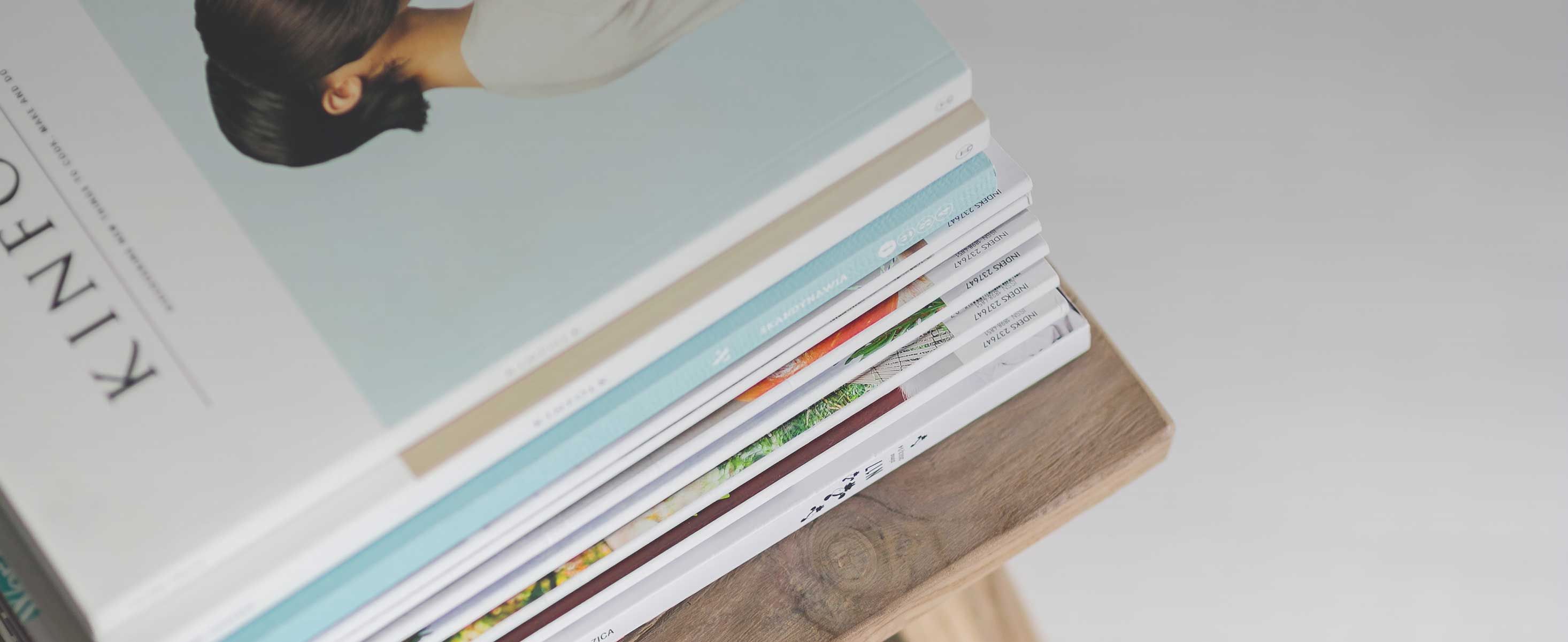
1 minute read
Fuel system - Service procedures
from Volvo Penta TD1030ME VE TWD1030ME TWD1031VE TAD1031GE TAD1231GE TWD1231VE TAD1232GE Workshop Manual
Injectors, reconditioning
1
Clean the outside of the injectors with chemically pure gasoline.
2
Dismantle the injectors. Pull out the nozzle needle from the nozzle sleeve, and place all parts in chemically pure gasoline.
NOTE! If several injectors are cleaned at the same time make sure that the springs and adjusting washers as well as the needles and sleeves which belong together are not mixed.
3
Wash the parts in an Ultrasonic washer. Blow them dry.
4
Opening pressure, adjusting
1
Connect the injector to an injection tester.
2
Check the nozzle needle and the nozzle sleeve thoroughly.
Inspection is carried out in an illuminated magnifying glass or a diffuser microscope. If the seat is dented the nozzle needle must be replaced together with the nozzle sleeve.
5
Check all other parts. Dip them in testing oil.
6
Reassemble the injector with the same thickness of adjusting washer as origin.
Check opening pressure and spray pattern, see Opening pressure, adjusting on this page.
Slowly press down the tester lever until the injector opens and releases fuel.
3
Read off the opening pressure on the tester pressure gauge.
4
If the reading does not agreee with the pressure stipulated by the Workshop Manual, Technical Data for each engine concerned, the setting must be altered. This is done by fitting adjusting washers.
Note! No more than two washers may be used. If sufficient pressure cannot be obtained using the two thickest washers, the spring must be replaced.
Opening pressure/setting pressure
See engine Workshop Manual, Technical Data for each engine concerned concerning opening pressure and setting pressure (new spring).
Spray pattern
At a pump speed of 4–6 strokes per second, the spray pattern should be uniform and the fuel finely atomised. On completion of testing, plug the pipe connections and protect the injector tips with caps.
Copper sleeve for injectors, replacement
Special tools: 6419, 6643, 6647, 8134, 8140, 9812546
Drain the cooling system.
Remove the injectors, see Injectors, replacement
Make threads in the copper sleeve’s tap with 8134
Rotate the engine until the piston in the cylinder where the replacement of the copper sleeve is to be carried out is in its lower position. 4
Grease the threaded tap on tool 8134
NOTE! The grease ensures that swarf will not fall into the cylinder and cause damage. Set the tap so that it extrudes approx. 22 mm (0.87")
Remove the steel ring with tool 6419