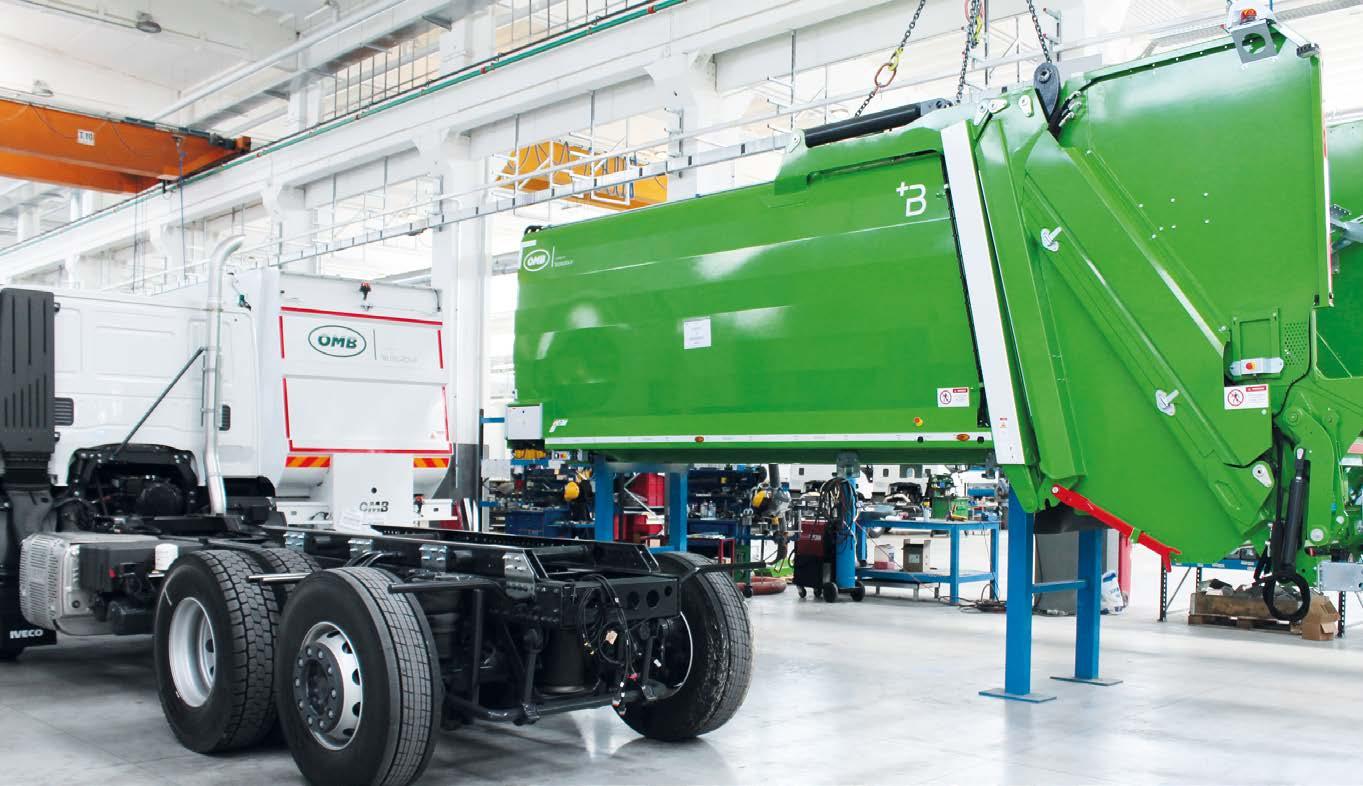
27 minute read
APUESTA POR LA TECNOLOGÍA FOCO NA TECNOLOGIA
En el nuevo taller de pintura de OMB, el innovador sistema de tratamiento del aire instalado se convierte en una ventaja competitiva en el sector de los vehículos para la recogida de residuos urbanos
En un mercado cada vez más competitivo como el de los vehículos para la recogida de residuos urbanos, cuya gestión mueve un volumen de negocios de casi 200 000 millones de euros a nivel mundial, la automatización total del sistema de gestión del proceso de pintura, y, en particular, de la aspiración y filtración de las áreas de aplicación, puede brindar una ventaja competitiva: lo cree firmemente OMB Technology Spa, empresa especializada desde 1961 en la producción de contenedores y vehículos para la recogida de residuos, que ha colaborado con el grupo Rimor (del que forman parte Tekimp y Camit) para crear un nuevo taller de pintura 4.0.
No novo departamento de pintura da OMB o avançado sistema de tratamento de ar torna-se uma vantagem competitiva no setor de veículos para a coleta urbana
Em um mercado cada vez mais competitivo como o dos veículos de coleta urbana, cuja gestão movimenta um volume de negócios de quase 200 bilhões de euros a nível mundial, a automatização completa do sistema de gestão do processo de pintura e, em particular, da aspiração e filtração das áreas de aplicação, pode ser uma vantagem competitiva. A OMB Technology Spa tem certeza disso: especializada, desde 1961, na produção de contentores e veículos para a coleta de lixo, que colaborou com o grupo Rimor (do qual fazem parte Tekimp e Camit) para criar uma nova oficina de pintura 4.0.
Según los datos más recientes del World Bank Group, la organización mundial que busca soluciones sostenibles para combatir la pobreza en los países menos desarrollados, producimos unos 2.000 millones de toneladas de residuos sólidos al año. En todo el mundo, los residuos producidos por persona al día corresponden a unos 0,74 kilogramos, variando de un mínimo de 0,11 a un máximo de 4,54 kilogramos1. La gestión de residuos mueve un volumen de negocios que en 2020 se mantuvo en torno a los 200 000 millones de euros, y se prevé que alcanzará unos 255 000 millones de euros en 20272. A raíz de estos datos, Francesco Garda, jefe de operaciones de OMB Technology Spa de Rezzato (Brescia, Italia), empresa especializada desde 1961 en la producción de contenedores y vehículos para la recogida de residuos urbanos, describe un mercado muy dinámico y en fuerte expansión: «El tema de la ecología es cada vez más crucial tanto en la vida cotidiana como en las agendas de las cumbres mundiales más importantes: el sector de la recogida selectiva, que empezó a desarrollarse en los años noventa, ha experimentado un aumento exponencial por lo que las empresas de recogida y transporte de residuos son cada vez más numerosas y cada vez más desarrolladas en cuanto a tecnología y prestaciones».
1 https://datatopics.worldbank.org/what-a-waste/trends_in_solid_waste_management.html
2 https://www.marketreportsworld.com/global-solid-waste-management-market-17765463 De acordo com os dados mais recentes divulgados pelo World Bank Group, organização mundial que busca encontrar soluções sustentáveis para combater a pobreza nos países menos desenvolvidos, produzimos cerca de 2 bilhões de toneladas de resíduos sólidos por ano. No mundo inteiro, o lixo produzido por pessoa por dia corresponde a aproximadamente 0,74 quilogramas, variando entre 0,11 e 4,54 quilogramas1 .
A gestão dos resíduos movimenta um volume de negócios que, em 2020, foi de cerca de 200 bilhões de euros e deve atingir cerca de 255 bilhões de euros até 20272 .
Em posse desses dados, Francesco Garda, diretor de operações da OMB Technology Spa, em Rezzato (Brescia, Itália), especializada desde 1961 na produção de contentores e veículos para coleta de lixo urbana, descreve um mercado muito dinâmico e em rápida expansão: “O tema da ecologia é cada vez mais predominante, desde a vida cotidiana até a agenda das mais importantes cúpulas mundiais: o ramo referente à coleta seletiva, que se desenvolveu a partir dos anos 90, viveu um aumento exponencial e, por isso, as empresas do setor de coleta e transporte de lixo se multiplicaram e se aprimoraram, em termos de tecnologia e desempenho ”.
1 https://datatopics.worldbank.org/what-a-waste/trends_in_solid_waste_management.html 2 https://www.marketreportsworld.com/global-solid-waste-management-market-17765463
© ipcm
OMB Technology está especializada en la producción de contenedores y vehículos de recogida de residuos.
Vista panorámica de las cabinas: en primer plano, la cabina de arenado.
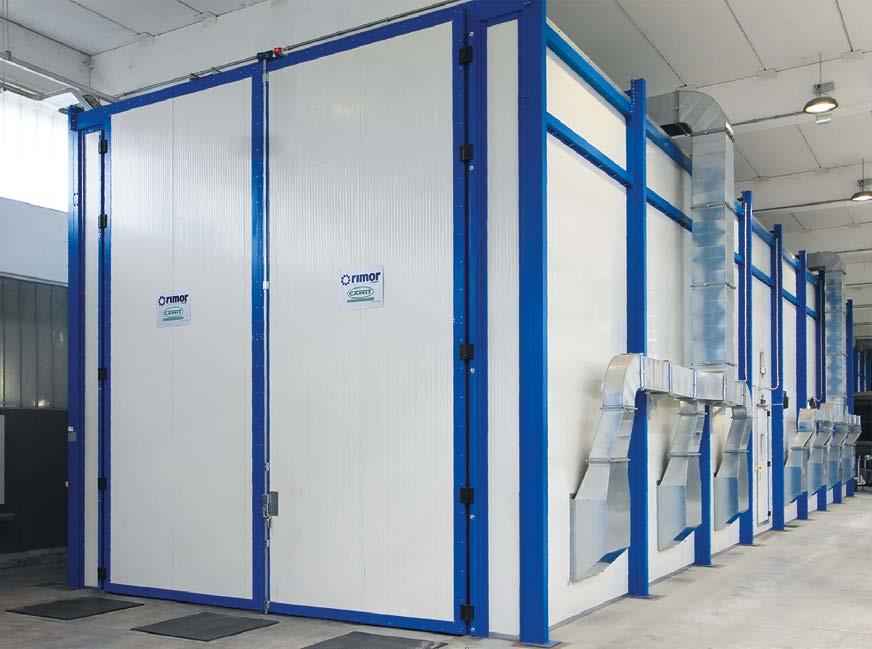
A OMB Technology é especializada na produção de contentores e veículos para coleta de resíduos.
Visão geral das cabines: em primeiro plano, a cabine de jateamento.
© ipcm
© ipcm
Interior de la cabina de arenado: zona A. Interior da cabine de jateamento: zona A.
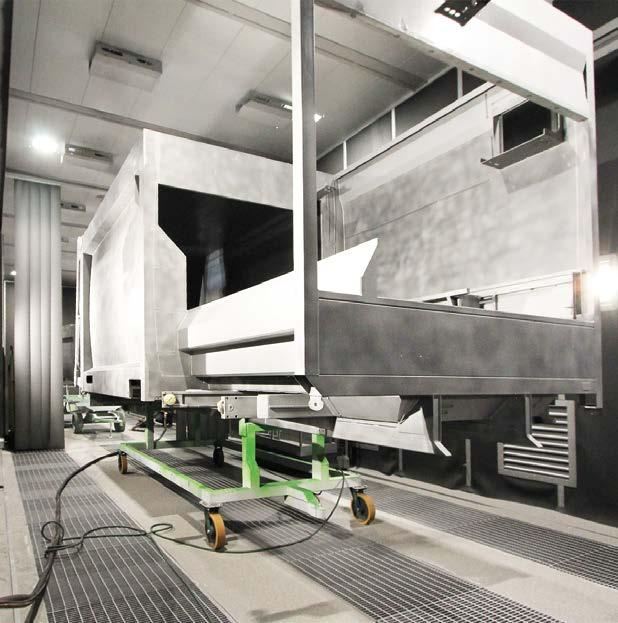
El soplado antes de la pintura. Sopragem antes da pintura.
Desde hace 60 años, OMB produce para este sector contenedores estáticos de chapa de diversos tipos y camiones para la recogida de residuos con sistema de carga lateral, trasera y puerta a puerta, así como los llamados vehículos satélites o minicompactadores ligeros que recogen los residuos y los descargan en el compactador nodriza el cual los llevará al vertedero. «Nuestra empresa es renombrada en el sector por haber concebido y realizado el primer sistema de recogida vial de carga lateral con un vehículo monoperador y contenedor estático». En 2014, la empresa de Brescia fue adquirida por Busi Group, líder en Italia en cuanto a fabricación de productos y sistemas de recogida, compactación y transporte de residuos, y con distribuidores presentes en todo el mundo, desde Sudamérica hasta los Emiratos Árabes y Singapur. «La oferta a nivel mundial de un paquete completo es la clave del éxito de nuestro grupo, que aún es relativamente joven, pero con grandes expectativas para el futuro. Tratamos de estar a la altura de los tiempos y ofrecemos productos tecnológicamente avanzados: todos nuestros equipos están interconectados y son gestionados por un sistema informático central que recopila los datos de la recogida de residuos, una función especialmente apreciada en el extranjero y que también en Italia se está solicitando cada vez más. Es una consecuencia de la integración de sistemas desarrollados con un enfoque de Industria 4.0 también en el sector de la gestión de residuos y que se refleja, a su vez, en los procesos de producción en nuestra fábrica». La mudanza a nuestra nueva sede de Rezzato en 2020 nos brindó la posibilidad de actualizar las instalaciones y ponerlas a punto de acuerdo con los parámetros más innovadores de la cuarta revolución industrial. «En el marco de este proyecto – continúa Garda – decidimos renovar el anterior taller de pintura3 y para ello decidimos colaborar con Rimor Srl, hoy propietaria de la marca Camit y responsable de la dirección y coordinación de Tekimp S.r.l., empresas especializadas en instalaciones industriales para el tratamiento de superficies, con el objetivo de crear un entorno de trabajo más sano y seguro, con un alto rendimiento y bajo consumo de energía, completamente gestionado y controlado a través de sistemas informáticos avanzados. Rimor nos ha proporcionado las instalaciones de arenado y pintura 4.0 que complementan nuestra visión de conjunto».
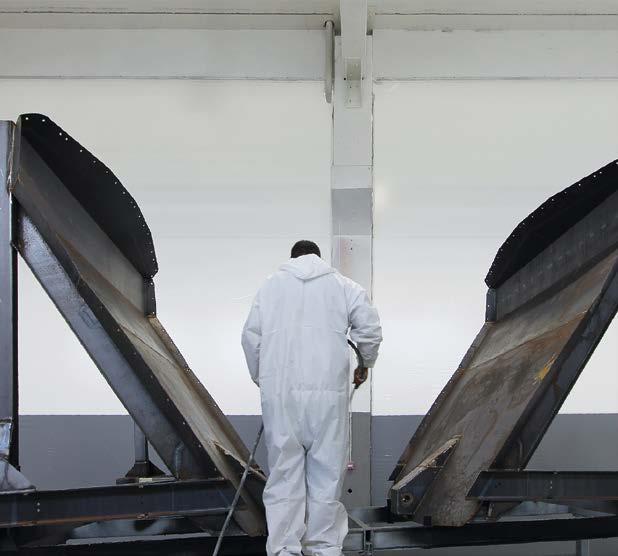
Un paquete completo en nombre de la ecología
Como parte de Busi Group, OMB se ha sumado a otras dos empresas que operan desde hace años en el ámbito de la recogida urbana, trabajando en sinergia con éstas para diseñar y comercializar productos integrados destinados a empresas
3 https://www.ipcm.it/en/open/ipcm/2010/5/30-36.aspx
Há 60 anos a OMB produz, para este setor, contentores estacionários de chapa de aço de diversos tipos e veículos para a coleta de lixo com sistemas de carregamento lateral, traseiro e porta-a-porta, como os veículos satélites, os compressores, que recolhem o lixo e o descarregam no compactador, antes de chegar no depósito de lixo. “Nossa empresa é conhecida no setor por ter projetado e construído o primeiro sistema de coleta urbana com carregamento lateral, com veículo para um operador e contentor estacionário”. Em 2014 a empresa de Brescia foi adquirida pelo grupo Busi, líder na Itália na fabricação de produtos e sistemas de coleta, compactação e transporte de resíduos, e com distribuidores em todo o mundo, da América do Sul aos Emirados Árabes e Cingapura. “A oferta a nível mundial de um pacote completo é o segredo do sucesso do nosso grupo, que ainda é relativamente jovem, mas com grandes expectativas para o futuro. Procuramos estar sempre atualizados e oferecer produtos tecnologicamente avançados: todos os nossos equipamentos são interligados e geridos por um sistema informático central que recolhe os dados da coleta de resíduos, função bastante apreciada no exterior, mas que também vem sendo bastante solicitada também na Itália. Uma consequência da integração de sistemas desenvolvidos para a Indústria 4.0 também no setor da gestão de resíduos e que se reflete, por sua vez, nos processos de produção da nossa fábrica”. A oportunidade de atualizar os sistemas e prepará-los seguindo os parâmetros mais inovadores da quarta revolução industrial foi a transferência, em 2020, para a nova sede de Rezzato. “No âmbito deste projeto - continua Garda - decidimos renovar a já ultrapassada3 oficina de pintura e trabalhamos com a Rimor Srl, hoje proprietária da marca Camit e responsável pela direção e coordenação da Tekimp Srl, empresa especializada em sistemas industriais para o tratamento de superfícies, para criar um ambiente de trabalho mais saudável e seguro, com alto desempenho e baixo consumo de energia, totalmente gerenciado e controlado por avançados sistemas informáticos. A Rimor nos forneceu os sistemas de jateamento e pintura 4.0 que completam esta nossa visão geral“.
Um pacote completo, em nome da ecologia Como parte do grupo Busi, a OMB colaborou com outras duas empresas que atuam há anos no setor de coleta urbana, trabalhando juntas em sinergia para projetar e comercializar produtos integrados para empresas privadas e públicas que
3 https://www.ipcm.it/en/open/ipcm/2010/5/30-36.aspx
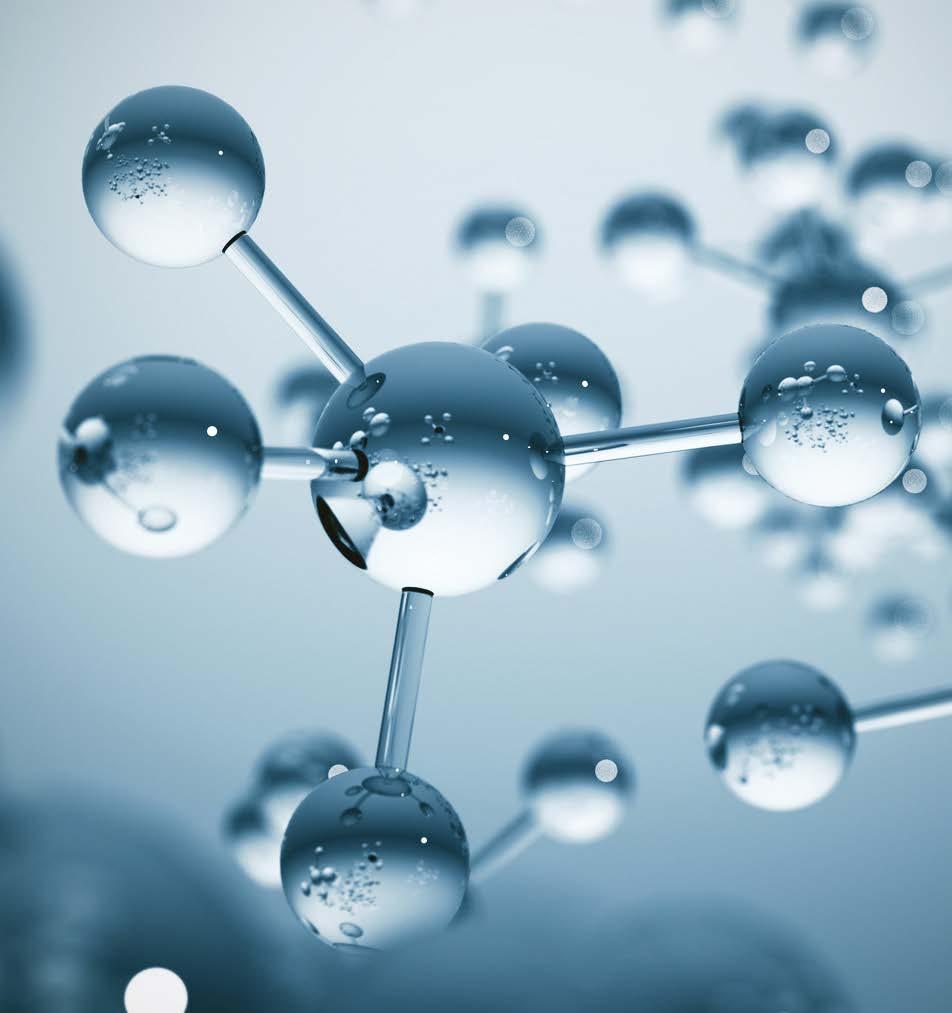
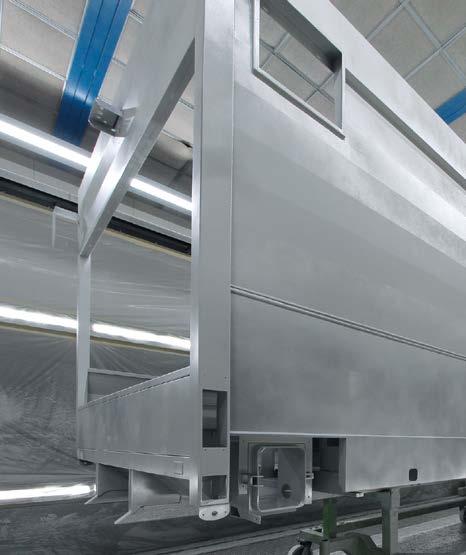
© ipcm © ipcm
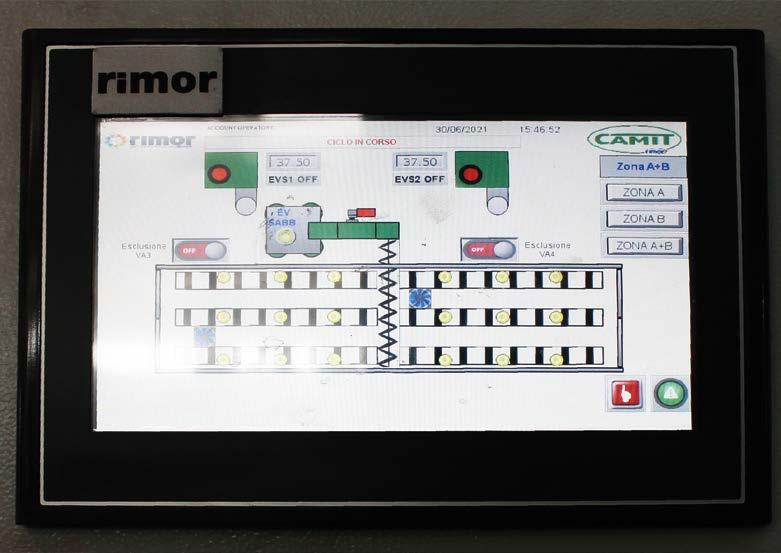
privadas y públicas que se ocupan de la recogida y gestión de residuos con arreglo a los 2 principales sistemas de recogida: vial y en islas ecológicas y puntos de recogida. «Cada empresa del Grupo, que emplea actualmente a unos 400 empleados y que en 2020 alcanzó un volumen de negocios de más de 100 millones de euros, está especializada en la fabricación de productos manufacturados específicos – interviene Erika Busi de Busi Group – para poder ofrecer a nuestros clientes un paquete completo de soluciones. Además de OMB, forman parte del grupo: B.T.E. SpA, situada en Paitona, provincia de Brescia, la cual fabrica desde 1991 autocompactadores y contenedores de gancho y prensas estáticas, y que se encarga de montar los equipos principalmente diseñados y fabricados por las empresas de todo el Grupo (de gancho, basculantes y con pinza); y MEC Spa, una empresa fundada en 1966 en Mondovì, provincia de Cuneo, especializada en la construcción de camiones con pinza, equipos de gancho y de cadenas, remolques industriales y remolques de gancho agrícolas». «Inicialmente, OMB se ocupaba principalmente de la producción de contenedores y camiones para la recogida vial de residuos con compactadores monoperador laterales», precisa Garda. «Para ofrecer una gama aún más amplia de productos y alinearnos con la política empresarial del grupo Busi, que aspira a una propuesta de 360° en particular para los compradores de la rama de mercado que se ha ido transformado poco a poco en recogida puerta a puerta, hemos implementado nuestra gama de vehículos con compactadores traseros y vehículos satélite para la recogida en los pequeños municipios». lidam com a coleta e gestão de resíduos, segundo os 2 principais sistemas de coleta: urbana e através da entrega em estações ecológicas e pontos de coleta. “Cada empresa do grupo, hoje com cerca de 400 funcionários e que, em 2020, atingiu um volume de negócios superior a 100 milhões de euros, é especializada na produção de artigos específicos - explica Erika Busi, do grupo Busi - para poder oferecer aos nossos clientes um pacote completo de soluções. Além da OMB, fazem parte do grupo: B.T.E. Spa, com sede em Paitone, na província de Brescia, que produz, desde 1991, compactadores e contentores móveis e prensas estacionárias e é especializada na preparação dos principais equipamentos projetados e produzidos por empresas de todo o grupo (móveis, basculantes e carregadores); e a MEC Spa, empresa fundada em 1966 em Mondovì, na província de Cuneo, especializada na construção de carregadores, equipamentos móveis e poliguindastes, reboques industriais e reboques agrícolas móveis”. “Inicialmente a OMB fabricava principalmente contentores e veículos para a coleta urbana de resíduos com compactadores laterais, com um operador” - explica Garda. “Para ampliar a oferta de produtos e nos alinharmos com a política da empresa do grupo Busi que visa uma oferta a 360°, especialmente para os clientes do ramo de mercado que, aos poucos, vai se transformando em coleta porta a porta, implementamos a nossa série de veículos com compactadores traseiros e compressores para a coleta em pequenos municípios”.
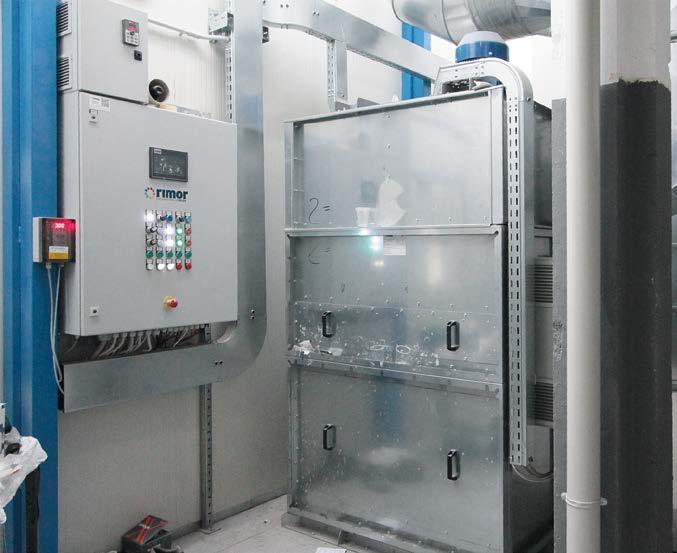
© ipcm
La nueva visión productiva de Busi Group
La entrada de OMB en el Grupo ha dado lugar a importantes cambios en la gestión de los procesos de producción. «Desde que entramos en el grupo Busi – continúa el director de producción – hemos introducido en primer lugar un sistema de producción lean encaminado a la mejora continua de los procesos de producción y, por tanto, de las tecnologías y de los tiempos de producción. En particular, uno de nuestros cuellos de botella era el departamento de montaje que antes estaba estructurado como una isla y que ahora hemos transformado en estaciones operativas en línea, optimizando los tiempos de paso de los productos manufacturados, exactamente como ocurre en la industria del automóvil para el montaje de los vehículos». OMB realiza un seguimiento constante de cada fase del proceso, actualmente simplificado gracias a los instrumentos informáticos integrados en el sistema de gestión empresarial, a fin de garantizar un producto de calidad y fiable desde el punto de vista operativo. «En este sentido, el acabado juega un papel determinante: el recubrimiento de nuestros vehículos debe ser perfecto y homogéneo, sin efecto piel de naranja ni otros defectos comunes, también debe garantizar su duración a lo largo del tiempo y no mostrar trazas de oxidación debidas al contacto con las sustancias más agresivas de los residuos recogidos. Los recubrimiento que se aplican en nuestros vehículos deben superar las 750 horas en las pruebas de niebla salina. Seguimos las especificaciones estándar, pero también podemos satisfacer exigencias especiales si nuestros interlocutores nos las solicitan». El proceso de producción inicia con la recepción de los productos
De izquierda a derecha: - PLC para el control del sistema de ventilación en el interior de la cabina de arenado. - Gracias a las plataformas móviles con control por pedal, los operadores alcanzan fácilmente los puntos más críticos. - El sistema de tratamiento de aire Recube desarrollado por Rimor.
Da esquerda para a direita: - PLC de controle do sistema de ventilação dentro da cabine de jateamento. - Graças às plataformas móveis com controle por pedais, os operadores chegam facilmente até os pontos mais críticos. - O sistema de tratamento de ar Recube desenvolvido pela Rimor.
A nova visão de produção do grupo Busi A entrada da OMB no grupo trouxe mudanças importantes na gestão dos processos de produção. “Quando entramos no grupo Busi - continua o gerente de produção – em primeiro lugar, introduzimos um sistema de produção enxuta, para melhorar continuamente os processos de produção e, portanto, as tecnologias e os prazos de produção. Especificamente, um dos nossos pontos de engarrafamentos era o departamento de montagem, antes estruturado em estação isolada e, atualmente, transformado em postos de operação em linha, otimizando os tempos de passagem dos produtos, exatamente como acontece na indústria automobilística para a montagem de carros”. A OMB monitora constantemente cada fase do processo, agora simplificado pela informática, integrada ao sistema de gestão da empresa, para garantir um produto de qualidade e seguro do ponto de vista operacional. “Neste sentido, o acabamento desempenha um papel decisivo: o revestimento dos nossos veículos deve ser perfeito e uniforme, sem rugosidades e outros defeitos comuns, mas também deve garantir grande durabilidade e não apresentar vestígios de oxidação devido ao contato com as substâncias mais agressivas dos resíduos coletados. Os revestimentos aplicados em nossos veículos devem superar 750 horas em testes de névoa salina. Seguimos especificações padrão, mas também podemos atender a pedidos especiais dos clientes”. O processo de produção começa com a chegada dos produtos
semiacabados, fabricados con una aleación de acero al carbono y Hardox para carpinterías externas; luego se cargan en carros diseñados específicamente para ello y se remolcan con carretillas elevadoras. «Hemos diseñado este tipo de transportador con manipulación manual porque nos garantiza la flexibilidad y la velocidad necesarias ya que tratamos artículos diferentes entre sí: sus volúmenes pueden oscilar entre 10 y 30 m3». A continuación, las piezas semiacabadas se someten a un lavado manual con hidrolimpiadora y detergentes naturales para eliminar los residuos de aceite y las posibles impurezas; y luego al arenado, un proceso que antes se encomendaba a terceros y que ahora se ha internalizado tras la mudanza al nuevo establecimiento. «Con Rimor - continua Garda - hemos realizado un estudio específico para identificar el sistema de filtración adecuado que pudiese garantizar la ausencia de contaminaciones superficiales después del arenado. Obtenemos artículos con un grado de rugosidad de 2,5 e intervenimos tras el arenado solo con algunas operaciones para mejorar el soporte y que provienen, también en este caso, del sector de la automoción, como son el pulido, el soplado y el estucado antes de la pintura con ciclo de dos capas (imprimación + esmalte) completamente al agua, y el sellado de los intersticios después de la cocción».
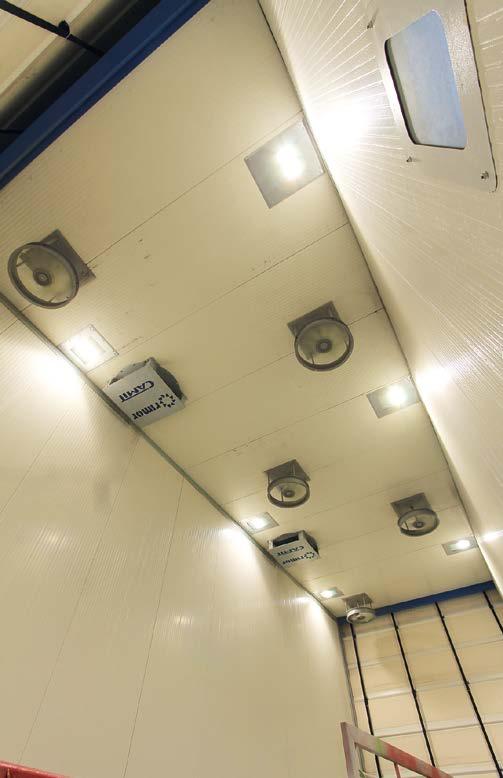
© ipcm
Los dispositivos de ventilación de techo dentro del horno de cocción.
semiacabados, feitos de liga de aço carbono e Hardox por empresas externas, e carregados em carrinhos projetados ad hoc e rebocados por empilhadeiras. “Projetamos este tipo de transportador com movimentação manual porque nos garante a flexibilidade e rapidez necessárias, pois não tratamos produtos iguais: as cubagens podem variar de 10 a 30 m3”. As peças semiacabadas passam pela lavagem manual com lavadora de alta pressão e detergentes naturais para eliminação de resíduos de óleo e outras impurezas, e ao jateamento, processo anteriormente feito por terceiros, e internalizado depois da transferência para a nova fábrica. “Com a Rimor - continua Garda - realizamos um estudo específico para identificar o melhor sistema de filtração que ajude a garantir a ausência de contaminação da superfície após o jateamento. Conseguimos produtos com grau de rugosidade de 2,5 e fazemos pós-jateamento apenas com algumas operações de beneficiamento do suporte, também emprestadas do Os dispositivos de ventilação de teto dentro setor automotivo, como lixamento, do forno de cozimento. sopragem e rejunte antes da pintura, com ciclo de duas demãos (primer + esmalte) totalmente à base de água, e a vedação dos interstícios após o cozimento“.
Instalaciones compartimentadas de arenado y pintura para lograr la máxima capacidad de producción
Desde la fase de diseño hasta la puesta en marcha de la nueva instalación de pintura ha transcurrido un año. «Unos de los aspectos más críticos del estudio de las dos instalaciones de arenado y de pintura para OMB era el problema de la disponibilidad de espacio», interviene Alessandro Avonto, Director Ejecutivo de Rimor. «En el taller de pintura se tratan tanto los cajones, es decir, la parte más consistente del compactador, como también accesorios de distintos tamaños, como, por ejemplo, el sistema de expulsión. Disponíamos de una nave de 200 m de longitud y propusimos optimizar la instalación Sistemas compartimentados de jateamento e pintura para a máxima capacidade de produção Um ano se passou desde a preparação do projeto, até a inauguração da nova fábrica de pintura. “Um dos aspectos mais críticos do estudo dos dois sistemas de jateamento e pintura para a OMB foi o problema de disponibilidade de espaço” - disse Alessandro Avonto, diretor executivo da Rimor. “Na oficina de pintura, são tratados tanto as lixeiras, que é a parte mais consistente do compactador, quanto vários tamanhos de acessórios, como por exemplo o sistema ejetor. Tínhamos um galpão de 200 m de comprimento e decidimos otimizar os sistemas de jateamento
de arenado y la de pintura disponiéndolas en una estructura compartimentada: la instalación manual de arenado tiene una longitud de 23 m y una doble cabina que permite arenar 2 compactadores al mismo tiempo con un consumo de energía reducido». El sistema de aireación desarrollado por Rimor se basa en la regulación de un flujo vertical con aspiración downdraft. «Esta solución – confirma Avonto – evita tener que instalar puertas intermedias para dividir la cámara de trabajo: es posible arenar al mismo tiempo en las dos zonas de trabajo comunicantes, sin riesgo de contaminación recíproca, ya que el sistema de aspiración con flujo vertical permite filtrar el aire en cada una de las dos zonas delimitadas de arenado. El mismo principio se ha aplicado en la cabina de pintura de 15 m de largo y dividida en 5 zonas y con un consumo de energía reducido: el sistema de gestión central activa o desactiva la ventilación de cada zona según el tipo de producto manufacturado que se va a pintar, una flexibilidad que garantiza las máximas prestaciones con el mínimo consumo de energía. También la aplicación de los principios de fluidodinámica en el horno permite impulsar la misma cantidad de aire, independientemente del tipo de producto que se introduzca, gracias a la presencia de dispositivos multiplicadores del aire producido por el generador. De este modo, se puede conseguir un curado homogéneo de toda la superficie de la pieza». e de pintura com uma estrutura compartimentada: o sistema de jateamento manual, por exemplo, tem 23 m de comprimento, com uma cabine dupla que pode jatear dois compactadores ao mesmo tempo, com consumo de energia reduzido“. O sistema de ventilação desenvolvido pela Rimor é baseado na regulação de um fluxo vertical com aspiração downdraft. “Esta solução - diz Avonto - evita a instalação de portas intermediárias para dividir a câmara de trabalho: é possível jatear simultaneamente nas duas áreas de trabalho comunicantes, sem o risco de contaminação recíproca, pois o sistema de aspiração com fluxo vertical permite filtrar o ar em cada uma das duas áreas circunscritas de jateamento. O mesmo princípio foi aplicado na cabine de pintura de 15 m de comprimento e dividida em 5 zonas, com menor consumo de energia: a ventilação de cada zona é ativada ou desativada pelo sistema de gestão central, dependendo do tipo de produto a ser pintado, uma flexibilidade que garante o máximo desempenho, com o mínimo consumo de energia. A aplicação dos princípios de dinâmica dos fluidos no forno também permite introduzir a mesma quantidade de ar, independentemente do tipo de artigo introduzido, graças aos dispositivos multiplicadores do ar produzido pelo gerador. Desta forma, é possível obter uma secagem uniforme em toda a superfície da peça”.
© ipcm
La cabina de pintura (a la izquierda) y el horno de cocción. A cabine de pintura (à esquerda) e o forno de cozimento.
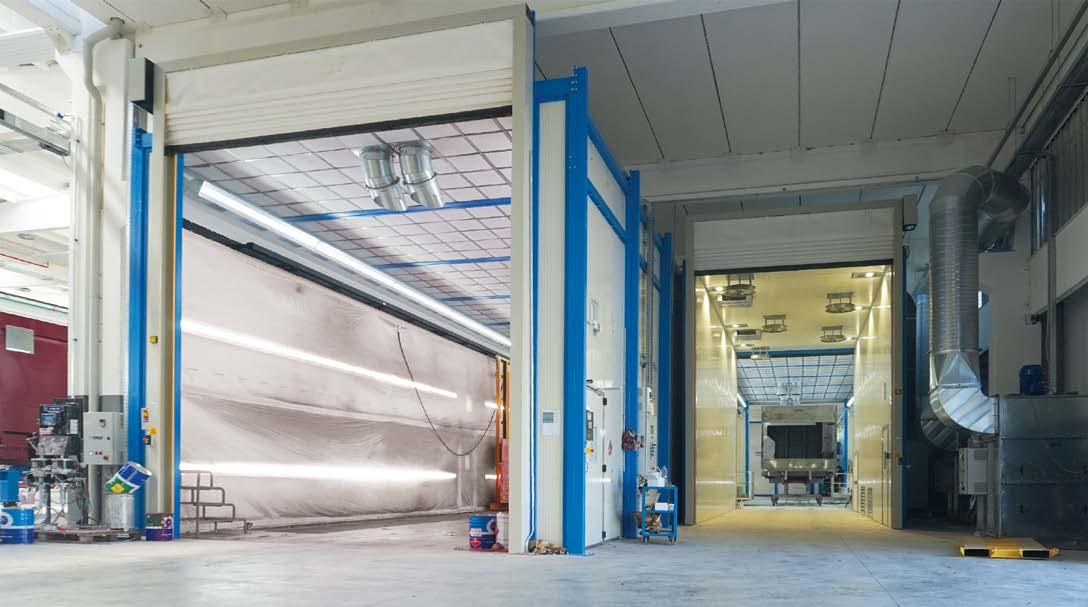
© ipcm
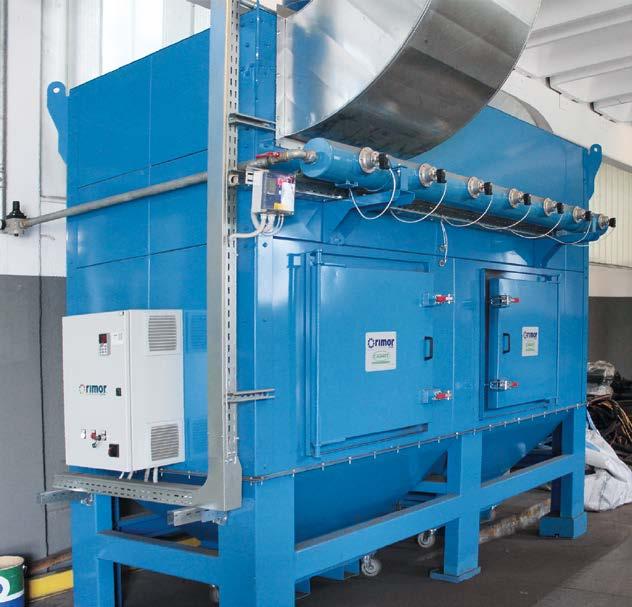
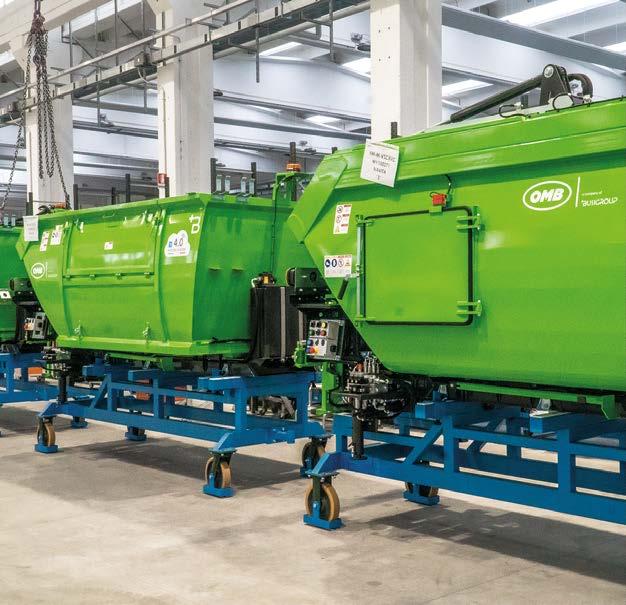
De izquierda a derecha: uno de los sistemas de filtración instalados en el establecimiento de OMB, algunos cajones pintados y los vehículos de recogida de residuos urbanos OMB que salen del sector de montaje.
Da esquerda para a direita: um dos sistemas de filtragem instalados na OMB, algumas caçambas pintadas e veículos de coleta urbana da OMB saindo do setor de montagem.
Tratamiento del aire: el corazón del concepto de pintura de OMB
«Para este nuevo concepto de pintura nos habíamos planteado objetivos bien precisos», explica Garda. «Además de la eficiencia en términos productivos, apostamos por un sistema que garantizase a nuestros operadores poder trabajar con el máximo confort y total seguridad, con elaboraciones de bajo impacto ambiental y sin riesgo de afectar a los demás departamentos productivos, como el taller adyacente de pintura. Hemos utilizado pues los conocimientos técnicos en el sector aeráulico del personal de Rimor, junto con la especialización de Camit y Tekimp en el ámbito de los tratamientos superficiales. Encomendarles la gestión de todos los dispositivos aeráulicos de la instalación, desde los compresores hasta las bombas de pintura, fue la elección acertada». Avonto describe así el sistema de tratamiento de aire Recube desarrollado por Rimor y elegido para regular los flujos de aire en la cabina de pintura de OMB: «Se trata de una tecnología que hemos patentado y que ya se ha instalado en muchas empresas de los sectores más dispares. La instalación está formada por un dispositivo monobloque con motor de eje vertical en el que se han eliminado las juntas antivibratorias, las conexiones y los tubos y, por consiguiente, O tratamento do ar: o coração do conceito de pintura da OMB “Para o novo conceito de pintura, tínhamos objetivos específicos em mente” - explica Garda. “Além de oferecer mais eficiência em termos de produção, apostamos em um sistema onde os nossos operadores pudessem trabalhar com o máximo conforto e em total segurança, com processos de baixo impacto ambiental e sem risco de prejudicar outros departamentos de produção, como o da montagem, adjacente à oficina pintura. Assim, aproveitamos o know-how da equipe técnica da Rimor no setor aeráulico, junto com a especialização da Camit e da Tekimp na área de tratamentos de superfície. A decisão foi entregar a eles toda a gestão de todos os dispositivos aeráulicos do sistema, desde os compressores até as bombas de pintura”. Avonto descreve o sistema de tratamento de ar Recube, desenvolvido pela Rimor e escolhido para regular os fluxos de ar na cabine de pintura da OMB: “É uma tecnologia patenteada por nós e agora instalada em muitas empresas dos mais diversos setores. O sistema é constituído por um dispositivo monobloco com motor de eixo vertical, em que foram eliminadas as juntas antivibração, as conexões e os tubos e, consequentemente, as dispersões. O sistema
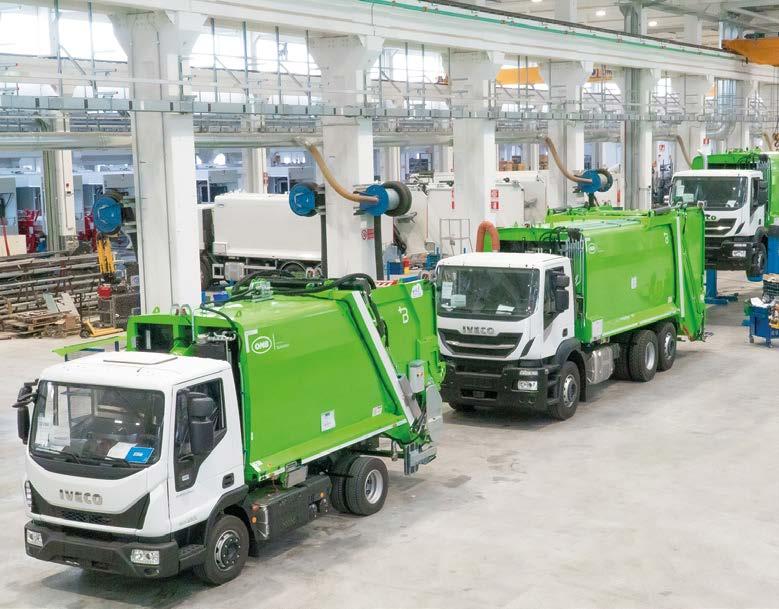
© ipcm
las dispersiones. Este sistema compacto y totalmente insonorizado permite aislar mucho mejor el polvo y garantizar una duración casi ilimitada. Recube nace para asegurar el ahorro de energía, gracias al funcionamiento a baja velocidad sin presencia de codos en las tuberías. El medidor de presión interno se encarga de que el polvo no salga de la cabina y no vaya a depositarse sobre los artículos presentes en la zona de la nave dedicada al montaje, en la que se encuentran las dos cabinas de pintura». Uno de los aspectos más innovadores de los sistemas Rimor son los simuladores fluidodinámicos con los que se pueden visualizar y calcular los flujos dentro de la cámara de trabajo y verificar que el operador reciba la cantidad justa de corriente de aire. «Para garantizar la homogeneidad y la correcta direccionalidad del flujo de aire, hemos optado por cabinas con planos inclinados». La iluminación de la instalación también se ha estudiado meticulosamente para crear un entorno de trabajo más confortable. «Hemos creado un sistema innovador de iluminación con luz natural específica para la pintura, gestionado mediante un PLC que puede regular la intensidad de la luz de manera que no sea molesta ni demasiado tenue. Esto contribuye a mejorar el trabajo del
© ipcm
compacto e totalmente insonorizado permite isolar muito melhor o pó e garantir uma duração quase ilimitada. A Recube foi criada para garantir economia de energia, graças ao funcionamento a baixa velocidade e a ausência de curvas nas tubulações. O medidor de pressão interno evita que o pó saia da cabine e se acumule nos produtos na área de montagem no galpão, onde estão as duas cabines de pintura”. Um dos aspectos mais inovadores dos sistemas Rimor são os simuladores da dinâmica dos fluidos com os quais é possível visualizar e calcular os fluxos dentro da câmara de trabalho e verificar que o operador receba a quantidade certa de corrente de ar. “Para garantir a uniformidade e o correto direcionamento do fluxo de ar, optamos por cabines equipadas com planos inclinados”. A iluminação do sistema também foi cuidadosamente projetada para criar um ambiente de trabalho mais confortável. “Criamos um novo sistema de iluminação com luz natural específico para pintura, controlado por um PLC que regula a intensidade da luz para que não seja muito incômoda, nem muito baixa. Isso melhora o trabalho do operador,
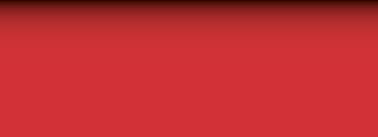
operador ya que sus ojos no se cansarán ni verán sombras o halos superficiales inexistentes. Además, para mejorar la comodidad, el sistema está equipado con plataformas móviles controladas mediante pedal, con las que los operadores se pueden desplazar de forma segura y sin interrumpir su trabajo».
© ipcm evitando o cansaço dos olhos e a distração por sombras ou halos superficiais inexistentes. Além disso, para aumentar o conforto, o sistema é equipado com plataformas móveis controladas por pedais, com as quais os operadores se movimentam com segurança e sem interromper o trabalho ”.
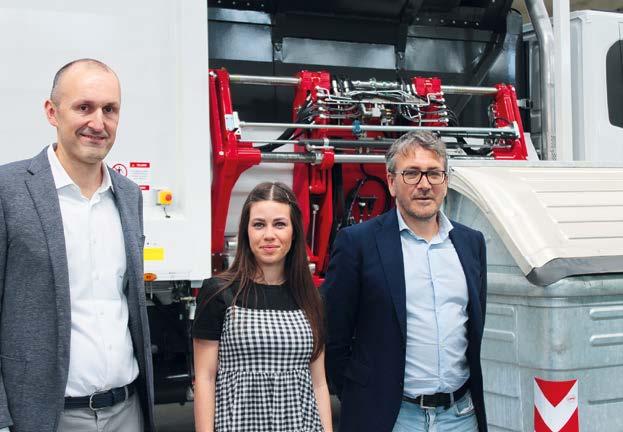
O novo projeto da OMB “O projeto da Rimor nos convenceu porque, em um contexto de fábrica atípico como o nosso, conseguiu incluir todas as tecnologias de engenharia industrial de que precisamos para renovar o sistema de pintura de forma eco-sustentável, saudável e com ótimos resultados de qualidade, mostrando-se flexível para satisfazer as nossas exigências. Após um ano de funcionamento, nenhum tipo de intervenção foi necessário, apenas a manutenção normal, reduzindo os custos de gestão do sistema ao mínimo indispensável e com poucas trocas de peças. Por último, mas não menos importante, também melhoramos a capacidade de produção: se, há um ano, produzíamos um compactador equipado com acessórios por dia, hoje, também graças a um estudo ad hoc focado no sistema de movimentação para otimizar a distribuição do material nos ganchos, fabricamos um compactador e dois compressores por dia, gerenciando três tipos de produtos diferentes, que pretendemos implementar ainda mais”. A introdução de mais automação dos processos de produção faz parte dos projetos futuros da OMB. “Preparamos todos os sistemas para que em um futuro não muito distante possamos automatizá-los rapidamente. A Indústria 4.0 trouxe uma onda de inovações neste setor cada vez mais competitivo: ter atualizado o sistema de pintura sob este prisma, para nós é a vantagem que buscávamos em um mercado cada vez mais competitivo e tecnologicamente avançado”.
El innovador proyecto de OMB
«El proyecto de Rimor nos convenció porque, en un contexto de fábrica no clásico Empezando por la izquierda: Francesco Garda y Erika Busi de OMB Technology junto con Alessandro Avonto de Rimor. como el nuestro, hemos logrado Da esquerda: Francesco Garda e Erika Busi, incluir todas las tecnologías de da OMB Technology, junto com Alessandro Avonto, da Rimor. instalación que necesitábamos para renovar la planta de pintura de forma ecosostenible, salubre y con excelentes resultados cualitativos; unas tecnologías que han demostrado ser flexibles y poder satisfacer nuestras necesidades especiales. Después de un año de funcionamiento, no ha sido necesario efectuar ningún tipo de intervención, excepto el mantenimiento ordinario, reduciendo así los costes de gestión de la instalación al mínimo indispensable y con un número limitado de piezas de repuesto que desechar. Sin olvidar que también hemos implementado la capacidad de producción: hace un año producíamos un compactador con todos sus accesorios al día, hoy, gracias también a un estudio personalizado centrado en el sistema de manipulación para optimizar la distribución del material en los bastidores, producimos un compactador y 2 vehículos satélite al día, gestionando tres tipos de artículos diferentes, y esperamos implementarlo aún más». OMB cuenta con seguir automatizando los procesos de producción en el futuro. «Hemos preparado todos los sistemas para que en un futuro no muy lejano podamos automatizarlos rápidamente. La Industria 4.0 ha traído consigo toda una serie de innovaciones en nuestro sector que cada vez es más competitivo: el haber actualizado la planta de pintura nos brinda en tal sentido la ventaja competitiva que buscábamos en un mercado cada vez más competitivo y tecnológicamente avanzado».