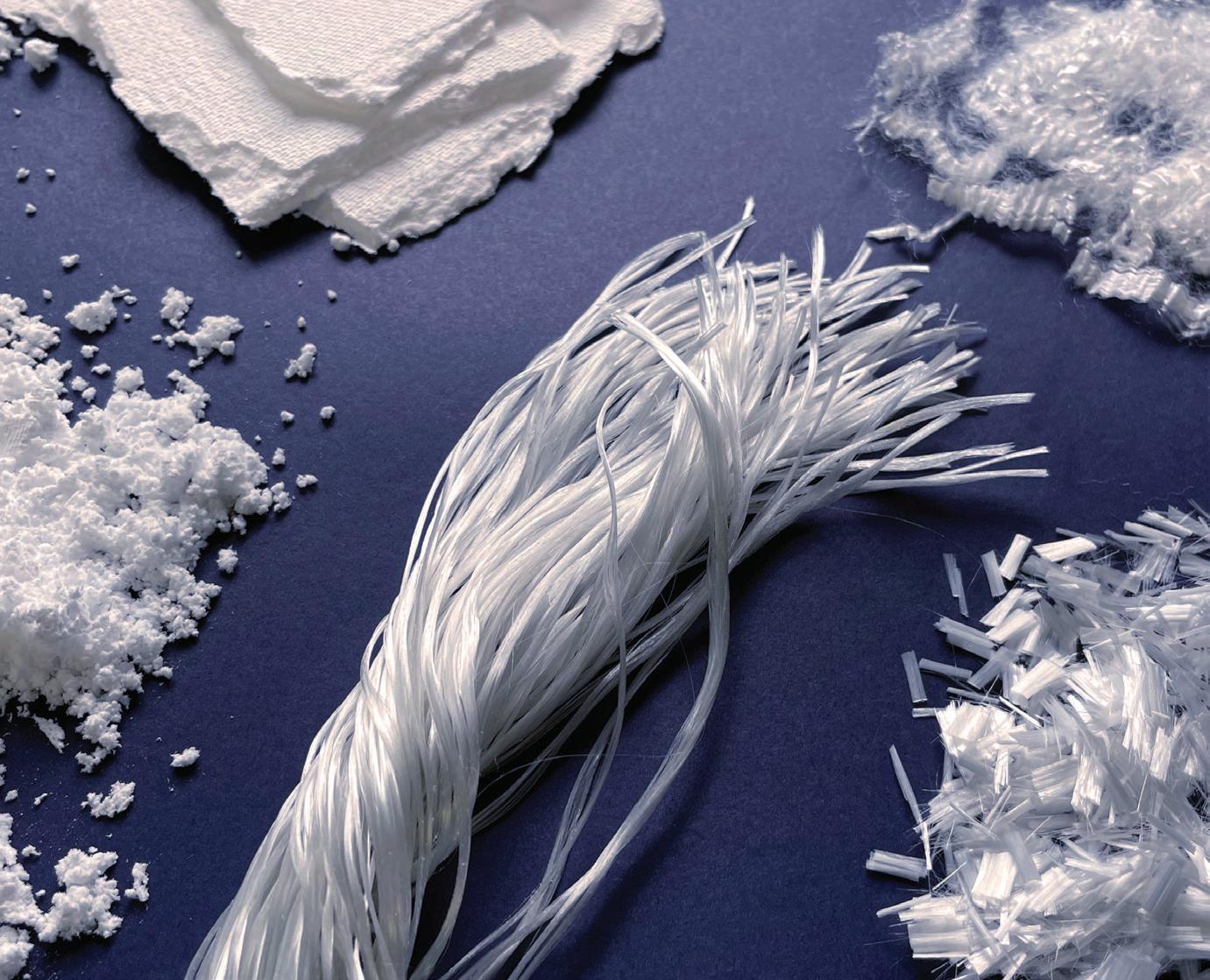
5 minute read
The Cutting Edge
By Chris Plotz
The cutting of short industrial fibers, like seen below, is a crucial step in the production of various industrial products, such as composite materials, non-woven fabrics, and other highperformance materials. Over the years, various fiber cutting or chopping technologies have been developed, each with its own advantages and disadvantages. However, with advances in technology, the future of cutting short industrial fibers is expected to be shaped by new innovations and developments.
There are many processes leading up to the formation of a fiber – whether it’s a man-man or natural fiber – to prepare it for precision cutting. While there many different types of equipment necessary to form and further process fibers, the two types of equipment that are essential to the process of cutting industrial fibers are crimping and cutting.
The crimping process is commonly utilized in the production of industrial fibers. This process involves creating a permanent crimp or wave in a fiber, which enhances its properties for use in various applications. Crimping can be applied to various types of fibers, including natural fibers, synthetic fibers, and composite fibers, and the process can be performed using different methods, including mechanical crimping, chemical crimping, and thermal crimping in a tow format. A similar crimping effect can also be accomplished on an individual fiber through the use of two different polymers extruded into a single bicomponent fiber. When the bicomponent fiber is drawn, the two polymers extend to different degrees, producing a helical crimp when the strain is relaxed.
The quality of the crimped fibers is influenced by several factors, including fiber composition, crimp pattern, and crimp frequency. The fiber composition affects the properties of the crimped fiber, as different fibers have different melting points, moduli, and tensile strengths. For example, synthetic fibers tend to have a melting point and higher modulus than natural fibers, which do not melt, and they are more resistant to shrinkage and abrasion in the process.
The cutting process involves cutting long continuous fibers into shorter lengths 2mm to 100mm, depending on the final application. The primary objective of cutting fibers is to create a homogenous fiber distribution, which enhances the properties of the final product. During the process, the speed, volume and cutting load are optimized cutting parameters.
History of the Fiber Cutting Category
The evolution of the fiber cutting category over the last decade has seen advancements in machine speed and scale. The largest manufacturing plants have capacities of up to 300 tons per day of highquality commodity PET cotton-type fibers. These integrated facilities are highly energy efficient due primarily to the scale. Crimping is one of the essential steps in the production of staple fibers. Stufferbox crimping, which is one of several crimping methods, has created new application possibilities and has made it possible to advance man-made staple fibers in textiles and nonwovens.
Stuffer box crimping is a process in which yarn coming from the supply package is pressed in a zig-zag form into a heated box (the stuffer box, usually with wet steam) in which tow or filament yarn is jammed against itself, causing a permanent crimp. Natural fibers aren’t typically straight. They have an inherent texture and crimp so crimping is not needed to facilitate further handling. Processing of manmade and natural fibers both have innate issues. Processing either fiber imparts high stress on the material and the activity is very sensitive to heat, humidity, and tension. It is essential to have a uniform distribution of incoming tow fibers to assure quality and consistency.
Advantages of Different Technologies
There are several different technologies employed in processing industrial fibers. The best technologies to employ will depend on the specific application and the end requirements. It is important to choose the current technology to ensure that the fibers are cut accurately and cleanly, and that the cut fibers are suitable for the intended application.
Guillotine cutters are great for cutting soft materials as well as specialty fibers. These machines are versatile as they can be used to cut tow as well as cut shorter noncontinuous fibers. They are adjustable in the following working parameters: cutting length, cutting speed and feeding speeds and can typically be modified while the machine is running in modern equipment.
Rotary cutters require a continuous fiber with the proper tow presentation. These cutting devices are great for highspeed and high-volume cutting. This type of cutting devise can be integrated into a comprehensive fiber manufacturing line with melt preparation, spinning, quenching, drawing, and crimping or simply crimped and cut offline when nonintegrated. The size of the tow and correct tension are critical to consistent and precision cut fibers.
Some materials are not crimped prior to cutting. These would include composite reinforcement materials such as glass, carbon and aramids. These materials do not lend themselves to crimping technologies, however they can be cut with shear cutting or rotor methods.
Key Considerations
When cutting fiber, there are several key technical considerations based on the fiber chemistries. The type of fiber material, such as carbon fiber, hemp or polyester will determine the type of cutting tool and method that is most appropriate. The diameter of the fiber will impact the cutting process and type of tools required. For example, a smaller fiber may require specialized tooling to avoid damaging the fiber. Tensile strength of the fiber will also determine the amount of force that can be applied during the cutting process. If too much force is applied, the fiber may break, become damaged or not be in tolerance. The hardness of the fiber will impact the type of cutting tool that can be used and the amount of force that can be applied. Lastly, the presence of a coating on the fiber will also impact the cutting process. Some coatings can be easily damaged while others may aid in a cleaner cut.
Trends Going Forward
The future precision fiber processing is exciting and looking ahead, developing trends could yield some amazing advancements in the next 10 to 15 years. Automation is expected to play a significant role in the future of fiber processing, both in crimping and cutting. The use of robotic systems and automation technologies will improve the efficiency and accuracy of these processes, reducing labor costs, and minimizing the risk of injury or equipment damage.
Artificial intelligence and machine learning technologies are expected to become increasingly prevalent in the future of precision fiber processing. These technologies will allow for real-time monitoring and analysis of the process, as well as the optimization of crimping and cutting parameters to improve precision and efficiency.
Non-contact crimping and cutting technologies also look to be a potential area for innovation. Nontraditional crimping and cutting utilizing ultrasonics technologies offer several advantages, including higher precision and reduced ma- terial waste. Laser and water-jet cutting do not utilize a mechanical cutting blade to function, thus reducing heat build-up due to the cutting tool. These technologies are expected to become increasing popular in the years to come.
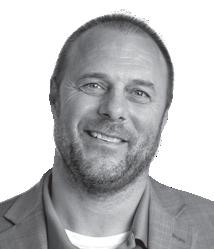
Sustainability is becoming increasingly important in all industries including precision fiber processing. The development of environmentally friendly fiber crimping and cutting technologies and the use of renewable energy sources are expected to play a significant role in the future of precision short cut and staple fiber production.
The cutting of short industrial fibers is a crucial step in the production of various industrial products, and advances in technology are expected to continue to shape the future of this process. From automation and artificial intelligence to non-contact cutting and sustainability, the trends and developments that are happening now are expected to drive the future of precision fiber cutting and improve the efficiency of the process. As demand for high-performance materials continues to grow, it is expected that the precision cutting industry will continue to evolve and adapt to meet the changing needs of its customers.
Chris Plotz is the Director of Technical and Business Development at Minifibers Inc. in Johnson City, TN. Plotz is a business leader with 25 years of technical product and business development in a number of industries. He is responsible for leading and supporting all segments of growth of Minifibers’ markets including C.A.S.E., nonwovens, composites and textiles of both synthetic and natural fibers. He can be reached at cplotz@ minifibers.com or +1 423.616.2171.