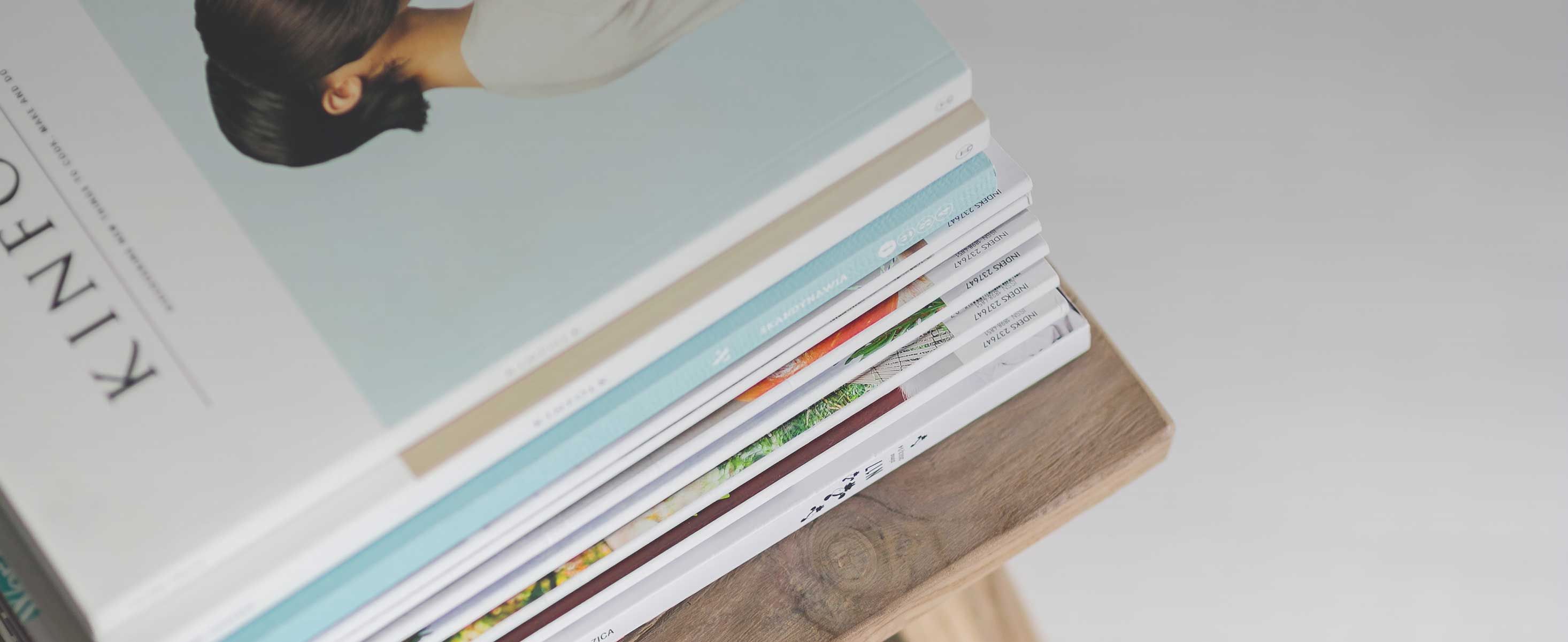
3 minute read
Service procedures
from Volvo Penta TD1030ME VE TWD1030ME TWD1031VE TAD1031GE TAD1231GE TWD1231VE TAD1232GE Workshop Manual
Boost pressure, checking
Special tools: 6065, 6223(TAD), 6591 (TWD)
1
Fit the nipple 6223 (6591) in the existing socket in the inlet pipe. Connect manometer 6065
TAD-engines
TWD-engines
2
Measurement shall take place continuously with full load with full throttle, while the engine revs slowly passes a given number of revs for the engine; see Workshop Manual, Technical Data for each engine concerned. The pressure must not be less than the given values.
NOTE! Full load must be maintained long enough so that the pressure can stabilize.
The pressure varies, depending on the temperature of the inlet air. The boost pressure is given at +25°C (77°F), which implies that the measured pressure must be corrected as per the diagram below, if the inlet air does not have this temperature during the measurement.
Example: A pressure measurement of 100 kPa (14.5 ft/lb) at 0°C (32°F) corresponds to a pressure of 90 kPa (13.05 ft/lb) at +25°C (77°F).
A.Measured boost pressure
B.Correction curves
C.Temp. of inlet air
Rectifying low boost pressure
1
Air intake
Check that the air intake to the engine compartment is sufficient. See installation instructions.
2
Air filters
Check that the air filters are not blocked, and that correct filters are used. Replace filter when necessary.
3
Tightness
The inlet pipe, exhaust pipe and other connections must not leak. Check also that the joints between the compressor bearing housing and turbine housing resp. compressor housing are tight.
4
Throttle control
Check that the control can direct the injection pump’s throttle lever to max. position.
5
Turbocharger
Check if the rotor shaft is sluggish or if the turbine wheel and compressor wheel chafe against their housings. Turn the wheel at first with a slight pressure, and then with a slight axial pull. If the wheel is sluggish the turbocharger must be immediately replaced or reconditioned. Check the wheel for damage.
In the event of daily operation in dusty or oily air, regular cleaning of the compressor housing and compressor wheel is recommended. Fouled compressor parts can result in low boost pressure.
The compressor parts can be cleaned with the unit fitted as follows:
Remove the compressor housing. Clean the compressor housing, compressor wheel and the end-head in paraffin or the like. Fit the compressor housing and measure the boost pressure again.
Cleaning of compressor parts
6 Back pressure
Check that the back pressure in the exhaust system is not excessive when installed. See: Exhaust back pressure, checking.
7
Injection pump
Check the pre-injection angle and high idling speed. Check the whole pump in necessary in a pump testing bench.
8 Feed pressure
Replace fuel filter if necessary. There must be no fuel leaks.
9
Injector/pressure pipes
Check that the correct injector is used. Check also the opening pressure and spray pattern. Check that the pressure pipes are not damaged.
10
Engine condition
Check valve clearance and compression pressure. If the boost pressure remains unsatisfactory after checking the above items, the turbocharger should be reconditioned or replaced.
Exhaust back pressure, checking
Special tools: Measuring flange kit 884969 (12 ltr), 884971(10ltr) 1
Remove the exhaust pipe from the turbocharger’s exhaust outlet. Remove the studs.
Clean the sealing surfaces. Fit the longer studs included in the flange kit. 3
Fit the measuring flange on the turbine housing with gaskets on both sides.
Fit the exhaust pipe.
10 litre: 884971
12 litre: 884969
4
Connect a transparent plastic hose to the measuring flange as per fig. or alt. a low-pressure manometer.
The difference between the water columns (A) gives the back pressure of the exhaust pipe in mm water column.
5
Run the engine with full load and full throttle for a few minutes and check the back pressure. See Workshop Manual, Technical Data for each engine concerned, for max. permissible back pressure.
An exhaust system with an excessive back pressure reduces the boost pressure, gives reduced engine output and increases exhaust smoke and exhaust temperature, which in turn can result in burned valves and turbo breakdown.
Bearing clearance, checking
Checking of axial and radial clearance is usually only carried out in connection with reconditioning, when it is necessary to determine the extent of wear in the unit.
Axial clearance
Set the tip of the dial test indicator to zero on the end of the turbine shaft, at the arrow in the figure. Press the compressor wheel in the direction of the dial test indicator and read off the measurement value. Press the turbine shaft in the direction of the compressor housing and read off the measurement value.
Axial clearance:
Holset ....max.0.102 mm (max 0.004")
KKK..........................................max, 0.160 mm (max0.006")
Schwitzer..................................max 0.170 mm (max 0.007")
Measurement of axial clearance
Radial clearance
The radial clearance only needs to be checked on the turbine side.
Place the tip of dial test indicator as per the arrow in the figure. Press the turbine wheel downwards and read off the measurement value.
Press in the turbine wheel in the opposite direction and read off the measurement value.
Radial clearance:
Holset .......................................max. 0.58 mm
(max. 0.0228")
KKK..........................................max. 0.46 mm
(max. 0.0181")
Schwitzer ..................................max 0.70 mm
(max 0.028")