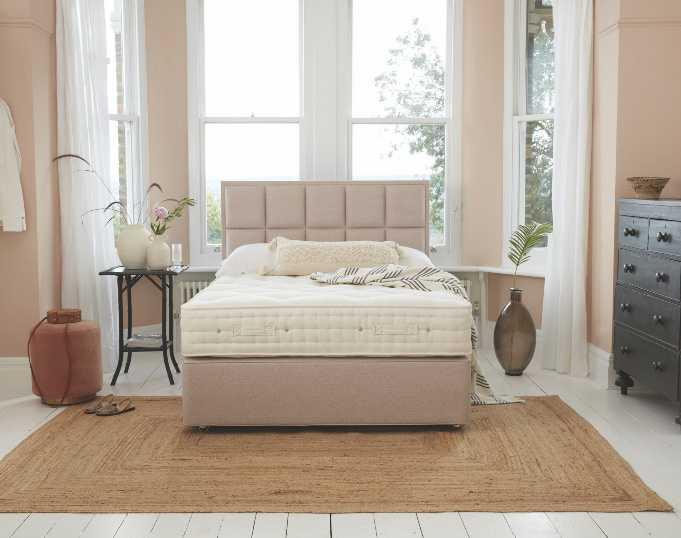
4 minute read
Sustainability
Comfort with integrity
Hypnos continues to introduce initiatives
In handcrafting luxury beds and mattresses, Hypnos provides retailers with comfortable, sustainably made beds for their customers. Recently presented with the Sustainability Award by the National Bed Federation, Hypnos was recognised for its commitment and passion in all areas of sustainable design and manufacture.
The ethos at Hypnos centres around creating comfort with integrity: products that are great for sleep and well-being and better for the environment. Whether it’s investing in developing new recyclable carbonneutral packaging, using only sustainable and natural materials, or generating its own energy with biomass boilers, reducing its environmental impact is a core target.
Collaboration is key to this success, and this includes being part of The Woolkeepers, a quality assurance platform for traceable British wool – undervalued for decades. It brings together wool farmers with the supply chain to ensure high-quality wool products and prompt, fair payment so that farmers can plan for the future. Meanwhile, Red Tractor certification gives consumers confidence in the standards of farming.
‘We are extremely proud to be the first bed maker to win the NBF Sustainability Award. Breaking new ground when it comes to sustainable bed design is where we lead the way. Take our unique collaboration with John Lewis: we created two new sustainable mattress collections using wool provided by its award-winning Waitrose sheep farms, ensuring a known ethical supply chain – very important to the John Lewis and Waitrose consumer,’ says James Keen, Hypnos ceo.
‘We also presented our new Orthos Support collection at the Bed Show, which has been redesigned in line with our values and as the next chapter of our Origins story. This popular firmsupport range uses a comprehensive mix of sustainable fibres including organic cotton, flax and hemp, breathable eOlus (recycled fibres) and layers of British wool, traceable to Red Tractor assured farms.’
Hypnos has also begun a five-year partnership the Eden Project. ‘This is incredibly exciting for us. As our official charity partner, we’ll be collaborating to enhance our consumers’ knowledge and understanding on issues around climate change and sustainability, and that of our employees and stakeholders. The partnership will influence new, forwardthinking ways to integrate sustainability into all aspects of our business and our products too. There’s lots planned – just watch this space,’ he says. Visit: www.hypnosbeds.com
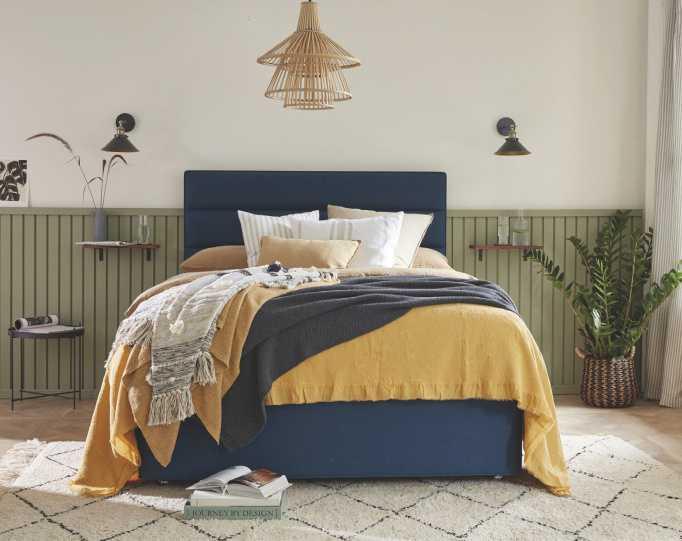
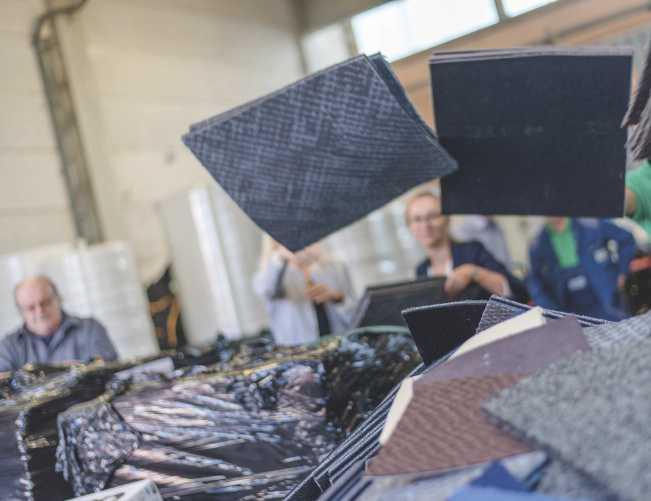
Second life
Production waste can make new products

Residues are collected, shredded, then flocculated. All this is done mechanically, without the use of chemicals.
Object Carpet has succeeded in recycling 100% of the materials used to make carpet tiles in a single, economical process. Its tiles are designed specifically to be fully recyclable, while the soundproofing mat that is produced gives a new lifecycle to production waste. The company is now investing in a fully sustainable production cycle at its Krefeld, Germany site.
‘We’re taking matters into our own hands. Conserving and not wasting resources, recycling products – protecting the environment is firmly embedded in our company’s DNA,’ says

Production waste can be turned into new products Daniel Butz, Object Carpet md. ‘By 2024, we want all of our new products to be part of the circular economy. This means fully recyclable designer carpets without an environmental footprint. We will thus be closing the environmental loop.’
Avoiding waste, preserving resources and reducing emissions has always been the guiding principle since Butz’s father Roland set up the company in 1972. Object Carpet began early on to design its carpets, rugs and carpet tiles in such a way that they only contain clean materials from the circular economy and recyclable substances without any toxic chemical compounds. They have been free from bitumen, latex and PVC since 2017 and are fully recyclable as a secondary raw material. This means that no chemical recycling processes are required either, something that can only be achieved with clean, circular materials. That is because the entire product is always recycled in a single process and does not undergo laborious and timeconsuming separation, which may involve transportation to several locations.
Instead, remnants such as trimmings from finished goods, cut-offs from edges, leftover yarn, test pieces, material formulations, backing material and rejects are collected up and shredded. These are then turned into a secondary raw material in a purely mechanical process involving no chemicals. This secondary raw material is composed solely of the materials that were fed in – nothing is added or generated as waste. The material is then heated and cooled to produce stable matting, which is cut into individual pieces and given a new lease of life as a soundproofing building material.
Three-quarters of all the products in the company’s collection are made from 100% recycled yarn at present, including Econyl in its Places of Origin collection.
‘By designing products to be recyclable, we want to save resources and combat waste. Protecting the environment, the human race and the natural world is always our top priority,’ says Butz.
The first new product with an unlimited number of lifecycles will soon be making its debut, explains Lars Engelke, Object Carpet production and development md. ‘We are laying the foundations for a completely sustainable production loop at Krefeld. These are investments that will pay off in the future in every sense of the word. We’re taking an existing building product and turning it into a completely new one, while staying in the same industry and with the same customers.’ Visit: www.object-carpet.com