
15 minute read
100 Years of South Australian Engineering
All things have a beginning, and for FW Hercus it came one morning in May 1920, when Frederick William Hercus moved into a small building on Payneham Road in St Peters.
The engineering industry in Adelaide was in its infancy. Specialisation as it is understood today was unknown, and the small engineering business was eager to grasp any work that was offered. While accepting whatever work came along, Fred Hercus never lost sight of his longterm ambition and that was to become a machine tool maker.
Advertisement
By 1925 Hercus was producing a small range of simple machines. In 1926 the business moved into a larger premise at Chapel Street, Norwood. The remainder of the 1920s saw the business grow, the product range extended and new industries open up as the motor vehicle industry began to develop.
Unfortunately, all good things must come to an end, and by 1930 the economic catastrophe that was the great depression had hit. This was a time that no job was turned away and Hercus produced anything from butchers’ equipment to flywheels, ring gears and automotive repair equipment.
By 1936 business had improved and Hercus returned to machine tool manufacturing in earnest, developing a range of drilling, grinding, milling and slotting machines along with a range of metal turning lathes. This range of machine tools proved to be so successful, that in 1939 Hercus had to move into much larger premises on Anderson Street in Southwark (known today as Thebarton).
The first years at Southwark saw the development of machines that were destined to become the workhorses of Australian industry. The most prominent being the Hercus 9-inch swing lathe.
During the early 1940s World War 2 was in full swing and under the direction of the Department of Machine Tools and Gauges, Hercus was producing only certain machines from its range for the war effort. During the war years Hercus produced in excess of 2300 machines. With the advent of peace, Hercus once again was able to refocus on developing and producing its range of machine tools.
The 1950s and 60s saw continuing redesign and improvement of its machine tool range. Hercus needed to meet the changing needs of industry and the realities of a competitive and discriminating market.
To this day some see the 1960s as the pinnacle for manufacturing at Hercus as well as for Australia.
The 1970s presented Hercus with a raft of new challenges mainly from cheaper imported competition. This led to a reduction in the range of machine tools that were being manufactured. Hercus decided to retire its mainstay, the 9-inch swing lathe after around 15,000 units and by the end of the 1970s had introduced the more modern 260 lathe. The 260 lathe
proved to be as popular as the previous model.
The 1980s saw the widespread introduction of CNC machine tools, and to meet this demand Hercus developed its own, the Hercus HNL lathe, the Computurn lathe and Compumill machining centre. These CNC machines were sold throughout Australia and exported to Asia and North America.
Unfortunately, the challenges of the 1970s only intensified during the 1980s, and by 1987 Hercus found itself in deep financial trouble and was eventually purchased by the Durden Group who had been producing woodworking machinery since the late 1940s.
With the enthusiasm of the new owners Hercus embarked on a programme to further develop their CNC machine tools. This saw the machines go from using dedicated controllers to personal computers and windows-based software to operate the machines, which at the time was state of the art.
Early in the 1990s Hercus moved to its present location at Regency Park where it continued to produce the CNC machine tools, at the time being sold throughout Australia and exported to North America as Rockford CNC. Other products being manufactured were the 260 lathe, OLM mill and the Durden Range of woodworking machine tools. One of these, the Durden Top Turn Lathe, was being exported to north America as the Delta Top Turn Lathe.
However, by the late 1990s those challenges that appeared during the 1970s were still there and this meant that tough decisions had to be made. Hercus ceased production of a majority of its machine tool range: this included the 260 lathe

of which around 7000 units were made. The manufacture of all machine tools had ceased by 2005.
One essential aspect of machine tool manufacturing is to produce accurate components, whether they be one off or mass produced. Hercus had always offered a general engineering service to other companies, and as Australian industry grew so did this side of the company. It was in 2000 that Hercus decided to reinvent the company and make the general engineering services its main focus. This meant Hercus was able to compete on a level playing field with other Australian companies.
The 2000s was a time of moderate growth. However, this period was essential for the consolidation of the company and for the development of some key customers.
Since 2010 Hercus has seen continual growth within the general engineering sector. This, however, has not always been easy. Hercus has invested heavily in new, up to date, computerised machinery, operating software and quality assurance accreditation, while also improving its manufacturing and factory processes, which include training and all OH&S requirements.
Looking to the future, Hercus sees a positive outlook with further expansion in the key areas of mining and mineral processing. Also having the Australian federal government commit to large defence projects gives Hercus the opportunity for further expansion.
FW Hercus 08 8346 5522 www.hercus.com.au
DURABLE HOSE PUMP SOLVES DELICIOUS DILEMMA
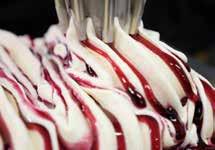
Tough and durable pumps are hard to come by. With the complexities that come with pumping abrasive or corrosive fluids, an understanding of applications, including operational and production requirements, is crucial.
With its head office in South Australia and representatives around the country, Global Pumps has more than 40-years’ experience solving difficult pumping applications. Having worked across all industries, the team understands the desire for reliable, durable and safe pumps.
One of the company’s core products, the Verderflex range of peristaltic hose pumps, is an example of Global Pumps’ commitment to offering consistent and tough solutions to industry concerns.
The peristaltic action of the Verderflex hose pump is the gentlest and most abrasion resistant pumping action available. Able to self-prime, run dry and pump in reverse, they are extremely versatile. There are no valves or seals in contact with the process fluid, eliminating sealing and “vapour lock” problems.
These features make them suitable for harsh abrasives and thick slurries through to food and beverage, chemicals and highly corrosive substances. The Verderflex hose pumps are capable of pressures of 15bar and flow rates of 180m3/h.
When looking for the most rugged slurry pump or accurate dosing pump, it’s the hose that is the life of the Verderflex pump. They are designed to minimise the effects of fatigue, giving an extremely long hose service life. Having been tried and tested over numerous arduous applications, Verderflex hose pumps give substantially longer service life than competitors.
the Verderflex peristaltic hose pump range was selected. This pump allowed the team to create premium dairy products to exacting requirements, minimising waste and facilitating increased production efficiencies.
The Rapide Series by Verderflex offered Gelista a compact design, simple operation and easy maintenance for accurately metering the fruit syrup. The hose is simple and quick to remove, giving the gelato manufacturer the certainty that the staff could efficiently clean the pump between production cycles.
As the Verderflex Rapide is capable of handling viscous fluids with total containment and leak-free pumping, it offered the perfect solution for fruit pulps and other gelato inclusions.
Peter Cox, founder at Gelista, chose the peristaltic hose pump due to its flexibility in speed, accuracy and serviceability, making it one of the more versatile pumps on the market.
“One of the other major advantages of the peristaltic pump was [Gelista’s] ability to very quickly and easily clean and sanitise the pump, prior to next production.”
Global Pumps was also able to add a stainless-steel cover to the pump to ensure it meets with stringent food handling requirements.
Verderflex in action
Recently, Global Pumps was approached by South Australian ice cream and gelato manufacturer Gelista, which was looking for an efficient and effective pump to evenly distribute fruit ripples through its ice cream.
Having briefed the expert Global Pumps on the operational requirements, Delicious results
Following the pump’s installation, Gelista successfully increased production uptime, reduced cleaning downtime and expanded its capabilities across all operations.
Installing the correct pump through consultation with experts ensures the best solution is achieved. By gaining assistance from Australia’s leading team at

Global Pumps, delicious results continue to be achieved for the South Australian manufacturer months after the purchase.
Global Pumps offers free site visits to customers around Australia, with options to hire hose pumps before committing to purchase. This reassurance is crucial in selecting the right peristaltic hose pump for any application, and guaranteeing it meets production and operational requirements.
Global Pumps 1300 1 GLOBAL www.globalpumps.com.au
100 YEARS
1920 - 2020
www.hercus.com.au
CNC Machining - Gear Cutting - Fitting & Assembly Gearbox Refurbishment - Industrial Transmission Equipment
Dynamic Solutions from Concept to Manufacture
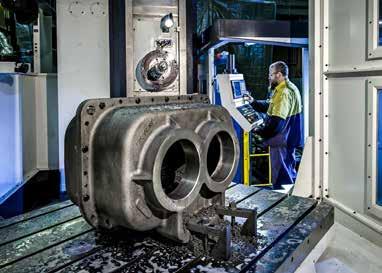
Hercus Pty. Ltd. 12 Camira Street, Regency Park, South Australia, 5010. P 08 8346 5522 F 08 8346 5811 E - sales@hercus.com.au
GASSING ABOUT COMPRESSED AIR SAFETY AND EFFICIENCY IN THE TOP END
After 15 years in the Top End, Compressed Air Australia is transforming safety and energy efficiency right across the country. Which means life is quite literally a gas for June Lindsay-Lorman, Director of the Darwin-based compressed air specialists.
June likes to say that the company she helps run is ‘a breath of fresh air’, as it’s on a mission to do more than simply shift product. Compressed Air Australia has set itself broad industry wide goals aimed at maximising efficiency and dramatically cutting energy costs while improving all round safety for compressed air users. And it’s doing this with latest EXAIR products
that amplify existing room air to maximise efficiency – making them a safer and more efficient replacement that literally pays for itself compared to some of the homemade compressed air solutions still in use, some of which are ‘unsafe’ according to June.
Industry Update Editor-In-Chief, Laurence Marchini caught up with June recently to find out how the mission was progressing. Before getting into specifics he discovered that Compressed Air Australia now offers a range of products in keeping with an industry leader. The comprehensive list includes: air amplifiers, air knives, air nozzles, optimisation products, air wipes, safety air guns, air fuses, in-line regulators, vacuum generators and air operated conveyors.
The range also extends into liquid atomising nozzles, industrial vacuums, vortex tubes and applied products utilising vortex tube technology, such as coolers for electrical cabinets and ionising products to eliminate static electricity.
Naturally, in line Compressed Air Australia’s commitment to boosting user safety, all of these products meet CE requirements, OSHA and WorkSafe Australia standards for dead-end pressure and noise exposure, as well as RoHS compliance.
Laurence then asked June how business was progressing generally, particularly as more and more businesses are seeking to boost energy efficiency and compressed air applications are famous using large chunks of electricity or gas.
June replied: ‘Things are going well. With energy prices constantly on the rise, companies are looking for ways to drastically cut their use of compressed air. Our EXAIR products are designed to replace the homemade compressed air products that so many facilities have been using up to now” she then explained: ‘In many cases, the EXAIR product retrofits into the existing application. And, they’re ideal because they amplify surrounding room air. As an example, the Super Air Knife pulls in 40-parts room air to the one-part compressed air consumed.’
LM: June, we all know that Australian industry is struggling with energy price rises. Has this helped you push your energy efficiency message?
June’s enthusiastic reply was: ‘That’s a resounding yes! We can help companies identify the homemade low efficiency products in their facility and make a recommendation for their replacement. In many cases, replacing homemade blowoffs with an EXAIR Super Air Nozzle drastically reduces air consumption and noise. The Super Air Nozzle pays for itself within 2 weeks.’
LM: So, what sort of companies are coming to you now for help? Are they larger or smaller?
‘Large and small. When a company upgrades to a high efficiency EXAIR product, the compressor runs less. We’ve found that, in some cases, they’re saving enough compressed air that they can even turn a backup air compressor off.’
LM: The other major aspect of your company’s mission is to improve the safety of compressed air applications. Do you think that the safety culture has changed for the better in Australian industry over the last 15 years?
In answer to this June stressed: ‘There are still companies out there who manufacture products that are not safe. EXAIR on the other hand makes products that can operate at full line pressure but not breach the 30 PSIG dead-ended pressure limitation.
She then went on to outline some major safety benefits within Compressed Air Australia’s product rage, ‘We also have the Protect-Air HoseGuard that acts as an air fuse, so in the event that a hose is cut or damaged, the air is turned off immediately, eliminating whiplash hazard. And, Protect-Air ToolReg inline regulators, have automatic secondary pressure relief that eliminate accidental activation of the pneumatic tool once disconnected from the compressed air line.’ She explained this is crucial safety feature when working with nail guns and staplers.

LM: Do these improved safety features only relate to the safety of compressed air systems? Or do they make using compressed air a safer power source option for other applications?
June was typically forthright, simply saying: ‘We think it applies to the overall safety of personnel and equipment.’
LM: Finally, I do have to ask the question, what’s it like running a nationwide business from Darwin? Has it been a problem? Or is Australia getting smaller?
June responded with a shrug, saying: ‘It's no problem at all. We have great coverage throughout the country. The key is our distributor network. They know our products well and cover most of the primary business centres in Australia.’
Compressed Air Australia 1300 787 688 www.caasafety.com.au
DEFENCE COMPANIES VIE FOR SLICE OF $35 BILLION FRIGATE PIE
Detailed planning for Australia’s Hunter Class Frigate Programme is well underway as South Australian companies vie for a slice of the $35 billion project.
Nine antisubmarine warfare frigates will be built by ASC Shipbuilding at the Osborne Naval Shipyard in South Australia in what is being described as the largest surface ship project in Australia’s defence history.
Construction of the first test blocks for the project will begin towards the end of this year with defence companies now being short-listed to carry out part of the work.
Among them is Adelaide defence company AFL services, which has been downselected for lucrative blast and paint work.
AFL services was one of four Australian companies recently invited to tour global defence company BAE Systems’ world-class shipyards in Scotland to inspect painting processes used on the Type 26 Global Combat Ship. “AFL Services has a proud history of working on defence projects, from land vehicles with BAE/Tenix toll defence, and components for Navantia to the Collins Class submarines,” General manager Adam Levi said. “We appreciate that BAE System is embracing Australian industry content and helping small businesses reach their potential to bid for the Hunter Class Frigate Programme work,” Levi said.
AFL Services now has more than 60 staff and winning a slice of the Frigate work would boost projections.
ASC Shipbuilding won the head contract to provide the design and build framework of the nine anti-submarine warfare frigates that will be replacing the nation’s eight Anzac Class frigates. ASC Shipbuilding has become a subsidiary of BAE Systems throughout the build process before ownership is returned to the Commonwealth at the completion of the project.
The two-year first building of five test blocks at the world-class digital shipyard in Osborne, Adelaide, is beginning in December this year with building of the first frigate expected to commence in 2022. “Personally being from South Australia, I have set goals to assist industry at Osborne and create flow-on to the schools and the community for years to come.
“The Hunter class project is a national endeavour that will provide many Australian small businesses with unprecedented opportunities.”
Three other Australian companies, Broadspectrum, Eptec Group and Altrad Services – Asia Pacific, are all vying for the work that involves blasting back material of the ship to create the right conditions for painting.
The Hunter programme is designed to create a continuous naval shipbuilding endeavour in Australia, creating more than 5000 jobs across BAE Systems and the wider Australian defence supply chain over the life of the decades-long project.
More than 1000 Australian suppliers have registered through the Industry Capability Network Gateway to compete for work on the frigate programme, with placing of contracts for the prototyping phase of the project happening throughout 2020 and 2021.
“The prototyping phase is one of the first real chances for Australian industry to be actively involved in the manufacturing phases of the programme,” ASC Shipbuilding MD Craig Lockhart said.
The nine antisubmarine warfare frigates will be built at the ASC shipyard in Osborne using local workers and Australian steel.
Work on the frigates is expected to create 1000 apprentice and graduate jobs throughout the programme’s life, with opportunities for engineers and project managers, specialists in steel work, mechanical, electrical and technical trades.