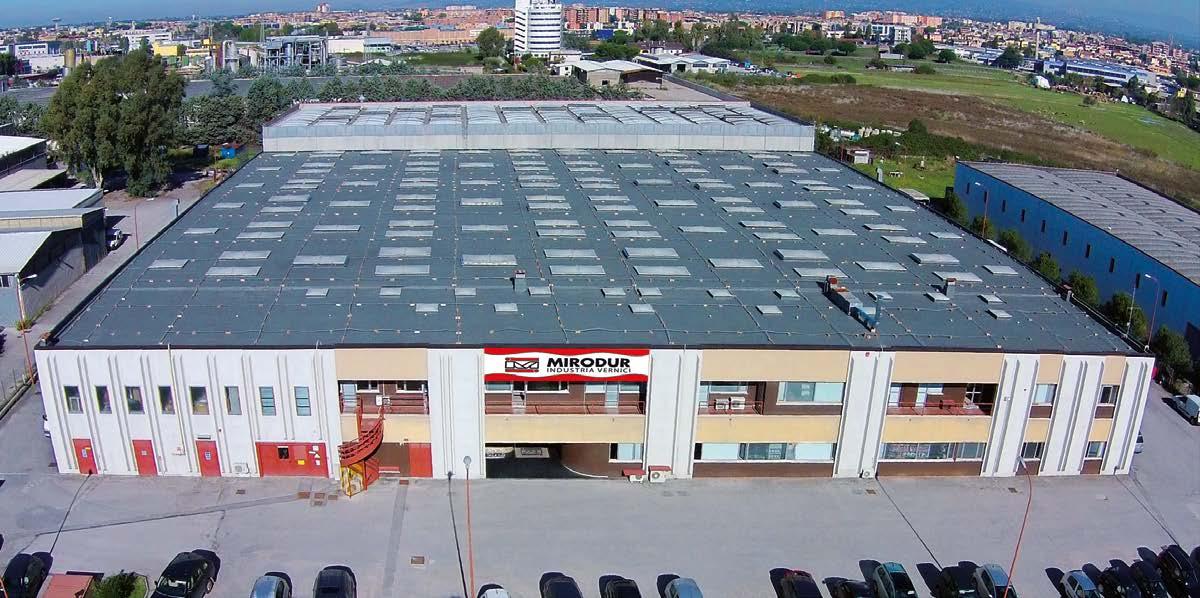
6 minute read
HIGHLIGHT OF THE MONTH
Preempting Market Needs: Mirodur’s Forward-Looking Vision
From an interview with Marco Vitelli, Massimo Vitelli, and Riccardo Vitelli
© Mirodur
Mirodur factory in Aprilia (Italy).
The world of paints and coatings has always been extremely competitive and carving out a place for one’s own company in this environment is no easy task. Italian firm Mirodur has managed to do so thanks to its ability to innovate and preempt the needs of the sector through both new technologies and new products, thus establishing itself in the international market and getting included on the vendor lists of leading companies such as Gazprom. ipcm® had the opportunity to interview two of the three generations carrying on Mirodur’s story: Marco Vitelli and Massimo Vitelli, sons of one of the company’s founders and its current directors, and Riccardo Vitelli, its marketing and communication manager, belonging to the third generation of the family.
How was Mirodur created?
Marco Vitelli: Our father, Ugo, together with his brothers Mario and Renato, founded Mirodur in 1957. They bought a patent from a Belgian company that had developed a paint used to protect mirrors. Hence the name Mirodur, from “miroir durée”, referring to the durability of mirrors guaranteed by this coating. They started producing this paint in a small factory on the outskirts of Rome and they were immediately successful, especially because this sector did not exist in Italy at the time. This opened up new growth prospects for our father and uncles, thus enabling them to move to a larger factory in Pomezia. The range of paints offered was also extended to include industrial coatings. In 1982, it became necessary to move to an even larger building in Aprilia, which is still our headquarters today. In 2016, finally, we acquired the industrial branch of Turin-based Albesiano-Sisa Rossi, bringing its production operations here to Aprilia.
How is Mirodur now?
Marco Vitelli: Nowadays, we no longer deal with the glass sector, but we specialise in industrial paints, producing water and solventbased liquid coatings for both the heavy industry and the general industry. Our production area extends over 15,000 m2, of which 8,000 m2 are covered. Besides coatings, we have developed our Miromix colour mixing systems with converters and colouring pastes of our own production. This has allowed us to collaborate with several retailers, which are increasingly crucial for the quick distribution of small batches especially at a time when all companies tend to stock less. Massimo Vitelli: Another business branch that is very important to us and that has contributed to the reputation of Mirodur is the design and production of our Turbomill devices. More than thirty years ago, we patented a paint production machine, which we decided to market in the 1980s: since then, we have sold more than 1,500 Turbomill devices in over seventy countries around the world, both to small and medium-sized firms and to multinational companies. It is an immersion mill with a patented rotating basket system: the centrifugal force created by the rotation of the basket compresses the beads and gives them greater shear force, thus ensuring excellent grinding results despite having a smaller grinding chamber than other mills. Milling and cleaning times are also shorter, bringing a significant advantage in terms of production times.
Besides product diversification, what is your main strength?
Marco Vitelli: Undoubtedly our service. Mirodur has distinguished itself in the market by its ability to fine-tune its coatings to its customers’ needs and production lines. In fact, apart from a few standard ones, we do not have a stock of finished products: our fifteen mills are used to develop ad hoc paints at the time of our customers’ requests. In order to do so, we closely cooperate with each customer from the very first moment, providing it with the know-how of our technicians to create its required product according to the time schedule and characteristics of its coating plant, the intended use of the paint, and its expected performance. Clearly, our service does not stop at the product development stage: we are also present in the subsequent phases, from the first application
Turbomill, the immersion mill with a patented rotating basket system designed and manufactured by Mirodur.
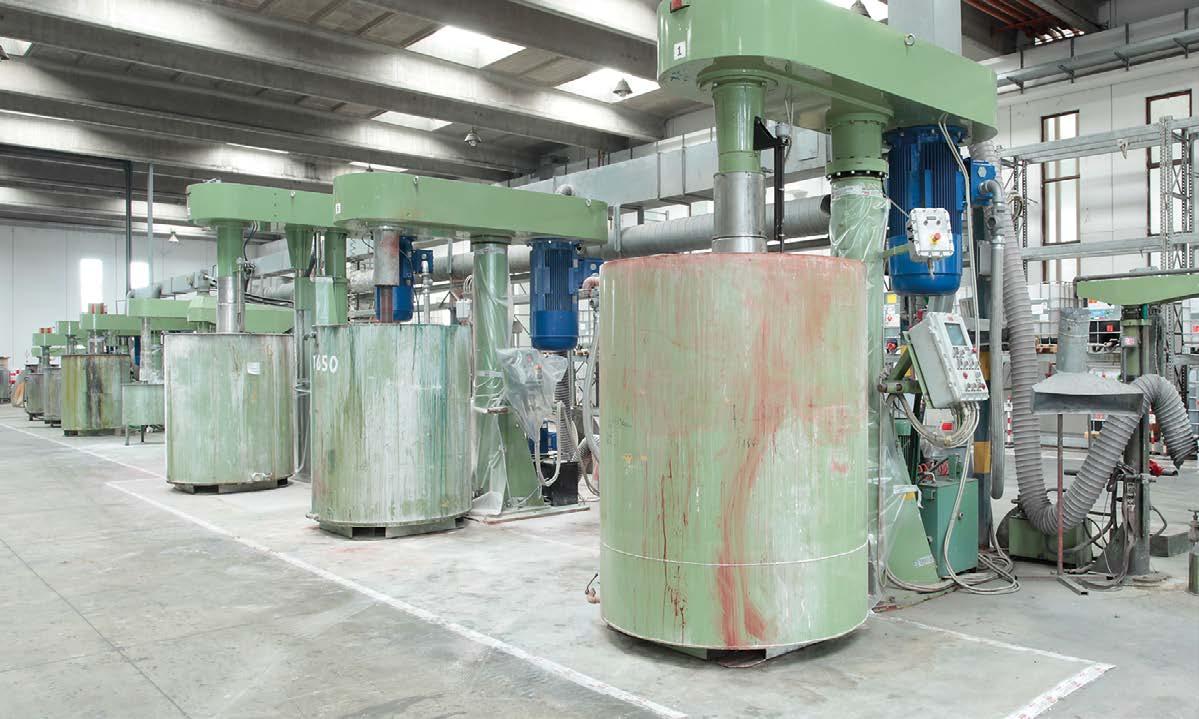
© Mirodur
Pipelines coated with an anti-friction product without solvent.
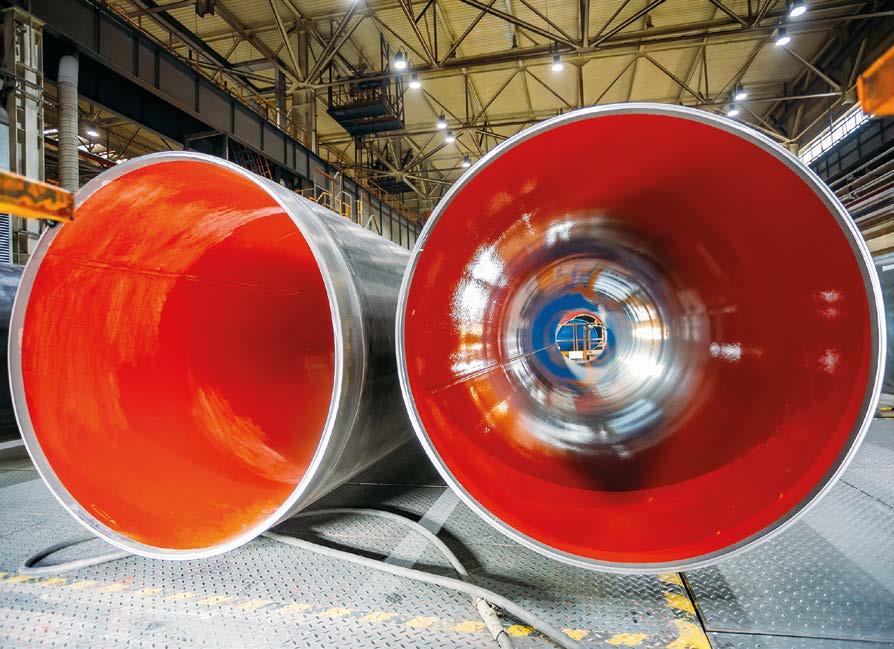
to the resolution of any problems or any emergency interventions. We manage to do all this despite being a small-to-medium sized company with thirty-five employees thanks to a very organised production and our Turbomill systems, which help cut production times.
What are your target sectors?
Massimo Vitelli: The most important sectors for our firm are those in which two-component, solvent-based or water-based, epoxy or polyurethane paints are used. We cater for both the general industry, including the ACE and earthmoving sectors, where functionality and aesthetics go hand in hand in terms of quality and performance, and the heavy industry. A particularly important sector for us is oil & gas, where we have many important customers, especially in Russia. This has led us to certify several of our products, including Epomir PTG, an ultra high-solids epoxy coating applied inside gas pipelines and approved by SNAM, Gazprom and C4Gas – an excellent calling card at the international level. We are the suppliers to two of the three largest Russian pipes manufacturers; we are still providing
© Mirodur

them with our coatings, albeit at a slower pace due to Covid-19. Marco Vitelli: Another important field is the military one. Indeed, we have developed some coatings, including finishes with special IR reflective pigments, that have been certified by the Italian Ministry of Defense Directorate General for Land Armaments for the application on vehicles of the Defense Administration. We operate also in the field of the remediation of tanks containing petroleum products, solvents or acids. We are one of the leading manufacturers of this type of paints for non-destructive remediation and this has enabled us to work with one of the largest applicators in the industry. Therefore, epoxy paints have carved out an increasingly important role in our production volumes, in addition to our wellestablished paints for the general industry.
How are you coping with the current situation, which is dominated by the pandemic and by several problems in the supply of raw materials?
Massimo Vitelli: Despite the difficult year marked by the pandemic, Mirodur has never stopped working, in fact reaching in 2020 the same turnover as 2018, after a record-breaking 2019. Currently,
© Mirodur
Hydrocarbons tanks.
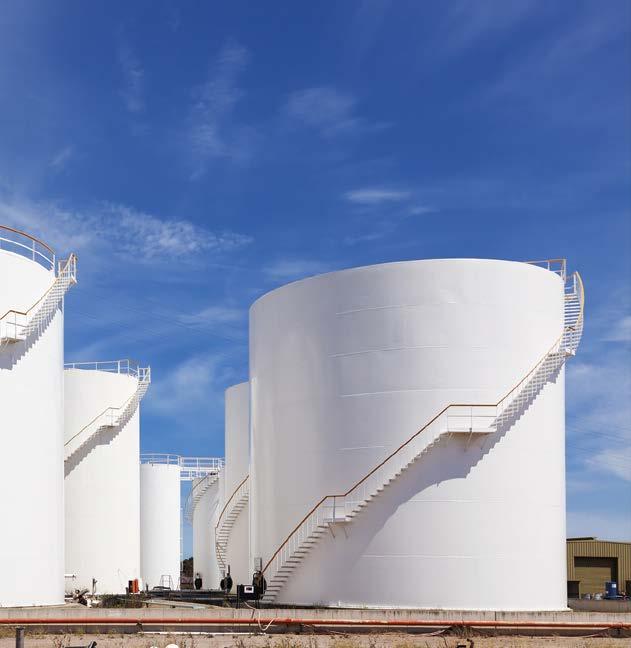

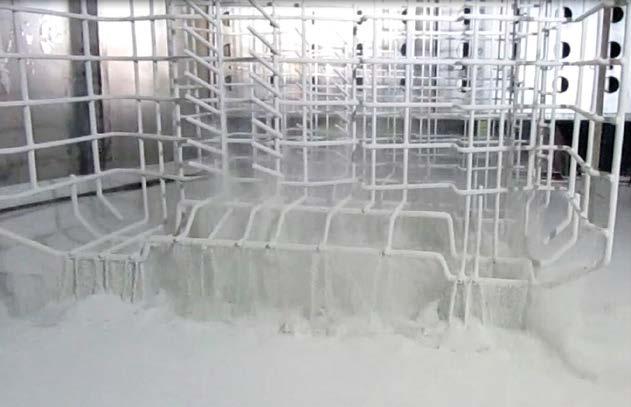
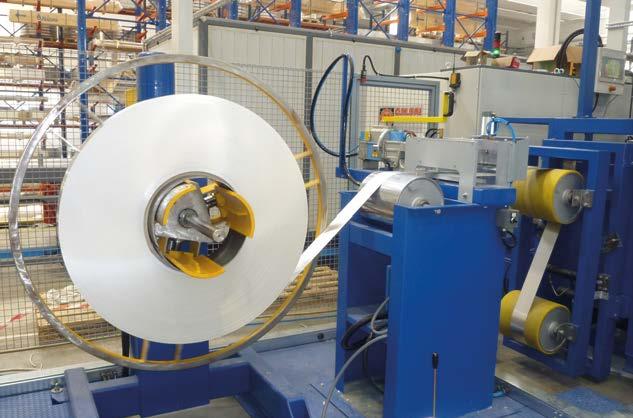
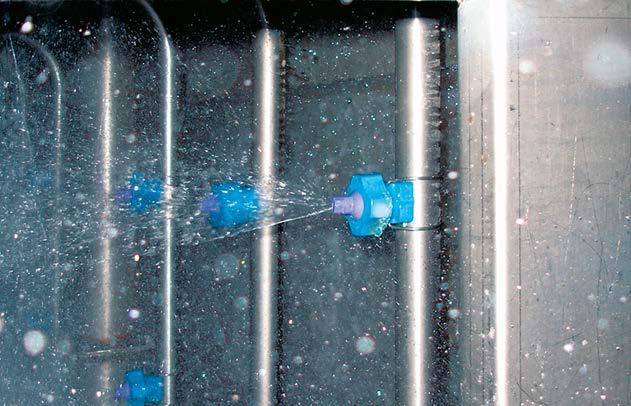
another challenge, partly triggered by Covid-19, is that of raw materials’ supply issues and rising prices. In many years of business, we have had to deal with several raw material crises, but these were limited to individual products. Now, this situation is affecting all of the more than 600 raw materials we have in our catalogue, as well as several other sectors besides coatings. This leads me to think that we will never get back to where we started. Therefore, we will need to plan production for the long term in order to be able to stock up on the raw materials that are essential to us, such as epoxy resins, isocyanates, and titanium, as well as to implement a strategy geared towards innovation and flexibility in order to be able to cope with every situation. We are trying to meet the demands of the market as much as possible and, in some cases, to preempt them, as we have done in the past with our gas pipelines paints: we were the first to make solvent-free internal flow coatings. If a company is not able to continuously renew its offer and production methods, it cannot survive. ‹
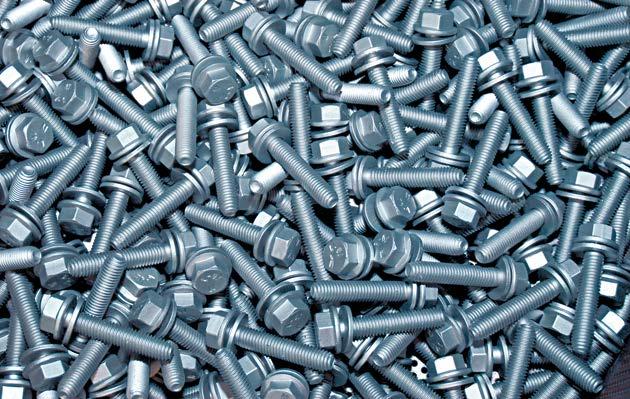
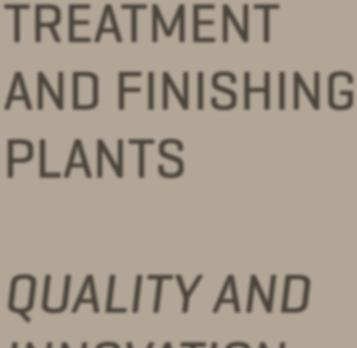
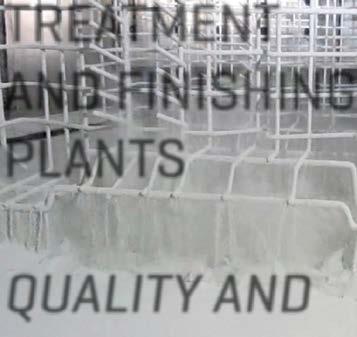