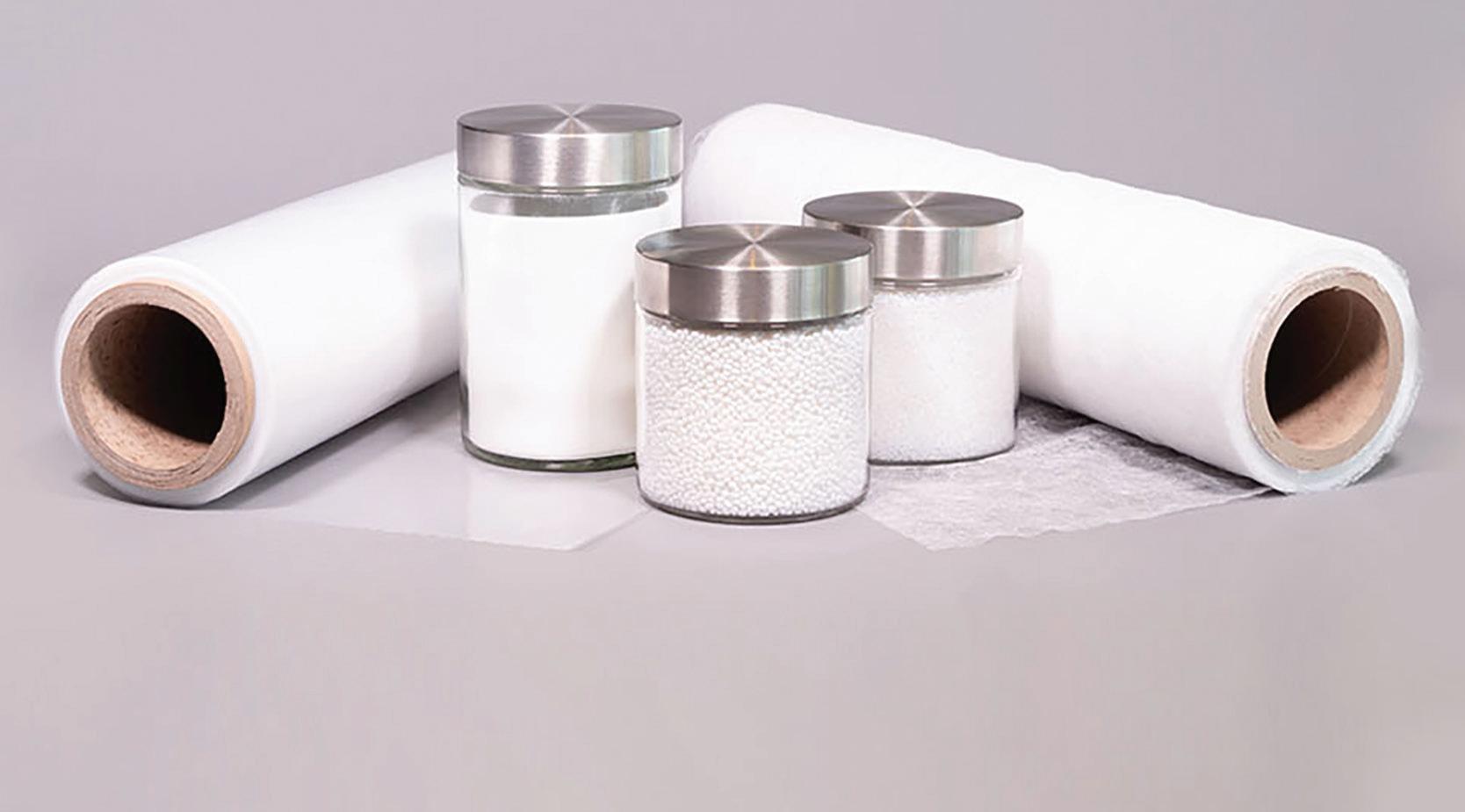
5 minute read
SUSTAINABLE TEXTILE DESIGN WITH ADHESIVES IN MIND
By Bostik, Inc. Technical Experts
n today’s market, textile manufacturers strive to enhance product sustainability while meeting high performance standards such as durability, breathability, waterproofness and softness. This sustainability focus stems from needing to address regulatory and societal pressures as well as corporate social responsibility (CSR) initiatives. However, adhesives are one component often overlooked in the sustainability journey primarily due to a lack of awareness and understanding about their impact. Instead, manufacturers may focus simply on whether the adhesive works without considering its broader impact on sustainability.
IIn fact, adhesives’ formulation, performance attributes and their impact at the end of a product’s life all influence textile manufacturing sustainability. By considering these elements during product development and throughout the product’s lifecycle, manufacturers can better design for sustainability.
Consider an Adhesive’s Formulation
An adhesive’s sustainability begins with its raw materials selection, which impacts chemistry selection for textile bonding applications. Water and solventbased adhesives provide various characteristics for textile bonding; however, they can use valuable resources (water), can contain VOCs (solvent) and require energy for evaporation (waste production) that impede sustainable design. When considering sustainable design, specialty hot melt adhesives (pellets, powders, webs and films) should be explored. In addition to reducing reliance on valuable resources and VOCs, they can be based on sustainable raw material sources, such as castor beans. For example, copolyamide hot melt adhesives (castor-based) are a great choice for more sustainable launder resistant bonding applications.
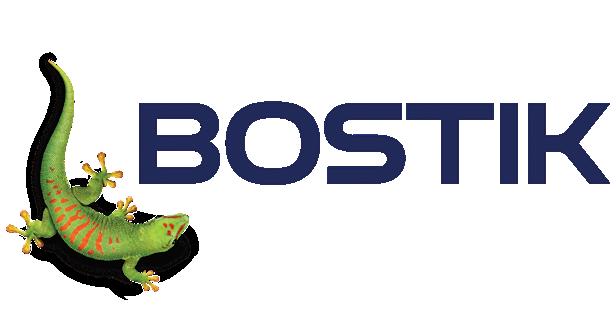
Consider an Adhesive’s Performance Attributes
Historically, certain materials, such as polyurethanes, PTFE and other petroleum-based solutions have been used in the textile industry, because they possess soft hand feel, elasticity and breathability characteristics. However, when designing for sustainability, manufacturers can consider other technologies. For example, copolyester chemistries can be designed to provide soft hand feel and elastic properties similar to that of polyurethanes while bringing monomaterial design into mind for polyester textiles. Although not an adhesive, a bio-based, breathable film membrane can pro - vide breathability and elastic properties without relying on unsustainable fluorinated chemistry in PTFE.
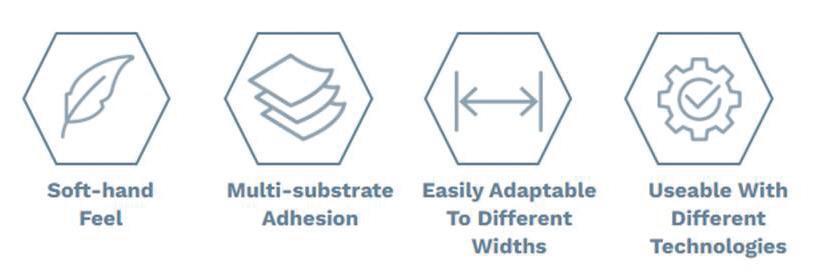
Consider an Adhesive’s Ability to Influence a Product’s End of Life
Recycling and reuse of textiles are key trends in sustainable end-of-life design, and adhesives can be a factor in more complex textile products. Disassembly and monomaterial chemistry selection are common asks for all components
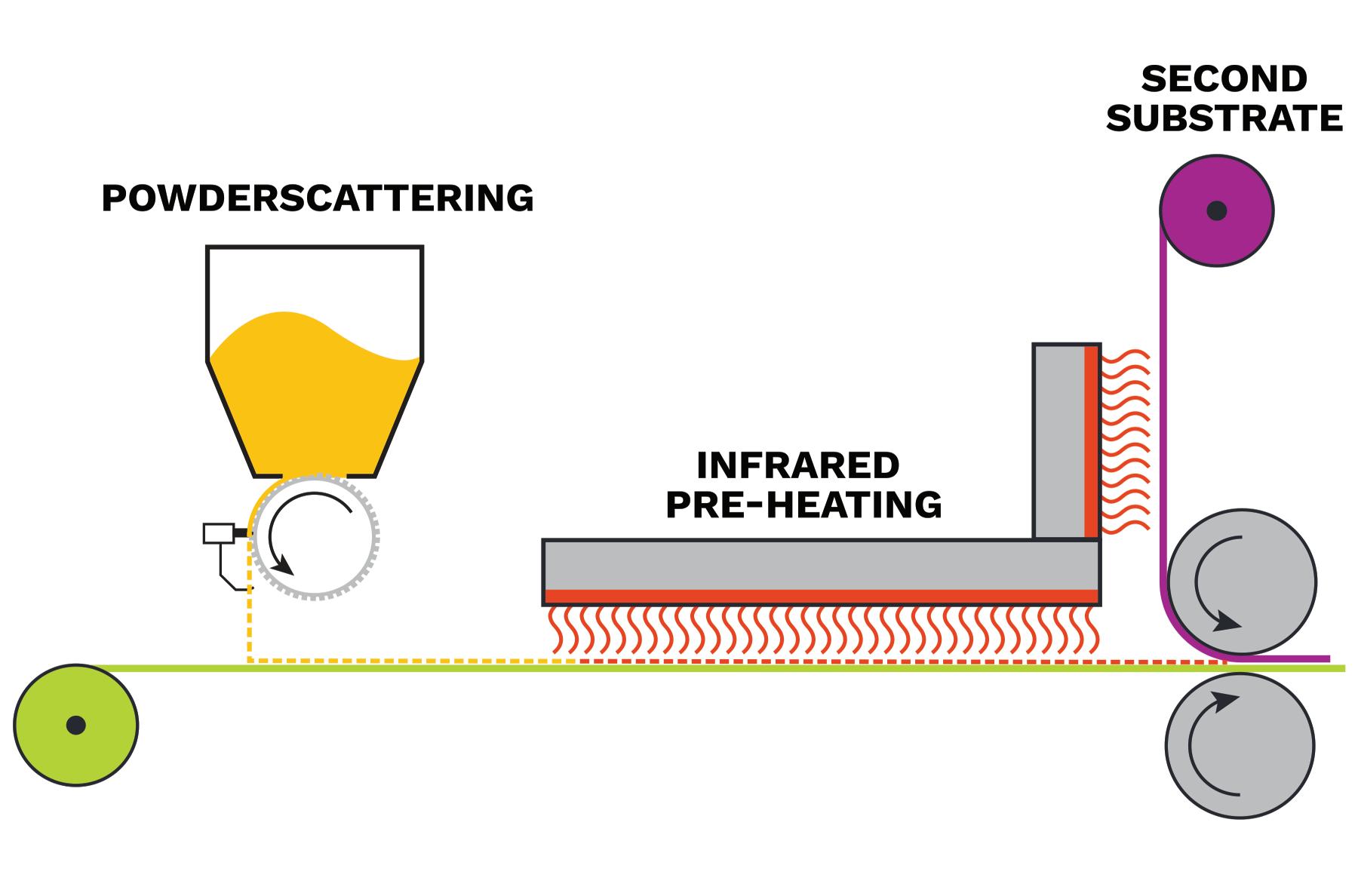
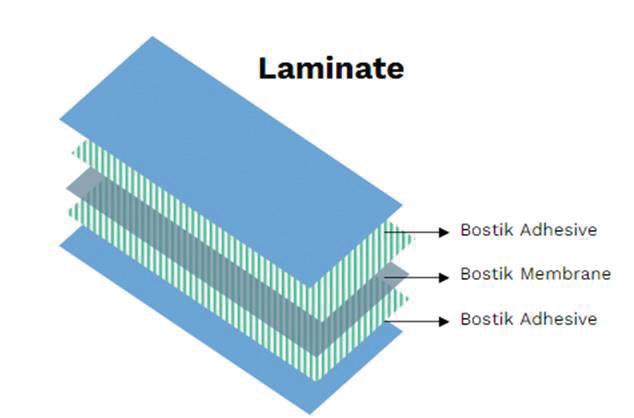
(including adhesives) of sustainable textile design. In addition to meeting performance requirements, thermoplastic specialty hot melts can offer material separation when subjected to high heat unlike thermosetting adhesives. While polyester and nylon monomaterial textile designs mitigate the need for disassembly and enhance material reusability, these designs may be difficult to achieve due to chemistry compatibility and performance. To combat this, consider copolyester and copolyamide adhesive chemistries. With similar raw materials, they can allow for flexibility in mechanical and/or chemical recycling.
By carefully selecting adhesives based on their formulation, performance and textile end-of-life impact, manufacturers can enhance their product sustainability efforts.
As an Arkema company, Bostik offers an unmatched range of specialty hot melt copolymers (pellets, powders, webs and films) to aid in sustainable textile design. These include:
• Castor bean bio-sourced adhesives for sustainable raw material selection.
• Soft hand feel copolyesters for monomaterial design and performance.
• Arkema Pebax® membrane for a sustainable alternative to PTFE membranes.
• Thermoplastic specialty hot melts for product disassembly.
To learn how these products can help you design for sustainability and get in touch with a Bostik expert at https:// tinyurl.com/munewmwn.
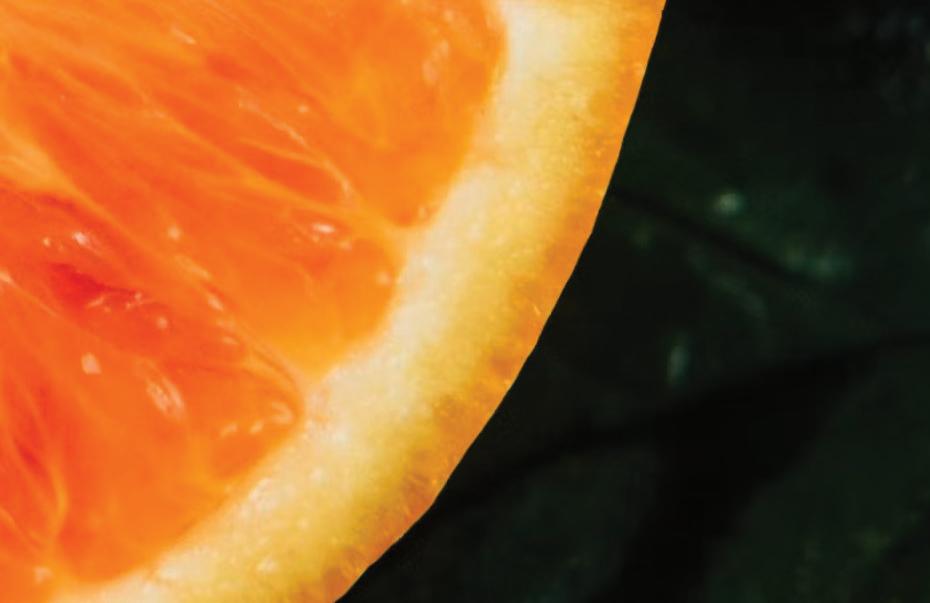

Jowat Corporation Announces New Biobased Hot Melt Adhesive Technology For Improved Sustainability
Jowat Corporation is proudly announcing the expansion of our biobased adhesive technology into the textile and product assembly markets. This biobased adhesive technology, known as GROW, replaces a high percentage of fossil-based ingredients with renewable resource ingredients for improved sustainability. This GROW biobased technology has been successfully used for two years in the packaging industry, and is now being offered for adhesives in the textile and other industries.
With GROW technology, Jowat is able to provide adhesive with up to 47% biobased content, and new formulas are being tested which will exceed 50% Biobased content. For a customer using 10,000 lbs. of adhesive per month, a Biobased adhesive can eliminate nearly 50,000 lbs. of fossil fuel-based ingredients, replacing them with renewable resourcebased ingredients.
While this improved sustainability is a welcome result, perhaps the most notable development is that this biobased adhesive requires no change in performance or processing requirements over fossil-based hot melt adhesive. It requires no change in equipment and is a drop-in replacement for fossil-based adhesives.
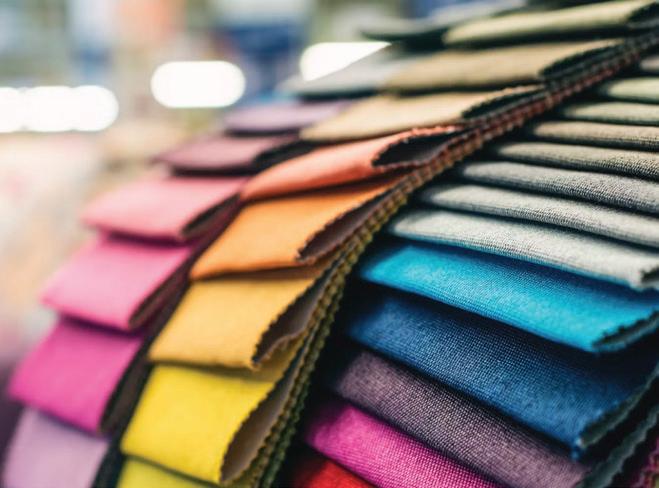
“Sustainability has been an increasingly popular adhesive topic for several years, but has remained a challenge since most options require expensive upgrades to equipment of complicated processing changes,” said John Elder, VP Sales. “This biobased adhesive is the first real world solution, where manufacturers can substantially improve their manufacturing sustainability, immediately and without disruption to their existing adhesive application.”
This technology was initially proven successful in the packaging industry, where the GROW biobased adhesive has been recognized as USDA Biobased Certified – the only hot melt adhesive to achieve this designation. This sustainability technology is now available to hot melt adhesive users in textile lamination and assembly applications, where Jowat can offer both biobased and recyclable hot melt adhesive technologies.
“Sustainability and concern for the environment is a topic that will only grow in importance for the manufacturing world,” said John Elder. Biobased adhesive can significantly reduce the use of fossil fuel, and these new developments finally offer a solution that performs without compromise.
For more information about biobased hot melt adhesive for improved sustainability, please contact Jowat Corporation at info@jowat.com, or visit us online at www.jowat.com.
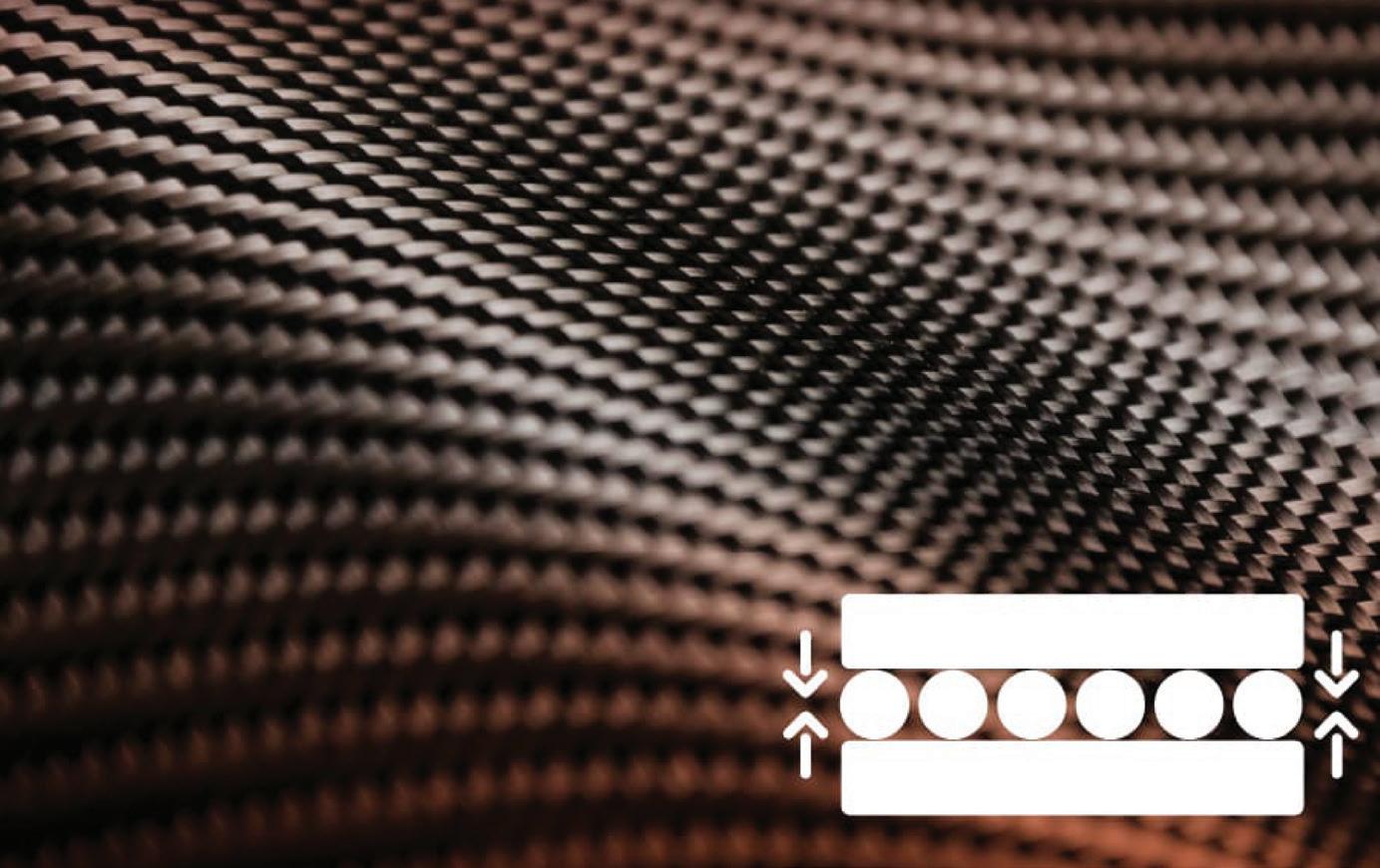
MICHELMAN'S INNOVATIVE SOLUTIONS FOR TECHNICAL TEXTILES
Michelman’s Unyte® line represents a significant leap forward in technical textile technology. By offering a non-fluorinated range of water-based, environmentally friendly solutions that enhance multiple aspects of textile performance, Michelman enables manufacturers to create more durable, functional, and versatile products. Michelman’s comprehensive portfolio of products provide the ability to improve adhesion, water repellency, and other vital properties, both for synthetic and natural fibers, without relying on fluorinated compounds or substances of concern.
For the medical market, Unyte® 211 binds multiple layers of fabric together, improving durability and wet strength, allowing medical wipes to withstand stringent performance requirements in a medical setting.
Our next-generation binder for UltraHigh Molecular Weight Polyethylene (UHMWPE) balances bind strength and adhesion between ballistic fabric layers. The binder does not degrade or change performance when exposed to high heat conditions. Beyond binding, the fiber aids in protection against bullets and sharp objects, protecting the wearer.
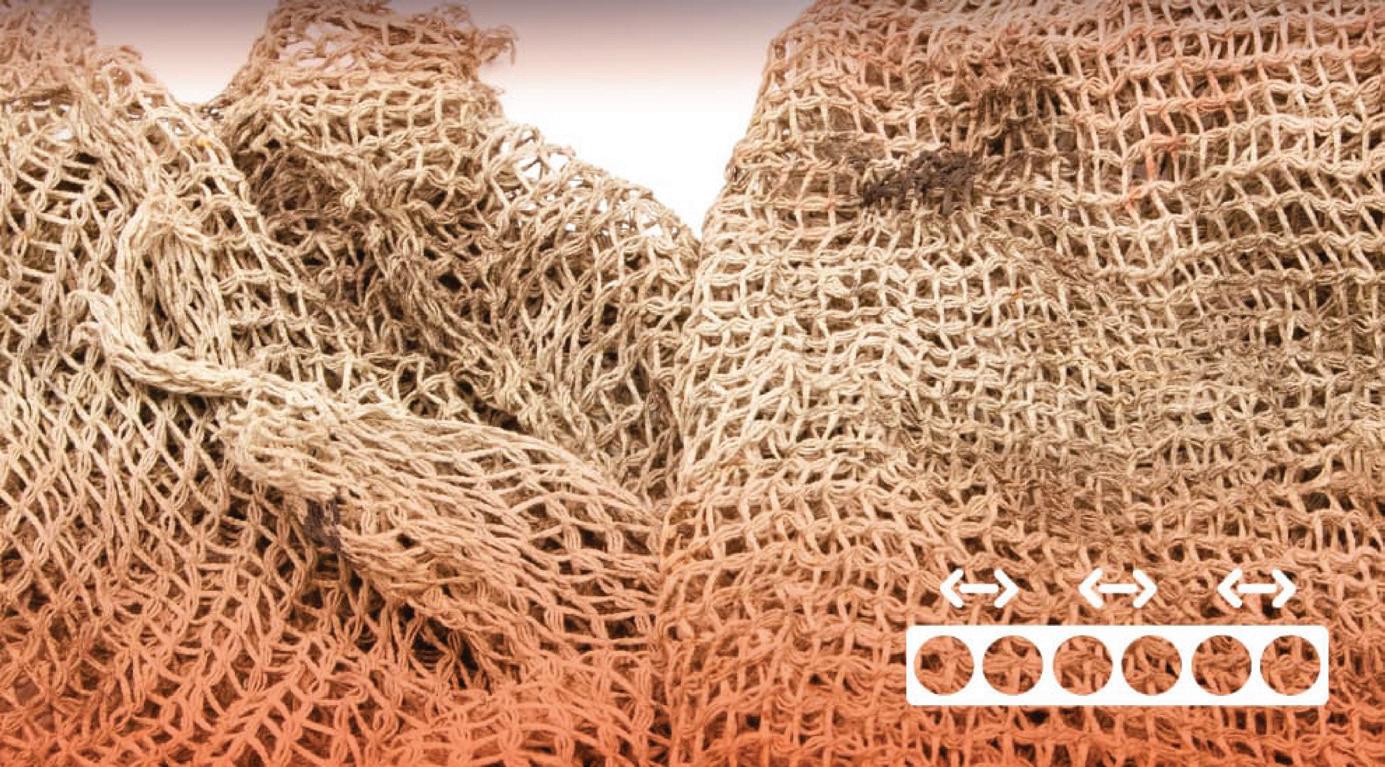
Polyimide-based Unyte® 620 is used for products that need to withstand high-heat applications. The product is heat stable up to 500ºC and retains the fiber’s adhesion properties. It also offers abrasion resistance.
As more emphasis is put on sustainability, not only do adhesion and bonding agents need to perform – there is a shift to biobased and biodegradable solutions. This aligns well for Michelman, a global developer and manufacturer of environmentally friendly materials across multiple markets. Michelman offers surface additives and polymeric binder solutions for the fibers, technical textiles, composites, coatings, printing, and packaging markets.
Michelman’s expertise extends to a diverse range of applications, including ballistics, synthetics, polymeric and natural fibers, non-woven fabrics, and composites. In these applications, adhesion and binding performance are critical to the success of the specific application and its final use. Reach Michelman at www.michelman.com.