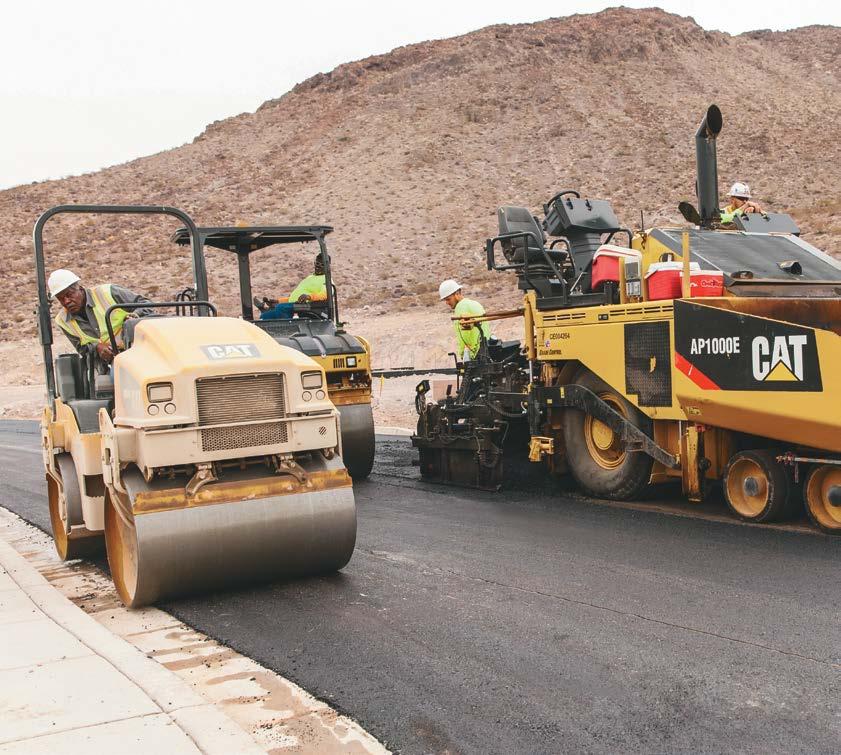
7 minute read
A Seamless Mat
SEAMLESS A MAT
CREW ALL BUT ELIMINATES COLD LONGITUDINAL JOINTS
Advertisement
Tom Hart has been working with asphalt for decades—ever since his “summer job” became a career.
During that time, he has worked with crews that have placed millions of tons. Hart personally put down much of the material, and to this day still steps in and operates the equipment when needed—though he is officially Vice President of Paving at American Pavement Preservation, a Las Vegas-based contractor. Hart has learned several lessons over time. Two of the biggest: 1. The site work done before paving can make your job easy—or almost impossible.
2. Extra effort and creativity can nearly eliminate cold joints.
Residential work
American handles a variety of jobs in the Las Vegas area, including a high volume of residential work. “Over the last few years, we’ve probably done 50 percent of all the residential work in the Las Vegas area,” Hart said. It’s substantial business, as the area’s once-decimated housing market has made a strong recovery.
In the broadest sense, Hart believes residential work is less challenging than commercial. “There is a lot of drainage to contend with when working with commercial,” he said. “With residential, you usually start at point A and end at point B.”
That’s when all goes well, which of course doesn’t always occur in the paving world. Hart recently was reminded of this—not that he needed a refresher—while paving new roads in a subdivision. Although the project didn’t have the high tonnages seen on some production jobs, it does show how a contractor and crew must adapt.
Poor grade
Hart visited the subdivision ahead of the paving crew and quickly spotted problems. “I knew it was going to be a challenge,” he said. “The grading contractor had some issues. He just couldn’t get the grade down properly.”
More thorough surveying showed the site was off grade and inconsistent from start to finish. American crews met the challenge by running gravel through the Cat ® AP1000E Asphalt Paver. The aggregate was placed using Cat Grade and Slope technology, ensuring the grade requirements would be met.
“I’ve done that on several jobs,” Hart said of placing type 2 aggregate with the paver to achieve the proper grade. “It’s the
TOM HART VICE PRESIDENT OF PAVING AMERICAN PAVEMENT PRESERVATION “ It looks like a single mat. It’s as close as you can get to not having a longitudinal joint.
”

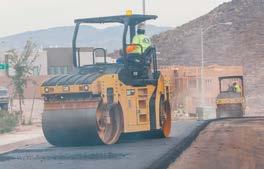
quickest way to reach grade. We actually process the gravel, adding the correct moisture, and enddump into the paver. We run the automatics off the curb and gutter.” American placed 1,500 tons of the aggregate on a Monday and paved the next day.
Placing the asphalt
When it was time to pave, the AP1055E went back to work. Most residential streets require lifts of only 50-75 mm (2-3 in). The exterior roads, those providing the main access to the subdivision, often are 100-175 mm (4-7 in) deep. “Anything more than 4 inches is handled in multiple lifts,” Hart said. Slight grade variances are easily corrected during paving, using the grade and slope control. “All the automatics, the grade and slope, help with quality,” Hart said. The firm also takes other quality-assurance steps, including

continuous paving. Another detail: The paver operator makes sure he or she initiates the contact with the truck, instead of the truck backing into the paver. “That contact can cause a bump,” Hart said.
No cold longitudinal joints Perhaps the biggest factor in achieving quality and smoothness is the way American crews handle longitudinal joints.
Streets in new subdivisions are typically 9.7-11 m (32-36 ft) wide. Many paving crews would make two passes, starting at one end and working as far forward as they could, then returning to make a second pass and leaving behind a cold joint.

American crews instead make three passes, and straddle the crown during the middle run. “With the Extend-A-Mat, you can break the screed in the middle to get that crown where you want it,” Hart said. American paves in narrower widths to all-but-eliminate the cold longitudinal joints. “It looks like a seamless mat,” Hart said.
American crews usually move about 152 m (500 ft) from the starting point in the right lane. Then they stop, back up and place the middle section next to the first. The third run, in the left lane, begins at the same starting point. The paver then works that 152 m (500 ft), as did the two previous passes. But during the third pass, the paver continues for another 152 m (500 ft) before stopping, backing up and placing the next middle section of 152 m (500 ft).
Next the paver works in the right lane, at a length of 304 m (1000 ft).
ELIMINATING COLD LONGITUDINAL JOINTS As seen from above
3.7 m (12 ft)
3.7 m (12 ft)
3.7 m (12 ft)
PAVER DIRECTION 2
1
3
ORDER OF PASSES
4
5
It covers the same length of the previous passes, and then continues on to become the first paved area of the next section.
Rollers compact the first pass, but leave about 150 mm (6 in) unrolled. When the middle pass is placed, the operators cover that 150 mm (6 in) and the remainder of the mat up to the next edge, where they leave a few inches uncompacted.
That area is then rolled and pinched when the third pass is placed. That means the mat and longitudinal joints have been compacted while still hot. “It looks like a single mat,” Hart said. “It’s as close as you can get to not having a longitudinal joint.”
There is a cold transverse joint, but it is minimal. “At the 500 foot mark, we roll and trim the edge with a loader,” Hart said. “Instead of having a 1,000-foot-long cold joint, I have a 24-foot-wide cold joint.”
Temperatures matter
A close eye is kept on the plant— on the subdivision jobsite it was about 20 km (12 miles) away—to ensure material flows consistently. Crews monitor temperatures in their efforts to create the “single mat.” The mix arrives at a temperature of about 132-149º C (270-300º F), and is close to 132º C (270º F) behind the paver. The asphalt temperature is not allowed to cool below 77º C (170º F) before the adjacent mat is placed to ensure the joint is hot enough for proper compaction.
American often uses two vibratory drum and two pneumatic rollers, followed by a finish roller. Breakdown rollers make two full vibratory passes in both directions and usually achieve compaction of 85-87 percent. Pneumatics increase the compaction to 91 percent, and the finish rollers typically squeeze another 1 to 3 percentage points. They typically work at about 82º C (180º F) and rarely operate on a mat with a temperature below 77º C (170º F).
There are production goals, too. Crews try to place 145 metric tons (160 U.S. tons) per hour, while also “eliminating” the joint.
“I’ve worked on much higher production jobs, and we can do that type of work,” Hart said. In fact, he once had two crews place 9,435 metric tons (10,400 U.S. tons) in a 10-hour period. “With the residential work, we’re trying to achieve some production, but we’re most concerned about delivering very high-quality, eye-appealing work.” ■
ALL CAT LINEUP
American has been purchasing Cat pavers since 1999. “Our fleets are now 100 percent Caterpillar,” Hart said. “They’re great products, and Caterpillar and the dealership, Cashman Equipment, stand behind them.”
Hart previously ran some competitive products, but now runs only Cat pavers and rollers. “There’s nothing out there that compares to a Cat paver,” Hart said. He also likes the rollers—his fleet includes Cat CB34B and CB44B Tandem Vibratory Rollers—and is pleased to have all his needs met by Cashman Equipment.
6 7