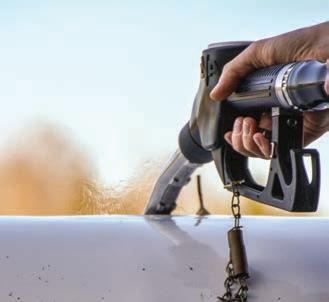
32 minute read
My Take NewsLines _______________________________________________6
Got The Inflation Flu?
Inflation is on the news and all over the dot com as loggers grapple with rising costs for just about everything they need to operate. And there’s no doubt that, despite all our earnest attempts to believe and be “over it,” the COVID pandemic’s impact, especially on labor and supply chains, is something we’ll be living with and operating under for a while.
Both the Professional LoggingContractors of Maine and the American Loggers Council have recently surveyed their memberships who detailed cost increases for a wide variety of equipment, supplies and services. The ALC survey found an average price increase of 25% (some much more) across more than 20 items. Inflation canalsotake on a life of its own up and down thesupply chain: An official with the Southern Loggers Cooperative noted that during recent fuel price run-ups members were shooting themselves in the foot by maxing out fuel purchases in fear of higher prices in the next week—which inreturn lowered inventories and hindered SLC’s ability to ride out market swings.
There’s also aninteresting note in the mid-April North American Woodfiber & Biomass Markets report from Fastmarkets-RISI about a growing debate among procurement officials and others involved in the fiber supply chain in the South Atlantic Region from northeast Florida to southeast Virginia about whether elevated wood prices from 2021—up roughly 10-15% or around $3-$4 per ton that have persisted into 2022 represent a new elevated cost structure or temporary spike?
According to the report, some say higher prices are“more or less here to stay” while others claim prices eventually revert to a historicaltrend.
That’s the funny thing aboutinflation: You have fuel prices thatalmostdouble in three or four months but take a year or more to get back to“normal.” There are those contractors whose prices seem to keep rising: Recent tree work on my leafy lot compared to some we had done 25 years ago showed a solid 300%+ price increase. Then there are the loggers, who are working for prices that are little changed from years ago.
The issue is pointed uprepeatedly bysurveys andconversations withloggersthemselves: A supply chain that doesn’t allow its suppliers to keep up with inflation will eventually have trouble finding suppliers.
Fuel gets the headlines, but costs have increased across the board for loggers.
Impacts Continue
As part of the recent Panel & Engineered Lumber Conference in Atlanta hosted by TH companion publication Panel World magazine, I had the good fortune of listening to a presentation from award-winning economist Roger Tutterow of Kennesaw State, who delivered a presentation that noted the impacts of the pandemic on leading economic indicators and overall economy.
For the forest products and construction industries, the biggest issues are inflation and labor leading to higher construction costs, and it’s uncertainty along the supply chain that’s a big contributor to higher prices, he said.
Still, there are good housing and construction demand dynamics, with the inventory of new and existing housing currently at generational lows, Tutterow said. He added that recent interest rate increases may provide headwinds but historically a mortgage even between 5-6% is considered a good deal.
As he covered the current leading economic indicators; he noted that the pandemic recession of 2020 was the worst in U.S. history but also the shortest, and how we’re all living in a time of unprecedented economic dynamics during the world’s first truly global pandemic of the modern digital era.
Tutterow identified another big issue is how the economy will move forward without major federal stimulus funds and reduced Federal Reserve “quantitative easing” while grappling with pandemic recovery. All the stimulus money and “paying people not to work” is in the rear view mirror now, he said.
Amongst all the economic numbers and graphs, Tutterow made an important insight: We all love to talk about the mandates and shutdowns and those always grab the headlines. But 10 years from now, he said, we’re more likely to be talking about the impact ofvoluntarychanges in our lives and businesses: the great resignation that was real, lower workforce participation, more work from home and other societal changes that will affect how the forest products industry and all of society does business.
DAN SHELL
Business Survey
Please take time to visit timberharvesting.com and complete the 2022 Logging Business Survey, and keep an eye on your inbox as we’ll send out a couple more links to the survey before it closes on Memorial Day.
As the economist noted, loggers have the current misfortune of living through “interesting times” as the world continues to work its way through the pandemic and a business roller coaster that started with shutdowns and social distancing that eventually led to high demand for logging services and the highest prices on record for basic forest products like 2x4s and 6s and plywood panels.
The 2022 Logging Business Survey takes a close look at how loggers’ businesses have fared in the two-plus years since the pandemic and its impacts on labor, the supply chain and companies throughout the industry.
Results of the TH Logging Business Survey will be shared in the July/August issue.
If your company has a case of the inflation flu, let us know! TH
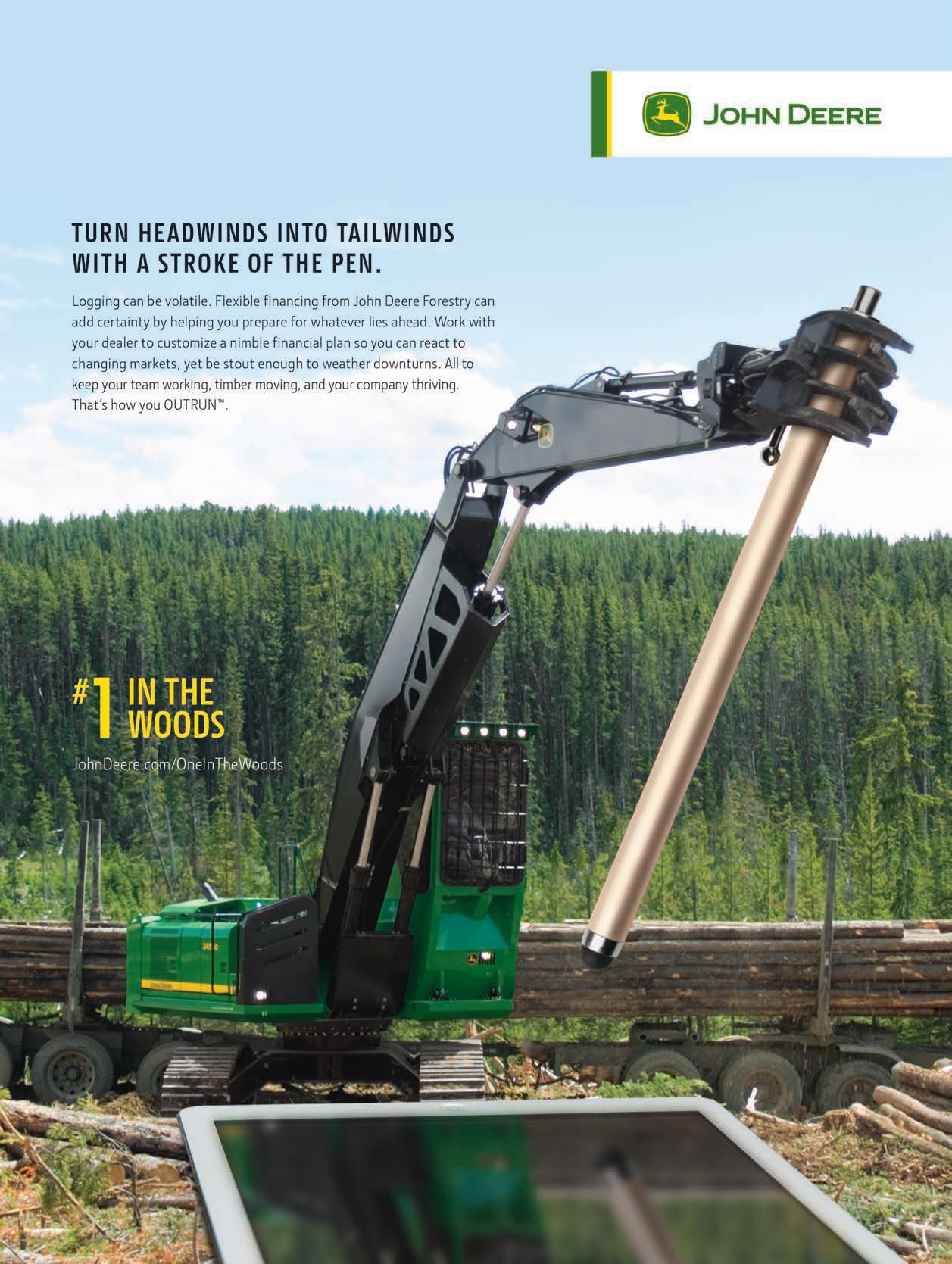
WestRock Closing Mill At Panama City, Fla.
Northwest Florida fiber markets were jolted in April after WestRock announced that it will permanently shut pulpwood operations at its major Panama City, Fla. mill in early June.
According to a recent Fastmarkets-RISI report, the move eliminates 2.75 million tons of annual wood consumption, with Enviva’s pellet mill at Cottondale, Fla. and Georgia-Pacific’s linerboard mill at Cedar Springs, Ga. expected to be the future destinations for much of the WestRock plant’s incoming wood.
The move comes as a result of several issues, including closing an aging facility that operates an outdated linerboard line and also produces non-core business market pulp. The facility’s procurement area had also taken a big inventory hit in 2018 with damage from Hurricane Michael as pine plantations in the region were hammered. The mill itself was down more than six weeks in 2018 after sustaining hurricane damage. In addition, there’s a wave of new containerboard capacity coming on line later this year. The facility’s fast-track closure—less than three months from announcement to shutdown—marks the end of a hundred-year era as city officials note the site is to be re-purposed with a new owner. Most of the current complex came into production back in the late 1950s, but the site in an area known as “Millville” on the outskirts of Panama City has been a major regional log destination for wood consuming operations for more than a century, starting with a sawmill in 1920. International Paper Co. built the site’s paper mill in 1930. Southwest Forest Industries bought it in 1979. Stone Container Corp. purchased it in 1987 and merged with the Jefferson Smurfit Corp. in 1998 to make Smurfit-Stone Container Corp., which filed for Chapter 11 bankruptcy protection in 2009. RockTenn purchased the mill Hurricane damage contributed to mill from Smurfit-Stone in May 2011, and it’s been a WestRock mill since the 2015 closure decision. merger with MeadWestvaco.
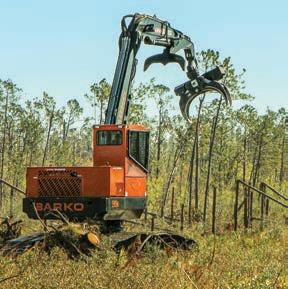
PLC, ALC Surveys: Inflation Bites Loggers
Surveys by the Professional Logging Contractors of Maine and the American Loggers Council have both confirmed inflation is taking a big bite out of loggers’ operations and affecting the cost of many items.
Earlier this year in Maine, the PLC asked members to report their increase in costs for 20 goods and services that are vital to logging operations over the period of January 2020 to January 2022. Loggers reported increases ranging from 17-30 percent, with truck and equipment insurance the lowest at 17 percent while oil and lubricants saw the highest increase at 30 percent. Many of the costliest items on the list including heavy equipment tires rose 24-26 percent in cost.
According to Dana Doran, Executive Director of the PLC, “It is clear that Maine logging companies are being hit harder than many at a time when most are already struggling with difficult markets and wood prices that are not keeping pace with rising expenses.” He added that spiking energy costs are projected to add to even more to the price of most goods and services in the coming months, worsening an already critical situation.”
The American Loggers Council surveyed its national membership on the same issues and found average inflationary impacts for industry specific items and services were 25% increase, some much more.
According to the ALC survey report, by contrast, the delivered wood prices increased for only 30% of the respondents, with delivered wood prices remaining the same for 50% of the respondents and declining for 20%. With tight profit margins the logging industry cannot absorb these increases while wood prices remain flat, calling the current situation “not sustainable.”
Major Restoration Project Begins In Washington
Loggers are beginning work on the 50,000 acre Mission Restoration Project in the Okanogan-Wenatchee National Forest in central Washington in May.
The three-year project includes more than 10,000 acres of thinning and ladder fuels reduction work, and as many as 20 contractors could be working on the project at any given time, national forest officials say.
Hampton Lumber successfully bid on the project in 2021. Douglas fir logs are going to Hampton’s Darrington, Wash. mill, with pine logs destined for the Randle mill. Small log thinning operations are scheduled to begin in June.
BC Harvesting Deferrals Kick In
For the time being no harvesting will be allowed on nearly 1.7 million hectares (4.2 million acres) of oldgrowth in British Columbia as the province and First Nations throughout it develop a new approach to sustainable forest management.
“Our government’s new vision for forestry is one where we better care for our most ancient and rarest forests, First Nations are full partners in forest management, and communities and workers benefit from secure, innovative jobs for generations to come,” says Katrine Conroy, Minister of Forests. “By deferring harvest of nearly 1.7 million hectares of old-growth, we are providing the time and space we need to work together to develop a new, more sustainable way to manage BC’s forests.”
The 1.7 million hectares figure is down from the BC government’s original intention to defer 2.6 million hectares. BC Council of Forest Indus-
tries stated the deferrals would have a devastating impact across the province, resulting in multiple sawmill closures, as well as pulp mills and value-added facilities.
The government’s plan is based on recommendations from a panel of advisors with ties to environmental organizations. Known as the Old Growth Technical Advisory Panel, it has come under criticism from some sectors of the forest products industry.
A recent independent study commissioned by the Council of Forest Industries of forest inventory commissioned by COFI indicates BC has about 11.4 million hectares (28.2 million acres) of old forests, the majority of which—more than 75%—is already protected or is outside the timber harvesting land base.
As a result of these engagements, deferrals have been implemented on approximately 1.05 million hectares of BC’s most at-risk old growth, which are ancient, remnant and priority large stands identified by the Old Growth Technical Advisory Panel. This includes areas where sales have been paused by BC Timber Sales while engagements with First Nations are ongoing. In total, more than 80% of the priority at-risk old-growth identified by the advisory panel is currently not threatened by logging because they are already protected, covered by deferralsor uneconomic to harvest, according to the Panel.
In addition to biodiversity, many First Nations expressed interest in managing old-growth on their territory in support of broader, related values such as wildlife habitat, cultural practices, clean water, healthy salmon populations and species at risk. As a result of integrated land-use planning processes underway, deferrals have also been implemented on another 619,000 hectares of old-growth forests.
The new Ministry of Land, Water and Resource Stewardship will have a crucial role to play in supporting the implementation of 14 recommendations of the Old Growth Strategic Review in partnership with First Nations. Government is working towards a new Old Growth Strategy for BC to be completed in 2023.
Budget 2022 provides an additional $185 million over three years to provide coordinated and comprehensive supports for forestry workers, industry, communities and First Nations who may be affected by new restrictions on old-growth logging. This includes funding for short-term employment opportunities for contractors and their workers, rural economic diversification and infrastructure projects, bridging to retirement for older workers, education and skills training, and on-the-ground economic development and community support services.
Oregon: What’s Next For Forest Accord
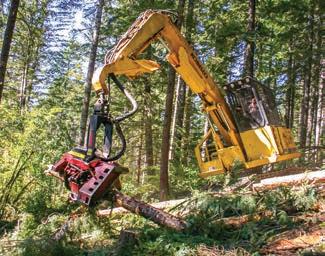
Oregon loggers face rule changes.
There’s lots of work ahead as Oregon’s new Private Forest Accord (PFA) forest management rules are developed and ultimately required as of January 1, 2024, according to a recent report by Associated Oregon Loggers Forest Policy Manager Amanda Sullivan-Astor.
Key deadlines this year include October 14, the last day for public comment, and November 30, when rules are scheduled to be adopted by the Oregon Board of Forestry, Oregon Dept. of Fish & Wildlife and Fish & Wildlife Commission. The new rules are part of a Habitat Conservation Plan application that Oregon will submit to the U.S. Fish & Wildlife Service by December 31, 2022.
The PFA is part of an agreement between major state timberland owners and environmental groups to avoid costly court cases and legislation by modifying the state’s Forest Practices Act by increasing streamside protection rules that will reduce some private timberland harvests while providing certainty for the future.
New landslide and fish models are due May 1, 2023 and new rules for fish buffer zones are due July 1, 2023. Additional rules are scheduled to go into effect in 2024.
Having groups like AOL, Oregon Department of Forestry, Oregon Forest Resources Institute, OSU Extension, industry trade associations, landowners and others participating in PFA rulemaking, modeling, training and implementation processes is a “heavy lift” but necessary for Oregon forestry interests to have their viewpoints included at each step, Sullivan-Astor writes.
“The intent is to ensure flexibility is still allowed so that economic viability and operational feasibility continue to be attainable throughout Oregon,” she says.
Drax Officially Opens Demopolis Pellet Plant
Drax Group has opened a new pellet plant in Demopolis, Ala. At full capacity the plant, which is Drax’s second production facility in Alabama, will produce 360,000 tonnes of sustainable biomass pellets a year.
“Drax’s wood pellet plant that’s being commissioned in Demopolis represents a major investment that will drive long-term economic growth and spark significant job creation in Marengo County. The opening of this facility is an exciting development for this rural region, and I look forward to seeing Drax develop new growth plans in Sweet Home Alabama,” commented Governor Kay Ivey at the official opening.
Will Gardiner, Drax CEO; Mayor Woody Collins; Ashley Coplin, executive director of the Demopolis City Schools Foundation; and Matt White, Drax Executive Vice President, Pellet Operations also participating in the ceremony held April 5.
Weyco Purchases More Acreage In Carolinas
Weyerhaeuser Co. is purchasing 80,800 acres of timberland in North and South Carolina from a fund managed by Campbell Global for $265 million. The acquisition is composed of highly productive timberlands situated in strong coastal markets and strategically located to deliver immediate synergies with existing Weyerhaeuser timber and mill operations. Additionally, the acquisition is expected to deliver portfolio-leading
cash flow and harvest tons per acre within the company’s Southern Timberlands business.
Key components include: —Fee ownership with 89% planted pine acreage and strong site productivity delivering attractive long-term timber returns —Well-stocked timber inventory with a mature age class producing attractive sawlog mix and average harvest of 6.5 tons per acre (or 520,000 tons) annually over the first 10 years —Expected average Adjusted EBITDA of approximately $160 per acre (or $13 million) annually from timber operations over the first 10 years
With this acquisition, Weyerhaeuser will own or manage more than 900,000 acres of timberland in the Carolinas, and the company also operates four mills, a distribution center and tree nursery and hosts multiple mitigation banks and real estate development projects, while employing more than 700 between the two states.
Enviva Will Build Pellet Mill In Bond

Enviva mill building continues.
Enviva, Inc., the world’s leading producer of sustainable wood bioenergy, announced it will invest approximately $250 million in Bond, Miss. to build a new wood pellet production plant. The facility is a key component of the company’s growth strategy to double production capacity from the current 6.2 million metric tons annually to approximately 13 million metric tons annually over the next five years.
“Markets for our renewable products have been growing rapidly as countries look for new ways to reduce their dependence on coal, natural gas, and other fossil fuels for heat and power generation. Demand from manufacturers driving to reach ‘net-zero’ by decarbonizing industrial production of steel, cement, lime, and sustainable aviation fuel is also growing rapidly for us,” comments John Keppler, Enviva’s Chairman and CEO.
The facility site, directly off Highway 49 in Bond, was selected in close collaboration with Governor Tate Reeves, the Mississippi Development Authority, and Stone County officials.
The plant is fully contracted under long-term take-or-pay supply contracts with customers around the world. In addition to creating around 100 local jobs with wages projected to be approximately 70% higher than the county average, the Bond plant will generate more than $1 million in taxes per year for the county and school district and deliver over $250 million annually in economic impact in the region. Once operational, the plant will support more than 350 jobs, including those in related industries such as logging and transportation.
The new plant in Stone County joins two other Enviva facilities in Mississippi, one in Amory, which is Enviva’s first production plant in the state, and the company’s most recent manufacturing facility in Lucedale. The company also owns and operates a deep-water marine terminal at the Port of Pascagoula from which pellets are shipped to customers in Europe and Asia. Combined, Enviva’s total investment in the Magnolia State is more than $600 million and supports over 850 direct and indirect jobs in Mississippi.
Construction is expected to begin in early 2023, subject to receiving the necessary permits, and is expected to take 18 months. The Bond plant is expected to have a production capacity of more than 1 million metric tons of wood pellets per year.
The plant intends to use low-value and low-grade softwood and hardwood fiber sustainably sourced within 75 miles of the facility.
Origin Announces Biomass Facility
Origin Materials, a carbon-negative materials company, announced plans to invest at least $750 million to develop a biomass manufacturing facility in Ascension Parish that will result in more than 1,000 new direct and indirect jobs.
The plant in Geismar will utilize sustainable wood residue sourced partly from Louisiana’s timber mills and managed forests—to produce plant-based polyethylene terephthalate (PET) used in packaging, textiles, apparel and other applications. Hydrothermal carbon, which can be used in fuel pellets, also will be produced at the site.
Made with renewable feedstocks, Origin’s patented technology platform is designed to reduce the carbon emitted during the production of widely used products ranging from food and beverage containers to parts for the automotive industry.
The plant will be located on an LED Certified Site—the 150 acre Parks Geismar site in Ascension Parish— signifying that it has been deemed development-ready after an extensive review. The company expects construction to begin in mid-2023 and for the plant to be mechanically completed and operational by mid-2025.
“The demand for ‘net zero’ enabling materials is extremely strong, and we believe this plant will be instrumental in addressing demand for our products in the United States and internationally,” Origin Materials CoFounder and Co-CEO John Bissell says. “We are grateful for the partnership of Louisiana Economic Development, the Baton Rouge Area Chamber and Ascension Parish for the support they have provided in the site selection process.”
The site sits along the Mississippi River with easy access to barge and rail and plentiful local wood residue feedstock. The proposed incentive package for building in the area is compelling and the local industrial cluster can provide access to hydrogen, ethylene, water treatment and more.”
Headquartered in West Sacramento, Calif., Origin Materials was founded in 2008. The company has partnered with leading consumer brands including Danone, Nestlé Waters and PepsiCo in its creation of recyclable, plant-based PET plastic consumer products, as well as Ford Motor Co. and global chemical companies. This largest-of-its-kind Geismar-based facility will join the company’s network of locations, including its West Sacramento-based pilot facility and its Ontario, Canada-based production site, which is currently under construction.
Increase Log Trailer Visibility
Make trailers stand out to help prevent accidents
Every logger operating a log truck needs to be diligent about making sure their vehicles are conspicuous and easily visible in virtually all weather and light conditions, especially the log trailers. The time of day or weather can create conditions that make it difficult to stand out to other drivers. In the event of a crash, whether or not it’s an “at fault” accident, you can be sure the plaintiff’s attorney will introduce, explicitly or implied, that their driver did not see the truck/trailer. Why? The lack of or poorly maintained conspicuity tape, inoperative lights, reflectors, or obscured lamp lenses among others.
Inspections Work: Do It
To discover unsafe conditions, drivers should perform pre-and post-trip inspections. Inoperative lights and lamps (tail/brake, turn signals) are commonly noted during many DOT roadside inspections as being: broken, having missing reflectors and high visibility tape issues. These are especially common in heavy duty log hauling applications. Always check for these issues before leaving the yard or work site.
Maintenance
It is highly recommended that drivers have the necessary replacement and repair parts with them to act immediately. Keep extra bulbs, lenses, reflectors, and a supply of reflective tape on hand.
Periodically, drivers should wipe off the reflectors, lenses, and tape to ensure visibility. Another tip is to replace filament bulbs with LED bulbs to increase serviceability and brightness.
Reflective Tape and Lights
In 2001, TheNational Traffic Highway Safety Administration(NTHSA) conducted a study on the impact of using reflective tape on trailers. The results concluded that the consistent use of reflective material would prevent over 7,800 accidents per year and 191 fatalities. The study reported that tape is quite effective and significantly reduces side and rear impacts into heavy trailers in the dark.
Inaddition to the DOT requirements at the federal and state level, for good measure add reflective tape to the rear bolsters, covering at least 50% of the height of the bolster. Add a beacon light centered on the rear of the trailer and use it, whether loaded or empty, before dawn and after dusk or when weather conditions dictate to make your trailer more visible. If your drivers often forget to turn on their beacon lights, the lights can be wired to activate when the truck’s ignition switch is turned on.
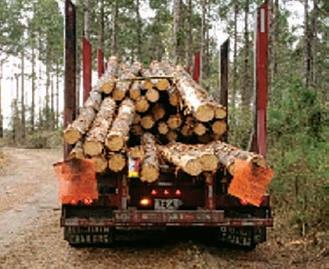
Always inspect lights, reflectors before hauls.
Excessive Speed Causes Fatal Accident
Background:
A truck driver was hauling a load of wood chips to a local paper mill. It was a clear winter evening in the Appalachian Region. Weather conditions were not a contributing factor.
Personal Characteristics:
The accident victim had less than one year of experience as a truck driver. The driver preferred to travel at night and had authorization for late shift transport.
Accident:
The truck was traveling north on a four-lane highway separated by a grass median. The posted speed limit was 55 MPH. The driver entered a slight left curve, and upon exiting the curve, drove off the road striking the guardrail in the process. The cab and trailer rolled over onto its right side. The entire rig slid down the grassy shoulder of the highway and eventually came to a stop while still on its side. There were no witnesses to the crash. A passing motorist discovered the accident scene and called 911. The accident investigators estimated the driver’s speed was 75 MPH when the truck left the road.
Injury:
The driver was ejected from the cab during the crash and was pronounced dead at the scene by EMT personnel. It was determined during the accident investigation that the driver was not wearing a seatbelt.
Unsafe Acts/Conditions:
The driver’s speed was estimated to be 20 MPH over the posted speed limit. The driver was not wearing a seatbelt.
Recommendations:
Always abide by posted speed limits. Always wear a seatbelt when traveling in a moving vehicle.
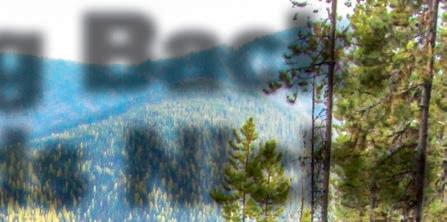
No Looking Back: J Shar Finds Niche

Brothers Jared and Matthew Fitchett run a tether-assisted CTL job on steep Montana terrain.
DAVIDAbbott
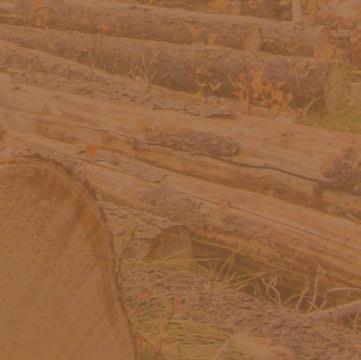
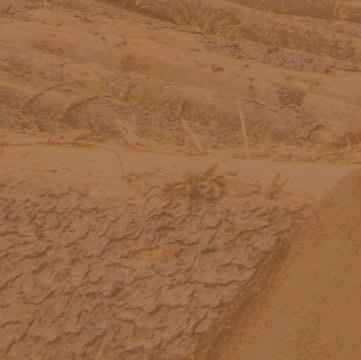
LIBBY, Mont.
Rising to new opportunities is a hallmark of the Fitchett brothers: At J. Shar Timber Harvesting, owner Jared Fitchett, 39, works with his “little” brother Matthew, 33 (little is misleading; Matt stands 6-foot-7). Their dad, Dan, 67, hauls his sons’ production under his own company, Dan Fitchett Trucking, using a T800 Kenworth with Pierce mule train trailer. Jared has his own truck as well, a 1984 Mack with Alpine short log pup, that he drives when needed, and Matthew is getting his CDL, too.
The Fitchett brothers man a Ponsse CTL team, using tethered cable winches to access and stabilize on steep slopes. Both the harvester and the forwarder have cable winches attached, tethered to an anchor, either a good stump or another machine (they have a spare John Deere track loader that can serve this purpose when not otherwise in use).
The winches are by Herzog Forsttechnik in Switzerland. “They are a very small, family-owned company,” Jared says. “A father and son custom build these when you order them.” The winches were $140,000 each; it’s a little less to buy a new machine with it already installed, but these had to be modifi ed to retrofi t on used machines (buying new was out of the budget). The Fitchetts have a Bear harvester and an Elephant King forwarder.
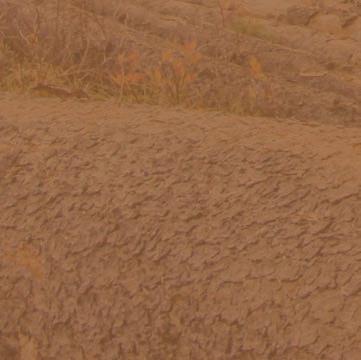
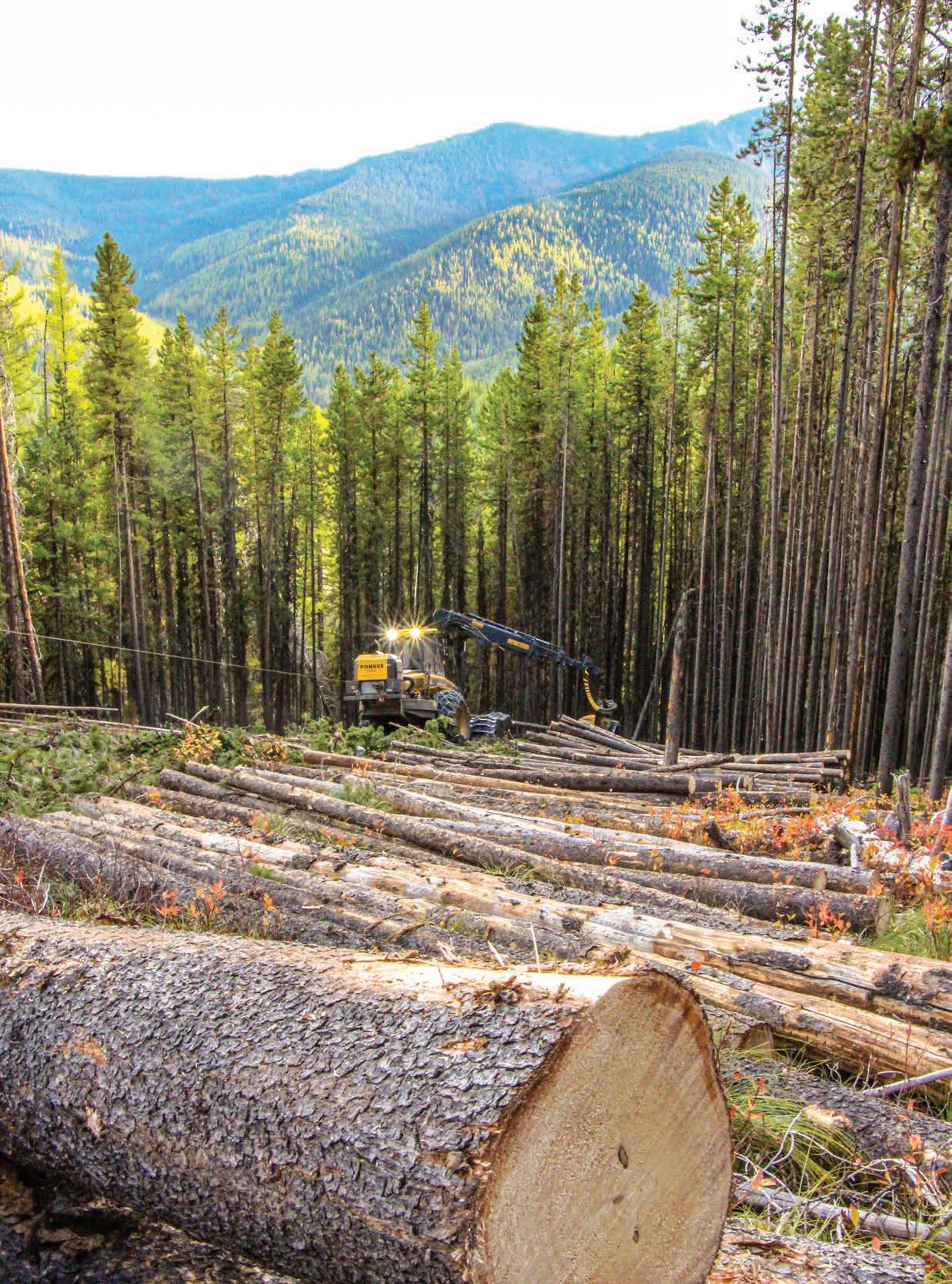
The cable, Jared emphasizes, is to assist: to increase traction and stability, not to pull a machine up the hill— the winch only has 10 ton max pull. Slopes are steep, but not vertical. The grade on the job they were working in October was between 40-60%. “The maximum recommended (safe slope for tethering) is 70%, and we don’t like going over 60%,” Jared says. “Anything over that is questionable. We should not be on any ground where that machine cannot sit on its own if that cable fails. You hook up and before you tighten the cable, slack the cable manually and if that machine tries to slide or move then it is too steep. It is unsafe and should not be on that slope.”
J. Shar has been using the tethered assist system since mid-late 2020. Jared believes his company was the fi rst, and maybe still the only, such operation in Montana. “Some other systems started up recently but we are the only cut-to-length tethered system in Montana right now, and the only six wheel Bear with winch assist balanced bogies in North America, to my knowledge.”
And he has no intention of going back to how he did it before. “This is our future, and I think it will be a lot of people’s future once they see the outcome of the operations that are in place right now,” Jared predicts.
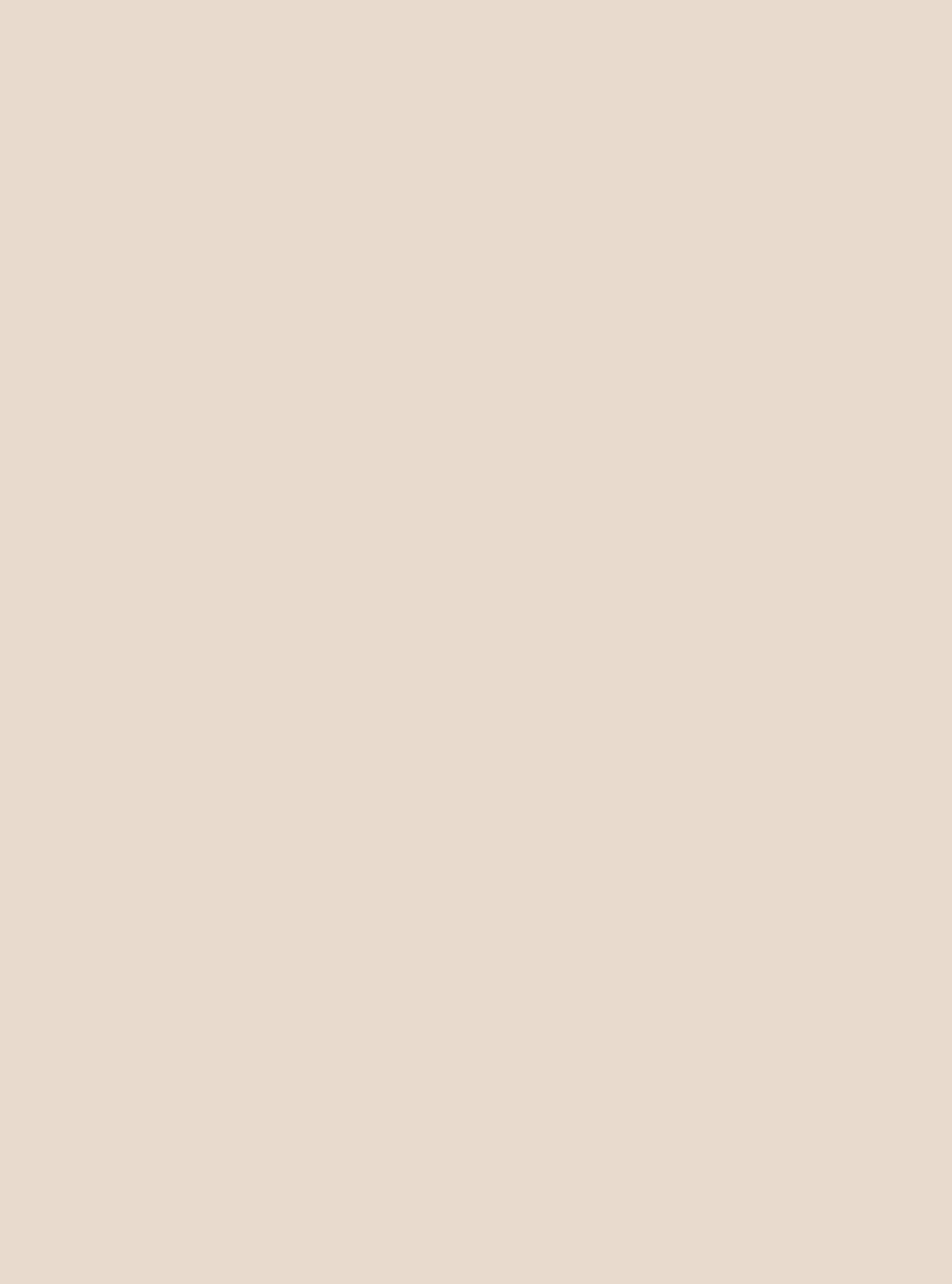
The Show
Before he was a tethered CTL logger, Jared Fitchett was a TV star. He was one of the loggers on the Discovery Channel series Siberian Cut, which fi lmed and originally broadcast in 2014. Nine episodes were produced but only six aired in the U.S.; all episodes aired in Finland, Russia, the UK, Asia and elsewhere. You can fi nd it now on YouTube and Hulu.
The opportunity came at the right time in Jared’s life, when everything in the business was going wrong. Back then they were still doing conventional treelength logging, felling with chain saws, and it wasn’t going well; there had been many years of struggling. So he thought, why not try something different? “My thinking was this could help my family,” he relates—whether it was just making money from the show to reinvest in the business, or, he hoped, he might make useful connections with someone or learn new ideas or methods that he could bring home and implement to help his business be more successful at home.
He turned out to be right. His experience on the show altered his entire approach to logging. The U.S. loggers selected for the show departed for Russia in the middle of January. First, producers sent the team to Rhinelander, Wisc., to train on Ponsse cut-to-length machines for two weeks. There he formed relationships with members of the Ponsse North America team: Pekka Ruuskanen, Brad Brown, Jouni Viitikka, Diana Olkowski in marketing and her husband Matt Olkowski in tech support. “I got to meet all those really good people who I am still close to today.”
His switch from treelength to CTL logging started there. “That fi rst two weeks in Rhinelander already got my mind rolling about just what I could do at home with that equipment,” he recalls. “Before I left I told Pekka I would like to pursue this at home.”
Jared and the crew—two other Montana loggers and one from Oregon, none of whom knew each other before—fl ew to Siberia for almost three months to make the show, logging on Russian Federation land. The American loggers worked with a Russian crew, only one of whom spoke English. “It was extremely diffi cult,” Jared recalls. “And of course being a TV show they wanted it to be diffi cult, to create drama. We knew going in there would be some of that but it was way worse than we ever imagined. You’re in a foreign country; you don’t know how things work. Me being an independent logger, I am used to fi nd-
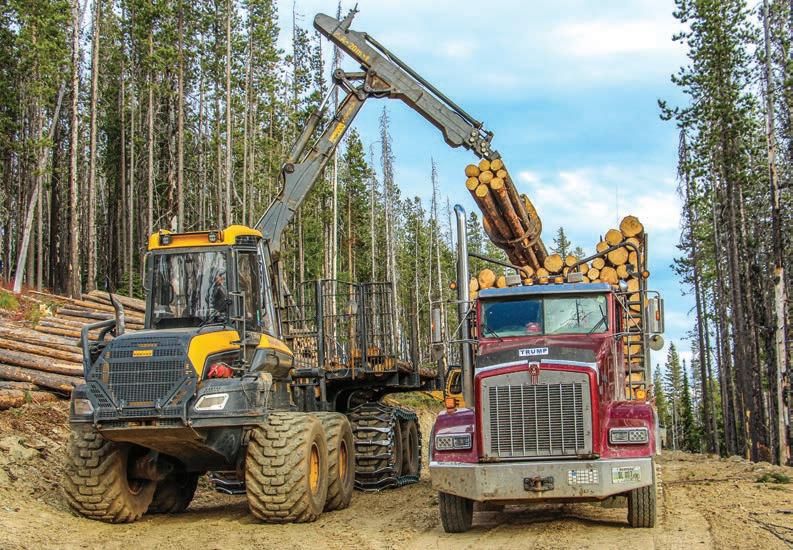
J. Shar Timber Harvesting switched to CTL logging eight years ago.
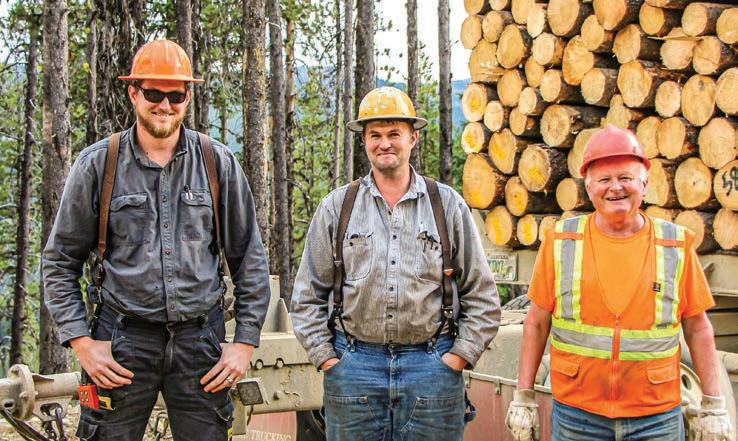
From left: Matthew, Jared and Dan Fitchett

The Fitchetts have used the tethered-assist method for the last two years, and say it’s their future.
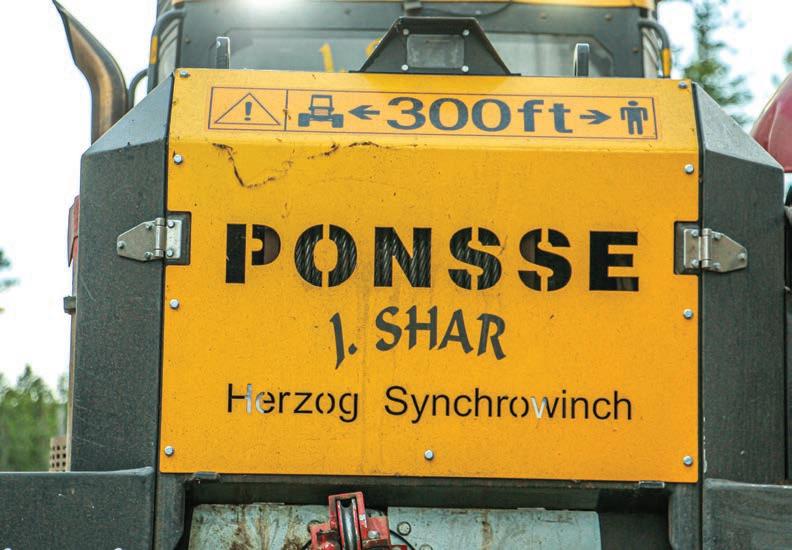

The winches, by Swiss company Herzog, were retrofi tted onto used Ponsse machines.
ing my own way. You don’t know what (the Russians) are saying about us, or what they have been told about us. We are stuck with each other for three months, living in a woods camp, all in the same trailer. It was very interesting and aggravating.”
Long story short, he says, the show came out that summer and was something less than a hit. But he got out of it exactly what he’d hoped: some money to reinvest, and more importantly, connections and ideas. “The show didn’t do worth a damn, but in between that time I was still communicating with Ponsse.”
Gone CTL
After three tough months away, Jared returned home in April 2014 and went right back to work. Spring breakup was over, and he knew he wanted to evolve into a CTL operation. Ponsse’s Ruuskanen visited J. Shar.’s operation in June. Jared sold every piece of equipment he had in October; by November he had his fi rst harvester, a used six-wheel Ergo with 17,000 hours. Their fi rst forwarder was a ’95 Timberjack. “It was 20 years old but it was the only machine they had available at the time,” Jared says. “We made it work.” They ran it for 13 months, then replaced it with a rebuilt Buffalo. “It was nice,” Matthew recalls. “It was almost like a brand new machine.”
Since then, the Fitchetts have upgraded to the Ponsse Bear harvester and Elephant King forwarder they use in the tethered system today. It’s been almost eight years since the CTL conversion, and the brothers have no desire to go back to conventional logging. “It’s the best thing we ever did,” Jared asserts.
Ponsse has no dealer network in Montana. The closest is in Oregon, 12 hours away, but the Fitchetts still deal with Rhinelander, 18 hours away. “We have driven back there with broken parts,” Jared says. “We broke a differential after we got the Bear; I hauled it to Gladstone, Mich., and they rebuilt it right there; it was a two and a half day drive. They had the parts from Finland overnighted.” He doesn’t mind the distance. “In the past seven years that whole area, the Lake States, has become a kind of a second home for me.”
Still, the brothers tackle 99% of repairs and maintenance themselves. “Anything we don’t understand, we talk to people on the phone like Matt Olkowski, Brad Brown and Jouni Viitikka; they help us with anything we can’t fi gure out,” Jared says. “We have always been able to fi gure it out over the phone and keep running. They have a very good overnight for parts.” J. Shar. is insured through the Montana Loggers Assn. and PayneWest Insurance in Kalispell. Dan Fitchett Trucking gets insurance through Associated Logging Contractors of Idaho.
Operations
J. Shar. works about seven months a year on private commercial land and three months a year on federal land. “We could do more (on federal land),” Jared says. “But we have built such good relationships and have such a good future on our private industrial thinning.” The private land they primarily work is now owned by Green Diamond Resource Co. and managed by American Forest Management. The federal jobs are for Thompson River Lumber, a mill in Thompson Falls.
“We are lucky to work 10 months a year, due to spring breakup,” Jared says. During those months, they work on machines, take time off for family and pinch pennies. “Breakup is a very
tough time because if we don’t do good enough in the months we’re working, breakup can literally break you.”
And, Matthew points out, there’s no knowing how long it can last. “Sometimes it might last a month and a half, sometimes three months,” he says. “So you have to be prepared to survive during that time and you never know when exactly you’re going back to work. Then summer hits, it’s hot and dry and we get restrictions because of fire, so it is tough.”
Last October, when Timber Harvesting visited, J. Shar. was working on federal land, 18 miles of winding gravel road uphill and around the Cedar Creek elevation. The timber here, predominantly lodgepole pine, was 100-120 years old. “Some of it should have been harvested 20 years ago because a lot of it is dead or dying now,” he said. “If it wasn’t a government tract it would have been.”
The small diameter stems here are very high value and sought after as post and pole material because it is very straight with tight grain. “Even the dead wood, they are able to recover lumber out of some of that,” Jared says.
Sawlogs and dead logs from this job went to the Thompson River mill, about 80 miles away, a 5.5-hour round trip. Post/pole material went to a small plant in St. Regis, a 30-mile drive. “Dad can get two loads a day, and if it is green wood, he can haul 35 tons,” Jared says. “We try to focus on 70 tons a day, but we do more than that. We average 70-100 tons a day, depending on the job. What we are cutting here, if it was all green, it would be 100-plus tons a day, but not with how light the dry dead wood is. We’re moving that much in volume but not in weight. The dead is 50% lighter than the green, and we get paid by weight.”
On jobs like this one, the brothers live in a camper in the woods during the week, going home on weekends. Jared lives in Libby, Matt in Columbia Falls, north of Kalispell, and Dan lives in Marion between Kalispell and Libby, so this job site was quite a trek. The rest of the year, on private land jobs, they work within 100 miles from home.
The company has an active presence on social media: look them up on Instagram and Facebook to see videos and photos they post. Matthew also takes a lot of overhead aerial footage with his drone. They use this content as marketing for their business, for the industry as a whole, the Ponsse brand, and the tethering method.
The drone is also useful in scouting potential timber tracts. “We use it to look at some of these sales ahead of time, with aerial views to see what we’re getting into,” Jared says. “For instance here we could pick out how much dead is in it, which was kind of hidden on the ground.” Matt adds, “Sometimes we walk in and think it’s not too bad but then you fly over it and see a whole different view. We use it to help plan pricing and what the wood quality might be.”
Originally, Jared called his company Jared Fitchett Logging. “But I wanted to change that,” he says. “I wanted something unique, not just my name.” His dad suggested an abbreviation for Jared and his wife’s name, Sharlyn. “I call her by her full name, but everyone else calls her Shar.” In 2005, not long before they were married, he renamed the company J. Shar. “It’s something different.” TH

