaur Sachdev,
Zingametall Singapore PTE LTD – Singapore info@zinga.com.sg
Front Line Maintenance (FLM) is the preservation of tools and assets in a company in order to allow operations to continually run smooth transactions and avoidance of major hinderances. FLM is more convoluted than other forms of maintenance since it requires maintenance crews to fix issues whilst the assets are in use [2]. An example of FLM in application is when trains in metro stations are delayed due to maintenance issues. In order to increase profitability and availability of services with steady operations, workers have to adhere to strict guidelines and training courses for the best FLM practices. For the purposes of this article, Front Line Maintenance (FLM) will be mostly associated to the Oil and Gas industry unless stated otherwise.
Performance improvement
Narayanan, Wardhaugh and Das (2021) stipulate that the improvement of performance in the realms of maintenance works hangs in the balance between both efficiency and execution. In other words, teams have to plan accordingly under strict timelines and scheduling along with constructive resource administration and allocation. Findings on performance benchmarking of refinery or plant operators conclude that their time is being mismanaged, and around 25% of it should be appointed to maintenance efforts. Workers should be able to find and fix issues like corrosion in equipment as early as possible to increase productivity.
Safety
Safety is usually a top priority for FLM in the Oil and Gas industry – especially in marine and offshore worksites. Frontline workers have to be “responsible for managing process safety and other risks in their hazardous workplaces,” [6] with the use of either their own knowledge or others’ in order to manage critical situations. Aging assets tend to pose as a threat to safety because of the “cumulative degradation” due to corroded machinery that may cause erosion and fatigue in the mechanisms – this eventually causes normalisation of deviance (complying to degraded asset conditions) [5]. Other safety barriers on assets include structural, mechanical, process and marine integrity, fire and explosions, pipelines, corrosion, human factors and others [5].
Asset life
The Oil and Gas (OG) industry requires recurring maintenance of all parts, structures and engines to ensure optimal performance of
© Zingametall © Zingametall assets. Should the performance of assets be reduced, it results in downtimes, high costs and endangerment of labourers. According to Márquez and Papaelias [8], the three types of maintenance that are undertaken for assets are “corrective”, “preventative” and “predictive” maintenance respectfully. Corrective maintenance is conducted when a failure occurs; preventative maintenance decreases the likelihood of failure when performed at specific periods according to strict criteria determined through a time-schedule or through system sensors, testing or analytics. Predictive maintenance is carried out according to the expected asset condition to avert failures. Khan, Mad, Osman and Aziz [5] claim that asset degradation factors include namely corrosion, erosion, fatigue, asset obsolescence and normalizing of substandard conditions/operations. These issues are exacerbated when there is a large amount of aging assets to maintain. The NOROG [10] mention that manipulations of fluid composition influence occurrence of corrosion in specific systems.
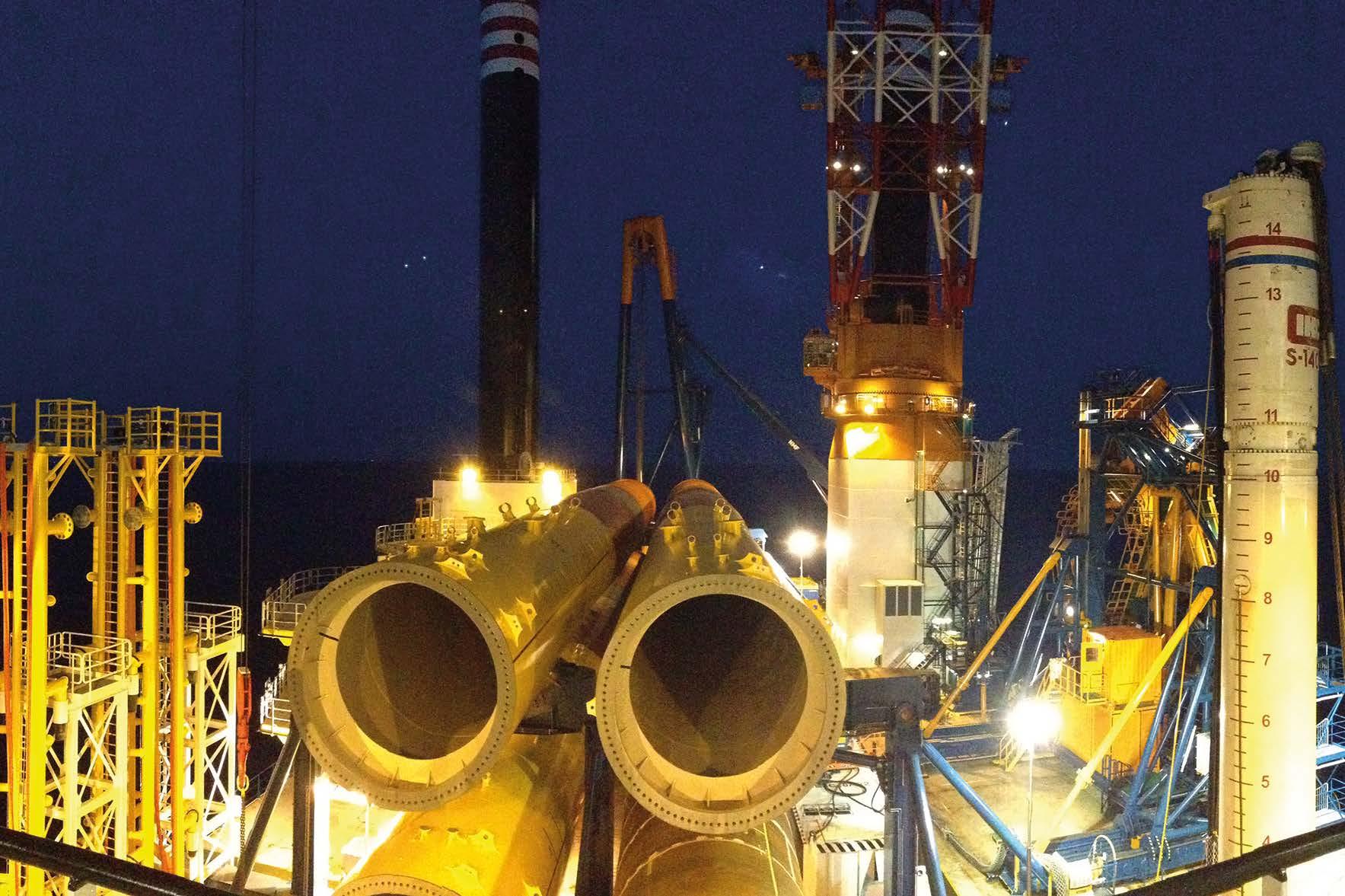
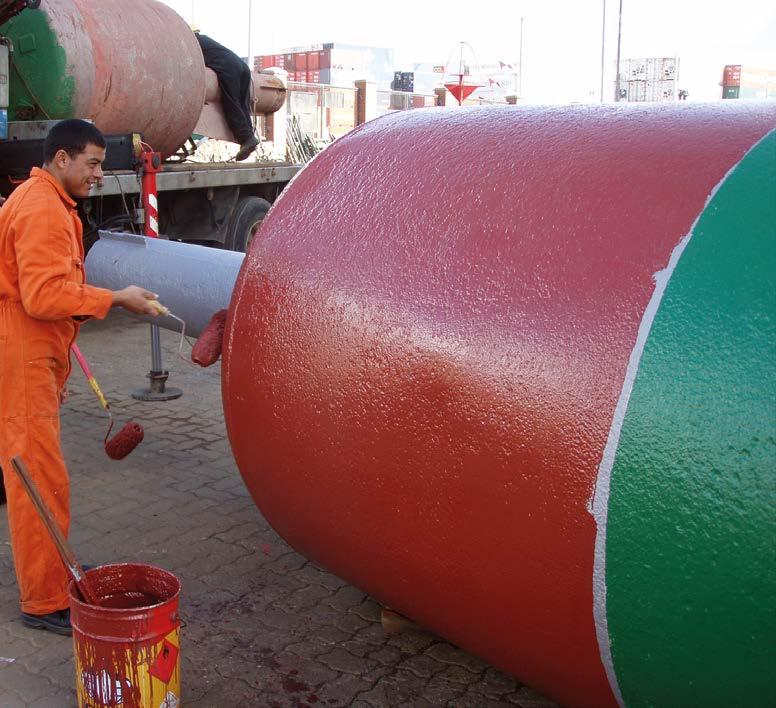
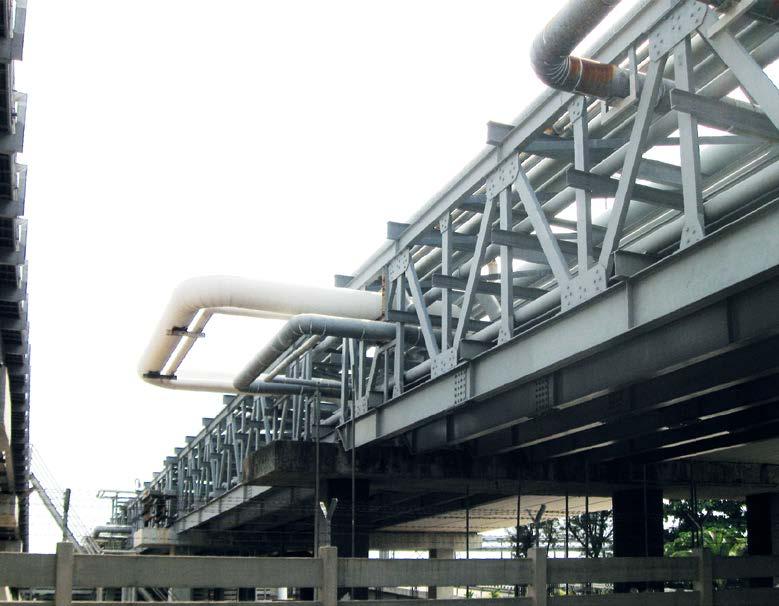
© Zingametall
© Zingametall
Hydrocarbon release
Hydrocarbons comprise of various compounds that naturally occur in crude oils like petroleum and natural gas [3]. Hydro-carbon releases (HCRs) causes major casualties in off-shore facilities and even though accidents have reduced since 1992, there are over 140 accidents occurring in a year just in the UK itself [4]. HCRs tend to be performance indicators of asset integrity management of offshore installations as they potentially herald severe accidents [1]. According to the Hydrocarbon Release Reduction Toolkit, HCRs do not occur mainly through involuntary lapses in equipment operations, but basic human error instead; in terms of designing, maintaining and operating [14]. HCRs are also caused due to corrosion in pipelines or other storage tanks and facilities mainly in the Marine and offshore institutions. In order to keep these HCRs from occurring frequently, rapid action must be taken on-site to mitigate corrosion and strengthen asset integrity.
Addressing corrosion issues
Rahuma & M. [12] specify the following; the “economic loss” in the OG industry is “extremely high” and some products used to combat it are corrosion inhibitors since they are very economical [7] and are categorized according to their chemical, cathodic, anodic or mixed nature. Inhibitors that are made in the form of coatings extend the life of an asset as they produce a protective thin film that prevents the substrate underneath from corroding. Potential of the substrate is increased when the metal “enters the passivation region” where an oxide film is created and the inhibitor reacts with the corrosive elements and removes them [11]. Compatibility with the environment, economical constraints, providing corrosion protection with minimal side-effects should be the top priority of OG companies that choose to use the coating to mitigate corrosion. In order to save on costs, the selected coating being used must be able to be applied and be
used within a short period of time to revive the asset and allow for flawless operations. Application of this coating should ideally be without the use of large equipment, excessive manpower and tools or equipment and should be applied onsite as opposed to a third-party site. In order to articulate the entire process of using such a ZINGA’s coating to address and fix corrosion issues on-site, a flowchart has been provided and can be used as a checklist when applying ZINGA onto surfaces that need corrosion protection as a corrective, preventative or predictive maintenance application. ZINGA has become a staple in the OG Industry for both upstream and downstream in Malaysia and Singapore. It has been tried, tested and proven to meet the stringent requirements to protect and preserve aging assets since 2015. Various trial tests have been conducted to validate the corrosion protection performance of ZINGA that are now implemented across the board.
Corrosion protection of ZINGA
ZINGA is a one component zinc rich coating or film galvanising system containing 96% zinc (dust) in its dry film. It is a metallic coating and not a paint. The purity of the zinc used, is so high that dry ZINGA does not contain any toxic elements. ZINGA provides active and passive protection and therefore can be applied as a paint. Active protection refers to the zinc (anode) sacrificing itself in favour of the steel substrate (cathode); where the electron flow in the circuit prevents corrosion from occurring. As for passive protection, paints and cladding create a barrier between the steel substrate and the elements that are eventually breached –that allow for corrosion to compromise the substrate beneath the coating. As for ZINGA, the zinc oxide layer and organic binders create an additional impervious barrier by blocking the zinc’s natural porosity with oxide particles. Once the barrier is breached however, the zinc will

© Zingametall

© Zingametall © Zingametall
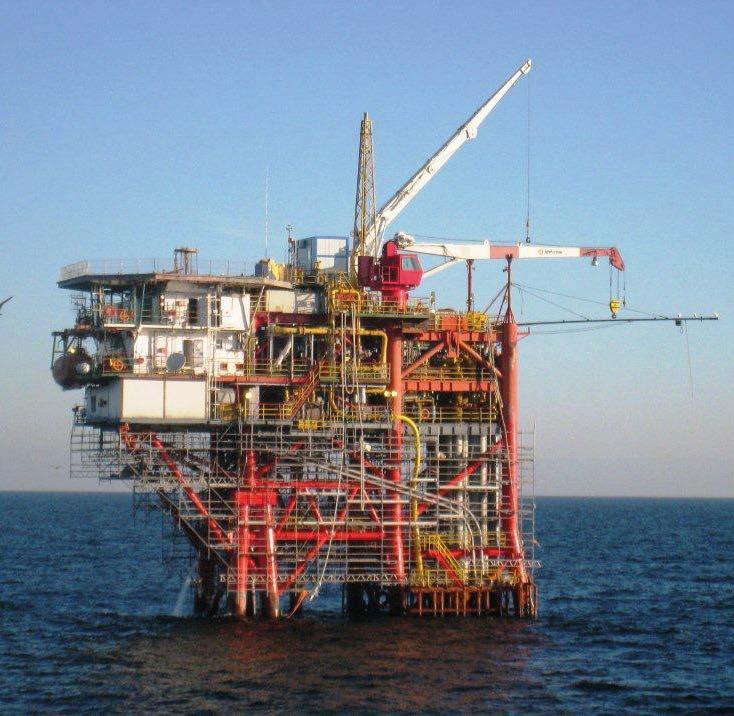
re-oxidise and will once again to provide anti-corrosive protection. ZINGA is known to be a stand-alone system as its protection standard is comparable to that of galvanization without the need for topcoats. ZINGA can be re-applied on itself with minimal surface preparation without compromising its anti-corrosive integrity.
Characteristics of ZINGA
ZINGA is known to have record drying times compared to other coatings in the industry. It is touch dry in around 10 minutes at 20 °C (40 μm DFT). It can be recoated with a new layer of ZINGA an hour after being touch dried (other paints 6 to 24 hours after touch dry). Faster system applications allow for shorter application times, less man hours and shorter close down time of assets and structures. Since the cost of equipment, personnel and cost through economical loss due to nonfunctioning of the structure is the highest of a coating project, this means ZINGA is immensely cost-effective. ZINGA can be recharged without major surface preparation – only the accumulated zinc salts need to be removed. Depending on the age of the layer, salt removal can be performed through a water wash or steam cleaning at 150 bar at 80 °C or by sweep blasting. Each new layer of ZINGA makes the former layer liquid, ensuring that the layer is homogenous. In the case of drilling or welding surfaces, the first layer of ZINGA acts as a primer and can intercept severe damages. Another ZINGA layer can be reapplies and local damages can be repaired but welding seams need to be cleaned beforehand. If the entire surface need not be coated with ZINGA, it can instead be applied on damaged spots for corrosion protection to maintain structural integrity. ZINGA happens to be fire retardant as well – which bodes well since most resources in the oil and gas industry are prone to combustion. It does not spread flames or produce toxic flames and his been tested by independent laboratories. A fire test at SGS Yarsley Technical Service (UK) found that ZINGA has a class 0 surface (best ranking) in flame spread ranking. A reaction to fire test was performed at Efectis (Netherlands) in 2013. ZINGA showed to propagation of the fire, no toxic smoke or droplets.
Conclusion
OG industry organisations are forced to continue operations despite having aging assets and having to deal with the high costs and safety risks that come with it in such a competitive and highly regulated environment. ZINGA meets these criteria for corrosion protection, safety, and productivity. It is easy to use, reduces downtime and contains non-toxic elements within the formula that allow for harmless application. This increases its economic value and provides OG companies with a viable and effective solution that can be carried out at flexible timeperiods.
The author would like to thank Rehan Ahmed (Petronas MY), Kiran Chandram (Exxonmobil SG), and Vijay Perinpanayagam (Exxonmobil MY). ‹
References
[1] Adejugba, O. (2013). How has industry achieved a significant reduction in Hydrocarbon Releases? (Masters). University of Aberdeen. [2] Brightside. (2021). What is maintenance?. Retrieved 14 October 2021, from https://www.brightknowledge.org/engineering/what-ismaintenance [3] Clark, C. (2018). What are hydrocarbons? - Gulf Coast Environmental Systems. Retrieved 16 October 2021, from http://www.gcesystems.com/ what-are-hydrocarbons/ [4] Gilroy, J., Dumolo, D., & Porter, D. (2012). Identifying the causes of hydrocarbon releases on offshore plastforms (1st ed., pp. 33-38). Rugby, Warwickshire: Institution of Chemical Engineers. [5] Khan, R., Mad, A., Osman, K., & Aziz, M. (2019). Maintenance Management of Aging Oil and Gas Facilities. Maintenance Management. doi: 10.5772/intechopen.82841 [6] Lilburne, C., Lant, P., & Hassall, M. (2021). Exploring oil and gas industry workers’ knowledge and information needs. Journal Of Loss Prevention In The Process Industries, 72, 104514. doi: 10.1016/j. jlp.2021.104514 [7] Miksic, B., Furman, A., & Kharshan, M. (2009). Effectiveness of the corrosion inhibitors for the petroleum industry under various flow conditions (pp. 1-2). NACE International, Corrosion Conference and Expo. Retrieved from https://www.cortecvci.com/Publications/Papers/ Nacereviewed/09573.pdf [8] Márquez, F., & Papaelias, M. (2020). Introductory Chapter: An Overview to Maintenance Management. Maintenance Management. doi: 10.5772/intechopen.86892 [9] Narayan, V., Wardhaugh, J., & Das, M. (2008). 100 Years of Maintenance & Reliability: Practical Lessons from Three Lifetimes at Process Plants (1st ed.). New York: Industrial Press. [10] NOROG. (2017). 122–Norwegian Oil and Gas Recommended Guidelines for the Management of Life Extension (2nd ed., pp. 9-12). Stavange: Norwegian Oil and Gas Association. [11] Popoola, L., Grema, A., Latinwo, G., Gutti, B., & Balogun, A. (2013). Corrosion problems during oil and gas production and its mitigation. International Journal Of Industrial Chemistry, 4(1), 35. doi: 10.1186/2228-5547-4-35 [12] Rahuma, M., & M, B. (2014). Corrosion in Oil and Gas Industry: A Perspective on Corrosion Inhibitors. Journal Of Material Science & Engineering, 03(03). doi: 10.4172/2169-0022.1000e110 [13] Reliabilityweb. (2021). Operators as a Maintenance Resource - Reliabilityweb. Retrieved 16 October 2021, from https://reliabilityweb. com/articles/entry/operators_as_a_maintenance_resource [14] Step Change in Safety. (2010). Hydrocarbon Release Reduction TOOLKIT (1st ed., p. 4). Aberdeen, UK: Step Change in Safety.

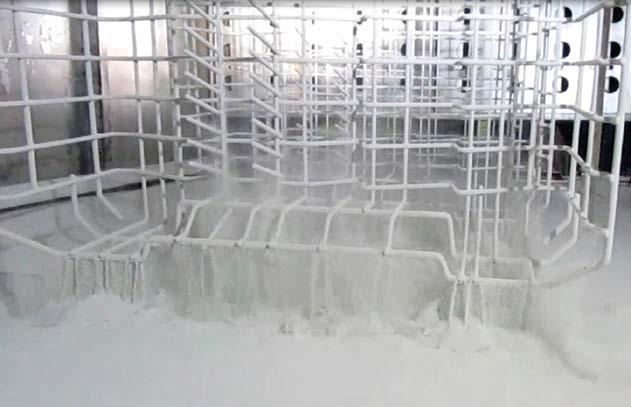
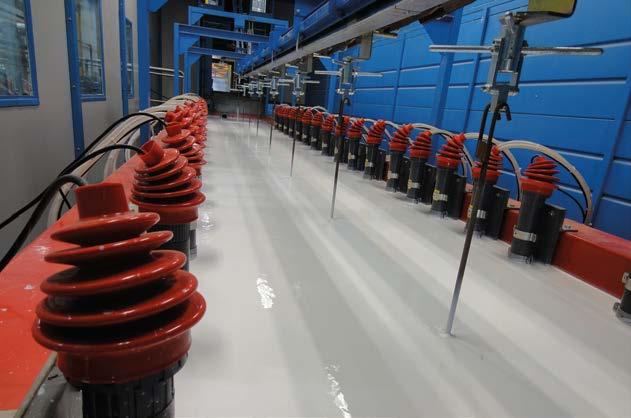

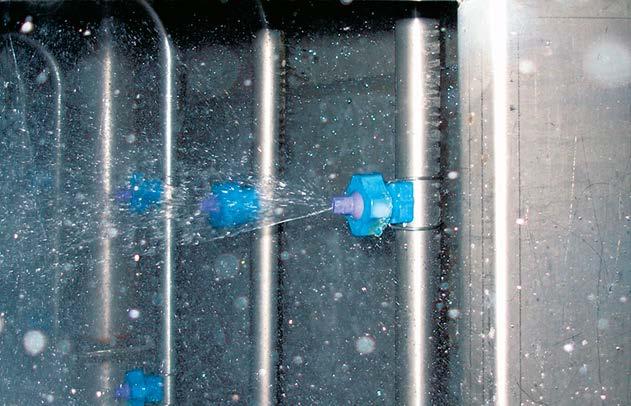
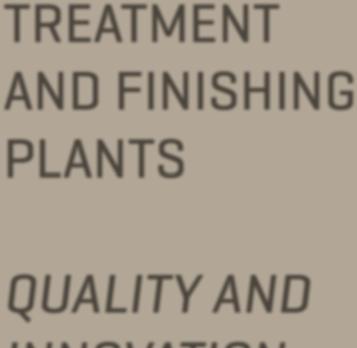
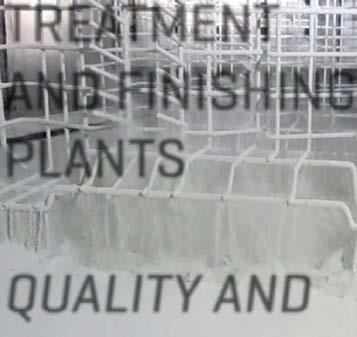