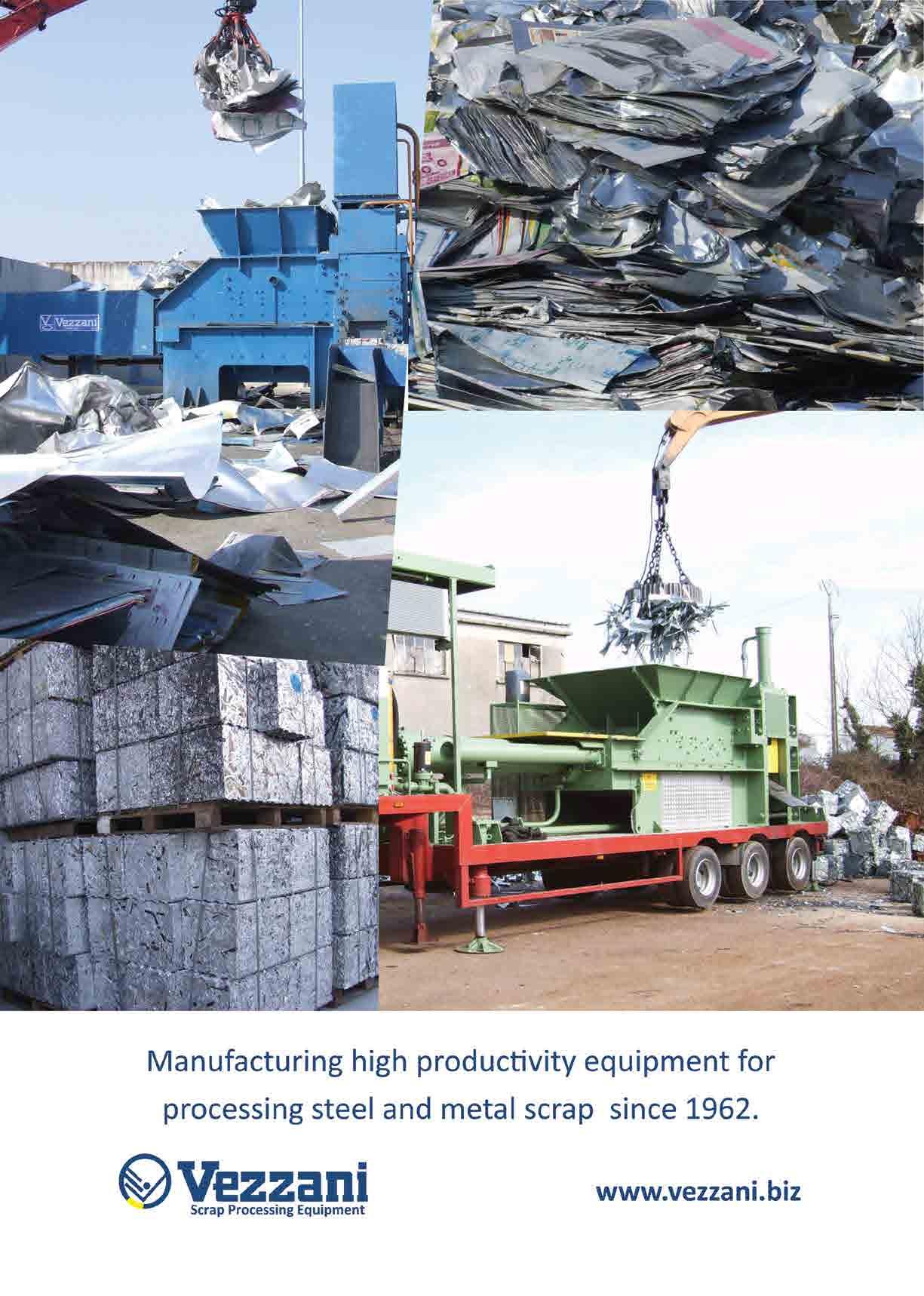
3 minute read
Experts in glass moulds and casting Omco
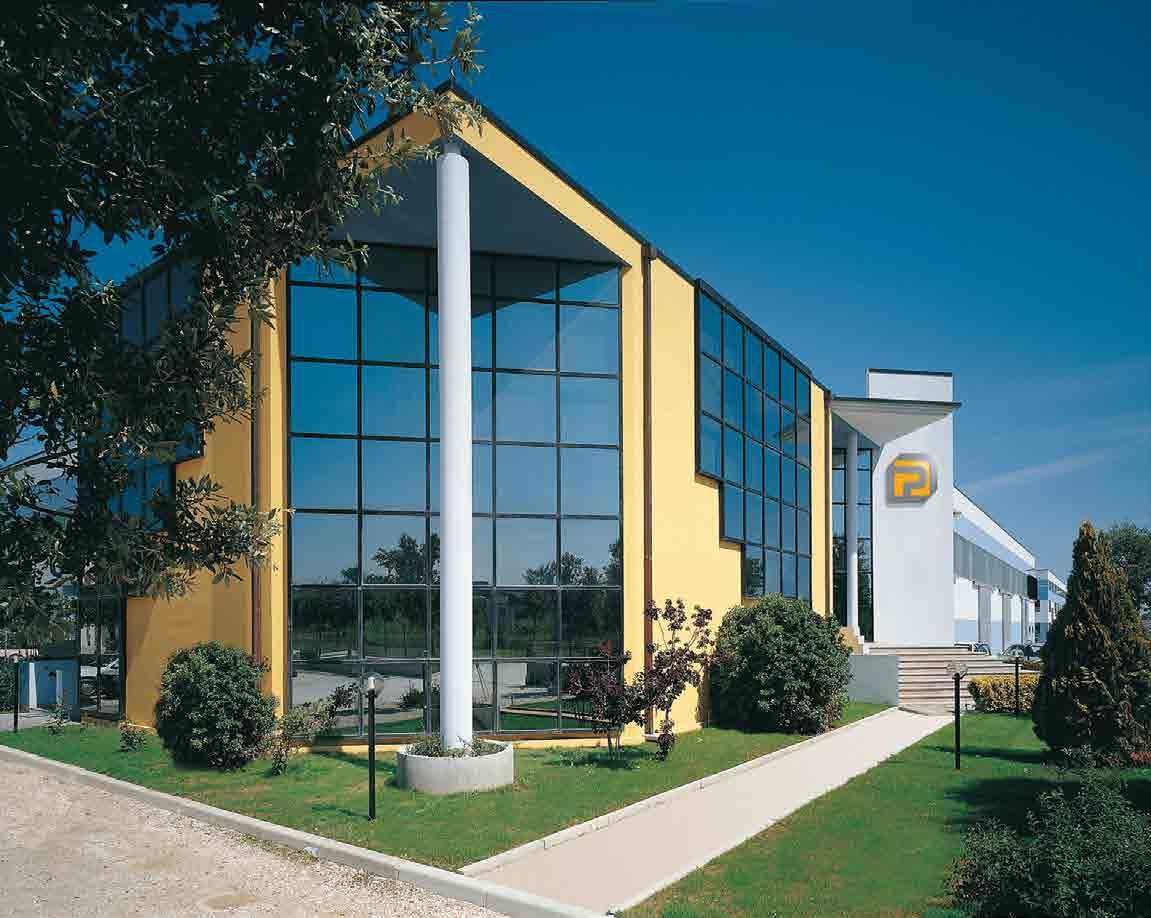
Moreover, we supply Egyptalum with technical and engineering support for their plant, with a whole section of our technical department dedicated to this task.” When asked about new products and technologies Mr Petrucci replies, “We are increasingly focusing on magnesium alloys for the automotive sector, high thickness metal sheets and other similar products.” Profilglass is developing ever more products for the automotive sector because this segment offers the greatest expansion and growth opportunities for the aluminium industry, and will do even more so in future. “For instance, we are in direct contact with the Fiat Mirafiori plant, testing and sampling new alloys in the 5000 series.”
Although the company has subsidiaries, as Profilglass it operates from a sole production site, covering an area of 250,000m2. Important innovations have been implemented here in the last couple of years, especially in terms of environmental friendliness. Roof areas has been equipped with a photovoltaic panel system, producing fourteen megawatt of clean energy. Furthermore, health and safety is regarded as an absolute priority. Work safety training courses are conducted on a regular basis and over half of the company employees have recently completed a course of this kind, which they had attended during working hours for 18 months. The motivation of the employees was so high that they managed to maintain the same productivity levels, despite the fact that part of their working day was dedicated to this course. “We are implementing continuous improvement in all our processes.”
Fresh and young
While the company is keeping its renowned name, it has a new, younger and fresher logo, now mainly centred on rolled products rather than profiles (the latter now generate 15 per cent of turnover). “We will be at the next biannual Dusseldorf aluminium trade fair next 7–9 October, where we will present our new company image and will launch a new motto “R2R – Ready to Run”
Export stands at about 75 per cent and is mainly generated in Europe, with Germany and Spain being particularly important markets (as well as Italy, which accounts for the remaining 25 per cent of turnover). Rolled products have opened up new geographical markets in Arab countries, Russia and especially Brazil, where a commercial subsidiary has been opened in Sau Paolo and Profilglass d.o. Brazil has been set up. The Brazilian market features strong growth, especially in the construction sector.
As the Profilglass facilities offer further potential production capacity, the current target is that of reaching an output of 150,000 tonnes in the next two to three years. Linked to this, there is the objective of achieving sales volume growth in both EU and non-EU markets. Still talking about future development and strategies, Mr Petrucci adds, “We are increasingly focusing on product and internal process quality. We are ISO 9001 certified and we are in the process of acquiring the UNI EN ISO 14001 environmental certification.” n

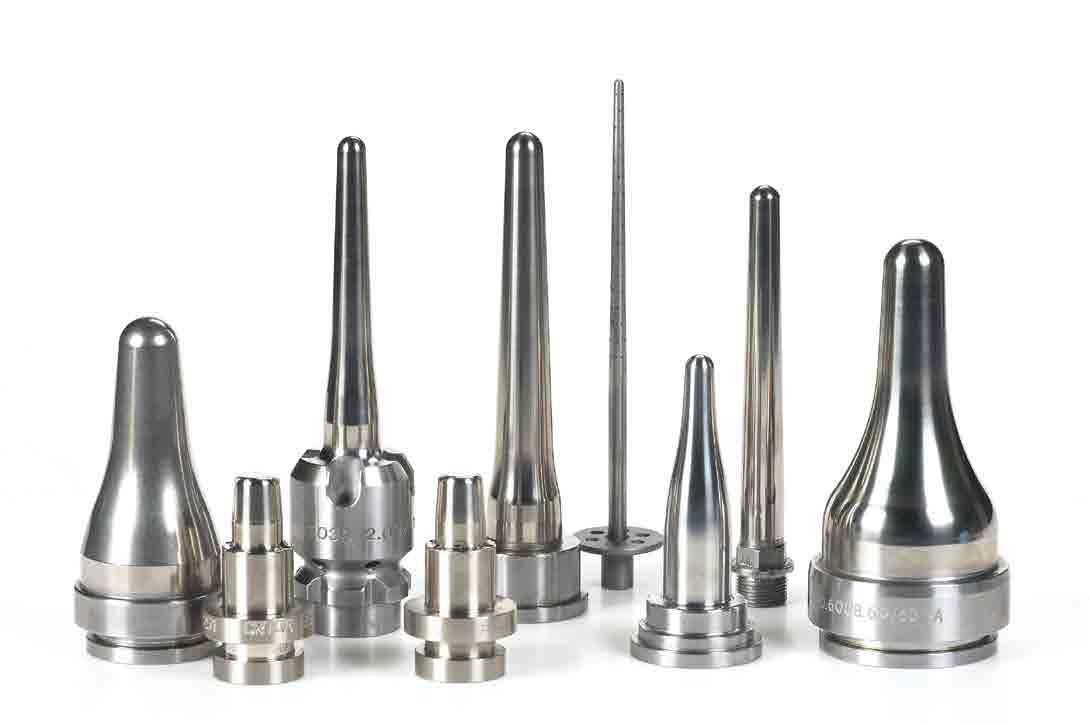
EXPERTS IN GLASS MOULDS AND CASTING
Omco is a global leader in the development and manufacture of tailor-made glass moulds for industry. Industry Europe looks at how the company has achieved its enviable position in the sector.
IN June this year (2014) Omco celebrated 50 years of operations in Belgium where a division of the Overmeyer Mould Corporation was established in Aalter in 1964. Initially the company outsourced its requirements to third parties but by the early 1970s the demand for its products had increased to the point where it was necessary to establish its own foundry, and when the Bekaert foundry in Hamme, Belgium, came up for sale, Omco purchased it without delay.
Difficult trading conditions in 1984 led to a management buy-out and from that time onward, Omco became a Belgian company. Following 20 years of consistent growth, Omco NV merged with BMT NV and subsequently became a publicly traded company. In the year 2000 a second foundry was acquired in Slovenia, which was then geared to produce industrial glass moulds for Croatia and Austria whilst the company’s main foundry in Hamme became increasingly focused on manufacturing moulds for customers outside of the group.

The pillars of success
Omco’s global success is built around five key steps: engineering, foundry, manufacturing, quality assurance and moulds. Each of these business units is supported by a multinational group of engineers who are available to service its customers worldwide. The company’s foundry division has strategically located facilities in Belgium and Slovenia from which it can guarantee flexible supplies of high-quality cast iron and aluminium