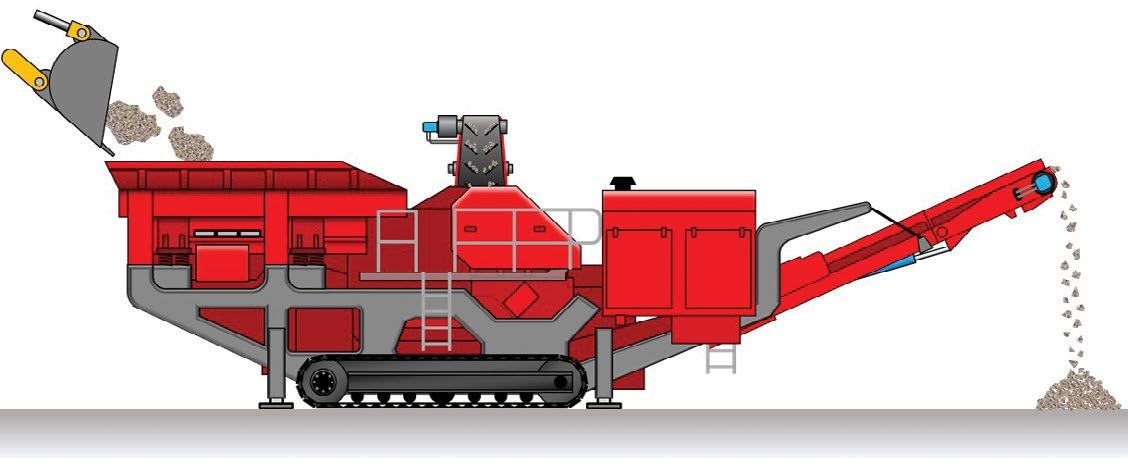
5 minute read
CRUSHING & SCREENING Productivity in Hydraulic Control & Monitoring
Forthousands of years, quarrying has supplied building materials, often carried out under arduous conditions far from home by simple, hard-working folk who measured daily output in baskets of rocks. Over the years, what was accomplished with a pickaxe and a shovel evolved into highly automated, mobile production lines that are thousands of times more productive than manual labor. Today, modern workers require rugged solutions that are simple to use and maintain, and in which problems are easily resolved by operators with minimum delay.
Crushing and screening in modern quarries involves crushing large pieces of material into smaller ones and sorting into similar-sized fragments. The starting material is typically freshly quarried or excavated rock or demolition material. Crushing machinery uses different crushing mechanisms, depending on the material. Where a considerable size reduction is required, the output of one crusher can feed a second one, and in some cases, a third may be necessary. Traditionally, material crushing has occurred in permanent locations where heavy-duty tipping trucks transport material to the plant. Recently, mobile crushing plant has proved practical and cost effective. Such equipment moves with wheels or caterpillar tracks to a convenient position. The same principles used in crushing and screening are now also applied to shredding, washing, and recycling machines that shred and sort waste for recycling.
Two- and three-port valves
The Webtec VFC Series of pressure compensated flow control valves ensure that actuator speeds remain virtually constant over all load conditions. When controlling the speed of a hydraulic motor powering a conveyor, for example, the motor rotates at the same speed, regardless of the amount of material on the conveyor belt. This ensures a consistent delivery position of the material. Once set, the weatherproof adjusting knob can be locked in position to avoid any inadvertent adjustment.
If a two-port flow control valve is used with a fixed displacement pump, then the excess pump flow has to pass across the system relief valve at full pressure. The excess pump flow is the flow the pump creates above the flow control valve’s setting. If the hydraulic motor (or other controlled actuator) is operating lightly loaded, then a large pressure difference across the flow control valve occurs. Flow passing across the relief valve and the large pressure drop across the flow control valve create inefficiency that results in heat.
When used with a pressure-limiting variable displacement pump, the pump flow rate automatically reduces to the rate determined by the flow control valve’s setting. But if the motor is lightly loaded, the pump outlet pressure remains at its maximum, i.e., the set pressure of the pump compensator. Since power in a hydraulic system is a product of flow multiplied by pressure, the output of a variable displacement pump only partially matches the power requirements of the actuator. Varying the pump displacement matches the flow requirement, but the pressure at the pump outlet can still be higher than what’s required by the actuator’s load. A lightly loaded actuator is still likely to cause a large pressure drop across the flow control valve, causing inefficiency and consequent heat generation. Two-port flow control valves are therefore best suited to variable pump systems in which the actuator only operates lightly loaded for short periods of its duty cycle. They can, of course, be used outside of these parameters by making provision for adequate fluid cooling.
A mobile crushing plant uses either an electromechanical or a hydraulic drive for the main crushing mechanism. Auxiliary functions are most often carried out by hydraulic cylinders and motors (actuators), which are ideally suited to operation in harsh working environments. Auxiliary functions on mobile crushers include track and conveyor drives, conveyor folding and positioning, and screen and deflector plate operation.
For over 40 years, Webtec has supported crushing-and-screening OEMs with rugged and reliable hydraulic valves that control the speed of actuators with varying loads, such as conveyor drive motors. The nature of the job means that motors can see rapidly varying loads, but ensuring that all machines work together requires continuous steady throughput. Machine designers, therefore, use pressure-compensated flow controls, including those made by Webtec, such as its conventional flow control valves, including three-port priority flow dividers and mono-block directional, flow, and pressure control valves.
A three-port flow control valve, also known as a priority flow divider, provides a pressure-compensated flow output from its priority port in a similar way to the two-port valve. So as before, this can be used to maintain a virtually constant speed of an actuator regardless of its load. Any excess flow directs to the valve’s bypass port. When used with a fixed displacement pump, therefore, the excess pump flow can be directed back to tank via the bypass port, rather than across the system relief valve. This means that the pump outlet pressure will only be slightly higher than the load pressure (typically 1-1.5 MPa [145-217 psi]) rather than the full relief valve pressure, thus reducing heat generation when the actuator is lightly loaded. So depending on the application, a simple, fixed displacement pump combined with a three-port flow control valve may be as efficient as a more complex and costly variable displacement pump and a two-port valve. U.S. research suggests that the average power transmission efficiency of current mobile hydraulic systems is around 21%. Both fuel prices and global emission targets demand improvement in that figure. An emphasis on control valve efficiencies is becoming increasingly important.
Rather than directing the bypass outlet flow to tank, it can also be used to power another function on the machine. In this case the priority port flow remains virtually constant, and the available bypass flow is the difference between the inlet and priority flows. In some applications this may negate the need for a dual pump to power both functions.
If remote speed adjustment is required, a proportional version of the priority flow divider enables an electronic signal to be used to vary the priority flow. All the necessary electronics are incorporated within the valve so it only requires an input signal that can be provided by a simple toggle or rocker switch to increase or decrease the priority flow setting. The hydraulic function of the valve is the same as for the manually adjusted version.
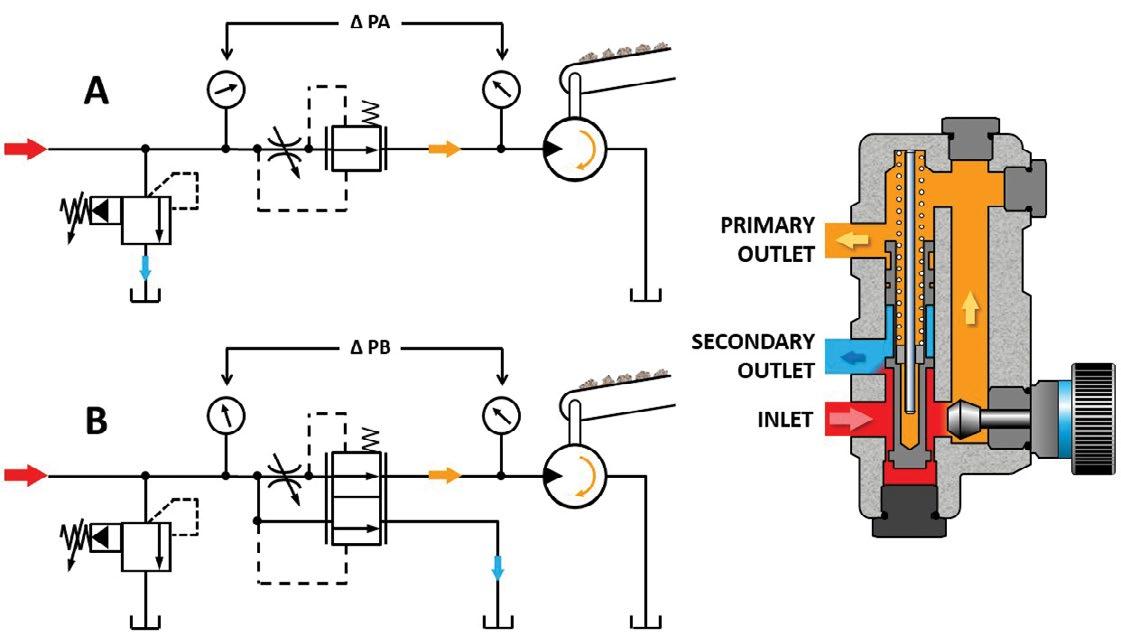
Monoblock valves
A priority flow divider can also be combined with a manually operated directional valve to enable the priority flow to be switched between two machine functions such as conveyor drives. A two-stage relief valve is also included to limit the maximum pressure in the priority outlet port. So the Webtec CV120 combination valve combines a single directional, flow, and pressure control in one compact, simple-to-install unit, with the opportunity for multiple valves to be connected in series using a high-pressure carry-over port. When connecting valves in series, a second pressure relief valve is incorporated in order to limit the carry-over port pressure. Combining functions in this way reduces both the cost and size of the installation by reducing the number of hoses and fittings required. Despite its compact design the CV120 combination valve doesn’t compromise on functionality, using the same pressure compensated flow control technology as used in the VFD range.
When the movement of two actuators needs to be synchronized, for example with track drives or conveyor positioning mechanisms, the FDC Series flow divider/combiner can be used to ensure equal flows to or from each actuator, irrespective of load. In one direction the flow dividing function will split the single flow input into two outputs, either equally or in a pre-defined ratio. In the opposite direction the two flow inputs will be combined into one, either equally or in the same predefined ratio as before. For cylinder applications, a levelling-up function may also be required to ensure that both cylinders fully reach their end strokes.
Certain functions on mobile crushers need to be interlocked to prevent dangerous or damaging situations. For example, operation of the track drive may need to be prevented unless a conveyor is moved to a transport position. The Webtec SV/DV 80 diverter valve can be used in such situations to prevent flow to a certain function unless mechanically actuated by the appropriate section of the machine.
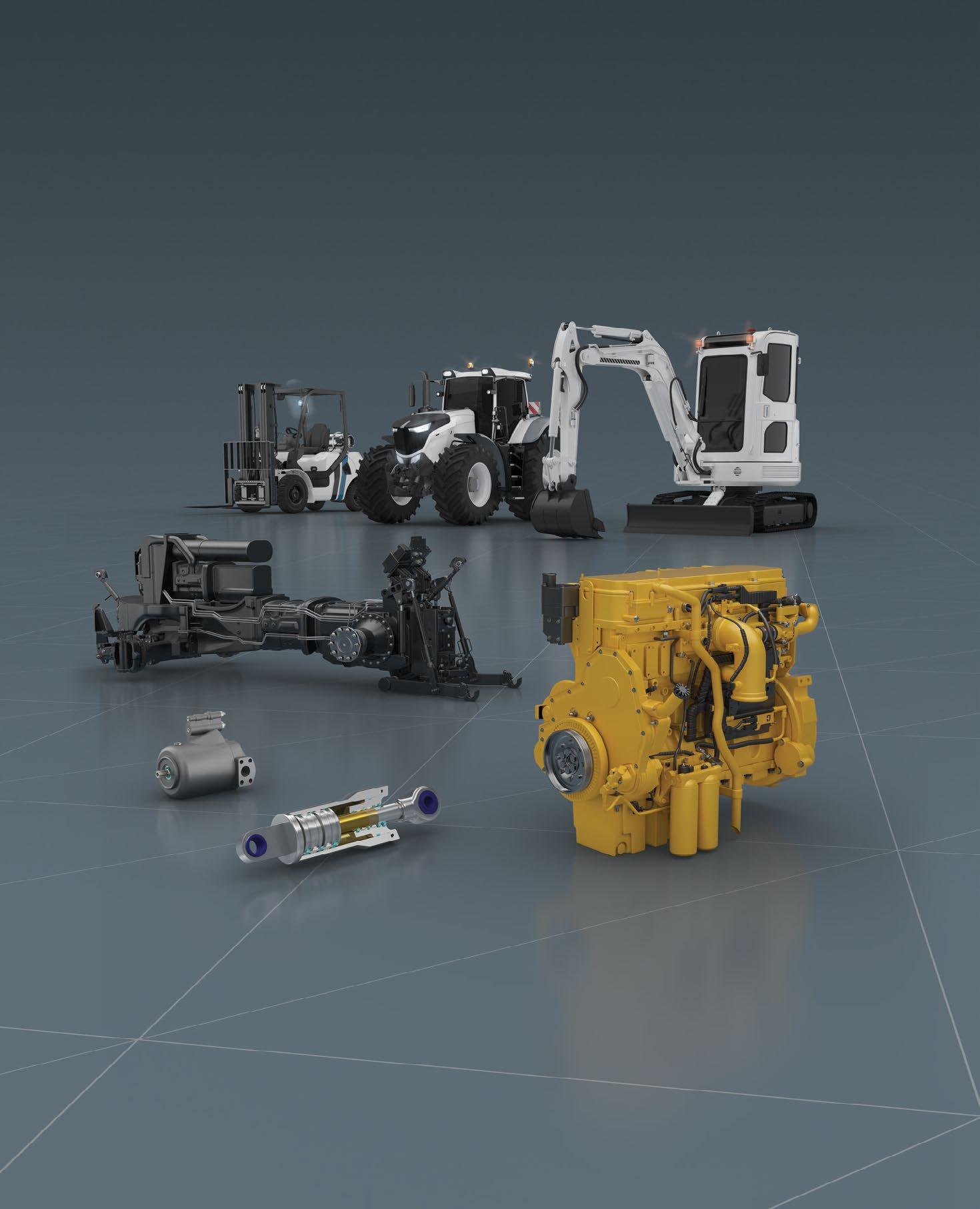