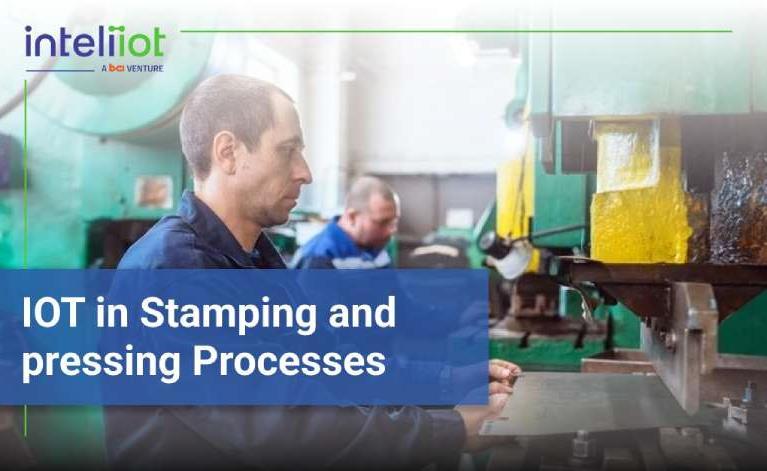
3 minute read
IOT in Press and Stamping processes - Inteliiot
by Inteliiot
Press and stamping processes are manufacturing processes used to shape and form metal sheets or parts using a press or stamping machine. In these processes, a metal sheet or coil is fed into the machine, and a die (or set of dies) is used to shape or cut the metal into the desired shape or form.
The press or stamping machine applies force to the metal, which causes it to deform and take the shape of the die. The dies are typically made of hardened steel and can be customized to produce a wide variety of shapes and forms.
Advertisement
There are several types of press and stamping processes, including:
Blanking: A process where a flat piece of metal is cut into a specific shape, such as a circle or rectangle.
Punching: A process where a whole or other shape is punched out of a metal sheet or part.
Drawing: A process where a metal sheet or part is pulled through a die to create a cylindrical or other complex shape.
Forming: A process where a metal sheet or part is bent or shaped to create a specific form or profile.
Press and stamping processes are used in a variety of industries, including automotive, aerospace, appliance, and electronics. These processes are known for their speed, precision, and ability to produce high volumes of parts with consistent quality.
The key performance indicators (KPIs) in press and stamping process typically include:
Cycle Time: Cycle time refers to the time it takes for a press or stamping machine to complete one full cycle, which includes the time it takes to feed the sheet metal, stamp or form the part, and ejects the finished part. Reducing cycle time is often a key goal in press and stamping process optimization, as it can lead to higher throughput and lower manufacturing costs.
Production Rate: Production rate measures the number of parts produced per unit of time. This KPI is useful for assessing the overall efficiency of the press or stamping process and can help identify areas where productivity improvements can be made.
Quality Rate: Quality rate refers to the percentage of parts produced that meet the required quality standards. This KPI is critical in ensuring that the press or stamping process is producing parts that meet customer requirements and can help identify quality issues that need to be addressed.
Scrap Rate: Scrap rate measures the percentage of materials that are discarded as waste during the press or stamping process. This KPI is closely related to quality rate, as defects or errors in the process can lead to increased scrap rates.
Equipment Availability: Equipment availability measures the amount of time that the press or stamping machine is available for production. Downtime can be caused by equipment breakdowns, maintenance, or changeovers, and reducing downtime is critical for maximizing productivity and reducing costs.
OEE (Overall Equipment Effectiveness): OEE is a measure of the overall efficiency of the press or stamping process, taking into account factors such as availability, performance, and quality. It provides a comprehensive view of the performance of the process and can help identify areas for improvement.
Setup Time: Setup time refers to the time it takes to prepare the press or stamping machine for a new production run. Reducing setup time can help increase overall throughput and reduce costs by enabling more frequent changeovers and smaller production runs.
First Pass Yield (FPY): This measures the percentage of products that are produced correctly on the first attempt. It is an important KPI because it reflects the efficiency and effectiveness of the production process, and can also have a significant impact on the bottom line.
Machine Utilization: This measures the percentage of time that the press/stamping machine is in use. A high machine utilization rate can be an indication of an efficient and productive production process.
Throughput: These measures the number of units produced over a specific period of time. It is an important KPI because it reflects the overall productivity of the production process.
By monitoring and analyzing these KPIs, manufacturers can identify areas of improvement in their press and stamping process and make data-driven decisions to optimize their production efficiency and quality.
This process of monitoring and analysis can be enabled by Internet of Things (IOT).
IoT has the potential to revolutionize the press and stamping industry by enabling manufacturers to optimize their processes and improve productivity. By embedding sensors and other devices in press and stamping machines, manufacturers can collect real-time data on the performance of the machines and the quality of the parts being produced.
Some of the ways in which IoT can be used in press and stamping processes include:
Machine Monitoring: By installing sensors on press and stamping machines, manufacturers can monitor machine performance in real-time, collecting data on factors such as temperature, pressure, and vibration. This data can be used to identify potential issues before they cause downtime or quality problems, and to optimize machine performance.
Asset Maintenance: IoT sensors can also be used to monitor the condition of press and stamping machine components, such as bearings and belts, to identify when they are likely to fail. This allows manufacturers to schedule maintenance proactively, reducing the risk of unexpected downtime and improving overall machine reliability.