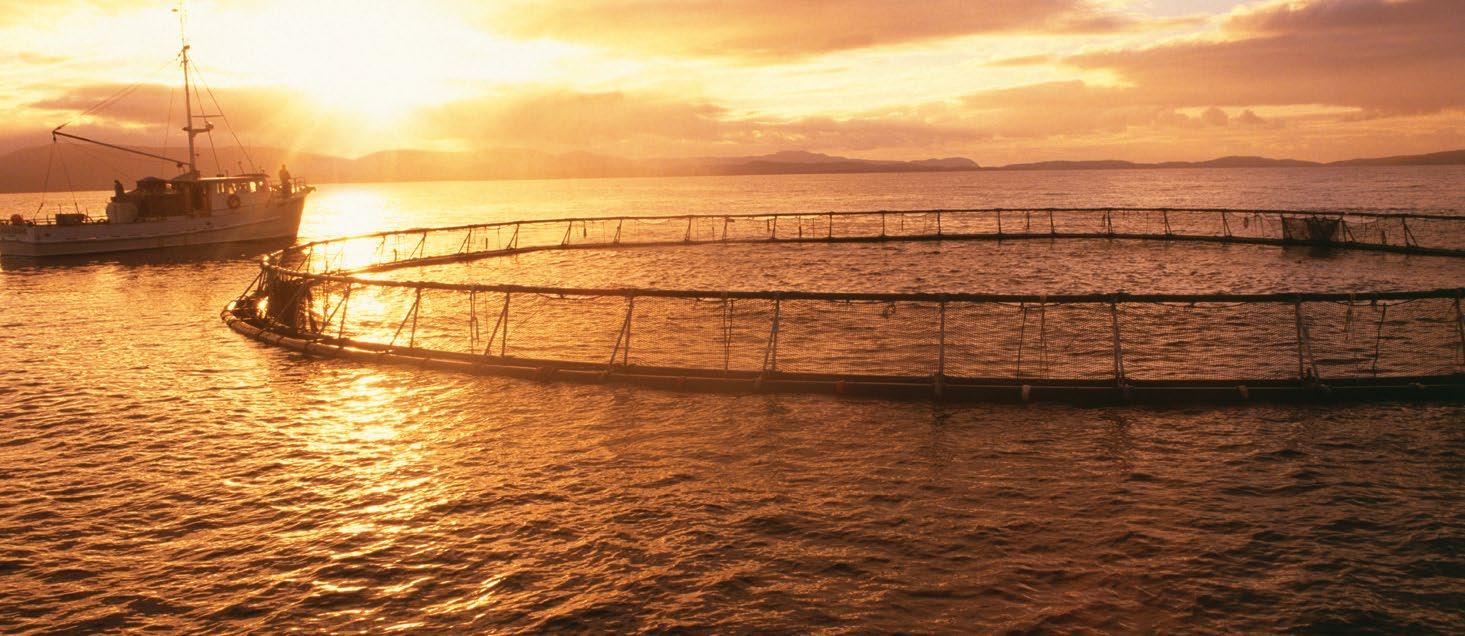
6 minute read
Cover story
35 Years Of Fish Pens: Continuous Improvements Through The Decades
–An 80 metre pen at Hideaway Bay –
Advertisement
Take a look at salmon farmers anywhere in the world and they all have one thing in common—the desire to create better fish pens that keep stock safe, exclude predators and provide a safer working environment for employees. The way to achieve this is through investing time and money in improving pen design; something that Huon has done plenty of over the past 35 years.
When Huon Aquaculture began farming at Hideaway Bay, the first fish pens used were only 40 metres in circumference—tiny by today’s standards. Gradually as production increased, so did the size of the pens—from 40m to 60m, to 80m, to 120m, 168m in 2006 and finally, 240m in 2014. “I remember when Huon was using a number of different sizes from 80 metre through to 120 metres,” said Leigh Savage, Huon’s Assistant Farm Manager. In more recent times, Leigh has been involved in modelling pen updates and alongside the Project Team has rolled out various upgrades and retrofits. “The old pens were hard to move around on as they didn’t have any walkway plates so employees got around them by walking on slack chains strung between the two collars, or the collars themselves. Needless to say, lots of people got wet and hurt by falling through.”
–In 2006, Huon launched a 168 metre pen which was the largest in the industry at the time. –
“During this time we were experimenting with poles and netting to stop seals from jumping into the pen and ways to strengthen pen parts to withstand towing.” Seals are incredibly smart and will find any weakness in a pen to exploit. This is as true today as it was back when salmon farming was first established.
“One thing we did add to try and stop seals was aluminium poles that slid into the side of the stanchions and held a net above the handrail. The mesh was also then sewn to the jump fence of the inner net. These worked okay but still allowed the seals to haul out onto the pen to rest,” said Leigh.
–It was clear that while pen technology was heading in the right way, the design needed accelerating to enable Huon to move into more open waters and to provide a safer working environment. –
–The notorious chain walkway –
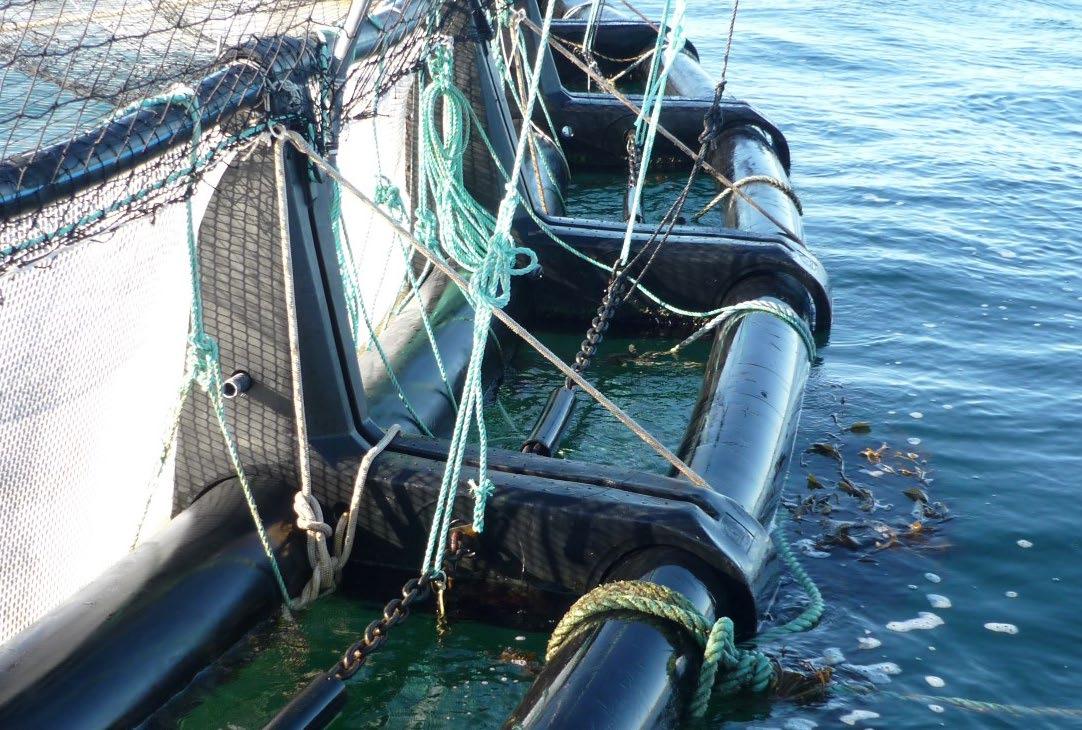
“In 2011, David Morehead, then Business Development Manager, started looking at how we could upgrade our pens so they could withstand larger seas and worse weather, keep predators out as well as be more practical and safer for the teams using them,” said Leigh. This led to a staff callout in 2012 to ask for ideas on how we could change our current setups to achieve these goals. Four pen designs were put forward along with new ideas for how to moor the pens in deeper, rougher water. “Once all of the ideas were received, we then worked on the best design and ended up with a double net system with a single weight and a seal fence above the outer collar.”
David recalls, “we were nearing the end of one of our meetings back in 2012 and couldn’t resolve a few issues and Phillip Dayton, now Huon's Pen and Mooring Manager, said “let’s just build one and we’ll sort it out as we go”. That was exactly the attitude this project needed. We ended the meeting on that note and went and built the first pen.” The prototype developed is still in use at Hideaway Bay today. “The participation and enthusiasm of employees during this process really should be commended as they were the driving force behind the project. For many of these people, the pen was where they worked so there was no-one who knew the issues more intimately than them.” The inner net, that is part of the double net prototype design, was tapered inwards to allow for greater separation between stock and predators. This minimises fish from being spooked by seeing predators which leads to improved performance. “David spoke to many aquaculture and netting companies around the world over the next few months and finally landed on a company called Aqualine from Norway who had steel stanchions and were willing to modify them to a triple collar design for testing,” said Leigh.
–The prototype pen demonstrated that steel pen components, which looked great on paper, simply weren’t the answer. –
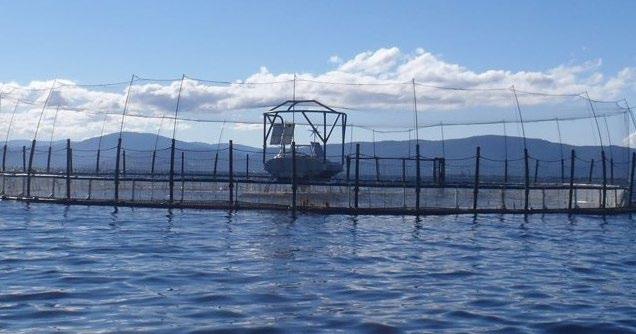
–The prototype pen –
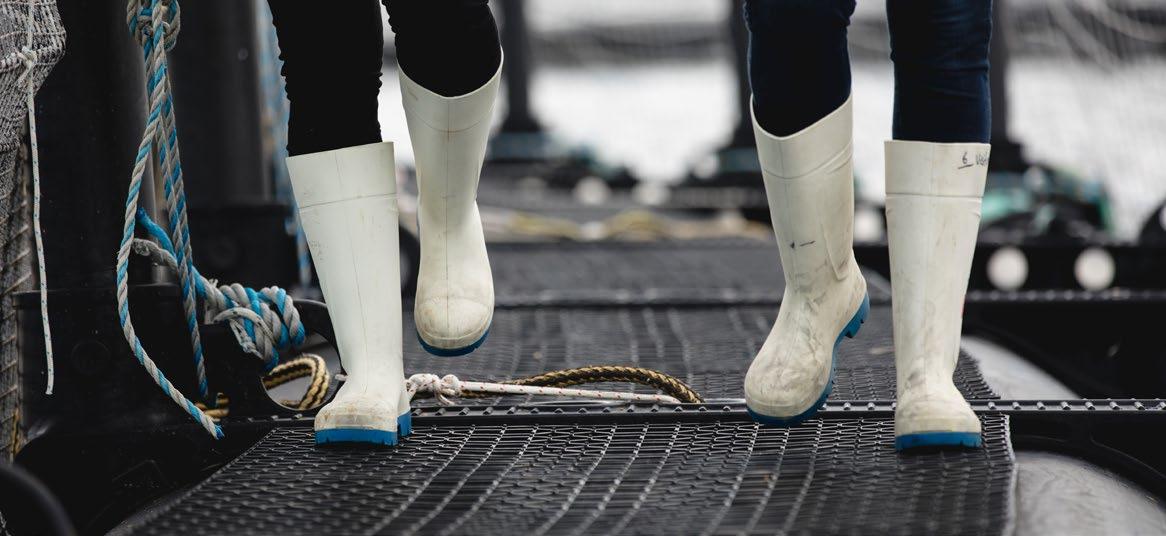
“We looked into injection moulded highdensity polyethylene (HDPE) stanchions because this material was stronger, more durable and a better price. Huon engaged a moulding specialist called John Rafferty who designed our stanchion moulds along with walkway plates, handrail T’s, pin lockers, cotton reels, and other small components,” said Leigh.
_ At rough farming sites, it is important that each component of a pen can move and flex with the waves. Anything that is stationary will sheer off and compromise the overall integrity of the pen. –
“The Fortress Pens were integral towards enabling Huon’s move into Storm Bay. We’ve seen some pretty significant swells come through this site so it is really important that the pens move with the wave.”
The key to making the new Fortress Pens safer, was to include an enclosed walkway that significantly improved safety outcomes for employees. The walkway is accessible through gates which prevent seals from hauling out around the circumference of the pen. This reduces the potential for aggressive and territorial seals interacting with employees. The Fortress Pen system received the Innovation in Safety award from the 2015 Tasmanian Community Achievement Awards in recognition of its innovative approach to on-water employee safety. “Over time it became clear that making the stanchions out of Nylon, at John Rafferty’s suggestion, would almost double their breaking load which would make the pens even more suitable for offshore use.”
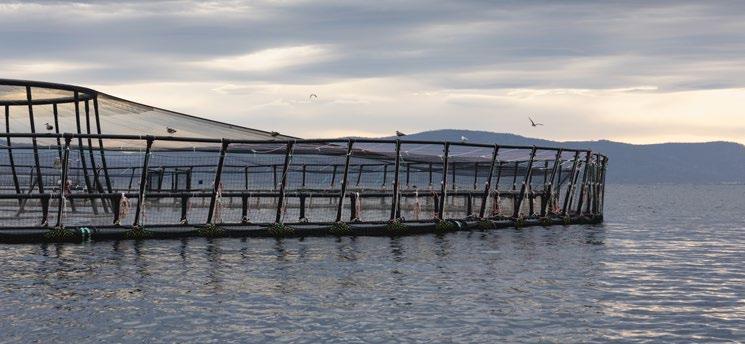
From the original design, the pens have undergone a lot of changes. Some ideas have been successful and rolled out, while others have been not quite as successful and discontinued.
“Notably, recently we went back to Dave’s 2012 concept drawings and rolled out a top rail to stop the seal poles from rolling in.” “This was implemented in 2019 when we kept having issues with seal getting over the seal fence and the bird nets not tensioning properly. We have since removed all bird poles and retrofitted these top rails onto every pen.” This has enabled the bird nets to be better tensioned, as well as to keep the seal poles in their correct position. There’s been discussion about making even bigger pens but in Leigh’s words, “what we have now is working well.” “We are always looking for tweaks to the design and it has been great to see people submitting ideas through the Innovation Program. We’re currently trialling new ways of rigging to see if it reduces chafing on the ropes which is an ongoing challenge for aquaculture producers across the globe,” said Leigh. So while the pathway to the current Fortress Pen design has been 35 years in the making, it is far from the end of the continuous improvement journey.
–The top rail keeps nets tensioned –