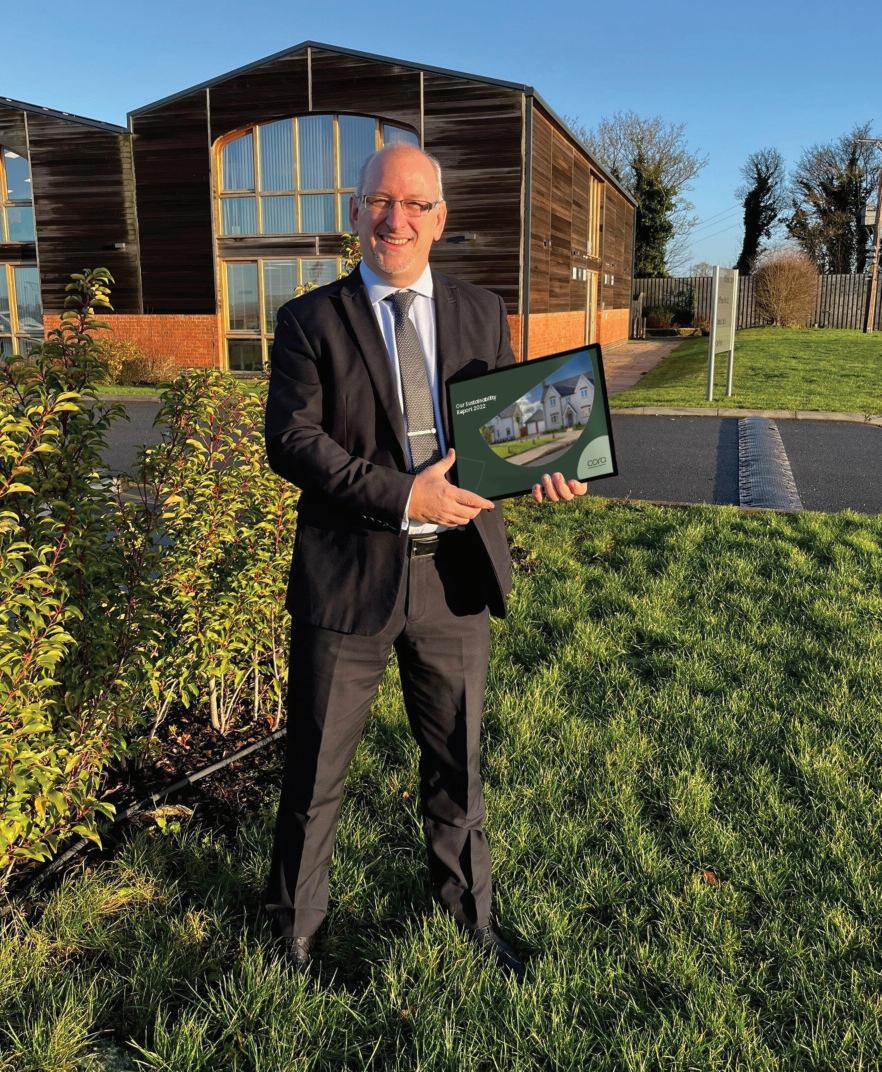
3 minute read
Speed is of the essence
Luke Simmons, managing director of Northamptonshirebased Cora, looks at the future of environmentally aware housebuilding and the role off-site construction will have in creating a more sustainable sector.

The housebuilding sector has the power to make real difference in lowering carbon emissions and protecting the environment – and Modern Methods of Construction (MMC) will be an important tool in achieving that goal.
The housebuilding industry in England and Wales is now worth over £65 billion a year, employing more than 700,000 people, so even small changes can make a big difference Most homes in the UK are still constructed the traditional way - from bricks and blocks on site – however, MMC is becoming increasingly more common
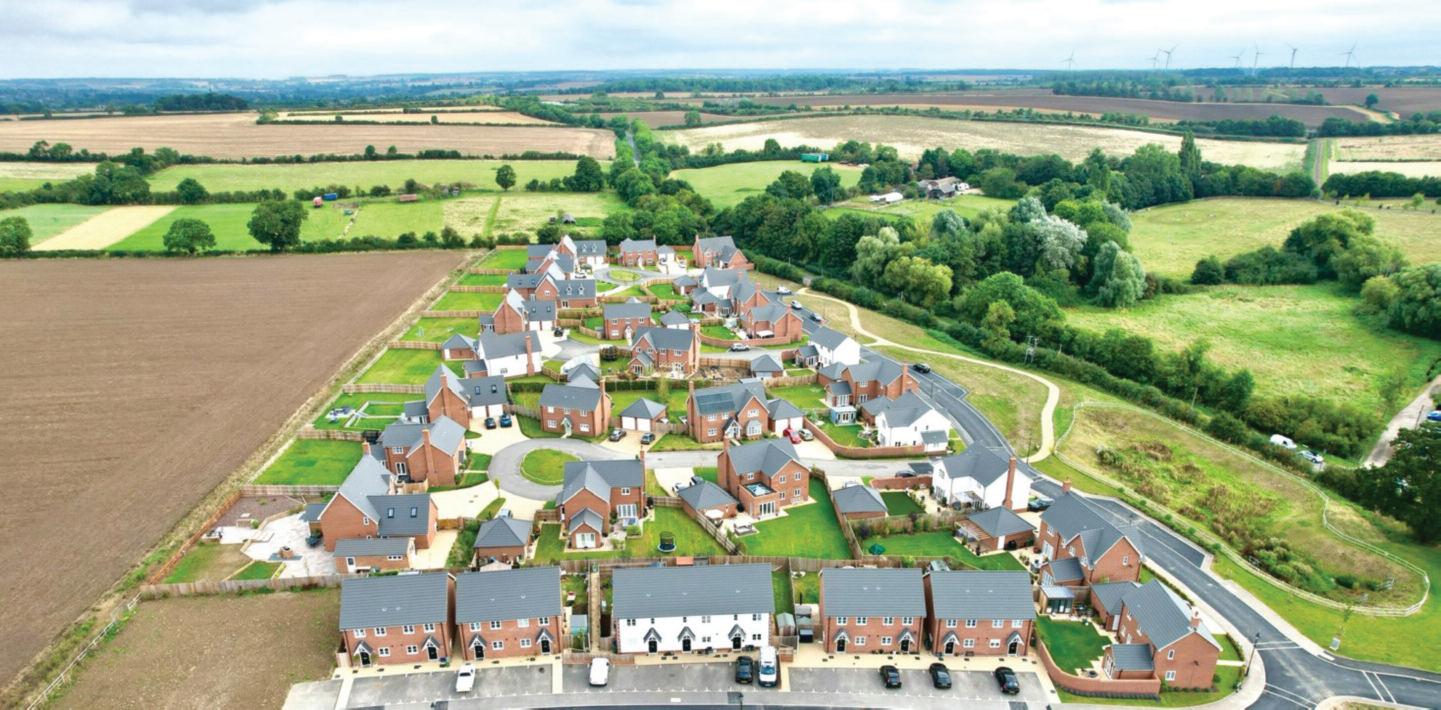
Essentially, MMC involves the use of off-site construction techniques, taking fabrication that has traditionally been delivered on site and doing it in a controlled factory environment This could be constructing the entire building off-site – known as volumetric construction – or it could mean panellised systems, where the walls and roof are made in a factory and put together on site
These methods have huge advantages from an environmental point of view, in that they drastically cut down the carbon footprint of the materials by reducing transport costs. There are advantages economically too, as these prefabricated items can be put together by semi-skilled labour
Houses built using this method can be up in around a week, rather than months. This is something we at Cora are right behind – and have set a goal of using offsite construction in 80% of home completions by 2025
The benefit of all modern methods of construction is that because it is produced in a controlled factory environment, huge energy savings can be made as parts can be mass produced
Energy is one of the global baddies in terms of greenhouse gas emissions so moving more construction from the construction site to the factory is a big step in the right direction.
On top of that, more factories are moving towards using renewable energy to power them, cutting down the carbon produced even further.
The less you are doing on site using petrol or diesel machinery and the more you move to the factory, the less emissions you will produce. Then there are the savings that can be made through simply reducing the time it takes to build the homes.
Building houses the traditional way on a development site in wind, rain snow and mud is not easy, and in most cases is better to manufacture the parts in a factory. Through using off-site methods, developers can complete homes much quicker, which itself brings time savings and sustainability savings. If you are bringing in completed pieces rather than lots of different materials, you can really cut down on transports costs, and the extra emissions they bring.
Benefits to the customer
MMC not only help developers lower the environmental impact of developments, they are also brilliant homes to live in.
As homes are assembled off site rather than built brick by brick, with each part created under factory-controlled conditions, the air tightness and energy efficiency of the homes is vastly improved.
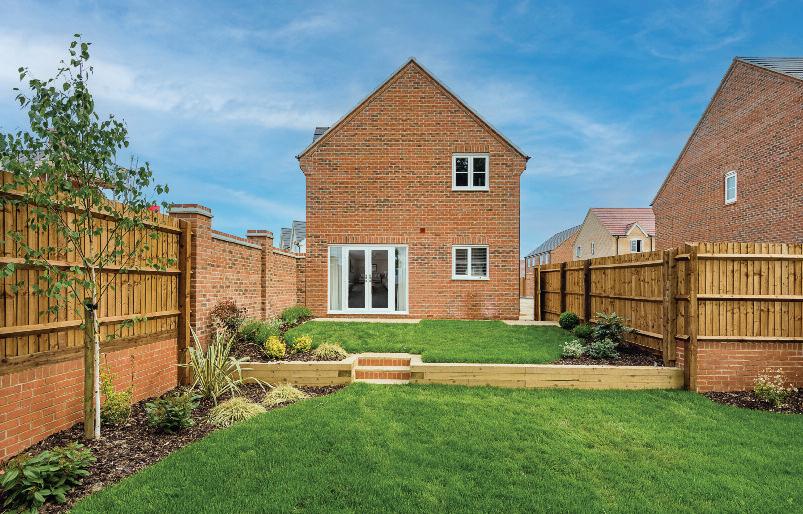

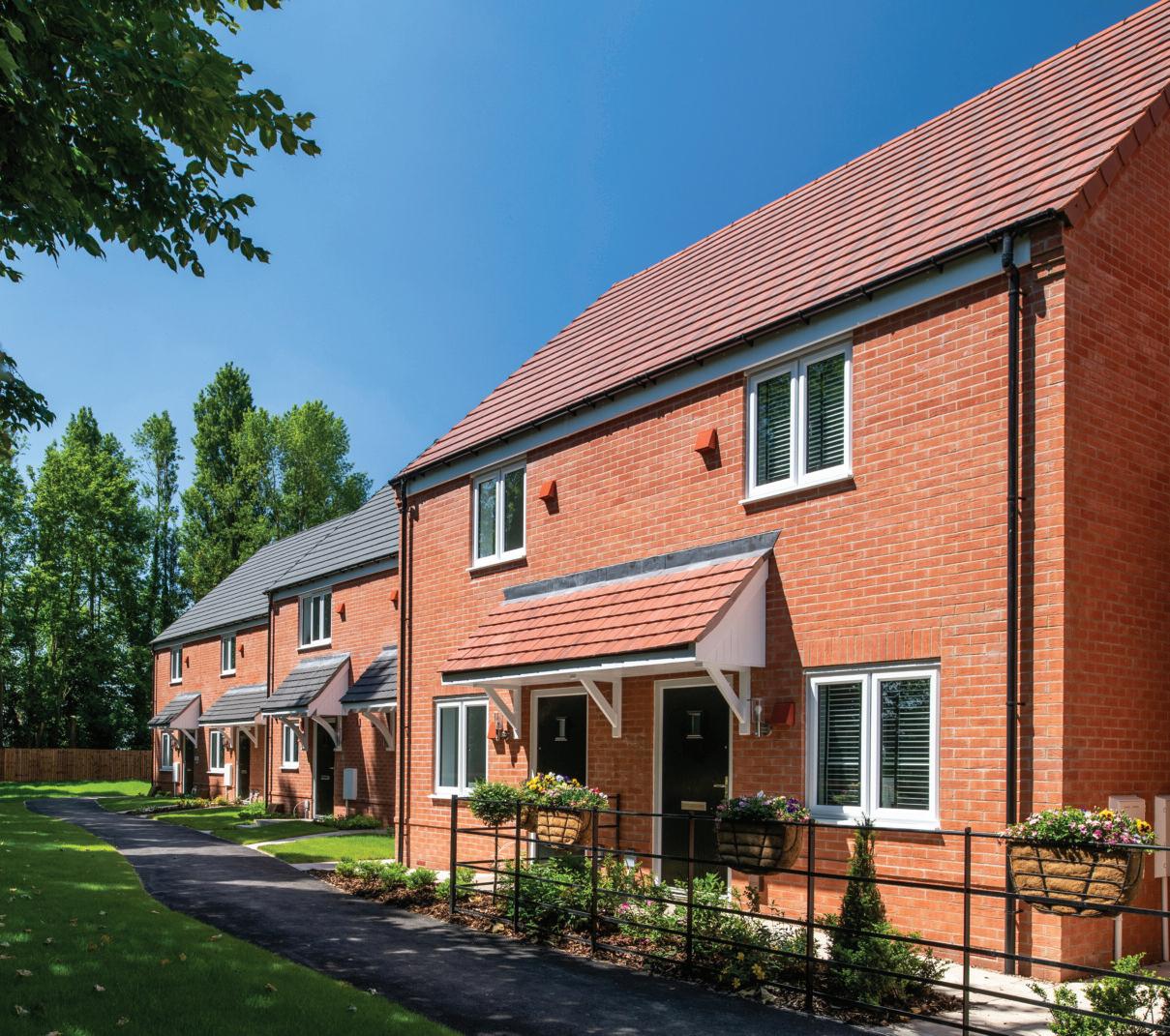
Using high-performance, long-lasting materials, with increased insulation and ventilation, the homes require less energy to run – potentially cutting down how much customers pay to heat them and emitting less greenhouse gases into the atmosphere directly and indirectly.
Sustainability goals
I think it is clear to most people that the climate crisis is a threat to nature, our economy and society at large – and we need to act.
The construction industry, being a large contributor of emissions due to the sheer scale of the sector, I think can play a huge role in lowering emissions and building a more sustainable future.
At Cora, we are determined to show how developers can create excellent homes and thriving communities in an environmentally conscious way. Since our rebrand last year, we have produced an in-depth Sustainability Report , identifying ways in which we will reduce our emissions, construction waste and carbon footprint.
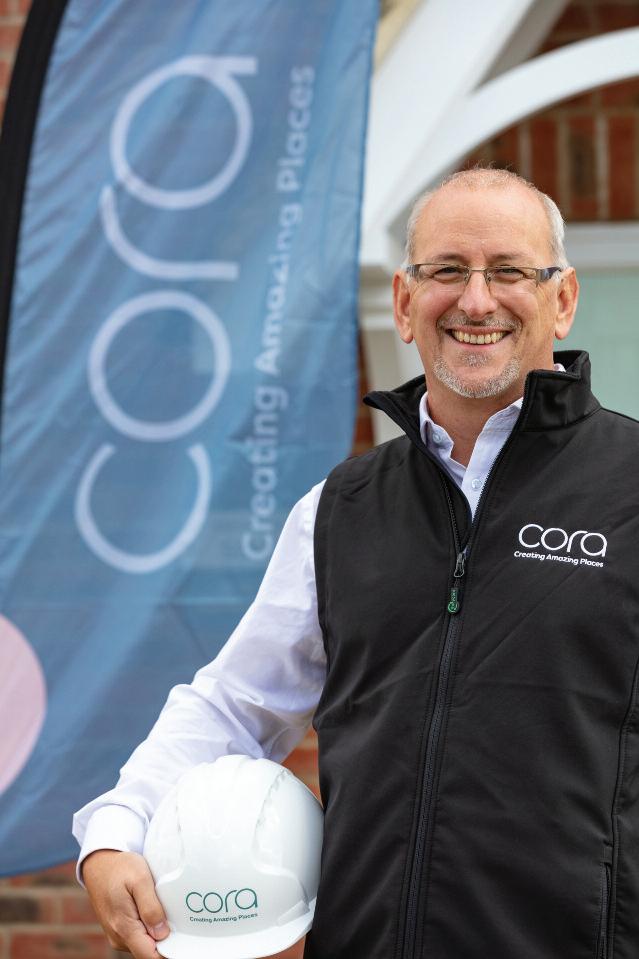
We have pledged to halve our greenhouse emissions by 2030 and to achieve net zero by 2050, signing up to the SME Hub Climate Change Commitment and the UN’s Race to Zero. MMC of Construction will play a key role in this goal.
However, we don’t want to walk this path alone – we want to see a change in the sector as a whole. The construction industry is at the forefront of the climate emergency, and we want it to play its part in changing the world for the better.
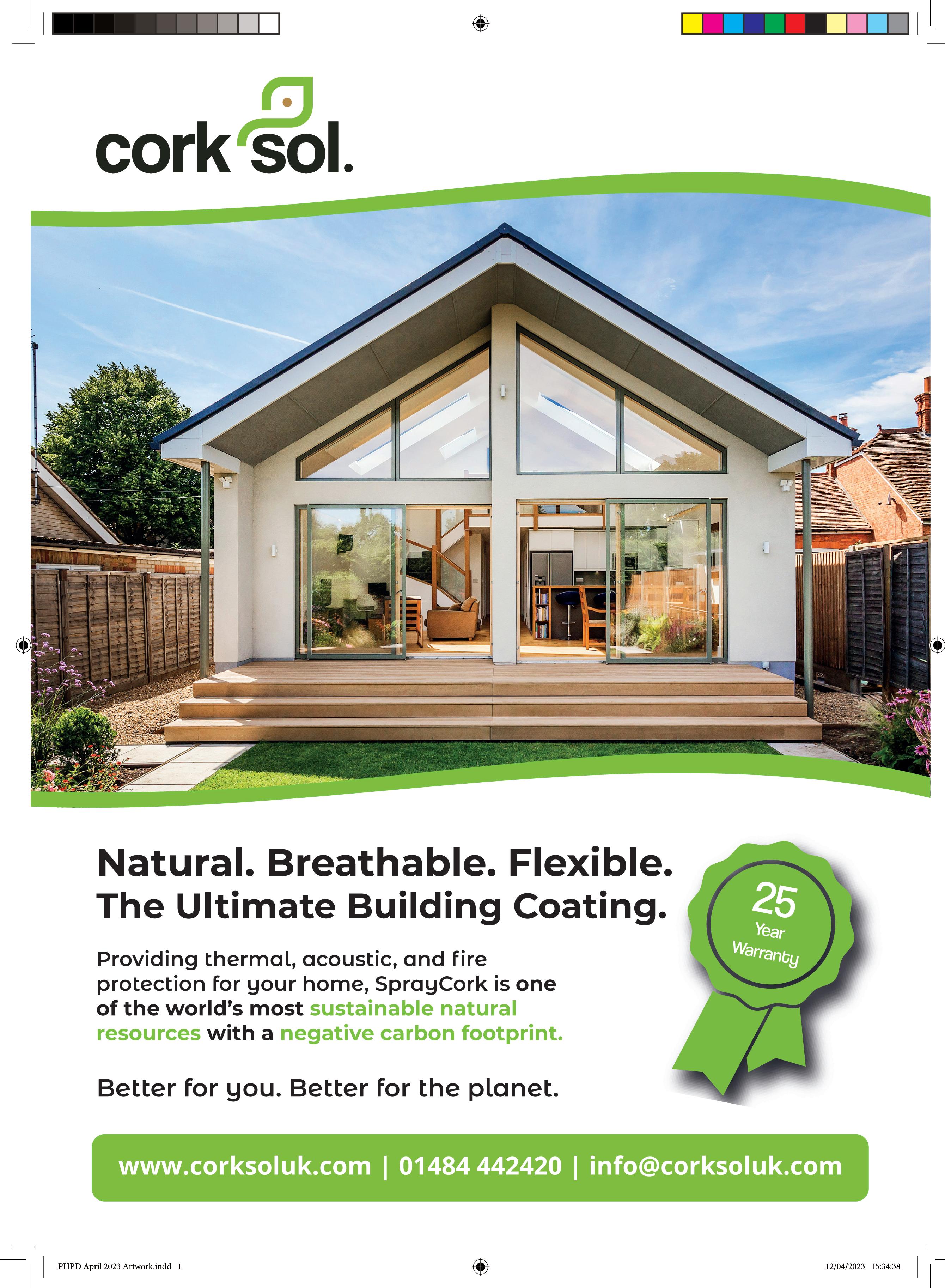