
11 minute read
ARF RESEARCH
Ammonia Refrigeration Foundation Research
Recently Completed Projects and Deliverables
Recent ARF-funded research has produced important new information that has already made its way into various IIAR standards and publications. Following are some examples of how the IIAR Research Committee has put ARF funding to good use.
CFD Simulation of an Ammonia Dispersion Event Within Refrigerated Spaces
Deliverables: Scientific justification for current ammonia detection requirements plus the addition of a new informative Appendix A to IIAR-2.
Summary: Historically, ammonia detection has been required by IIAR-2 as well as the model codes, however, specific guidance on the appropriate number and placement of ammonia detectors for a given type and size of space was not given. Applying Computational Fluid Dynamics (CFD) analysis to answer a number of questions related to the appropriate number and placement of detectors in various types of refrigerated spaces was the object of the study. Principal Researcher, William Greulich, of Kensington Consulting conducted the research and delivered the results of the work in 2020 with a well received technical paper and presentation at the IIAR annual conference.
The results of the study were used by the Standards Committee to determine if there was merit in requiring additional detectors beyond the minimum requirement of one in every room with ammonia equipment. The study showed that having additional detectors would indeed reduce detection time, however, the reduction was small enough that it was determined that the addition of more than one detector in each room would not be justified. For example, an additional detector on average would reduce detection time by only a few minutes in a large room. Adding more detectors would only reduce response time by a few seconds. It was concluded that the actual leak response (action taken by either plant personnel or in some cases automatic system reaction) would not be significantly improved by the addition of detectors. In summary, the Safety Committee used the study to reinforce the requirements that are already included in IIAR-2 and made no new requirements for additional detectors.
The study also showed that detector placement is not extremely critical, but that placement can influence response time. The study is referenced in the latest IIAR-2 informative Appendix A to aid people with complying with the requirement that detectors be “mounted in a position where ammonia from a leak is expected to accumulate”.
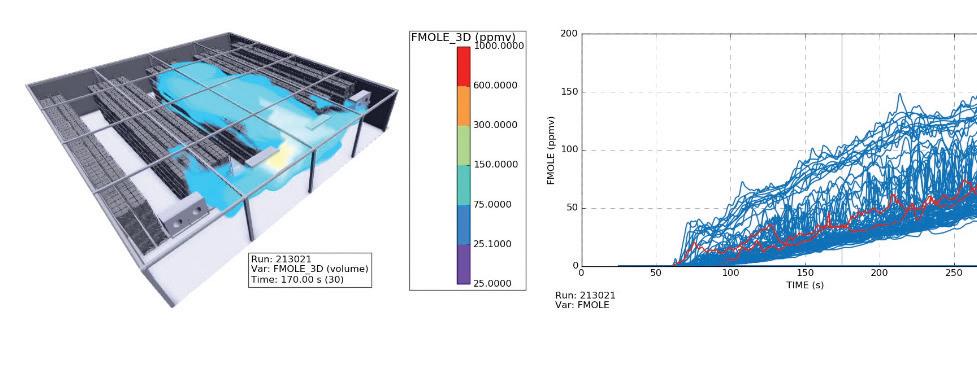
Development of a Mechanical Insulation Installation Guideline for Refrigeration Applications
Deliverables: A new currently available IIAR Guideline. The information from the project will also be included in future revisions to the Piping Handbook.
Summary: Mechanical (pipe, tank, and equipment) insulation is a critical contributor to energy efficiency and process control in cold applications. Water and water vapor intrusion into these insulation systems is their main failure mechanism. The resistance of the insulation system to water is controlled by the materials used and the quality of the installation. Water resistance of the insulation and vapor retarder materials is well understood but the impact of joints and terminations in these materials and the role installation plays in the water resistance of the insulation system has not been well studied.
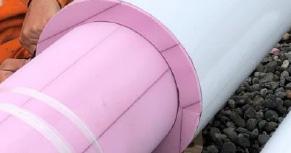
The Principal Investigator (PI), Gordon Hart, of Artek Engineering visited 20 refrigerated facilities in 14 states to examine insulation removal and new insulation installation at older facilities, as well as insulation installation at newly constructed facilities. The project has resulted in a number of recommended installation processes and joint treatments for insulation systems which, if followed, will increase the resistance of insulation systems to water vapor intrusion thus improving their lifespan.
Optimum Pipe Sizing
Deliverables: Updated optimum pipe sizing calculation method and software tool now included in the Piping Handbook.
Summary: The concept of economic or optimum pipe sizing considers the trade-off between the increasing capital costs associated with proportionally larger pipe sizes against the lower energy costs attributable to decreased frictional pressure drop afforded by the larger piping. In 1984, Bill Richards brought the concept of “economic pipe sizing” to the industrial refrigeration community. The IIAR Piping Handbook previously included the results from Richards work as one method for pipe sizing in ammonia refrigeration system applications.
Given the many changes that have taken place in the industry, including changes to electricity costs, pipe and valve installation methods, and the increased use of stainless steel pipe, to name a few, the need to revisit the economic sizing methodology proposed by Richards and to update the Piping Handbook was identified. A primary aim of this project was to provide a computer-based analysis tool that allows users to explore optimum pipe sizing based on input data that includes: piping system capital cost information, system energy cost data, piping system life expectancy, and refrigeration system operating efficiency information.
Principal Investigator, Rob Sterling, of Sterling Andrews Engineering successfully completed the project which was presented as a technical paper at the 2017 annual conference and the work included in the recent revision to the Piping Handbook. The spreadsheet software tool is included with the purchase of the Piping Handbook.
Prediction of Pressure Drop in Ammonia Wet Suction Risers
Deliverables: An improved vertical wet suction riser design method now included in the latest edition of the Piping Handbook
Summary: As a contributor to the ASHRAE research project RP-1327, which measured pressure drop in 2” and 4” ammonia wet suction risers, IIAR/ARF was given access to the data taken during the project. The RP-1327 data, originally taken at the Danish Technologic Institute (DTI) in Aarhus, Denmark, was used in a ARF-funded research project to develop an accurate method for predicting pressure drop and properly designing ammonia suction risers.
Dr. John Thome, of JJ Cooling Innovation in Switzerland, was selected as the Principal Investigator for the project and successfully delivered a calculation method to determine void fraction and pressure drop in ammonia two-phase upward flow based on the DTI data. The results of this work were presented by Dr. Thome at the 2019 annual conference. The new calculation method was then incorporated into a software design tool written by Morten Stovrup of Danfoss, a member of the Project Monitoring Subcommittee (PMS). The information from the study is also included as a new manual calculation method in the latest edition of the Piping Handbook.
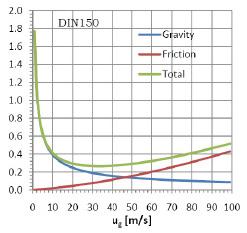
ARF is currently funding three research projects with highvalue deliverables which are described below.
Machinery Room Ventilation and Ammonia Release CFD Study
Principal Investigator: Dr. Scott Davis, Gexcon US
Summary: The study aims to evaluate ventilation system designs and requirements for ensuring adequate fire and explosion protection during accidental ammonia releases in machinery rooms using CFD analysis. The potential benefits include reduced capital cost, improved safety, and greater consistency in design practice. The study is being performed by Gexcon US, with Dr. Scott Davis as the Principal Investigator. Work began in March 2020 and is expected to complete by June 2021.
Multiple ventilation arrangements are considered for two example machinery rooms containing realistic equipment and geometries, with multiple release conditions, locations, and quantities, along with multiple ventilation rates and consideration of transient conditions to represent low-charge ammonia systems. A preliminary set of runs and results analysis has been completed and reviewed in a workshop with the Project Monitoring Subcommittee, leading to decisions on the remaining volume of CFD simulations.
Development of Design Guidelines for Avoidance of Hydraulic Shock in Ammonia Hot Gas Piping Using CFD Modelling
Principal Investigator: Dr. Chidambaram Narayanan, AFRY Switzerland AG
Summary: Incidents of ammonia releases due to hydraulic shock in the refrigeration pipework have been reported in the past and could potentially occur in the future. Such shock events carry significant commercial risks and is a concern for health and safety of humans. Two locations where hydraulic shock occurs most frequently are, (a) in the evaporator coil headers at the beginning of a hot gas defrost sequence, and (b) in the wet suction piping from the evaporator at the end of the hot gas defrost sequence. Research on characterizing hydraulic shocks in ammonia systems was carried out through two impactful projects funded by ASHRAE. The first one being RP-970 where detailed experiments resulting in a database of hydraulic shock amplitudes for various operating conditions such as gas flow rate, residual liquid amount, and operating temperatures were carried out. This was followed up by RP-1569 wherein a verified and validated CFD model was developed using the experimental data as a basis. Application of this CFD model to a real incident predicted shock amplitude upwards of 8000 psia; such amplitudes were deemed necessary from metallurgical analysis for the kind of rupture of the pipework observed C. Narayanan, AFRY Switzerland URP – Design basis for hydraulic shock avoidance in ammonia systems in this incident.
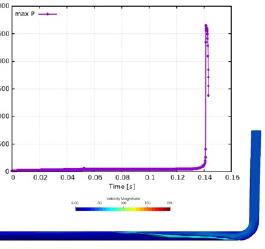
Based on the success of this CFD model, a study is being conducted with the objective of performing a large set of simulations of generic hot gas and wet suction pipework condition in order to establish a design basis for such systems and contribute significantly to the safety of ammonia systems. The comprehensive parametric study is estimated to involve 100+ three-dimensional unsteady simulations using High Performance Computing (HPC) systems. The simulation results will be analyzed to answer questions on what type of valves (fast acting or slow motorized) should be employed for hot gas defrost process, sizing of valves, dependence on suction temperature, risk due to trapped liquid, among other important drivers of hydraulic shock risk. The project is scheduled to be completed by June 2021. It is expected that this new design data will be incorporated into the Piping Handbook and other IIAR publications. A technical paper on a related CFD study has been co-authored by Dr. Narayanan and Bent Wiencke, and submitted for presentation at the 2021 annual meeting.
A Step by Step Guide to Estimate Ammonia Releases and Reporting
Principal Investigator: Bent Wiencke, Consultant
Summary: The project deliverable will be an IIAR step-by-step guidance document and accompanying spreadsheet calculator that will aid end-users dealing with ammonia releases. This type of guidance document does not presently exist and is expected to be of significant value to IIAR end-user members. Expected delivery date is June 2021.
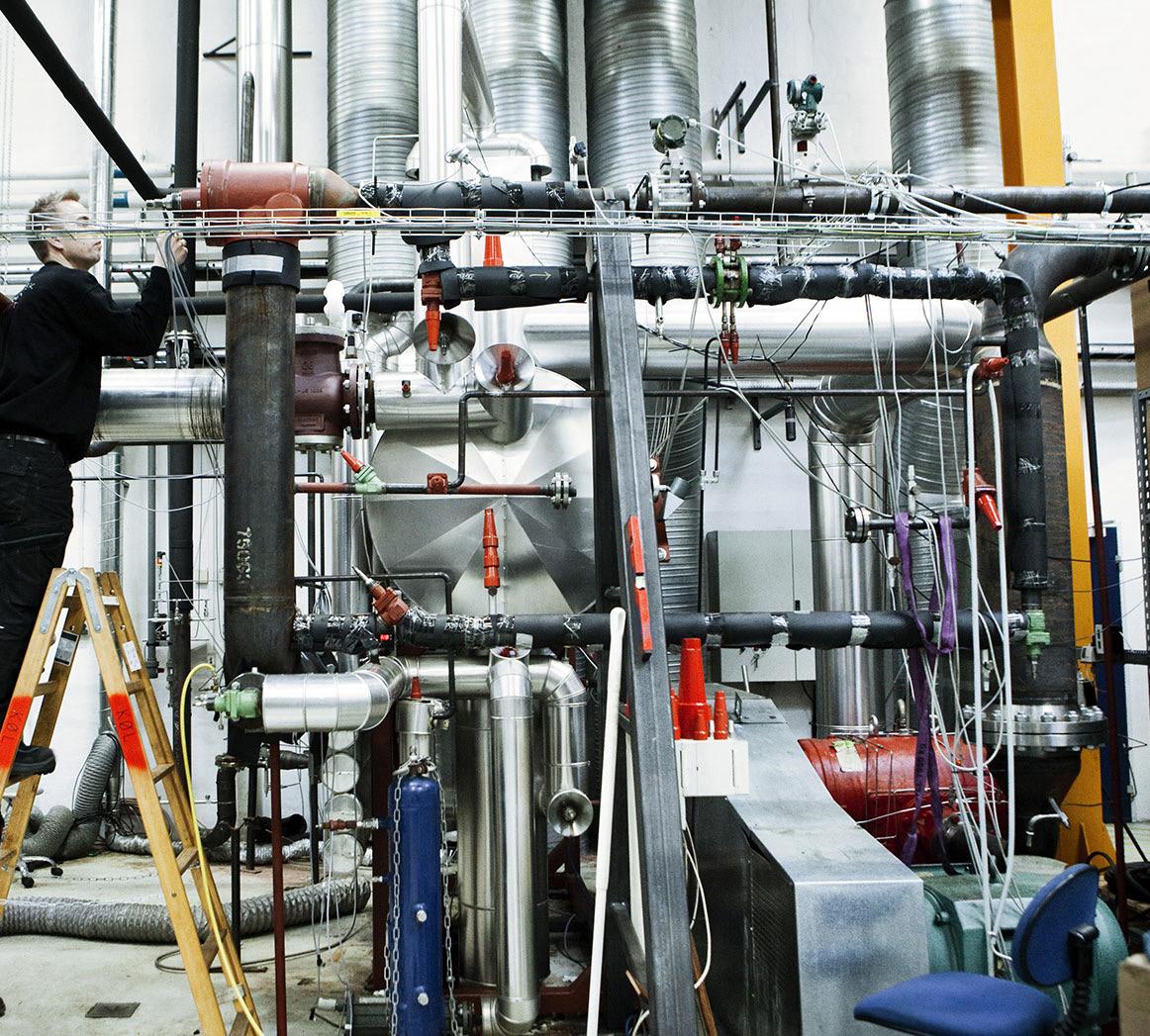
RESEARCH PROGRAMS MOVING FORWARD

The contributions that will be realized through the completion of the three current programs demonstrates the important impact scientific research can have on the refrigeration industry and the important benefits proved to our membership and all sectors of our industry. A challenge is presented to the IIAR membership and its Research Committee to identify the next generation of programs for the Foundation to consider for funding.
The IIAR Research Committee is currently reviewing a number of excellent research proposals submitted by the IIAR Membership. Each research program will go through the vetting process to ensure all value and benefit objectives are achieved. A detailed research work scope is drafted for those programs receiving the highest priority and presented to the ARF Board of Directors for funding consideration.
One research project that has completed vetting is related to relief valve piping network design. This project is to coordinate with the Industrial Refrigeration Consortium to study and further develop its computer based tool and user’s manual that aids designers in determining back pressure, pipe diameters and lengths used when relief valve outlets are combined into headers. The goal is to include published relief valve data in a lookup library and to allow input of non-standard data. The program is to be applicable for ammonia, CO2 and Propane.
Other projects currently being considered are those for determining pressure drop of CO2 for two phase flow in various riser sizes, development of guidelines to design for rooftop piping wind loads, and a project to determine burst pressure in multiple piping/tubing sizes and material thicknesses for use in CO2 piping networks. The Research Committee objective is to have at least three new projects approved and funded by your Foundation’s Board of Directors for work to begin in 2022.
ABOUT THE AMMONIA REFRIGERATION FOUNDATION The Foundation is a 501c(3) non-profit, education, research and training association dedicated to the natural refrigeration industry. Founded in 2006 by the membership of the International Institute of Ammonia Refrigeration (IIAR), its mission is to support research for the safe, reliable, and efficient use of ammonia and other natural refrigerants and to promote the development of industry talent through scholarships, academic alliances and outreach. ARF is based in Alexandria, VA. For more information, please visit www.iiar.org/foundation, call (703) 312-4200, or email foundation@iiar.org
ABOUT THE INTERNATIONAL INSTITUTE OF AMMONIA REFRIGERATION The International Institute of Ammonia Refrigeration is a global organization that acts as the leading advocate for the safe, reliable, and efficient use of ammonia and other natural refrigerants. IIAR is an ANSI approved standard writing body and produces standards, publications, and training material to promote safety for the natural refrigeration industry. IIAR’s mission is to provide advocacy, education, and standards for the benefit of the global community in the safe and sustainable design, installation and operation of ammonia and other natural refrigerant systems. IIAR is based in Alexandria, Va. For more information, please visit www.iiar.org, call (703) 312-4200, or email info@iiar.org