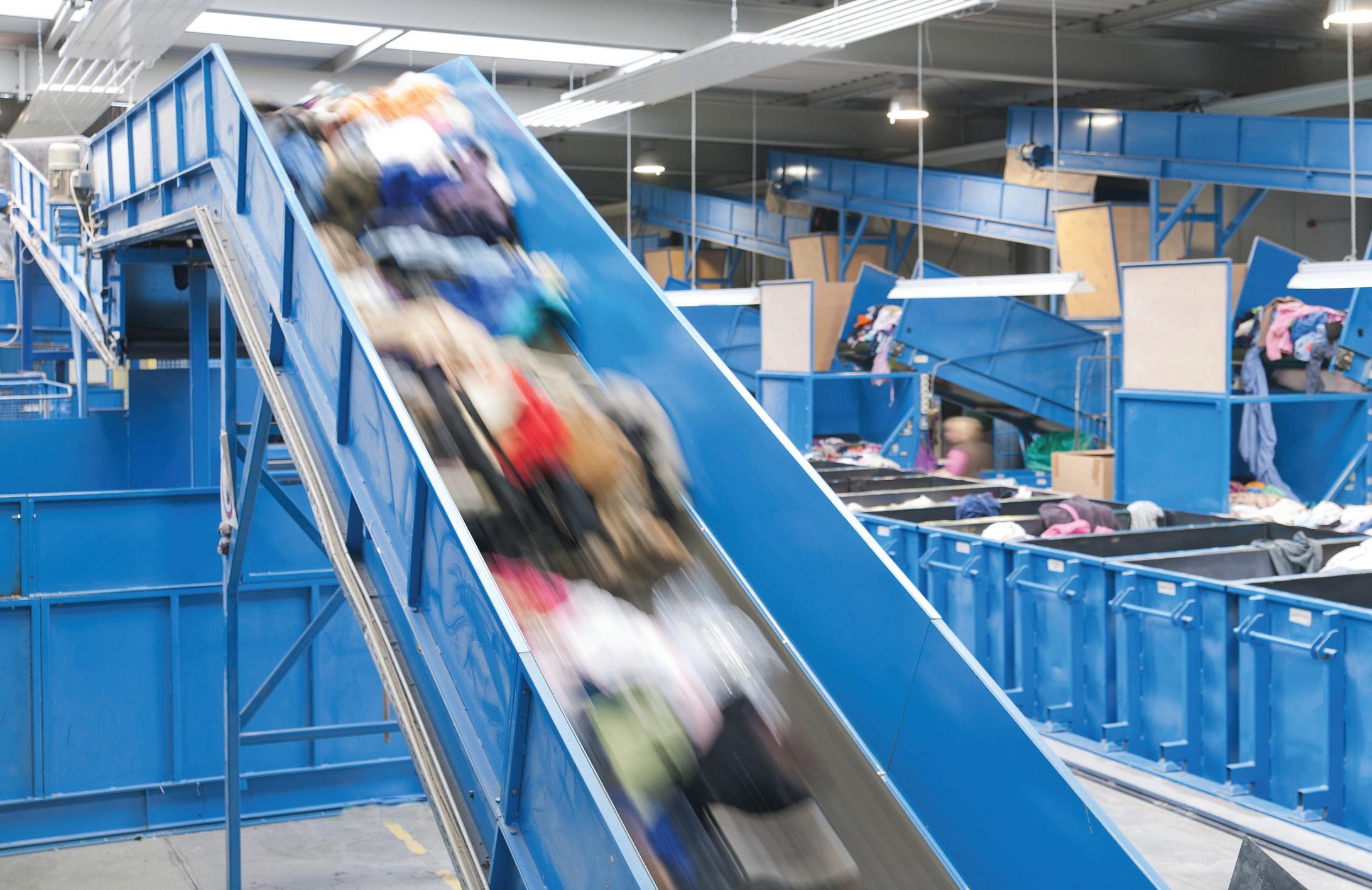
9 minute read
REDEFINING Textile Waste Sorting
Impulses and Findings for the Future on Next-Gen Sorting Facilities
The “Transform Textile Waste into Feedstock” (TTWiF) project (initiated by TEXAID within the ReHubs initiative) conducted a technology assessment to identify the best available sorting techniques and processes for textile recycling. The assessment identified the need for automated and scalable textile sorting solutions to address the challenges in recycling. The assessment evaluated various technologies and identified requirements for material composition recognition, fiber-to-fiber recycling, and pre-processing. While some technologies showed promise, there were limitations in accurately identifying material composition and capturing other performance metrics. A two-step sorting process was recommended for precise sorting in fiber-to-fiber recycling. Overall, the project aims to revolutionize the textile recycling industry and promote a more circular textile economy.
The problem is that European textile consumption contributes significantly to environmental pollution and climate
By Samanta Fruci, Anna Pehrsson and Gesine Köppe
change. There is a large amount of textile waste being generated, but only a small percentage of it is being collected and recycled. By 2025, all EU member states will be required to collect textile waste separately, which will increase the quantity of waste collected but may decrease the quality. To create a circular textile loop, the sorting process for recycled materials needs to be improved and automated.
The aim of the “Transform Textile Waste into Feedstock” project was to understand the current state of textile waste sorting in Europe and develop a blueprint for a more advanced sorting process. The project focused on three segments: semiautomated sorting for reuse, automated sorting for recycling qualities, and automated pre-processing for recycling.
The goal is to automate and enhance the sorting process by implementing technologies such as sensor-based parameter detection and digital product passports. Additionally, the project aimed to improve the accuracy of material composition determination for recycling purposes by scanning both the inside and outside of garments. Pre-processing techniques are also explored to remove impurities from products before fiber-to-fiber recycling.
Sorting on a Mission
TEXAID is a company that specializes in textile sorting and recycling. They collect and process approximately 80,000 tons of textiles each year, employing over 1,200 people and operating second-hand shops in Germany. The “Transform Textile Waste into Feedstock” project involved collaboration between TEXAID and various companies, organizations, and institutions in the textile industry to promote scaled textile sorting in Europe.
The project aims to exchange knowledge, drive innovation, and address challenges within the industry. The assessment of technologies for the project was commissioned to ITA Academy GmbH in collaboration with Institut für Textiltechnik Augsburg gGmbH, Institut für Textiltechnik of RWTH Aachen University (together representing ITA Group – International Centre for Sustainable Textiles), and SAS CETIA, France.
Batch 0
Batch 1 Batch 2
This interdisciplinary team is responsible for evaluating current processes and technologies related to textile sorting. The partnership between TEXAID and ITA Group has allowed both parties to enhance their capabilities, research expertise, and develop new relationships within the industry.
The Technology Assessment is divided into three segments that can be used independently or together. The first segment provides an overview and emphasizes the integration between the segments. A promising approach was defined to effectively sort garments, considering various competencies and technologies while avoiding duplication and maximizing synergies.
The following steps outline the recommended approach:
1. Establish general requirements and sorting criteria for recycling technologies.
2. Compile a list of best-available technologies on the market, adaptable to various process steps, conducting a technology assessment.
3. Carry out comprehensive tests for the most promising technologies to elaborate the technology readiness level, and relevant key performance indicators (KPIs).
4. Employ a decision matrix for technology and supplier evaluation, incorporating prioritization and risk analysis.
5. Develop a comprehensive plan for a demo plant.
6. Conduct a gap analysis between the current state and desired outcomes, identifying areas for improvement and optimization in the recycling process.
To achieve the capabilities in automatic sorting for reuse and recycling, several technologies in transportation, preparation, feeding, detection, sorting, and logistics were analyzed. For the observation, current state-of-the-art machines, processes and software solutions were researched, tested, and evaluated aligning and incorporating automation, robotics, sensor technology, and artificial intelligence.
Key Requirements
During the research phase of the project, over 160 requirements for technologies and feasibilities were gathered and evaluated by an international consortium of recyclers, manufacturers, tech startups, and brands. The consortium identified key requirements such as autonomous operation and non-damaging effects on garments. They also emphasized the importance of storing historical sensor and machine data for traceability purposes. Product and quality categories are crucial for recycling, with fiber composition being a fundamental factor in sorting. The system should be able to scan both external and internal aspects of garments, including trims. Accuracy in sorting categories is essential for fiber-to-fiber recycling, with a tolerance level of no more than 5%. Color sorting should also be facilitated. The aim is to automate over 90% of the recycling process. The system should be extendable to accommodate future upgrades or adaptations as recycling technologies evolve. Timely implementation by the end of 2023 is necessary to meet project timelines and objectives.
At the start of the research project, a comprehensive survey was conducted, involving a diverse spectrum of companies representing the entire recycling process chain. This survey involved participants from different textile recycling sectors, with active participation by the entire project consortium. The survey’s overarching objective was to elicit insights into the prerequisites associated with source materials, processing methodologies, and sector-specific requirements.
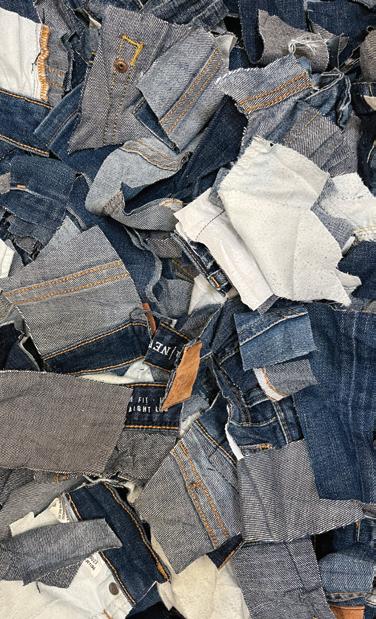
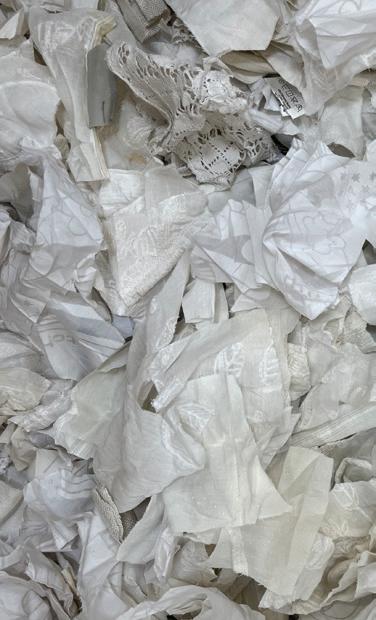
The survey focused on both existing and potential recycling methods, with an emphasis on supporting circular economy practices. It also analyzed mechanical, chemical and thermomechanical recycling processes to identify relevant categories. Key performance indicators were derived from the survey results and ranked through a pairwise comparison to enable a systematic approach to technology selection.
Sorting and Testing
The assessment focused on sorting solutions for reuse and evaluated AI-based algorithms for pattern recognition and handling garments. Different technologies such as tray sorters, separation robots, and garment-on-hanger systems were ex- amined for feasibility. Sorting categories were developed for recycling scenarios, and various sensors were trained through a program. Industrial individual solutions and complete sorting solutions were considered based on market readiness.
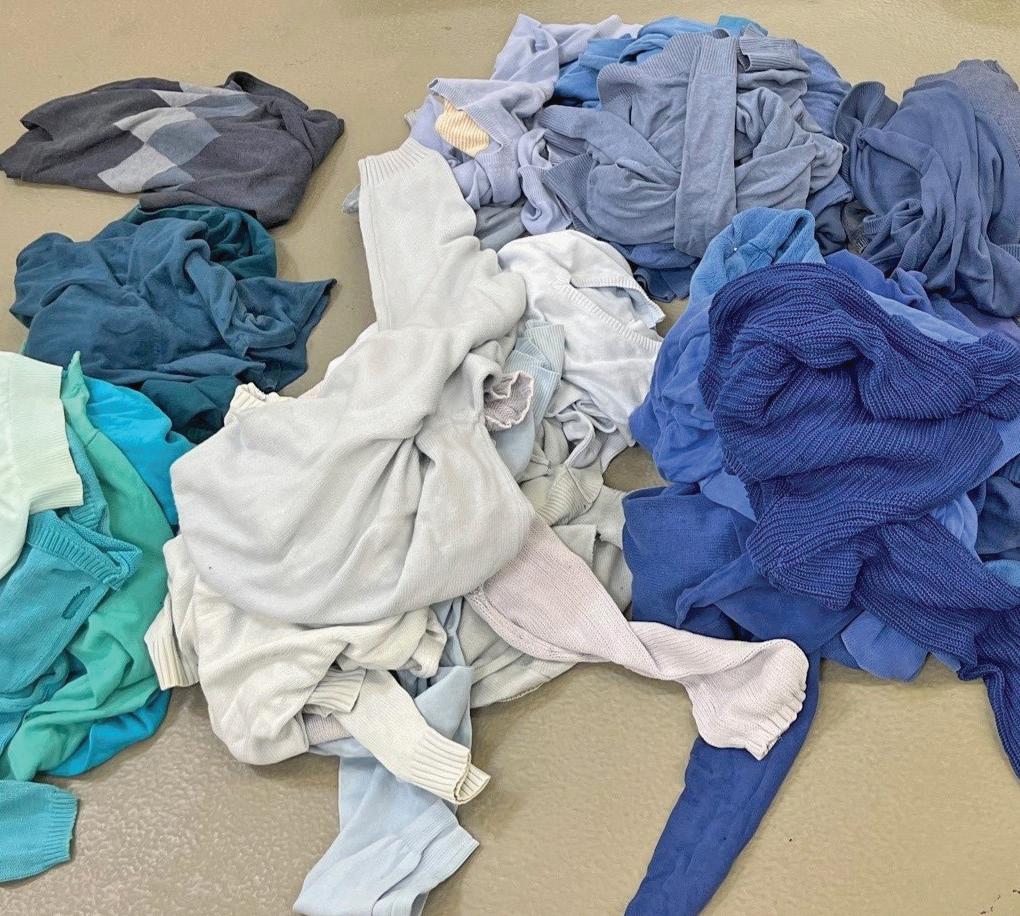
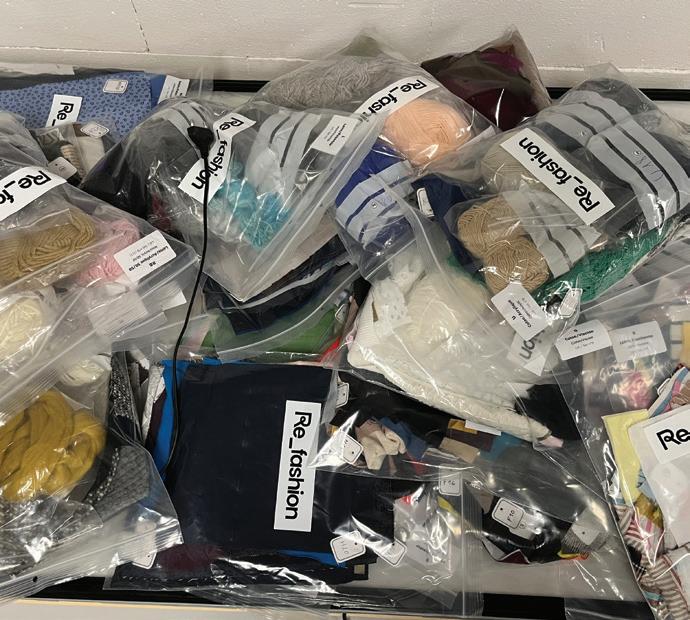
The testing process involved evaluating material composition recognition using different batches of textile samples. The results showed that while color recognition was satisfactory, material composition recognition had significant deviations in the case of mixtures. A two-step sorting stage was determined to be necessary due to unmeasured performance metrics such as impurities, contaminants, feedstock format, fabric structure, and weight.
The process flow for multicategory sorting and binary category sorting in recycling was elaborated upon, including the use of spiked lattice conveyors, sensors for composition detection, pressure nozzles for diverting textiles into chutes based on their composition, bale pressing mechanisms to compress sorted textiles into packages, cutting processes to enhance purity before sensor-based detection in binary sorting, and the removal of metal contaminants but limitations in detecting plastic contaminants or patches like leather or embroidery. The binary sorting solution is considered a quality control step for recyclers to ensure precision in feedstock specification before recycling.
Challenges that Shape Solutions
To conclude the main challenge is that it is difficult to develop a process where different steps with different TRLs are combined throughout the process. Added to this, there is the complexity of the unevaluated area of textile waste sorting and several technologies not developed for the use case of textiles. Dealing with the complexity of textile waste is another issue, as textile waste is not standardized by comparison to other waste streams, where sorting for reuse is also not the case.
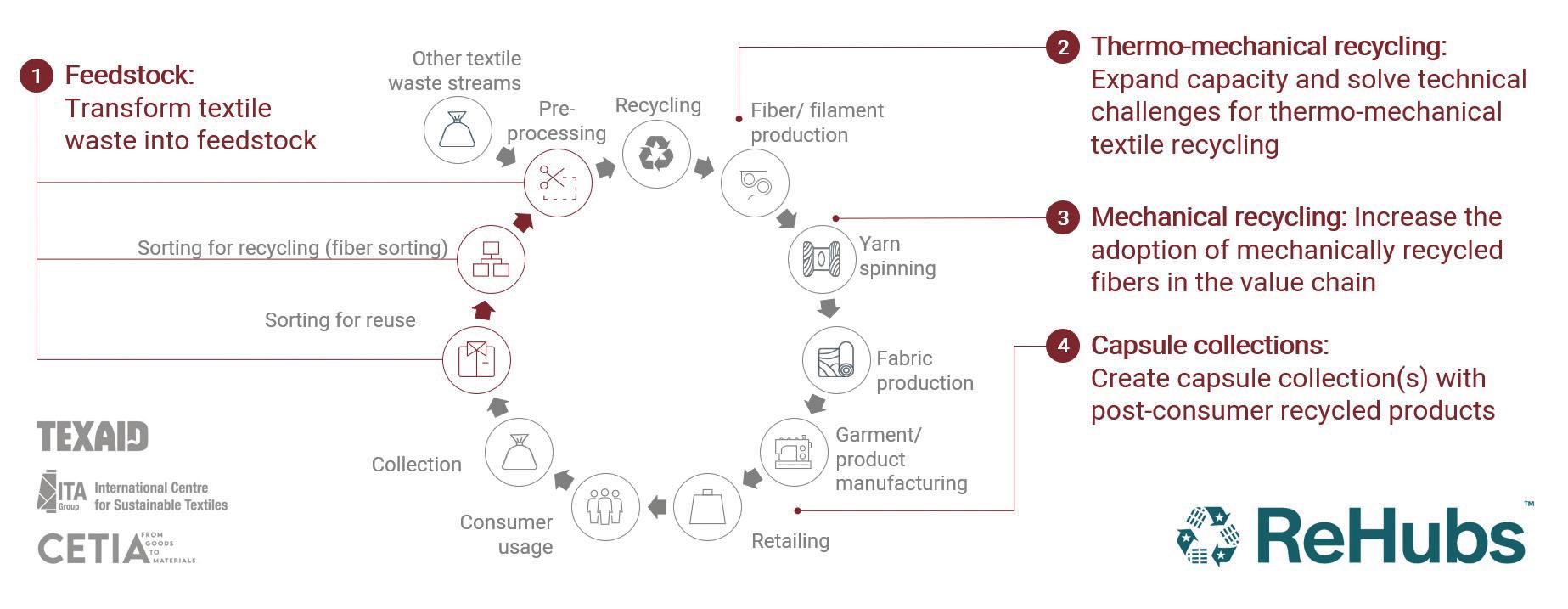
For the semi-automated sorting for reuse, the TRL is still very premature, and it will be challenging to fully automate this step in the future. Skilled operators will still be key when sorting textile waste according to the waste hierarchy. When it comes to automated sorting for recycling, theoretical research and testing show that the sensors are not mature enough to sort as exactly and precisely as the recyclers need their feedstock to be.
There is a technology gap and two main points were found that will be important to develop further. Firstly, the databases behind the technologies and secondly the accuracy and precision of the scanning itself.
Pre-processing is also very specific and different depending on the use case and the specific recycler, which makes a standardized solution difficult. Therefore, the idea of two-step sorting for recycling could be a way to tackle the issue of quality control and pre-processing. In general, the requirements vary considerably for the different use cases, the value chains, and stakeholders per use case, which makes sorting and pre-processing for reuse and recycling more complex.
It was also found that from a technological point of view, there is not only a lack of datasets but also the need to digitalize the entire sorting process to unlock the potential of data in sorting in the future.
The collaborative project has revealed the current challenges in developing an innovative process with new technologies due to the unexplored field. Following the vision to shape the textile circularity in Europe and therefore to significantly reduce CO² emissions, TEXAID is committed to investing in an infrastructure of 50,000 tons of new sorting capacity in Europe using new technologies.
For a spin-off project proposal to address the current gaps, TEXAID is inviting interested parties to expand the network and work together on innovations that will make the future more sustainable.
Samanta Fruci is in Marketing at TEXAID AG.
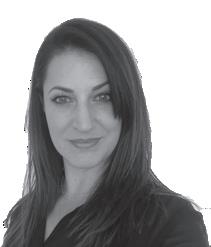
Anna Pehrsson is in Recycling Solutions Lead at TEXAID AG. As a textile Engineer with specialization in textile recycling, her passion is for turning the textile industry circular.
Gesine Köppe is a Member of managing board, ITA Academy GmbH who focuses on textile design enriched by technical product development and digital applications that streamline the production process.
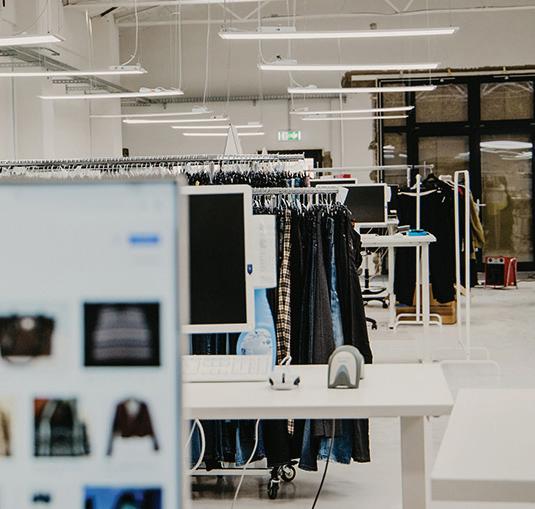
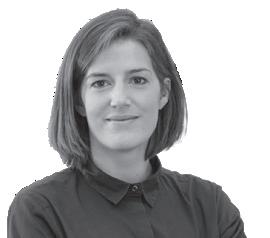
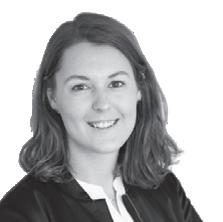