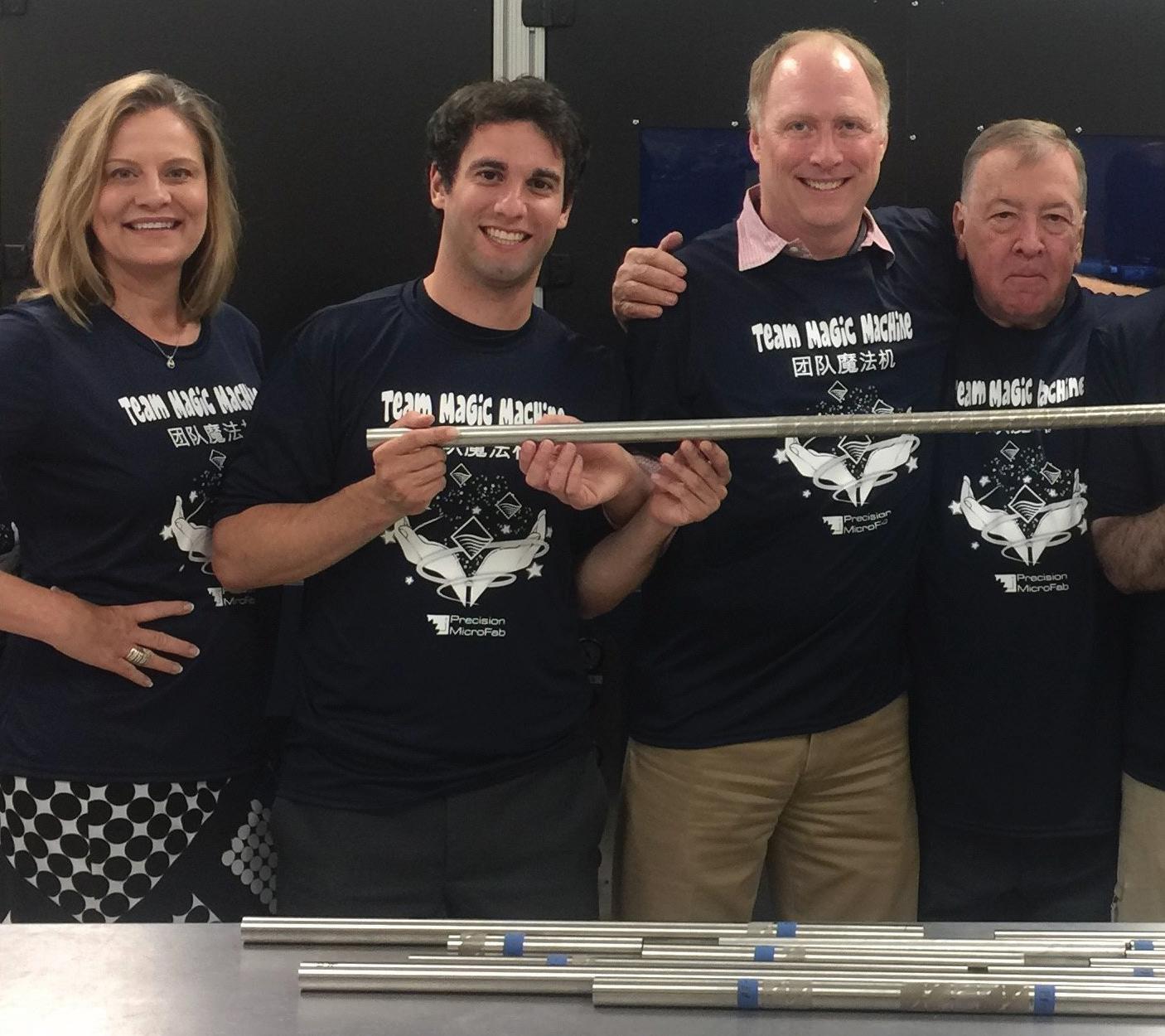
3 minute read
Innovating Tubular Filtration
2022 AFS Engineering Merit Award Takes Metal Filtration to a New Level
A stand-out company at the spring American Filtration Society FILTCON 2023 was Spectubular Technologies, makers of Precision Micro-Cut Filter Tubes. Their innovation took home the society’s coveted 2022 AFS Engineering Merit Award for their new filter element produced from seamless metal tubes through a proprietary, patented laser cutting process. They are produced from a single homogenous layer and offer significant benefits over traditional metal mesh, sintered metal, and multi-layer metal fiber filter elements.
Tubular Perks
Advantages of the company’s Precision Micro-Cut Filter Tubes provide greater durability in high temperature, high pressure, and corrosive environments, resulting in longer element life and reduced maintenance costs. The manufacturing process produces higher quality control on pore size. This technology works well for lower micron ratings from wedge-wire with similar or better flow (open area) and produces a better cleanable finish. The filter tubes were designed and developed to address specific challenges encountered with traditional metal filter media technologies. Easier cleaning and maintenance reduce production downtime and energy required for backwashing the filter element. Reduced material content (support structure and multiple media layers are not needed) result in a more cost-effective filter element. The process is designed to produce filters to custom specifications. These tubes are particularly beneficial where long-lasting back washable solid to liquid filtration of micron-level particles is required. This would include liquid filtration that is in sticky, sour, or critical service around higher temperatures or harsh environments. They could be applicable in most applications that use metal mesh, sintered media and porous or perforated metal filter elements.
Current Application
The filters are currently used in Fischer-Tropsch reactors in coal liquefaction. Syngas is converted to a synthetic crude through a series of reactions assisted by a catalyst. The syncrude is then filtered from the catalyst so that the syncrude can proceed to the next section and the catalyst can be recycled in the reactor. The Spectubular Technologies Precision Micro-Cut Filter Tubes could be an advantage for applications where the catalyst is protected by upstream filtration or a downstream collection of materials. Note, that catalyst loss is a very significant concern in refineries, as some are precious metals.
Traditional perforated tubes tend to have much larger openings where the Spectubular Technologies Precision MicroCut Filter Tubes can be as small as 10 microns and go up to 100 microns. Currently used mesh and sintered media have multiple layers through which a particle would need to travel and can get stuck within the media. This requires more time and energy to backwash and a shorter lasting filter.
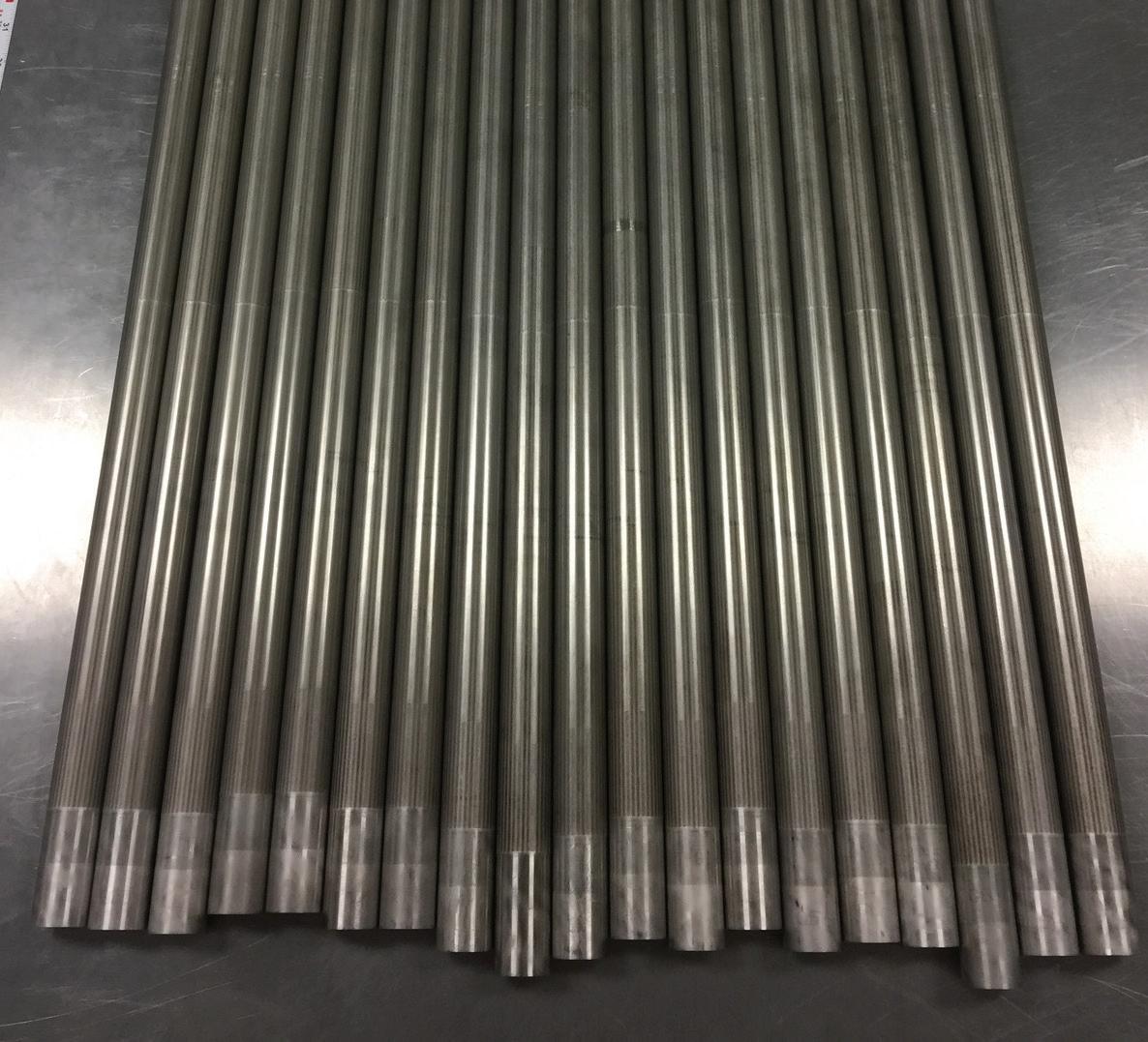
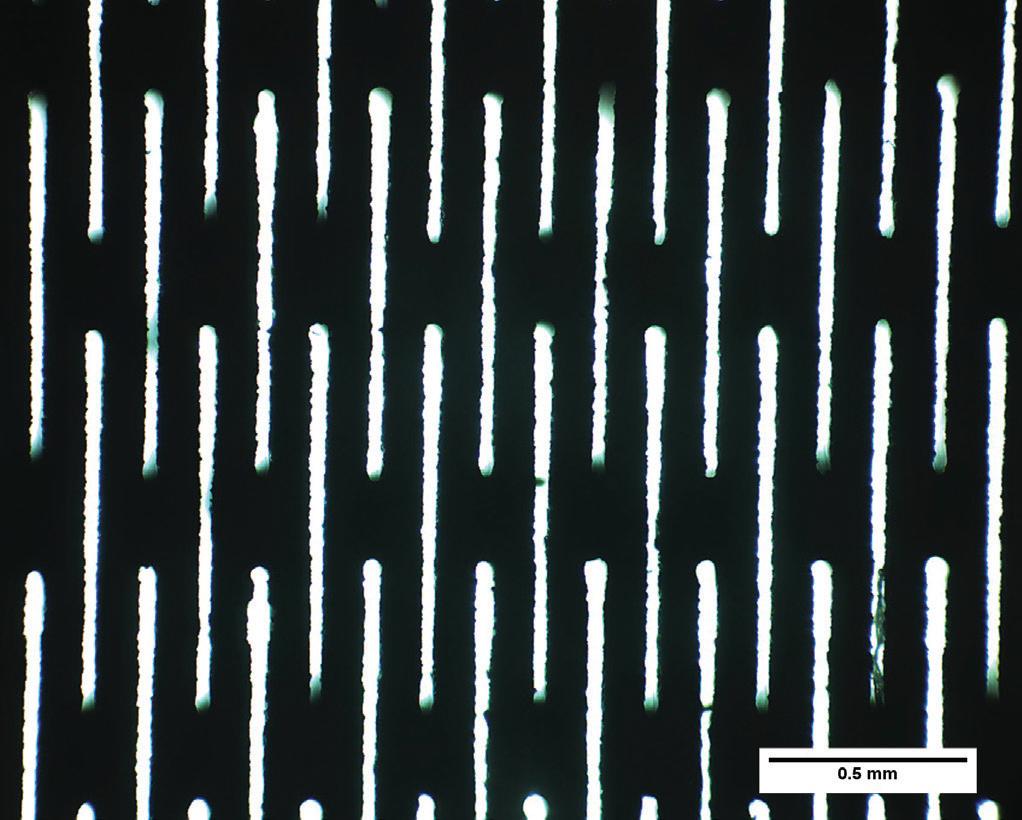


Product Inspiration
Judd Swift, President & CEO of Synfuels Americas, is quick to extend much of the credit of the Spectubular Precision MicroCut Filter Tubes to Dr. Yong Wang Li, the founder and president of Synfuels China Technology Co. Ltd., a Beijing-based company focusing on advanced conversion technologies for coal, natural gas, and other energy assets. Dr. Li is considered one of the world’s top scientists focused on FischerTropsch technology. As a leading professor at the Chinese Academy of Science and the director of the National Energy Research Center for Clean Fuels, Dr. Li leads a research team that carries out advanced research projects in industrial conversion processes. He has published more than 500 scientific papers and obtained more than 80 authorized patents. His research has won several international awards.
Dr. Li is also the Chairman of Synfuels Americas Corporation, the global platform for Synfuels China Technology Co. technology licensing, located in Dulles, Virginia.
“While working with the USA team,” explained Swift, “Dr. Li came up with the initial, high-level concept for a new type of filter that would be made from a seamless metal tube for use in the Synfuels China Fischer-Tropsch reactors. Its design would exceed the life and efficiency of filter solutions that are currently available. The filtration challenge for Fischer-Tropsch reactors is that the process must keep the valuable 20-micron catalyst inside the reactor while allowing the fluid to move quickly on to the next stage. The reactor operates at a temperature of 270°C, a pressure of 10 Bar, a pressure differential of 2-3 Bar and a plant is producing up to 100,000 barrels per day of liquid fuels.
Synfuels Americas was tasked with the job of developing a new filter design to outperform the existing filter solution that would be better able to withstand the extreme conditions and harsh environments.
R&D Ensues
Synfuels Americas’ established a new R&D filtration division, called “Spectubular Technologies,” which is led by mechanical engineer Stephen Truncale. He oversees the laser lab operations, which are in the Baltimore Maryland area. The Spectacular Technologies team works with engineers from prospective companies to develop multiple filter concept designs for testing. In the case of Synfuels China, the diameter and length specifications of the final filter product were fixed, however other aspects of the filter tube were variable and therefore needed to be tested. This included testing different materials, material thicknesses, and slot geometries. This in turn required continual modifications to the filter production process and refining of the cutting parameters.
Many iterations of the precision microcut filter tubes were developed and sent to the customer testing locations to collect data on the performance. As performance data was gathered, certain aspects of the