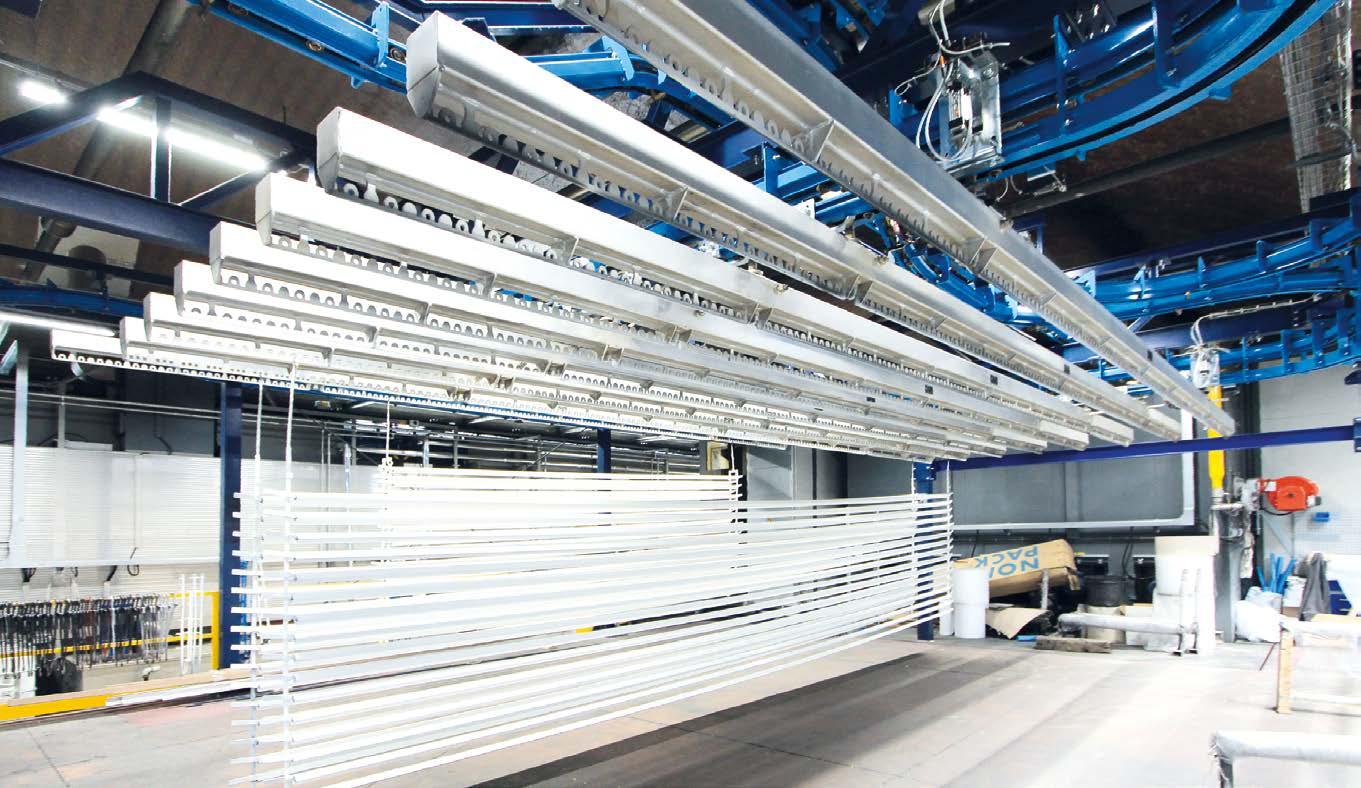
23 minute read
FOCUS ON TECHNOLOGY
VAFE festeggia 60 anni con una nuova linea di verniciatura orizzontale di profili, lamiere e accessori per architettura. Aumento della produttività grazie a una progettazione intelligente di convogliatore e impianto
Alessia Venturi, ipcm®
Qualsiasi terzista che si rispetti ha un imperativo: soddisfare tutte le richieste dei clienti senza mai fermare la linea produttiva. Ciò è ancora più imperativo per un terzista di verniciatura, soprattutto se inserito in un mercato dove è richiesta l’eccellenza qualitativa, ossia quello dell’architettura. VAFE ha trovato lo strumento tecnologico per tenere fede a questo diktat nell’impianto di verniciatura orizzontale progettato da Omsa, Futura Convogliatori Aerei e Gema, una linea che, grazie a circuiti di trasporto indipendenti con velocità di catena diverse tra loro, automazione 4.0, tunnel di pretrattamento a celle e doppio forno di polimerizzazione (uno per ciascuna cabina), fornisce a VAFE una produttività elevata senza mai fermare la linea, estrema flessibilità sia di trattamento sia per tipologia dei pezzi appesi, e una qualità pregevole del rivestimento.
“Noi sappiamo bene chi siamo e cosa possiamo offrire”. Queste poche parole di Giampiero Gritti racchiudono la chiave del successo di VAFE Srl, verniciatura conto terzi di Grassobbio (BG), specializzata nella verniciatura di lamierati e profili speciali e fuori standard per l’architettura metallica. “Le nostre finiture sono superficiali, la nostra competenza no” è lo slogan di questa azienda che, negli anni, ha saputo introdurre un’ampia gamma di cicli di trattamento e verniciatura in grado di soddisfare qualsiasi esigenza del settore dell’architettura nonché di conquistare tutte le certificazioni, qualifiche ed omologazioni necessarie per lavorare in questo settore così esigente, multiforme e – talvolta – capriccioso. Nel 2022 VAFE ha compiuto 60 anni: fondata dal nonno dell’attuale generazione – la terza – che ora la gestisce, opera nel settore del pretrattamento e della verniciatura industriale dei metalli sul territorio nazionale ed europeo dal 1962. Dalla originale sede “in un pollaio” – come ricorda Gritti – nella Città Alta di Bergamo, ben presto VAFE si trasferisce a Grassobbio, dove ha sede oggi, introducendo le vernici in polvere fin dalla loro prima apparizione sul mercato della finitura industriale. Oggi VAFE offre trattamenti ad alto livello tecnologico per strutture, profili e componenti in alluminio estruso, pressofuso e laminato, nonché ferro, ferro Senzimir e acciaio zincato che assicurano al materiale verniciato qualità estetiche e resistenza nel tempo senza pari. Negli anni ha conquistato tutte le qualifiche e le certificazioni necessarie per lavorare per una committenza internazionale: Qualicoat e Qualicoat Seaside per alluminio – gli unici in Italia e fra i pochi in Europa a possedere questa certificazione per profili fino a 13 metri; Qualisteelcoat per ferro e acciaio zincato fino alla classe di corrosività C5 nonché le qualifiche dei principali committenti italiani nel settore dell’architettura e delle infrastrutture. Subentrato al padre alle redini di VAFE, Giampiero ha dato impulso allo sviluppo dell’azienda, conquistando una nicchia di eccellenza all’interno del mercato dell’architettura metallica, che è quella della finitura di profili speciali e fuori standard (fino a 13 m di lunghezza per un peso di 8-10 kg/m2), lamiere di collegamento per facciate continue, accessori, tubi quadri per tende da sole, fino a sconfinare nei settori del design, dell’illuminazione, dell’auto e dei trasporti. Settori in cui la qualità di finitura è tenuta in altissima considerazione, non solo per motivi estetici ma anche per funzionalità, resistenza alle intemperie, resistenza all’invecchiamento e alla corrosione. Attualmente, Giampiero ha ceduto l’azienda ai figli, Matteo e Francesco Gritti e al nipote Stefano Algeri, la terza generazione della famiglia che sta continuando a far crescere l’impresa. Sono proprio loro che, in occasione delle celebrazioni per i 60 anni di attività lo scorso luglio, ci hanno spiegato le ragioni alla base del più recente investimento di VAFE, la sostituzione di uno degli impianti di verniciatura esistenti per barre fino a 8 m di lunghezza, con una nuova
© ipcm © ipcm
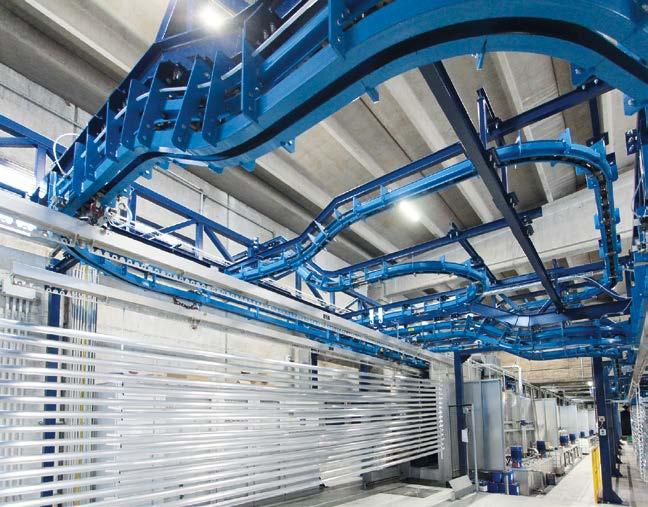
VAFE ha celebrato i 60 anni dalla sua fondazione con un evento che ha coinvolto soci e dipendenti con le loro famiglie, fornitori e clienti. L’ingresso delle bilancelle nel tunnel di pretrattamento. È ben visibile il circuito veloce indipendente dalla catena principale che conduce i profili lungo il pretrattamento.
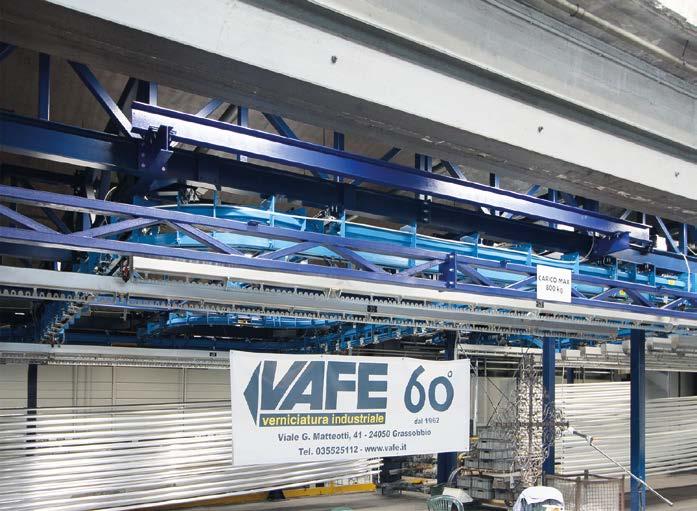
Foto di apertura: Profili verniciati in avvicinamento alla baia di scarico del nuovo impianto installato da VAFE e progettato da OMSA con convogliatore Futura.
© ipcm © ipcm
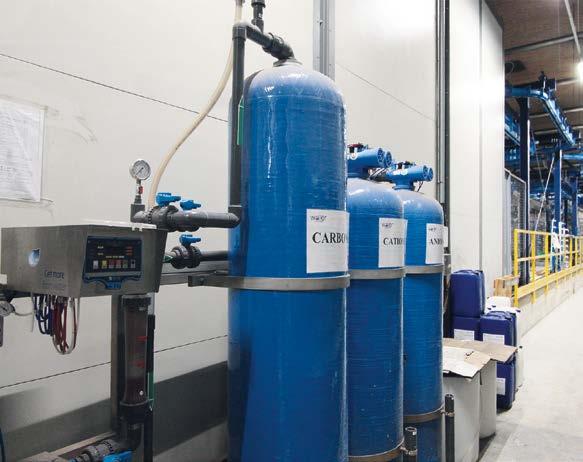
Il tunnel di pretrattamento e il demineralizzatore fornito da WaterEnergy.
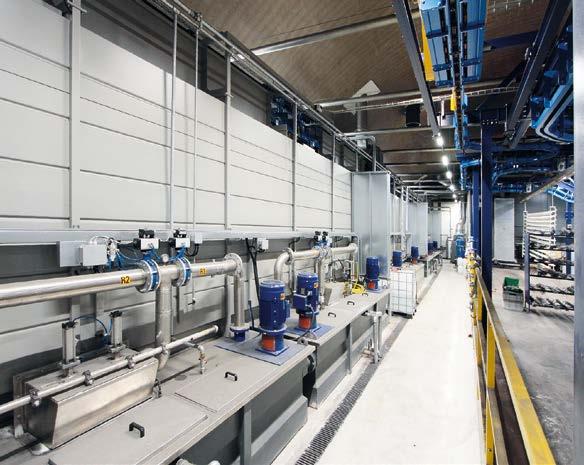
linea all’avanguardia progettata da Omsa di Besana in Brianza (MB), Futura Convogliatori Aerei di Robecco Pavese (PV) e Gema Europe di Trezzano s/N (MI), una linea completamente automatica in grado di garantire una produttività molto elevata e una flessibilità tale da consentire a VAFE di soddisfare – come un terzista di verniciatura che si rispetti – qualsiasi esigenza e richiesta del cliente senza mai fermare l’impianto. Vediamo come.
Tre impianti di verniciatura per lavorazioni su misura
Con tre impianti di ultima generazione, VAFE offre un’ampia gamma di cicli di lavorazione che garantiscono e durabilità dei risultati anche per i progetti più complessi.
Impianto di verniciatura orizzontale per materiali fino a 13 metri
• lunghezza massima > 13.000 mm • altezza massima > 3.000 mm • larghezza massima > 1.500 mm • portata massima > 3.000 kg
Impianto di verniciatura orizzontale per materiali fino a 8 metri
• lunghezza massima > 8.000 mm • altezza massima > 2.000 mm • larghezza massima > 450 mm • portata massima > 800 kg
Impianto di verniciatura verticale per materiali fino a 3 metri
• lunghezza massima > 1.200 mm • altezza massima > 3.000 mm • larghezza massima > 600 mm • portata massima > 120 kg.
Il nuovo impianto nato dai reparti progettazione di OMSA e Futura ha sostituito una linea pre-esistente per materiali fino a 8 metri, che, dopo trent’anni di pieno utilizzo, era necessario cambiare con le nuove tecnologie sul mercato. “Il progetto di questo impianto è partito circa 5 anni fa. Mio zio Giampiero aveva compreso che, per differenziarci all’interno di un mercato variegato come quello del terzismo di verniciatura, in cui si trovano aziende di natura e con competenze molto diverse fra loro, VAFE doveva emergere offrendo un servizio molto specifico, pregiato per la qualità e per la flessibilità. Era dunque strettamente necessario aggiornare l’impianto che possiamo definire medio, per materiali fino a 8 metri, dedicandolo esclusivamente alle lavorazioni per l’architettura”. “Questo nuovo impianto ci ha consentito di migliorare produttività e qualità non solo dal punto di vista della qualità del prodotto ma anche della qualità del lavoro. Il fatto che sia strutturato a fasi su diversi circuiti indipendenti l’uno dall’altro, ci permette di fermare le singole catene in caso di ritardi o necessità mutate in alcuni stadi di trattamento. Un impianto così progettato e così automatizzato, ottimizza tempi di ogni singola fase di processo, gli operatori non devono “rincorrere” la produzione dunque il tasso di errore è ridotto al minimo, la velocità della linea è costante e la qualità di finitura è alta e parimenti costante” prosegue Stefano Algeri.
“Al servizio di questo impianto abbiamo fornito un trasportatore birotaia
con portata massima di 1 ton (800 kg + il peso della bilancella) e diversi circuiti di trasporto indipendenti” esordisce Stefano Gerletti, responsabile vendite di Futura Convogliatori Aerei. “La parte più complessa a livello progettuale si è rivelata la necessità di inserire un convogliatore di questa portata e con 1 km di catena in uno spazio molto piccolo all’interno della fabbrica di VAFE. Le baie di carico sono due, una principale per i lotti standard con un fronte di pre-carico che consente di caricare l’impianto alla fine della giornata e dargli un’autonomia operativa automatica di un’ora il giorno successivo, anche non presidiato. Una seconda e più piccola baia di carico per pezzi fuori sagoma, prodotti speciali o volumi più piccoli”. “Nell’ottica di garantire la produttività massima consentita per lavorazioni di questo tipo, abbiamo dotato il convogliatore di circuiti separati con catene indipendenti” prosegue Gerletti. Inoltre, su ogni bilancella abbiamo

© ipcm
La cabina MagicCompact EquiFlow BA04.
SIMPLY STRIKING –powerful blue from every angle
Get to know the world’s first effect pigment with such a strong, highly chromatic dark blue. Thanks to ECKART’s patented anti-fading technology, EDELSTEIN Sapphire Blue retains this powerful color from any viewing angle.

Contact us for more information:
ECKART GmbH · Guentersthal 4 · 91235 Hartenstein · Germany Phone +49 9152 77-0 · info.eckart@altana.com · www.eckart.net
© ipcm
© ipcm
Il powder center OC06 All-In-One.

Vista prospettica del sistema di scambio del trasportatore dopo le cabine di verniciatura.
montato un oscillatore da 400 mm per ottimizzare il drenaggio fra uno stadio e l’altro. Il sistema sgancia le bilancelle dalla catena veloce e l’oscillatore entra in funzione”. “La genialità della progettazione di questo impianto risiede nel fatto che, grazie ai vari circuiti di cui è dotato il convogliatore, le cabine possono lavorare in modo indipendente oppure si possono ricircolare le bilancelle sulla stessa cabina” precisa Stefano Algeri. “Ogni cabina è dotata di un proprio polmone di accumulo che permette di applicare cicli a doppia mano senza perdere produttività. Lo stesso vale per i cambi colore: gli accumuli generati lungo il percorso del convogliatore, uniti a una programmazione intelligente della produzione, ci garantiscono estrema flessibilità. Quella flessibilità che ci consente di soddisfare qualsiasi richiesta dei nostri clienti senza mai frenare la produttività e continuando ad alimentare la linea”.

Caratteristiche generali della linea
“L’impianto è composto da un tunnel di pretrattamento a spruzzo a passaggio a 7 stadi con 4 celle (di cui due, quelle dei risciacqui, doppie) e un ultimo stadio di nebulizzazione del prodotto passivante no-rinse. Il ciclo è certificato sia Qualicoat sia Qualisteelcoat poiché tutti i bagni attivi (fosfosgrassante alcalino, diossidazione acida e conversione finale) utilizzano chimiche diverse a seconda che il materiale in trattamento sia alluminio o ferro/zincato. Il software di gestione dell’impianto esegue uno switch del prodotto in base alla ricetta assegnata in fase di carico” spiega Gilberto Riva, tecnico-commerciale di OMSA. “L’impianto prevede poi un forno di asciugatura con scambiatore in vena d’aria, due cabine automatiche di applicazione polveri, un forno di gelificazione e un forno di polimerizzazione, entrambi con scambiatore di calore indiretto. Ognuno dei due forni è assegnato a una cabina di verniciatura: il forno di gelificazione serve per gelificare il primer
© ipcm
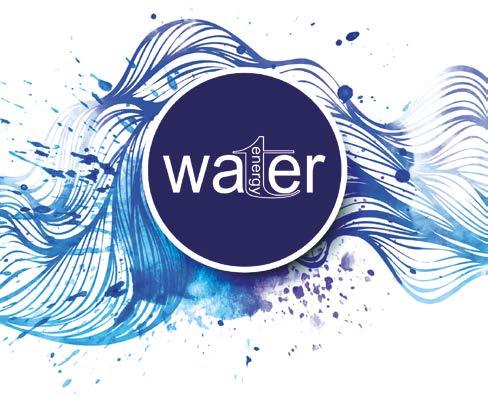
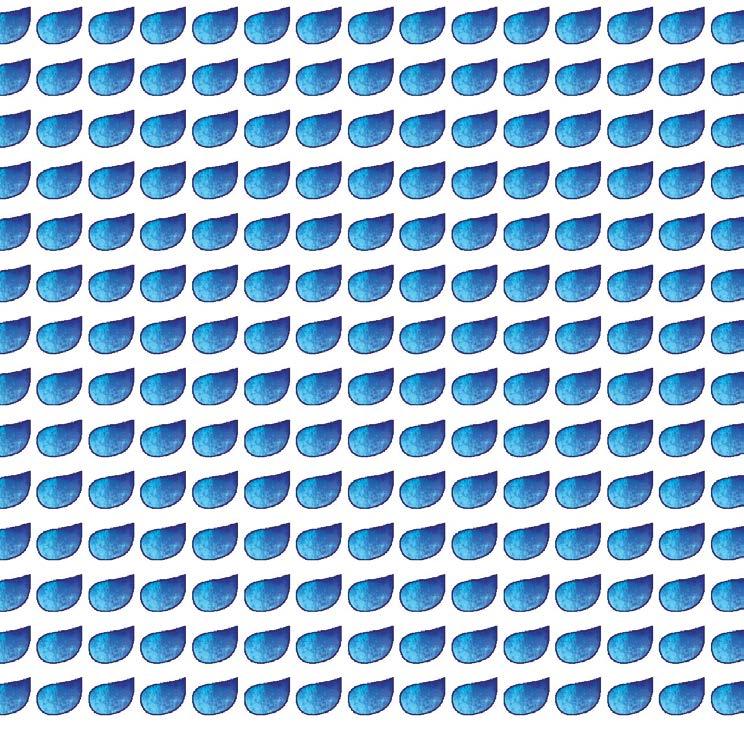
I polmoni di accumulo posizionati da Futura lungo il convogliatore birotaia.
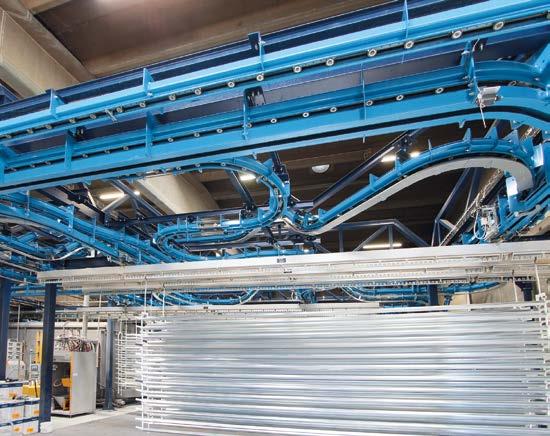
nel caso di cicli di finitura a doppia mano (ed evitare così il doppio passaggio in cabina), oppure per la polimerizzazione di piccoli lotti di colore. Cabine e forni possono lavorare in parallelo”. Le cabine di verniciatura utilizzano un sistema di applicazione con tecnologia tradizionale Venturi sui reciprocatori e con tecnologia in fase densa sui gruppi manuali destinati ai ritocchi. “Abbiamo due cabine, una revampata con apparecchiature Gema a venturi e una nuova cabina MagicCompact EquiFlow di Gema, allestita con la più recente versione di centro polvere, l’OptiCenter OC06 All-In-One” spiega Francesco Gritti. “Sulla nuova cabina, abbiamo deciso di uniformare la tecnologia di applicazione, rimanendo sul sistema a venturi, ma scegliendo la nuova versione All-in-One, dove le prestazioni e la velocità applicativa sono risultate molto più elevate mentre, a seguito di una serie di prove comparative che ho personalmente condotto, ho riscontrato che la fase densa, con le pompe di applicazione OptiSpray AP01, fosse invece fondamentale per abbattere l’effetto Gabbia di Faraday sui ritocchi manuali, risultando decisiva su alcuni prodotti particolarmente complessi”.
Industria 4.0
Futura e OMSA hanno sviluppato in co-progettazione il software gestionale 4.0 della linea di VAFE. “Tutti gli ordini sono caricati nel gestionale, ad ognuno di essi è assegnato un codice che contiene la tipologia di vernice, il ciclo di trattamento e i tempi di cottura” spiega Stefano Gerletti di Futura. “Al carico e allo scarico vi sono due pannelli operativi dove gli operatori, tramite pistola bar code o manualmente, possono inserire il codice allocato alla bilancella, selezionano dal PC
Get more from water
Turn key solutions for industrial wastewater treatment Design and manufacturing of plants and chemicals for industrial wastewater treatment Chemical-physical plants Sludge treatment and compactor systems Ion exchange demineralization systems and reverse osmosis systems Oil separators Filtering systems Batch type systems Flotation units Chemicals and spare parts for water treatment Technical service, support and maintenance of wastewater treatment plants
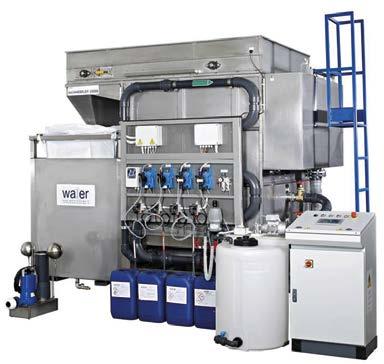
Beware of imitations, buy the original!
© ipcm

Il quadro di controllo dell’impianto.
la lavorazione richiesta. La bilancella parte e, dal quel momento in poi, segue tutto il flusso in base alle informazioni che le sono state attribuite. L’errore umano è ridotto al minimo, poiché l’operatore può sbagliare solo a selezionare la lavorazione, dettaglio che però viene più volte controllato durante il flusso. Davanti al tunnel di pretrattamento il software Futura passa il codice al software OMSA che processerà il prodotto in base alle informazioni contenute in quel codice. Lo stesso avviene davanti ai forni di polimerizzazione. Attraverso lo shift-register (il sistema virtuale di tracciamento) è possibile seguire la posizione della bilancella sul touch panel. Cliccando sulla singola bilancella si apre un’ulteriore finestra che contiene tutte le informazioni legate a quella bilancella”.
L’investimento che ci voleva
“Grazie all’investimento in questo impianto non solo abbiamo aumentato la capacità produttiva e raggiunto un alto livello di flessibilità, ma possiamo anche investigare e correggere, in tempo reale, qualsiasi problema si presenti durante il trattamento” dichiara Matteo Gritti. “La flessibilità è l’aspetto che ci ha soddisfatto maggiormente perché stiamo spingendo molto il ciclo di verniciatura a doppia mano” interviene Stefano Algeri. “Applichiamo tanti cicli a doppia mano sui manufatti in ferro da esterno o in Senzimir, ossia una lamiera pre-zincata che non ha una vera protezione degli spigoli. Ma stiamo spingendo la doppia mano anche sull’alluminio, per i prodotti che saranno installati fronte mare ad esempio: laddove il budget lo consente, preferiamo abbinare la protezione Qualicoat Seaside a quella data dall’applicazione di un primer”. “Possiamo dunque dirci molto soddisfatti dell’investimento, era proprio ciò che ci voleva per sviluppare ulteriormente il mercato di VAFE” conclude Francesco Gritti. “Siamo soddisfatti anche del pool di fornitori, non solo per le tecnologie installate ma anche per il servizio e il modo in cui ci seguono”.
© BT Group
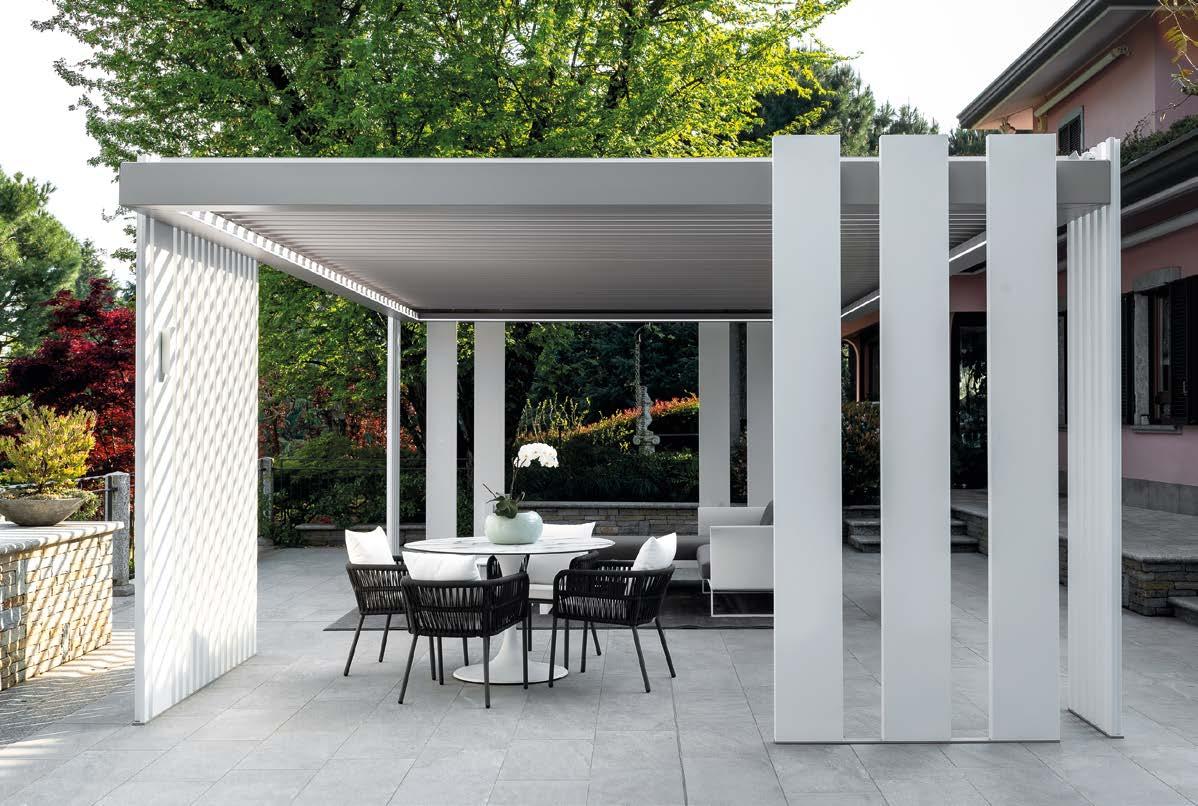
Una pergola della gamma CODE interamente costruita e verniciata da BT group.
FOCUS ON TECHNOLOGY
SPECIAL ISSUE ON ALUMINIUM
Personalizzazione totale di strutture in alluminio da esterni per la protezione solare: la sfida di BT Group
Gabriele Lazzari, ipcm®
BT Group è protagonista di mercato per il settore italiano ed esterno di pergole e tende da sole, grazie alla flessibilità della propria produzione e l’elevato grado di personalizzazione che offre ai propri clienti. L’incremento di richieste a cui è stata soggetta l’industria della protezione solare negli ultimi anni ha consentito all’azienda di espandere la propria produzione utilizzando un nuovo impianto automatico di verniciatura in polvere progettato, costruito e installato da Silvi in collaborazione con Futura, Chemetall e Wagner.
©ipcm
Le due mazzette colori standard messe a disposizione da BT Group.

Dopo aver chiuso il 2018 con un fatturato pari a 1.244 milioni di euro, Pambianco – società di consulenza operante nel settore del lusso – riporta che anche negli anni successivi l’industria italiana delle tende da sole e delle pergole ha generato un aumento di fatturati e marginalità1. Federlegno Arredo riporta inoltre che la domanda è ulteriormente incrementata subito dopo il lockdown, come testimoniato anche da BT Group, gruppo multinazionale con sede a Lesmo (MB) attivo nella produzione di strutture domestiche da esterni per la protezione solare. L’azienda fu fondata nel 1954 da Ambrogio Radaelli a Monza, un territorio saldamente legato alla tradizione artigianale. Nel corso degli anni ha ampliato la propria produzione, le tipologie di soluzioni e il grado di personalizzazione offerti ai clienti, arrivando a servire non solo il mercato italiano ma anche quello internazionale. “BT Group è protagonista di mercato nella protezione solare grazie alla flessibilità produttiva. Le nostre tende da sole, pergole e bioclimatiche sono infatti il proseguimento dell’interno della casa dei clienti e sono dunque in grado di rispondere a tutte le necessità: la personalizzazione non riguarda solo i colori e la finitura, ma anche le dimensioni, le forme, i meccanismi di movimentazione e gli accessori,” esordisce Andrea Radaelli, CEO di BT Group. “La pandemia di COVID-19 ha incrementato a dismisura le richieste, perché il pubblico si è accorto di quanto i nostri prodotti siano un’ottima soluzione per vivere l’esterno senza abbandonare la comodità e la sicurezza della propria abitazione”. Per fronteggiare l’aumento degli ordini, l’azienda si è rivolta a Silvi srl di
1 https://design.pambianconews.com/fatturati-in-aumento-per-i-big-dei-sistemi-diprotezione-solare/ Peregallo di Lesmo (MB) per la progettazione, costruzione e installazione di un nuovo impianto di verniciatura che permettesse a BT Group di velocizzare la produzione senza sacrificare la qualità dei propri prodotti.
Produzione e finitura interamente personalizzati
L’azienda si occupa internamente di tutta la fase di progettazione, rimanendo sempre in stretto contatto con i clienti per offrire il massimo livello di personalizzazione possibile. L’azienda acquista i profili di alluminio estruso grezzo e tutti gli altri componenti utilizzati nelle proprie strutture da aziende italiane. “Utilizziamo ancora alcuni componenti in plastica, ma il mercato si sta spostando verso soluzioni maggiormente ecosostenibili, perciò anche noi cerchiamo – quando possibile – di sostituire la plastica con l’alluminio stampato in pressofusione. Questa nuova tendenza ci sta avvantaggiando, dato che tra le aziende del nostro gruppo fa parte Form, una fonderia specializzata nello stampaggio di particolari in alluminio e zama”, commenta Alessandro Citterio, direttore degli acquisti. “Il profilo è acquistato grezzo e poi tagliato per raggiungere le dimensioni desiderate e subisce le successive lavorazioni meccaniche realizzate tramite macchine a controllo numerico di ultima generazione nel reparto di carpenteria leggera. Infine, il pezzo è inviato al reparto di finitura”. “Il processo di verniciatura è la fase più importante di tutto il nostro ciclo produttivo”, dichiara Luca Grazzi, direttore dello stabilimento. “Oltre ad essere spesso la prima caratteristica che il cliente nota, è
©ipcm
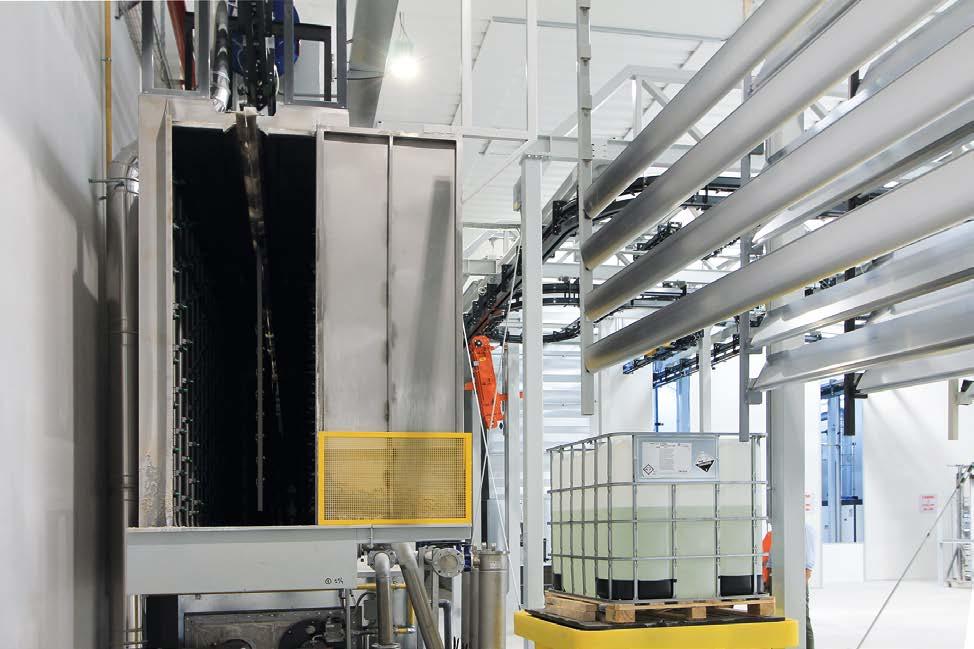
L’ingresso del tunnel di pretrattamento con processo sviluppato da Chemetall.
anche l’aspetto dove potremmo subire più contestazioni sulla qualità, a causa delle continue manipolazioni, dei trasporti e delle operazioni di assemblaggio in cantiere”. BT Group propone ai propri clienti molteplici tonalità da due differenti mazzette colori: una include colori RAL opachi testurizzati con una finitura leggermente bucciata, mentre l’altra include colori metallizzati. “I colori maggiormente richiesti sono il bianco, che occupa il 40% della nostra produzione, e le tonalità di grigi e marroni con finitura testurizzata, che creano un bellissimo effetto estetico. Ma nel settore delle tende da sole sono i colori lucidi ad essere i più apprezzati, in particolare bianco, avorio e grigio 7035” spiega Citterio. “Inoltre, come già spiegato in precedenza, la flessibilità è il nostro punto di forza. Pertanto utilizziamo anche vernici in polvere scelte personalmente dai clienti, purché soddisfino tutti i nostri requisiti di qualità. Il prodotto sarà sicuramente esposto in ambienti esterni, ma per alcune commesse non conosciamo approfonditamente le caratteristiche ambientali del luogo in cui sarà installato e il grado di corrosione a cui sarà soggetto. Pertanto seguiamo sempre lo standard qualitativo della certificazione QUALICOAT classe 2 e utilizziamo prodotti vernicianti in polvere poliestere, perché conferiscono una resistenza maggiore e penetrano maggiormente anche su pezzi con geometrie complicate”, interviene Grazzi. La necessità di nuovo impianto di verniciatura in polvere
BT Group era già in possesso di un impianto di verniciatura realizzato ad inizio secolo nel proprio storico stabilimento di Lesmo. Destinato alla verniciatura di barre, pezzi in pressofusione e telai in ferro, era stato recentemente aggiornato proprio da Silvi. Ma, con l’aumento delle richieste, l’azienda non è stata comunque più in grado di reggere i nuovi ritmi produttivi. Si è rivolta inizialmente anche a terzisti di verniciatura, ma nemmeno loro potevano assicurare il rispetto dei tempi di consegna richiesti. BT Group ha dunque deciso di investire in un nuovo impianto di verniciatura. “Eravamo, e siamo tutt’ora, completamente soddisfatti delle prestazioni dell’impianto revampato da Silvi. Inoltre, abbiamo visitato gli stabilimenti di altri verniciatori per comprendere meglio i vantaggi e gli svantaggi di altre tecnologie di verniciatura. Dopo un’iniziale fase di analisi, abbiamo deciso di affidare nuovamente a Silvi la commessa del nuovo impianto. Abbiamo perciò acquisito un terreno sul quale realizzare il nuovo reparto di verniciatura e un magazzino dedicato alle barre”, continua Citterio.
Il ciclo di pretrattamento
Il nuovo impianto a disposizione dell’azienda è dotato di un’ampia zona
©ipcm
L’interno del tunnel di pretrattamento a spruzzo.
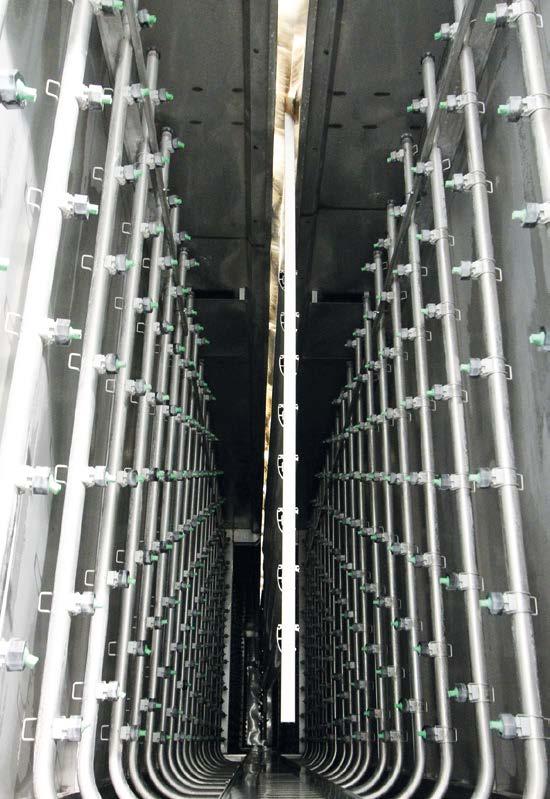
di carico dalla quale si sviluppa un trasportatore aereo birotaia realizzato da Futura Convogliatori. Il tunnel a spruzzo – realizzato interamente in acciaio inossidabile – è configurato a stazioni isolate da porte che consentono un processo più efficace ed esente da contaminazioni fra i bagni. Tutte le rampe di spruzzatura sono dotate di filtri particolari, normalmente utilizzati nelle vasche di cataforesi per migliorare l’applicazione delle soluzioni di trattamento. Il tunnel è completato da due demineralizzatori di ricircolo da 3.000 litri per la produzione di acqua demineralizzata, che è anche stoccata in un serbatoio di accumulo, e un evaporatore sottovuoto da 12.000 litri per trattare le acque reflue di risulta, consentendo così alla linea di raggiungere lo “scarico zero di liquidi”. “Durante la fase di progettazione del nuovo impianto”, interviene Andrea Monti, Technical Coordinator dell’unità di business Surface Treatment della divisione Coatings di BASF, che opera sotto il brand Chemetall, “abbiamo analizzato le esigenze di BT Group e abbiamo infine scelto congiuntamente il ciclo di pretrattamento con
©ipcm
©ipcm
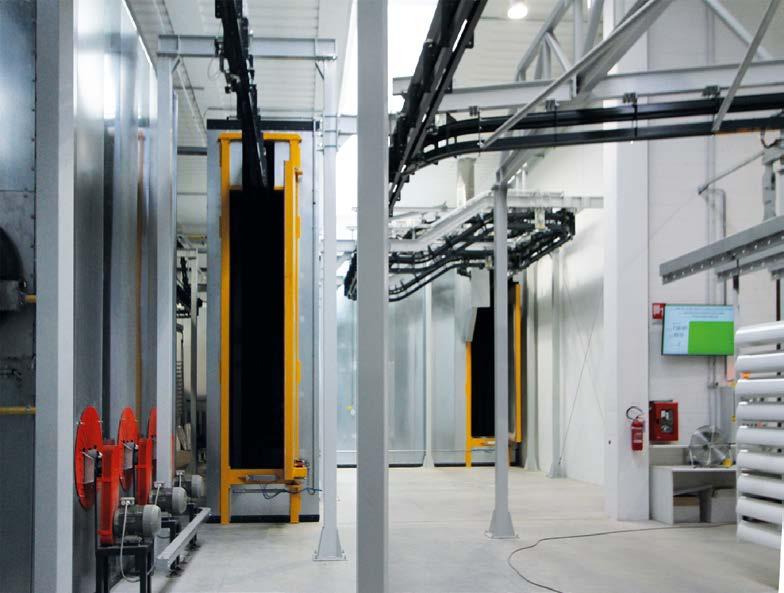
Il convogliatore in ingresso nel forno di asciugatura (in alto) e il polmone di accumulo con il trasportatore di Futura.
la soluzione nanotecnologica ibrida Oxsilan© thin-film, che combina le proprietà di inibizione dalla corrosione dei metalli inorganici come lo zirconio con la flessibilità fornita dal supporto a base di silani. È la stessa soluzione utilizzata anche nel primo impianto da quando è stato revampato perché l’azienda aveva deciso di sostituire il processo con cromo esavalente. Sebbene alcune vernici QUALICOAT classe 2 in passato hanno presentato dei problemi di adesione, la parte polimerica inorganica all’interno delle tecnologie di Chemetall la migliora considerevolmente. In questo modo, la superficie del profilo risulta adatta alle molteplici vernici utilizzate da BT Group”. Il ciclo di pretrattamento è composto da dieci stadi. Il primo prevede un decapaggio alcalino forte per sgrassare e disossidare i profili, al fine di eliminare il “deformation layer” che si genera in fase di estrusione ed eliminare la contaminazione organica. Successivamente a due risciacqui con acqua di rete, è previsto uno sgrassaggio acido multi-metal per completare la dissoluzione degli alliganti riaffiorati sulla superficie a causa dell’asportazione del “deformation layer”, che potrebbero causare la corrosione filiforme. Seguono un risciacquo con acqua di rete per eliminare i metalli residui dalle fasi precedenti e uno con acqua demineralizzata che asporta invece i metalli contenuti nell’acqua di rete e prepara il profilo ad entrare nella camera di conversione nanotecnologica. Infine, dopo un ulteriore lavaggio con acqua demineralizzata, il sistema di tilting del trasportatore riporta le bilancelle con i profili sul proprio asse orizzontale e li conduce all’interno del forno di asciugatura con bruciatore a fiamma indiretta a 120-140° C.
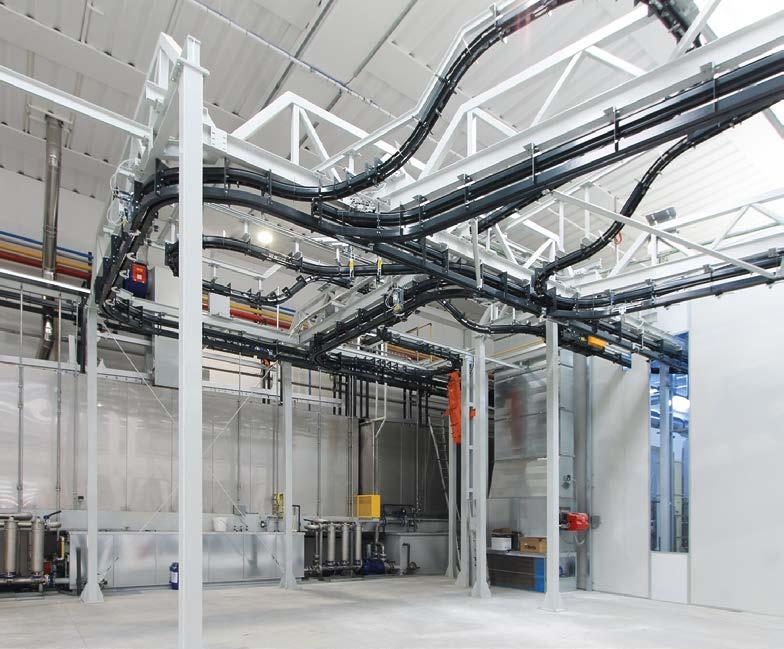
Verniciatura di alta qualità con 15 cambi colore per turno
In uscita dal forno di asciugatura, il convogliatore aereo smista le bilancelle all’interno delle due cabine di verniciatura a spruzzo automatiche di J. Wagner GmbH, una dedicata ai colori chiari e l’altra ai colori scuri. Entrambe sono inserite in una Clean
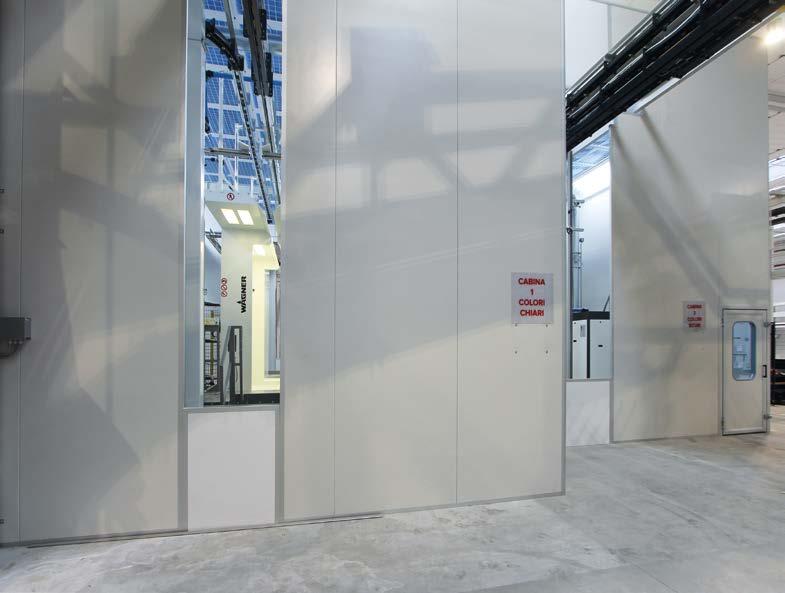
Room pressurizzata e climatizzata con temperatura costante a 25° C al fine di evitare qualsiasi contaminazione. Ciascuna cabina è dotata di due reciprocatori contrapposti, due postazioni manuali per il pre- e il post-ritocco e dodici pistole automatiche con tecnologia di alimentazione tradizionale Venturi che, grazie ad un lettore ottico posto all’ingresso della cabina che rileva le dimensioni e la geometria del pezzo, si avvicinano oppure si allontanano da esso per favorire un’adesione e una penetrazione ottimale della vernice in polvere. “Abbiamo inoltre richiesto espressamente il centro polvere SuperCenter EVO, grazie al quale abbiamo la possibilità di setacciare e miscelare polvere vergine e di recupero – mantenendo così costante la qualità di applicazione – e che è in grado di dettare ed eseguire automaticamente le fasi del cambio colore, a prescindere dall’esperienza dell’operatore. Attuandone anche quindici per turno lavorativo, volevamo che i cambi colore fossero gestiti in totale autonomia e nel mondo più efficiente possibile. Attualmente un cambio colore richiede da quattro a tredici minuti (con una media di otto) in base alla durata del lotto e alla tipologia di polvere utilizzata. Tuttavia, ora non abbiamo la necessità di velocizzare questa fase della nostra produzione”, continua Grazzi. “Preferiamo essere sicuri di ottenere un’elevata qualità. Infatti abbiamo anche studiato alcune differenti disposizioni dei profili sulle bilancelle, per provare ad ottimizzare il processo di verniciatura. Inoltre, a fine lavorazione i nostri operatori controllano accuratamente la qualità di ogni singolo profilo”. Una volta usciti dalle due cabine di verniciatura, i componenti sono trasportati verso un’avancamera di gelificazione – per evitare la dispersione del colore – e successivamente nel forno di polimerizzazione. Infine, i manufatti stazionano in un buffer per il loro raffreddamento prima di essere scaricati e immediatamente imballati per evitare manipolazioni e danneggiamenti durante il trasporto.
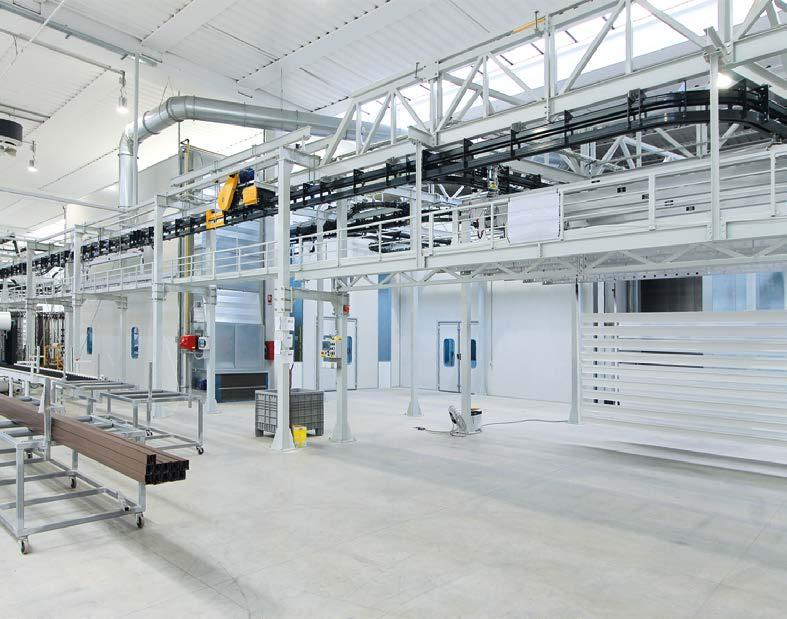
©ipcm
©ipcm
Dettaglio del convogliatore aereo birotaia (in alto) e l’esterno della Clean Room con le due cabine divise per colori chiari e scuri.
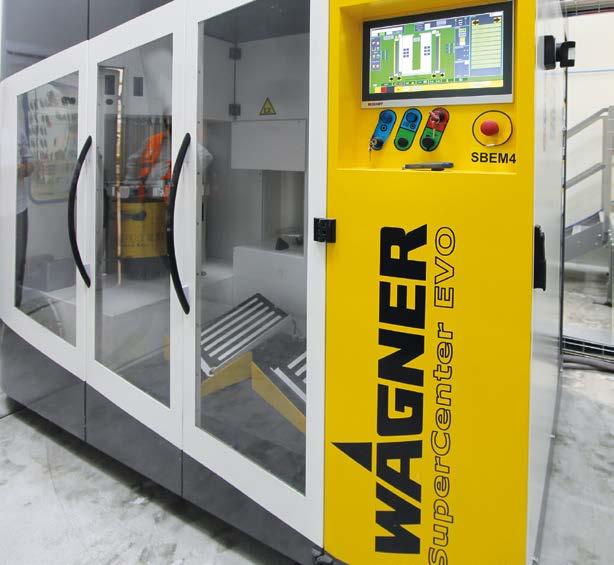
©ipcm
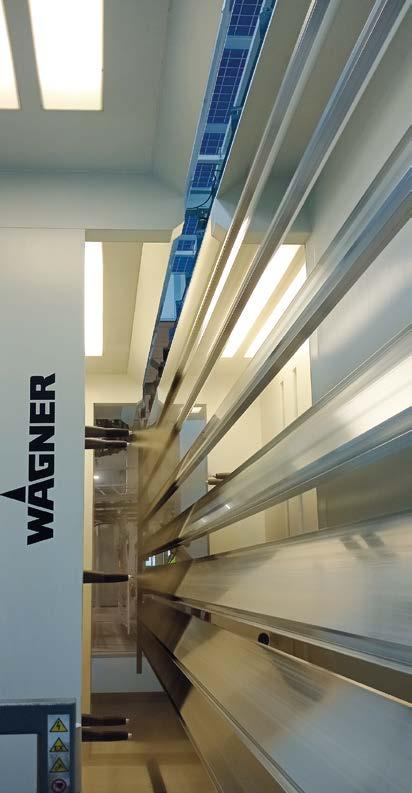
©ipcm
I profili di alluminio verniciati dalle cabine automatiche di Wagner.
Il centro polveri.
Il team di BT Group davanti al nuovo impianto.
©ipcm
Il ruolo di Silvi e l’importanza della collaborazione
“Con questo impianto siamo stati in grado di superare le mille ore di resistenza in nebbia salina. È estremamente efficiente e ne siamo completamente soddisfatti. È in funzione da oltre cinque mesi, ma non abbiamo mai incontrato alcuna difficoltà o problematica. Ciò è anche merito di BT Group, che si è interfacciata con tutti i partner coinvolti affinché fossero fornite le soluzioni più adatte a ogni nostra singola esigenza”, afferma Citterio. “La prima attività è stata quella di creare un gruppo di lavoro che includesse noi di Brianzatende, la dirigenza tecnica di BT Group, Futura, Chemetall e Wagner. Abbiamo ascoltato le richieste del cliente e ognuno ha fornito un tassello fondamentale per risolvere una problematicità specifica. Successivamente ci siamo interfacciati anche con il fornitore del gestionale di produzione BT Group, al fine di interconnettere fin da subito il nuovo impianto in industria 4.0 con il software gestionale interno dell’azienda. Grazie alla flessibilità dimostrata da tutti i partner coinvolti, siamo riusciti ad installare e collaudare in tempo tutto l’impianto, nonostante i problemi causati dalla carenza di materie prime”, dichiara soddisfatto Daniele Fumagalli, General Manager di Silvi. “La scelta di affidarci a Silvi si è rivelata nuovamente vincente. Ci ha portato vantaggi quantitativi, perché siamo riusciti ad incrementare la produzione, e qualitativi. Non pensavamo che lo sviluppo e l’implementazione del progetto potessero procedere così rapidamente. Siamo inoltre felici di aver coinvolto fin da subito tutti i nostri operatori, perché sono stati così in grado di apprendere tutte le funzionalità dell’impianto e renderlo altamente performante. Infatti a breve avvieremo la produzione su due turni”, conclude Grazzi.
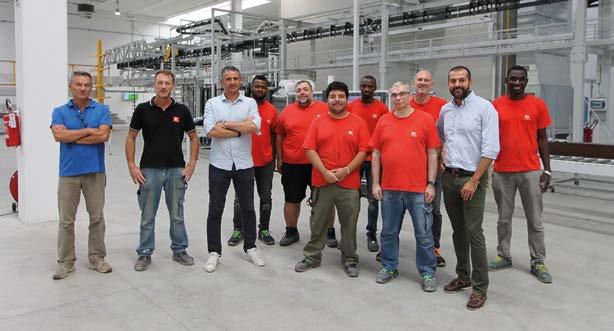