
4 minute read
Know-how in steel Siderval
KNOW-HOW IN STEEL
Italy-based Siderval is one of the clear market leaders in special hot extruded steel bars produced through hot extrusion. Industry Europe looks at its activities and some of the more recent projects in which it has been involved.
Founded in 1971, Siderval is now recognised as a leading player in its field. From its headquarters in Talamona, Italy, Siderval operates using the latest, state-of-the-art equipment. It runs an automated peeling system with an annual production capacity of some 42,000 tonnes. Its special automated saws cut round steel bars into ingots of different lengths according to their specific weights and to the length of the profile to be produced. A modern horizontal hydraulic press with a capacity of 2400 tonnes extrudes bars of up to 16m in length with complex sections, solid or hollow, designed with a maximum diameter of 200mm.
“Nowadays the company makes use of cutting-edge technology which offers technically innovative and economical solutions,” begins Ernesto Riva, member of board of Siderval. “We make complex and unusual profile shapes in tubular and solid sections which cannot be produced using either traditional hot or cold working techniques. We are able to transform high alloy steels which, owing to their fast cooling properties and sequential hardening of the material, require short deformation time. Also, we are able to produce small quantities at competitive prices thanks to limited tooling costs; as such the production of a number of sample bars at no added cost has become possible. This is a great advantage that we share with clients.”
As a result, extruded steel bars have become fundamental in many different industries, including: the energy industry (where they can be used to manufacture thermo-nuclear and hydraulic power stations), aeronautics, marine, construction, automotive, automation & tooling, chemicals and so on.
Road to Panama
The extension of the Panama Canal is one of the most high-profile projects in which Siderval is currently involved. The Canal is considered to be one of the most important works of engineering in the world as well as being of strategic importance for global commerce and security. In order to accommodate the next generation of over-sized vessels, the Panama Canal is getting its most ambitious upgrade in 93 years: a third channel hemmed in by its enormous flood gates. Due for completion by the end of
2014, this upgrade is set to double the shipping lane’s capacity.
Each of the 16 gates involved in this project has been produced by the Italian steel structural manufacturer Cimolai. Siderval’s vital contribution was to make the 46 tonnes of steel required for the bulkhead frame. This project was carried out in close cooperation with Cimolai’s project management team.
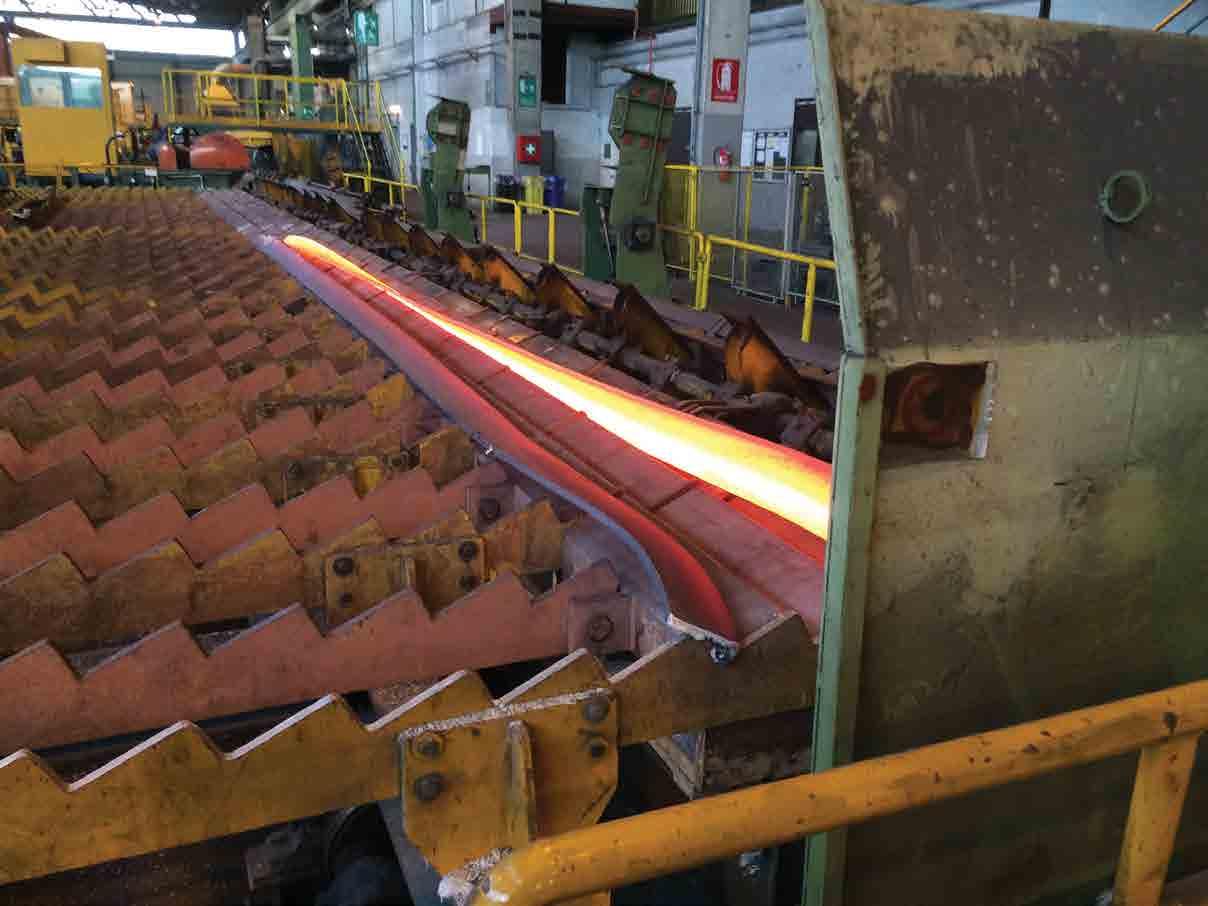
The ‘Titanium’ way
As with many other industry sectors, innovation and technological development are both key to Siderval’s continued growth. Innovative ingredients and suitable combinations of existing materials allow it to develop new products and increase efficiency to achieve better results for its clients.
Technology based on titanium is becoming increasingly important and the company has therefore recently extended its product range to include it. To this end, it has purchased new machinery based on hot straightening technology – the only way to work with titanium. This material is employed in the medical industry and aeronautics, for example to make special profiles for motor rings and seat fixing systems.
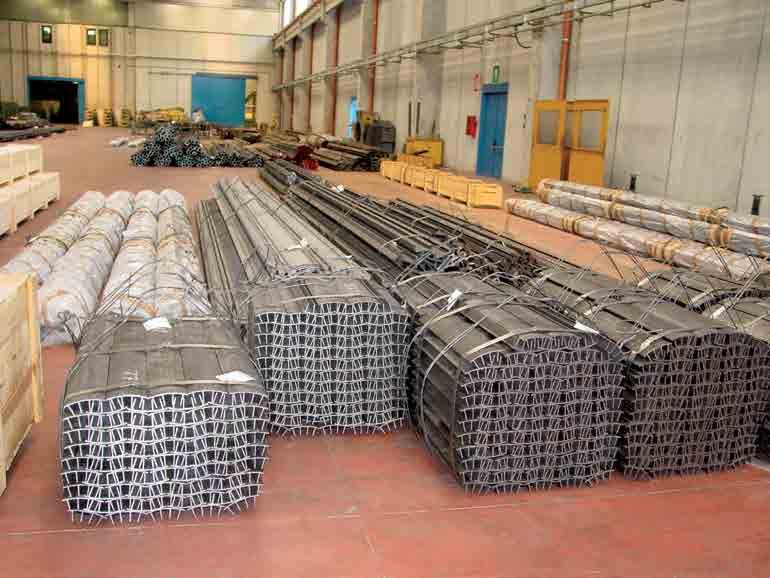
Achieving CO2 reductions
The development of special profiles for big boilers has been Siderval’s response to the issue of pollution and to the G7 requests to
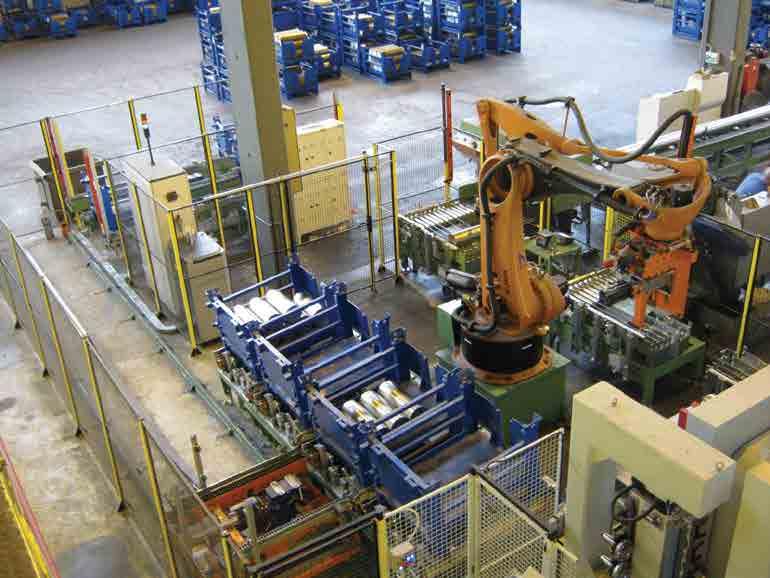
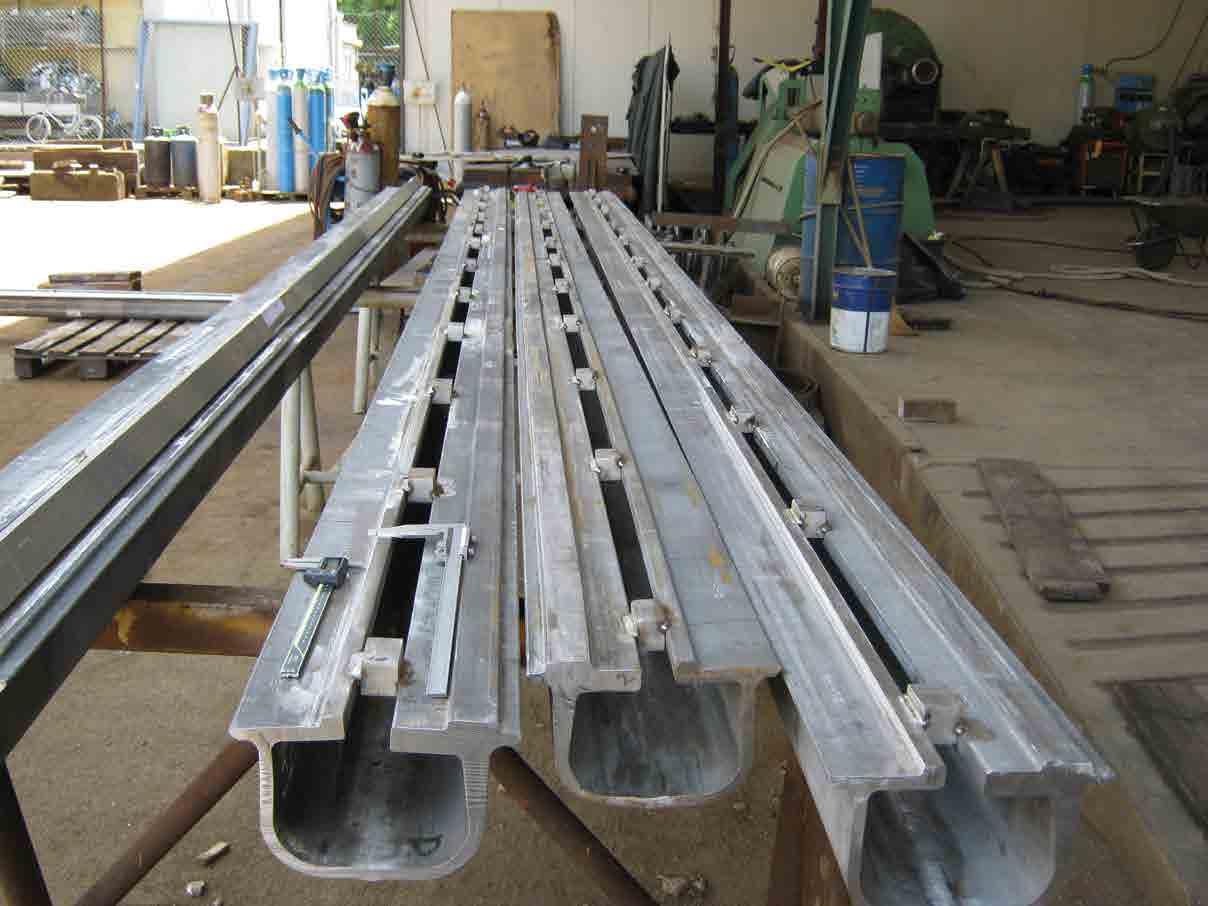
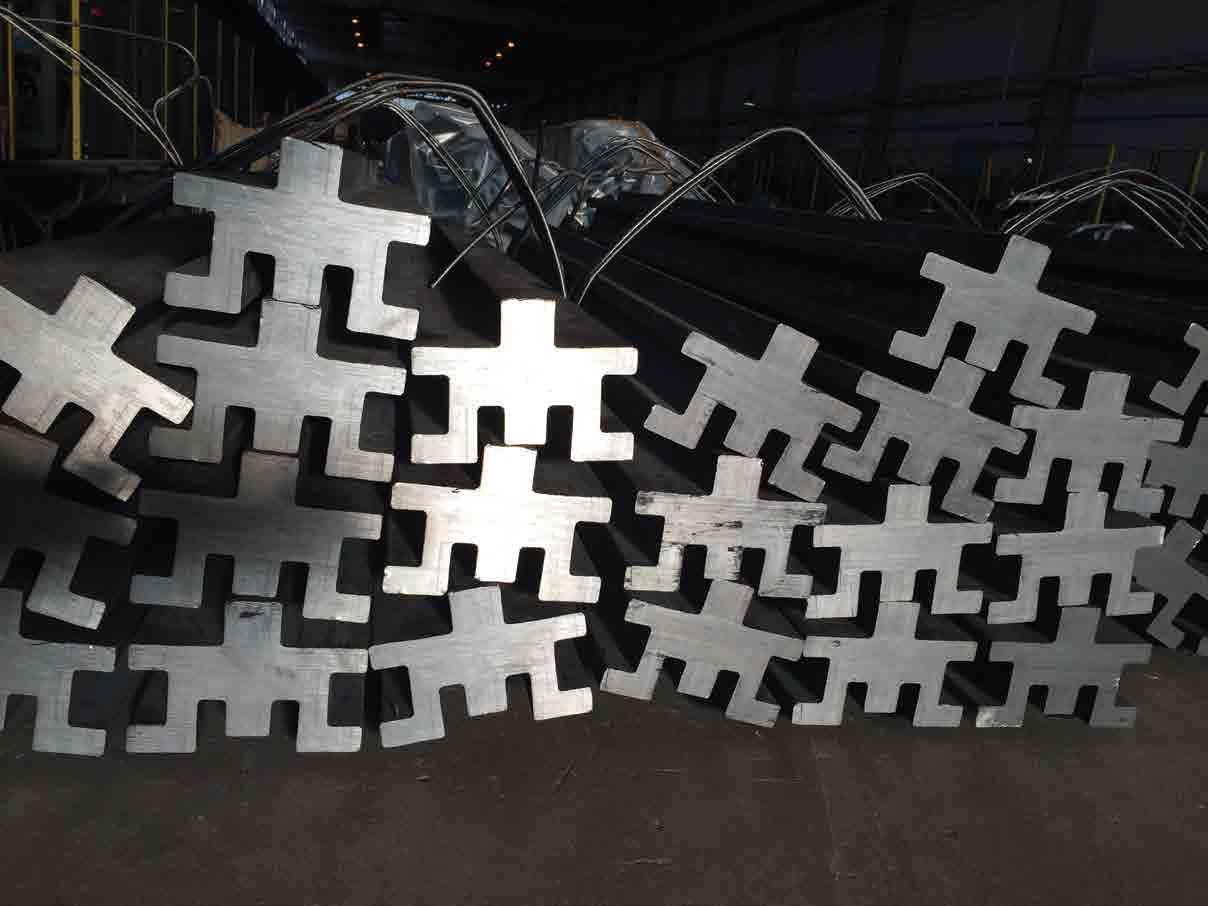
lower carbon emissions – particularly in areas such as Asia. The company recently received an order in China for the replacement of old coke boilers with new gas fired ones made from Incoloy 800 and Incoloy 825.
To clarify, Incoloy 825 is a nickel-iron-chromium alloy which also contains molybdenum and copper. The chemical composition of this alloy has been specially designed to provide exceptional resistance to many corrosive environments and high temperature. It offers excellent resistance to both reducing and oxidising acids, to stress-corrosion cracking and to localised attack such as pitting and crevice corrosion. It is used for chemical processing, pollution-control equipment, oil & gas well piping, nuclear fuel reprocessing, acid production and pickling equipment. Architectural structures
During the 2012 Olympic games in London, Siderval provided the raw material for the new Olympic bridge. Across the ocean, it supplied material for the NYC freedom tower. The latter is an open, innovative building that simultaneously radiates and is filled with light. The plan for rebuilding the 16-acre site devastated by the September 11th attacks retains 2.6 million
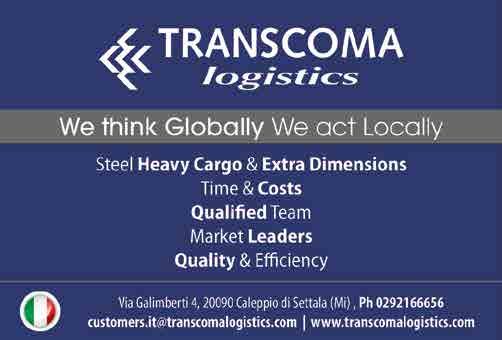



square feet of office space and an observation deck. Sixty-nine office floors will sit on top of a 200 square-foot high reinforced base.

Looking ahead
“Our aim for the next few years,” concludes Mr Riva, “is to enter new niches such as aeronautics in the US, industries for environmental applications in China, and nuclear in Russia. We are still growing and will continue to grow our international network. We like to think of our group as being much more than a single company, but rather an authentic partner that brings a wide range of solutions to enable our clients to obtain the best possible result.” n