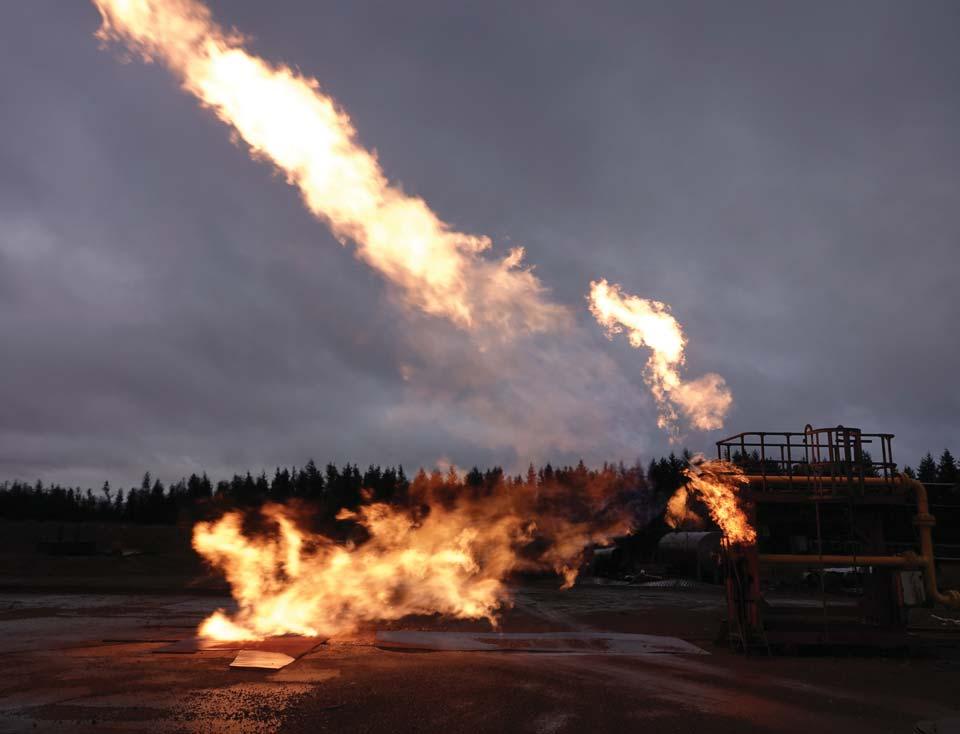
8 minute read
ANALYSIS
Designing a New Standard of Safety into Onshore Passive Fire Protection
Richard Holliday
PPG Protective and Marine Coatings – Warrington, United Kingdom
holliday@ppg.com
The adoption of international standards covering jet fi res has been slow, but agencies are responding to a real and critical need, writes Richard Holliday, Global Director – Hydrocarbon PFP, PPG Protective and Marine Coatings.
The onshore energy and petrochemicals sector are defi ned by the strength of its safety culture, but it has only latterly begun moving towards adoption of the highest fi re protection standards. For many years, industry practice has been to protect onshore assets primarily against pool fi res but recently the industry has begun to recognise the need to adopt standards covering the more dangerous hazards of jet fi res. This is particularly important in light of the huge increase in gas processing, transport and handling, whether from US shale gas extraction, growth in Liquefi ed Natural Gas (LNG) or other sources such as hydrogen. The expansion of gas import and export capacity creates hazards diff erent from those in refi neries or petrochemical plants. In order to adequately protect these plants designers and operators need to consider protection from jet fi res at a design level.
Emerging standards
The requirement for a standard against jet fi res came to the public’s attention after the Piper Alpha disaster in the North Sea in 1988, in which 165 people on the platform and another two from the rescue boats lost their lives. One of the key fi ndings of the subsequent enquiry was that the passive fi re protection (commonly referred to as “fi reproofi ng”) in place on the platform did not survive as long as predicted. In fact, the jet fi re on Piper Alpha destroyed the fi re protection materials within a matter of minutes, rather than one to two hours that most systems were designed for. For the off shore industry it was a wake-up call. Much research was carried out into the behaviour of jet fi res with many large-scale experiments carried out to study their eff ects. However, such testing is prohibitively expensive and in the early 1990’s work started on a more economical and repeatable test that could become a standard for testing for passive fi re protection materials. The resulting standard passed through several iterations within the UK Health and Safety Executive before being passed across to an ISO working group, resulting in the ISO’s 22899-1 standard. This became an internationally recognised standard that could be
© PPG Industries
Medium scale jet fi re test to ISO 22899-1. used to test the ability of fi reproofi ng to withstand jet fi re, and today it is still the only recognised standard of its type. For many years the onshore industry paid much less attention to jet fi res than to pool fi res, despite the fact that these types fi re can happen anywhere, onshore or off shore and the result is a credible fi re scenario that should be mitigated against. Fire protection in the onshore market has largely been driven by the American Petroleum Institute’s API 2218 standard which did not address jet fi res until an incident at Valero’s McKee Texas refi nery in February 2007 that escalated signifi cantly because jet fi res were much more far-reaching than the pool fi res for which the facilities fi re protection was designed. Again, fi reproofi ng was installed, but in the wrong place and to the wrong performance standard. The main body of API 2218 is only applicable to pool fi res but the revised standard now includes an annex stating that asset owners should consider jet fi res in the design of their fi reproofi ng.
Industry trends
Until recently, the lack of applicable standards for jet fi res has meant that many manufacturers of fi reproofi ng materials developed products that were optimized for pool fi res. Even at a time when the industry was recognizing that hazards were becoming more severe, PFP manufacturers were designing materials for the less severe fi re because jet fi re resistance standards did not exist in any meaningful way. These pool fi re resistant materials are already in use on the US LNG export facilities that are currently in operation, but when the potential risks are considered in detail, these coatings do not accurately address the hazards present at these facilities. A gas facility will have a low risk of pool fi re but a very high risk of jet fi re but some designers will still specify coatings designed only for pool fi res because they are less costly than those designed to resist jet fi res. It is important to note that the intensity and high momentum of jet fi res means that water deluge is not eff ective as a means of active fi re protection. The jet will punch straight through water and will heat up the steel, vessel and pipe work very quickly to the point where rupture and resultant BLEVE is a real risk. Another problem is that deluge may extinguish the fi re without stopping the leak, which can result in clouds of gas that can then ignite and cause an explosion which is potentially even more lethal than the jet fi re, risking damage to active fi re proofi ng or passive fi re protection if it’s not resistant to explosion. There is no compulsion for fi reproofi ng manufacturers to design against the most hazardous potential event and designing against jet fi res is certainly more complicated and potentially more costly than for pool fi res alone. Part of the brief in developing our new high-performance fi reproofi ng coating PPG PITT-CHAR® NX, was that it must have a minimum of 30 minutes’ jet fi re resistance. This ties into the API standard 520-1 which recommends that an operator should be able to de-pressurize their
plant quickly enough to halve working pressure in 15 minutes. Designing a good jet fi re system requires a highly robust char which is still open and lightweight structure for optimal insulation. PITT CHAR NX sits in a ‘sweet spot’ with very eff ective insulating char at a lower thickness than pool fi re-only products, but still providing good jet fi re resistance. By using very high temperature resistant carbon fi bre mesh, we were able to extend the jet fi re resistance of PITT CHAR NX to up to four hours while keeping the thickness and weight of the system very low.
Jet fi re fi rst
Mostly recently, Underwriters Laboratories (UL) which underwrites safety standards at US onshore chemical and energy plants has agreed to adopt the ISO 22899 standard for jet fi re testing. PPG began discussions with UL to test PITT CHAR NX to the UL 1709 Revision 5 and has achieved the fi rst full listing of a fi reproofi ng product against jet fi re from multiple durations and multiple jet fi re scenarios. The process of testing for jet fi res has undergone its own evolution from some simple observation providing a basic recognition to a minimum of three samples of each type of certifi cation sought. The test standard includes diff erent confi gurations for structural steel, piping, walls, decks and bulkheads, each requiring a series of tests. When preparation of test specimens, witnessing of the test, assessment and certifi cation are included the total could easily cost $50,000 per test. It’s a process that requires a large investment to be done properly and it’s only by completing a full series of such tests that PPG gained the very comprehensive level of certifi cation that PITT CHAR NX has achieved. The test result recognizes that it is not necessary to select one mesh type for jet fi res and another for pool fi res and the UL approval for jet fi res means PITT CHAR NX future-proofs customer choices because it is compliant with the latest revision 5 standard and the ISO is the only jet fi re test standard recognized by UL. In addition, PITT CHAR NX is designed to withstand explosion forces that may preceded jet fi res, even though this is another area where currently there is no recognized test standard, though one is being developed within an ISO working group.
Large Scale Jet Fire Test at Spadeadam research facility.
© DNV-GL
A new way forward
Developments in safety that have taken place in the off shore industry over decades have demonstrated how standards can help to eff ectively manage risk but this needs to happen more and faster in the onshore market. It remains an issue of concern that 31 years after the Piper Alpha disaster, the industry is still only at the drafting stage of an explosion resistance test method for onshore fi re protection materials. Energy is an industry that sometimes moves slowly in adopting new or best practices but development of new standards and recognition by US agencies of international standards for resistance to jet fi res is an encouraging step forward. The fact there has been, until recently, no published guidelines for jet fi re resistance is not a defence that asset owners can use when it comes to protecting their people and assets to the highest degree possible. ‹
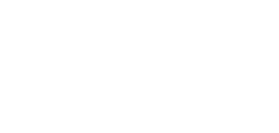
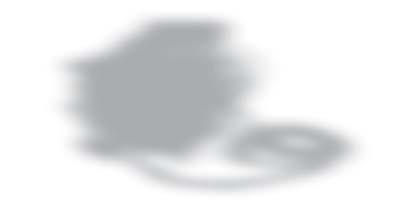

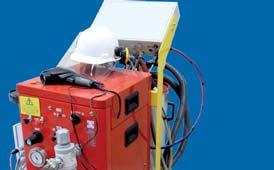
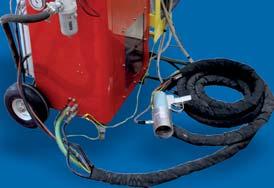



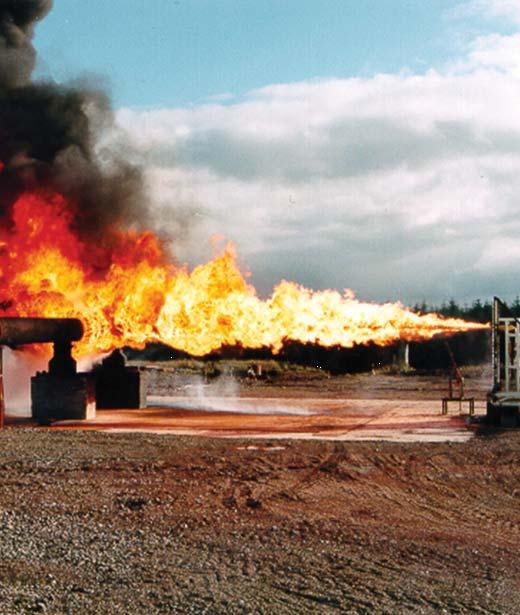
Multi-directional jet fi re release from leaking fl ange joint.
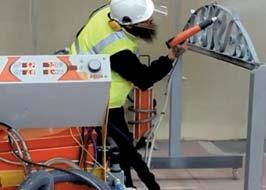
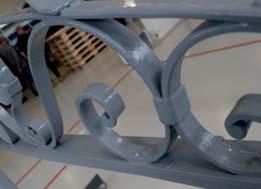
© DNV-GL