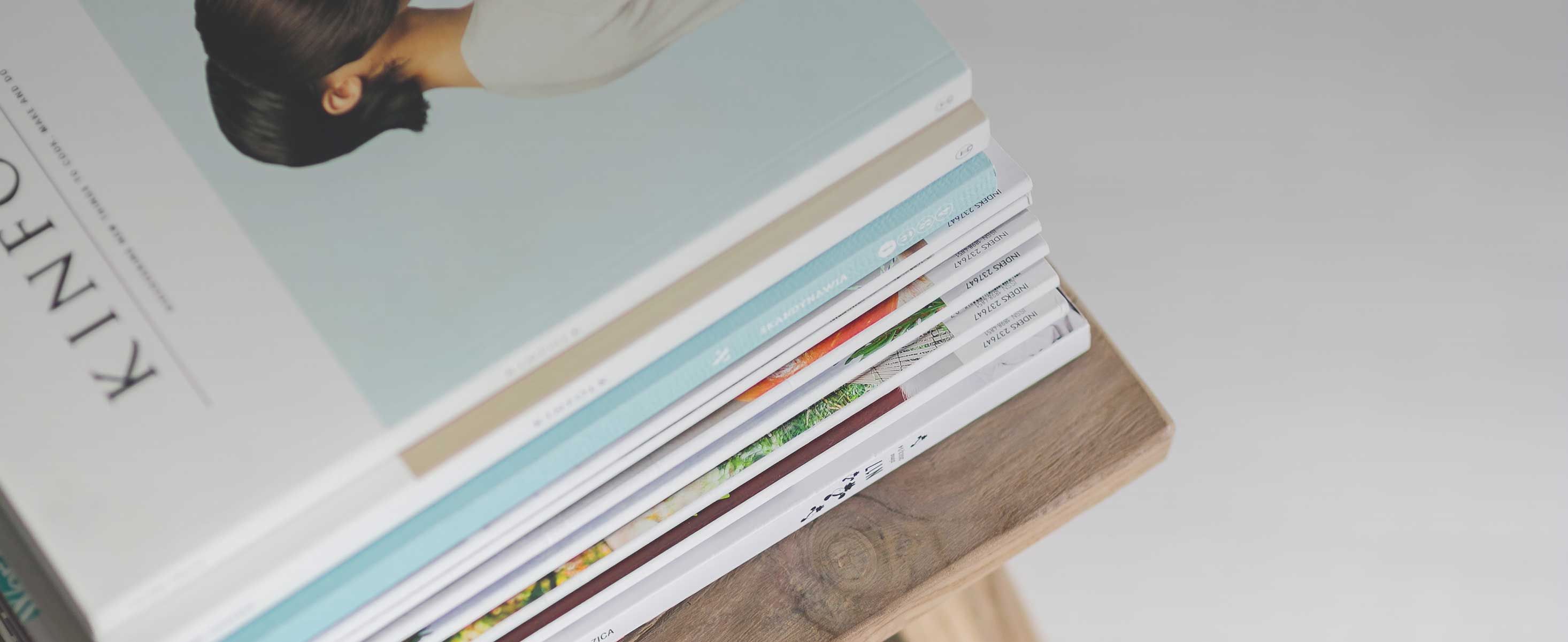
3 minute read
Fuel system - Service procedures
from Volvo Penta TD1030ME VE TWD1030ME TWD1031VE TAD1031GE TAD1231GE TWD1231VE TAD1232GE Workshop Manual
General fault-tracing
1.The valve plunger can bind if dirt gets into the valve. Is there a pre-filter? Does the fault occur when the installation is started up?. Has the dirt in the tank installation been cleaned out after installation.
Action: Dismantle and clean dirt off the plunger. Check that the tank installation has been cleaned. A pre-filter should be installed between the fuel tank and the fuel shut-off valve.
2.Have the pre-filter and/or the engine fuel filter been blocked by contamination or water?
Action: Check or change the filter insert.
3Check that the valve has not been fixed askew in its bracket. There should be spacers between the bracket and the valve.
Action: Undo the valve fixing screws. Does the stop function work properly after this action?. If so, check the bracket, and ensure that the spacers are fitted.
4.Leakage in the system.
Action: Check that all hoses, pipes and unions are tight, including those which go to the fuel supply side of the tank via the pre-filter. Check that the mating surfaces of hose cones have not been tightened as far as they go. This can cause leakage. Tightening torque: 22 Nm (16 lbf.ft). Hose unions should not be tightened as far as they go.
5. Is there a non-return valve installed in the engine inlet pipes?. Some pre-filters may have a non-return valve.
Action: There must not be a non-return valve.
Engine is difficult to start
Current supplied to stop:
1.Is there any residual voltage during the start operation? The electrical pulling winding can keep the solenoid pulled at very low voltages.
Action: Ensure that there is no residual voltage on the electrical pulling winding during the start operation. Check by disconnecting the valve connector.
Current supplied to start:
2.Make sure that the starter motor or other large loads do not draw current from the battery at the same time as the solenoid should pull. The coil might not get enough voltage.
Action: Measure the valve connector, pins 1 and 2 with a multimeter at the same time as the stop is activated by the ignition key on the instrument panel. The voltage must not vary outside 10–15 V for a 12 system or outside 20–30 V for a 24 V system.
Both versions:
3.Is the pressure drop on the supply pump and the fuel supply side so high that the pump is not able to suck up fuel? (Too great lift height, fuel pipes too long or too narrow, dirt.)
Action: Measure the pressure drop before the fuel shut-off valve. Maximum pressure drop: 0.4 bar (5,8 psi).
4.Has the fuel system been vented properly? The injection pump has to be ventilated as well. An air pocket can remain for a long time in some installations, after the engine has been taken into service.
Action: Also vent the injection pump. Please refer to pages 97-98.
5.Does the by-pass valve give the correct working pressure?
Action: Check the fuel pressure in the engine. Change the by-pass valve if necessary.
6.Have all the above points been attended to?
Action: Check the injection pump on a test bench.
Engine stops slowly or not at all
Current supplied to stop:
1.Make sure that the starter motor or other large loads do not draw current from the battery at the same time as the solenoid should pull. The coil might not get enough voltage. Also check to ensure that there are no cable breaks, or poor contact in the valve connector.
Action: Measure the valve connector, pins 1 and 2 with a multimeter at the same time as the stop is activated by the ignition key on the instrument panel. The voltage must not vary outside 10–15 V for a 12 system or outside 20–30 V for a 24 V system.
Fuel filter, replacement
Special tool: 9179
1
Wash the filter cover well, unscrew the old filters and scrap. Use tool 9179.
2
Make sure that the new filters are absolutely clean and that the gaskets are not damaged.
3
Current supplied to start:
2.Is there any residual voltage during the stop operation? The electrical pulling winding can keep the solenoid latched at very low voltages.
Action: Ensure that there is no residual voltage on the electrical pulling winding during the start operation. Check by disconnecting the valve connector.
Both versions:
3.Check that the by-pass valve on the injection pump seals in the reverse direction.
Action: If not, change the by-pass valve
4.If the acceleration arm has a setting of >1000 rpm, this can give a slower stopping sequence.
Install the new filters by hand until the gasket mates with the cover. Tighten the filter an additional 1/2 turn.
4
Bleed the fuel system, pump up the feed pressure and check tightness.