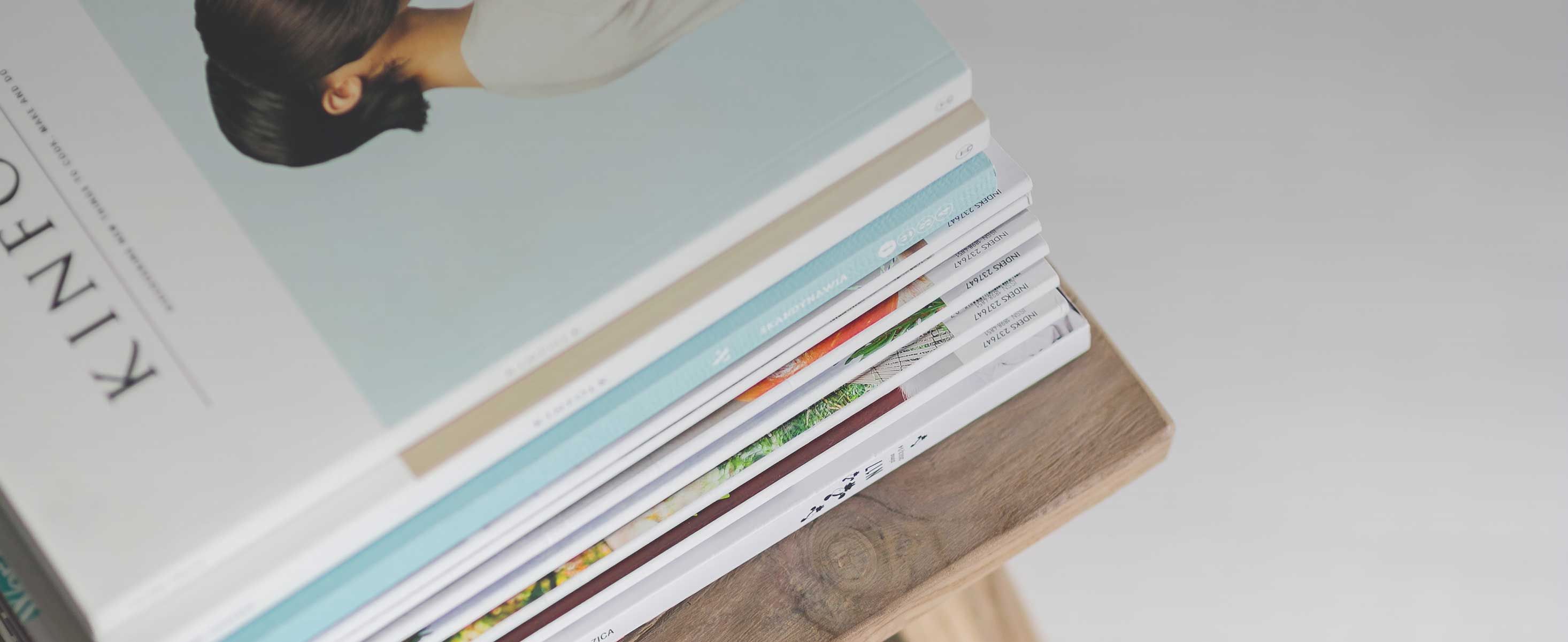
4 minute read
International Journal for Research in Applied Science & Engineering Technology (IJRASET)
from Study on Mechanical and Durability Characteristics of Sustainable Geopolymer Concrete
by IJRASET
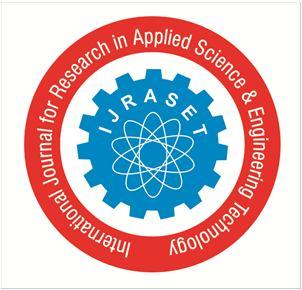
ISSN: 2321-9653; IC Value: 45.98; SJ Impact Factor: 7.538
Advertisement
Volume 11 Issue III Mar 2023- Available at www.ijraset.com
C. Flexural Strength
The implicit measure of the stiffness of unreinforced concrete is the modulus of rupture, also referred to as the flexural strength of concrete. Instead, the modulus of rupture can be characterised as a measurement of the excessive fibre stresses when a member is bent. Together with external force, other factors such as warping, steel corrosion, drying shrinkage, and temperature gradient can also cause tensile stresses.
ISSN: 2321-9653; IC Value: 45.98; SJ Impact Factor: 7.538
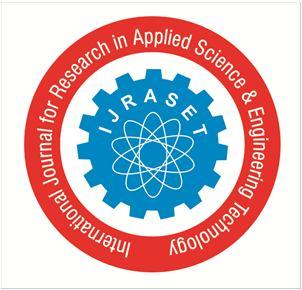
Volume 11 Issue III Mar 2023- Available at www.ijraset.com
IV. CONCLUSION
GPC that uses by-product materials is highly sought after for more environmentally friendly construction. The goal of this study was to improve the qualities of high-strength ecologically friendly concrete by adding MBS and GGBS to the mix. The main goal of this experimental inquiry is to ascertain the effects of mixing MBS with various amounts of concrete and mortar that have been alkali activated using slag.
Also to determine the effects of MBS inclusion on the final product, which included testing various amounts of slag-based alkali activated mortar and concrete,
1) From the process used, it can be deduced that the geopolymer mix with 90% GGBS and 10% MBS has a compressive strength that is 22.41% higher than regular portland cement.
2) Because of the replacement materials' ability to bond, it has been found that when the amount of micronized biomass increases gradually, silica gradually loses some of its mechanical qualities.
3) Comparing the observed concrete to regular portland cement, the split tensile strength is 37.75% higher.
4) When the findings for compressive strength, split tensile strength, and flexural strength are compared to those of regular portland concrete, the results for geopolymer concrete with ground granulated blast furnace slag and micronized biomass silica are found to be greater.
5) For all specimens, the concrete's ability to absorb water is below the limit, indicating high concrete quality. By adding micronized biomass silica, the chloride ion penetration is also successfully resisted.
6) In conclusion, this developed GPC mix has been proven to be promising for use in a variety of constructions, including loadbearing, concrete highway, and non-load bearing structures.
References
[1] Hajimohammadi, T. Ngo, and J. Vongsvivut, “Interfacial chemistry of a fly ash geopolymer and aggregates,” J Clean Prod, vol. 231, pp. 980–989, Sep. 2019, doi: 10.1016/j.jclepro.2019.05.249.
[2] R. J. Myers, S. A. Bernal, and J. L. Provis, “Phase diagrams for alkali-activated slag binders,” Cem Concr Res, vol. 95, pp. 30–38, May 2017, doi: 10.1016/j.cemconres.2017.02.006.
[3] C. Shi, A. F. Jiménez, and A. Palomo, “New cements for the 21st century: The pursuit of an alternative to Portland cement,” Cement and Concrete Research, vol. 41, no. 7. Elsevier Ltd, pp. 750–763, 2011. doi: 10.1016/j.cemconres.2011.03.016.
[4] M. Amran, R. Fediuk, S. Klyuev, and D. N. Qader, “Sustainable development of basalt fiber-reinforced high-strength eco-friendly concrete with a modified composite binder,” Case Studies in Construction Materials, vol. 17, p. e01550, Dec. 2022, doi: 10.1016/j.cscm.2022.e01550.
[5] M. Amran et al., “Properties and performance of polypropylene fibered high-strength concrete with an improved composite binders,” Case Studies in Construction Materials, vol. 17, p. e01621, Dec. 2022, doi: 10.1016/j.cscm.2022.e01621.
[6] X. Xue, Y.-L. Liu, J.-G. Dai, C.-S. Poon, W.-D. Zhang, and P. Zhang, “Inhibiting efflorescence formation on fly ash–based geopolymer via silane surface modification,” Cem Concr Compos, vol. 94, pp. 43–52, Nov. 2018, doi: 10.1016/j.cemconcomp.2018.08.013.
[7] G. Liang, H. Zhu, Z. Zhang, Q. Wu, and J. Du, “Investigation of the waterproof property of alkali-activated metakaolin geopolymer added with rice husk ash,” J Clean Prod, vol. 230, pp. 603–612, Sep. 2019, doi: 10.1016/j.jclepro.2019.05.111.
[8] Y. C. Choi and S. Choi, “Alkali–silica reactivity of cementitious materials using ferro-nickel slag fine aggregates produced in different cooling conditions,” Constr Build Mater, vol. 99, pp. 279–287, Nov. 2015, doi: 10.1016/j.conbuildmat.2015.09.039.
[9] C. S. Poon, Y. L. Wong, and L. Lam, “The influence of different curing conditions onthe pore structure and related properties of fly-ash cement pastes and mortars,” Constr Build Mater, vol. 11, no. 7–8, pp. 383–393, Jan. 1997, doi: 10.1016/S0950-0618(97)00061-5
[10] Y. Jun and J. E. Oh, “Microstructural characterization of alkali-activation of six Korean Class F fly ashes with different geopolymeric reactivity and their zeolitic precursors with various mixture designs,” KSCE Journal of Civil Engineering, vol. 19, no. 6, pp. 1775–1786, Sep. 2015, doi: 10.1007/s12205-0150132-7
[11] D. L. Y. Kong and J. G. Sanjayan, “Effect of elevated temperatures on geopolymer paste, mortar and concrete,” Cem Concr Res, vol. 40, no. 2, pp. 334–339, Feb. 2010, doi: 10.1016/j.cemconres.2009.10.017.
[12] D. Adak, M. Sarkar, and S. Mandal, “Effect of nano-silica on strength and durability of fly ash based geopolymer mortar,” Constr Build Mater, vol. 70, pp. 453–459, Nov. 2014, doi: 10.1016/j.conbuildmat.2014.07.093.
[13] A. Kusbiantoro, M. F. Nuruddin, N. Shafiq, and S. A. Qazi, “The effect of microwave incinerated rice husk ash on the compressive and bond strength of fly ash based geopolymer concrete,” Constr Build Mater, vol. 36, pp. 695–703, Nov. 2012, doi: 10.1016/j.conbuildmat.2012.06.064.
[14] A. N. Givi, S. A. Rashid, F. N. A. Aziz, and M. A. M. Salleh, “Assessment of the effects of rice husk ash particle size on strength, water permeability and workability of binary blended concrete,” Constr Build Mater, vol. 24, no. 11, pp. 2145–2150, Nov. 2010, doi: 10.1016/j.conbuildmat.2010.04.045.
[15] M. Amran, G. Murali, R. Fediuk, N. Vatin, Y. Vasilev, and H. Abdelgader, “Palm Oil Fuel Ash-Based Eco-Efficient Concrete: A Critical Review of the ShortTerm Properties,” Materials, vol. 14, no. 2, p. 332, Jan. 2021, doi: 10.3390/ma14020332.
[16] Y. H. M. Amran, R. Alyousef, H. Alabduljabbar, and M. El-Zeadani, “Clean production and properties of geopolymer concrete; A review,” J Clean Prod, vol. 251, p. 119679, Apr. 2020, doi: 10.1016/j.jclepro.2019.119679.
[17] Y. H. M. Amran, R. Alyousef, H. Alabduljabbar, and M. El-Zeadani, “Clean production and properties of geopolymer concrete; A review,” J Clean Prod, vol. 251, p. 119679, Apr. 2020, doi: 10.1016/j.jclepro.2019.119679.