
15 minute read
Additieve vervaardiging met glas voor façade engineering
from IM20201NL
Figuur 1: Additieve vervaardiging met glas: render van een beoogde toekomstige spider-verbinding
Advertisement
In de laatste decennia is de rol van glas in moderne façades steeds prominenter geworden. Door de specifieke combinatie van sterkte, transparantie en duurzaamheid biedt glas een unieke combinatie van materiaaleigenschappen die van waarde zijn in verschillende industrieën zoals architectuur, kunst, interieurontwerp, auto’s, jachten, het optische bereik, laboratorium glaswerk, serviesgoed, datakabels, enz. Afhankelijk van de samenstelling kan glas worden ervaren als transparant of doorschijnend en als gekleurd of helder. Ondanks het feit dat glas vaak als zodanig wordt bestempeld, is het echter nooit onzichtbaar. De Technische Universiteit Darmstadt, met in het bijzonder het Institute of Structural Mechanics and Design (ISMD), het Center for Structural Materials (MPA-IfW) en het Glass Competence Center (GCC), onderzoekt het potentieel van additief vervaardigde glascomponenten op het gebied van materiaaleigenschappen, productietechnologie, structurele integriteit, ontwerp en mogelijke toepassingen.
Additieve vervaardiging
Er is tegenwoordig een grote verscheidenheid aan additieve vervaardigingsprocessen beschikbaar. Wat deze technieken, zoals Rapid Manufacturing, Rapid Tooling, Rapid Prototyping of, meer in het algemeen, additieve vervaardiging (Additive Manufacturing (AM)), met elkaar verbindt, is het feit dat ze allemaal gebaseerd zijn op 3D-computer gegenereerde data als raamwerk voor een productieproces. De gewenste componenten worden digitaal ontworpen voordat deze gegevens worden omgezet in een toegepaste computertaal, die het AM-systeem de opdracht geeft om de specifieke componenten te vervaardigen. De meest gebruikte methoden voor additieve vervaardiging zijn (figuur 2): c) Fused Deposition Modelling (FDM): Deze technologie is een continu filamentgeleidingsproces door een verwarmde nozzle, waarbij laag voor laag een complexe geometrie wordt gecreëerd. Door de nozzle en/of de bouwplaat te bewegen, kan elk driedimensionaal coördinaat binnen het volume van de printer worden bereikt.
a) Stereolithography (SLA): Deze techniek beschrijft een laag voor laag printstijl waarbij een lichtbron monomeren in een bad met elkaar verbindt tot polymeren.
b) Selective Laser Sintering (SLS): Bij deze technologie wordt een laserstraal als krachtbron gebruikt om plaatselijk poedervormig materiaal samen te sinteren. De laser is gericht op specifieke punten die zijn afgeleid van een 3D-model, waarbij alleen daar waar gewenst een solide structuur wordt gecreëerd. De technologie is nauw verwant aan Selective Laser Melting (SLM), waarbij het belangrijkste verschil is dat het materiaal bij SLM volledig smelt in plaats van gesinterd te worden, wat leidt tot verschillen in materiaaleigenschappen zoals kristalstructuur, porositeit, enz. e) Direct Ink Writing (DIW): Deze technologie vertoont grote gelijkenis met FDM, aangezien een kleine nozzle filament of een pasta extrudeert terwijl deze over een bouwplatform beweegt. Het verschilt van FDM omdat het geprinte object niet afhankelijk is van directe stolling of droging om zijn vorm te behouden na extrusie. In plaats daarvan wordt het hele gedrukte en vaak nog fragiele deel achteraf gedroogd en gesinterd om zijn gewenste mechanische eigenschappen te verkrijgen.
a) b) c)
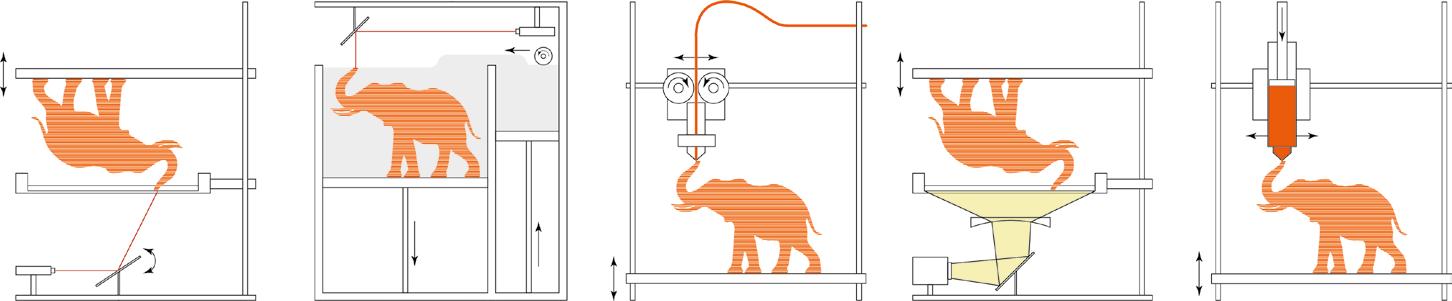
d)
Figuur 2: De meest gebruikte methoden voor additieve vervaardiging, a) SLA, b) SLS, c) FDM, d) DLP, e) DIW
e)
d) Digital Light Processing (DLP): Deze technologie presenteert een vergelijkbaar proces als SLA, waarbij het belangrijkste verschil de bron van het licht is. Door een meer conventionele lichtbron te gebruiken en deze in één keer op het gehele oppervlak van de hars aan te brengen, is het over het algemeen sneller dan SLA. aan gebieden te ontwikkelen waarvoor producten kunnen worden vervaardigd. Tegenwoordig gebruiken al deze methoden van AM één of twee materialen tegelijk en het kruisen van deze processen en daarmee het verbeteren van de materiaaleigenschappen lijkt de kern van de zaak te zijn. Naast kosten en materiaalefficiëntie als argumenten om het gebruik van AM-technologieën te rechtvaardigen, kan een derde en minstens even belangrijk argument worden gegeven in termen van vormvrijheid. De vormvrijheid die deze technologieën bieden, kan onder meer bestaan uit betere structurele en technische materiaal- of producteigenschappen, naast een toename van de individuele ontwerpmogelijkheden.
Al deze methoden hebben met elkaar gemeen dat ze 3D-data zonder extra gereedschap omzetten in fysieke modellen door het stollen van lagen materiaal op elkaar. Het hebben van een groot aanbod aan toepasbare materialen stelt de ingenieur in staat om een breed scala Als we kijken naar de huidige stand van zaken bij additieve vervaardiging, dan zien we dat componenten van metalen en kunststoffen de afgelopen jaren wereldwijd veel aandacht hebben gekregen van onderzoekers en beschouwd kunnen worden als een state of the art technologie in verschillende industrieën. Vergeleken met metalen en kunststoffen kan AM met glas nog steeds worden beschouwd binnen een embryonale staat van onderzoek.
AM met glas
Tot nu toe hebben ongeveer 25 gedocumenteerde projecten zich gericht op AM met glas, waarbij het eerste project dateert van 1995 van de Universiteit van Texas, VS. Het is duidelijk zichtbaar dat het onderzoek met betrekking tot dit onderwerp de laatste jaren aanzienlijk is
toegenomen. De projecten worden gedreven door een breed scala aan industrieën zoals optica, architectuur, bio-engineering, microfluïdica en meer. In deze projecten zijn veel verschillende printtechnieken en glassoorten onderzocht. Bovendien kan een verscheidenheid aan schaalniveaus worden geïdentificeerd, variërend van 3D-geprinte glasobjecten met een totaaldiameter van minder dan 5 mm en een resolutie van 150 µm tot glasobjecten met een totaaldiameter van 25 cm en een resolutie van ongeveer 5 mm. De meest bekende projecten met betrekking tot AM met glas werden uitgevoerd door MIT, zoals gepubliceerd in Innovatieve Materialen nummer 1 2019.
Aan de Technische Universiteit Darmstadt werd het onderzoek naar AM met glas in eerste instantie aangestuurd door het Institute of Structural Mechanics and Design (ISMD), afdeling Façade Engineering. Door het analyseren van de huidige manier waarop glazen façade panelen worden gemonteerd, is het denkbaar om het huidige verlijmen en/of het boren van gaten in de glasplaat te vermijden, inclusief de bijbehorende nadelen zoals veroudering en voortijdig falen van de glasplaat. Als mogelijke oplossing stelt de TU Darmstadt zich de mogelijkheid voor om de verbindingen van de glazen façade panelen direct op een glasplaat te printen (zie figuur 1). Om dit te onderzoeken moest een proof of concept worden opgesteld dat de samenwerking tussen ISMD, het Center for Structural Materials (MPA/IfW) en het Glass Competence Center (GCC) van de TU Darmstadt in gang zette. Het doel van dit proof of concept was het verkrijgen van een verbinding tussen een glasplaat en het geprinte glas zodat krachtoverdracht door dit versmolten gebied mogelijk zou zijn. Het onderzoek omvatte experimenten met soda-lime-silicaatglas en borosilicaatglas en produceerde punt-, lijn- en gestapelde polylijn samples zoals te zien is in figuur 3.
Er is besloten om deze samples met de hand te vervaardigen met behulp van de ervaring van de glasblazers van de faculteit Scheikunde van de TU Darmstadt. Deze handgemaakte samples bieden voldoende kwaliteit voor een proof of concept en vormen tevens de basis waarop de blauwdrukken voor een toe-
a)
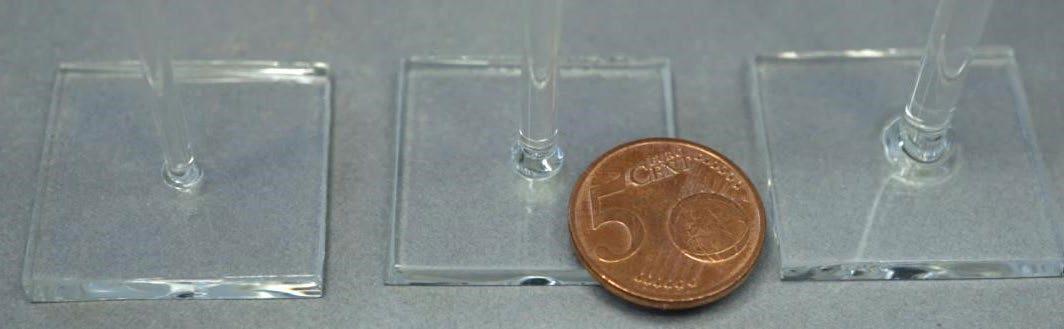
b)
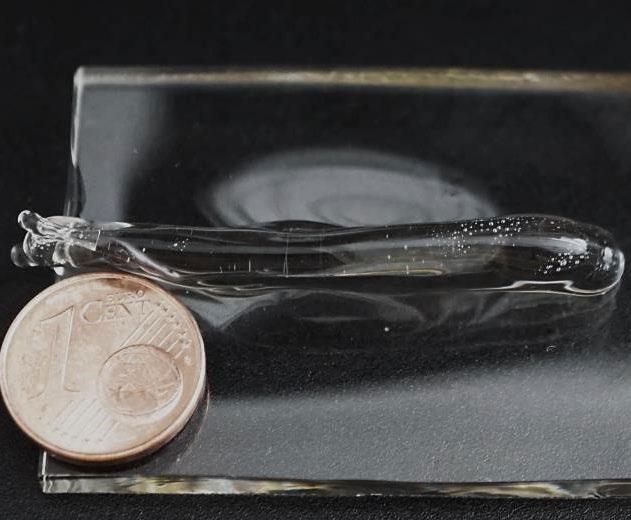
c)
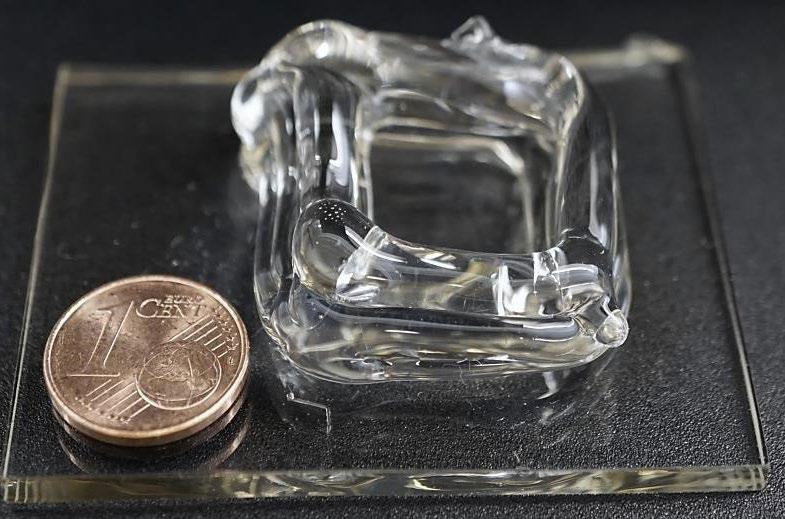
a)
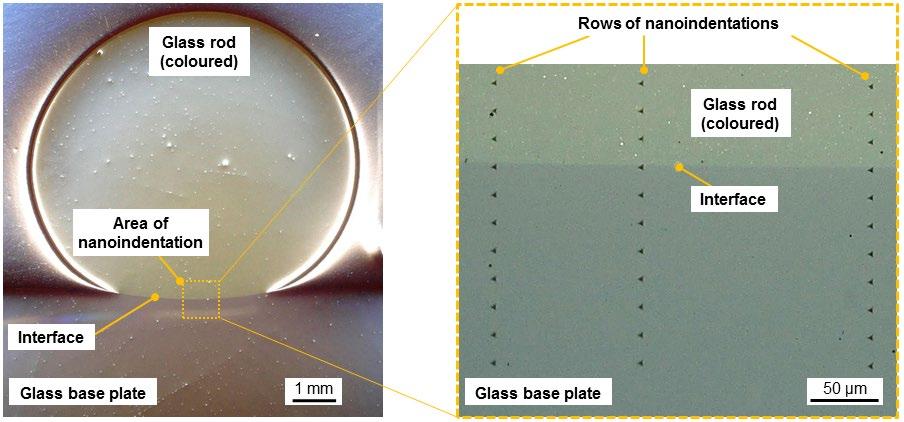
b)
Figuur 4: Microscoopbeeld van een versmolten glazen lijn sample (gekleurd borosilicaatglas) op een glasplaat (borosilicaatglas) a) overzicht (doorsnede) en b) nano-indentaties in het versmolten gebied
komstige glas 3D-printer zijn gebaseerd. De belangrijkste uitdaging voor het bouwen van deze printer is namelijk het omzetten van de kennis en ervaring van vakmensen in een geautomatiseerde machine en daarmee het vertalen van subjectieve vaardigheden naar objectieve parameters zoals temperatuur, printsnelheid, extrusiesnelheid en meer (zie FGDM-video op volgende pagina). Deze printer is nodig om objecten te maken met herhaalbare kwaliteit in een sterk gecontroleerde omgeving waarbij de procestemperaturen variëren van kamertemperatuur tot meer dan 1000 °C. Een grote uitdaging in het productieproces zijn de thermische en brosse materiaaleigenschappen van glas. Daarnaast kunnen thermische restspanningen, poriën en materiaalinhomogeniteit (bijvoorbeeld kristallisatie) tijdens de productie optreden, met glasbreuk als mogelijk gevolg. Na de productie van de glas samples werden materiaal- en componentonderzoeken uitgevoerd om de homogeniteit (restspanning, morfologie, enz.) en de prestaties (sterkte, hardheid) van het verbindingsoppervlak en het raakvlak tussen de versmolten glaslagen en de glasplaat te analyseren (figuur 4). De handgemaakte punt samples werden vervolgens onderworpen aan een destructieve buigproef die veelbelovende resultaten liet zien. Als voornaamste resultaat is aangetoond dat belastingoverdracht door de versmolten glasverbindingen mogelijk is, waardoor het concept wordt bewezen en een groen licht werd gegeven voor het bouwen van een 3D-printer om het proces te automatiseren en het onderzoek naar een hoger niveau te tillen in 2020.
a) b) c)

d)
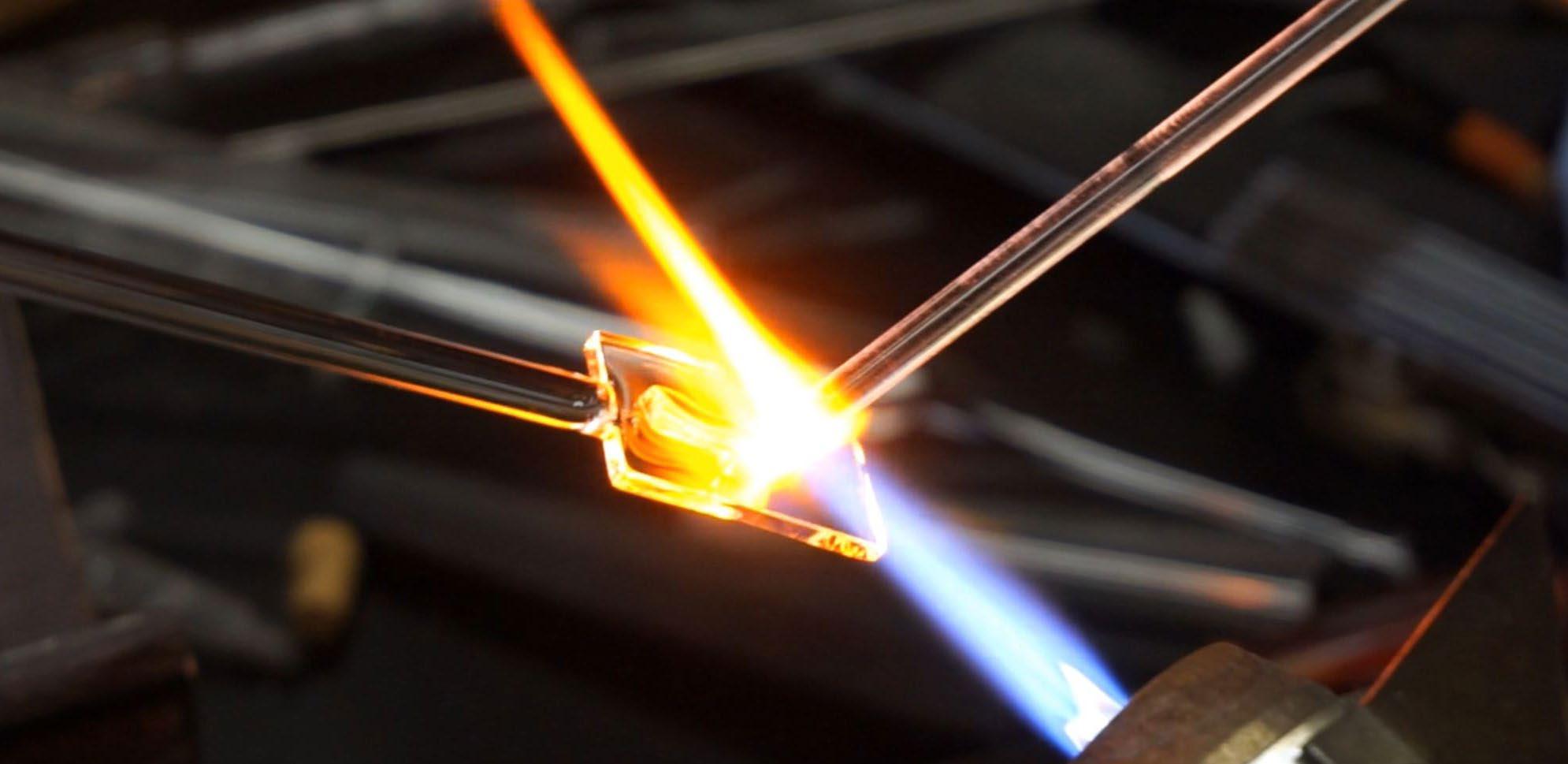
Potentiële toepassingen
Zoals in figuur 1 al was te zien, is een mogelijke toepassing vanuit het perspectief van de afdeling façade engineering om AM met glas te gebruiken voor het ontwerpen van glasverbindingen direct op een glasplaat. Vanuit een ontwerpperspectief is voor te stellen welke mogelijkheden er hier zijn op het gebied van transparantie en vormvrijheid, terwijl de huidige technische problemen met betrekking tot lijmen of boorgaten kunnen worden geëlimineerd. Bovendien zou het mogelijk zijn om lokaal glas op een glasplaat te printen om deze zonodig te verstevigen op basis van een constructieve analyse, waardoor zowel de hoeveelheid gebruikt materiaal als het totale gewicht van de glasplaat tot een minimum kan worden beperkt. Een derde toepassing vanuit het perspectief van façades zou zijn om AM met glas te gebruiken voor een nieuwe generatie vacuüm geïsoleerde beglazing (VIG) waarbij de kleine zwarte afstandhouders tussen de glasplaten vervangen zouden kunnen worden door transparante afstandhouders van glas die direct op een van de glasplaten gedrukt worden. Het zou ook een mogelijkheid zijn om AM met glas te gebruiken om de parameter van de VIG te dichten, vergelijkbaar met een lasproces. Ten vierde is het denkbaar dat voor geïsoleerde beglazing (IGU) een hoge
re mate van transparantie gewenst is. AM met glas zou de noodzaak van de (zeer zichtbare) afstandhouder kunnen elimineren, waardoor de omvang van de afdichting (vaak butyl) tot minimale proporties zou kunnen worden teruggebracht.
Vanuit het perspectief van andere industrieën is het denkbaar om AM met glas in de auto- of jachtindustrie te gebruiken als stand-alone object of om nieuwe functionaliteit direct op de beglazing van een auto/jacht te printen. Ook voor binnenhuisarchitecten zou deze technologie een heel nieuw spectrum aan ontwerpmogelijkheden kunnen bieden, met direct denkbare badkamertoepassingen zoals kranen, douchecabines of decoratie. De optische industrie is ook direct een potentiële markt voor de implementatie van AM met glas, gebaseerd op hun wens voor complexe glasobjecten met een extreem hoge kwaliteit en nauwkeurigheid die denkbaar is met een computergestuurde technologie. Hoe de additieve vervaardiging met glas zich ook precies zal ontwikkelen, de TU Darmstadt streeft ernaar om op de voorgrond te staan met geavanceerd onderzoek, waarbij de grenzen voortdurend kunnen worden verlegd.
Het artikel ‘Fused glass deposition modelling for applications in the built environment’ is online (pdf)>
Research team: Robert Akerboom 1 , Matthias Seel 2 , Ulrich Knaack 1 , Matthias Oechsner 2 , Jens Schneider 1 , Peter Hof 2
1 Technical University of Darmstadt,
Faculty of Civil Engineering and Environmental Engineering, Institute of Structural Mechanics and Design, ISMD, Franziska-Braun-Straße 3, 64287 Darmstadt, Germany.
2 Technical University of Darmstadt,
Auteurs: Robert Akerboom,
akerboom@ismd.tu-darmstadt.de,
Matthias Seel
Video: met de hand vervaardigde versmolten glas sample
Center for Structural Materials, MPA
IfW, Grafenstraße 2, 64283 Darmstadt, Germany.

Afbeelding 1: BESE-elements. Module opgebouwd uit zes lagen. De lagen hebben een afmeting van 922x455x20 mm
Structuur voor natuur:
Aardappelresten krijgen een tweede leven in zee
Nederlandse mariene biologen recyclen aardappelresten tot matten die ze gebruiken voor natuurherstel, zoals kwelders, riffen en zeegrasvelden. Deze Biodegradable Elements for Starting Ecosystems, of BESE-elements, bestaan uit lagen die samen opbouwen tot een biologisch afbreekbare matrixstructuur (afbeelding 1). Het ontwerp combineert porositeit met een complexe structuur en is modulair. In zekere zin toont het gelijkenissen met de welbekende speelgoed bouwstenen: een eenvoudig ontwerp met oneindige mogelijkheden. Proeven met het materiaal, wereldwijd, hebben als doel de natuur te herstellen.
Het materiaal is ontstaan door een samenwerking van partijen die het belangrijk vinden dat materialen die we inzetten in de natuur en voor natuurherstel, niet achterblijven in de natuur. Daartoe is een link gelegd tussen een partij met praktijkkennis van de natuur, een universiteit met brede kennis van hoe de natuur functioneert, een bedrijf met ervaring in spuitgieten en een bedrijf gespecialiseerd in het verwerken van reststromen tot biopolymeren. Na twee jaar ontwikkeling, met de nodige uitdagingen, was in 2013 de eerste batch BESE-elements beschikbaar en werd in 2014 een eerste test uitgevoerd in de Waddenzee.
Potato farm
Coral Oyster/mussel
Mangrove Sea grass Salt marsh
Ecosystem restoration projects

ELEMENTS
Potato chip factory
Chips
Starch (waste)
Biopolymer factories
Afbeelding 2: De resten uit de patatindustrie dienen als grondstof voor de biopolymeren waarvan BESE-elements gemaakt zijn
Natuurfundament
De modules dienen als startpunt: een tijdelijke structuur die aanhechting, stabiliteit en bescherming biedt voor organismen, zowel plant als dier. Normaal gesproken doet de natuur dit zelf, maar door toedoen van de mens zijn natuurgebieden, en daarmee structuurvormende planten en dieren, op veel plekken verdwenen. Zonder de bescherming van de oudere planten is het voor veel jonge planten en dieren niet mogelijk op een nieuwe plek te starten: de omstandigheden zijn te moeilijk. De structuur neemt de bescherming tijdelijk over, remt op kleine schaal de stroming en golven en zorgt dat in de luwte vestiging kan plaatsvinden. Na vestiging vormt de natuur zelf een structuur en is kunstmatige ondersteuning niet meer nodig. Tijdens deze ontwikkeling kan het materiaal langzaam afbreken en neemt de natuur het over.
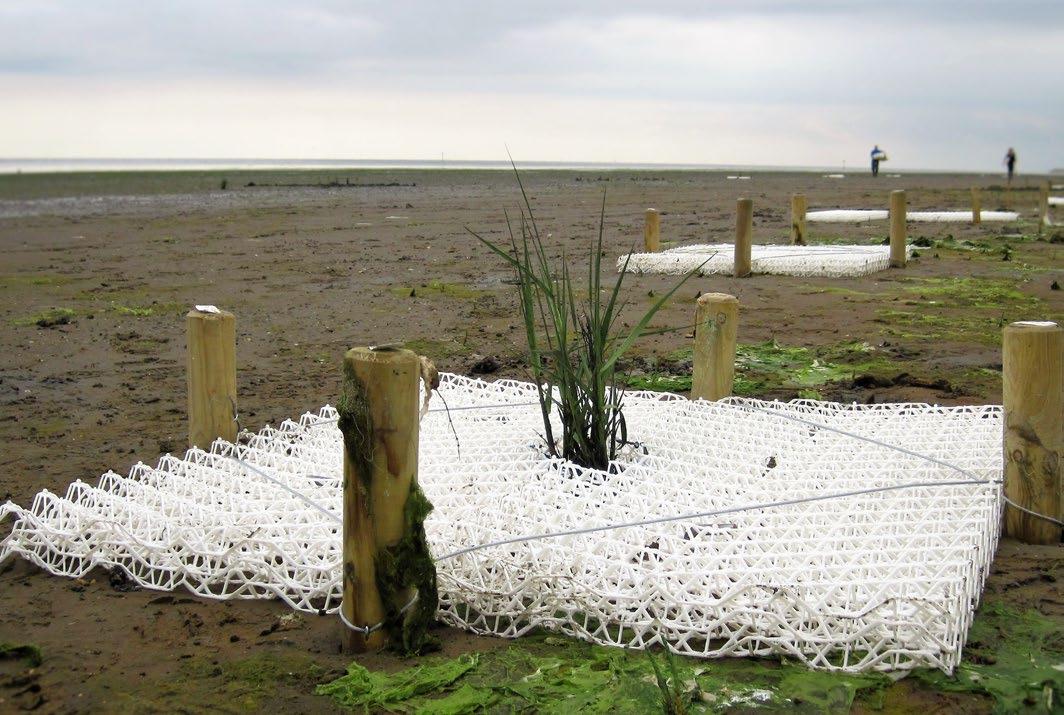

Afbeelding 3b: BESE-elements volgroeid met kwelderplanten (Salicornia en Spartina) een jaar na plaatsing. Op dezelfde locatie zijn ook planten geplaatst zonder structuur, maar deze hebben het niet overleefd
Materiaaleigenschappen
Het materiaal bestaat uit losse lagen, die stapelbaar zijn voor transport en vervolgens ter plaatse op elkaar kunnen worden geklikt (afbeelding 1). Samen vormen de aan elkaar geklikte lagen een complexe driedimensionale structuur, met een groot oppervlak en veel holtes. De hernieuwbare grondstof, Solanyl, is biologisch afbreekbaar, koolstofneutraal en niet giftig.
Vorm
Het materiaal is ontworpen voor modulaire assemblage en installatie waardoor, afhankelijk van de behoeften, verschillende combinaties, structuurhoogten en afmetingen mogelijk zijn (afbeelding 1). Het basiselement is een rechthoek van circa 0,5 x 1 meter. Het aantal lagen en de vorm past men aan op de gewenste locatie, toepassing of soort. De kleur is naar wens aan te passen met een biologisch afbreekbare kleurstof.
Biologisch afbreekbaar
Het materiaal is gemaakt van Solanyl, een hernieuwbare grondstof die bestaat uit een mengsel van biolpolymeren. Een belangrijke component die als grondstof gebruikt is, bestaat uit aardappelresten uit de patatindustrie (afbeelding 2). Het materiaal voldoet aan het Vincotte OK Compost en zijn gecertificeerd conform EN13432 (industrial composting). Buiten de gecontroleerde composteer
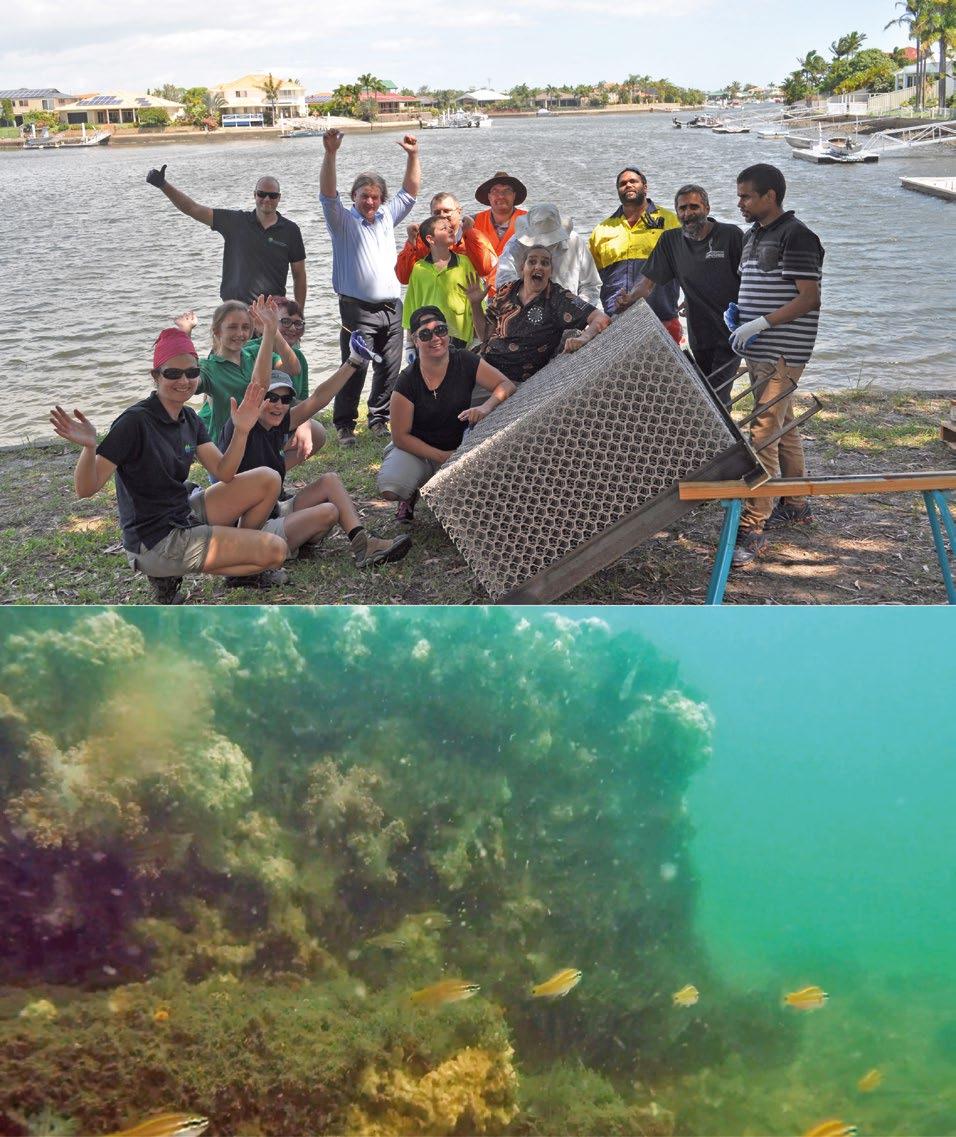

Afbeelding 5: Mangrove herstel met BESE-elements in Pumicestone passage, Australië (foto: HLW)
omgeving, die de certificerende instanties gebruiken, is biologische afbreekbaarheid een proces dat onderhevig is aan de elementen. Ter vergelijking: een tafel van hout, een materiaal dat biologisch afbreekbaar is, kan eeuwen blijven bestaan in een droog binnenklimaat, maar zal in een vochtige bosgrond snel wegrotten. Dit maakt dat er op locaties een sterk wisselende afbreektijd van het materiaal waar te nemen is. In een zoetwaterbron in Florida was het materiaal na drie jaar helemaal zacht. In Nederlands buitenwater zien we dat het wellicht één of meerdere decennia gaat duren. Er is daarom sinds 2019 een tweede materiaalmix beschikbaar die sneller afbreekt, in circa een tot twee jaar. De afbraak gebeurt door micro-organismen en resulteert uiteindelijk in water, koolstofdioxide en microbe biomassa. Herstel van natuur o.a. kwelders, mangroves, zeegras, duinvegetatie, riffen en veengebieden; Aquacultuur en waterkwaliteit; Creëren van (onderwater) habitat. boekuitgave in 2020) en in eigen land in Huis Marseille (‘When Red Disappears’, Elspeth Diederix 2019). Ook is het materiaal te zien als achterwand bij expo’s en in etalages (afbeelding 6).
Prijzen en expo
De structuur won in 2018 de Circulaire Innovatie Challenge van de Unie van Waterschappen. Het materiaal heeft daarnaast architecten en kunstenaars geïnspireerd en is onder andere tentoongesteld bij Art Park, Warapuke, Nieuw Zeeland (‘Biobased Experiments’ Natasja Rodenburg 2017), de Boston Society of Architects (‘NatureStructure’ 2018, met
De voornaamste toepassing, momenteel gebruikt op locaties verspreid over vier continenten, zijn watersystemen en kustecosystemen die onder druk staan door menselijke activiteiten. Deze ecosystemen zijn van groot belang, onder andere voor kustbescherming, drinkwatervoorziening, recreatie en aquacultuur. Daarom is het vooral in deze systemen belangrijk dat er gewerkt wordt aan herstel van kwetsbare natuur, bijvoorbeeld door het gebruik van Biodegradable Elements for Starting Ecosystems. De mogelijke toepassingen voor deze 3D-structuren zijn veelzijdig. Een greep uit de potentiële mogelijkheden:
Wereldewijde toepassingen
Tekst: Bureau Waardenburg
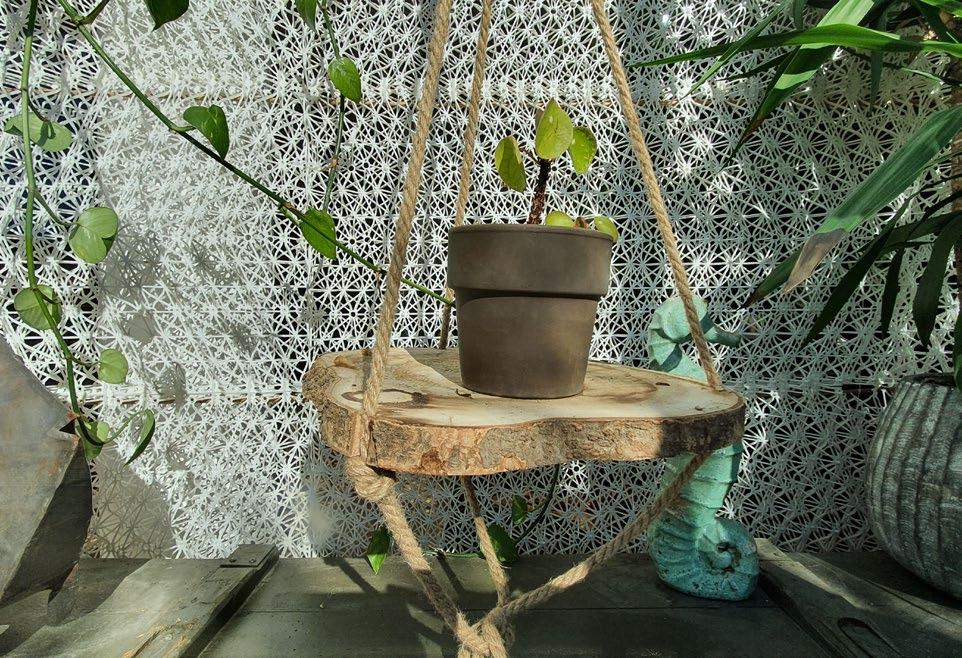
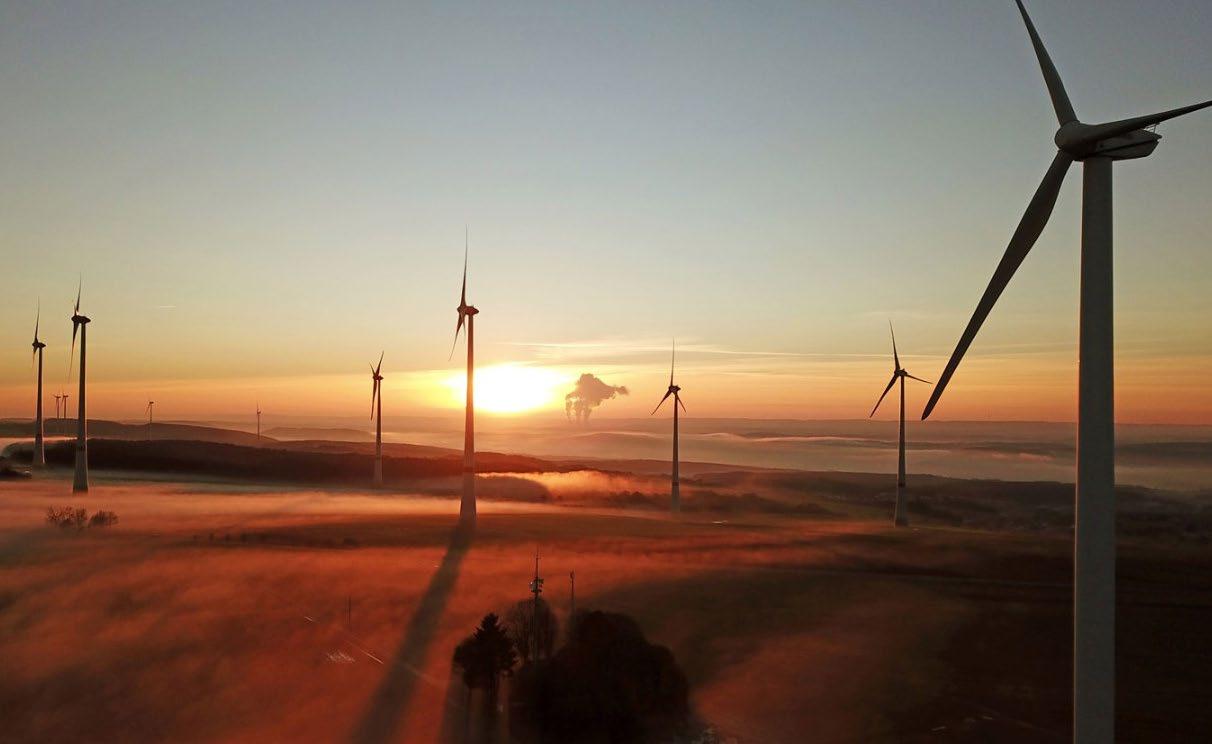
Recycling van balsa-composiet rotorbladen
Onderzoekers van het Duitse Fraunhofer Institute for Wood Research, Wilhelm-Klauditz-Institut, WKI, hebben een nieuwe recyclingtechniek ontwikkeld om balsahout in de rotorbladen van windturbines terug te winnen en te verwerken tot isolatiematten. In Duitsland zijn 30.000 windturbines in bedrijf, waarvan er veel verouderd beginnen te raken en moeten worden vervangen en herverwerkt. Alleen al in 2019 werden zo tweeduizend rotorbladen afgedankt. Een studie van het Fraunhofer Instituut voor Chemische Technologie ICT voorspelt dat in 2024 ongeveer 15.000 rotorbladen moeten worden verwerkt en in 2027 nog eens 72.000. Die rotorbladen zijn grotendeels gemaakt van glasvezelversterkte kunststof en balsahout (gemiddeld 15 m 3 per rotorblad), verlijmd met epoxy of polyesterhars. Die verbinding is extreem sterk, en dat moet ook want de rotorbla
den halen snelheden van meer dan 250 kilometer per uur, waardoor een enorme kracht moeten verduren. Maar in geval van recycling is juist die sterke binding een probleem, aangezien het erg moeilijk is om de afzonderlijke componenten van het composietmateriaal te scheiden. Het restmateriaal wordt nu doorgaans verbrand, meestal in cementfabrieken.
ReRoBalsa
Fraunhofer en een aantal industriële partners zeggen nu dus een nieuwe techniek te hebben ontwikkeld om dit balsahout te recyclen: het zogenaamde ReRoBalsa-project: ‘Recycling of rotor blades in order to recover balsa wood/ foam for the production of insulation materials’. Eerst worden de afgedankte rotoren ter plekke met een waterstraallans in grote stukken gesneden, waarna de segmenten met een mobiele shredder in stukken worden gehakt ter grootte van een hand. Ten slotte worden de stukken bij hoge snelheid vermalen waarbij de individuele componenten worden gescheiden. Het composietmateriaal desintegreerd omdat het hout viscoplastisch is, terwijl glasvezels en hars erg hard zijn. Bij Fraunhofer WKI worden de balsa-stukken verwerkt tot onder meer
ultralichte houtvezelisolatiematten.
Met een dichtheid van minder dan 20 kilogram per kubieke meter hebben deze matten isolerende eigenschappen die te vergelijken zijn met die van materialen op basis van polystyreen.