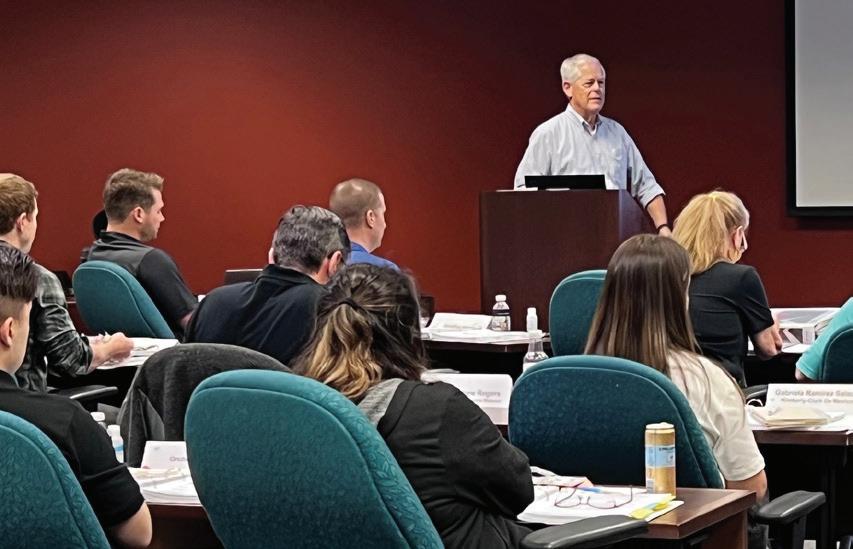
2 minute read
ADVANCE YOUR NONWOVEN SKILLS AND CAREER
Train with the nonwoven experts!
Excel in your career with one of these world-class courses designed for newcomers and seasoned nonwovens professionals alike.
Intermediate Nonwovens
April 30-May 3 & October 15-19
Elementary Nonwovens
May 7-8 & September 10-11
Nonwoven Fabric Property Development & Characterization
June 4-7
WIPES Academy
June 17-18
Fiber & Filament Extrusion Fundamentals
July 24-27
Nonwoven Product Development & Innovation
August 13-16
Absorbent Hygiene Course
August 27-29
For more information, visit: inda.org/training
Questions? Contact the Registrar registrar@inda.org +1 919 459 3724 plastic fibers, glass fibers, thermoset binders, and additives. These media exhibit a much higher bursting strength than conventional oil filter media, while eliminating the use of expensive metal meshes that support the pleated structure to save some material cost.
There are also many other patented multiple-layer structures developed by other companies every year for the purposes of automotive and aerospace filtration. These activities indicate strong demands for new composites and structures in these industries, which have driven new advanced materials to enter the market as well. Examples include blended fibers made from electrospinning high-strength or high-thermal-resistant resins, such as aramids, polysulphonamide (PSA) and polyimide (PI), with other polymers. Although these materials still have not been available in the market at a large scale, their research and development will no doubt provide new solutions for filters used in tough or new environments, such as fuel-cell vehicles in the future.
Also, every material also has potential to provide additional benefits – a fiber could exhibit significantly different characteristics when it is in different forms. For example, researchers from China’s Xi’an Polytechnic University (XPU) developed a needle-punched nonwoven from regular PET and three-dimensional crimp PET as filter media for engine oil. When the proportion between regular PET and its three-dimensional counterpart readjusted, the nonwoven’s strength, bulk, pore sizes, permeability, and filtration efficiency of the filter material would change accordingly. A desirable combination of different filtration properties can be achieved in this process.
Nanofibers made from different types of materials have also long been used to increase the filters’ ability to capture small particles. For example, the UltraWeb® Media Technology by the MNbased Donaldson Company, Inc., which adds a layer of nanofiber on cellulose media, provide a filter media with high dust holding capacity and high filtration efficiency in engine air filtration.
Recycling filter paper from used engine oil fibers is not yet economically viable, TUST’s patented technology does open a door to the future possibility.
The China-based Newstar Industry (Newstar) also developed a filter material with a nanofiber layer. The base filter paper is a composite made of cotton pulp fibers and softwood pulp fibers. Newstar’s research showed that with additional 4% nanofibers added on the filter paper’s surface, the filter media will have an average porosity of 23.8 μm, while maintaining an air permeability of 115.4 L/m2s when the pressure difference is at 200 Pa. This filter material also shows desirable bursting strength and excellent initial filtration efficiency for removing nanoparticles.
Evolving Media
The cited examples illustrate that cellulose fibers are often partially or even totally replaced by petrochemical-based and non-biodegradable fibers when pursuing durability and reliability. On the other hand, bio-based or biodegradable fibers, such as PLA, chitosan and nylon 56, are also being researched to replace petrochemical fibers in these applications. Some research even focuses on the development of PLA composites for air filtration applications, including cabin air filtration. Although the use of these bio-based materials is still in early stages, a promising and fast-growing market could be expected for the future – similar to what has occurred in the bioplastic industry.
Jason Chen is an international correspondent for International Fiber Journal . He is a leading journalist covering the fiber industry in Asia and a senior analyst who has published more than 50 books and reports for polymers, composites, and other advanced materials and technologies. He can be reached at jasonchen200501@hotmail.com.