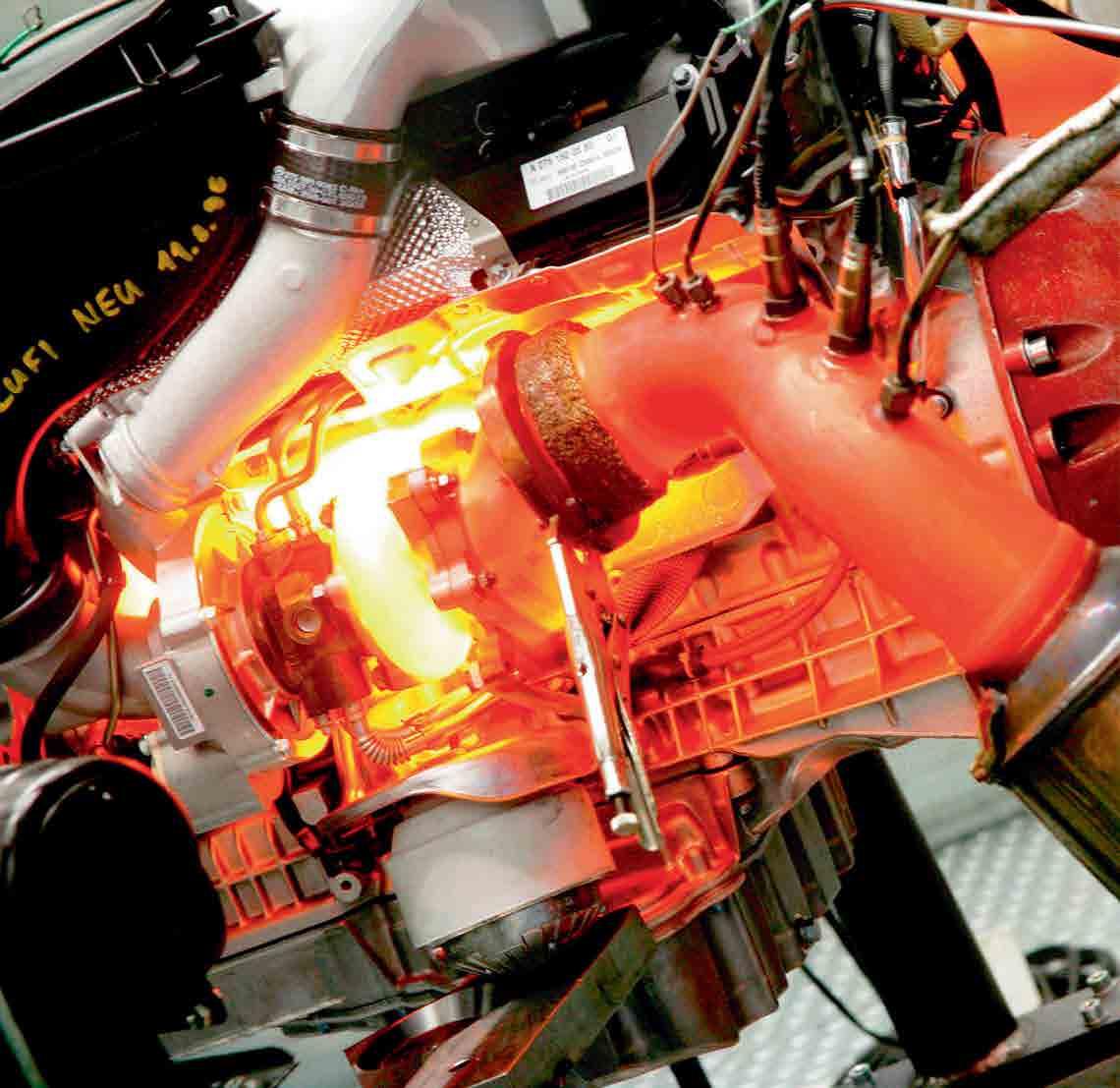
5 minute read
Precise productivity Mikron Machining
PRECISE PRODUCTIVITY
Mikron Machining, a leading supplier of customised, highly productive machining solutions, utilises its five platforms to enable its customers to be more competitive and more productive. Emma-Jane Batey spoke to Axel Warth, head of marketing and business development, to find out how this is achieved.

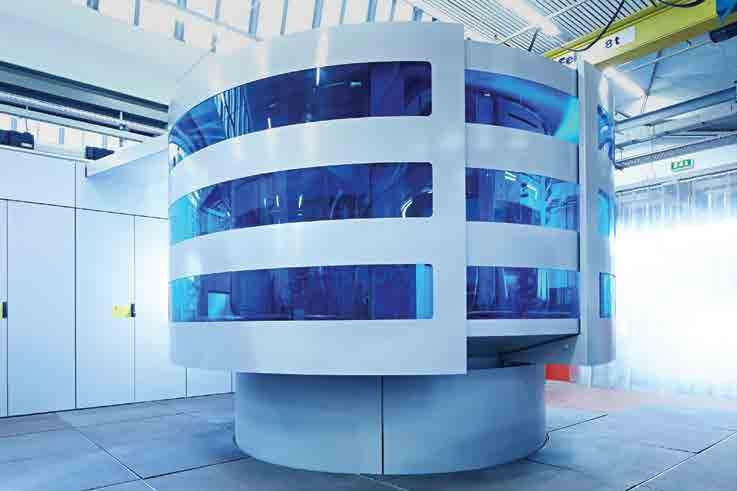
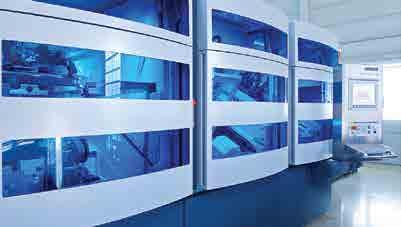
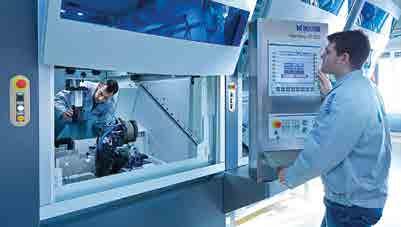
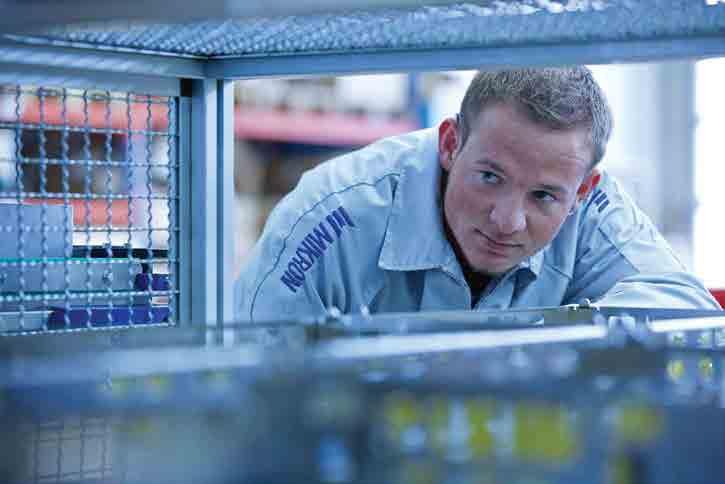
Mikron Machining employs around 530 people at its production companies – Mikron SA Agno (Switzerland, headquarters), Mikron Tool SA Agno (Switzerland) and Mikron GmbH Rottweil (Germany) – and its sales and service company Mikron Corp. Monroe (USA). As the leading supplier of customised highly productive machining solutions for the manufacturing of complex high-precision metal components, the company’s machining solutions are widely regarded as some of the best in the world. The high-performance cutting tools used on the systems are developed and produced in-house at Mikron Machining.
Having installed over 7000 machining systems worldwide, Mikron Machining customers are primarily found in the fields of automotive, electronics and telecommunications, consumer goods, building and pneumatics and hydraulics. All of the solutions offered by Mikron are developed and created in-house, thanks to a team of dedicated engineering experts.
Making customers more competitive
Axel Warth, Mikron’s head of marketing and business development, spoke to Industry Europe to explain how the company’s solutions enable its customers to be more productive. He said, “Our products and solutions support industrial production companies in a wide variety of sectors in manufacturing their products more quickly and cost-effectively, thus reducing unit costs, space requirements and staffing costs. Furthermore, customers also increase their manufacturing quality as we enable them to be more efficient. By supporting our customers in being more competitive in their markets, we are a true partner.”
Mikron Machining’s core products feature five standard platforms which effectively form the foundation of every customer solution offered by the company. Offering the Mikron Multistar family, the Mikron Multifactor, the Mikron NAM, the Mikron NRG and the Mikron Multistep XT-200, it can deliver machining solutions for work-piece sizes ranging from 20mm right up to 200mm, ensuring the highest levels of both productivity and flexibility in order to meet its customers’ myriad needs.
Working with clients to develop the ideal machining solution by carefully and expertly customising one of its five standard platforms is integral to Mikron’s ongoing, long-term success. Mr Warth explained, “We always deliver a highly productive solution for our customers because we take the time to completely understand their needs. Usually, customers come


to us with details of the product they want to manufacture or are already manufacturing and then we begin to think about how to make that product in as efficient, effective a way as possible. Through our deep understanding of our standard platforms and the unrivalled expertise of our dedicated workforce, we can deliver the best solution for them.”
Mikron Machining’s two main areas are automotive components, which currently accounts for 51 per cent of its activities, and pen tips for the writing industry, which accounts for 11 per cent. With 145 million pen tips produced daily on Mikron machines, or 40 billion tips a year, the company is proud that 95 per cent of all pen tips in the world are produced by Mikron’s customers on its machines. Mr Warth added, “There are so many astonishing numbers with Mikron! Those 40 billion pen tips a year means there are 6.5 each for every person in the world produced a year on Mikron machines. And for the automotive sector, seven million automotive parts are produced daily on Mikron machines. So this is why and how we have built our reputation for being highly productive.”
Mikron Machining‘s future is expected to yield even more ‘astonishing numbers’ for the company. With plans for continued development of its five standard platforms, it aims to maximise its recent investment in a stateof-the-art Product Lifecycle Management system. Mr Warth explained, “We introduced a PLM system in 2013 and it runs on SAP software. This impressive tool supports the standardisation of base components and the modularisation of sub-systems. Mikron Machining has continued to invest systematically in the expansion of its tool distribution network and associated global logistics in the
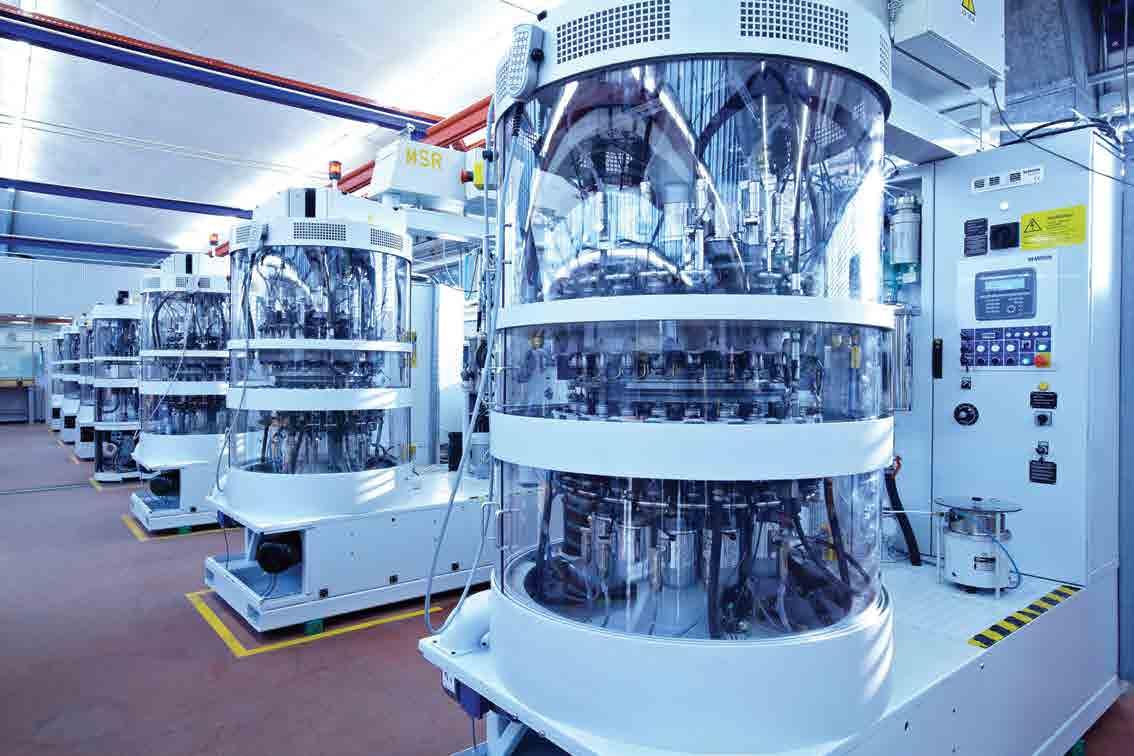
year under review, and is also ensuring that its own machinery is always up to date with the latest technological developments.
Global outreach
Currently most active in Europe and Switzerland, which account for 55 per cent and 16 per cent of its turnover respectively, the company also serves Asia Pacific, India and North America – which together account for 28 per cent of turnover. Furthermore, Mikron is also increasing its activities in other global markets. As it is able to deliver its products worldwide, the company is happy to work with customers in any sector in any country, with the common denominator being a desire for increased productivity.
Mr Warth concluded, “From our key production sites in Switzerland and Germany, together with our global network of skilled service personnel, we can serve customers anywhere in the world. As a company that is experienced in delivering solutions that enable customers to produce more in a more effective, efficient manner, we are ready to assess each customer’s needs on an individual and highly customised basis – with the end result always ensuring increased productivity through precise machining solutions.” n

TORQUE MOTORS BY TECHNAI TEAM
QUALITY FIRST, on standard or individual executions.
Since 1993, we have been developing Direct Drive technology and system design integration.
Technai Team offers a full range of standard Torque motors or individual executions, from Ø 93 to Ø 1220 mm.
The successful relationship between TECHNAI TEAM and MIKRON SA Agno, is founded on an efficient cooperation during the machine design activities, with the common aim to achieve the optimal integration between quality and performance rationality.
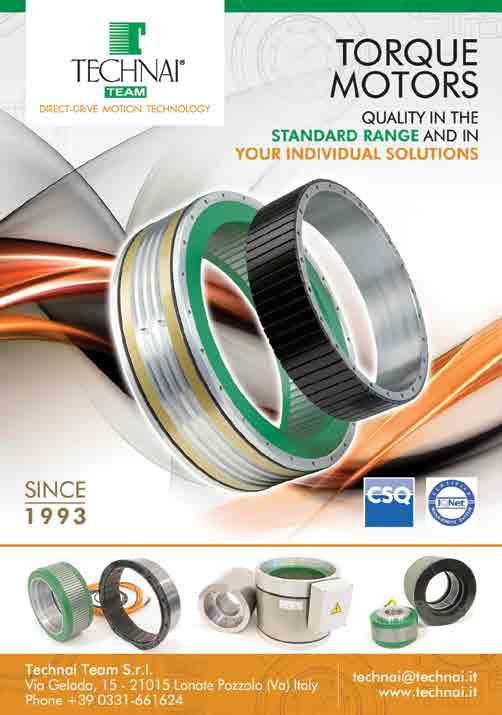