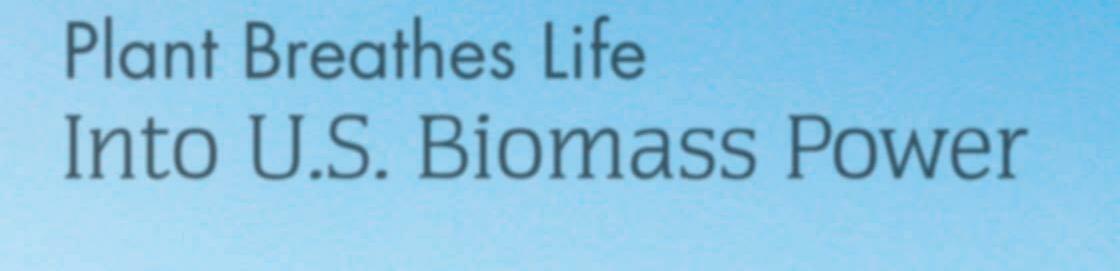
7 minute read
ALBANY GREEN ENERGY
Plant Breathes Life Into U.S. Biomass Power
By Jessica Johnson
ALBANY, Ga.
Biomass power plants have faced more challenges in the U.S. compared to other options for woody biomass utilization, such as industrial pellet production where plants are adding capacity as demand overseas rises. While standalone biomass power plants have been built in recent years, some have closed thanks to the country’s fluctuating political climate and ever-changing energy and fuel pricing structure. For reasons beyond the industry’s control, woody biomass has never gotten the love and attention solar and wind have in this country under the keyword “renewable.”
But, there’s one plant that changes that tune, Albany Green Energy (AGE): A biomass power plant in south Georgia that sells 52 MW to Georgia Power. And will for the next 19 years. The Georgia Public Service Commission wanted to see renewable energy come into their grid, and AGE is able to fulfill that desire.
The plant is also helping to support the U.S. Marine Corps. renewable energy goals, by selling them steam

to power their base in Albany over the next 23 years. AGE is also selling steam to Proctor & Gamble’s adjacent manufacturing facility for the next 19 years.
Construction
Plant Manager James Luckey, a product of the nuclear Navy and who had experience in other biomass power plants, joined the team as Plant Manager halfway through the construction by previous owner Exelon. For Luckey, having worked in both coal and biomass power plants over his career, he says he saw where coal was heading, and thanks to the facility’s long-term contracts there was a certain security that was incredibly attractive.
Construction, which was done by Exelon but led by DCO Energy Construction Services as a partner, was completed in 2017. Luckey says the project was a good match for everyone involved, including P&G to have DCO run the project. The facility had reliability issues in the beginning, but overall from 2017 to 2019, things were running—the plant was making steam. However, it wasn’t perfect, and while at a regional meeting with Exelon corporate, Luckey and a few others from Albany were pulled aside in December 2019. They were made aware the plant was put up for sale.
The plant was sold July 1, 2021—marking just about a year to get through due diligence with ReGenerate Energy Holdings, a joint venture between Ember Infrastructure and ReEnergy Biomass Operations. ReEnergy is no stranger to biomass operations, having run biomass power plants in the Northeastern U.S. Plant personnel welcomed the ownership change.
Luckey says, “I’ve been through a few transitions in my career, but this has been the smoothest. It was a big change, coming from a large Fortune 500 company and going to a company like ReEnergy that is smaller. ReEnergy has plants like ours—that has helped us.”
The timing of the transaction made things a little more difficult as Albany, Ga. was one of the original hot beds of COVID-19 transmissions in the U.S. Luckey had to work with those coming from other places for due diligence to minimize risk to operators on-site was well as the travelers. Thanks to emails and phone calls, the team persevered—but no one is eager to see happen again.
However, he’s quick to say that the plant was able to successfully maintain operations; despite how people might have felt personally about the challenges the outside world offered, the people on-site were a team in

every sense. “We care about each other,” he adds. “We have some people here who have children with respiratory issues. We were more careful for their sakes. At the end of the day, we all wanted to do the right thing by the company and the people here. We held each other accountable.”
One of the first things Luckey says the ReEnergy team did was help evaluate what processes Exelon had put in place that were sound and what might need to be revisited.
“ReEnergy was good about recognizing if we were doing something right, letting us keep it. Our structure stayed the same. The biggest difference has been in the experience that ReEnergy brings to the table in terms of biomass,” he reiterates. That experience helped AGE worked better with P&G to meet that facility’s needs in a more focused approach than before.
ReEnergy’s Technical Director Erik Norgren spent a lot of time supporting Albany in the transition and working to make outages more efficient, Luckey says. The plant’s goal is to run from one outage to the next, 330 days per year. During the November 2021 outage, AGE with the helpful eye of Norgren, worked primarily on fuel handling and baselining fuel handling equipment’s runtime— which helps plan for the next outage, something the plant hadn’t been particularly good at in the past.
These implemented changes helped the plant reach 94% availability in December 2021, a figure that has increased since ReEnergy took over in July. Most of the previous inconsistencies in reliability had to do with fuel handling, hence why the outage focused so heavily on it, Luckey reports. “It wasn’t the equipment,” he says. “It was more of bringing someone in on what the baseline is and what we can do to improve the reliability. Coming in and doing some modifications to the screws so there’s a longer life expectancy.”

Operations
Over 30 ReEnergy employees staff the facility from end-to-end. AGE has what Luckey calls “world-class equipment” in Bruks, Raumaster and Valmet. Bruks and Raumaster handle fuel, with a Valmet circulating fluidized bed boiler. AGE burns material composed of mill residues, forest residues, and paper fines from P&G’s process, sourced from a 75 mile radius. Luckey says the plant has experimented with peanut hulls and pecan shells: “Anything that is not economically viable for anyone else, we can burn it here.” Thanks to the Valmet boiler design, A Valmet boiler gets it done for AGE. the fuel can come in a variety of moisture content—as high as 45%. The plant processes between 110-120 trucks per day, Monday through Friday, using Saturday as a catch-up if needed with three Bruks truck tippers. Once brought in, fuel is conveyed to a Bruks stacker-reclaimer where it will sit for no longer than 15 days, on a first-in first-out basis. The yard can store about 40,000 tons, which translates to about 20 days of runtime for AGE as it burns about 2,000 tons per day. Material is rotated and reclaimed using the 270° radius of the Bruks stacker-reclaimer before being conveyed to the boiler. The Bruks system helps minimize the need for rolling stock, Luckey says, though some Caterpillar machines dot the yard for on-demand uses. When the Valmet boiler is at temperature, wood fuel, which AGE calls solid fuel, is brought in for burning. The bed temperature is around 1500° F, while the boiler itself gets to the range of 1700° F. If the boiler has been down, AGE will burn natural gas to reach the 800° F temperature, at which point solid fuel is injected. Steam is sent through the furnace,
with heavier particulate going through a loop seal where it is fed back to the boiler to burn it again for full utilization. Three super heat sections super heat steam sent to the GE/Alstom condensing steam turbine with extraction.
The turbine is what is sold on the Georgia grid. Steam is sent to P&G through an export line. That same P&G export line has a second export line, which sends steam to the Marine Corp. base’s Siemens 8.5 MW MCLB steam turbine-generator, which AGE maintains under contract. The ash product formed in the boiler is emptied by the ash handling system. Lighter particles go through a baghouse and stored in a fly ash silo until disposal, while heavier particles are emptied through the bottom ash system and go into bins. All the ash is transferred off-site by a local company that repurposes the ash for fertilizer.
All water used for condensing the steam comes from a well the city of Albany installed well before AGE was planned. An on-site cooling tower helps AGE reuse as much water as possible.
Plant-wide, Johnson Controls installed fire-fighting controls, and the fuel yard has hydrants. Luckey says the Albany Fire Department comes in periodically to make sure they are familiar with the plant in case of emergency.
Luckey says simply of the philosophy over the last two years, “We’re in the business of running the plant to operate the plant. So let’s do everything we can to make sure we’re in the position to do that.”
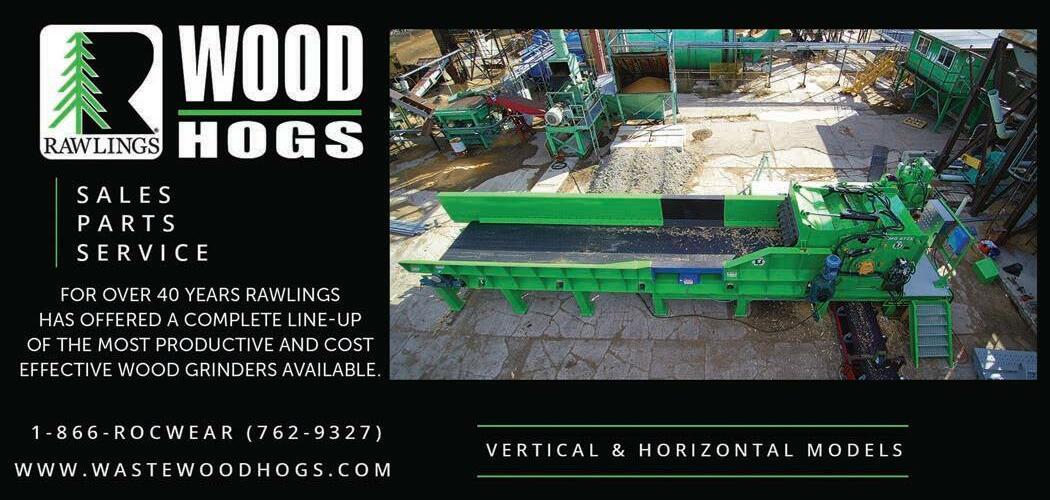
