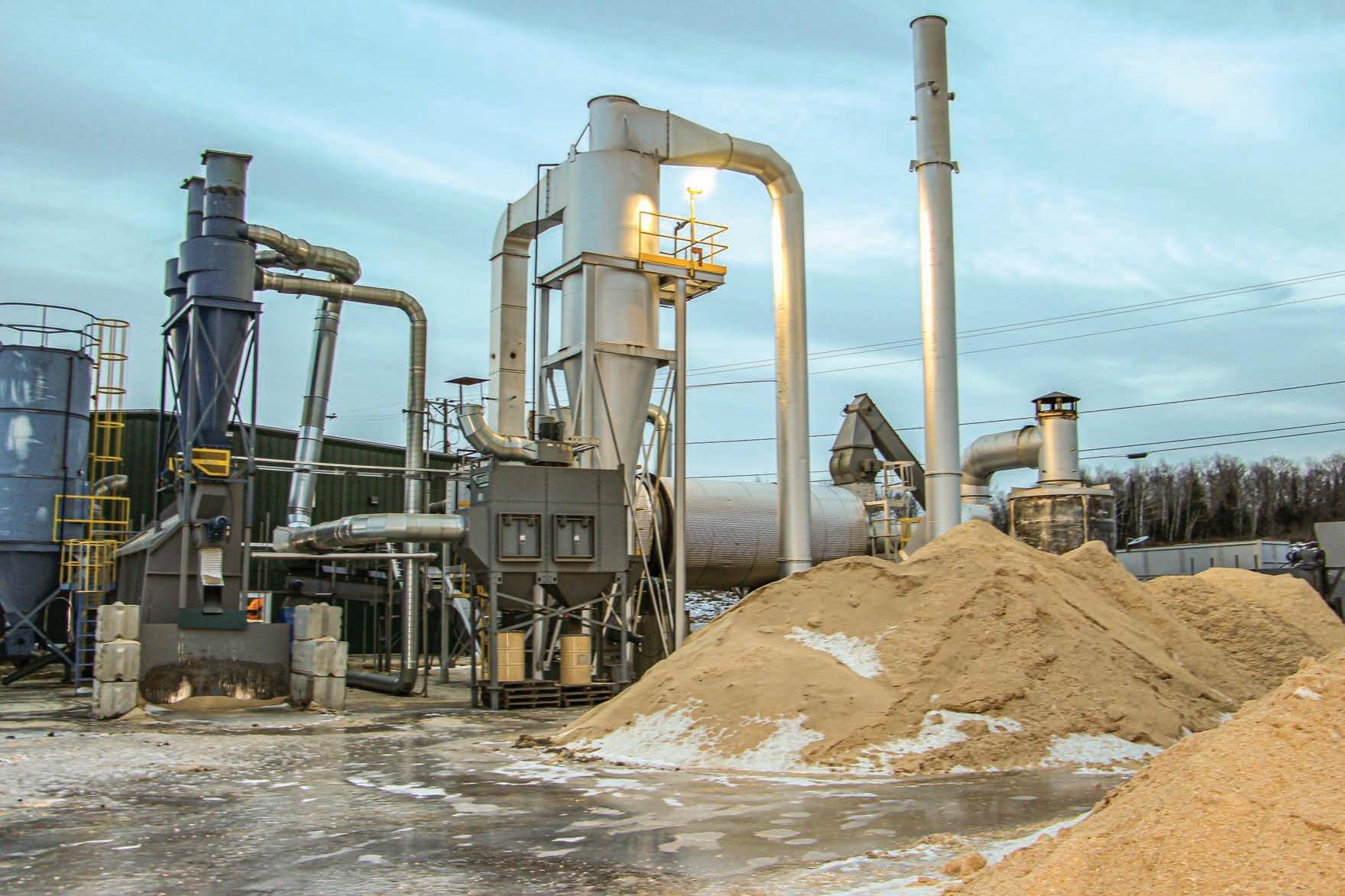
9 minute read
BRIQUETTES & PELLETS
Engineering Firm Beco
By Jessica Johnson
ASHLAND, Me.
For mechanical engineer Tyler Player, a native of Aroostook County, Maine, converting biomass from the forest to useable energy wasn’t his life’s work. It was on his radar, as he wound a path through forest products in his career—but not his life’s goal. The engineer quickly developed a knack for wood dryers and soon would leave his job with a corporate plant to start his own firm, Player Design, which among other products and services builds drying systems. PDI dryers are popular with North American domestic pellet plants for a variety of reasons, with capacities ranging from 1 ton to 20 tons.
Knowing how to build a dryer and building a pellet mill (or in the case of Maine Flame, a briquette plant) is a lot different than building a plant and then running it after commissioning. But that’s the exact challenge Player and his team took head on with the Maine Flame proj-
o mes Owner/Operator
ect. 20 miles due west from Player Design’s office in Presque Isle sits the Maine Flame briquette plant, which also houses the only operating steam extruded pellet process that makes the patented CoalSwitch product. (See sidebar.)
Player leaned heavily on his own experience, but also PDI Director of Engineering Michael Edge-


Plant Manager Lee Haskell
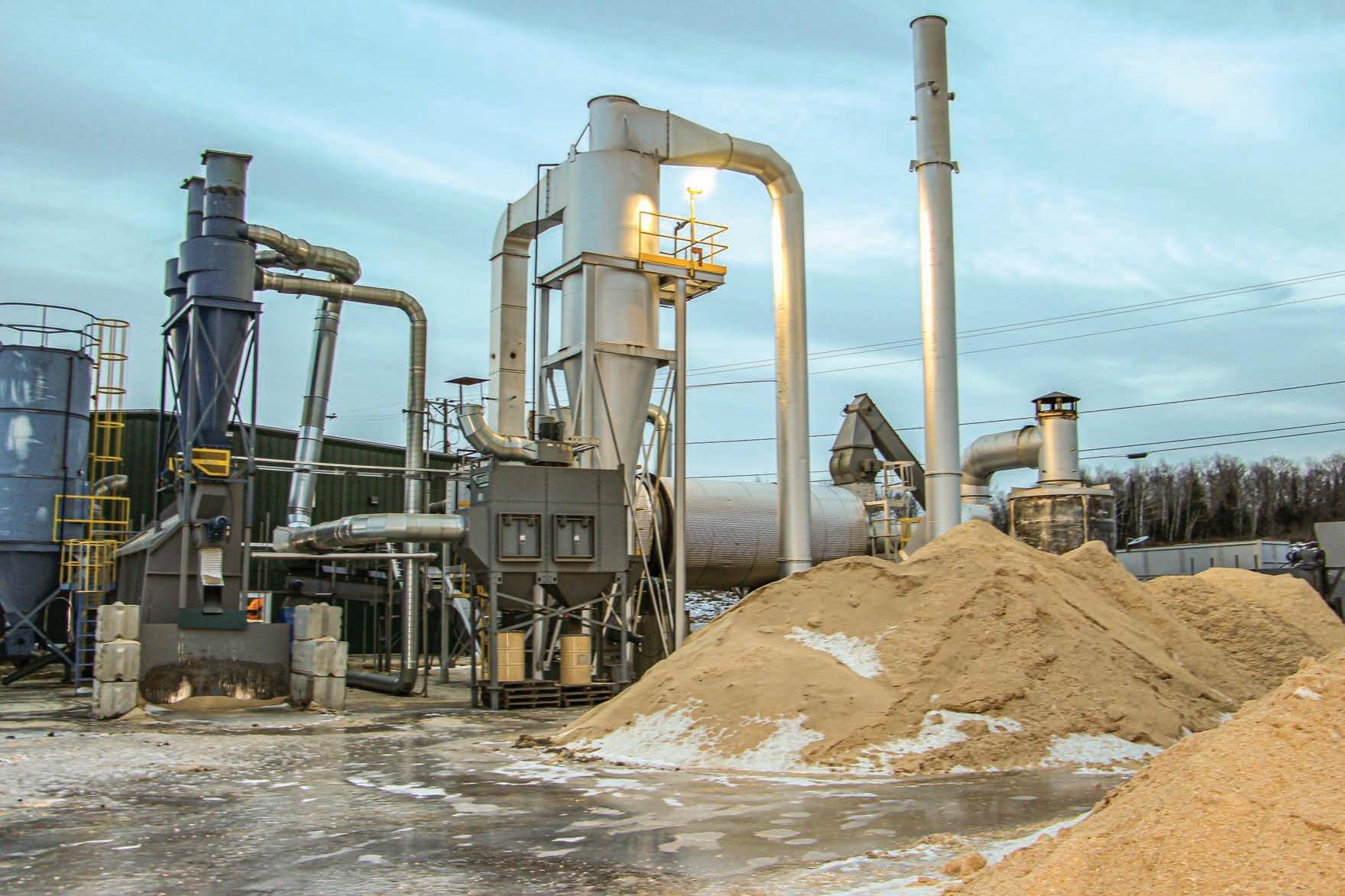
A Switch To CoalSwitch
In addition to making the Maine Flame-branded briquettes at the Ashland, Me. facility, Player Design’s team is working with UK based, Active Energy to produce a next generation “black pellet” that is steam exploded, not torrefied, known as CoalSwitch. According to Tyler Player, whose engineering firm and processing facility is a site manufacturer of CoalSwitch, a trademarked process and patented product owned by Active Energy Group, plc. Player says the increased heating value of the steam exploded pellet is just one of the many benefits of the product for industrial users.
Explaining, “You can manufacture and upgrade the heating value so you go from 8,500 BTU/lb. to well over 10,000. Because of the mechanical properties, it can be exposed to water without turning itself back into mush. But you don’t have to create all the air emissions you do with torrefaction. The result is all of the mechanical benefits of a torrefied pellet without all the problems,” Player says.
Like other industrial pellet products in North America, CoalSwitch is a next generation pellet made from predominately sawmill residuals. The idea Player and Active Energy have is to use residuals from a single sawmill and cut down on freight by co-locating. Why pilot the facility in Northern Maine? Player says it is to be close to a relatively controlled cost and he knew the reality was CoalSwitch wouldn’t be big enough in the short term to make a dent in an area with multiple markets for residuals and other byproducts.
But he doesn’t think CoalSwitch should be pigeonholed to just Northern Maine. The group is actively seeking to identify other facilities that could use a way to manage residuals, and are interested in working with them to build either on the sawmill site or very near it, as long as a solid offtake agreement is in place for getting their materials.
Player adds, “We don’t own forests and we don’t manage them. But we can build and run CoalSwitch manufacturing plants. We need partners that have a residuals problem and what we need is an offtake agreement for their residuals and we will take care of all the rest.”
The Concept
Aside from the desire to co-locate with a facility looking to have a market for their residuals, Player says access to a port is nearly crucial because CoalSwitch at this point is purely an export product.
“The idea with CoalSwitch is you can co-burn it with coal. It’s a bit of a spin on the standard industrial pellet business model, buying next generation pellets that are much more environmentally friendly and easier to control the logistics getting them from the
Tyler Player
February 2022 / Wood Bioenergy 19
East Coast of the U.S. over the ocean, without getting them wet,” he explains.
Sales are targeted to areas of the world where the infrastructure investment has not been made to burn white pellets, but also countries interested in trying to move away from burning coal for energy. Player explains, in the short term, using CoalSwitch is ideal for partner companies that are trying to improve their environmental positions but are currently burning coal.
He adds that “We can cut their emissions corresponding with the amount of CoalSwitch that they burn.” Player acknowledges that CoalSwitch is a slightly more expensive final product than traditional industrial grade white pellets, nonetheless, its improved environmental credentials will more than justify any increase in costs.
While CoalSwitch is the first of its kind to be produced in this specific manner, it is not the first black pellet to be produced in North America. What makes Player and Active Energy think its facility will work long-term when others have failed? Scalability. “The CoalSwitch process doesn’t produce the VOCs that require RTOs and precipitators and all the other equipment to treat the air. We are going to make the product a 10-20% premium to white pellets but we get that back in energy,” he says, noting how expensive it is to treat everything that comes out of an emissions plume.
“At over 10,000 BTU/lb. we are gaining 1,500 on the 8,500 BTU/lb. from white pellets. We get the energy savings and we have worked out a process that is simple enough that it can be done at scale and produce an economical steam exploded pellet,” he adds.
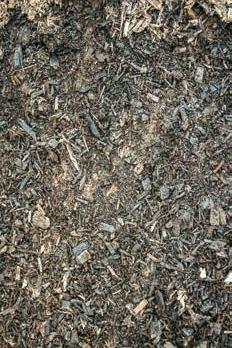
Raw material to steam exploded material to CoalSwitch.

comb, who served as Maine Flame’s project manager and chief engineer. The premise of the plant is straightforward: At a rate of 3 tons per hour, the facility’s automated line produces briquettes for residential use in packages of four. Edgecomb is happy with what the facility is currently producing, saying it is running well. “There’s always things to figure out,” he adds. “Stuff to fix; what die is best to get the right briquette. But we are overall happy with how things initially turned out.”
A pet project for all involved that has now mushroomed to more, Maine Flame takes leftover sawmill chips, other residues from local sawmill processes and planer mill shavings to make the briquettes. Annual capacity is around 20,000 tons. Player admits the facility is not as high-speed as others—and that’s by design. While the home heating market in New England is strong, there’s still a matter of establishing a customer base.
Player explains the product is meant to be positioned around cordwood, still a commonly used option in the region for home heating. Capacity will ramp up, he says, as the market demand does. Adding, “We’re not running enough because of the growing sales to compensate for a production volume uptick. Over the next year, we will get the market built to where it needs to be.”
Anther one of the advantages to building Maine Flame was if anyone wants to see Player Design equipment in action, there is a readily available and running plant at Edgecomb and Player’s fingertips.
Edgecomb emphasizes, “We did a similar [to Maine Flame] plant in Quebec, but with a different briquette
The Process
The process for making Active Energy’s CoalSwitch is proprietary, while also being fairly straightforward. Chips are brought in and ground. Ground material is then put into a pressurized reaction vessel, bringing the pressure up. Then, using a rapid release process, pressure is released. According to Player, this renders the wood effectively waterproof. Pellets are made using Bliss pellet machines in Ashland.
While Ashland is the first, Player and Active Energy already have the funding indicated together for a second CoalSwitch production facility in Northern Maine. Construction will begin as soon as Player and Active Energy are able to obtain an air permit, which is expected to be sometime in the second quarter of this year. Production therefore is expected to begin in the fourth quarter of this year with a projected annual capacity of 70,000 tons.“What we are trying to do in Ashland was prove out a concept with a minimal capital investment,” he says. The second plant built will be of equivalent size but, the end goal is to have small modular plants in multiple places, then collect volume and move it that way—instead of building behemoth plants. Taking in 20 tons of raw material an hour, the plant capacity will be around 8-10 tons/hour. Player admits that the raw material intake amount might seem like a lot but for a typical sawmill it should be just about right.
20 Wood Bioenergy / February 2022
machine, same dryer and burner. So we know what we are doing with this design.”
Plant Flow
Player says the idea for Maine Flame was born out of almost necessity—when ReEnergy’s power plants in the area shuttered, there was a massive amount of logging and sawmill “waste” that was going unused that had previously been feeding those biomass power plants. Now, the leftovers were becoming a huge problem for the sawmills especially, which is where Maine Flame was able to step in. All material accepted is spruce or fir. Player says that spruce and fir have two advantages for the briquetting process, firstly, “It’s easy to make a log out of, and two, it is readily available.”
Edgecomb says the process is pretty typical and straightforward. Since wood drying is what PDI does, the facility has a full dryer set-up, which allows them to be somewhat flexible in the products they take in from the sawmills. Material is trucked in, and passes through a non-recycling dryer to bring out any extra moisture. From the dryer, material is conveyed to a hopper and cyclone. A drag chain pulls it up into the sizing process. A reversing drag chain was installed ahead of the West Salem hammermill in case of a dryer fire or other incident that would necessitate a slowing down of the process. There is Flamex spark detection throughout the process.
From the hammermill, material goes down to another bin with a reversing screw to feed a dry storage bin. Another drag chain pulls material into the plant, up into one of two silos to feed the CF Nielsen briquette machine. Twin screws push material together in the briquette machine—which uses a high temperature to seal and compress the briquettes. Finished briquettes have a moisture content of around 10%.
A 125 ft. long line inside the press keeps pushing all the extruded material through, with the end being a saw to cut briquettes to Maine Flame’s spec of 10-12 in. long, 3.5 in. diameter. A belt conveyor moves finished briquettes to an accumulation table. Briquettes are manually moved from the accumulation table to the packaging line, where they are shrink wrapped and a label is affixed.
The plant staffs 10, and is led by Plant Manager Lee Haskell.
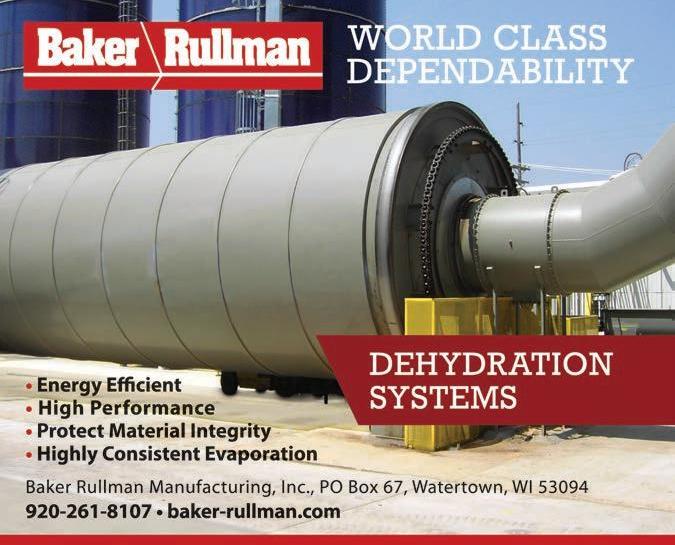
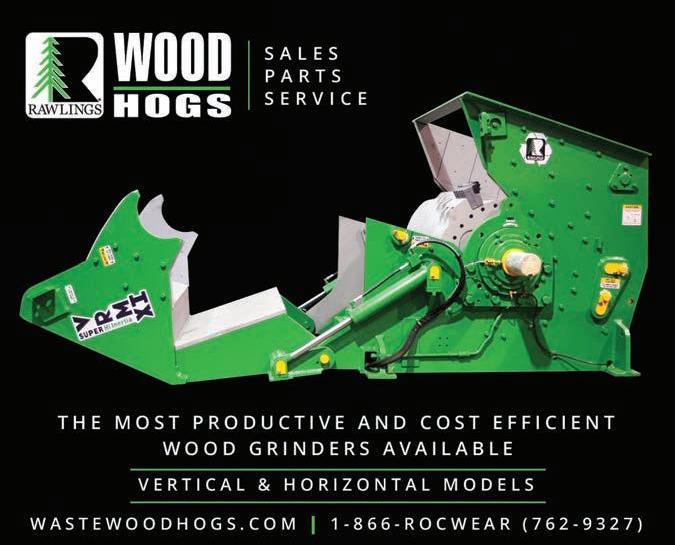
February 2022 / Wood Bioenergy 21