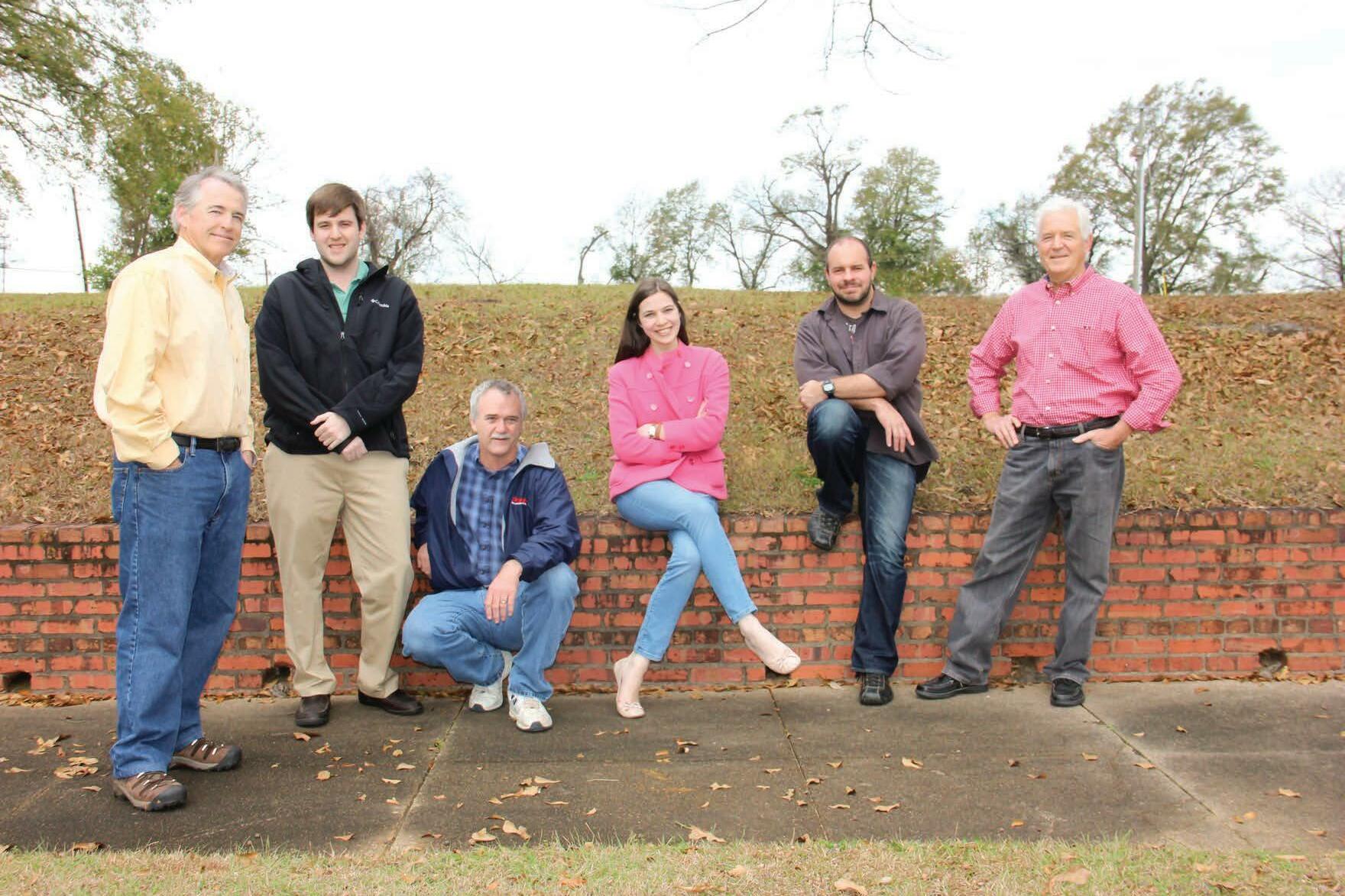
36 minute read
Southern Stumpin’
By Jessica Johnson • Senior Editor • Ph. 334-834-1170 • Fax: 334-834-4525 • E-mail: jessica@hattonbrown.com
What’s Next?
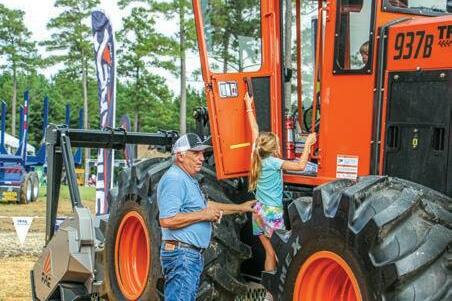
NOTE: This month Jessica Johnson (our youngest editor, even though she’s been at it 10 years) asked to tackle the Stumpin’ column. It was her idea to focus on young loggers and the future of the industry, after the last two issues referenced older loggers retiring or considering it.
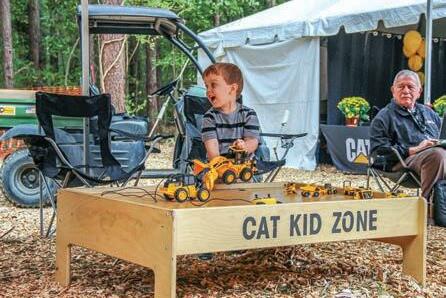
As I look at my little boys I often think about what’s next for them; how can I set them up for success? Is playing ball their future? Am I doing right by forcing them to eat zoodles? In my personal life, in the daily grind, it is easy to see how fast (and slow) time moves. I know one day I will no longer be my kids’ taxi service and will be ugly crying at their high school graduations. But that’s expected: the natural order of time marching on.
This industry is a bit different. The natural order of cut-skid-load is not going to change, and neither are the numbers coming into the bank—even though the numbers going out are only getting higher and higher.
You might not see my name as much on these pages as you used to, but don’t worry. I’m not gone. I’m also not a casual observer of this industry like I once was. As I’ve become more intimately aware of the daily inner workings of owning a multi-crew operation in recent years, I’ve thought about what’s next: where do we go from here? How is everyone going to survive?
Things are getting tough. A “good” year now means hopefully not a greater than 10% loss. Woods hands and truck drivers are scarce in every corner of the South. What happens when there’s no one left to run the machines? Will the mills finally raise rates then? Loggers are working 16-hour days, making sure they are keeping every dime they can.
We might never be able to bring back the logging glory days of the ’80s and ’90s (which, if you ask me, some of those hairstyles at least shouldn’t be considered the glory days).
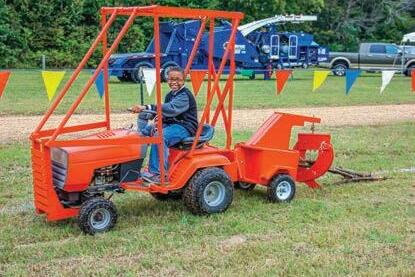
Future loggers of America
The Future Is…Cloudy
I was told recently that my generation, our generation of “young” loggers, is just getting started. The world needs paper towels and biomass energy. Things have been bad before, but we’ve always made it through. And we will make it through again.
The future is in the forest. We just have to figure out how to make the most of it, to get everyone, from California to Maine, Wisconsin to Washington, DC, to little towns like Dodson, La., and everywhere in between, to agree that wood is good. When logging towns and logging families thrive, America thrives.
While I have a few fancy college degrees that I will have hopefully paid for before I die, I’m by no means a fancy thinker. And since I have a lot of questions and not a lot of answers, I figured I’d ask a few friends to help me out. What’s next for logging?
More than a few of them told me they really didn’t know what to do. So they’re doing what they always do—get up, go to work and advocate for themselves and their employees and families. One logger told me, “I don’t have to log and my woods crew knows it. But I always will because that’s what my family has always done.” But another said, “I won’t go broke doing this. It’s not worth it. If there comes a time where I have to quit, I will.” So how do we find the middle ground?
Mississippi’s Drew Sullivan told me he was scared to death about the future for all of us. “I sound like doom and gloom, but it’s scary,” he added. “This is all I know how to do. Our whole livelihood is wrapped up in this. I want to log; I love to log. I don’t want to get out. I don’t want to
walk away from it. We’re not behind, but we’re not making any money. You can’t save. Ever since Covid, I cannot get ahead. We pay the bills and make a mediocre living.”
Sullivan said he has noticed a trend: mill companies setting up their own logging crews. It’s a trend I’ve seen in other parts of the country, but not so much in the South. I am not naïve enough to think it hasn’t started happening here though. There aren’t many 25 year-olds who can go to a bank and borrow the needed $1 million to get a logging job started. And let’s not forget the issue of finding good employees. The barriers to starting a logging job are far greater, it seems, than starting about any other business in America. No wonder most young loggers are second or third (or fourth or fifth) generation operators.
Whether they come from a long line of loggers or not is irrelevant. By and large they are overworked, trying to still do more and more, feeling like it doesn’t matter. When asked about a plan, most of the guys I spoke to said they didn’t have one. Sullivan laughed, “If you find anyone that has a plan, let me know their secret so I can make my own plan. I wish I had a plan. The plan is to keep running. We’re in survival mode.”
Sullivan, an active member of the Mississippi Loggers Assn., did say one of his plans is to stay engaged with the group. He is a big proponent of the idea that the collective voice is stronger and louder than a single person shouting. And, in my opinion, he’s right. Sticking together for a common goal has worked throughout history. But, when you’re talking about a group of people who make their living 15 miles off the paved road, I can see where it might be a challenge to get them together. Yet, the work of David Livingston in Mississippi, Toni McAllister in Louisiana, Crad Jaynes in South Carolina and all the rest of the incredibly important association folks will be a critical piece of the puzzle for the future.
Sullivan says he’s noticed that some of the older guys are perhaps hesitant to rock the boat with the big companies—or maybe they’ve just been fighting for so long they don’t have a lot of fight left. Either way, we, the young ones, have to keep fighting. To keep moving forward, we have to have a goal—a vision for the end of the
line. I don’t know what that vision is. I want more paper to be used, in schools and in our homes. At work and at play I want to see things made of wood. I want to continue to see housing starts of single-family homes rise. I want to learn more about mass timber innovations and how influences of the forest can calm the senses. I want to not just buy a candle that smells like a tree. I want to see trees growing in planted rows as far as the horizon when I drive just 45 minutes from any major metro area in the South.
I did not grow up in the industry. I did not grow up in a small town. For generations us Johnsons have worked good honest jobs, but not 16-plus hour days six days a week in the elements. The powers that be of Southern Loggin’ Times took a chance on me, and I found my little place in the world. Southern logging got me a decade ago, and for better or worse it’s going to have me forever. Let’s knock some dents in this universe together. Let’s figure out what’s next and go for it, all guns blazing. And know I’m cheering for each and every one of you—every one of us—because the future is the forest. The future is you. What’s next? SLT
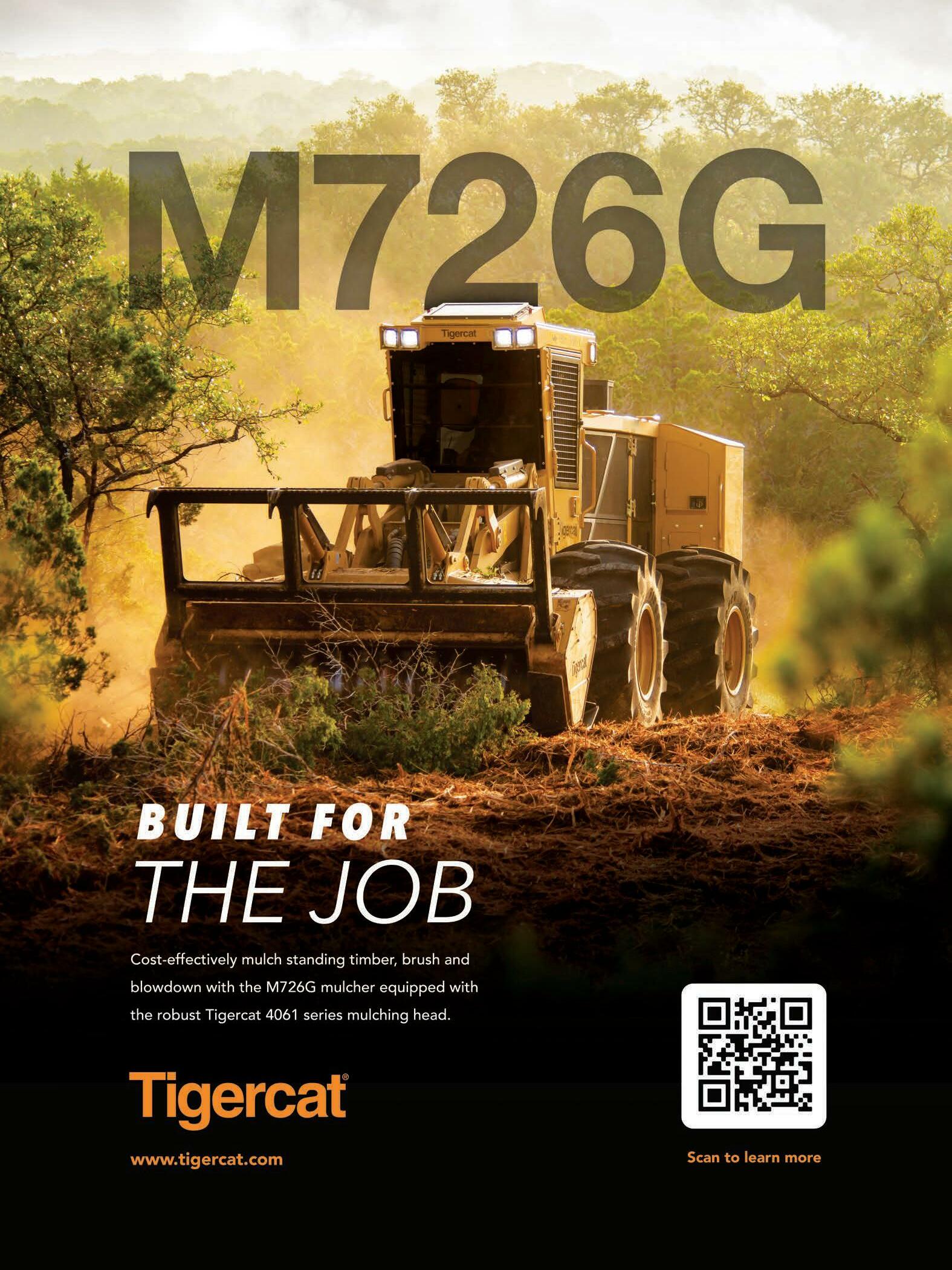
Young Gun
■ Optimistic young logger Rick Bennett is glad to get his shot and eager to prove himself.
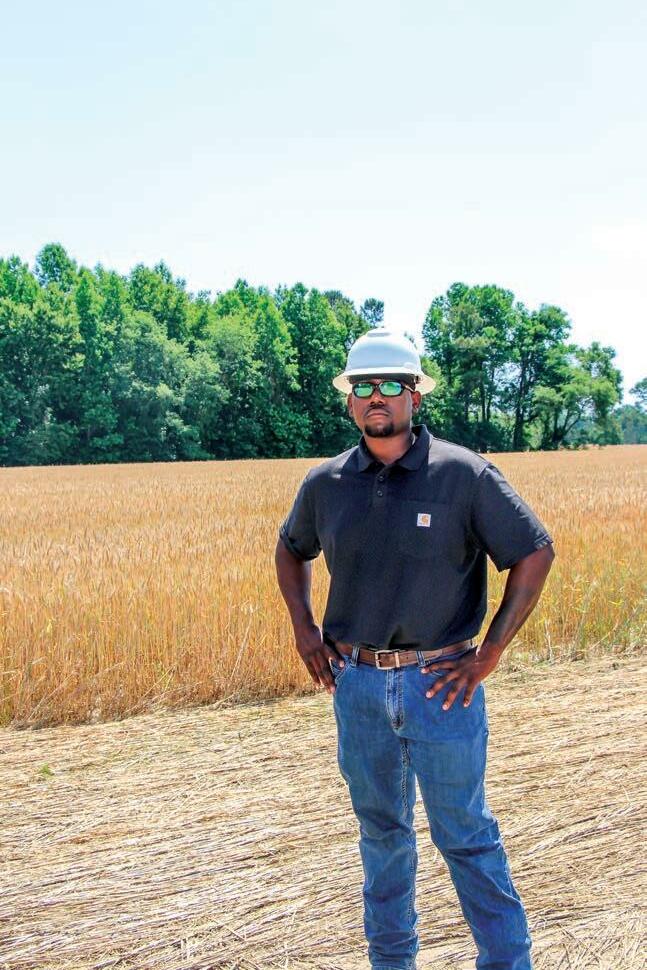
By David Abbott
SUMMERVILLE, SC
Rick Bennett, 29, embraces his identity as one of the younger generation of loggers. In one sense, he’s super green: Bennett just started his company, Bennett and Sons Logging LLC, in October of 2021, less than a year ago. But in another sense, he’s far from a novice. In fact, you could say he’s been preparing for this his whole life.
First of all, he came from a long line of loggers, though he is the first in his family to have his own company. “My granddaddy is real proud,” he smiles.
“I remember being a little boy, going out with my granddad on some jobs. My granddad, all my uncles, they had been in logging and forestry many years. I heard so many stories of going in the woods with just a saw, a can of gas and a lunch pail, and stumping trees by hand, loading trucks by hand. I used to hear those stories when I was young and thought, ‘Oh, I want to do it!’”
When he finally came of age and finished high school, he knew college wasn’t for him. Another logger in the area, Steve Moran, owner of Steve’s Logging, gave him the opportunity to learn the trade. With 30+ years in the business, Moran became a mentor to Bennett, and the younger logger appreciates it. “I call him dad,” he reveals. Bennett started out as a deck man trimming trucks. “I didn’t know anything but I was real eager to get on equipment,” he recalls. “When the guys would go to lunch I would hop on a skidder or the cutter and play around for a little while; that was how I learned everything.” Eventually, Bennett became a foreman for Moran’s crews.
After four years, though, he had to try a different direction, mainly be cause he’d become a father, he ex plains. “At the time logging didn’t have the benefits, so I stepped away to try to better myself.” He got a job in safety at the DuPont plant in Moncks Corner, where he spent another four years.
The new job made sense, but his passion was for the outdoors. “I love to fish and hunt and logging had always been in my family, so it was something I always knew. As a kid I wanted to be a logger. But I just didn’t see a way I could get into it. You’re talking four pieces of equipment nowadays is over a million dollars. Someone my age walking into a bank, it’s a big risk for the bank, for yourself, for everyone involved.”
Still, he couldn’t escape it: he didn’t want to sit in an office the rest of his life. His heart, he realized, was still in the woods, where it had always been. But he knew he didn’t want to work for anyone else anymore. “I wanted to do it for myself. So I decided, if I’m going to go back into logging, I need to figure out what I need to do to have my own job. I set that goal the last year at the plant, and in six months I did it.” His old boss, Moran, and wood dealer Claybourn Walters Logging Co. of Fairmont, NC, helped him get started, and he took it from there.
Since then, Bennett says a lot of people around his age ask him how they can get started like he has. “I always say it’s not easy, but if you got the want to, you can figure it out. Work on someone’s job and work hard, and learn logging. Respect it. Learn that it is a natural resource. Maybe one day you’ll get lucky like I did and someone will notice your hard work and work ethic.”
Perhaps not surprisingly, some of his elder peers in the industry don’t share his optimism. “A lot of the older guys in the game will try to push you away from it, especially right now with fuel prices and insurance costs and trucking. They’ll say, ‘Aw, you don’t want to get into logging.’ But without young people like me, the industry would go down. So I always encourage everyone who comes to me and asks me about it.”
His advice to those interested in trying: “Save your money, and be smart with your credit. Most young adults don’t pay attention to credit. I was one who didn’t, I will be the first to tell you,” he admits. “But if you can get a hold of that at a young age and start establishing credit, and find
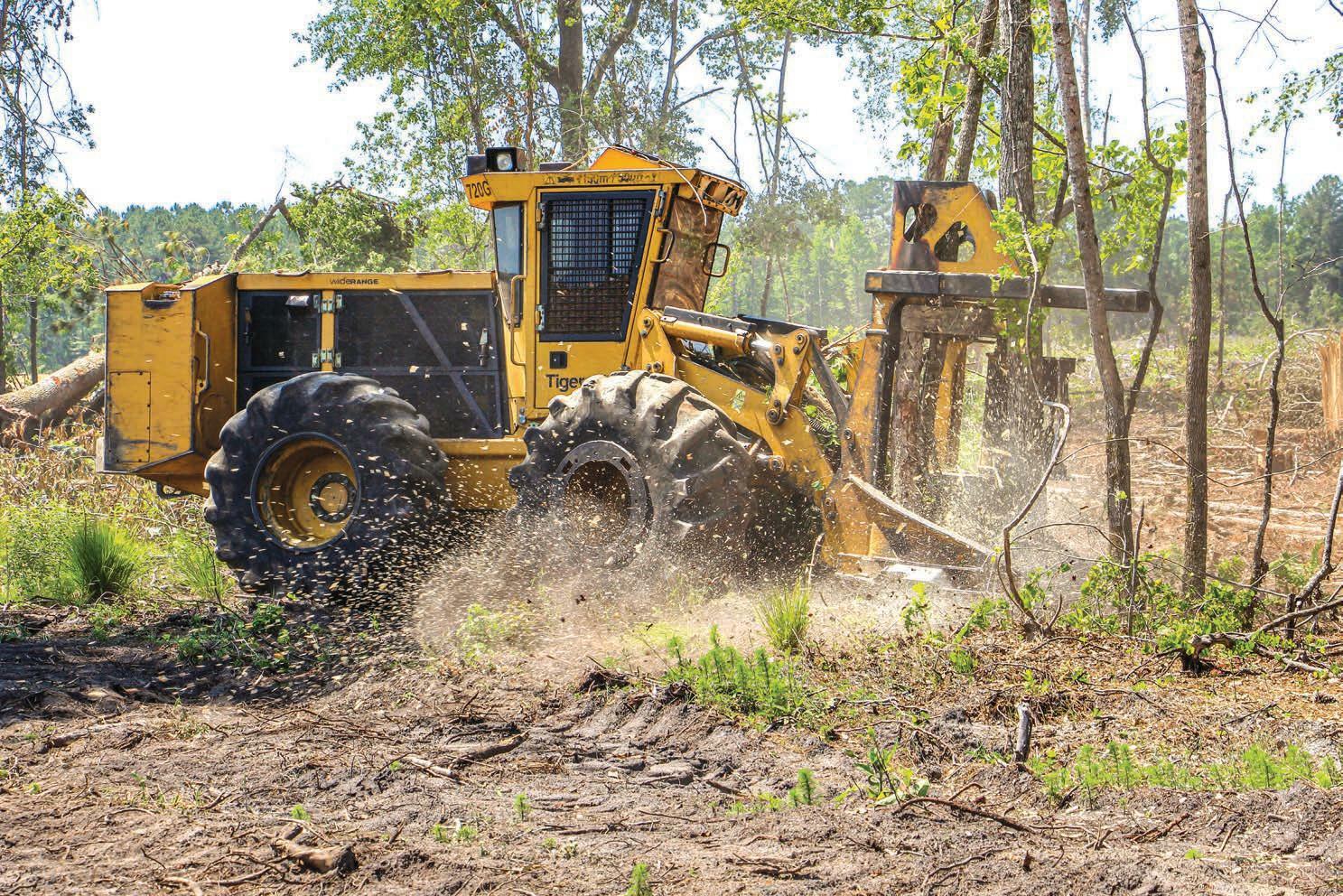
Rick Bennett
Bad Timing
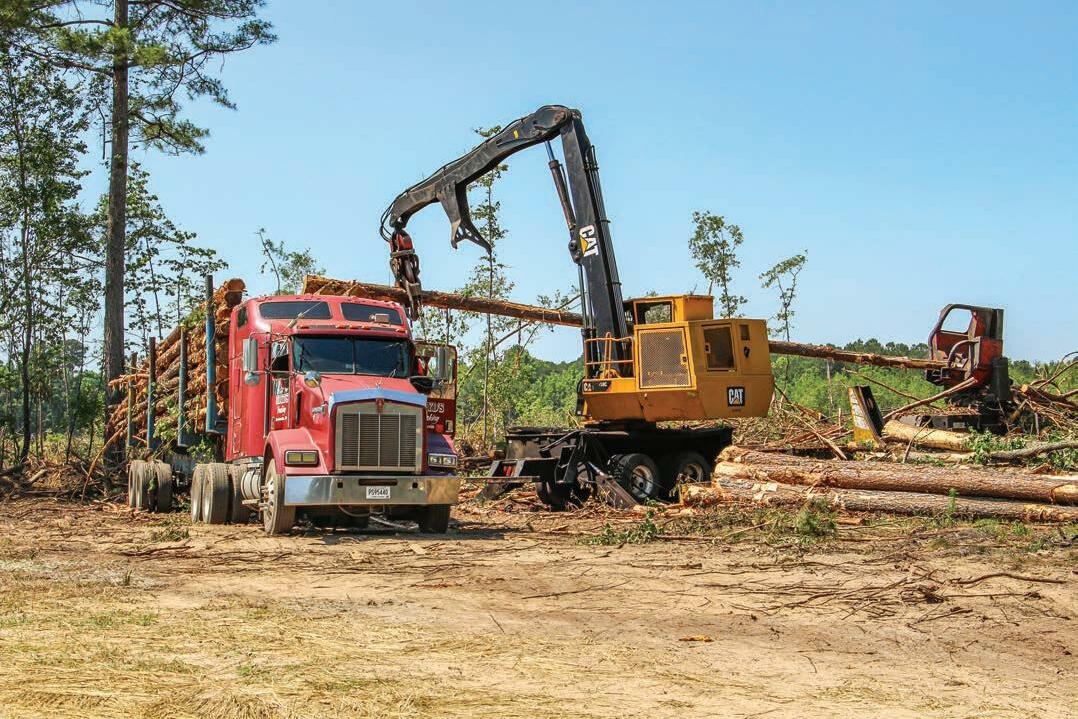
Getting started is even harder these days than normal, Bennett acknowledges, but adds, “If you have a good support system, someone who recognizes your hard work, there are opportunities; you just have to work for it. I don’t think I could make it without a good support system. If it wasn’t for Mr. Steve, Claybourn Walters, my granddad introducing it to me, I don’t think I’d be doing it. I appreciate all they’ve all done to push me and drive me.”
In many ways, 2022 is shaping up to be arguably worse than the “great recession” of 2008—higher fuel cost, higher insurance, out of control inflation, supply chain delays, labor shortages, and so on. So what’s it like starting a new business in the midst of one of the more challenging business environments for loggers in a generation or more? “It’s stressful at times,” Bennett admits (that is perhaps an understatement). “Especially right now with fuel prices going up, and the trucking. It’s not just fuel. The cost of living, the price of hy draulic oil, the price of parts, and you can’t get parts; it’s all making it more challenging. But I want to stay in the business so every day I wake up and figure out what I can do to keep going.”
Despite all these problems, forest products mills are still making great profits, but it doesn’t trickle down to the raw material suppliers—and that fact hasn’t gone unnoticed. “That’s the biggest thing that all of us loggers, especially someone small like me, we scratch our heads with everyday,” Bennett says. “The mills give you a little bump here and there, but by the time they give it to you, it’s too late.”
Understanding that he represents one link in the supply chain, Bennett says he can relate to contract haulers. “There’s not a lot of new drivers and it’s hard to find drivers with a good driving record, with insurance. The younger guys, why would they drive a log truck when they can drive for Wal-Mart and make $100,000 a year? Our industry has to be competitive and we need young people like my self to thrive and push it. So when I do get a bump (from mills), I am going to generally give it to (the truck drivers). Without them I can’t get my wood moved.” It’s an understanding that consuming mills could perhaps stand to emulate.
It seems in Bennett’s nature to look for the silver lining, and he applies that positive outlook to the current state of affairs. Basically, he figures, if he can survive this, he can survive anything. “We will take the good with the bad, and I am pretty confident that I will get through it. Once I do I’ll take it as a lesson learned. I’m kind of glad I went through this early in running this business. If I make it through how the economy is now, it will help me learn that if something like this happens again, I will know what I need to do to keep pushing and go through it.”
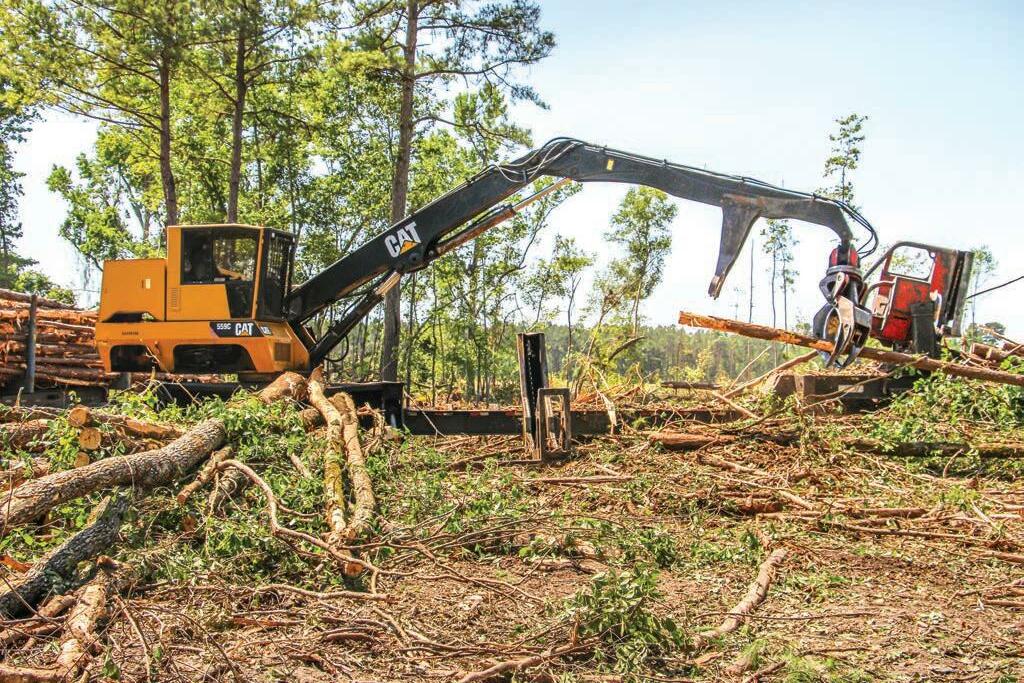
Blessed with short hauls to partially mitigate high fuel costs this summer, Bennett hauls about 40 loads a week with contract trucks.
The young logger bought his equipment used from other loggers.
Operations
Bennett bought all his equipment used from other loggers. “When I got started, that was something I looked into: do I need to buy new equipment? When I looked at new equipment, I realized that the notes on new equipment, with what I could haul a week, wouldn’t make sense on paper. So I went the used equipment route.”
Bennett grew up in Moncks Corner, near “the famous” W&W Truck & Tractor, he says. He hasn’t bought anything from an equipment dealer yet, but he does look to W&W for parts and other support. “They are a lifesaver when you’re in a pinch or in a bind, you need a part, especially right now with parts where you can’t get it.” For repairs beyond his knowledge, he also looks to Tidewater Equipment branches in Conway and Walterboro, whichever has time to get to it first.
The logger handles most minor repairs himself on weekends, while operators do routine maintenance at the end of each day. “This equipment takes a beating,” Bennett says. “For estry equipment is the roughest. I look at things just to make sure. You might miss a crack or a bearing gone bad, and if you can catch it early it saves you thousands of dollars.”
His machines include a Caterpillar 559C loader, Tigercat 720G feller-buncher and Tigercat 630E skidder. He bought the skidder and cutter used from Steve Moran’s son,
who had been in the business but decided logging wasn’t for him. Bennett got the loader from another logger who want ed to upgrade to something new. Moran and Walters helped him get financed. “They have done a lot for me.” On the day SLT visited in late May, Bennett and his team were working outside a wheat field. “This farmer has about 35 acres and he is wanting to expand his field,” the logger explains. Normally he doesn’t cut tracts this small, he says, but the mill (WestRock in Florence) was only six miles away, and with fuel prices so high, the short haul distance made too much sense to pass up. The tract was a mix of pine SLT SNAPSHOT and hardwood. “Right now that’s what you want,” Bennett asserts. “You don’t want a full pine tract; if the mill gets Bennett and Sons Logging LLC backed up, all your trucks are bennettscontracting.llc@gmail.com waiting there. You want to have a little bit of a blend. That’s Founded: 2021 Owner: Rick Bennett No. Crews: 1 really my goal.” Besides the Florence WestRock mill, other mill outlets are also typically under a 35-mile haul from most Employees: 3 tracts. Regular destinations Average Production: 40 loads/week include Willowcreek Lumber Average Haul Distance: 35 miles Tidbit: Rick Bennett comes from a logging family, but he is the first to (sister to Charles Ingram Lumber Co.) in Effingham (near Ingram) and Canfor in Conway. “We do haul some wood to own a company of his own. Georgetown (International Paper), and every blue moon
we go haul some hardwood up to the IP mill in Eastover, but that’s a long haul, about 80 miles from here.”
The young logger owns no trucks of his own as yet, relying solely on contract haulers, four of them for now. “As far as trucking goes, I knew a couple of guys who were committed to coming with me,” he says. “I take care of them and they take care of me.” Anything under 35 miles he pays them a flat rate, and anything over that he pays by the mile. They haul around 40-45 loads a week, or around 35 on a bad week, he figures.
On the crew, Joe Woody mans the loader, Trey Lewis drives the skidder, and Tremaine Lavine runs the cutter. Woody and Lewis are experienced vets in the woods—they’ve been at it longer than their employer has been alive. It’s a valuable asset for the young owner. “A lot of times if I get in a bind, they make it so easy. I love having their experience out here.” Bennett himself runs for parts and fills in on machines when needed. No matter what, he is out here every day. “I have to be on the job,” he says.
Swamp Fox Agency in Moncks Corner handles his insurance needs. “They’re a real good company,” he says. “They cover everything. When I first went in, I started getting quotes on equipment, and insurance was the next thing.”
Those years he spent away from logging weren’t wasted; he learned lessons at the DuPont plant that he’s applied to logging, particularly in terms of safety. “I was sent to OSHA school for the plant. One of my good mentors at the plant was Brandon Blackmon, and a lot of things I learned from him relate here.” He says other loggers sometimes call him to speak to their crews about awareness because they know he has a safety background.
With his own crew, he goes over two topics every Tuesday and Thursday. Also, every morning they talk about things that can present a danger. “We talk a lot; the main thing with safety is you got to communicate,” he believes. In the woods his men wear safety vests and other PPE; chaps usually aren’t necessary as they hardly ever do any chain saw work. “If we get in a hardwood tract and can’t get that big wood in the delimber or buck saw we just top trees with a saw. It’s very seldom, but when we do we wear the right
PPE.” He also recently completed his South Carolina Top Logger training.
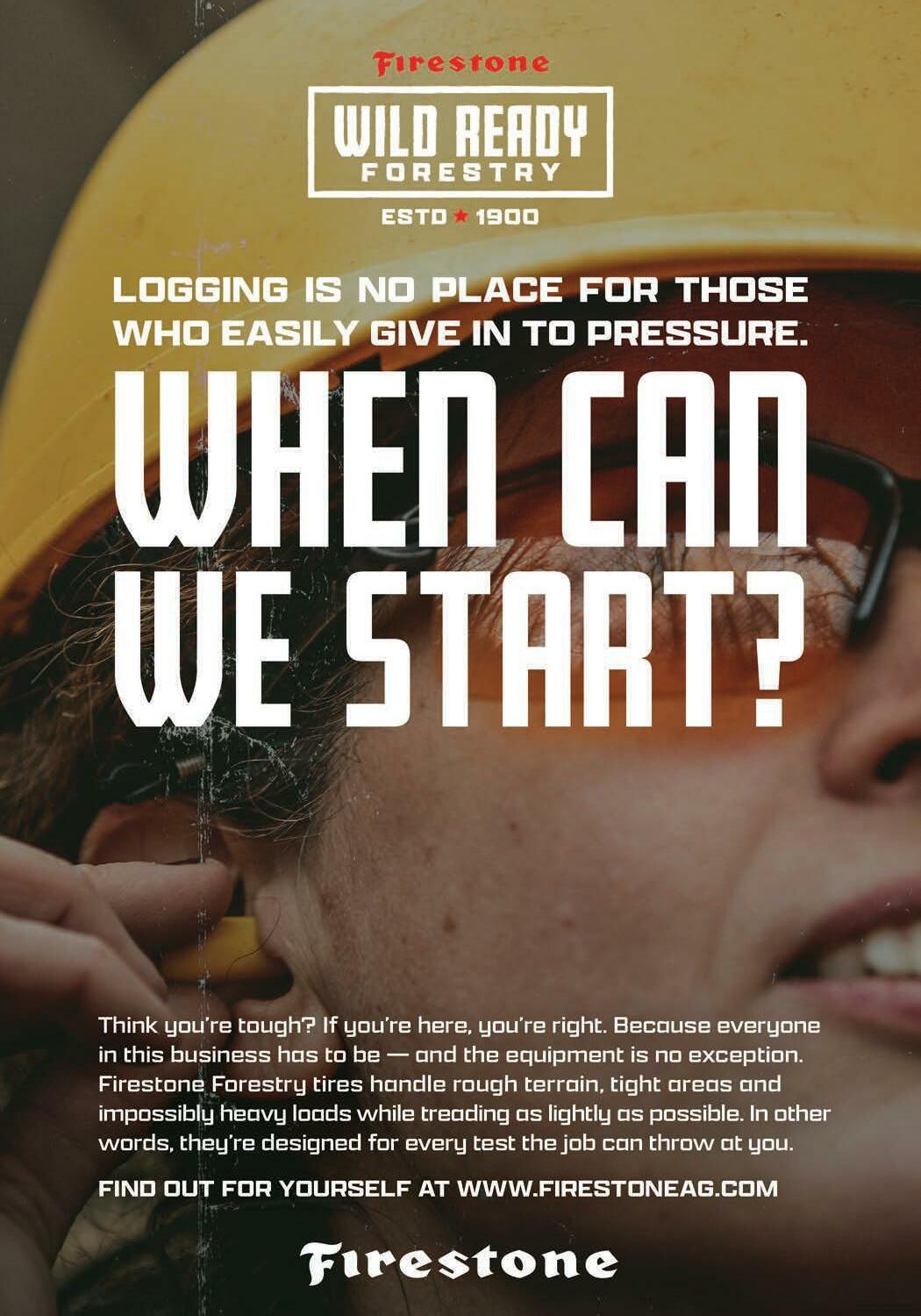
Family, Future
Bennett’s sister is an accountant for John Deere corporate. “She keeps an eye on me and looks at my books for me, and makes sure I am on track with everything.” His wife Kaitlyn works a full-time job in accounts receivable for UniFirst Corp. She also keeps up with bookwork for the logging company. “We use QuickBooks. It makes it so easy; it kind of lays out everything for you.” Bennett and Kaitlyn have a son, Hunter, who turns 5 in August.
Now wait, one might wonder; the company name is Bennett and Sons, but Bennett only has one son, and he’s only five; why Bennett and Sons? Chalk it up to his optimistic outlook again. “My wife and I want to have another boy,” he explains. “My last name is something I want to be known, I want to pass it down to my sons one day.”
Like many of his generation, Ben nett is active on social media: he posts logging videos, including overhead drone views, on his You Tube channel, Rick Bennett RB Fish ing. “I dabble my foot in it,” he says modestly. “I get a lot of feedback from young kids who like to see equipment. It’s pretty fun actually.”
Looking to the future, Bennett says he wants to grow his business, but not too much. He wants to run 80 loads a week, so he wants to add another skidder and another loader to do it efficiently. He’s also thinking about stepping into running his own trucks, but for now he wants to wait and see what the economy does. Come what may, he says, “For estry is life; at the end of the day, we are going to need it. People don’t do logging for the money; there are better ways you can make money with less risk. You do it because you love it.” SLT
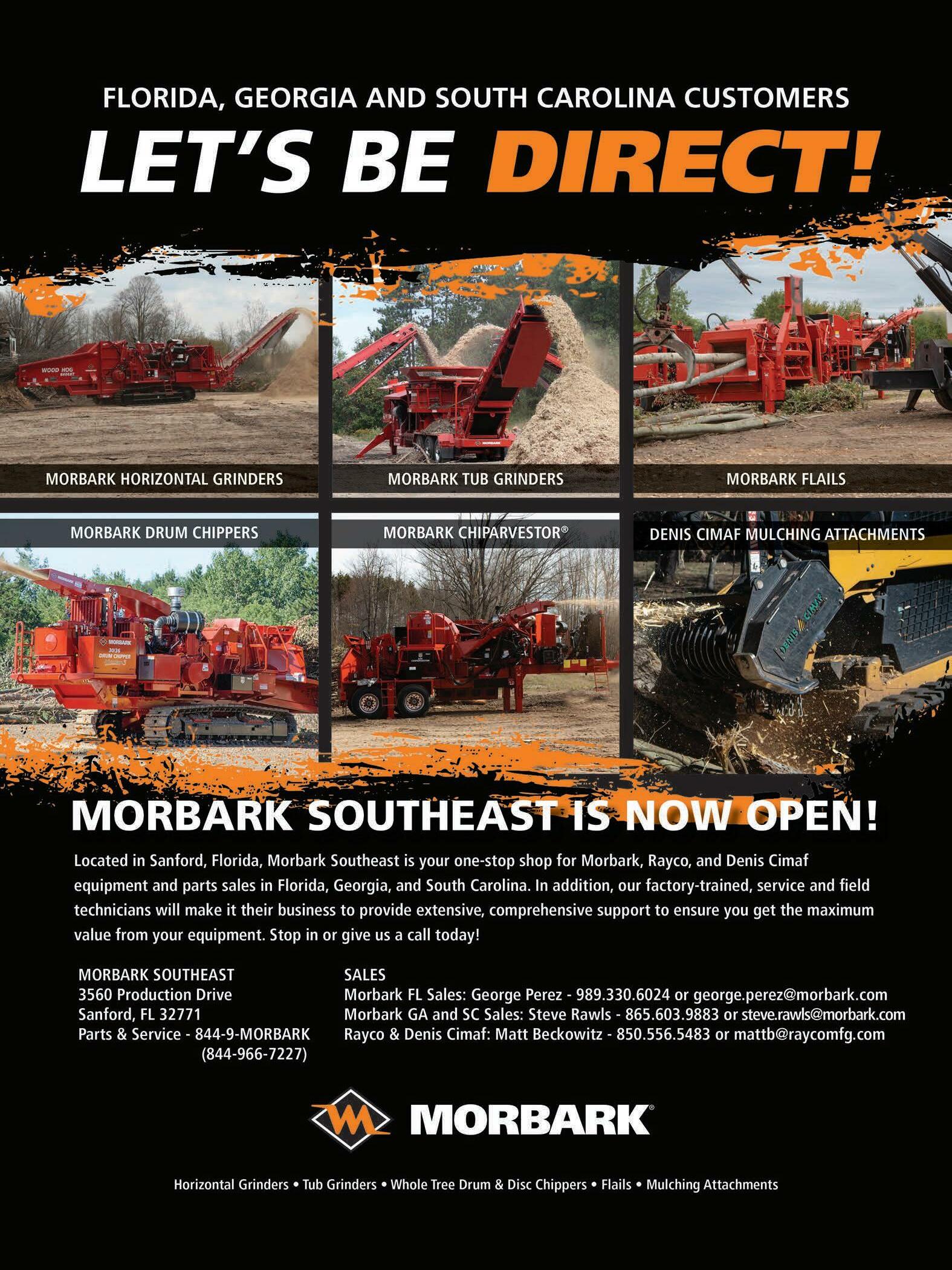
Up To Bat
■ New blood Zachary Comer keeps his nose to the grindstone in the Tennessee Valley.
By Patrick Dunning
CROSSVILLE, Tenn.
At 28 years old, Zachary Comer, owner of Comer Logging, is one of the youngest loggers currently contracting for Huber Engineered Woods in Spring City. Being a greenhorn in the wood-products industry is something Comer is proud to acknowledge; he believes more millennials are getting involved with the business. His employees are even younger; loader man Jacob Futrell is 27, and cutter driver Seth York is 25. They have been with Comer Logging since the start.
Comer gives his grandfather, Danny Futrell, 70, credit for the sawdust in his blood. “We’ve always been in logging,” the young Comer reveals. “My grandfather and his brother even had a sawmill for a little bit. Logging can get the best of you sometimes but I enjoy it.”
Grandfather Danny belongs to the old guard that used horses and mules to skid logs and loaded trucks by hand. Danny’s two sons, Jason and Little Danny, were part of the family business and regularly hand-felled high-grade hardwood in Cumberland County State Park. Comer’s grandfather and uncles still hold the state record for harvesting the largest registered white pine tree in Tennessee in 1995. Ruby Selby, landowner of the property in Big Lick at the time, said the tree was damaged by a hailstorm in 1990 and was already diseased and slowly dying before the storm. The tree stood 150 ft. tall and measured 5 ft. across at its base. Zachary says the tree was older than anyone knew but only took 15 minutes to fell with a 3 ft. chainsaw blade. They cut the logs into 10-12 ft. sections and hauled them to Rose’s Sawmill, Savannah, where it yielded nearly 3,500 sq. ft. of lumber. Zachary still has the article and photo of him at 16-months-old next to the stump, the chain saw bar towering over him. “The bar on the saw was taller than I was,” he says.
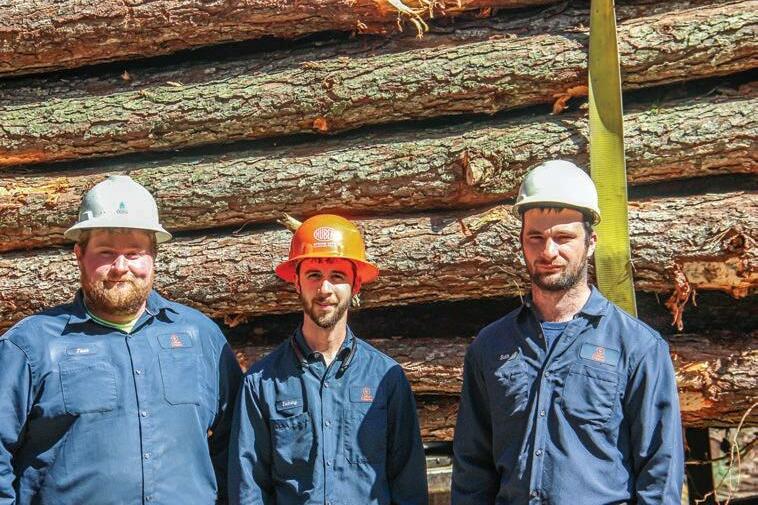
Jacob Futrell, Zachary Comer, Seth York
Starting Up
When Comer graduated high school he attended Tennessee College of Applied Technology, Crossville, and earned a certificate in welding technology. He then worked at the Y12 National Security Complex in Oak Ridge for a stint, maintaining the nuclear plant’s roads and pathways. Then his uncle, Jason Comer, decided to leave the logging industry after 15 years to work for Huber as a crane operator and was selling some of his woods equipment. It gave Comer something to consider.
He founded Comer Logging in 2016 by purchasing two Franklin C7 Tree Farmers, a ’95 and ’98 model, from Jason. Each had more than 20,000 hours but both were still in decent shape. Comer also acquired a 372 Husqvarna chain saw and started shopping for a used loader. He found a deal on a 410 Prentice at Power Equipment Co., Knoxville, and ran it for two years before trading for a ’07 Caterpillar loader.
“I like buying machinery with 4-5 thousand hours on it, run them till 810 thousand and then swap it for something with less hours,” Comer says. “But as long as it’s doing good I’ll run the machine; haven’t bought anything brand new yet. When I started out I wanted John Deere equipment but couldn’t afford it so I had to go with what I could afford, and at the time Caterpillar was cheaper, so I became familiar with Cat equipment and have had really good luck.”
Comer's dad, Jeremy, worked with him in the woods early on before becoming a full-time fire fighter for Cumberland County, Tenn. Comer’s wife, Tosha, didn’t want him in the woods alone, so she started running the skidder. “She was intimidated by
Comer started out six years ago with equipment he bought from his uncle, who was retiring from the woods. Two years later he upgraded.

it at first because we were in the same rough ground,” he says. “We didn’t have a cutter at the time so in the mornings I cut by hand until 11 a.m. or so and she would pull the cable down the mountain and hook trees. We were only getting about a tractor per day until my cousin’s dad came to work for me and I was able to get a cutter and grew a little then.”
He adds, “My cousin started hauling for me and a couple other loggers to stay busy. Would load him, load my own truck and we’d both haul a load every evening. When I’d leave to go to the mill she’d be on the loader trying to learn. After about a week of that she promoted herself to loader operator and was out here until she got pregnant with our little boy.”
Operations
Comer has slowly expanded his machinery inventory over the last six years and established solid relationships with Stowers Cat in Cross ville and Forestry 21, which is roughly 265 miles south in Lafayette, Ala., servicing Tigercat. His woods equipment now includes ’09 Tigercat 724E cutter, ’16 Caterpillar 579C loader with CSI delimber, and ’16 Cat 535D skidder and ’17 Tigercat 630E skidder, both equipped with Eco-Tracks. “Eco-Tracks are maintenance free,” Comer asserts. “I’ve only had to tighten them once and have been running them all year. They’re expensive but worth it; really a game changer.”
On woods equipment, oil and fuel filters are changed every 250 hours using Mobil Delvac or Rotella interchangeably at Comer’s 40x80 shop, which was recently finished in Cumberland County next to Crossville. He hopes to hire a full-time mechanic in the future to help maintain equipment. Truck oil is changed at the 10,000-mile mark and greased daily.
When Southern Loggin’ Times visited Comer Logging in March, the four-man crew was performing a residential thinning on an 800-acre block Huber leases in Morgan County. The landowner had requested that one tree be left every 60 ft. Comer says he and four other logging operations contracting for Huber were staged along Red Hill Road in Sun Bright targeting all pine pulpwood with a 4 in. top and less than 30 in. DBH. Comer formerly cut exclusively private tracts, then contracted for Oak Ridge Hardwood, which subcontracted for Hu ber. He also delivered wood to Resolute Forest Products, formerly known as Bowater in Calhoun, until they idled the paper mill in December 2021, citing significant financial losses.
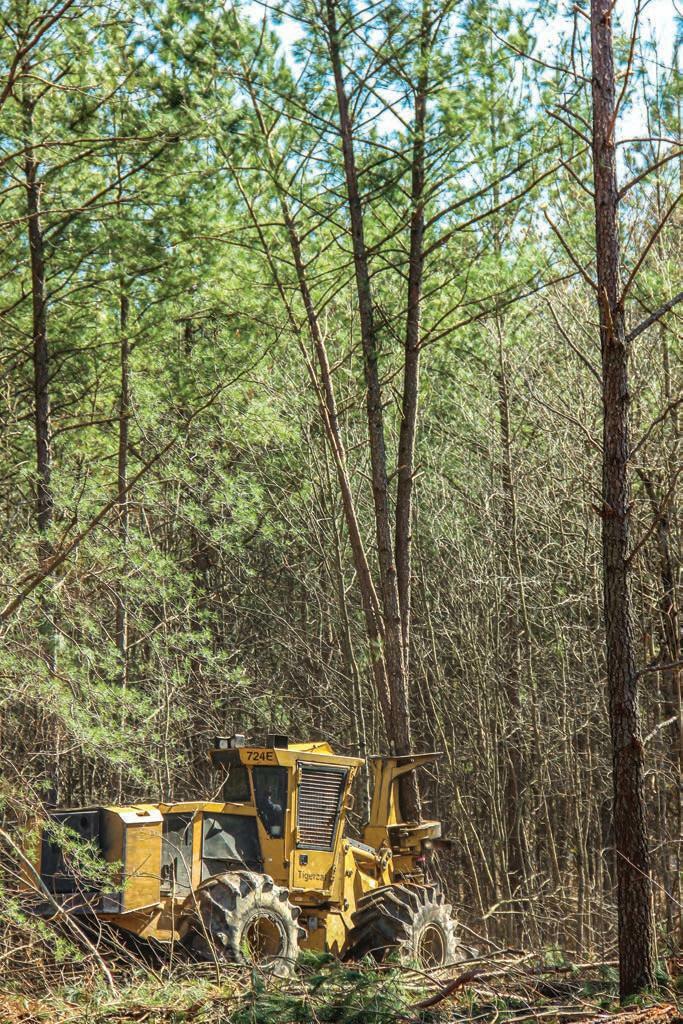
The closest Tigercat dealer for Comer is Forestry 21, 265 miles south. "They are very helpful and super friendly," says wife Tosha Comer.
SLT SNAPSHOT
Comer Logging Email: tdinw1@aol.com
Founded: 2016 Owner: Zachary Comer No. Crews: 1 Employees: 3 Average Production: 25 loads/week Average Haul Distance: 50 miles Tidbit: Early on, Zachary’s dad Jeremy worked with him, but after he went to work as a firefighter, Zachary’s wife, Tosha, worked with him for a while, running skidder and loader.
Comer started contracting for Huber 10 months ago and says that the Bowater shutdown at the end of 2021 created tight quotas at Huber. “We started out really strong and they were giving out load bonuses at Huber,” the logger states. “When Resolute shut down it clogged everything up. All the trucks going there started going to Huber. It’s just Huber around here. The next closest paper mill is WestRock in Stevenson, Ala.”
Huber’s Spring City facility originally opened in 1997 and halted production during the housing market downturn in 2011. The OSB plant, located in the Tennessee River Valley northeast of Chattanooga, reopened in 2018 and is one of few continuous press operations in North America dedicated to the production of OSB products. Right now Comer Logging is delivering between 850-1,000 tons per week to Huber, which breaks down to 25-30 loads.
Comer owns two Kenworths, a ’94 W900 and ’04 W900. He says trucking can be a large expense but it’s nice to have your own trucks and not rely on someone else. He contracts four trucks as well. “Owning your own trucks keeps the contract truckers honest and on moving day you don’t have to pay out to move your equipment,” he reasons. “You’re still spending money moving but you can absorb the cost better. It can be hit or miss contracting in this area but if you find a good group of people you’re set. It was hard when I first transitioned to cutting pine for Huber because I had to find more trucks going from hardwood stands.”
To alleviate some of the strain of finding truckers, Comer founded JTC Trucking a year ago to haul flatbed freight and lumber out of Huber.
Moving forward, Comer says he doesn’t want to be the biggest outfit around but definitely wants to be in the mix and compete. And when his newborn son, Timber, is of age, Comer looks forward to showing him the ropes as well. SLT
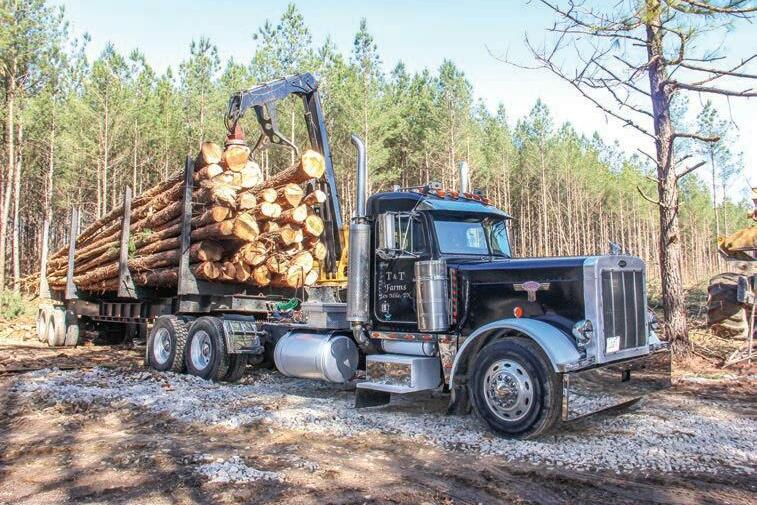
Both Comer's skidders use Eco-Tracks. The logger owns two trucks and hires four contract haulers.
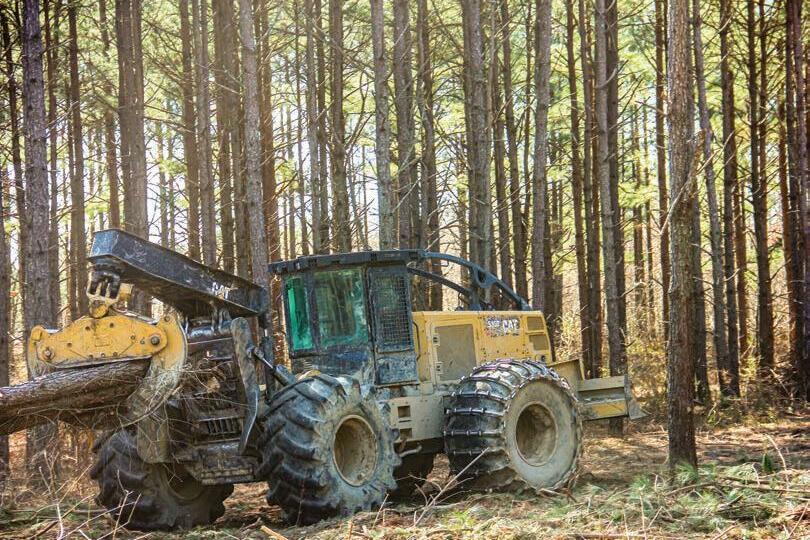
Something Different
■ At Cutting Edge, Thomas Johnson embraces technology and keeps going when others might cut out.
By Jessica Johnson
DeRIDDER, La.
Though it seems obvious after talking with 33-year-old Thomas Johnson for any length of time that he’s got logging in his blood, the relatively new owner of Cutting Edge Logging says in school he wasn’t sure it was what he wanted to do. When pushed, he explains that while he might have entertained other forms of work, Johnson has always been a logger, having got his start at the age of 11 picking trash off his dad’s job.
In 2021, the timing was right for Johnson to buy out the crew of his dad’s he’d been running and start his own journey as a business owner. After asking the timber company for a few months to get his financial house in order, and bring him and his wife up to speed on that side of running a job, Cutting Edge Logging was born. It was a pretty straightforward transaction, and Johnson signed as a contractor with Bennett Timber.
But after Cutting Edge got started was when it got interesting. “I utilize all types of advancements in technology,” he explains the business’s name. “Anything that will advance the job, I use it. I’ve always been one to stand out, and I try to do excellent work in how we do our job.”
Part of the advancements in technology in the woods is the prevalence of YouTube loggers. Johnson says that for a while, he would log all day and then go home and watch logging on YouTube. After sharing the passion with a coworker at the time, the two batted around the idea of having their own channel. Not tremendously different from the O’Bryant family in Mississippi running a processor, Johnson exclusively thins with a track fellerbuncher, something that is a little different than others in Louisiana. He thought it might be interesting for the world, so one day standing on the landing he took his phone out of his pocket, flipped it around to landscape and started recording.
“I didn’t think I had the drive for it,” he recalls. “But I just pulled the phone out and started videoing. It was awkward to talk about what we were doing. I wonder if I have deterred some help away because the cameras are here and some people are just a hard no against it. I catch a lot of flak over it.” But, ultimately, Johnson really liked the videos and started to get good at them.
A budding YouTube star, Johnson’s channel really took off before COVID hit when he invested heavily in camera gear and all the things to “do it right,” adding a drone to his equipment list. Going that way helped him get noticed, and soon the channel had partnerships. Unfortunately, COVID shut down a lot of the product testing and promotion for the channel, and now, Johnson says he doesn’t shoot as much.
Running the job from an operational side (as his dad’s foreman) was difficult enough, but being an owner-operator demands another level of time. Plus, as more and more users are moving to TikTok, a video-sharing platform with much shorter clips, Johnson says he has made the transition as well. He likes the platform because it is easier on him to create content—shorter videos require less editing.
Curveball
But the YouTube channel, and now the concentration on TikTok, has had to fall by the wayside. Johnson was
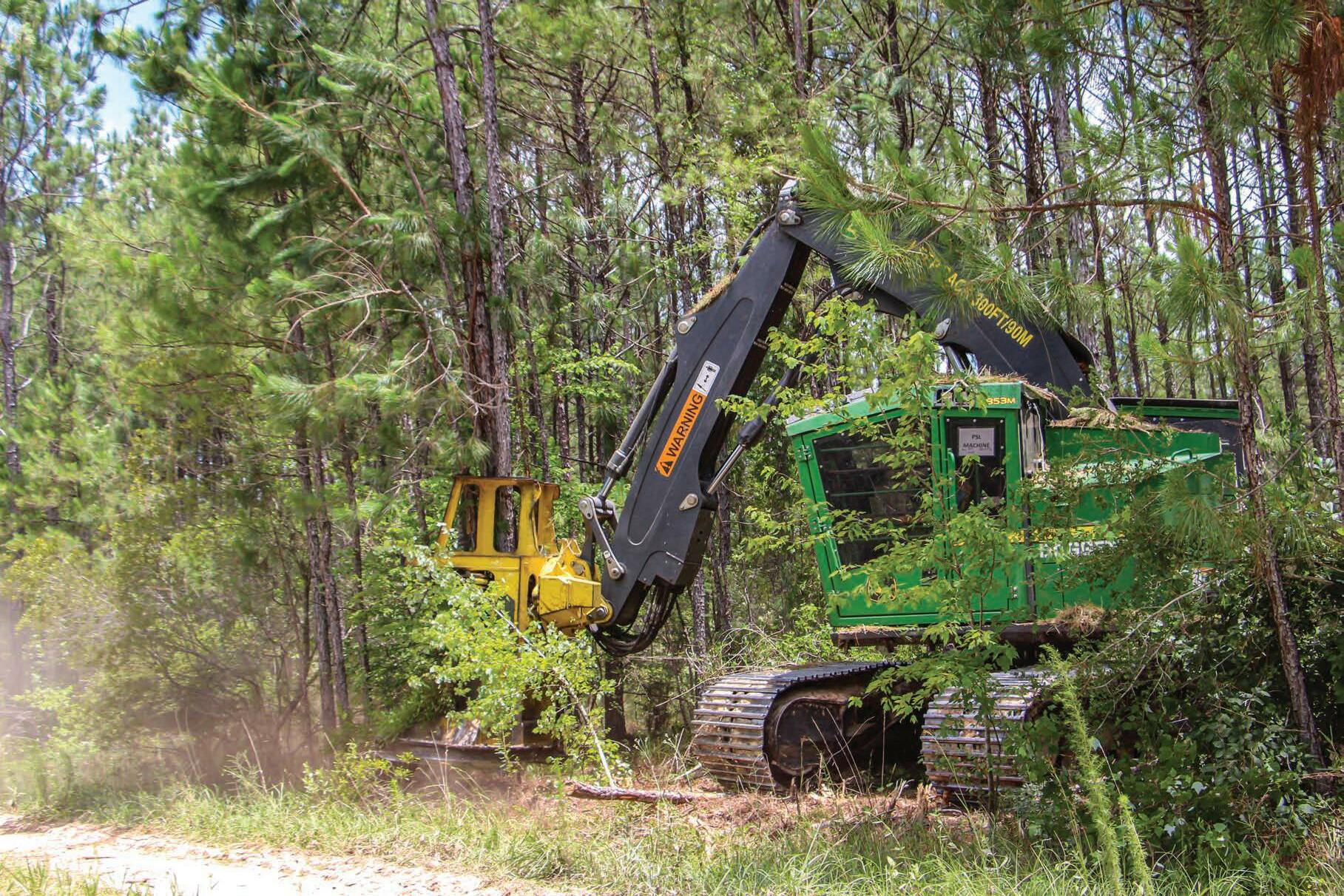
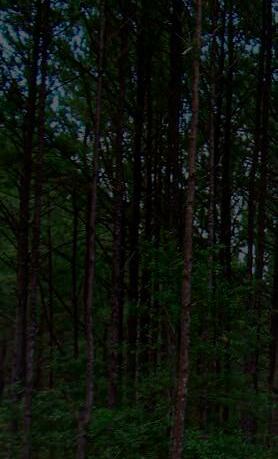
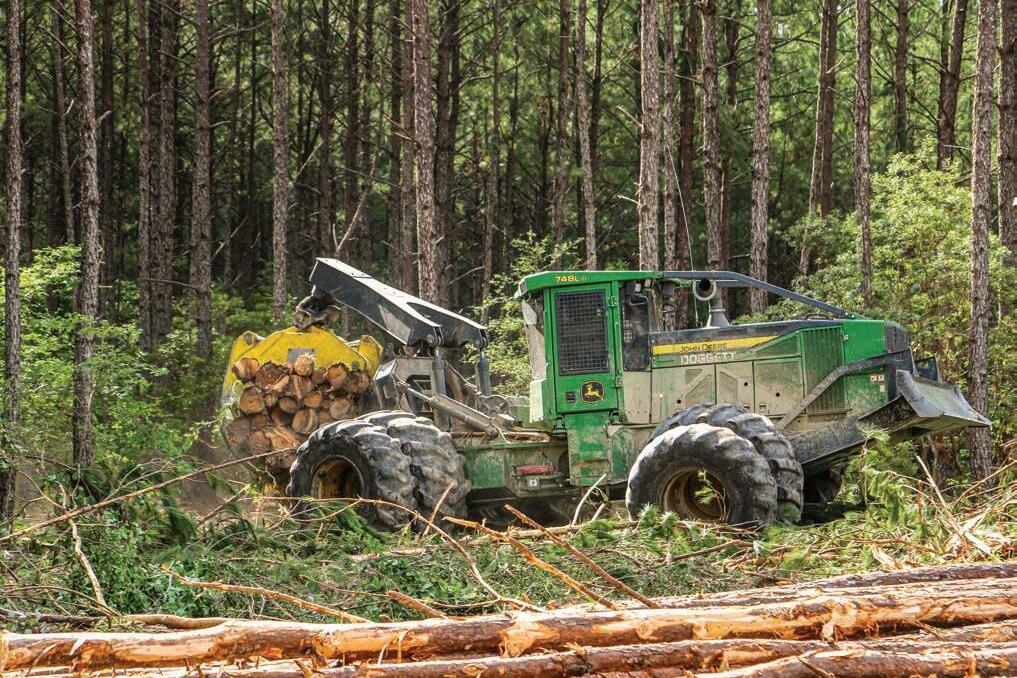

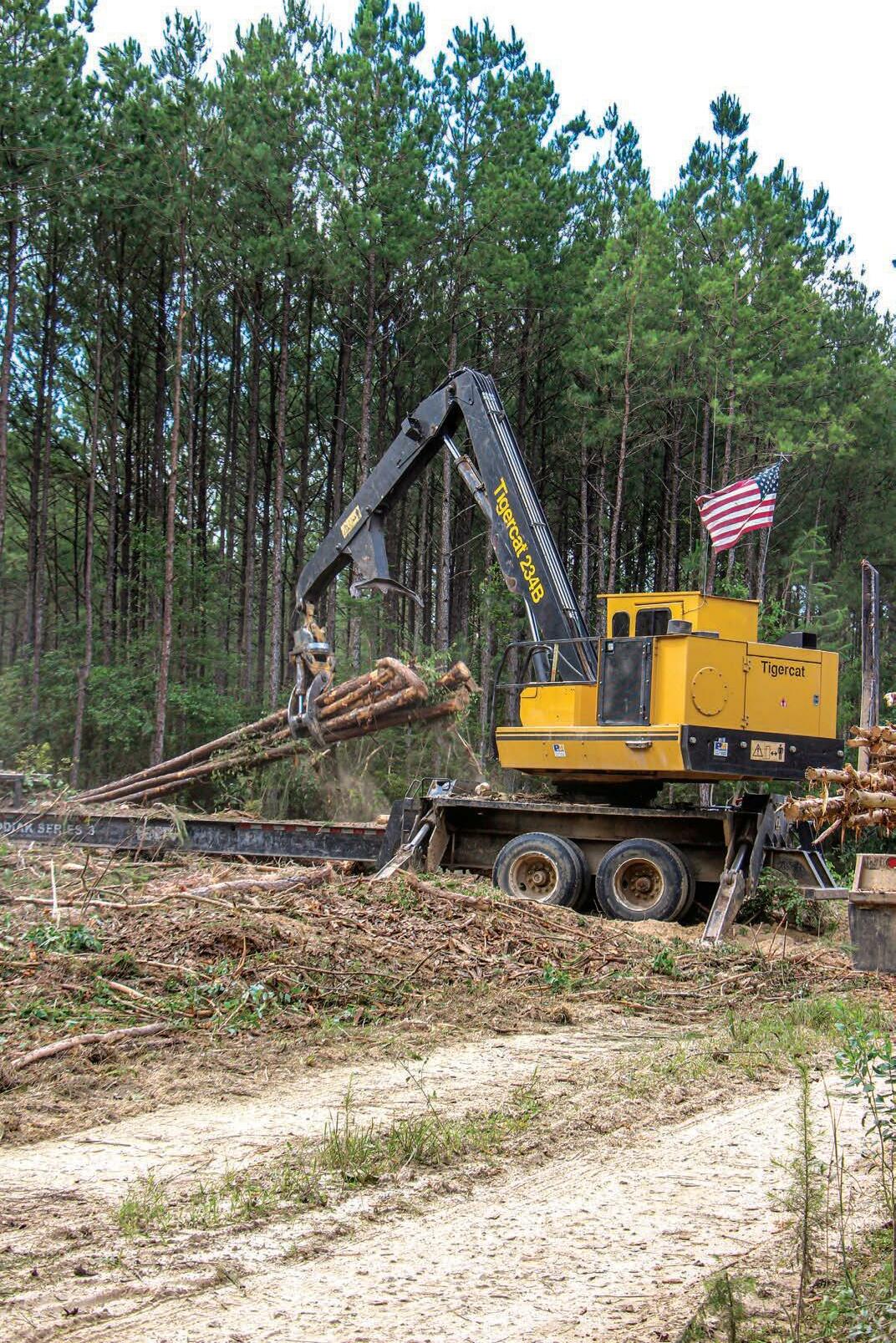
dealt a life-altering diagnosis after experiencing tremendous amounts of back pain in October 2021. He had a giant cell tumor in his lower back that had eaten through the vertebrae. He was flat out for a good chunk of time after having just gotten started. Just six months after getting his business off the ground, Johnson says it was a big blow. “Potentially it could just be fine. I don’t know where anything is going to go. It is a very complicated situation. I’ve always been told God won’t put you through what you can’t handle. Things were going well. I was investing back into the business. We were rocking and rolling. And then we got hit with that.”
Thanks to the support of the DeRidder logging community, his loyal crew, and his family, Johnson’s job barely missed a beat. “People stepped up and helped us through,” he emphasizes. Part of why he believes he was able to continue to be successful while going through intense chemotherapy was because of the John Deere cutting machine’s TimberMatic maps.
While he’d be waiting at the hospital, Johnson was able to draw on the maps what he wanted the fill-in cutter operator to do, highlighting that resilience is everywhere and what might have knocked another man down and out just showed how much grit the young logger truly has.
Operations
Johnson says his crew is admittedly low manpower, but still maintains a high production because of the loyalty and work ethic of the three-man crew. Cutting Edge is currently staffed entirely of family. The production numbers out of the single cutter, Johnson credits, are because of his use of a track cutter that can move quickly through the thinning rows.
“When I was 17, I fell in love with the felling side and saw the need for trained and experienced track cutter operators in our area. It is usually wet here, and it takes a skilled individual to do what needs to be done in this thinning application. Unheard of in other places, but it is really helpful,” Johnson explains of the niche he selected for himself early on in his logging career.
To support the track cutter, Johnson’s father used bogie skidders for a time, but the younger Johnson believes you can work wetter ground with a traditional four-wheel skidder in thinning than with a bogie machine. Instead, Cutting Edge runs a smaller skidder with a standard grapple. The crew moves a fairly aggressive 60 loads per week with three pieces. “Because we are such high production, you can’t expect an older machine to come
“The flag is a little tattered, but I look at it as that flag has been with me since we’ve started, it’s a representation of me and my company. We’ve been through a lot. We’ve been through two hurricanes, tumors, all the medical stuff, hyper inflation, everything else. It’s worn but it’s part of us. It’ll get to the point where we’ll get another one, but not yet.”—Thomas Johnson
From left, Mickey Townsley, Bradley “Puppy” Willis, Thomas Johnson, Charlie McKelvey and Michael Townsley
Johnson likes to use a mix of equipment brands, and has a good relationship with John Deere.
The young logger is active on YouTube and TikTok, and has a drone for overhead videos.
out here and run hard all day long,” he adds.
Operating under that mentality, the Cutting Edge iron registry includes 2018 Tigercat 234B loader, ’19 John Deere 748 L-II skidder, 2020 John Deere 853M track fellerbuncher with John Deere FR50 felling head, ’03 Chambers delimbinator, and two spares: ’08 Tigercat 234 loader and ’09 Tigercat 718E wheeled feller-buncher.
Johnson says the mixed lot is by design, as he does not want to lock himself into just one dealer, but also because he feels he picks the best machines available, and what he thinks will be the most dependable in the long run. He adds, “A thing I like with John Deere: if I start having issues I will speak up, and I feel like they really listen to the loggers.”
Over the years, Johnson has operated a lot of machines, he says, but John Deere has earned more of his attention lately thanks to his involvement with the engineering of the new track cutters. He formerly ran Tigercat feller-bunchers, through dealer Doggett
Machinery in Alexandria, but then John Deere reached out to
Johnson with a prototype 803M, looking specifically for his input on the RCS mode of the machine. Johnson says by that time he had over 15,000 operational hours on a track cutter, and after five minutes with the prototype he says he knew it wasn’t quite right.
He remembers having the project engineer in the cab with him and says that it was a sick machine: “Every time you went to cut a tree it nosedives. We were wasting my time and his.”
The next morning Johnson handed over a list of things he thought needed to be done differently. From there, he was folded into the development team and helped with the concepts on not just the M series, but other products as well, like the FR50 felling head.
Johnson’s biggest input on the
FR50 was that the head needed to be able to hold a high number of stems to make a bundle, especially in pine thinning applications or in South America working with eucalyptus. For Johnson it seems simple enough: “You need to be cutting 16-17 trees and making a bundle. The more trees you can hold, the less stops the skidder has to make. Time is money.”
Two contract trucks targeting six loads per truck per day haul wood. Like everyone right now,
Johnson is incredibly conscious of diesel prices. Before the crew might get started a little later in the day, or knock off and not wait on a delayed truck. Now, the crew doesn’t shut down until they get their loads for the day.
“To save fuel consumption, machines are dead if we’re not working,” he adds. “I monitor fuel use every day, and I am doing everything right now we can to eliminate waste. We lean heavily on the TimberMatic maps and aim to make the jobsite as efficient as possible.” SLT
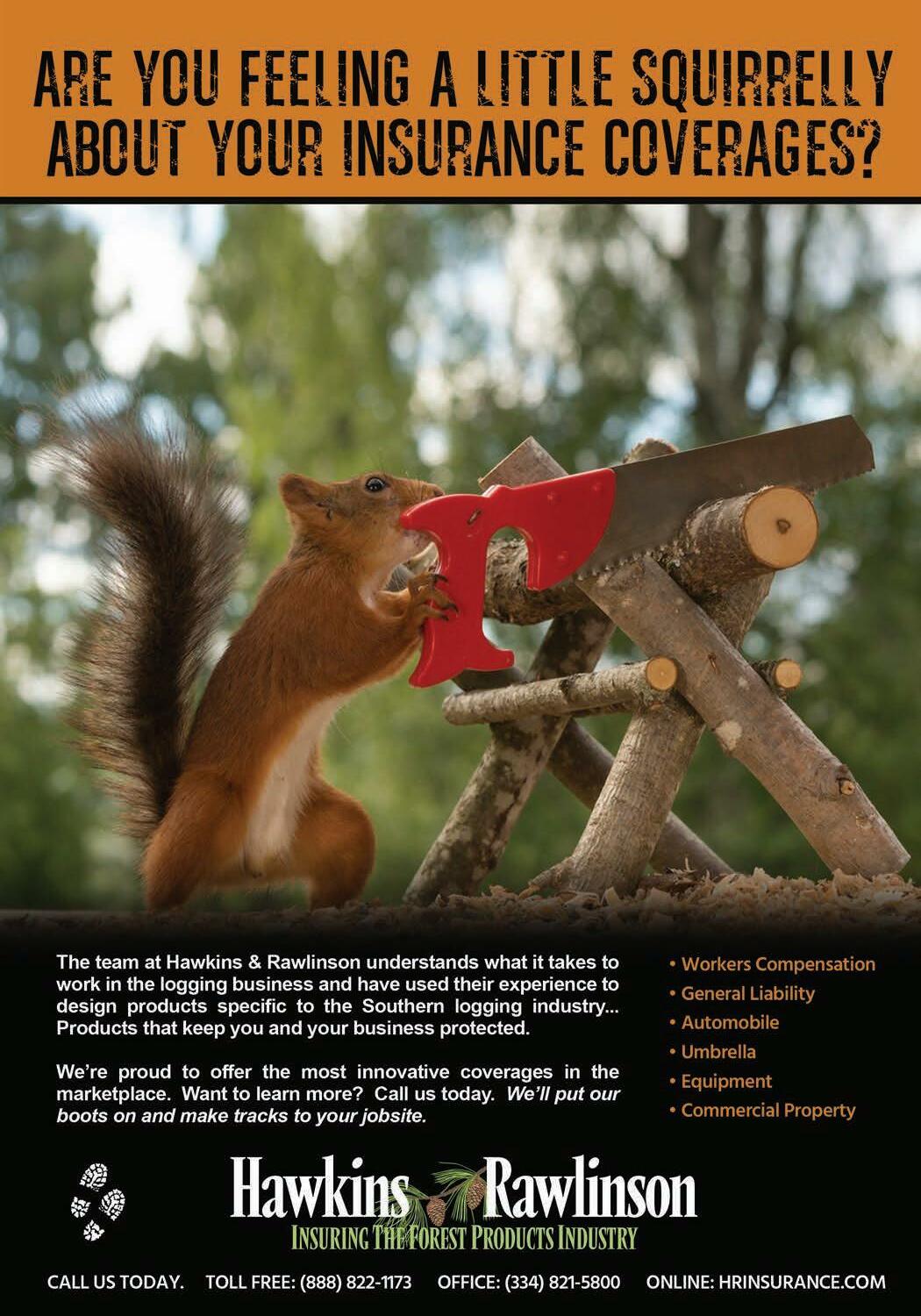
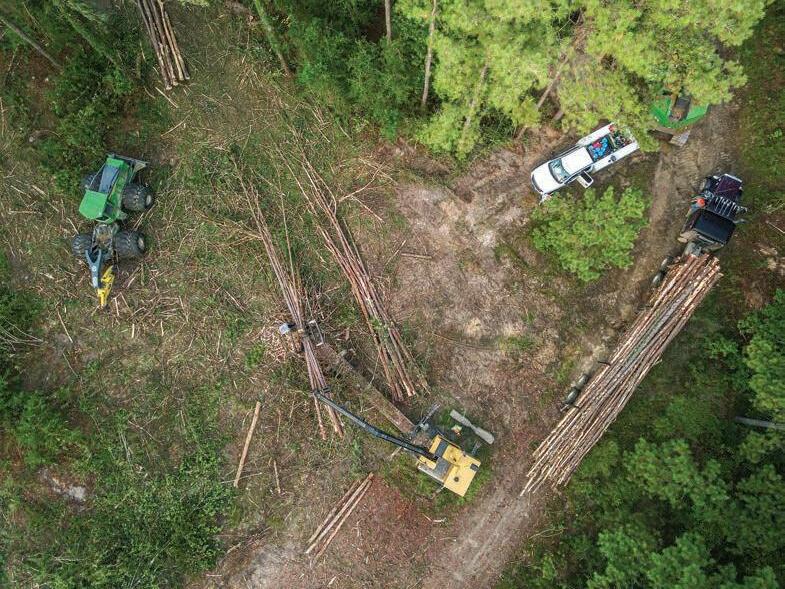
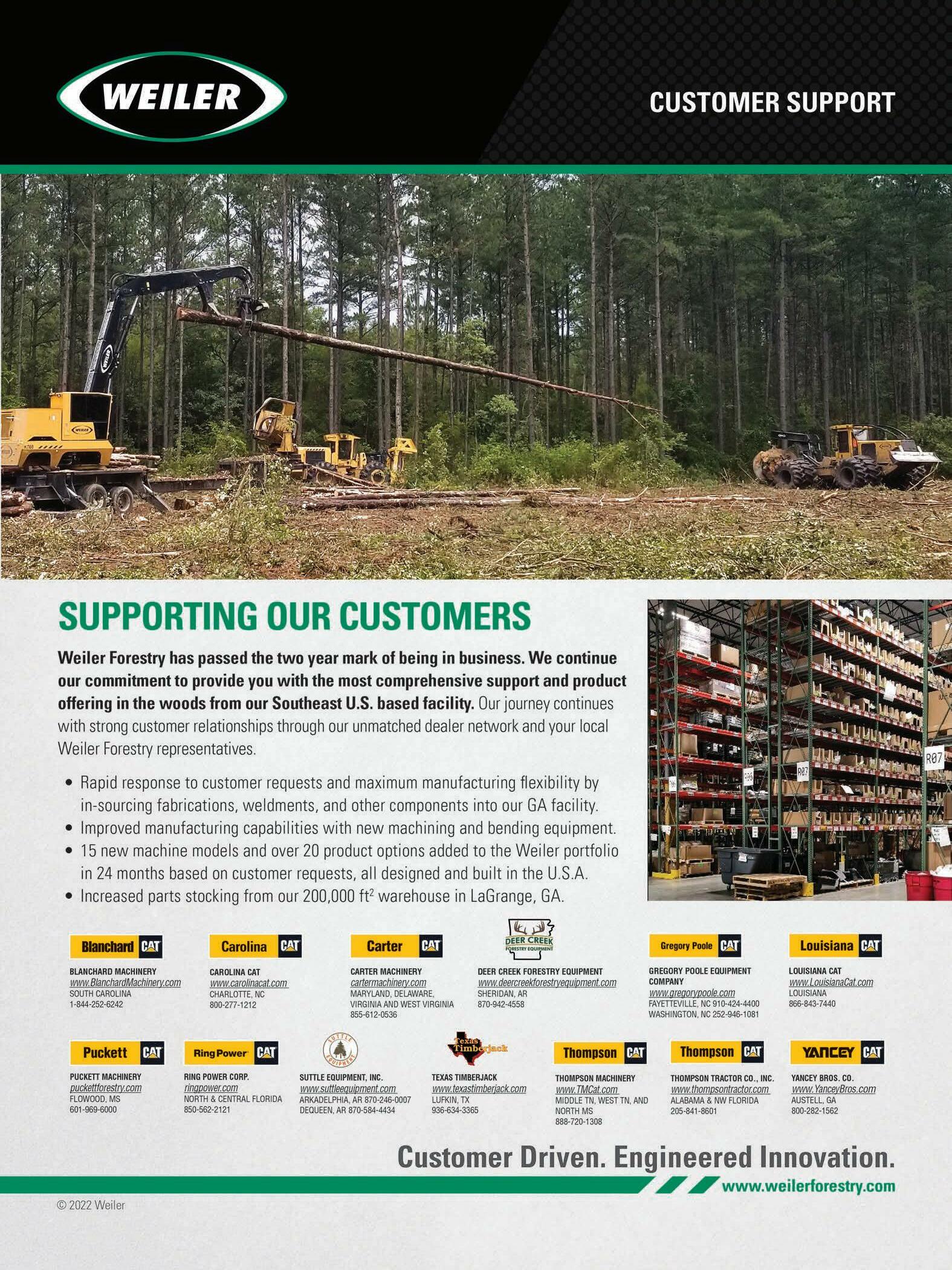