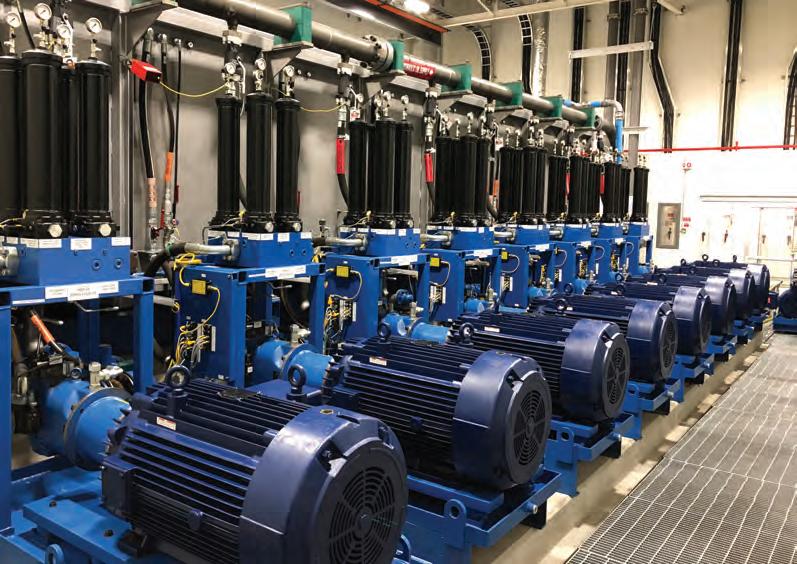
30 minute read
Case Study: Building an Industrial Hydraulic System
Case Study
Building an Industrial Hydraulic System
By Steve Misiakowski, Engineering Director, Exotic Automation & Supply
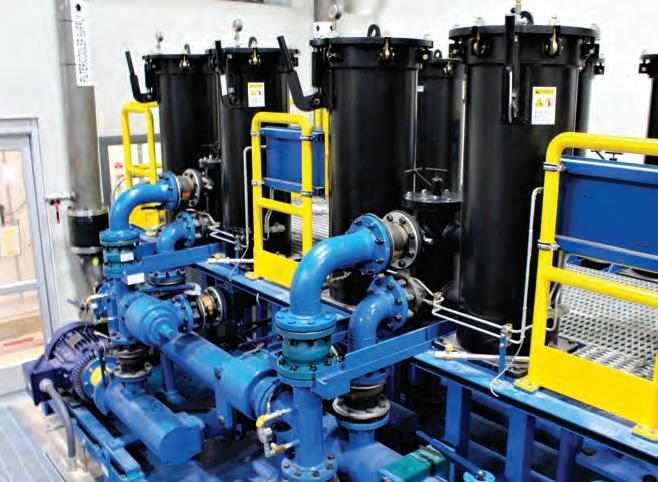
Recirculation skid for kidney loop filtration.
Designing a large central hydraulic system to support a new 138,000-square-foot industrial facility presents many unique challenges compared to the more common practice of designing hydraulic power units for OEM machine builder’s equipment. As this article shows, such a significant project for one of our customers presented similar key design challenges and considerations.
The customer’s new greenfield facility is a test lab responsible for structural advanced life-cycle testing. There are dozens of individual test locations throughout the building, each presenting unique hydraulic actuation requirements to facilitate the necessary tests. The customer’s goal was to partner with a turnkey supplier to design, construct, install, and commission a large central hydraulic system capable of providing stable hydraulic oil pressure at variable volumes.
The problem
The customer’s existing central hydraulic system had been designed and installed 35 years ago. That installation included fixed displacement gear pumps to provide flow and pressure throughout the facility. A great amount of energy was continuously wasted in the form of heat
Eight of the sixteen pump/motor groups.
generated by oil flow over relief valves at the pump units. Most of the test rigs throughout the facility included high-precision, high-speed servo valves that were sensitive to fluid contamination. Since the hydraulic system wasn’t airtight, the company couldn’t control the ingress of contaminants into the hydraulic fluid. The contaminated oil resulted in expensive, weekly repairs to maintain the servo valves. After 35 years, the customer knew what it wanted for its new building: an energy-efficient system that reduced component repairs and increased overall system uptime.
The requirements of this new central hydraulic system were very detailed and, in many instances, much more stringent than typically seen in general industrial hydraulic applications. The specs included: • Precise control of a large volume of fluid (over 18,000 gallons) • Flow variation up to 250 gpm in as little as 200 milliseconds • Stable system pressure (3,000 psi, + 0 psi/-100 psi) at variable volumes of 0-2,200 gpm • Engineered (nonwelded) piping • Maintain oil temperature between 112°F and 130°F during operation • Oil cleanliness of ISO 12/10/7 • Water content in the oil below 10 ppm • 24/7 year-round operation with a life expectancy 30-plus years
Other than known limited space constraints in the design for the pump room, concepting the hydraulic portion of the project began with a blank sheet of paper. We presented multiple concepts and detailed proposals that included 3D CAD models over the course of 12 months before the project was finally awarded. It took 4 1/2 years from initial inquiry to final customer acceptance.
The project involved many stakeholders. Countless design review meetings with the facility’s general contractor, design architects, structural engineers, representatives of other building trades, and the end user resulted in a system with the following major components: • Reservoir (11,000-gallon capacity) with closed loop air exchange • Pump/motor groups with duplex pressure filtration manifolds (360 cc pumps coupled to 16 300-hp motors) • Recirculation and cooling skid • Roof-top heat exchanger (6 million BTUs) • Vacuum dehydrator and particle counter • Return filter skid • 20 accumulator stands, including 104 15-gallon bladder accumulators
• About 10,000 feet of engineered piping • Controls architecture, including soft-starter panels, variable frequency drive panels, programmable logic controller panel, operator interface, I/O handling, sensors, and alarms
Design challenges
There were a number of unique characteristics and design challenges for each of the system’s major components.
Reservoir. The highly engineered reservoir had to be large enough to support the variability of worst-case operating and emergency-stop scenarios. The final dimensions of the reservoir were 7 feet high by 7 feet wide by 35 feet long.
The real challenge to designing this large 304-stainless steel reservoir was handling the velocity of return oil flow. We installed a custom 8-inch schedule 40 pipe with hundreds of 1-inch holes as a diffuser down the center of the tank. This effectively “calmed” the return fluid while minimizing aeration as it mixed with the tank’s volume. We incorporated numerous baffles to separate the return oil coming into the center of the tank from the pump inlet supply fluid outlets on either side.
This was truly a unique hydraulic reservoir that required a structural 3D CAD model, finite element load analysis of the reservoir lid segment, accommodations for pressure testing, and multiple locations for level and temperature sensors. Once built, it required exterior sugar blasting followed by a clear-coat application.
Pump/motor groups. We were challenged to design a system that eliminated the user’s ability to perform manual tweaking of the components.
The pump solution for the new central hydraulic system included pressure-compensated pump technology with load sense control for 24/7 year-round operation. Partnering with Parker Hannifin, we delivered a custom pump control scheme. Parker’s experience with large system applications and its load-sharing expertise led to a solution that included 16 360-cc displacement Parker PVplus Series pumps with load sensing control and electrical unloading.
While piston pumps were more expensive than the gear pumps in the customer’s existing hydraulic system, they provide longer life operating at higher pressure and longer continuous duty cycles. The load sensing system generates fewer power losses because the pump reduces both flow and pressure to match the load requirements of the system.
Each of the 16 pumps was coupled to a 300-hp inverter-duty-rated motor. These pump/motor groups were each incorporated into free-standing drip trays that supported a custom pressure filter manifold that held two duplex filter assembles rated to 5,000 psi with 3µ filter elements. We placed eight pump/motor groups on each side of the large main reservoir.
Recirculation and cooling skid. Another significant challenge was meeting the stringent oil cleanliness requirement of 12/10/7 per ISO 4406:99. An oil recirculation skid, or kidney loop filtration system, was needed. This recirculation skid provided a continuous flow of oil filtered at 2µ separate from the main supply pressure filters, and directed the filtered oil up to the 6 million BTU heat exchanger (cooler) located on the roof of the new building.
Roof-top heat exchanger. The large heat exchanger on the roof was exposed to weather conditions typical of the Midwestern U.S. – from subzero winter temperatures to 125°F in summer. With oil returning to the reservoir at 140°F, the challenge was to maintain the oil temperature between
(Continued on page 12)
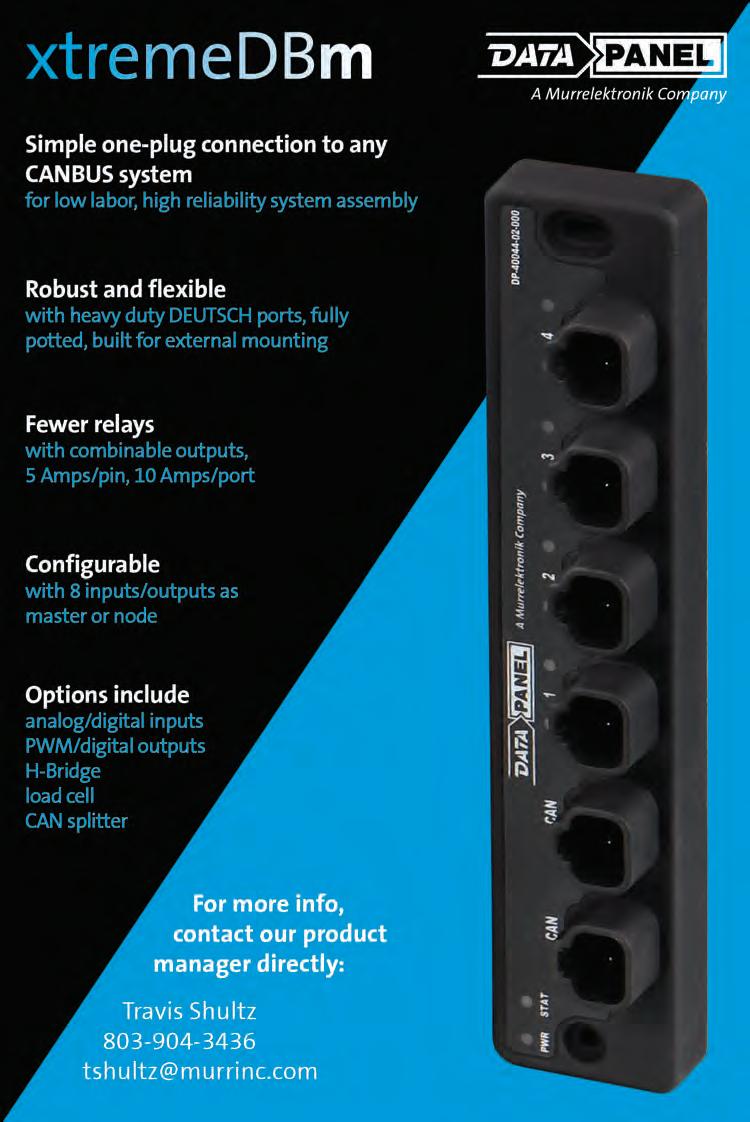
The engineered piping trench.
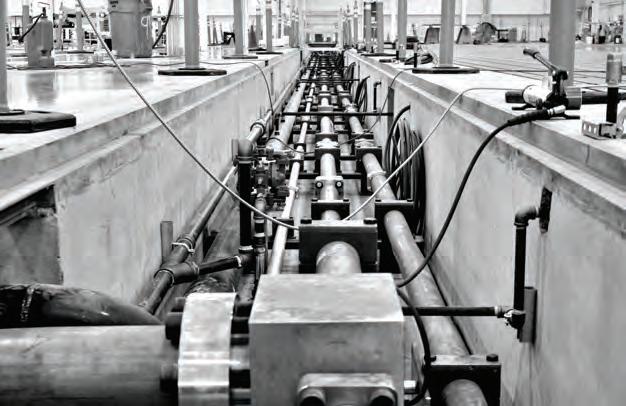
(Continued from page 11)
112°F and 130°F during operation, regardless of weather conditions outside.
The solution was to have the recirculation skid’s pumps individually cycle on or off as needed to keep the hydraulic system’s temperature regulated. We accomplished this by having each of the four screw pumps on the recirculation skid controlled with a variable frequency drive. The VFDs provided precise speed control (flow control) and energy efficiency. Since the fluid temperature was being monitored in numerous places throughout the hydraulic system, we could program the amount of fluid cooled by the rooftop cooler and the running of the cooling fans to effectively keep the oil temperature in the proper range during operation.
Vacuum dehydrator and particle counter.
Water is one of the most common and detrimental contaminants of industrial oils and related equipment. Water vapor enters the oil and condenses when temperatures drop. It depletes rust inhibitors and can cause direct corrosion of steel components in the hydraulic system.
We overcame this challenge by incorporating a properly sized vacuum dehydration unit. Vacuum dehydration is the only comprehensive method to effectively remove water vapor and other dissolved gases from the oil. Through low-temperature distillation in combination with fine filtration, oils can be kept in “like new” condition.
The vacuum dehydrator designed into our system was a stand-alone unit mounted on a structural steel base with an integral drip pan. It is capable of processing more than 1,200 gallons per hour at 1,800 rpm and contains an inline particle counter to monitor the oil cleanliness level. Its PLC communicates via industrial Ethernet to the hydraulic system’s main PLC, sharing critical fluid data. Return filter skid. Due to the central hydraulic system’s significant potential flow volume of up to 2,200 gpm, we combined two sets of large duplex filtration vessels on a single steel-base return filtration skid. Each of the four total vessels is populated with seven triple-length 20µ-filter elements.
Accumulator stands.
With the possibility of sudden flow changes due to test stands starting and stopping, we had to account for the resulting “shocks” to the hydraulic system. The solution was to incorporate strategically located banks of accumulators that are used to absorb and store energy. We located 20 accumulator stands throughout the new facility to provide an evenly distributed amount of shock absorption capacity.
Engineered piping. Another challenge to overcome was avoiding the energy lost by improper plumbing. Selecting the proper line size for a hydraulic system is critical to obtaining maximum performance and life from hydraulic components. Undersizing fluid lines results in high pressure loss and heat; oversizing lines increases the cost of the system. In typical applications, lines should be sized as follows: • Suction: 2-4 feet/sec. • Return: 10-15 feet/sec. • Medium pressure: 15-20 feet/sec. • High pressure: 20-25 feet/sec.
We reduced these velocities to prevent excess energy loss.
The almost two miles of piping, located in floor trenches throughout the new facility, used 95% weld-free connection technology, eliminating the risk of corrosion due to stress cracks during welding and increasing the lifespan for the piping system. We used facility CAD data in conjunction with the CNC cold bending machines to manufacture the precise tube segments. Orientable flanges gave the pipe fitters greater flexibility during assembly. This reduced installation time and will simplify maintenance, reduce operating costs, and improve safety.
Providing proper line sizes means improved performance of the hydraulic test equipment throughout the facility. It makes flow more laminar, reduces the effect of shock, decreases potential leak points, increases fitting and connector life, and reduces heat generation.
Controls architecture. For this central hydraulic system, the controls design and integration were part of the turnkey installation. Operating the hydraulic system 24/7 year-round required redundant PLCs. We designed controls that would monitor, record, and respond to system performance and health. The items monitored and displayed on the system’s main operator interface included: • 120 multiple emergency control stops • System flows and pressure • Reservoir fluid levels • Oil temperature • Multiple vibration sensors • Multiple bearing temperature sensors • Multiple differential pressure sensors (mainly across filters) • Multiple sump alarms • Valve position indicators • Security inputs, such as fire alarm, smoke detector, and sprinkler water flow • Fluid ISO particle count level, as well as water and air content • Status of all the system’s pumps, fans, and motors
The customer also required remote-access to the control system via their intranet to monitor, interrogate, or silence alarms. Having all user-editable parameters along with realtime system performance data located on the password-protected human-machine interface greatly enhanced the customer’s efficiency in maintaining the system and maximizing uptime.
The project achieved the customer’s system requirements for flow response, pressure compensation, and energy consumption. The customer received a turnkey custom hydraulic solution tailored to their unique application. Parker was the source of many system components, including filters, valves, accumulators, KleenVents, proportional valves with controllers, hoses, and fluid connectors.
The results
We addressed all the customer’s issues related to the old hydraulic system: • We improved the system’s energy efficiency with the variable displacement pumps. • We achieved oil cleanliness of ISO 12/10/7, maintainable by a multistage filtration strategy. • The cleaner oil significantly reduced repairs. • The modularity of the system’s design and redundant controls led to documented reductions in system downtime.
Using sound fluid power design principals, the new central hydraulic system achieved measurable benefits with a much smaller footprint than the customer’s previous system. •
Shipments Grew 20% Last Year
Data from the National Fluid Power Association shows that shipments of pneumatic, hydraulic, and total fluid power products continue to grow. From 2020 to 2021, total fluid power shipments grew 20.1%. Raw index data shows that mobile hydraulic and pneumatic shipments were down slightly in December, while industrial hydraulic shipments were up. These charts were drawn from NFPA’s Confidential Shipment Statistics (CSS) program.
Hydraulic and Pneumatic Shipments
Raw Index Data, Index: 2018=100
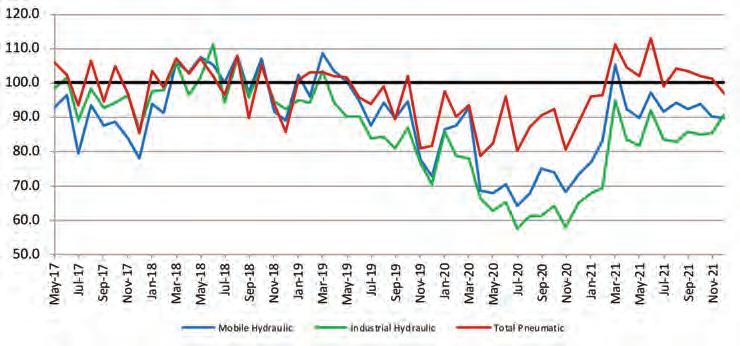
This graph of raw index data is generated by the total dollar volume reported to NFPA by CSS participants and compared to the average monthly dollar volume in 2018. For example, the December 2021 total dollar volume for pneumatic shipments is 96.7% of the average monthly dollar volume in 2018. (Base Year 2018 = 100)
SHIPMENTS
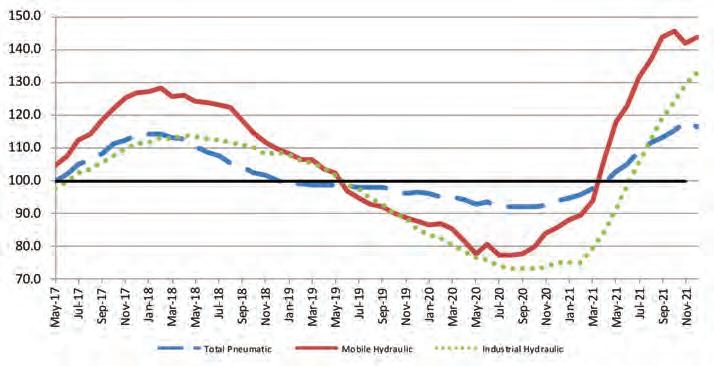
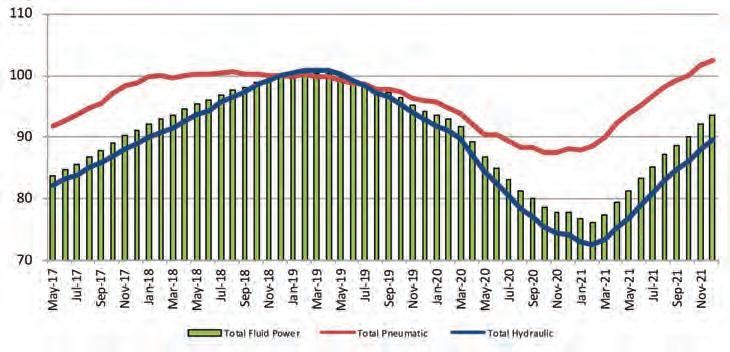
MONTH TOTAL FLUID POWER TOTAL HYD. TOTAL PNEU.
Oct. 2021 18.6 19.3 16.1
Nov. 2021 20.0 20.3 16.9
Dec. 2021* 20.1 20.9 16.3
*Preliminary data subject to revision.
Shipments – Cumulative year‐to‐date % change (2021 vs. 2020)
The table above is expressed in terms of cumulative percent changes. These changes refer to the percent difference between the relevant cumulative total for 2021 and the total for the same months in 2020. For example, December 2021 pneumatic shipments figure of 16.3 means that for the calendar year through December 2021, pneumatic shipments increased 16.3% compared to the same time-period in 2020.
Pneumatic, Mobile and Industrial Hydraulic Orders 12/12 Ratio
Each point on this graph represents the most recent 12 months of orders compared to the previous 12 months of orders. Each point can be read as a percentage. For example, 133.2 (the December 2021 level of the industrial hydraulic series) indicates that industrial hydraulic orders received from January 2021 to December 2021 were 133.2% of the orders received from January 2020 to December 2020. (Base Year 2018 = 100)
Total ‐ Hydraulic and Pneumatic Shipments 12 Month Moving Average
This graph of 12-month moving averages shows that in December 2021, the moving average for shipments increased across the board. (Base Year 2018 = 100)
Executive Profile
CELEBRATING 60 YEARS

Garrett Hoisington, CFPAI/AJPP, CFPS, CFPMHM – Vice President, Open Loop Energy
Q. How did you get started in the fluid power industry?
A. My family owns a business that services heavy equipment in the mining industry. While working for the business, I worked with a few certified fluid power specialists who inspired me to study for the test and become certified myself.
Q. How and why did you get involved in IFPS, and what have you gained professionally and personally?
A. I got involved with IFPS after a colleague, Rocky Phoenix, volunteered and was elected to the board. He felt I could contribute to the society and would enjoy working with other industry professionals.
Q. Why did you pursue certification, and how has it helped your career?
A. I was inspired by others I worked with in our family business. I really looked up to their knowledge and expertise in hydraulics.
Q. What have you learned by working in this industry?
A. I have learned how little I know. There are some amazing people involved with the society and many who have contributed to the industry through innovation, education, and service.
Q. Where do you see the industry heading in the next 10 years?
A. I see a continued trend of using hydraulics as the muscle with electronics as the brains and logic. Hydraulics and pneumatics will continue to fill the niche motion control needs they always have but with improved control and feedback interfaces.
Q. What advice would you give someone starting out in the industry?
A. Stick with the industry. There are many opportunities outside the mainstream careers. This means more job stability and the possibility of higher paying jobs.
Q. What are some of your hobbies and interests?
A. I love aviation, and I’m fortunate enough to fly for work and pleasure. I’ve played golf since I was 10 and still enjoy the game when I find time.
Q. What is something people would be surprised to learn about you?
A. I’m kind of a 1980s computer nerd. I grew up learning computers with DOS and simple computer games and have kept up with it as I’ve grown older. I’ll still play computer games with my kids. I also enjoy programming for PLCs in the motion control world.
Certify Your Workforce in 2022
»IFPS CERTIFICATION EMPOWERS fluid power distributors, manufacturers, and end users with: • Increased credibility • A fully trained and certified workforce • Standards for assessing the skill level of current or potential employees • A safer and more efficient workforce • Competency standards for advances in the industry • Effective sales and recruiting tools
MARKETING OPPORTUNITIES with a fluid power certified workforce include: • An IFPS certification-supporter logo for your website • Adding IFPS credentials to an employee’s name in signature lines, business cards,
LinkedIn profiles, etc. • Certificates to display in your office or shop • Your employee’s name and company listed in Fluid Power Journal as a “Newly Certified
Professional”
ABOUT IFPS CERTIFICATION programs: • IFPS has certified thousands of professionals since 1960. • Certifications are the industry standard for assessing an employee’s knowledge. • Certification tests provide an objective third-party assessment of an individual’s skill level. • Tests are psychometrically evaluated and meet defensible standards. • Certifications are portable and recognized industry wide. • Individuals recertify every five years to show their skills and knowledge keeping pace with the industry.

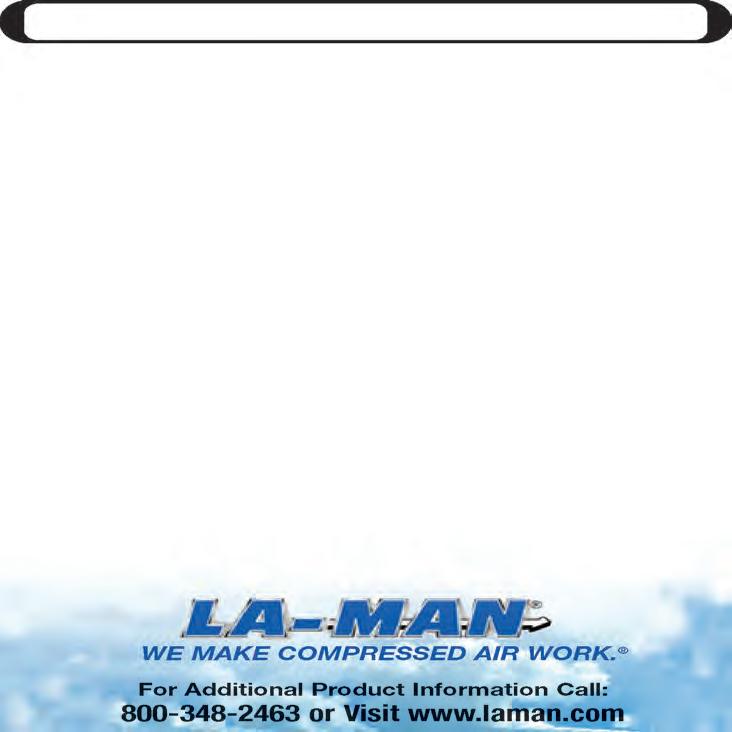
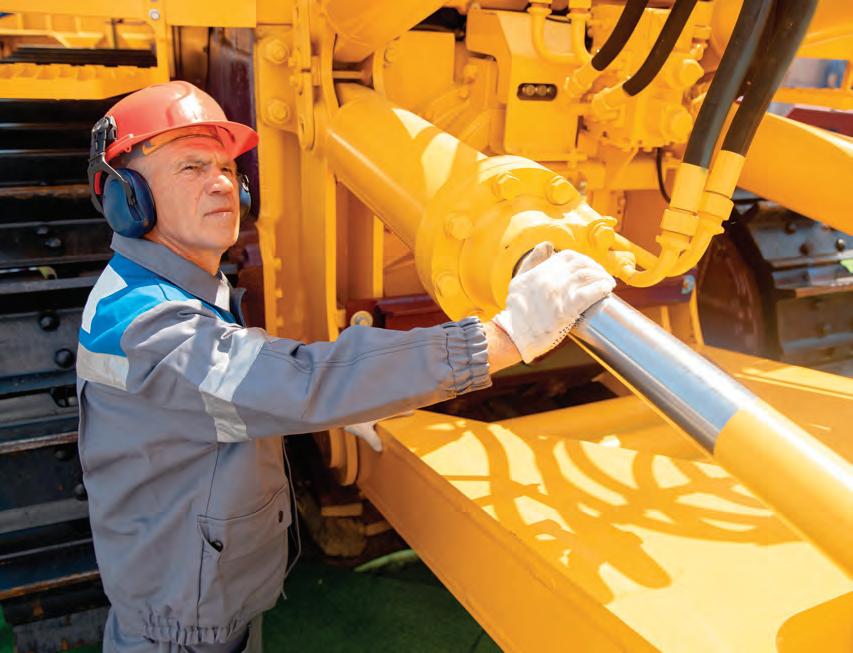
Air Compressors Clean Dry Air Improves Performance...
Clean, Dry Compressed Air Starts with The Extractor/Dryer® Manufactured by LA-MAn Corporation
• Point of Use Compressed Air Filter to
Improve and Extend Equipment Life • Removes Moisture and Contaminates to a 5-Micron Rating: Lower Micron
Ratings are Available • Models with Flow Ranges of 15 SCFM to 500 SCFM Rated Up To 250psi are
Easy Installation • Weep Drain is Standard; Float Drain or Electronic Drain Valves Optional
IFPS Launches Employer Resources Web Page
A newly designed page on the IFPS website, Employer Resources for Certification, helps employers decide which IFPS certification best matches an employee’s job responsibilities.
By selecting descriptions of an employee’s job duties, the page leads employers to concise information about the best path to certification. For example:
My employee • Designs or sells fluid power systems. • Troubleshoots or installs, fluid power systems. • Repairs or maintains fluid power systems. • Fixes leaks, installs and replaces pipe, tube, or hose.
IFPS certifications are renown as the industry standard for competence in fluid power and automation. A fully trained and certified workforce indicates an increased capability that sets your company apart from the crowd. The employee’s journey toward certification tests their drive, skill, and desire to advance toward a common corporate goal of excellence.
For more information, visit www.ifps.org/certifications.
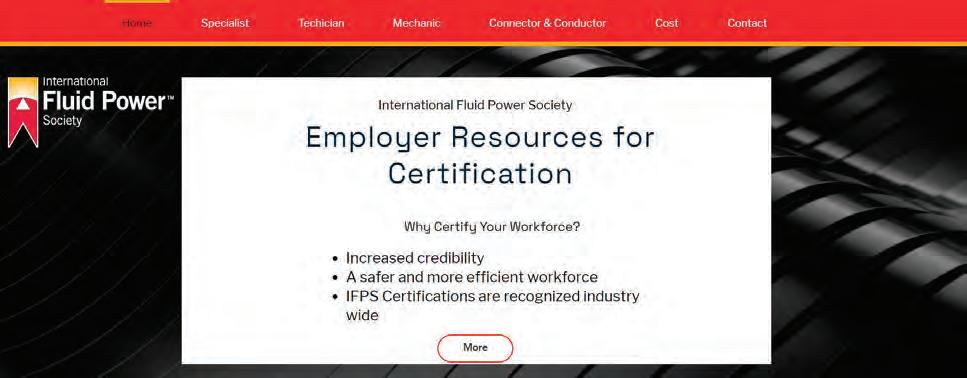
CELEBRATING 60 YEARS
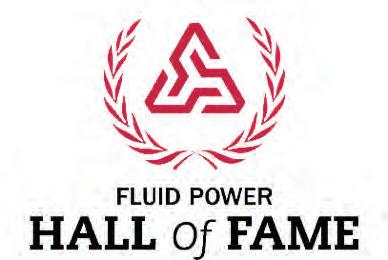
Hall of Fame Nominations Open
»NOMINATIONS FOR THE Fluid Power Hall of Fame are being accepted until April 15. A panel of judges reviews the applications and announces the inductees on Fluid Power Professionals Day, June 19. Inductees will be honored at an awards dinner during IFPS's fall meeting in October in San Diego.
Anyone can nominate a living or deceased professional who has 25 or more years’ experience in the fluid power industry. Living nominees will be contacted and asked to complete an application.
The Fluid Power Hall of Fame was established to acknowledge individuals who have made significant contributions to the fluid power industry. To make a nomination, visit www.fluidpowerhalloffame.org.
Newly Certified Professionals
December 2021
MASTER MECHANIC
holds IHM, MHM and PM certificaitons David Heldstab, The Boeing Company John Osko, The Boeing Company Christopher Scime, The Boeing Company Michael Sherman, The Boeing Company Paul Younglove, The Boeing Company
SPECIALIST
holds HS and PS certifications Jhoanna Hansen, Cargill Jesse Holmes, CERES Leate Rogers, GEFCO Christopher Johnson, Hennepin Technical College Kevin Milligan, Hennepin Technical College Kissinger Moua, Hennepin Technical College Touger Moua, Hennepin Technical College James Siglin, Hennepin Technical College Bridget Obermark, Hyspeco
HYDRAULIC SPECIALIST Ramin Askarifar
David Patrick, Airline Hydraulic Cameron Ruggiero, Alfred State College Brandon Dillenbeck, Alfred State College Nicholas Green, Alfred State College Joshua Jeziorowski, Alfred State College Lucas Ott, Alfred State College Dylan Perlino, Alfred State College Jake Young, Applied Engineered Systems (Engineered Sales) Jared Werner, Brand Hydraulics Christopher Heen, Continental Hydraulics Eric Jacobson, Danfoss Power Solutions Matthew Kruse, Danfoss Power Solutions Daniel Hernandez, Engineered Sales Jonathan Jefferson, Engineered Sales Logan Smith, Hennepin Technical College Alexander Broyles, HydraForce Cole Yungerman, HydraForce Gerold Curell, Hydraulic Controls Bridget Obermark, Hyspeco Mike Campbell, John Henry Foster Seth Koetje, MFP Automation Engineering Thomas Kok, Oxbo International Walker Gross, WAR Industrial Services
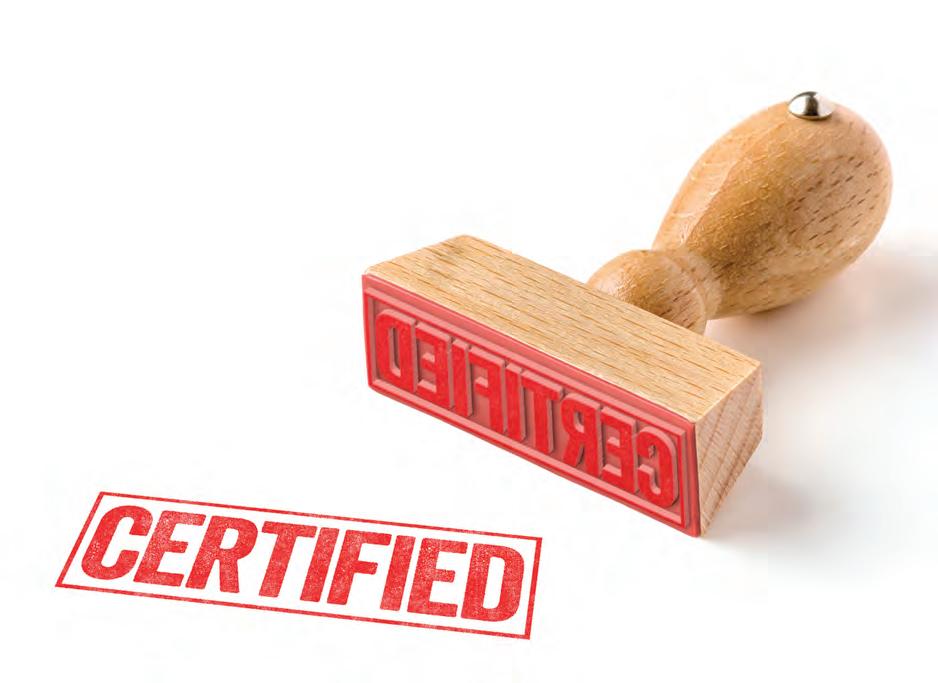
PNEUMATIC SPECIALIST
Jhoanna Hansen, Cargill Jesse Holmes, CERES Leate Rogers, GEFCO Christopher Johnson, Hennepin Technical College Kevin Milligan, Hennepin Technical College Kissinger Moua, Hennepin Technical College Touger Moua, Hennepin Technical College James Siglin, Hennepin Technical College Troy Hudson, IMI Precision David Hiscock, Norgren
CONNECTOR & CONDUCTOR
Patrick Brister, The Boeing Company Victor Diep, The Boeing Company Ivan Shih, The Boeing Company Brandon Welch, The Boeing Company
MOBILE HYDRAULIC MECHANIC
Kyle Cowell, Alliant Energy Shane Doerscher, Alliant Energy Nick Freeman, Alliant Energy Matthew Haag, Alliant Energy Andrew Martin, Alliant Energy Zach Mason, Alliant Energy Jared McRill, Alliant Energy Micah Stockberger, Alliant Energy Travis Birmingham, Altec Industries Jason Bush, Altec Industries Matthew Deters, Altec Industries Robert Gilpin, Altec Industries Gary Hatcher, Altec Industries Andrew Ramos, Altec Industries Kelsey Rutledge, Altec Industries Meagan Smith, Altec Industries Natividad Guerra, American Electric Power Co. Mark Bergerud, Ottertail Power Barry Schleske, Ottertail Power Isaac Fredrick, Terex Utilities Emily Hagge, Terex Utilities David Heldstab, The Boeing Company John Osko, The Boeing Company Christopher Scime, The Boeing Company Michael Sherman, The Boeing Company Sean Wynne, The Boeing Company Paul Younglove, The Boeing Company
PNEUMATIC MECHANIC
Miles Conn, Controlled Fluids Joshua Grisolia, The Boeing Company Grant Harvey, The Boeing Company Ryan Keller, The Boeing Company Dylan Longaker, The Boeing Company
CFPAI
Certified Fluid Power Accredited Instructor
CFPAJPP
Certified Fluid Power Authorized Job Performance Proctor
CFPAJPPCC
Certified Fluid Power Authorized Job Performance Proctor Connector & Conductor
CFPE
Certified Fluid Power Engineer
CFPS
Certified Fluid Power Specialist (Must Obtain CFPHS & CFPPS)
CFPHS
Certified Fluid Power Hydraulic Specialist
CFPPS
Certified Fluid Power Pneumatic Specialist
CFPECS
Certified Fluid Power Electronic Controls Specialist
CFPMT
Certified Fluid Power Master Technician (Must Obtain CFPIHT, CFPMHT, & CFPPT)
CFPIHT
Certified Fluid Power Industrial Hydraulic Technician
CFPMHT
Certified Fluid Power Mobile Hydraulic Technician
CFPPT
Certified Fluid Power Pneumatic Technician
CFPMM
Certified Fluid Power Master Mechanic (Must Obtain CFPIHM, CFPMHM, & CFPPM)
CFPIHM
Certified Fluid Power Industrial Hydraulic Mechanic
CFPMHM
Certified Fluid Power Mobile Hydraulic Mechanic
CFPPM
Certified Fluid Power Pneumatic Mechanic
CFPMIH
Certified Fluid Power Master of Industrial Hydraulics (Must Obtain CFPIHM, CFPIHT, & CFPCC)
CFPMMH
Certified Fluid Power Master of Mobile Hydraulics (Must Obtain CFPMHM, CFPMHT, & CFPCC)
CFPMIP
Certified Fluid Power Master of Industrial Pneumatics (Must Obtain CFPPM, CFPPT, & CFPCC)
CFPCC
Certified Fluid Power Connector & Conductor
CFPSD
Fluid Power System Designer CFPMEC (In Development) Mobile Electronic Controls
CFPIEC (In Development) Industrial Electronic Controls
Tentative Certification Review Training
IFPS offers onsite review training for small groups of at least 10 persons. An IFPS accredited instructor visits your company to conduct the review. Contact kpollander@ifps.org for details of the scheduled onsite reviews listed below.
HYDRAULIC SPECIALIST
May 2-5, Fairfield, OH. Contact info@cfcindustrialtraining.com. Written test May 6. Aug. 29-Sept. 1, Fairfield, OH. Contact info@cfcindustrialtraining.com. Written test Sept. 1.
PNEUMATIC SPECIALIST
June 13-16, Fairfield, OH. Contact info@cfcindustrialtraining.com. Written test June 16.
CONNECTOR & CONDUCTOR
May 24-25, Fairfield, OH. Contact info@cfcindustrialtraining.com. Written test May 26. Nov. 15-16, Fairfield, OH. Contact info@cfcindustrialtraining.com. Written test Nov. 17.
MOBILE HYDRAULIC MECHANIC
April 19-21, Fairfield, OH. Contact info@cfcindustrialtraining.com. Written and JP test April 22. Oct. 10-12, Fairfield, OH. Contact info@cfcindustrialtraining.com. Written and JP test Oct. 13. Online review for written test. Contact info@cfcindustrialtraining.com. IFPS members can email askus@IFPS.org for a 20% off coupon code. Test fees not included.
INDUSTRIAL HYDRAULIC MECHANIC
July 18-20, Fairfield, OH. Contact info@cfcindustrialtraining.com. Written and JP test July 21.
INDUSTRIAL HYDRAULIC TECHNICIAN
Onsite review training for small groups. Contact IFPS for details.
MOBILE HYDRAULIC TECHNICIAN
For dates, call 513-874-3225 or contact info@cfcindustrialtraining.com.
PNEUMATIC TECHNICIAN and PNEUMATIC MECHANIC
For dates, call 513-874-3225 or contact info@cfcindustrialtraining.com.
JOB PERFORMANCE TRAINING
Online review. Contact info@cfcindustrialtraining.com. Reviews includes stations 1-6 of the IFPS mechanic and technician job performance tests. Members can email askus@IFPS.org for a 20% coupon code. Test fees not included. To register, contact info@cfcindustrialtraining.com.
LIVE DISTANCE LEARNING JOB PERFORMANCE STATION REVIEW
Contact info@cfcindustrialtraining.com for information.
Certification Testing Locations
Individuals wishing to take any IFPS written certification tests can select from convenient locations across the United States and Canada. IFPS is able to offer these locations through its affiliation with the Consortium of College Testing Centers provided by National College Testing Association.
Contact headquarters if you do not see a location near you. Every effort will be made to accommodate your needs.
If your test was postponed due to the pandemic, please contact headquarters so that we may reschedule.
TENTATIVE TESTING DATES FOR ALL LOCATIONS:
April 2022
Tuesday 4/5 • Thursday 4/21
May 2022
Tuesday 5/3 • Thursday 5/19
June 2022
Tuesday 6/6 • Thursday 6/23
July 2022
Tuesday 7/12 • Thursday 7/28
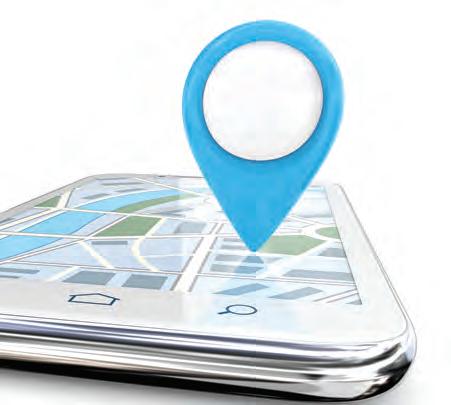
ALABAMA
Auburn, AL Birmingham, AL Calera, AL Decatur, AL Huntsville, AL Jacksonville, AL Mobile, AL Montgomery, AL Normal, AL Tuscaloosa, AL
ALASKA
Anchorage, AK Fairbanks, AK
ARIZONA
Flagstaff, AZ Glendale, AZ Mesa, AZ Phoenix, AZ Prescott, AZ Scottsdale, AZ Sierra Vista, AZ Tempe, AZ Thatcher, AZ Tucson, AZ Yuma, AZ
ARKANSAS Bentonville, AR Hot Springs, AR Little Rock, AR
CALIFORNIA
Aptos, CA Arcata, CA Bakersfield, CA Dixon, CA Encinitas, CA Fresno, CA Irvine, CA Marysville, CA Riverside, CA Salinas, CA San Diego, CA San Jose, CA San Luis Obispo, CA Santa Ana, CA Santa Maria, CA Santa Rosa, CA Tustin, CA Yucaipa, CA
COLORADO
Aurora, CO Boulder, CO Springs, CO Denver, CO Durango, CO Ft. Collins, CO Greeley, CO Lakewood, CO Littleton, CO Pueblo, CO
DELAWARE
Dover, DE Georgetown, DE Newark, DE
FLORIDA
Avon Park, FL Boca Raton, FL Cocoa, FL Davie, FL Daytona Beach, FL Fort Pierce, FL Ft. Myers, FL Gainesville, FL Jacksonville, FL Miami Gardens, FL Milton, FL New Port Richey, FL Ocala, FL Orlando, FL Panama City, FL Pembroke Pines, FL Pensacola, FL Plant City, FL Riviera Beach, FL Sanford, FL Tallahassee, FL Tampa, FL West Palm Beach, FL Wildwood, FL Winter Haven, FL
GEORGIA
Albany, GA Athens, GA Atlanta, GA Carrollton, GA Columbus, GA Dahlonega, GA Dublin, GA Dunwoody, GA Forest Park, GA Lawrenceville, GA Morrow, GA Oakwood, GA Savannah, GA Statesboro, GA Tifton, GA Valdosta, GA
HAWAII Laie, HI
IDAHO
Boise, ID Coeur d ‘Alene, ID Idaho Falls, ID Lewiston, ID Moscow, ID Nampa, ID Rexburg, ID Twin Falls, ID
ILLINOIS
Carbondale, IL Carterville, IL Champaign, IL Decatur, IL Edwardsville, IL Glen Ellyn, IL Joliet, IL Malta, IL Normal, IL Peoria, IL Schaumburg, IL Springfield, IL University Park, IL
INDIANA
Bloomington, IN Columbus, IN Evansville, IN Fort Wayne, IN Gary, IN Indianapolis, IN Kokomo, IN Lafayette, IN Lawrenceburg, IN Madison, IN Muncie, IN New Albany, IN Richmond, IN Sellersburg, IN South Bend, IN Terre Haute, IN
IOWA
Ames, IA Cedar Rapids, IA Iowa City, IA Ottumwa, IA Sioux City, IA Waterloo, IA
KANSAS
Kansas City, KS Lawrence, KS Manhattan, KS Wichita, KS
KENTUCKY
Ashland, KY Bowling Green, KY Erlanger, KY Highland Heights, KY Louisville, KY Morehead, KY
LOUISIANA
Bossier City, LA Lafayette, LA Monroe, LA Natchitoches, LA New Orleans, LA Shreveport, LA Thibodaux, LA
MARYLAND
Arnold, MD Bel Air, MD College Park, MD Frederick, MD Hagerstown, MD La Plata, MD Westminster, MD Woodlawn, MD Wye Mills, MD
MASSACHUSETTS
Boston, MA Bridgewater, MA Danvers, MA Haverhill, MA Holyoke, MA Shrewsbury, MA
MICHIGAN
Ann Arbor, MI Big Rapids, MI Chesterfield, MI Dearborn, MI Dowagiac, MI East Lansing, MI Flint, MI Grand Rapids, MI Kalamazoo, MI Lansing, MI Livonia, MI Mount Pleasant, MI Sault Ste. Marie, M Troy, MI University Center, MI Warren, MI
MINNESOTA
Alexandria, MN Brooklyn Park, MN Duluth, MN Eden Prairie, MN Granite Falls, MN Mankato, MN
MISSISSIPPI
Goodman, MS Jackson, MS Mississippi State, MS Raymond, MS University, MS
MISSOURI
Berkley, MO Cape Girardeau, MO Columbia, MO Cottleville, MO Joplin, MO Kansas City, MO Kirksville, MO Park Hills, MO Poplar Bluff, MO Rolla, MO Sedalia, MO Springfield, MO St. Joseph, MO St. Louis, MO Warrensburg, MO
MONTANA
Bozeman, MT Missoula, MT
NEBRASKA
Lincoln, NE North Platte, NE Omaha, NE
NEVADA
Henderson, NV Las Vegas, NV North Las Vegas, NV Winnemucca, NV
NEW JERSEY
Branchburg, NJ Cherry Hill, NJ Lincroft, NJ Sewell, NJ Toms River, NJ West Windsor, NJ
NEW MEXICO
Albuquerque, NM Clovis, NM Farmington, NM Portales, NM Santa Fe, NM
NEW YORK
Alfred, NY Brooklyn, NY Buffalo, NY Garden City, NY New York, NY Rochester, NY Syracuse, NY
NORTH CAROLINA
Apex, NC Asheville, NC Boone, NC Charlotte, NC China Grove, NC Durham, NC Fayetteville, NC Greenville, NC Jamestown, NC Misenheimer, NC Mount Airy, NC Pembroke, NC Raleigh, NC Wilmington, NC
NORTH DAKOTA
Bismarck, ND
OHIO
Akron, OH Cincinnati, OH Cleveland, OH Columbus, OH Fairfield, OH Findlay, OH Kirtland, OH Lima, OH Maumee, OH Newark, OH North Royalton, OH Rio Grande, OH Toledo, OH Warren, OH Youngstown, OH
OKLAHOMA
Altus, OK Bethany, OK Edmond, OK Norman, OK Oklahoma City, OK Tonkawa, OK Tulsa, OK
OREGON
Bend, OR Coos Bay, OR Eugene, OR Gresham, OR Klamath Falls, OR Medford, OR Oregon City, OR Portland, OR White City, OR
PENNSYLVANIA
Bloomsburg, PA Blue Bell, PA Gettysburg, PA Harrisburg, PA Lancaster, PA Newtown, PA Philadelphia, PA Pittsburgh, PA Wilkes-Barre, PA York, PA
SOUTH CAROLINA
Beaufort, SC Charleston, SC Columbia, SC Conway, SC Graniteville, SC Greenville, SC Greenwood, SC Orangeburg, SC Rock Hill, SC Spartanburg, SC
TENNESSEE
Blountville, TN Clarksville, TN Collegedale, TN Gallatin, TN Johnson City, TN Knoxville, TN Memphis, TN Morristown, TN Murfreesboro, TN Nashville, TN
TEXAS
Abilene, TX Arlington, TX Austin, TX Beaumont, TX Brownsville, TX Commerce, TX Corpus Christi, TX Dallas, TX Denison, TX El Paso, TX Houston, TX Huntsville, TX Laredo, TX Lubbock, TX Lufkin, TX Mesquite, TX San Antonio, TX Victoria, TX Waxahachie, TX Weatherford, TX Wichita Falls, TX
UTAH
Cedar City, UT Kaysville, UT Logan, UT Ogden, UT Orem, UT Salt Lake City, UT
VIRGINIA
Daleville, VA Fredericksburg, VA Lynchburg, VA Manassas, VA Norfolk, VA Roanoke, VA Salem, VA Staunton, VA Suffolk, VA Virginia Beach, VA Wytheville, VA
WASHINGTON
Auburn, WA Bellingham, WA Bremerton, WA Ellensburg, WA Ephrata, WA Olympia, WA Pasco, WA Rockingham, WA Seattle, WA Shoreline, WA Spokane, WA
WEST VIRGINIA
Ona, WV
WISCONSIN
La Crosse, WI Milwaukee, WI Mukwonago, WI
WYOMING
Casper, WY Laramie, WY Torrington, WY
CANADA ALBERTA
Calgary, AB Edmonton, AB Fort McMurray, AB Lethbridge, AB Lloydminster, AB Olds, AB Red Deer, AB
BRITISH COLUMBIA
Abbotsford, BC Burnaby, BC Castlegar, BC Delta, BC Kamloops, BC Nanaimo, BC Prince George, BC Richmond, BC Surrey, BC Vancouver, BC Victoria, BC
CELEBRATING 60 YEARS
MANITOBA
Brandon, MB Winnipeg, MB
NEW BRUNSWICK
Bathurst, NB Moncton, NB
NEWFOUNDLAND AND LABRADOR
St. John’s, NL
NOVA SCOTIA
Halifax, NS
ONTARIO
Brockville, ON Hamilton, ON London, ON Milton, ON Mississauga, ON Niagara-on-the-Lake, ON North Bay, ON North York, ON Ottawa, ON Toronto, ON Welland, ON Windsor, ON
QUEBEC
Côte Saint-Luc, QB Montreal, QB
SASKATCHEWAN
Melfort, SK Moose Jaw, SK Nipawin, SK Prince Albert, SK Saskatoon, SK
YUKON TERRITORY
Whitehorse, YU
UNITED KINGDOM
Elgin, UK
GHAZNI
Kingdom of Bahrain, GHA Thomasville, GHA
EGYPT Cairo, EG
JORDAN
Amman, JOR
NEW ZEALAND
Taradale, NZ
COMPONENT SHOWCASE
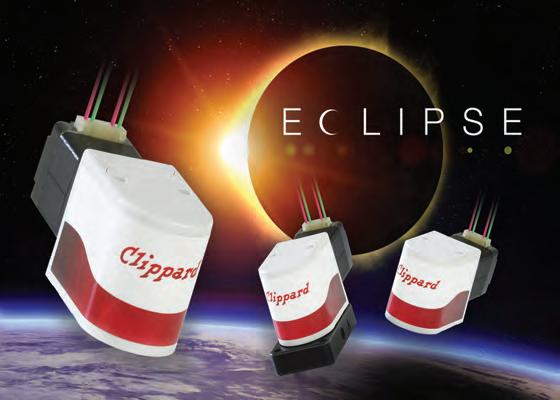
Clippard manufactures a full range of miniature fluid control devices and components including pressure controls, electronic valves, analytical and oxygen clean valves, proportional and proportional isolation valves, pinch and isolation valves, precision regulators, fittings, tubing and more. Clippard continues to be an industry leader in providing innovative products, application engineering and cost-saving solutions for a wide range of applications. Proudly made in the USA.
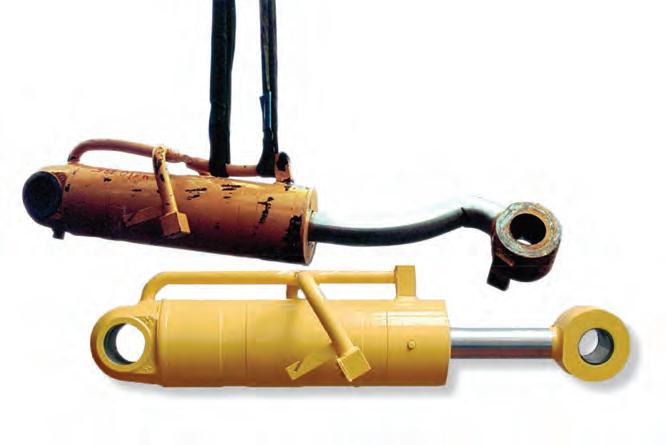
ACHIEVE ULTRA-FINE PROPORTIONAL FLOW CONTROL WITH ECLIPSE ISOLATION VALVES
Utilizing the industry’s most robust and powerful miniature linear actuator, the patented stepper-controlled Eclipse proportional isolation valve leads the industry in performance and durability. This award-winning valve is ideal in critical applications for liquid and gas delivery, medical, analytical and industrial automation requiring ultra-fine resolution and excellent repeatability. In addition, the unique design allows for custom flow profiles.
• Ceramic Sliding Seal • Stepper Motor Controlled • Gas & Liquid Compatible • Inert Wetted Materials • Zero Dead volume (Fully Flushable) • Soft Start to Help with Hammer & Flow in Rush • Leak free (<0.05 sccm) • Excellent linearity (<4% of full-scale) • Fast response (<2 ms reaction time) • Repeatability <0.5% of full travel
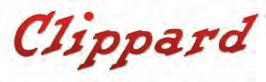
SO, YOU PURCHASED YOUR LAST HYDRAULIC CYLINDER BASED ON PRICE?
Don’t worry, you are not alone in this decision. But, do you know what your real costs are? Failure + Downtime + Repair = $$$ far more than you signed up for. We pride ourselves on partnering with our customers to ensure they get the life and performance they desire. From small to large, and with our experience and expertise, Hunger Hydraulics Group has not only produced the world’s largest hydraulic cylinders – over 260 tons! – but is also, proudly providing extensive manufacturing and repair in NW OHIO since 1981. Ask about our lifetime warranty – Hunger Hydraulics USA. #HOWBIGDOYOUWANTIT
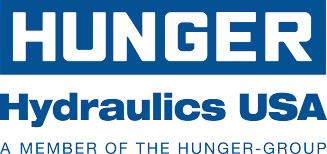
Hunger Hydraulics 1-800-248-9232 E-mail: info@hunger-hydraulics.com hunger-hydraulics.com
COMPONENT SHOWCASE
THE FLANGE CONNECTOR YOU NEED – QUICK AS 1, 2, 3
Why use MAIN MANUFACTURING PRODUCTS?
1QUICK: MAIN has a large and diverse inventory, including specials for same day shipping. MAIN’s US production facility, specialized manufacturing processes, and large raw material inventory allow your custom non-stock parts to be shipped in days.
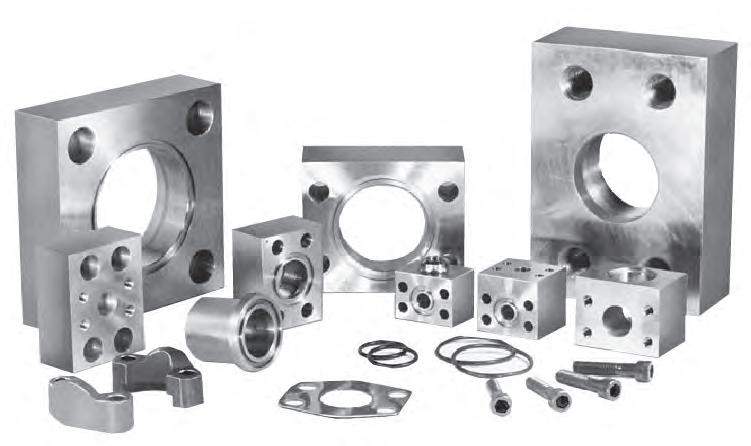
2INFORMED: MAIN’s engineers are active on ISO and SAE committees. They are available to assist you with your flange needs, call 800.521.7918, e-mail to info@MAINmfg.com or fax 810.953.1385.
3DEPENDABLE: MAIN has 60 years of experience in designing, developing, manufacturing and distributing quality hydraulic flanges and components.
Grand Blanc, MI 800.521.7918; FAX: 810.953.1385 E-mail: info@mainmfg.com Web: www. mainmfg.com/fpj
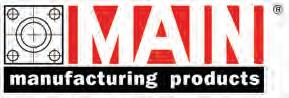
GOT PUMPS? GET DRIVES!
Stiebel Pump Drives allow Engineers to create space saving layouts by mounting multiple pumps in a single plane. Our ratio ranges also allow for use of smaller, lower cost or cost effective pumps operating at higher speeds to deliver hydraulics where and when they are needed. Highly responsive, with your application specifications, Stiebel can turn around quotes and application files (drawings and CAD files in pdf, stp, dxf …) within an average of 24-72 hours. Globally, Stiebel is Best-in-Class and the top provider over a range of pump drive configurations. Work with us, and we’ll show you how well your Design, Builds and Logistics can be supported when it comes to Pump Drives.
FIND US ON We Offer the Broadest in Custom Configurations for Pump Drives
