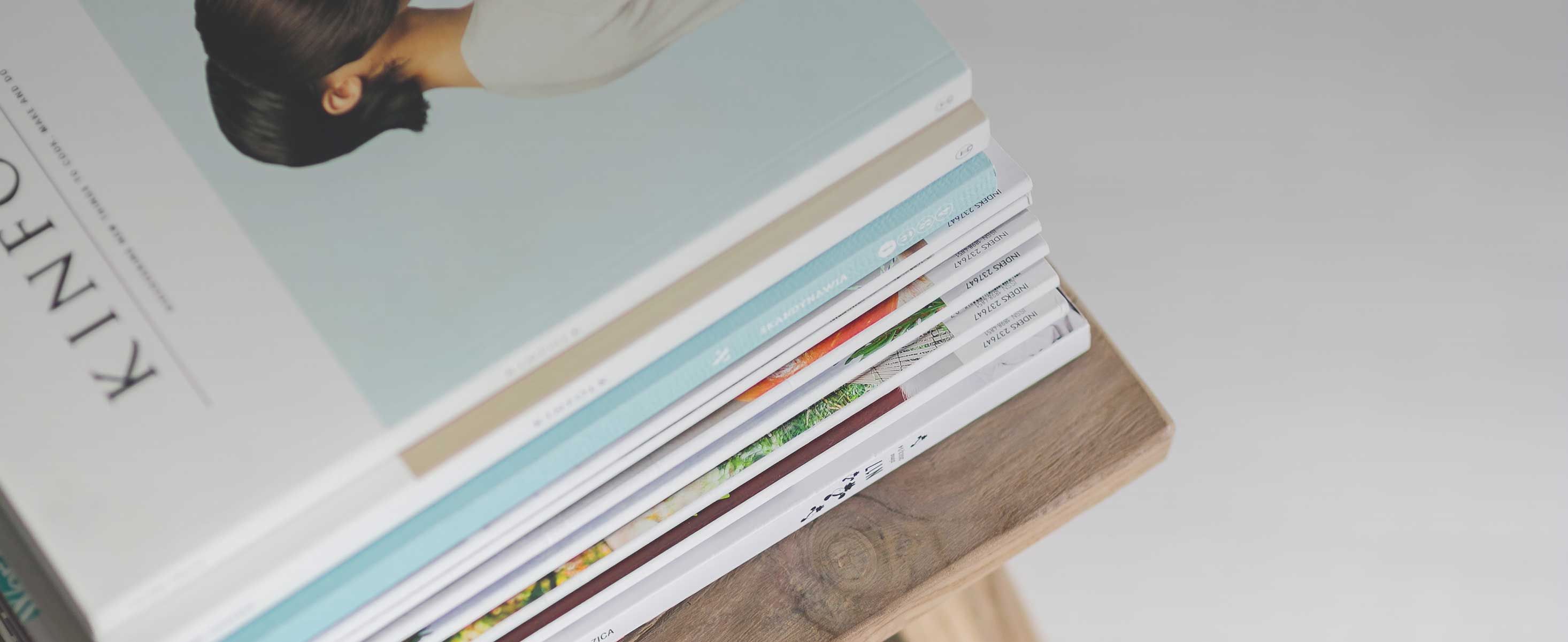
1 minute read
Engine body - Service procedures
from Volvo Penta TD1030ME VE TWD1030ME TWD1031VE TAD1031GE TAD1231GE TWD1231VE TAD1232GE Workshop Manual
2
The height of the cylinder head after surface grinding must not be less than minimun value specified in WorkshopManual,TechnicalData for each engine concerned.
The flame edge groove does not require machining.
3
12 ltr engines: New sealing grooves has to be milled in the head as per the following instructions.
Cylinder head, milling of sealing grooves, 12 ltr engines
Special tool: 9531
Before milling new grooves the cylinder head must be surface grinded so that the previous sealing grooves are completely removed.
The height of the cylinder head, and distance between the valve disk plane and the cylinder head plane, must not be less than the dimensions given in the specifications.
Check also that the valve guides are not worn, since the guiding of the grooving tool is fixed with guide pins through the valve guides.
Setting of cutting depth of the tool
1
Set up the tool in a vice with the cutting tools facing upwards.
2
Fit a dial indicator in the holder 2479 and place holder over the shoulder of the ring-shaped grooving tool.
3
Set the dial test indicator to zero to the shoulder.
4
Push the holder with the indicator sideways so that the indicator tip rests on the highest point on one of the cutting tools. Correct cutting depth (tool height): 0.20 mm (0.0079").
Adjusting
5
Milling of sealing grooves
1
Release the lock screw A (hexagon wrench 4 mm) and the adjusting screw B (hexagon wrench 5 mm), a few turns.
6
Press down the tool holder and tighten the lock screw slightly so that it presses to the holder.
Set up the cylinder head in a vice.
2
Screw tight the guide plate on the cylinder head. The plate shall be placed so that it centres between the holes for the cylinder head’s fixing screws.
NOTE! Do not over-tighten the nuts for the guide pins to avoid pressing the valve guides into the cylinder head.
3
Brush a little oil on the internal diameter of the milling head. Make sure that the cylinder head surface is completely clean and then carefully apply the milling head on the guide plate with a turning movement so that it does not chatter.
4
7
Place the indicator tip to the highest point of the tool and screw the adjusting screw upwards until the correct value of the tool height is obtained.
8 Tighten the lock screw.
NOTE! Check that the upper edge of the tool holder is level with the cutting head. If this is not so the dial test indicator has moved an extra turn.
Place the spring and nut in position and tighten the nut slightly.