
37 minute read
1. El envasado de frutas y hortalizas
2. Legislación sobre envasado y etiquetado de productos hortofrutícolas
José Mª Ferrer Villar * jmferrer@ainia.es
La aproximación a la legislación que aplica en cuestiones sobre el envasado de los productos hortofrutícolas debe realizarse desde tres enfoques, productos frescos envasados, materiales en contacto con los alimentos y los envases y residuos de envases.
En el caso de los productos frescos envasados contamos con legislación que de forma concreta establece los criterios básicos para este tipo de alimentos, entre los que se encuentran las frutas y hortalizas a través del Real Decreto 888/1988, de 29 de julio, por el que se aprueba la norma general sobre recipientes que contengan productos alimenticios frescos, de carácter perecedero, no envasados o envueltos. Se trata de un punto de partida, dado que es una norma muy general y que no ha desarrollado los distintos aspectos sobre los envases, como es el caso de las características que deben tener para poder estar en contacto con los productos hortofrutícolas.
En este punto es en el que entra la legislación sobre materiales en contacto con los alimentos para determinar qué tipo de materiales y que características deben tener para que puedan dedicarse al envasado de frutas y hortalizas. La disposición clave es el Reglamento (CE) nº 1935/2004 del Parlamento Europeo y del Consejo, de 27 de octubre de 2004, sobre los materiales y objetos destinados a entrar en contacto con alimentos y por el que se derogan las Directivas 80/590/CEE y 89/109/CEE. Como elementos clave de la legislación sobre materiales en contacto con los alimentos hemos de considerar el “ABC” básico que deben respetar lo materiales no transfiriendo sus componentes a los alimentos de forma que:
- Representen un peligro para la salud humana,
Envasado sostenible de frutas y hortalizas
- Provoquen una modificación inaceptable de la composición de los alimentos,
- Provoquen una alteración de las características organolépticas de éstos.
Sin olvidar la necesidad de la declaración de conformidad mediante la que se certifica la conformidad de los materiales de acuerdo con lo previsto en la legislación vigente.
Por último y por su novedad, considero relevante que se aluda a la reciente regulación sobre envases y residuos de envases:
La Ley 7/2022, de 8 de abril, de residuos y suelos contaminados para una economía circular y Real Decreto 1055/2022, de 27 de diciembre, de envases y residuos de envases constituyen en el nuevo marco regulatorio para los envases y residuos de envases y afectan a todos los productos envasados. En el caso que las frutas y hortalizas nos fijamos en una cuestión concreta sobre comercialización de este tipo de alimentos que ha regulado el artículo 7.4.a) del Real Decreto 1055/2022:
«4. Los comercios minoristas de alimentación adoptarán las medidas necesarias para: a. Presentar a granel aquellas frutas y verduras frescas que se comercialicen enteras Esta obligación no se aplica a las frutas y hortalizas envasadas en lotes de 1,5 kilogramos o más, ni a las frutas y hortalizas que se envasen bajo una variedad protegida o registrada o cuenten con una indicación de calidad diferenciada o de agricultura ecológica, así como a las frutas y hortalizas que presentan un riesgo de deterioro o merma cuando se venden a granel, las cuales se determinarán por orden del Ministerio de Agricultura, Pesca y Alimentación, en coordinación con el Ministerio para la Transición Ecológica y el Reto Demográfico y la Agencia Española de Seguridad Alimentaria y Nutrición, en el plazo de seis meses desde la entrada en vigor de este real decreto. Una vez publicada la lista anterior, los comercios dispondrán de un plazo de seis meses para su adaptación en el caso de las frutas y hortalizas no exceptuadas».
2. Etiquetado de productos hortofrutícolas
El etiquetado de las frutas y hortalizas considero oportuno que lo veamos aproximándonos a la legislación sobre la OCM, la regulación sobre etiquetado de productos a granel y finalmente lo establecido en materia de información al consumidor.
Si hablamos de OCM y aspectos que afectan al etiquetado de frutas y hortalizas tendremos en cuenta el Reglamento (UE) nº 1308/2013 del Parlamento Europeo y del Consejo, de 17 de diciembre de 2013, por el que se crea la organización común de mercados de los productos agrarios. La regulación sobre la OCM contempla la posibilidad de aplicar normas de comercialización a las frutas y hortalizas y que sin perjuicio de lo dispuesto en el artículo 26 del Reglamento (UE) nº 1169/2011, podrán abarcar, entre otros, uno o más de los siguientes requisitos, que se establecerán por sectores o por productos y estarán basados en las características de cada sector, en la necesidad de regular la puesta en el mercado:
- Denominaciones de venta www.bibliotecahorticultura.com sobre envasado y etiquetado de productos hortofrutícolas
- Criterios de clasificación, como la división en clases, el peso, el tamaño, la edad o la categoría;
- Especie, la variedad vegetal o la raza animal o el tipo comercial;
- criterios como la apariencia, consistencia, conformación, características de los productos y porcentaje de humedad;
- Lugar de producción y/o el origen;
Con carácter general para informar al consumidor, y por tanto para etiquetar los productos alimenticios hemos de considerar lo establecido por el Reglamento (UE) nº 1169/2011 del Parlamento Europeo y del Consejo, de 25 de octubre de 2011, sobre la información alimentaria facilitada al consumidor y por el que se modifican los Reglamentos (CE) nº 1924/2006 y (CE) nº 1925/2006 del Parlamento Europeo y del Consejo, y por el que se derogan la Directiva 87/250/CEE de la Comisión, la Directiva 90/496/CEE del Consejo, la Directiva 1999/10/CE de la Comisión, la Directiva 2000/13/CE del Parlamento Europeo y del Consejo, las Directivas 2002/67/CE, y 2008/5/CE de la Comisión, y el Reglamento (CE) nº 608/2004 de la Comisión.
Los elementos obligatorios que con carácter general se aplican a todos los alimentos se establecen en el artículo 9 del Reglamento (UE) nº 1169/2011:
- Denominación del alimento
- Lista de ingredientes
- Indicación ingredientes alérgenos
- Cantidad de determinados ingredientes o de determinadas categorías de ingredientes
- Cantidad neta del alimento
- Fecha de duración mínima o la fecha de caducidad
- Condiciones especiales de conservación y/o las condiciones de utilización
- Nombre o la razón social y la dirección del operador de la empresa alimentaria
- País de origen o lugar de procedencia
- Modo de empleo en caso de que, en ausencia de esta información, fuera difícil hacer un uso adecuado del alimento
- Indicación grado alcohólico (bebidas que tengan más de un 1,2 % en volumen de alcohol)
- Información nutricional.
Estos aspectos son aplicables a las frutas y hortalizas con algunas salvedades previstas en la normativa.
Por último, hemos de considerar la regulación para los alimentos que se comercializan sin envasar, algo que es frecuente con las frutas y hortalizas. En ese caso prestaremos atención al Real Decreto 126/2015, de 27 de febrero, por el que se aprueba la norma general relativa a la información alimentaria de los alimentos que se presenten sin envasar para la venta al consumidor final y a las colectividades, de los envasados en los lugares de venta a petición del comprador, y de los envasados por los titulares del comercio al por menor.
Las exigencias para estos productos son similares a las que se marcan en el Reglamento 1169/2011, aunque en una versión más sintética o abreviada. La información alimentaria se facilitará en alguno de estos cuatro supuestos:
Envasado sostenible de frutas y hortalizas
- Que se presenten sin envasar para la venta al consumidor final y a las colectividades;
- Envasados en los lugares de venta a petición del comprador;
- Envasados por los titulares del comercio al por menor para su venta inmediata en el establecimiento o establecimientos de su propiedad; www.bibliotecahorticultura.com
- Contemplados en los supuestos anteriores y ofrecidos para la venta mediante comunicación a distancia.
3. El envase de cartón y cartoncillo
4. Materiales plásticos convencionales, renovables y reutilizables
Envasado sostenible de frutas y hortalizas
1. Necesidad del envasado de productos hortofrutícolas
El envase se define según el Real Decreto 1055/2022 de envases y residuos de envases como “todo producto fabricado con materiales de cualquier naturaleza y que se utilice para contener, proteger, manipular, distribuir y presentar mercancías, desde materias primas hasta artículos acabados, en cualquier fase de la cadena de fabricación, distribución y consumo”. Por tanto, un envase tiene diferentes funciones:
- Contener, para albergar el producto
- Proteger de agentes externos como oxígeno, dióxido de carbono, etc. en función de las necesidades del producto envasado
- Manipular
- Distribuir a través de las diferentes etapas del ciclo de vida del producto.
- Presentar y comunicar, por ejemplo, la información nutricional del producto envasado o la reciclabilidad del envase, entre otros.
En concreto, para el envasado de productos hortofrutícolas frescos, hay que tener en cuenta que, tras la poscosecha, continúan sus procesos metabólicos, por lo que se deben seleccionar los materiales y el proceso de envasado adecuados para conservar el alimento desde su recogida hasta la puesta en venta en los lineales, de forma que el envase garantice la seguridad alimentaria. Otra función del envase es alargar la vida útil de los alimentos, lo que supone una reducción del desperdicio de comida y un ahorro en costes.
Además, debido al ritmo de vida de las últimas décadas, sobre todo en los grandes núcleos de población, los distribuidores de productos hortofrutícolas se han ido adaptando a las necesidades del consumidor tratando de simplificar y facilitar el consumo de dichos productos. Estos productos se pueden presentar al consumidor lavados, pelados y cortados, por lo que están más expuestos a su deterioro (deshidratación, oxidación, aceleración de la maduración, etc.) por la acción de factores externos. Por ello, es especialmente importante en estos casos preservar de manera óptima los productos hortofrutícolas mediante
El Sistema De Envasado
2. Materiales plásticos convencionales para el envasado de productos hortofrutícolas
En 2020 el consumo total de plástico en Europa fue de 50,7 millones de toneladas. De dicho consumo, un 39,6 % fue destinado al sector de envase en el año 2020. Por lo tanto, el sector envase es el principal sector de demanda de materiales plásticos. Esto se debe a su baja densidad, y, por tanto, ligereza, las diferentes propiedades
Que Puede Aportar Por
combinación de diferentes materiales y su bajo coste. En la Figura 1 se muestra la producción de material plástico en Europa en el año 2020 por tipología, indicando el sector al que va destinado www.bibliotecahorticultura.com
2.1. Conceptos básicos sobre materiales plásticos
Se denomina plástico a la mezcla de un polímero con unos determinados aditivos.
Los aditivos se añaden normalmente en concentraciones entre 0,5 – 5 % para mejorar las propiedades de los polímeros y facilitar su procesado.
Un polímero es una macromolécula ya que está formada por la reacción o polimerización de multitud de moléculas de monómero. De esta forma, el polímero se forma por la repetición múltiple de una o más unidades moleculares diferentes formando así una cadena polimérica.
Si la cadena polimérica está formada por una única unidad de repetición se obtiene un homopolímero y, si está formada por dos o más unidades de repetición diferentes se obtiene un copolímero.
Durante la polimerización se obtienen cadenas poliméricas de diferente longitud, es decir, se obtiene una distribución de pesos moleculares, por lo que los polímeros se caracterizan por un peso molecular promedio. Además, en función de cómo se produzca el crecimiento de las cadenas poliméricas durante su síntesis, se consideran diferentes estructuras poliméricas: lineales, ramificadas o entrecruzadas (Figura 2)
Los polímeros se caracterizan por su cristalinidad. Esta se refiere al grado de empaquetamiento de las cadenas poliméricas para obtener una disposición ordenada, por tanto, depende principalmente de la estructura química del polímero: la longitud de las cadenas, las ramificaciones, la voluminosidad de los átomos que forman la cadena, pero, también depende de las condiciones de transformación como la temperatura o la velocidad de enfriamiento.
Envasado sostenible de frutas y hortalizas
Mientras que, aquellos polímeros que se disponen al azar se denominan polímeros amorfos. En la realidad no es posible encontrar polímeros 100 % cristalinos, por lo que se habla de polímeros semicristalinos con diferente grado de cristalinidad. De esta forma, se considera que un polímero posee una cristalinidad elevada si el grado de cristalinidad es mayor del 70 % y, que tiene una baja cristalinidad con grados de cristalinidad entre 25 – 40 %. En la Figura 3 se muestra la estructura polimérica de un polímero semicristalino (Figura 3).
Los materiales plásticos se clasifican según su naturaleza en termoplásticos, termoestables y elastómeros. Los materiales termoplásticos son los que se utilizan en el sector envase ya que al aumentar la temperatura se reblandecen y funden y, al disminuir la temperatura recuperan su estado sólido, por lo tanto, son materiales que se pueden moldear y reciclar. La temperatura de transición vítrea (Tg) de un polímero es la temperatura a partir de la cual comienza a producirse el movimiento de las cadenas poliméricas de la zona amorfa, por lo que el material comienza a cambiar de estado sólido a deformable. Esta temperatura es siempre menor que la temperatura de fusión (Tf) del material, que es la temperatura a la cual el material funde. Además, las poliolefinas son aquellos polímeros sintetizados a partir de hidrocarburos alifáticos de cadena corta, por lo que dentro de este concepto se incluyen el polietileno y el polipropileno.
2.2. Polietileno (PE)
El polietileno es un hidrocarburo saturado de alto peso molecular. Tal y como se comentaba en el apartado anterior, se trata de una poliolefina. En la Figura 4 se muestra la estructura química del mónomero etileno y del polietileno, obtenido por la polimerización de multitud de moléculas de etileno.
Debido a su estructura simétrica tiene una gran capacidad de cristalización, por lo que se trata de un material semicristalino. En función de las condiciones de síntesis (presión, temperatura, catalizadores empleados, etc.) se pueden obtener estructuras lineales o ramificadas, por lo que dependiendo de esto y de la longitud de las ramificaciones se obtienen diferentes polietilenos. Los más utilizados se describen a continuación.
www.bibliotecahorticultura.com
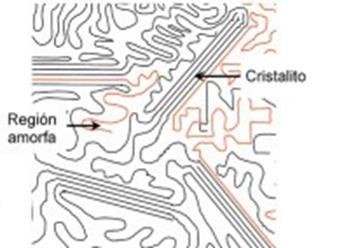
Materiales plásticos convencionales, renovables y reutilizables
- High Density Polyethylene, HDPE Presenta pocas ramificaciones y son de cadena corta, se puede decir que la estructura es prácticamente lineal, por lo que tiene una elevada densidad, cristalinidad y resistencia mecánica. Tiene un grado de cristalinidad entre 70 – 75 %.
- Low Density Polyethylene, LDPE. Presenta elevadas ramificaciones y son de cadena larga, por lo que tiene baja densidad, cristalinidad y menor resistencia mecánica que el HDPE. Tiene un grado de cristalinidad entre 40 – 50 %.
- Linear Low Density Polyethylene, LLDPE. Presenta un grado medio de ramificación y son de cadena corta, por lo que tiene unas propiedades intermedias entre los polímeros anteriores. Tiene un grado de cristalinidad entre 55 – 65 %.
En la Figura 5 se muestran las diferentes estructuras que presentan los tipos de polietileno descritos.
Por lo general, los polietilenos tienen una baja temperatura de transición vítrea (entre – 100 y –10 ºC) y, una baja temperatura de fusión (entre 100 y 135 ºC). Sin embargo, cada uno de los polietilenos descritos presentan diferentes propiedades finales debido a la diferente estructura que adquieren durante el proceso de síntesis. En la Tabla 1 se muestran las propiedades de los diferentes tipos de polietileno.
Material
Densidad de 0,940 – 0,965 g/cm3.
Fácil procesabilidad.
Propiedades
Mejores propiedades mecánicas (rigidez, dureza y resistencia a la tensión) que el LDPE.
Buena resistencia a tracción y química.
HDPE

Buena resistencia al impacto y a la abrasión.
Resistencia a temperaturas superiores que el LDPE, lo que permite la esterilización.
Baja resistencia a la radiación UV.
Excelente barrera al vapor de agua.
Elevada permeabilidad a gases y vapores, pero menor que el LDPE
Densidad de 0,915 – 0,930 g/cm3.
Muy buena procesabilidad.
Menor rigidez, resistencia al desgarro, dureza y resistencia química que el HDPE.
LDPE www.bibliotecahorticultura.com
Mayor flexibilidad que el HDPE.
Baja resistencia a tracción, pero buena resistencia al impacto.
Baja conductividad térmica.
Envasado sostenible de frutas y hortalizas
Excelente barrera al vapor de agua.
Elevada permeabilidad a gases y vapores, mayor que el HDPE.
Buena resistencia a tracción, rasgado y punción.
Buena resistencia al impacto a temperaturas bajas, de hasta -95 ºC.
Lldpe
Excelente elongación en film.
Excelente barrera al vapor de agua.
Elevada permeabilidad a gases y vapores
2.3.
El polipropileno (PP) es una poliolefina que se obtiene por polimerización de multitud de moléculas de propileno. Tiene una estructura química similar al polietileno, ya que el monómero de partida en ambos casos es similar, en el caso del PP tiene un grupo metilo (-CH3), tal y como se observa en la Figura 6
Se obtienen tres tipos de PP diferentes y, por tanto, con diferentes propiedades finales, dependiendo de la ordenación espacial de este grupo metilo: atáctico si los grupos metilo se ordenan al azar, isotáctico si los grupos metilo están dispuestos en el mismo lado de la cadena polimérica y sindiotáctico si los grupos metilo están dispuestos de un lado y del otro de la cadena polimérica. En la Figura 7 se muestra la disposición de los grupos metilo en los diferentes tipos de PP que se pueden obtener.
Sin embargo, el PP más utilizado en el sector envase es el isotáctico, ya que la distribución regular de los grupos metilo le otorga un elevado grado de cristalinidad de entre 70 – 80 %. En la Tabla 2 se muestran las propiedades del PP isotáctico.
Material
Propiedades PP isotáctico
Mejores propiedades mecánicas que el polietileno. Temperatura máxima de uso de 150 ºC, por lo que es microondable, pasteurizable y esterilizable.
Termosellable pero, con un peor comportamiento que el polietileno.
Buena barrera al vapor de agua.
No posee barrera frente a gases.
Baja tensión superficial www.bibliotecahorticultura.com
2.4. Poliestireno (PS)
El poliestireno (PS) se obtiene por la polimerización de multitud de monómeros de estireno o vinilbenceno. En la Figura 8 se muestra la estructura química del monómero de estireno, así como del poliestireno obtenido por polimerización de éste.
Al igual que el PP, en función de la ordenación espacial de la estructura molecular se pueden obtener diferentes tipos de PS: atáctico, isotáctico y sindiotáctico. El PS atáctico es amorfo ya que la disposición al azar del grupo funcional no permite el ordenamiento de las cadenas poliméricas y, por el contrario, el PS isotáctico y sindiotáctico es semicristalino. Sin embargo, el PS que se produce principalmente a escala industrial es el PS isotáctico. En la Tabla 3 se muestran las propiedades del PS.
Material
Densidad de 1,05 g/cm3.
Propiedades
Puede ser procesado en un amplio rango de temperaturas.
Resistencia mecánica media.
Elevada rigidez.
PS
Baja resistencia al impacto.
Baja absorción de agua.
Escasa resistencia a la intemperie.
Transparente.
Temperatura de uso entre 60 – 70 ºC
Además de su uso como plástico sólido, existen dos tecnologías diferentes para obtener PS expandido y PS espumado.
El PS expandido o Expanded Polystyrene (EPS) se obtiene mediante un agente de expansión, normalmente el pentano y, por aplicación de calor y vapor de agua se generan celdas de aire en su interior. Una vez obtenidas las perlas de PS expandido se transforman en moldes por aplicación de temperatura y presión para soldar las perlas entre sí y conformar el envase.
El PS espumado o Extruded Polystyrene (XPS) se obtiene por extrusión inyectándose en la propia línea de extrusión un gas, normalmente butano, para generar celdas de aire en el interior del material.
2.5. Polietilentereftalato (PET)
El polietilentereftalato (PET) es un poliéster, ya que contiene el grupo funcional éster en su cadena principal, semiaromático, formado a partir de la reacción de etilenglicol y, ácido tereftálico purificado (PTA) o dimetil tereftalato (DMT). En la Figura 9 se muestra la reacción de polimerización para la obtención del PET.
Se trata de un polímero lineal, por lo que tiene un alto grado de cristalinidad. Sin embargo, en función de las condiciones de procesado, es posible disminuir el grado de cristalinidad. Por ello, en las aplicaciones que requieren un alto grado de transparencia, se realiza un enfriamiento rápido del material para evitar el ordenamiento de las cadenas poliméricas, obteniendo así un menor grado de cristalinidad. En la Tabla 4 se muestran las propiedades generales del PET.
Material
PET
Elevada rigidez
Propiedades
Elevada resistencia al impacto incluso a bajas temperaturas
Elevada transparencia, si se enfría rápidamente durante su procesado
Buen coeficiente de deslizamiento
Buena resistencia térmica
Muy buena barrera a dióxido de carbono y, barrera media a oxígeno y vapor de agua
2.6. Poliamida (PA)
Las poliamidas alifáticas se obtienen por policondensación de un ácido dicarboxílico y de una diamina. En función de la longitud de los productos de partida se distinguen diferentes tipos de poliamida. La primera cifra de la nomenclatura corresponde al número de carbonos (longitud) de la diamina y, la segunda cifra al número de carbonos del ácido dicarboxílico. En la Tabla 5 se muestran los diferentes tipos de poliamida más utilizados en el sector envase, así como las propiedades generales de la poliamida.
Tabla 5. Propiedades generales y tipos de poliamida
Material
PA 66
PA 6
PA 612
Copolímero PA 6/66
Resistencia a la tracción y dureza
Resistencia al rayado
Propiedades
Resistencia a la temperatura, por lo que es esterilizable
Barrera al oxígeno y aromas
Resistencia a las grasas y aceites
Elevada transparencia
De entre los tipos de PA más utilizadas en el sector envase, destaca la PA 66 ya que presenta buenas propiedades mecánicas, rigidez y resistencia a la temperatura. Sin embargo, la PA 6 es más fácil de procesar y presenta elevada resistencia al impacto. El copolímero PA 6/66 tiene como principal ventaja una menor cristalinidad, por lo que tiene mejores propiedades ópticas de brillo y transparencia.
Envasado sostenible de frutas y hortalizas www.bibliotecahorticultura.com
2.7. Copolímero de etileno-alcohol vinílico (EVOH)
El copolímero de etileno-alcohol vinílico (EVOH) se obtiene en dos pasos. En primer lugar, mediante una reacción de síntesis entre etileno y acetato de vinilo se obtiene el polímero etilvinilacetato (EVA). Y, en un segundo paso, dicho copolímero se hidroliza para obtener EVOH. Por lo general presenta buenas propiedades barrera a gases, aceites y grasas, pero, es sensible a la humedad, siendo incluso soluble en agua. Destaca por sus excelentes propiedades barrera al oxígeno, sin embargo, expuesto a ambientes con alta humedad relativa (HR), disminuye significativamente su barrera al oxígeno, por lo que se utiliza como capa central en estructuras multicapa, protegiéndolo así de la humedad .
Al tratarse de un copolímero, sus propiedades dependen de la proporción de etileno y alcohol vinílico. Se pueden encontrar grados comerciales con diferente contenido en etileno: 27, 32, 38 y hasta 44 %. De esta forma, a menor contenido en etileno, se obtienen mejores propiedades barrera al oxígeno, pero, mayor solubilidad en agua .
También se debe tener en cuenta el grado de hidrólisis alcanzado durante el proceso de obtención, pues si el EVOH tiene un elevado grado de hidrólisis presenta una alta resistencia a la humedad y, por tanto, una mayor propiedad barrera al oxígeno que aquellos grados de EVOH con menor grado de hidrólisis
3. Materiales plásticos sostenibles para el envasado de productos hortofrutícolas
Los bioplásticos constituyen una familia de materiales plásticos derivados de materias primas renovables y/o biodegradables.
Los bioplásticos de fuente renovable se obtienen a partir de materias primas de origen natural, reduciendo así la dependencia de materiales de origen petroquímico, es decir, son biobasados (bio-based).
Los bioplásticos biodegradables son aquellos que se descomponen por la acción de los microorganismos. En función del medio y, por tanto, de las condiciones de biodegradación, se distinguen diferentes tipos:
- Biodegradación en suelo
- Biodegradación en medio marino
- Biodegradación en agua dulce.
Además, el concepto de biodegradable engloba el de compostable, ya que un material compostable es aquel que se descompone por la acción de microorganismos y, durante este proceso se liberan nutrientes necesarios para las plantaciones. En función de las condiciones llevadas a cabo para obtener compost a partir de dichos materiales, se distinguen dos tipos:
- Compostabilidad en condiciones industriales. La obtención de compost se lleva a cabo en una planta de compostaje industrial a una temperatura de 58 ºC durante un tiempo máximo de 6 meses.
Envasado sostenible de frutas y hortalizas
- Compostabilidad en condiciones domésticas (Home Compost). La obtención de compost se lleva a cabo a temperatura ambiente (20 – 30 ºC) durante un tiempo máximo de 12 meses.
Por tanto, el concepto de bioplástico puede referirse al origen del material (fuente renovable) como al fin de vida del material (biodegradable).
3.1. Material plástico reciclado
El reciclado de materiales plásticos es un proceso de valorización. Desde el punto de vista de la jerarquía de residuos, el reciclado se sitúa en el tercer eslabón tras la prevención y la reutilización.
Existen dos tipos de reciclado: mecánico y químico. El reciclado mecánico consiste en aplicar temperatura y cizalla para obtener para obtener el material reciclado. En este proceso, no hay ruptura de la cadena polimérica, excepto por la degradación debida al propio tratamiento. En este caso, se pueden distinguir dos tipologías de material reciclado: post-consumo y, postindustrial, que son las mermas de material que se generan en la industria.
Por otro lado, el reciclado químico se basa en la ruptura de la cadena polimérica, de manera que lo que se obtienen son los monómeros de partida para la obtención de polímeros. En este caso, las propiedades físico-mecánicas del material obtenido son las mismas que el material virgen. Este tipo de reciclado es especialmente interesante para plásticos mezclados donde el reciclado mecánico está limitado actualmente.
Actualmente, el reciclado mecánico es el más utilizado para la obtención de material plástico reciclado. Esto se debe a su menor consumo energético y a que existen un gran número de empresas recicladoras de plástico. En la Tabla 6 se muestra la cantidad que se recicla de cada material plástico, así como el número de empresas recicladoras en España.
Tabla 6. Material plástico reciclado en España en 2018
Sin embargo, actualmente, el material plástico reciclado proveniente del reciclaje mecánico que está aprobado para su uso en contacto directo con alimentos es el PET procedente del reciclado de botellas, ya que es un circuito cerrado de reciclaje, por lo que se puede asegurar la trazabilidad. Y, cualquier material plástico reciclado proveniente del reciclaje químico se puede utilizar para su uso en el envasado de alimentos.
3.2. Material plástico de origen renovable
Los materiales plásticos de origen renovable poseen la misma estructura química que los materiales plásticos convencionales y, por tanto, poseen las mismas propiedades físicomecánicas que su homónimo plástico convencional y, se deben tratar igual al final de su vida www.bibliotecahorticultura.com útil. Sin embargo, se obtienen a partir de materias primas renovables, por lo tanto, se tratan de bioplásticos. A continuación, se describen los bioplásticos de origen renovable que se podrían utilizar para el envasado de productos hortofrutícolas.
- Bio-PE. La fabricación de este material se realiza actualmente a partir de bioetanol. El bioetanol se obtiene principalmente de la caña de azúcar, aunque también se puede obtener a partir de la remolacha, almidón de maíz, trigo u otros granos. De dichas materias primas, se extrae la sacarosa, que es fermentada para la obtención de bioetanol. A partir del bioetanol se produce etileno que, finalmente se polimeriza para obtener polietileno.
- Bio-PP. Existen diferentes rutas para la obtención de polipropileno de origen renovable, como por ejemplo la fermentación de azúcares para la obtención de propileno, el monómero del PP. Sin embargo, a diferencia del Bio-PE, este material no se produce actualmente en grandes volúmenes.
- Bio-PET. Las materias primas empleadas para la obtención de PET: etilenglicol y, ácido tereftálico purificado (PTA) o dimetil tereftalato (DMT) se pueden obtener a partir de fuentes naturales. Por un lado, el etilenglicol se puede obtener a partir de sorbitol, o bien, a partir de etileno que, a su vez, se puede obtener a partir de biomasa. Y, por otro lado, el ácido tereftálico (PTA) se puede obtener a partir del ácido 2,5-furandicarboxílico (FDCA), cuyo origen es biogénico.
- Bio-PA. Existen diferentes rutas para la producción de poliamidas a partir de recursos renovables, sin embargo, desde el punto de vista comercial no todas estas rutas son viables debido a los altos costes de producción. En la Tabla 7 se muestran las poliamidas que se pueden obtener a partir de materias primas renovables. Sin embargo, actualmente las bio-poliamidas comercializadas son la PA11, de origen 100 % renovable y, PA610 de origen parcialmente renovable.
Tabla 7. Bio-poliamidas y materia prima de fuente renovable utilizada para su obtención
Poliamida Monómero
PA 66
Hexametilendiamina
Ácido adípico
PA 6 ε-caprolactama
PA 11 Ácido 11- aminoundecanoico
PA 610
PA 69
PA 46
Hexametilendiamina
Hexametilendiamina
Tetrametilendiamina
Ácido adípico
Materia prima renovable
Butadieno, propileno
Glucosa
Glucosa
Aceite castor
Butadieno, propileno
Butadieno, propileno
Acrilonitrilo y HCN
Glucosa
PA 36 Ácido dímero Ácidos oleico y linoleico
3.3. Material plástico biodegradable
Los materiales plásticos biodegradables son aquellos que se descomponen por la acción de los microorganismos, pudiendo ser su origen de fuente fósil o de fuente renovable. A continuación, se detallan los plásticos biodegradables más utilizados para el envasado de productos hortofrutícolas.
Ácido poliláctico (PLA)
Envasado sostenible de frutas y hortalizas
El PLA es un polímero termoplástico biodegradable y de origen renovable. Se obtiene por polimerización del ácido láctico y, éste, a partir de la fermentación bacteriana de polisacáridos presentes en el maíz, remolacha, trigo u otros productos ricos en almidón. Aunque el ácido láctico también se puede obtener por síntesis química, la ruta fermentativa es la más utilizada actualmente para la obtención de ácido láctico. Se trata de un poliéster lineal cuya estructura química se muestra en la Figura 10.
El peso molecular, la estructura macromolecular y el grado de cristalización del PLA depende de las condiciones de polimerización, sin embargo, por lo general presenta una temperatura de transición vítrea de 60 ºC y una temperatura de fusión de 150 ºC. En cuanto a sus propiedades físico-mecánicas, son comparables a las del PET.
Polihidroxialcanoatos (PHAs)
Los polihidroxialcanoatos constituyen una amplia familia de polímeros biodegradables y, de origen renovable, ya que se obtienen de la fermentación bacteriana de azúcares o lípidos. Estos polímeros se acumulan en el interior de los microorganismos en forma de gránulos como reserva de carbono y energía cuando hay limitaciones nutricionales en el medio de fósforo, nitrógeno y magnesio, entre otros, y hay un exceso de fuentes de carbono. El número aproximado de gránulos de PHA por microorganismo es de 8 – 10 con un peso molecular de entre 2·105 – 3·106 Daltons. Estos gránulos de PHA (Figura 11) pueden llegar a representar hasta un 90 % del peso total en seco del microorganismo.
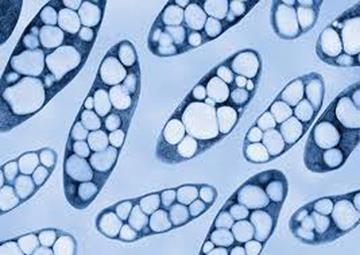
Los PHAs son poliésteres lineales de diferente longitud de cadena. En la Figura 12 se muestra su estructura química general.
www.bibliotecahorticultura.com
Dentro de esta familia de polímeros, los más comercializados actualmente son el poli (3hidroxibutirato) o PHB y, el copolímero polihidroxi(buterato y valerato) o PHBV. Los PHAs tienen una baja temperatura de transición vítrea, variando de -6 a 10 ºC dependiendo del tipo de PHA y, la temperatura de fundido varía de 135 – 180 ºC. Además, los PHAs destacan por su elevada rigidez y fragilidad y, por una baja permeabilidad al vapor de agua. Sin embargo, el copolímero PHBV presenta una mejor procesabilidad, resistencia al impacto y flexibilidad a mayor porcentaje de valerato.
Alcohol polivinílico (PVOH)

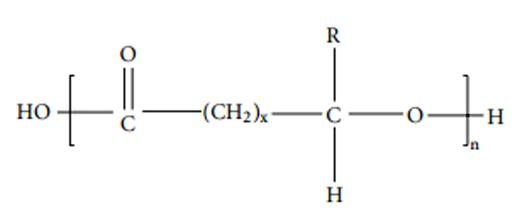
El alcohol polivinílico es un polímero termoplástico biodegradable y de origen fósil. En la Figura 13 se muestra su estructura química.
El PVOH es, actualmente, uno de los polímeros solubles en agua con mayor volumen de producción. Se fabrica comercialmente por hidrólisis de acetato de polivinilo, por lo que este polímero se puede encontrar parcial o completamente hidrolizado. Por lo tanto, las propiedades del PVOH dependen de su grado de polimerización e hidrólisis.
Los grados parcialmente hidrolizados tienen una temperatura de fusión de 180 – 190 ºC, mientras que, los grados totalmente hidrolizados tienen una temperatura de fusión de 230 ºC. Además, al igual que el EVOH, a mayor grado de hidrólisis, menor solubilidad en agua tiene el PVOH y, por tanto, mejor propiedad barrera al oxígeno presenta.
Por lo general, se trata de un polímero muy soluble en agua, que destaca por sus excelentes propiedades barrera al oxígeno. Debido a su alta solubilidad en agua, tiene tendencia a hidrolizarse rápidamente produciendo una disminución en sus propiedades mecánicas, por lo que debe ser protegido de la humedad en estructuras multicapa.
Bioplásticos basados en almidón
El almidón natural es un polisacárido que se encuentra en semillas, legumbres, cereales, patatas, bellotas y castañas. Se trata de un polímero natural formado por dos tipos de moléculas: la
Envasado sostenible de frutas y hortalizas amilosa que es un polímero lineal y, la amilopectina que es un polímero de estructura altamente ramificada. La ratio amilosa/amilopectina varía según el origen botánico del almidón, pero, por lo general, contienen un 15 – 30 % de amilosa y un 70 – 85 % de amilopectina. Para que el almidón nativo se pueda procesar mediante tecnologías de transformación de plásticos convencionales, es necesario destructurizar el almidón por aplicación de temperatura y cizalla y, plastificación de este por adición de plastificantes. Se obtiene así el almidón termoplástico (TPS, Thermoplastic Starch). Las propiedades físico-mecánicas del TPS dependen del origen botánico del almidón, así como del tipo y concentración de plastificante utilizado.
Bioplásticos basados en celulosa
La celulosa es el polímero natural más abundante en la naturaleza. Se trata de un polisacárido lineal de origen vegetal. Para que la celulosa se pueda procesar mediante tecnologías de transformación de plásticos convencionales, se modifica dando lugar a ésteres y éteres de celulosa, además, se utilizan plastificantes para la obtención de materiales poliméricos celulósicos. Las propiedades físico-mecánicas dependen de la tipología de polímero celulósico, así como del tipo y concentración de plastificante utilizado.
4. Tipologías de envase plástico para productos hortofrutícolas en este sentido, los envases juegan un papel fundamental para que el producto llegue en perfectas condiciones hasta el consumidor final y así no generar costes económicos adicionales ni desperdicio alimentario.
Cada tipo de producto hortofrutícola tiene unas necesidades de envasado diferentes y, por lo tanto, será necesaria una tipología de envase distinta (rígido, semirrígido o flexible). Además, dependiendo de la cadena de suministro, será necesario el uso, no solo del envase primario, es decir, aquel que está en contacto con el alimento, sino que será necesario el uso de envases secundarios y terciarios. En este sentido, los productos hortofrutícolas son una parte muy importante dentro del sector del envase alimentario.
4.1. Envases primarios, secundarios y terciarios
Según el tipo de material con el que estén fabricados los envases se clasifican en: www.bibliotecahorticultura.com
- Envases primarios: son aquellos que están en contacto directo con el producto o su contenido. Su función es proteger, contener y conservar los productos. También hay que tener en cuenta que este tipo de empaquetado resulte atractivo puesto que, será la imagen de la marca y, por tanto, la imagen que recibe el cliente. Ejemplos de embalaje primario serían las barquetas de plástico para el envasado de frutas y verduras, las botellas para zumos o las bolsas para el envasado de verduras lavadas y cortadas.
- Envases secundarios: contiene uno o varios primarios. Es un refuerzo del envase primario para facilitar su transporte y tratamiento, pero también puede ser utilizado para ofrecer el producto al público, o a los clientes, como ocurre en los supermercados o grandes superficies comerciales. Un ejemplo de ello serían las cajas de carga, para almacenamiento o transporte. Aunque también están dentro de este nivel las cajas plegables, el cartón corrugado, etc.
- Envases terciarios: envuelven al envase primario y secundario para protegerlos y que no se dañen, son envases de alta resistencia. Debido a esta responsabilidad, este tipo de formato ha de estar hecho con material resistente, aquí podemos incluir los diferentes tipos de cartón ondulado donde existen varios grosores, o los contenedores de madera. También podemos incluir como embalaje terciario algunos productos como los propios pallets, las cantoneras, el film retráctil y todos aquellos elementos que permitan mantener una estructura unitaria de una carga para el transporte o el almacenamiento de los productos.
Los envases secundario y terciario tienen que cumplir menos requerimientos técnicos que los primarios. Estos deben tener buenas propiedades mecánicas que permitan, sobre todo, el apilamiento de los mismos sin deformación, y deben proteger el envase primario durante su transporte y almacenamiento. Sin embargo, en el caso de los envases primarios, estos deben de cumplir mayores requerimientos técnicos (propiedades mecánicas, químicas, de barrera a gases y/o líquidos, legislación para el contacto alimentario, etc.), por ello, existen diferentes tipos de envases en función del alimento a envasar y los mecanismos de degradación.
4.2. Envases rígidos y semirrígidos
Los envases se pueden clasificar atendiendo a su constitución en envase rígido, semirrígido y flexible.
Envases rígidos
Se entiende por envase rígido, aquel que tiene una forma definida no modificable, esto posibilita el envasado de productos, sin que estos sufran daños. Entre sus ventajas cabe destacar:
- Utilizan las líneas de envasado tradicionales.
- Son resistentes a golpes, pérdidas y deterioros, en general y se pueden apilar.
- Facilitan la manipulación y la preparación de pedidos.
- Mantienen el vacío y son resistentes a la luz y al oxígeno.
Por el contrario, suelen tener un peso mayor que los semirrígidos y los flexibles, y por consiguiente su precio es mayor.
Los procesos de transformación de plásticos utilizados para la obtención de envases rígidos son el proceso de moldeo por inyección, el proceso de inyección-soplado y el proceso de extrusión soplado de cuerpo hueco (SCH).
El moldeo por inyección es uno de los procesos de transformación más utilizados en la industria del plástico. Se trata de un proceso a partir del cual pueden obtenerse piezas acabadas con la forma y características deseadas a partir de material plástico en forma de granza. Consiste en introducir el material plástico fundido, a presión, en un molde y enfriar el material hasta conseguir copiar la pieza, es decir, la materia prima se puede transformar en un producto acabado en un solo paso, además, se pueden obtener piezas de peso variado y con geometrías complicadas.
El equipo de inyección está formado por dos elementos; la unidad de inyección del plástico y la unidad de moldeo.
Envasado sostenible de frutas y hortalizas www.bibliotecahorticultura.com
- La unidad de inyección: es la encargada de fundir e inyectar los materiales. Está formado por un cilindro que está conectado en uno de sus extremos a una tolva por donde se introduce el material. Dentro del cilindro, hay un husillo, donde se mezcla y calienta el polímero y también actúa como un émbolo que mueve rápidamente el material fundido hacia el molde.
- La unidad de moldeo: sirve para abrir, cerrar el molde y expulsar la pieza. Consiste en dos placas, una fija y otra móvil y un mecanismo para accionar la placa móvil. El mecanismo consiste en una prensa operada por un pistón hidráulico o por dispositivos mecánicos articulados.
Las partes de la máquina de inyección se detallan en Figura 14.
El moldeo por inyección comienza con la alimentación de los pellets mediante una tolva colocada en el punto de entrada del material. Luego, los pellets se calientan, se funden y se plastifican por medio de calor y cizalla. Después, el material es forzado a través de la boquilla de la unidad de inyección, a continuación, pasa a un canal en el molde llamado bebedero y luego se distribuye por unos corredores ramificados en la cavidad del molde, Una vez entra el material en el molde, este se enfría y solidifica copiando la forma. Una vez que el material se enfría y se endurece, el molde se abre y la pieza moldeada se expulsa del mismo.
Es importante que el material fundido se distribuya de manera uniforme en todo el molde, ya que muchas veces hay más de una cavidad dentro del molde, que permite la producción de más de una pieza a la vez. Es por esto, que la geometría de los moldes debe diseñarse de manera cuidadosa.
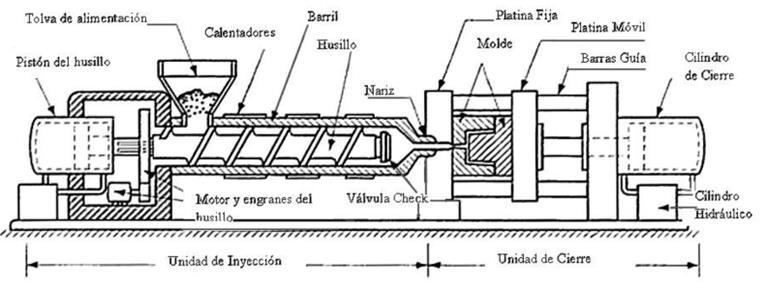
Si bien el moldeo por inyección es adecuado para la producción en masa, es necesario controlar diversas condiciones, como la temperatura, la velocidad de inyección, presión, calidad del material, entre otros.
Las fases del proceso se muestran en la Figura 15.
Los materiales más utilizados en el proceso de moldeo por inyección son: polietilentereftalato (PET), polipropileno (PP), polietileno (PE) y poliestireno (PS), siendo el PET el material más utilizado de todos ellos para la obtención de botellas principalmente.
Otro de los procesos de transformación del plástico para la obtencion de envase rígido es el proceso de inyección-soplado
Hoy en día es el tercer método más empleado en el procesado de plásticos. Durante muchos años se empleó casi exclusivamente para la producción de botellas y botes. Sin embargo, los últimos desarrollos en el proceso permiten la producción de piezas de geometría con mayor complejidad, espesor de pared variable, dobles capas, etc. Este proceso está pensado para su uso en la fabricación de productos de plástico huecos y entre sus principales ventajas podemos destacar:
- Su capacidad para producir formas huecas sin la necesidad de tener que unir dos o más partes moldeadas por separado.
- Buen control de espesor de las piezas
- Buena transparencia y propiedades mecánicas y de barrera.
- No se producen recortes.
- Amplia variedad de materiales (a diferencia de extrusión-soplado)
Sin embargo, por contra, sólo se puede emplear para piezas relativamente pequeñas, no se pueden incluir asas (a diferencia de extrusión-soplado) y el coste de producción es mucho mayor.
Es un proceso que combina dos tecnologías, primero se obtiene la preforma mediante inyección. La preforma se enfría de forma rápida para evitar la cristalización del material y así evitar la aparición de zonas opacas. Un material procesado de esta forma es mucho más tenaz y resistente que él mismo amorfo o cristalino. A continuación, el polímero debe recalentarse a una temperatura superior a su Tg (temperatura de transición vítrea). Una vez que se alcanza esta temperatura se introduce el aire en la pieza y esta copia el molde.

Envasado sostenible de frutas y hortalizas
El polímero que más se emplea en este proceso es el PET. Otros polímeros como el policloruro de vinilo (PVC), copolímero acrilonitrilo (SAN), poliacrilonitrilo (PAN), poliamida (PA) o polipropileno (PP) también presentan un buen comportamiento en este proceso, sin embargo, el PET se emplea, con preferencia, en los millones de botellas de bebidas que se fabrican diariamente.
Figura 16. Ejemplo de botella y su preforma
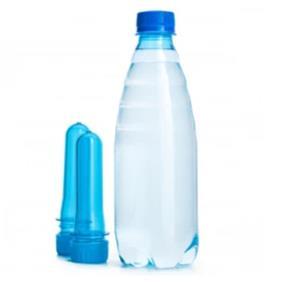
Hay dos tipos de procesos, el denominado “integrado” y el de “dos etapas”: www.bibliotecahorticultura.com
- Integrado o continuo: La fase de inyección y la de soplado forman parte de la misma máquina. Las preformas producidas en la fase de inyección son llevadas mediante un sistema transfer, tipo revolver y son introducidas o depositadas en el molde. Este sistema es utilizado en series cortas de producción y en envases de poco volumen.
- Dos etapas o recalentado: En esta técnica el material en estado fundido se inyecta a través de una o varias boquillas en un primer molde, formando un cuerpo hueco, denominado "Preforma". Esta se enfría hasta temperaturas en las que el material es todavía moldeable y se encierra en los semimoldes que darán lugar a la forma del envase. La preforma es soplada con aire a presión y se estira. Cuando toca el molde el material se enfría adquiriendo la forma definitiva, obteniendo así la botella. Este proceso, ha supuesto grandes ventajas como el ahorro de costes logísticos, ya que, evita el transporte de botellas llenas de "aire“.
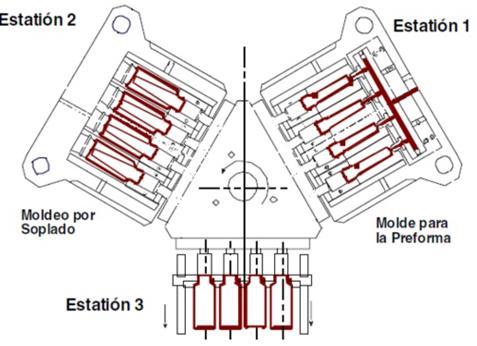
Otro proceso de transformación del plástico que puede ser utilizado para la obtención de envases rígidos hortofrutícolas, principalmente botellas, es el proceso de Extrusión Soplado de Cuerpo Hueco (SCH). En este caso los materiales utilizados son principalmente poliolefinas (PP y HDPE) y, también se puede utilizar PET, aunque es más común la obtención de botellas por inyección-soplado. El PP destaca sobre todo para el envasado de productos que necesiten ser pasteurizados o productos de llenado en caliente como, por ejemplo, los zumos.
El proceso de extrusión soplado consiste en formar un objeto hueco llamado parison, a partir de un termoplástico fundido. Cuando el tubo tiene las dimensiones adecuadas es atrapado por el molde. Se inserta una aguja, a través de la cual entra aire y expande el parison haciendo que se pegue sobre las paredes del molde adoptando su forma.

Las etapas del proceso son las siguientes:
- Apertura del molde y extrusión del parison a través de una boquilla, que generalmente es circular, pero puede variar en función de la geometría de la pieza a soplar. Una característica muy importante es la resistencia en fundido del material, ya que, si esta es muy baja pueden darse problemas de descuelgue, y la relación de espesores a lo largo de la pieza puede verse afectada.
- Cierre del molde.
- Inserción de la aguja y soplado mediante aire a presión. En algunos casos esta presión puede ir variando en función del tiempo, según los requerimientos de la pieza.
- Enfriamiento de la pieza, se disipa el calor de la masa fundida por ambas partes del molde y la pieza se enfría rápidamente. Las diferencias de espesores en el envase son críticas en el proceso de enfriamiento, pudiéndose originar zonas con diferente cristalinidad. Esta variabilidad puede dar lugar a contracciones en diferentes partes del envase (botella).
- Apertura del molde.
- Expulsión de la pieza.
- Eliminación de rebabas, ya que, cuando se cierra el molde parte del parison es aplastado, creando rebabas. La calidad de la línea de unión es muy importante, ya que, esta zona es punto débil del producto final.
Envasado sostenible de frutas y hortalizas
La ventaja de este proceso de obtención de botellas es que el envase se mantiene cerrado por la generación de rebabas hasta el envasado del alimento, por lo que se disminuye el riesgo de posible contaminación del interior del envase.
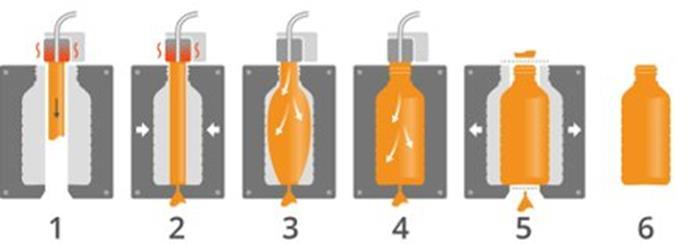
Envases semirrígidos
Los envases semirígidos son aquellos envases que tienen una resistencia a la compresión menor a la de un envase rígido.
Los envases semirrígidos se obtienen mediante dos procesos, el primero de ellos es extrusión de lámina plana, donde el objetivo es obtener una lámina de un espesor aproximado entre 350550 micras, que luego será termoconformado para la obtencion del envase. El proceso de extrusión de lámina plana consiste en la obtención de longitudes ilimitadas de producto con una sección transversal constante. El material fundido es obligado a pasar a través de una boquilla con la forma de la sección que se desee obtener, bajo condiciones controladas de presión y temperatura. Se trata de un proceso continuo que requiere de un sistema de control, donde la forma del producto extruido la confiere la geometría de la boquilla empleada.
Una línea de extrusión consta principalmente de los siguientes componentes: www.bibliotecahorticultura.com
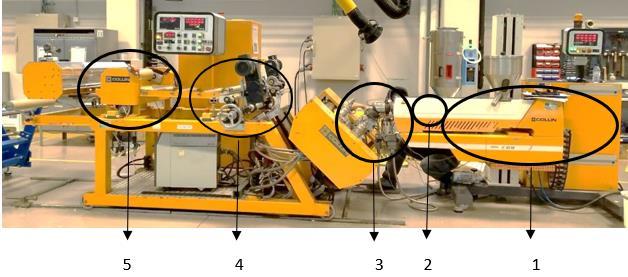
Los pellets del material se introducen en la extrusora mediante una tolva y estos pasan directamente por el husillo, el cual su función es transportar el material desde la tolva, plastificarlo y dosificarlo con presión suficiente para llenar la boquilla. El diseño del husillo consta de tres zonas: alimentación, compresión y dosificación.
El calentamiento se produce de forma gradual para evitar la degradación del polímero, ya que también hay una aportación de calor por la intensa fricción que tiene lugar en el interior de la camisa. El giro del husillo fuerza a la granza a avanzar por el cilindro, calefactado por una serie de resistencias a la temperatura de fusión deseada para el material. La presión generada fuerza al polímero, que es empujado hacia la boquilla.
Los parámetros de entrada en la extrusora son: perfil de temperaturas y la velocidad de extrusión y los parámetros de respuesta son: temperatura de fundido, par motor y presión de fundido.
En función del producto a envasar, puede que un solo material no cumpla con todos los requerimientos técnicos para el envasado de dicho producto, por ello, se pueden obtener lo que se conocen como estructuras multicapa, es decir, films obtenidos por combinación de dos o más materiales. Los procesos mediante los cuales se pueden obtener estructuras multicapa son: laminación (unión de materiales mediante adhesivos) y co-extrusión.
La coextrusión permite unir hasta 3,5, 7 y hasta 9 materiales. En este proceso los materiales son extruidos simultáneamente, cada uno de ellos en una extrusora diferente, y la principal diferencia con un proceso de extrusión monocapa radica en el diseño del cabezal. Existen dos métodos para producir estructuras poliméricas multicapa.
Cabezal multicanal cada uno de los materiales llega por separado a su correspondiente canal en el cabezal, allí se distribuye en los porcentajes deseados y se combina con el resto de las capas, justo antes de la salida. Este método permite combinar materiales con temperaturas e índices de viscosidad diferentes. En el caso del cabezal monocanal cada extrusora está conectada a una entrada del bloque de reparto, el cual tiene la función de formar la configuración final de las capas. Así, la estructura multicapa se forma antes de llegar al cabezal, dentro del bloque, y con los diferentes flujos dispuestos según una estructura plana multicapa se alimenta el cabezal. El cabezal lo distribuye en todo su ancho para obtener a la salida una lámina del ancho deseado y con la configuración de capas deseada.
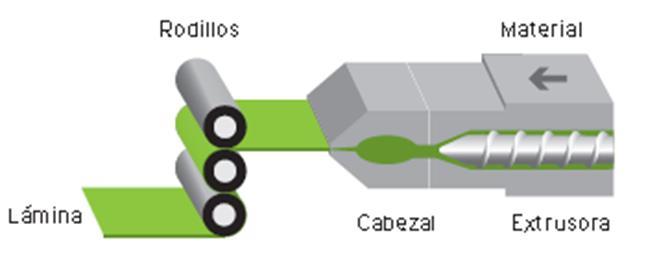
Envasado sostenible de frutas y hortalizas
Una vez se obtiene la lámina plana con el espesor adecuado en función del diseño del envase final, esta es termoconformada.
El termoconformado consiste en el moldeo de películas o láminas de materiales termoplásticos mediante la aplicación de calor y presión. Durante el proceso, la lámina es estirada de modo que se reduce su espesor original resultando una mayor área superficial.
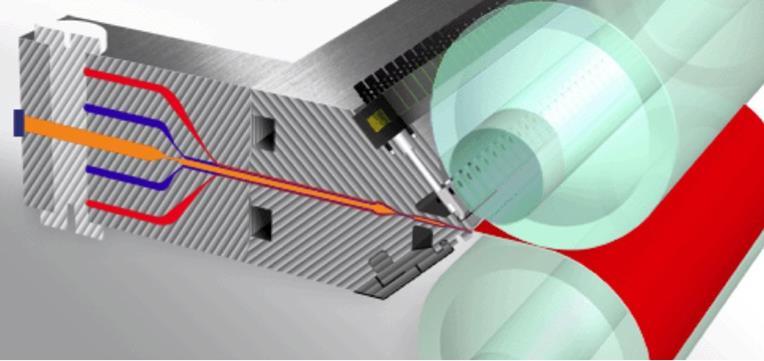
El material se calienta hasta el intervalo de temperatura específico en el que presenta las mejores propiedades de elasticidad, y posteriormente, se realiza el moldeo por vacío, por aire comprimido, por medios mecánicos, o combinando estas técnicas. A continuación, la lámina conformada se deja enfriar el tiempo necesario para que se copie correctamente la forma del molde y adopte dicha forma.
Etapas del proceso de termoconformado:

- Calentamiento
- Conformado de la pieza
- Enfriamiento
- Desmoldeo
El proceso de termoformado se puede emplear en plásticos reciclados y reciclables, como por ejemplo el PET. Esta puede ser usada tanto para la obtención de piezas plásticas de grandes www.bibliotecahorticultura.com superficies, como en la industria automóvil, embarcaciones, paneles interiores de electrodomésticos y construcción, por su puesto para la obtención de envases alimentarios, como, por ejemplo, barquetas para frutas o verduras, vasitos de yogur, hueveras, tarrinas de mantequilla, comida para llevar, etc.
4.3. Envases flexibles
Los procesos de transformación para la obtención de envases flexibles son principalmente extrusión de lámina plana y extrusión film soplado.
El proceso de extrusión de lámina plana ha sido explicado en el apartado anterior En este caso, las diferencias del proceso radican en el espesor de la lámina, ya que, los espesores de la lámina para termoconformado son superiores a los que se obtienen para envase flexible. Como se han comentado en el apartado anterior, si fuera necesario la unión de varios materiales para obtener un film multicapa con unos requerimientos deseados, se recurriría a la co-extrusión o a la laminación.
El proceso de extrusión soplado es el método más utilizado para la fabricación de films. Más de la mitad de los films producidos hoy en día se hacen de polietileno, en su mayoría de baja densidad. El polipropileno es otro de los materiales ampliamente utilizados.
El proceso consiste en extruir un tubo de termoplástico a través de una boquilla anular, para hincharlo con aire hasta varias veces su diámetro inicial, formando un producto tubular que se llama globo o burbuja, y que, tras ser enfriado, puede recogerse en forma de film doble o tubo, o bien puede cortarse por los laterales dando lugar a dos films que se separan y se bobinan de forma independiente.
El proceso induce un estiramiento del film tanto en la dirección longitudinal como en la transversal, lo que confiere unas propiedades, principalmente mecánicas, mejoradas respecto a los films obtenidos por extrusión de lámina plana.
Los principales componentes de una línea de extrusión de film soplado estándar son:
- Extrusora
- Cabezal
- Unidad enfriamiento
- Unidad de calibración
- Torre de soplado
- Unidad de arrastre - Unidad de bobinado
Al igual que la extrusión de lámina plana, en extrusión de films soplado se pueden obtener films multicapa mediante co-extrusión de film soplado.
4.4 Envases utilizados en sector
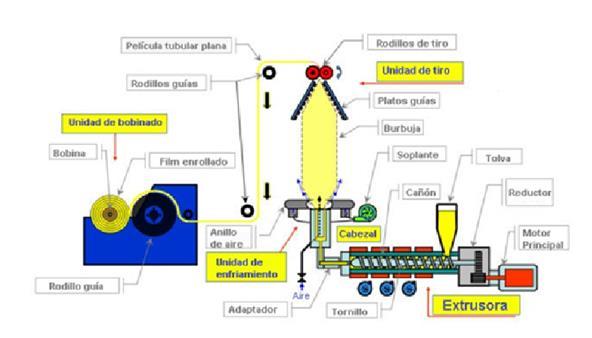
A continuación, en la siguiente tabla se recogen aquellos envases (rígidos, semirrígidos y flexibles) más usados en el envasado de productos hortofrutícolas.
Envasado sostenible de frutas y hortalizas www.bibliotecahorticultura.com
Botella transparente
Zumos naturales / pasteurizables
Inyección-soplado y/o Extrusión Soplado de Cuerpo Hueco (SCH)
PET rPET
PET pasteurizable PP HDPE
Aunque hasta hace unos pocos años estos productos se envasaban en tetra-brick la tendencia es hacerlo en botellas de PET, ya que es un material fácilmente reciclable
Estructuras de 2 capas: PA/PE, PET/PE
Estructuras de 3
Tarro pasteurizable
Zumos, encurtidos, café, frutos secos, etc.
Laminación y coextrusión capas: PET/Al/PE o PP
PET/PET/PE,
PA/PET/PE
PET/PE/Al/PET/PE
Dependiendo de los requerimientos de envasado del alimento se seleccionará la estructura de envasado. Ventajas respecto a otros envases rígidos, menos uso del material
Frutas y verduras procesada salsas, mermeladas y encurtidos Moldeo por inyección PET reutilizable Sustitución de los envases de vidrio
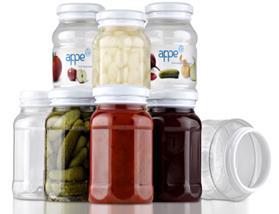
Envasado sostenible de frutas y hortalizas
Barqueta
Frutas y verduras frescas y procesadas (cortadas)
Lamina plana / termoconformado
PET rPET
En algunos casos se está cambiando la bandeja de PET por bandejas de cartón
Ensaladas listas para consumir Lámina plana / termoconformado
PET rPET
PLA
Barqueta
Frutas y verduras frescas
Extrusión lámina y termoconformado
PS
PS bio-degradable

PS espumado www.bibliotecahorticultura.com
Tarrina Salsas
Extrusión lámina y termoconformado/Moldeo por inyección
4. Materiales plásticos convencionales, renovables y reutilizables
Mallas
Bolsa
Bolsa congelados
PP Se envasan en atmosfera modificada www.bibliotecahorticultura.com
Frutas, verduras, tubérculos y hortalizas Extrusión PE, PLA
Verduras y ensaladas Extrusión film soplado
Todo tipo de verduras Coextrusión film soplado PE/PA