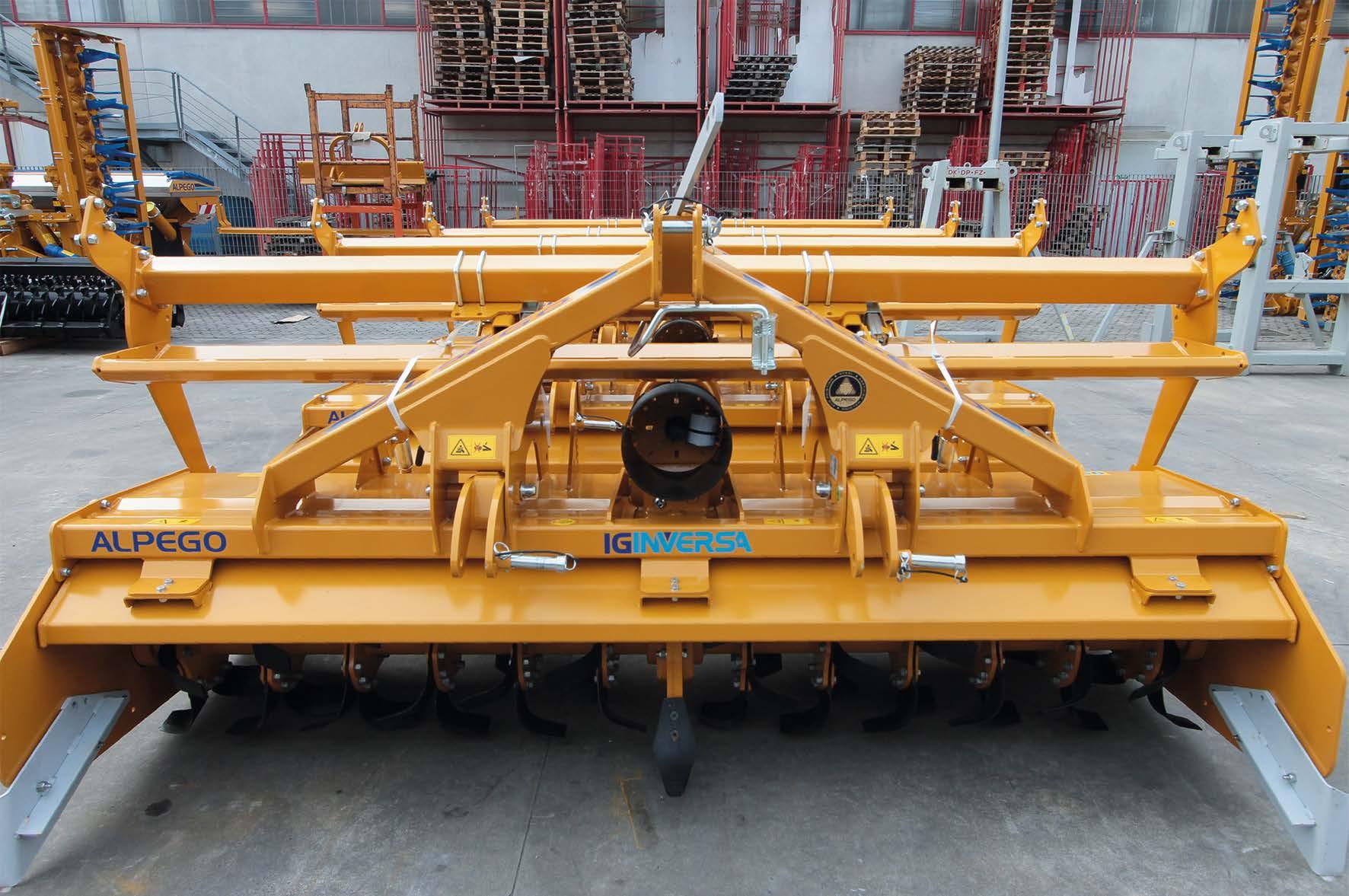
15 minute read
FOCUS ON TECHNOLOGY
SPECIAL ISSUE ON ACE & OFF ROAD VEHICLES
A “Cartesian” Coating System and a New Pre-Treatment Process to Increase Corrosion Resistance Fivefold. Alpego: When Chemistry Matters.
Alessia Venturi ipcm®
Providing a coating with corrosion resistance properties is never a one-man show, but rather teamwork involving all the different elements that make up a painting process. Alpego Spa, a global leading manufacturer of agricultural machinery, is well aware of this. Its new pre-treatment cycle developed by ALIT Technologies with Alufinish products, combined with an unconventional coating line that is perfectly suited to its needs, has increased its products’ salt spray resistance fivefold.
One of the agricultural machines included in Alpego’s range of products.
© ipcm

The agricultural, construction, and construction machinery (ACE) sector is comparable to the automotive one in terms of plant engineering, painting, outdoor resistance, and, last but not least, coating sustainability requirements. Not only does the heavy machinery and off-road vehicle market now demand finishes with a “bodywork” aesthetic quality degree comparable to those applied by automotive OEMs, but the issues of the durability and the mechanical, chemical, and corrosion resistance of coatings is also just as central as in the car industry. Although the coating departments typically set up in the two industries are not comparable, not least because in the ACE sector the metal masses involved are very large and therefore require very different plant arrangements than in a classic automotive paintshop, the issues of sustainability, energy efficiency, and the environmental impact of paint systems are equally important. For both sectors, the key process for guaranteeing the durability of coatings is surface pre-treatment. Only a perfectly deoxidised, clean, passivated surface with the correct surface roughness value can guarantee excellent adhesion of the paint film and increase its resistance to corrosion. Clearly, once the ideal pre-treatment has been found, it must also be integrated in a process context where the coating products and their application are handled as efficiently and effectively as possible. Alpego Spa (Almisano, Vicenza, Italy) is a company aiming at optimising agricultural production with its machines by listening to the needs of a constantly evolving sector. Its experience in this respect is paradigmatic. After years of intensive study of all possible coating system solutions, which required seven visits to the PaintExpo trade fair in Germany and countless trips around Europe to analyse its competitors’ choices, Alpego spent four years planning its perfect painting plant, which was finally completed in 2014.
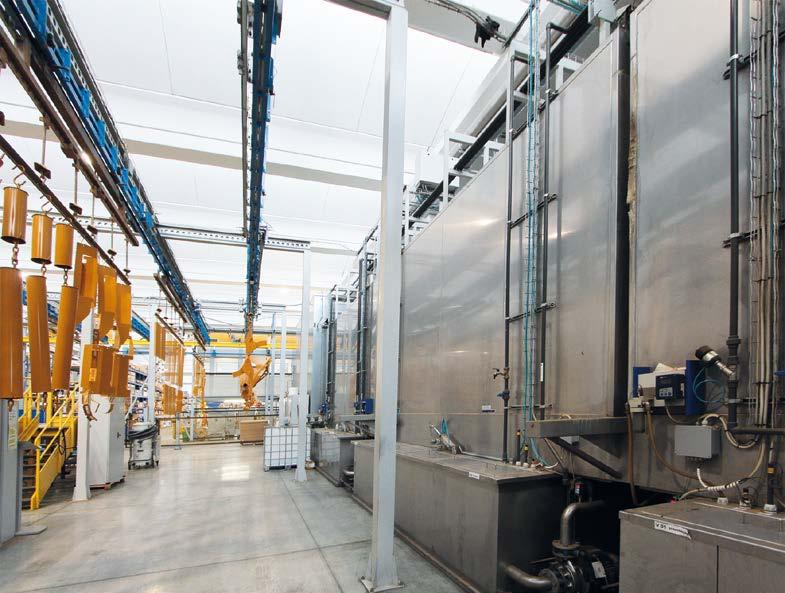
© ipcm
© ipcm
General view of the pre-treatment tunnel and the drying oven after the pre-treatment stage.
Components of agricultural machinery being powder coated.
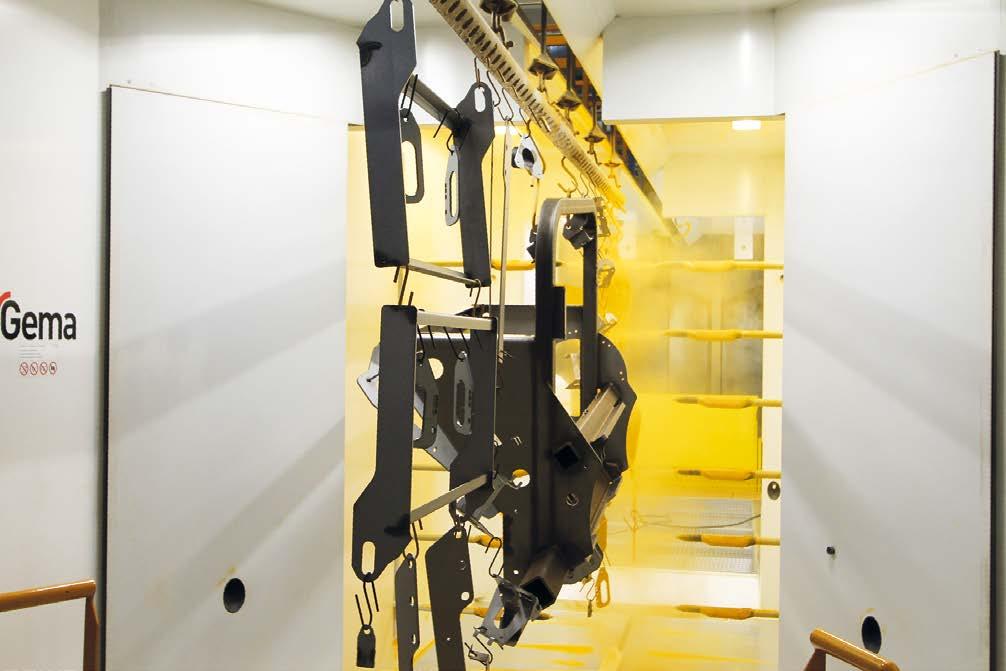
© ipcm
Its collaboration with Alit Technologies (San Bonifacio, Verona, Italy), a supplier of pre-treatment products that is the Italian distributor of German Alufinish products, was strategic in achieving its corrosion resistance targets.
About Alpego
It is in the middle of the Veneto region, one of the richest and most industrialised areas in Italy, covered in vineyards and surrounded by the splendid Dolomite Alps, that Alpego was founded in the 1980s as a small family business. It is still 100% owned by the Pegoraro family, now in its third generation. Flail mowers, subsoilers, tillers, rotary cultivators, seed drills, fertilisers, vineyard equipment, power harrows, and cultivators make up the vast product range of Alpego, which manufactures 4000 machines a year. All products continue to be conceived and designed in-house in order to maintain the complete know-how of each individual project. The company always reinvests 4% of its turnover in research and development and it has 40 active patents and trademarks. For the sake of quality and reliability, Alpego’s machines also continue to be produced in-house or with the help of high quality Italian suppliers. 80% of the components purchased are produced in Italy, while high-strength pickled sheets are purchased in Sweden, which is a leading producer in the sector, and the remaining 10% of purchased parts are made in Germany and the United States. Since its foundation, Alpego has boasted constant growth in all international markets, with double-digit increases in terms of both number of machines produced and turnover, reaching the threshold of 40 million Euros in 2021 with 190 employees. Today, the company has three plants with a total area of 41,000 m2, of which 15,000 are covered: • Almisano: the new headquarters since 2012, covering over 21,000 m2. It houses the administrative, technical, and sales offices, a large assembly department, the coating line, a machine dispatch area, and a spare parts warehouse. • Gambellara: the company’s first headquarters, now housing a carpentry shop with advanced laser cutting systems, press brakes, and welding robots. • Lonigo: an assembly service plant that was recently acquired in order to increase production capacity. Alpego has a wide sales network consisting of numerous importers and dealers, as well as two European subsidiaries, Alpego France and Alpego UK.
The development of an unusual coating system
“Alpego has always coated its machines in-house,” states Luciano Pegoraro, the current owner of Alpego together with his brother Giovanni. “Painting is too important to be assigned to an external supplier. At our original Gambellara site, we had a conventional liquid coating line with an overhead conveyor, a classic “ring” with a phosphodegreasing and a drying station, two painting booths for primer and top coat application, and a final baking oven. We used to apply a high-solids coating system but, although we complied with atmospheric emission limits, we wanted to switch to water-soluble products. However, our plant’s design did not enable us to do so. Too many parameters would have had to be monitored and adjusted to achieve high quality coating results with water-soluble products: the process was incompatible with the installation itself. In addition, we needed to increase the corrosion resistance of our machines, as many of them were exported by sea. Already with that old plant, we were collaborating with Alit Technologies, which supplied us with phosphodegreasing products. Our workpieces, mainly made of thick (8-10 mm) black iron sheets, called for an aggressive pickling process in order to obtain surfaces suitable for high quality painting. The only alternative would have been to combine chemical pre-treatment with a controlled shot blasting phase. However, once again, our line did not allow us to do that.” “Despite several adjustments to the pre-treatment cycle, with the coating products and plant conditions of the time, we could not make Alpego’s products achieve a salt spray resistance value over 170 hours,” says Loris Rossi, the CEO of Alit Technologies, the Italian distributor of Alufinish products. “The pretreatment tunnel presented a major problem of rinsing water pollution and the quality of surface preparation could not be further improved without modifying the plant.” “Based on all these reasons, in the early 2000s we decided that it was necessary to invest in a new coating line,” adds Luciano Pegoraro. “However, I did
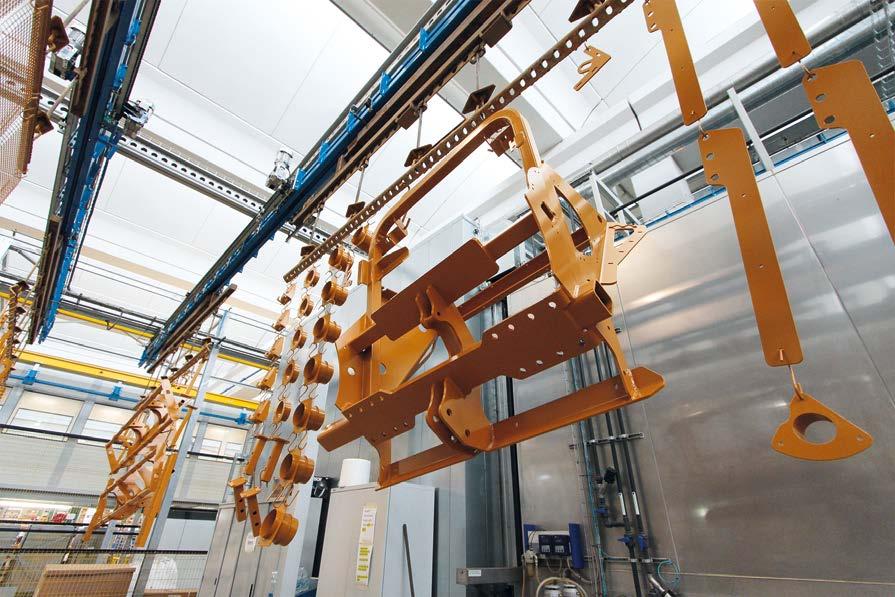
© ipcm
Finished components hanged onto the coating line designed by Tekimp of Castelfranco Veneto, Italy.
not want to install a traditional line with a two-rail conveyor again. I found the layout of those lines too rigid for our production flow. Moreover, this type of plants takes up too much space: in fact, the first project submitted to us covered more than half of our new Almisano plant. “We therefore decided on a clear change in several areas of our production flow. First of all, we changed our raw material: from black iron, we switched to buying only pickled sheet metal, mainly from Sweden. Secondly, we implemented laser cutting operations on sheet Luciano Pegoraro (left) with Loris Rossi in front of several Alpego’s agricultural machines ready to be shipped all over the world. metal in order to eliminate as much as possible the problem of oxidation on high thicknesses. Thirdly, we specified a water-based coating system consisting of an epoxy primer and a two-component acrylic top coat and we started considering using powder coatings, which we then actually did. Finally, at PaintExpo we were inspired to no longer design a ring system but a line of stations, based on a concept that is completely different from conventional plants.” Quintupling corrosion resistance with the right chemicals, applied with the right equipment

© ipcm
Tekimp (Treviso, Italy), part of Rimor Group, designed for Alpego a compact, functional plant that Pegoraro defines as “Cartesian” and storage buffer-free, to emphasise the absence of a classic conveyor in favour of a handling process using trolleys that take the workpieces to the relevant treatment stations, following pre-set routes that are independent of each other. The plant also includes an in-line modular shot blasting machine, which performs fine shot blasting of high thickness (8-10 mm) parts. These components undergo two pre-treatment phases, first mechanical and then chemical with the new Alufinish system, while thin sheet metal parts only undergo the chemical pre-treatment process. Each load bar can be assigned a different shot blasting grade. The Alufinish pre-treatment cycle supplied by Alit Technologies includes a strongly alkaline degreasing stage at 55 °C for 10 minutes, two rinses with mains water, a nanotechnology passivation stage, a rinse with demineralised water, and a drying stage. With this new pre-treatment process, combined with the selected coatings, Alpego has been able to achieve a salt spray resistance value of 500 to 700 hours but, above all, it has achieved excellent quality consistency. “This was a great team effort,” comments Luciano Pegoraro. “Alit already made sure we achieved good pretreatment results despite the difficult conditions of the previous line: with the new plant, the results are top notch!”. “Alpego placed great trust in Alit. We already had a good business relationship that had started when working on the old line, also thanks to the proximity between their factory and Alit’s,” says Loris Rossi. “Then, the four years spent on designing this plant were years of mutual technical growth and exchange of knowledge and experience. Alit felt valued by Alpego and we worked closely to fine-tune all chemical aspects.” “Although a few changes were made during the construction phase, the path mapped out in the design phase proved to be correct, in terms of both plant engineering and chemistry,” notes Pegoraro.
A new, challenging scenario
Working with the new system entailed a total change of paradigm for Alpego, from painting complete machines to coating individual components. “Initially, the system seemed gigantic compared to what we had before, so we had a few problems making it work well,” indicates Pegoraro. “For the first four years, we only applied liquid coatings. Then, in 2018, we implemented a one-coat powder finishing process by installing a Gema automatic booth, separating the components that could be powder coated from those that could not. The new painting line is very complex in terms of production scheduling software: start-up and industrialisation were difficult. Now, almost eight years later, the plant’s capacity is saturated and we would need a new one. Over the last few years, in addition to the painting plant, we have invested 7 million Euros in Industry 4.0-oriented production machinery. Now, we are ready for new coating challenges!”
INNOVATIONS: PRESENT&FUTURE

SPECIAL ISSUE ON ACE & OFF ROAD VEHICLES
Protect and Beautify Farm Machinery, a High-Tech Challenge
Edited by SAMES KREMLIN
Meylan – France marketing@sames-kremlin.com
Agricultural machinery manufacturers design machines that are able to withstand the weather, chemical and mechanical aggression. Today, they must also offer paints with finishes as meticulous as those on cars. This dual challenge requires the use of high-tech application equipment.
Who would have thought that metallic paints would one day make their appearance on agricultural machinery? But that’s what we’re seeing now: light grey, anthracite grey and metallic red are being used on tractors and trailers, which can even be customised. The shine of their painted surfaces is on a par with that of car bodies.
Combining durability and aesthetics, a challenge for paint manufacturers
This quest for aesthetics also affects, to a lesser extent, combine harvesters, sprayers, soil preparation and planting equipment. Agricultural machinery has always been required to be robust and durable to withstand the sun, frost, rain, dust, shocks, vibrations, chemical aggression and sometimes salt spray. Now they must also be beautiful. “It is understandable that farmers think like this”, says Gilles Valbrecq, Sales Director for Industry in France. “The acquisition of a piece of agricultural machinery is an investment over several decades. The quality of the finish is a guarantee of seriousness, a reassurance about the lifespan of the machine and ... a way of enjoying it, quite simply”. These requirements led to the development of new references by paint manufacturers who could not offer their usual products dedicated to the automotive market. Indeed, the chemical composition would not have withstood the harsh life of the fields. They expanded their ranges for agricultural machinery by introducing metallic colours, mainly in the form of liquid paints.
Hardeners, zinc or titanium particles...
However, the fundamentals of paints, those that ensure their durability, have not changed. These are mostly “two-component” paints. They combine a base (for example, an epoxy if maximum durability is desired, or a polyurethane for an impeccable finish) and a hardener. To reinforce
the mechanical properties of the coating, microparticles of zinc or titanium are sometimes incorporated. This very specific market relies on application equipment that is just as specific. Their role is first to extract the products from their container, drum or barrel. It is then to mix and dose them, particularly for twocomponent base-hardeners. Finally, it is to spray them onto the parts, combining precision, productivity, homogeneity of thicknesses and colours, low environmental impact, etc. SAMES KREMLIN, one of the major players in this market, relies on a wide range of proven technologies from other industrial sectors: automotive of course, but also construction, aeronautics, railways, furnitures, household appliances, etc.
From manual guns to automated industrial lines
In the agricultural machinery segment, SAMES KREMLIN equips from small-scale trailer manufacturers to world-class companies. For the former, it supplies manual electrostatic spray guns for painting large flat parts with high productivity (Airmix® range) or parts with complex geometry where the smallest gap must be protected (Airspray range). In the latter case, it sets up particularly innovative industrial lines. One example is an automated installation in Northern Europe that applies powder paint to beet harvesters. It includes a conveyor belt, a powder booth, a powder conveying and recycling system, a colour change module, pre-touch and touch-up stations and an oven. “Such a line paints simple shaped parts at a very high rate,” says Christophe Denis-Bosio, Global Business Development Manager. “In addition, a part recognition and measurement system place the guns at the optimum distance, without human intervention”. Another example of a SAMES KREMLIN installation for the application of liquid paints is the four booths installed on platforms for the top-down treatment of large elements. From these gondolas, the operators monitor their movements as well as the complete control of the paint lines, without having to return to the ground.
Pumping, mixing, spraying, the key links in the paint chain
To measure the high technical nature of the painting installations, it is best to describe their three main components: pumping, mixing and spraying. Bases and hardeners are transported from their original storage to a mixer by pumps. The hardener must be kept away from humid environments; it would crystallize, attack the pump seals and clog the injectors. SAMES KREMLIN has eliminated this risk with its Flowmax® technology, which has been on the market for over 25 years in its range of pumps. A patented bellow completely isolates the hardener from the air.
GLOBAL SOLUTIONS FOR WATER TREATMENT
with a complete service that includes system design manufacturing installation technical support chemicals
SPRAY BOOTHS WATER SLUDGE REMOVAL RESIN DEMINERALIZATION SYSTEMS REMEDIATION OF CONTAMINATED SITES BIOLOGICAL SYSTEMS BATCH TREATMENTS PHYSICAL-CHEMICAL SYSTEMS ADSORPTION FILTRATION REVERSE OSMOSIS MEMBRANE SYSTEMS EVAPORATORS BIOGAS BIOMASS SYSTEMS OIL SEPARATORS DESANDERS DESALINATION SYSTEMS PYROCHAR OTHER SYSTEMS CHEMICALS
The second step is the mixer where the base is combined with a hardener. Just like in the kitchen, the correct dosing of the ingredients and the quality of the mixing are decisive for the final result. The Cyclomix™ electronic dosing machine from SAMES KREMLIN meets these requirements. It prepares the required volume of paint in the right proportions. Compared to manual mixing, the advantages are major: repeatability of parameters, no risk of human error, and product losses reduced to a strict minimum. The resulting paint retains constant characteristics. This guarantees the stability of the colour and mechanical properties of the tractors or trailers that come off the line.

Paint droplets and grains charged at 80,000 volts
Finally, spraying uses electrostatic technology: the droplets or paint particles, electrically charged by a high-voltage unit that can reach 80,000 volts, are attracted to the metal parts to be coated and are deposited there. The resulting layer is more even than with a non-electrostatic hand gun, because the charged paint particles repel each other and do not clump together. Most of the paint ends up on the workpiece, without dispersing as it would with a compressed air spray gun. This “transfer rate” - as it is called - is a record 93% for the Nanogun Airmix® manual electrostatic spray gun from SAMES KREMLIN. This low product loss reduces costs, waste volumes and VOC emissions, which improves the environmental balance of the industrial tool. Sames Kremlin is also working on this issue with installations for water-borne paints. “We have already equipped several customers. They generally apply a solvent-based primer for durability, followed by a waterbased topcoat,” concludes Gilles Valbrecq, Sales Director for Industry in France.
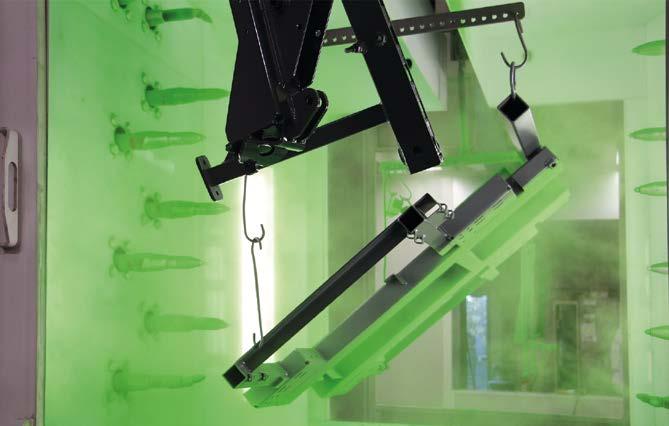
From top to bottom:
- Application with manual electrostatic spray gun for painting large parts with Airmix® high productivity technology.
- Automatic application of powder coatings.
- Electrostatic application.

© SAMES KREMLIN
© SAMES KREMLIN
© SAMES KREMLIN
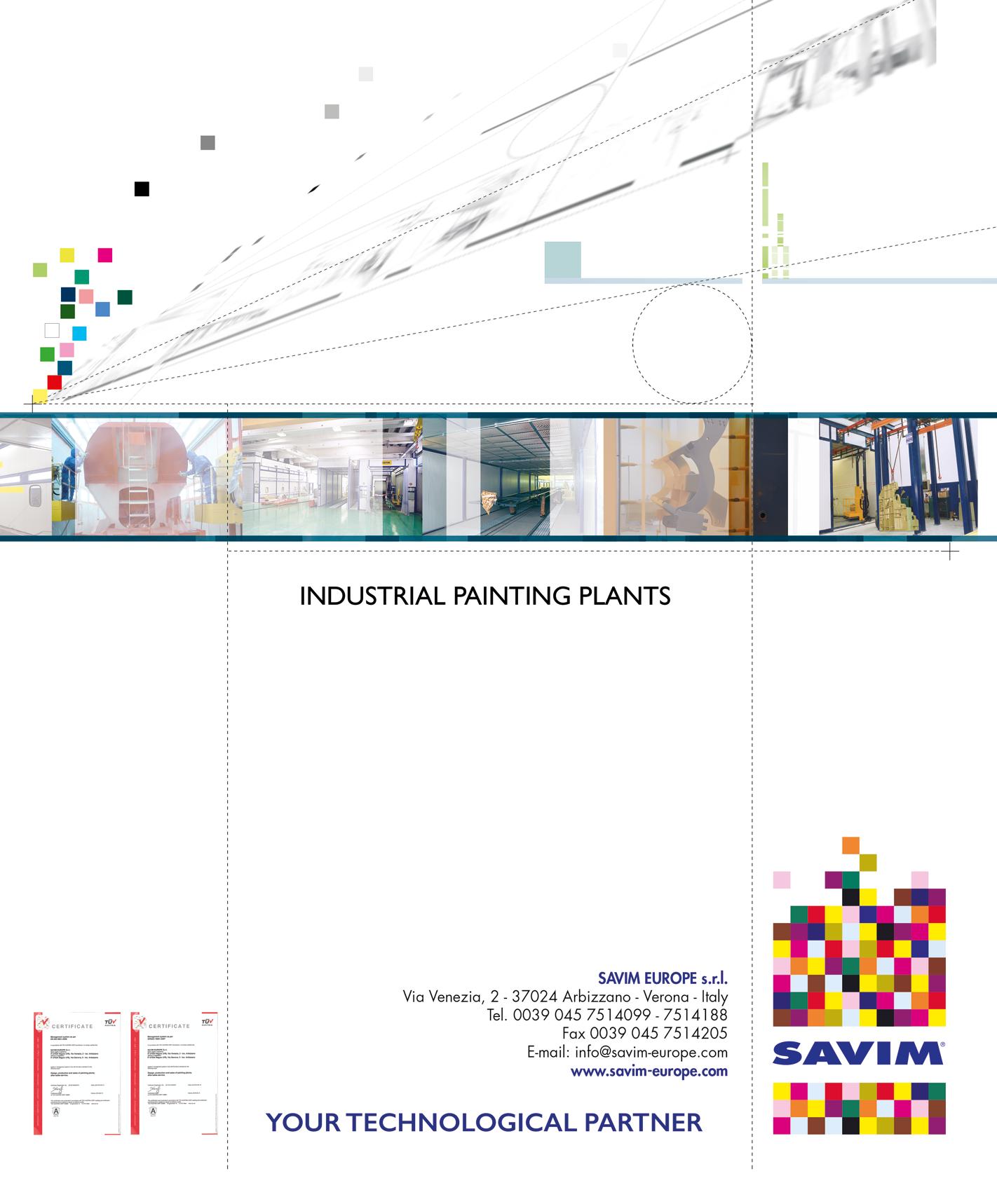