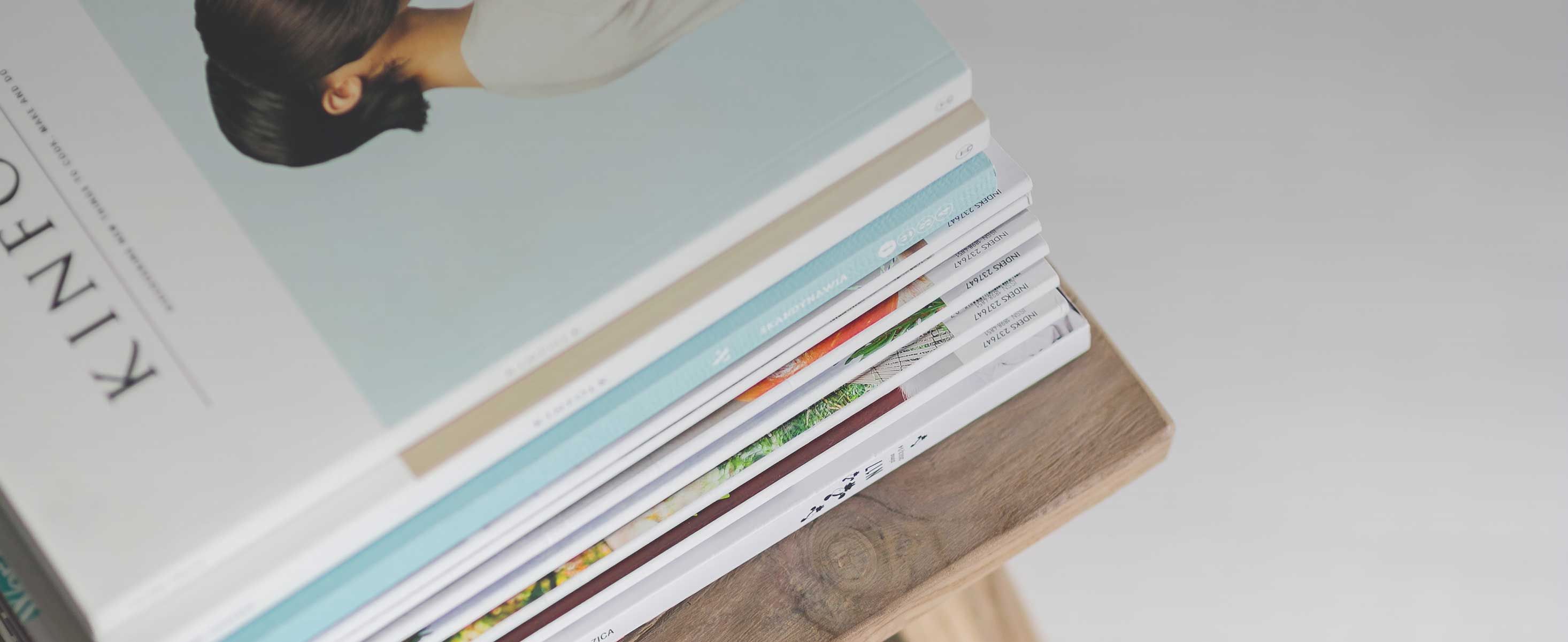
1 minute read
Faster, cheaper, cleaner: Low-Pressure Casting of aluminium parts eliminates process stage
from IM20231EN
Aluminium plays a key role in reducing the weight of a car and thus also helps to reduce fuel consumption. A modern car contains large amounts of aluminium and use of the metal is on the increase. A new casting technology, Low-Pressure Casting (LPC), developed in Norway, makes it possible to cast aluminium bolts with high-quality properties. Casting makes the production of aluminium car parts cheaper and more environmentally friendly and efficient.
It also reduces the amount of production scrap generated. The casting technology has been developed by the aluminium producer Hydro and is carried out under vacuum conditions. To research and demonstrate the capabilities of the technology, Norwegian research organization SINTEF and aluminum automotive manufacturer Raufoss Technology were invited to participate in Hydro's HyForge project. So far, according to the parties involved, the results are promising.
Advertisement
Extrusion
Currently, a car component production line is made up of several production steps, including casting, heat treatment, extrusion and the subsequent forging/ shaping process that ensures that the final product is fashioned with its intended shape. The new process eliminates the extrusion stage.
Currently, it is common for the industry to use extruded bolts in the production of suspension components. This is a costly, time- and energy-consuming process that also generates large volumes of waste. Recent research now shows that the new casting technique actually produces a high-quality material, with fewer defects and fully suitable for eliminating the extrusion phase from the production process. According to the parties involved, this is a breakthrough in the manufacture of aluminium car parts, because the process without the extrusion phase is both faster and cheaper.
The team then investigated how the cast material behaves and what properties it acquires during forging. In addition to laboratory tests, physical experiments have also been carried out in collaboration with the industrial partner of the project, Raufoss Technology. This involves the construction of a demonstrator of a production line for aluminium suspension components using cast materials.
Much more at SciTech >
More: www.sintef.no. www.raufosstechnology.com
HyForge project>