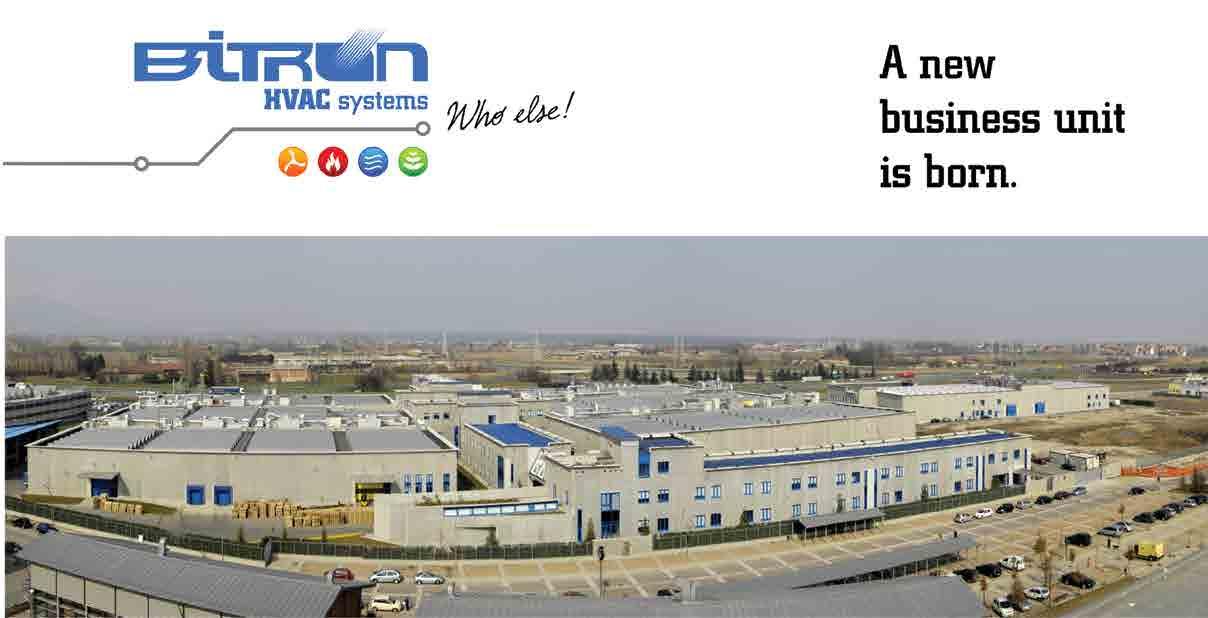
6 minute read
Advancing into new markets

Pier Balloi is the director of Bitron HVAC Systems, the new Bitron group business unit dedicated to the production of systems and components for the HVAC industry. This unit has been recently launched and has plans for an important future expansion, with the objective of increasing its turnover from the current €40 million to €80 million in 2015. Barbara Rossi reports.
The Bitron group was founded in 1955 in Turin, Italy, by Giovanni Bianco. Globally the group has 12 production sites, about 5000 employees, a turnover of €530 million and product distribution at worldwide level. It is a leading company in the development, manufacturing and distribution of systems and components for the automotive and household appliances industry. Every year the company reinvests about 7 per cent of its turnover in research and innovation.
In the past decade the company, in order to enter new markets, started producing components for the HVAC industry. In 2004 this activity was extended to the production of complete hydraulic systems for boilers and in a few years the company became the Italian leader in this field. This led, last year, to the idea of creating this third business division, following the existing automotive and household appliances activities, in order to dedicate resources to HVAC, for which there is increasing demand at worldwide level, due to both a general expansion of the heating sector and also to a need for replacement of older systems with renewable sourcesbased technology.
This third division, which aims to become an independent operation, intends to take advantage of the quality focus for which Bitron is renowned in the automotive sector and the competitiveness focus that the group has in terms of household appliances. Expansion
Growth will mainly be generated from outside Italy and six extra people are being taken on in order to follow new markets, starting with Europe as a priority, Germany, the UK, Holland, France, Spain and Italy, then followed by Turkey, China and Korea. At a later stage will be included eastern Europe and the USA. All these new markets will be approached both in terms of existing products and through the offering of new systems.
Up to now Bitron HVAC systems has exclusively supplied boiler manufacturers, but recently they’ve widened their customer portfolio to include all potential HVAC industry producers, including heat pumps, solar
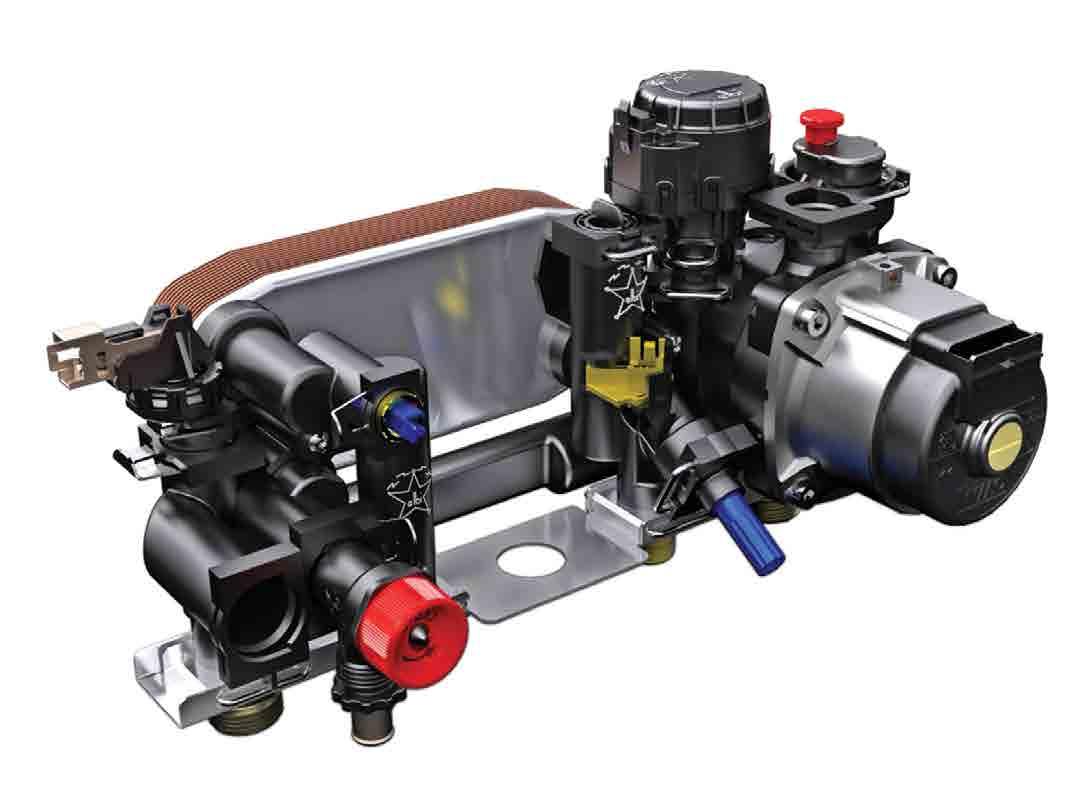
kits, pump and air cond tioning manufacturers, both in Italy and abroad. Current clients include BDR (Remeha, Baxi), Riello, ATG, BBT, Vaillant, Grundfos, Viessman and many others. In order to reach the highest level of client satisfaction the company works in close partnership with global suppliers such as Wilo Intec, Alfa Laval, Sabic and many other well-known brands.
At present the business unit produces the majority of its products at the Collegno site in Italy, but following the Bitron group strategy, there is a willingness to follow clients, which means that potentially there could be the establishment of production in Turkey or China, if there was a local request for products and systems. Some electronic components sold by Bitron HVAC Systems are already manufactured in China.
The Bitron group has made an investment to extend an existing Turkish plant, increasing its size from the current 3000 to 7000m2. This site, originally dedicated to the automotive and household appliances production lines, could also potentially be used, in the near future, for the manufacturing of HVAC systems and components.
There has also been the acquisition of 40,000m2 in China for the creation of a large site with the aim of putting together all its existing Chinese production, currently carried out at two other plants. The project should be completed by the end of 2012.
Brand and marketing
Branding and marketing are two key levers to do business today therefore Bitron decided to name the HVAC Division “Bitron HVAC Systems” in order to be well identified in the marketplace. This is the first step towards more branding activities. If you had been to ISH in March you would certainly have noticed a friendly new booth completely dedicated to customers and innovation.
A specific new website will also be developed in the coming months and technical articles in professional magazines will be published.
On-going R&D
R&D is crucial and is almost entirely conducted internally, although there are partnerships with some universities for particular projects, such as for renewable energy products. The company is particularly skilled at designing and manufacturing new products and has a series of procedures and laboratory tests guaranteeing product quality for new market launches. It employs a vertical production model, almost all internal, even at the level of the manufacturing of small components and is the only company which can pride itself in having, among its automated assembly facilities, a hydraulic group assembly line.
The HVAC division will focus on hydraulic groups and boiler electronics, both in terms
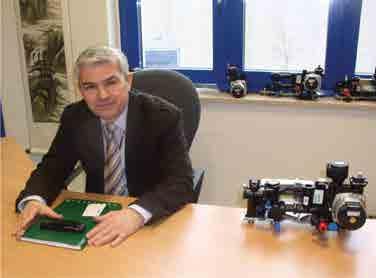

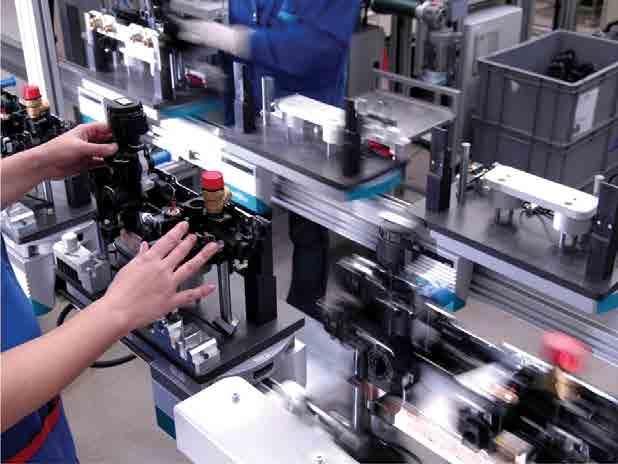
of user interface and of main boards. The unit research department is also working on new fields such as heat exchange with the aim of developing more system integration, offering systems including several components working and controlled together, and integrating functions to drive costs down. Luca Magnone, R&D director, says: “System integration” is in our DNA and we very often spot what our customers need. For example, we noticed that in some countries the boilers were drained through the safety valve; as a consequence the valve seat was full of dirt and the valve leaked. To solve that problem we made a safety valve with an integrated drain and separated channels – problem solved. Bitron is well known worldwide for its systems and components for automotive and household appliances and Bitron HVAC systems aims at replicating this reputation.
Future growth will be organic or through acquisitions of other companies both for their market share and/or for their technology and know-how.
The company holds all relevant certifications, including ISO 9001, ISO TS 16949, ISO 14001. From an environmental view point it has to be noted that its components can be easily disassembled and recycled. In addition to this all its packaging is recyclable and the Collegno site is equipped with a cogeneration system producing both heat and power (3MW). Manufacturing
According to Roberto Cazzola, manufacturing plant manager at Collegno, the main difference between household appliances, automotive and the HVAC Industry is the volumes involved. We talk about millions of components in the first two, while we talk about hundreds of thousands in the third. Eventually when you do both you cannot have two different production methods; that’s why we can be very efficient even for low volumes. The second most important difference is the quality level expected in the automotive and the household appliances – around 10 or 20 ppm. That forces you to really focus on your processes in order to limit inefficiency to its minimum. n
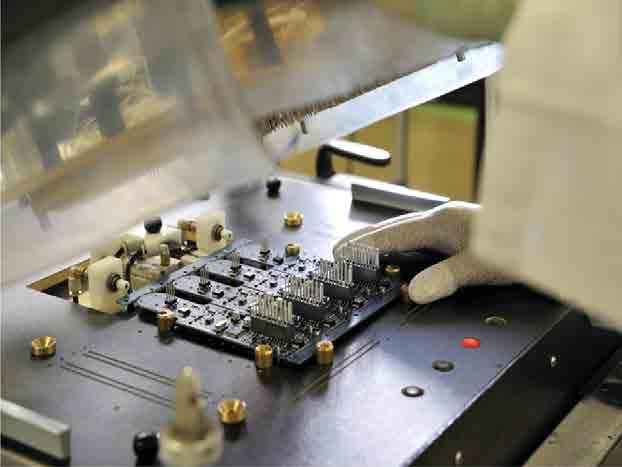
