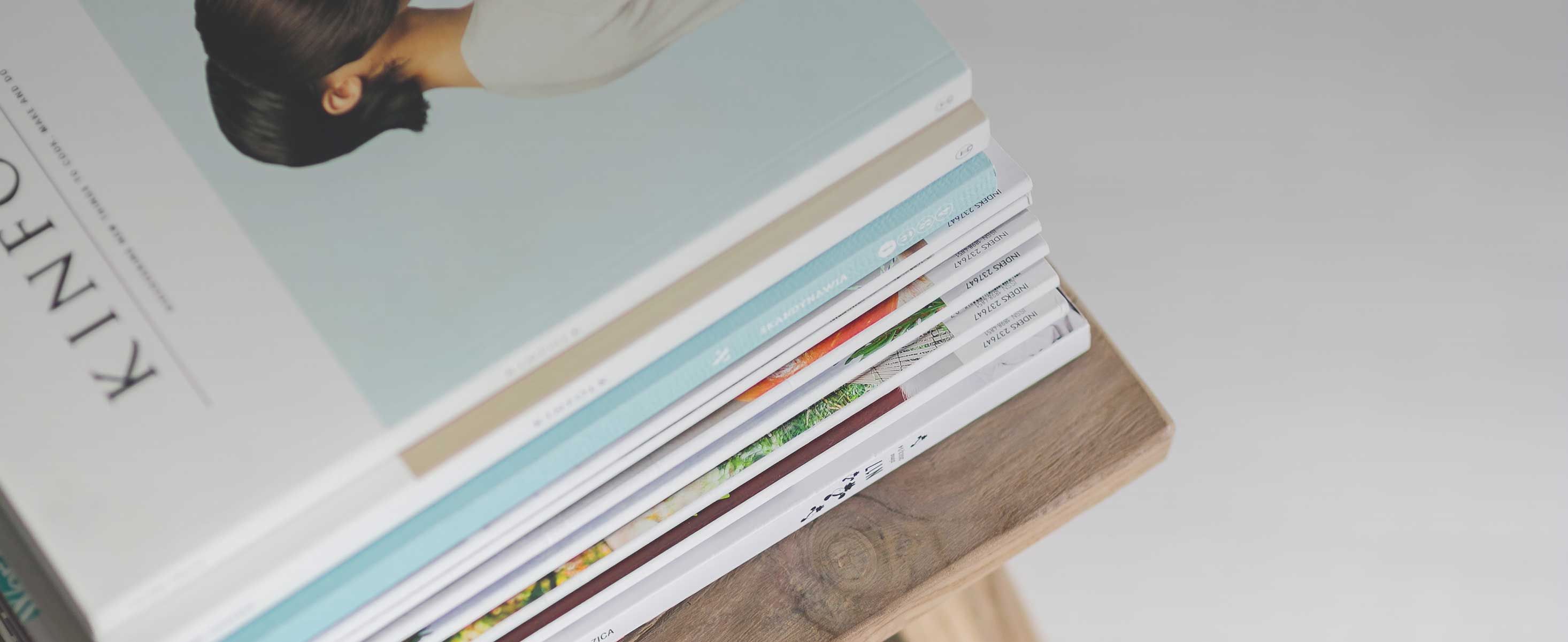
3 minute read
SPN 1485, FMI 4 - Power Relay Ground Short
Therefore, if two cylinders misfire on the same bank together they both may set the misfire fault even if neither cylinder individually exceeds the catalyst/misfire threshold.
Typically the driveability level is calibrated to set prior to the emissions/catalyst level if a two stage fault is desired. This fault would set to notify the user of a problem prior to it causing damage to the exhaust aftertreatment system.
Misfire is typically a result of one or more factors. These factors can include but may not be limited to: 1) a fouled or damaged spark plug(s), 2) a damaged or defective ignition coil(s) or coil wire(s) resulting in weak spark generation, 3) a plugged or contaminated injector(s) that intermittently sticks closed resulting in a lean cylinder charge, 4) an injector(s) that is stuck open causing an uncontrolled rich cylinder charge, 5) low fuel supply pressure resulting in multiple lean cylinders, 6) low cylinder compression due to a failed or worn piston ring(s) or non-seating valve(s) can result in a low cylinder pressure charge that may not be ignited, and 7) an exhaust leak in close proximity to an exhaust valve permitting uncontrolled amounts of oxygen to be drawn into a cylinder generating an excessively lean charge either directly resulting in misfire or possibly causing excessive combustion temperatures resulting in burned valves and loss of compression. Misfire can be difficult to correct as it may be a function of one or more of the conditions mentioned above and may require checking and/or changing several components for each cylinder or cylinders affected.
This fault sets if the misfire counter for cylinder #3 exceeds the driveability misfire limit set in the misfire diagnostic calibration and is based on a percentage of misfire over a certain number of engine cycles.
Indmar Products 2008 All Rights Reserved 247
SPN 1325, FMI 11 - Misfire Detected Cylinder #3
Diagnostic Aids
NOTE: If any other DTCs are present, diagnose those first.
Oil Level- Many engines have valve trains that utilize lifters that are hydraulically actuated and require specific levels of oil to maintain proper pressure for lifter actuation. If the engine has improper oil, insufficient oil level, or has too much oil the hydraulic lifters may not function as intended causing changes in valve lift and timing. As a result, incomplete combustion may occur as a result of oil problems. Check engine oil level and oil type according to manufacture maintenance procedures. Fuel Level- Misfire can occur due to intermittent or prolonged loss of fuel pressure due to a lack of fuel supply. If misfire counts or faults set and a fuel pressure fault is not recorded, question the operator(s) about the possibility of running out of fuel before replacing components. Ignition System- Wear or damage to ignition system components (spark plugs, spark plug wires, distributor or ignition coils) can result in weak or misplaced spark causing partial combustion and thus partial misfire. o Spark Plug(s) – Check for fouled or damaged spark plugs. Replace and regap according to manufacture recommended procedure(s). o Spark Plug Wire(s) – Check that spark plug wire is properly connected to ignition coil and spark plug. If equipped, ensure that spark plug terminal nut is tight to plug and that there is not substantial wear on nut. Check for cracks in insulation of spark plug wire or boot. Replace spark plug wire(s) if deemed necessary according to manufacture recommended procedure(s). o Distributor modules- Check distributor for oxidized or corroded spark distribution conductors including the distributor rotor and distributor cap poles. Fuel Pressure – Check fuel rail pressure at key-on/engine-off or with External Power-
All On test running. Monitor fuel rail pressure when key is turned off to determine if fuel pressure bleeds down too quickly. Run an injector fire test on a couple of injectors to monitor the pressure drop in the rail for each injector. If an injector appears to flow inconsistent compared to others, replace and retest. Cylinder Check – Run a compression test and cylinder leak test on suspected cylinder(s) to check mechanical integrity of piston rings and valve seats. Exhaust Leak – Pressurize exhaust system with 1-2 psig of air and check for pressure leaks around exhaust manifold gasket and pre-catalyst EGO sensor.
Replace gasket(s) and tighten fasteners according to manufacture recommended procedure(s).
Indmar Products 2008 All Rights Reserved 248