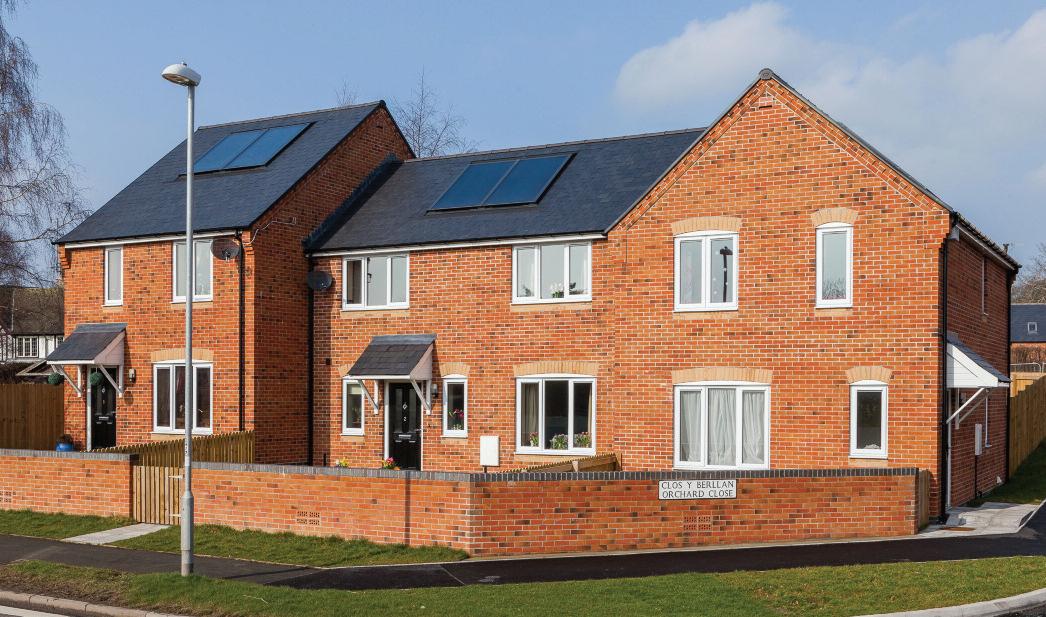
4 minute read
L for lower carbon
The industry has already had to get to grips with meeting upcoming standards, following its introduction in June 2022 and now, all future homes built must achieve an overall fabric U-value of 0 18 W/m2k or lower, before backstops Not only that, but it’s also encouraging a race to ensure compliance with the now-mandatory 31% carbon reduction guidelines
However, a rocky 12 months, which has resulted in material cost inflation and labour shortages are squeezing margins Additionally, a raft of other, incoming regulations, arising from the BSA and FSA, are also causing a significant headache It’s left many businesses looking for agile solutions to achieve Part L without the addition of significant expenditure
The future is systemic
An increasingly important improvement in residential construction has been the move towards improving fabric efficiency, set to become a regulated and default principle for construction by 2025 Low Uvalues, driven by fabric first principles are proven to improve thermal performance and further provide additional compatibility with efficient systems such as PV, ASHP, and GSHP.
We might argue we’ve been building in this way for centuries without realising it. Tried and tested masonry-built cavity walls provide a prominent example, especially in the here and now when they can be modified with widened cavities, efficient insulation and low-conductivity wall ties
Shown to achieve an ultra-low U-value of 0.18 W/m2k or lower, this type of construction also prevents the thermal bridging that can so often occur within other build methods, especially modular build forms Crucially, this system limits the likelihood of exposed elements coming into contact with the external leaf, which can also contribute to significantly reducing the thermal performance of a property
Even better, it’s a system that most of this country’s builders will be familiar with, and can easily train new recruits on-site
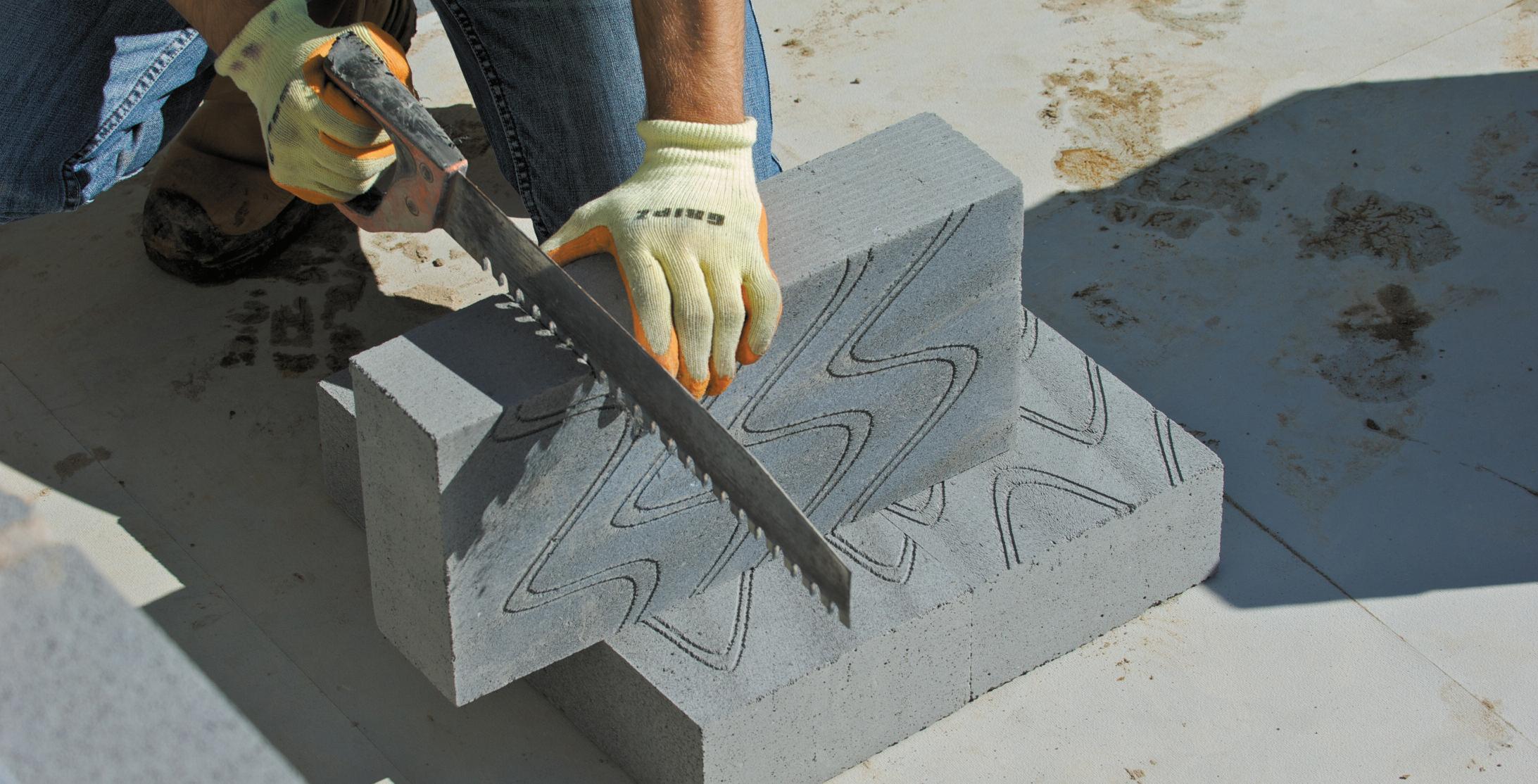
The right approach is a consistent one
Although fabric first became the norm in many parts of the residential construction sector, there remains a concern that some operators are still pushing towards offsite fabrication, which is facing an uncertain future currently with many businesses failing A lot of this has to do with the quality of the materials used and the way they are specified.
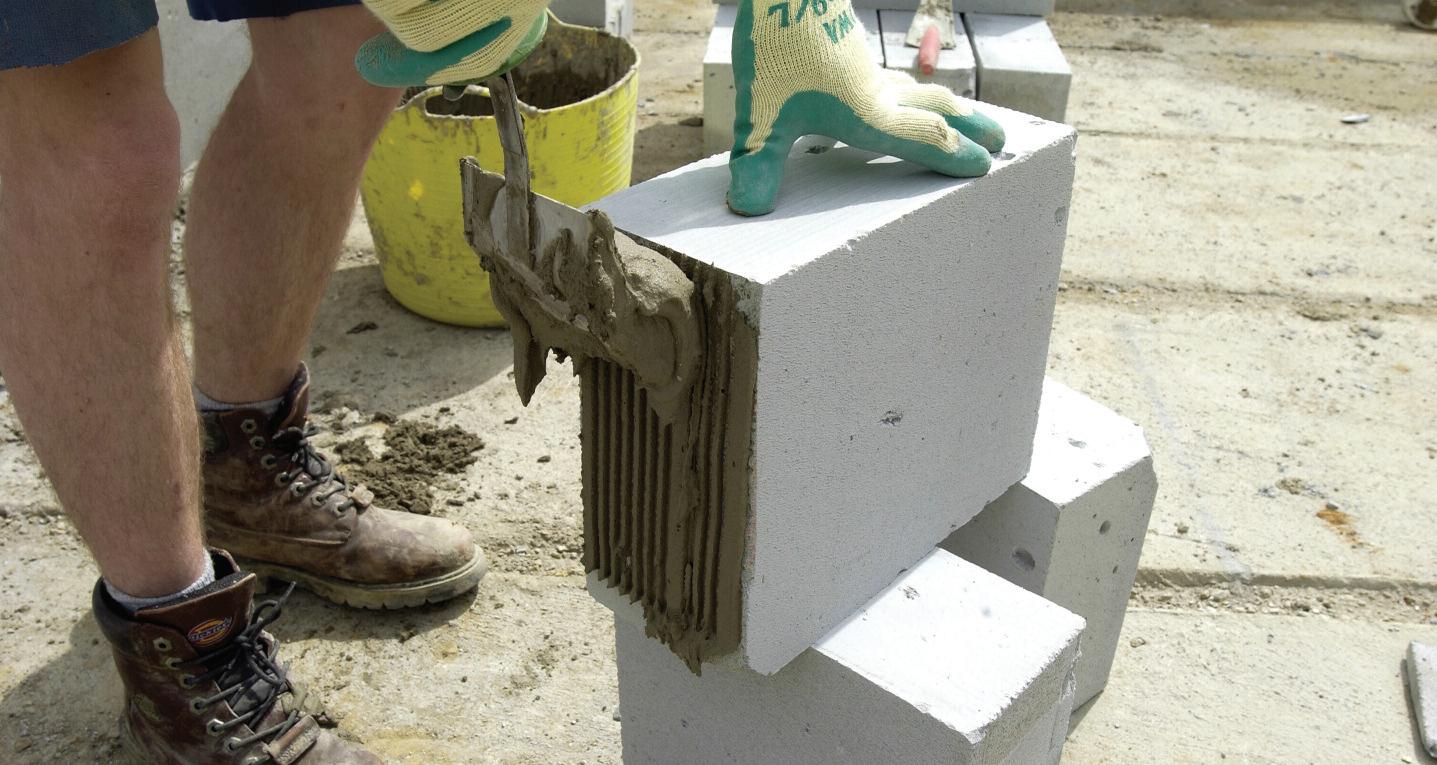
One clear example is poorly built inner leaves or badly installed insulation, which can result in thermal bridging or, worse, lead to damaging issues like damp and mould, These, in turn, can lead to serious health problems for occupants In these cases, the best laid plans for a thermally efficient home will be undermined, with residents also likely to have difficulty heating their homes, contributing to eyewatering energy bills
Consistency is the challenge, and standardisation, as found in Part L, is the answer After all, no-one wants to find themselves searching for new answers or under-resourced as the industry pushes for more units to be built
The better future is now
Furthermore, as the housing industry emerges strongly from the global resource shortage, the robust approaches, encouraged by standards like Part L, will undoubtedly pave the way to lower-carbon, more efficient homes
The popular push within the sector is towards modular builds and offsite, but the issues are rising concerning lifespan, sustainability, and the alarming recent examples of financial collapses in this industry When longevity is the goal, it should be in everyone’s interest to keep the stable approaches at hand.
Extensive work within the sector also indicates that the lowest fabric values needed for some of these developments will be a challenge for offsite construction, with the additional insulation criteria required being unachievable in many cases
U l t i m a t e l y , i t w i l l b e i n t h e s e c t o r ’ s b e s t i n t e r e s t s t o a c h i e v e h o m e s t h a t c a n a d d r e a l v a l u e t o r e s i d e n t s , p a r t i c u l a r l y w i t h t h e c o s t o f l i v i n g c r i s i s , e n e r g y t a r i f f s a t r e c o r d r a t e s a n d m o r t g a g e r a t e s s e t t o i n c r e a s e . T a k i n g a f a b r i c f i r s t a p p r o a c h , w i l l c o n s i s t e n t l y d e l i v e r o p t i m a l e n e r g y e f f i c i e n c y , a c h i e v i n g t h e i n c o m i n g F u t u r e H o m e s S t a n d a r d , m a i n t a i n m o m e n t u m t o w a r d s N e t Z e r o 2 0 5 0 a n d e n s u r e t h e U K ’ s v i b r a n t d e v e l o p e r c o m m u n i t y s t a y s c o m p l i a n t

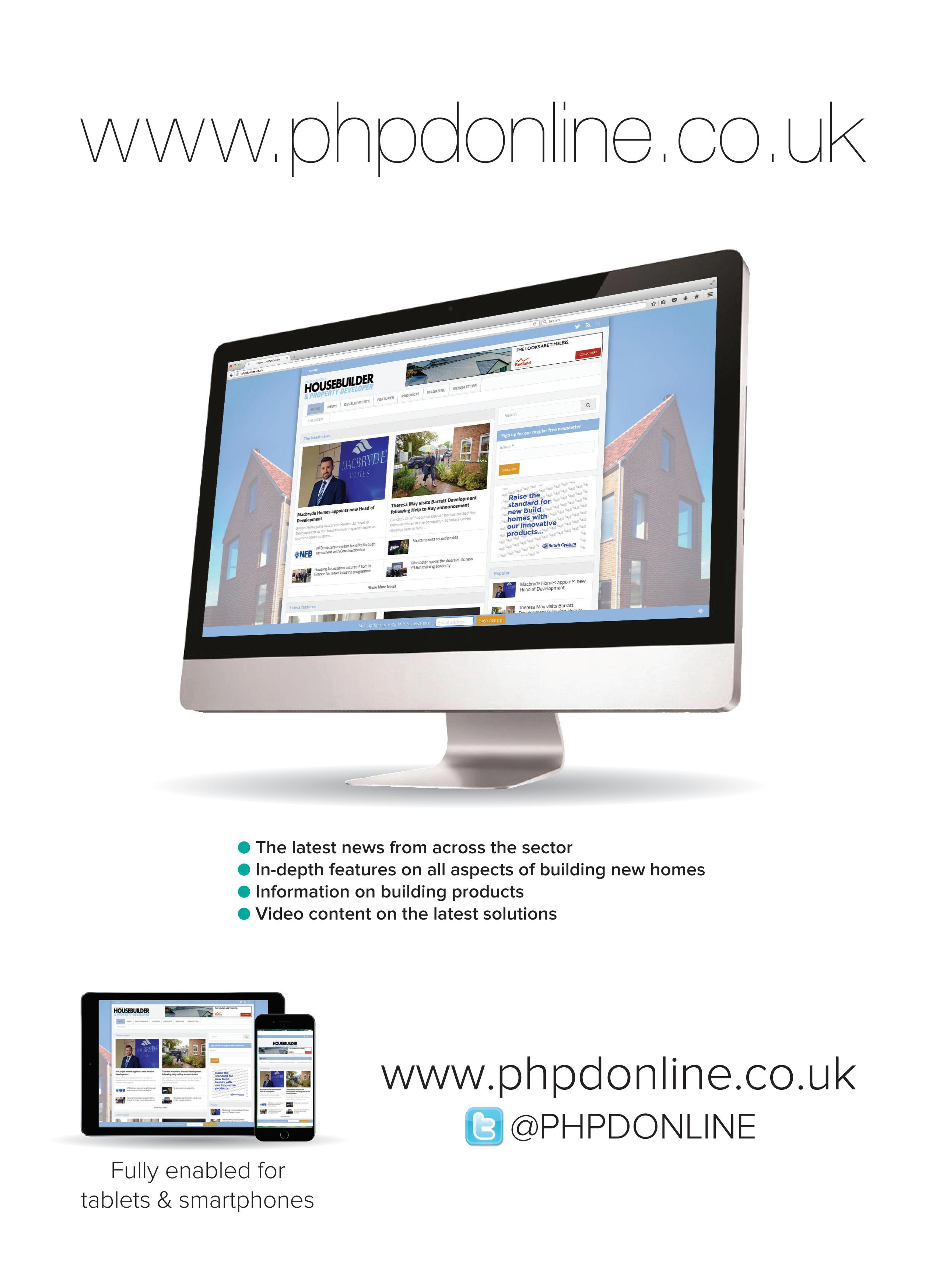
Paul Williams, ventilation product manager at Domus, looks at the revised Part F of the Building Regulations and the end of transition.